聆风全貌超越发动机车的新一代EV.docx
《聆风全貌超越发动机车的新一代EV.docx》由会员分享,可在线阅读,更多相关《聆风全貌超越发动机车的新一代EV.docx(10页珍藏版)》请在冰豆网上搜索。
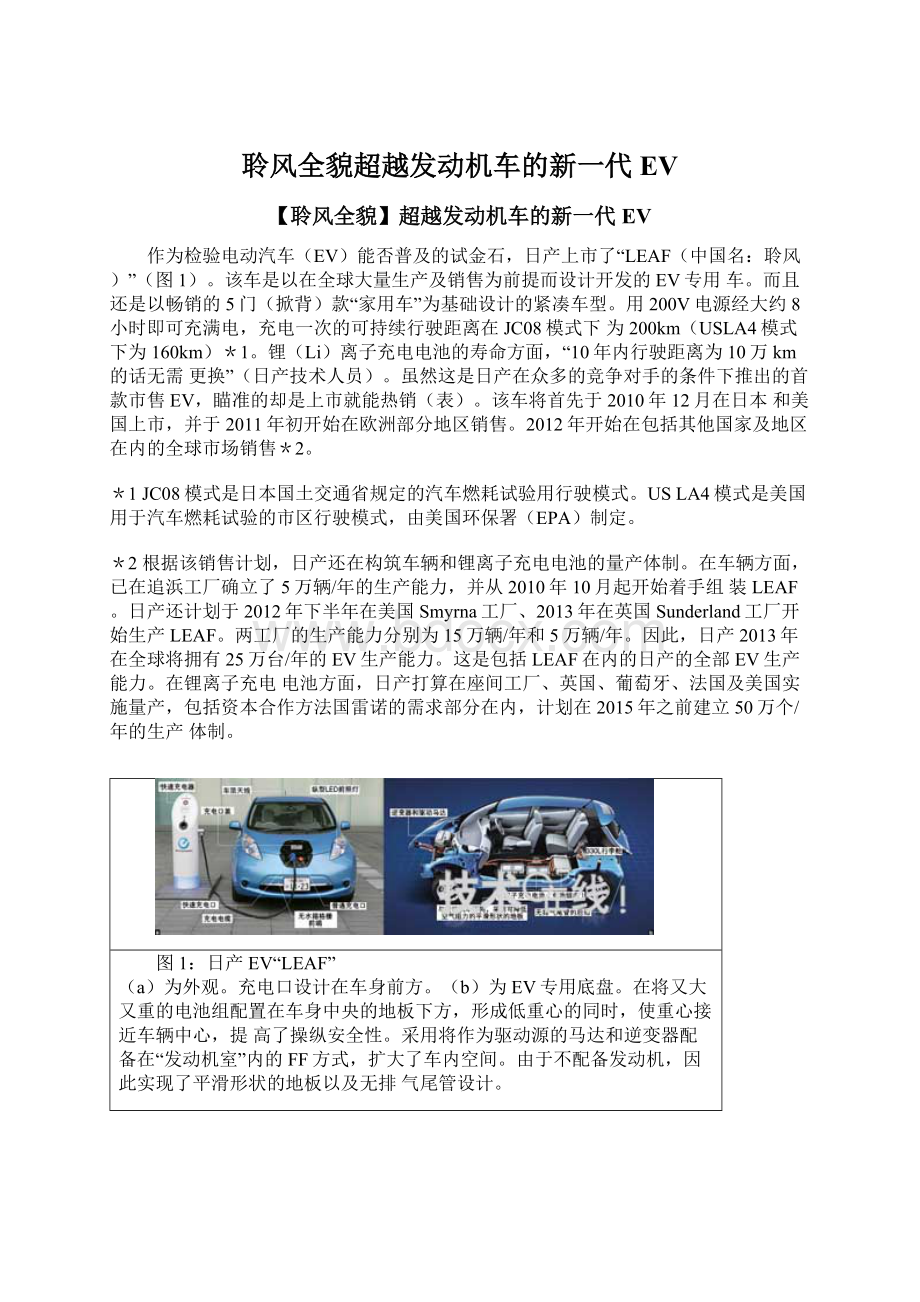
聆风全貌超越发动机车的新一代EV
【聆风全貌】超越发动机车的新一代EV
作为检验电动汽车(EV)能否普及的试金石,日产上市了“LEAF(中国名:
聆风)”(图1)。
该车是以在全球大量生产及销售为前提而设计开发的EV专用车。
而且还是以畅销的5门(掀背)款“家用车”为基础设计的紧凑车型。
用200V电源经大约8小时即可充满电,充电一次的可持续行驶距离在JC08模式下为200km(USLA4模式下为160km)*1。
锂(Li)离子充电电池的寿命方面,“10年内行驶距离为10万km的话无需更换”(日产技术人员)。
虽然这是日产在众多的竞争对手的条件下推出的首款市售EV,瞄准的却是上市就能热销(表)。
该车将首先于2010年12月在日本和美国上市,并于2011年初开始在欧洲部分地区销售。
2012年开始在包括其他国家及地区在内的全球市场销售*2。
*1JC08模式是日本国土交通省规定的汽车燃耗试验用行驶模式。
USLA4模式是美国用于汽车燃耗试验的市区行驶模式,由美国环保署(EPA)制定。
*2根据该销售计划,日产还在构筑车辆和锂离子充电电池的量产体制。
在车辆方面,已在追浜工厂确立了5万辆/年的生产能力,并从2010年10月起开始着手组装LEAF。
日产还计划于2012年下半年在美国Smyrna工厂、2013年在英国Sunderland工厂开始生产LEAF。
两工厂的生产能力分别为15万辆/年和5万辆/年。
因此,日产2013年在全球将拥有25万台/年的EV生产能力。
这是包括LEAF在内的日产的全部EV生产能力。
在锂离子充电电池方面,日产打算在座间工厂、英国、葡萄牙、法国及美国实施量产,包括资本合作方法国雷诺的需求部分在内,计划在2015年之前建立50万个/年的生产体制。
图1:
日产EV“LEAF”
(a)为外观。
充电口设计在车身前方。
(b)为EV专用底盘。
在将又大又重的电池组配置在车身中央的地板下方,形成低重心的同时,使重心接近车辆中心,提高了操纵安全性。
采用将作为驱动源的马达和逆变器配备在“发动机室”内的FF方式,扩大了车内空间。
由于不配备发动机,因此实现了平滑形状的地板以及无排气尾管设计。
专注于EV专用车
LEAF在日本的售价为376万4250日元(含税)。
利用日本政府补贴的话,则为298万4250日元(含税)的“较便宜价格”(日产首席执行官志贺俊之)。
销售取得开门红。
仅日美两市场的预订就获得了合计2万6000辆的订单。
日产为LEAF开发了EV专用底盘。
其中,将又重又大的锂离子充电电池配备在了车身中央的地板下方,即相当于前座到后座之间的位置(长度方向)上。
这里尤其要提到的是,日产将电池模块(由4块电池单元构成)更多地配置在了前座和后座正下方,而在后座乘客脚下配置得较少,不会让乘客感到不便。
另外日产还在车身骨架上增加了电池支架和逆变器固定支架。
这样不仅可以固定各自的部件,而且还具有提高车身刚性的作用。
驱动用马达(以下简称马达)位于逆变器固定支架下方,被固定于在发动机车的“发动机室”内的副车架上(图2)。
这也就是通常所说的前置发动机(马达)前轮驱动(FF)方式的车辆。
图2:
逆变器和马达的配备位置
作为FF方式的车辆配备在“发动机室”内。
逆变器设置在连接车身左右的、逆变器固定用支架上。
通过该支架,还提高了车身刚性。
不仅是逆变器和马达,DC-DC转换器、充电器及加热器等众多部件也都位于“发动机室”内。
这一手段旨在通过尽可能在车室外侧追加部件来扩大车内空间和后备箱容量。
发动机车无法体会到的性能
LEAF的特点之一是超越同级别发动机车的高行驶性能。
驾驶员踩油门时会强力加速。
通过以马达为驱动源,从转速几乎为零的状态即可产生最大扭矩(280N·m),因此起动时的加速性出色。
尽管是紧凑车型,但却可实现与排量为3L的发动机车相同的加速性能。
不过,马达的最大转速为9800rpm,最高时速为145km/h。
不适于在德国高速公路等无限速道路上超高速行驶。
此外LEAF还利用内部电阻小、可输入输出大电流的锂离子电池的特性,“以1ms为单位”(日产技术人员)高速控制马达扭矩。
这一点被充分用于抗振控制。
具体做法是通过精密控制驱动系扭振共振点付近的扭矩来抑制振幅,实现无生硬感的顺畅加速。
LEAF的操纵稳定性也很出色。
又大又重的电池组配备在车身中央的地板下方,因此与FF方式的发动机车相比重心较低,而且由于是配备在车辆中心附近,因此绕偏摆轴旋转的惯性力矩较小。
此外再加上前述以1ms为单位的马达扭矩高速控制,从而提高了转弯时的操纵稳定性。
日产LEAF的开发负责人门田英稔自信地表示:
“只要一打方向盘就能顺利转弯。
而且车尾的甩离感也较少,打造成了动作柔和的汽车。
”
当然,车内的静音性也很高。
这是因为不会产生发动机的声音、振动以及排气管声音,而且车身刚性也比发动机车提高。
另外,车身的振动也由此得以抑制。
彻底实施品质检测
此外LEAF还非常注重安全性能。
将电池组收放于车身中央的地板下面,其原因还在于为了强化对外部的机械性、热性及电气性侵入进行防范,使损伤控制在最小限度。
在所进行的冲撞实验中,正面冲撞以56km/h时速、后面冲撞以80km/h时速撞击了车身,“确认电池组未受到任何损伤”(门田)。
为了防止触电,高电压部件封闭到保护壳中并进行了绝缘。
此外还采用了发生冲撞时切断高电压的设计(图3)。
并且还通过用电线将这些保护壳与车身连接起来,使它们形成了等电位。
这样,即使在这些保护壳万一失去绝缘性时,而乘客刚好此时接触到了保护壳和车身,也会因为没有电位差而使电流不流经人体。
图3:
提高了对高电压的安全性
通过车身构造保护锂离子充电电池,包括该电池在内的高电压部件采用绝缘构造。
此外还会在发生冲撞时切断高电压。
另外还进行了积水路面的行驶实验。
比如,发动机车“TIIDA”在水深700mm的积水路面上行驶时,当水从进气管进入后发动机就会熄火,而LEAF在这样的路面上行驶时也没问题。
原因是电池组等已被严密密封起来。
用智能电话进行远程操作
比现有发动车更多地使用了IT技术,这也是LEAF的一项特点。
LEAF导入了专用的信息通信系统“EV-IT”,可接入日产车载信息服务“CARWINGS”的数据中心来获取汽车信息或操纵车辆。
由此提高了EV独有的便利性,消除了用户对电池用完等情况的担忧*3。
*3要想使用CARWINGS,需要加入“日产零排放支持计划”或签订“CARWINGSforEV”合同。
比如,配备了可在驾驶中显示当前的电池余量能够行驶多远距离(显示能够到达的区域地图),或者在电池余量不足时介绍附近可充电的地点及其设施信息的功能(图4)。
其中,对驾驶员来说尤为担心的是电池用完的问题,因此除了会根据过去的充电履历保存充电点信息之外,还会通过CARWINGS进行自动更新,使用户住宅周边的充电点信息总是保持最新状态。
图4:
EV-IT的功能
(a)为在导航仪屏幕上调出称为“零排放菜单”的EV相关功能的情形。
通过该功能可搜索充电站或确认预计到达地地图(b)。
CARWINGS的服务还可通过个人电脑、智能电话及手机查看电池的状态,在家中及办公室即可进行开始或停止充电的控制。
而且还可远程操纵空调,在充电时事先于出发前将车内温度调整到最佳程度。
这样便可在开始行驶后降低空调的负荷,从而延长可以行驶的距离。
另外还配备有可在任意时间充电的定时充电功能,可利用便宜的深夜电力来充电。
电池成本在200万日元以下
日产在LEAF的开发上尤其致力于主要部件即锂离子充电电池和马达的自制。
这样做除了考虑到这些都是日产首款EV配备的核心部件,需要确立相关技术之外,还有另外一个重要原因。
这就是“即使想从外部采购,也没有适合LEAF的部件”(日产副社长山下光彦)。
由于EV用部件及材料的开发刚刚就绪,市场上几乎没有可供选择的产品,因此日产只有自已来制造。
下面就从日产自制的锂离子充电电池来看一下。
作为EV的课题,必须要指出的是价格高且充电一次的持续行驶距离较短的问题。
要想解决这些课题,最有效的手段是降低锂离子充电电池的成本以及提高其性能。
降低成本自不必说,而从性能来看,具体而言就是要提高重量能量密度(以下简称能量密度),如果能够提高能量密度,则可通过配备少量电池来获得充分的一次充电持续行驶距离。
LEAF配备的锂离子充电电池在这两方面均得到大幅改善。
首先,电池的能量密度估计为140Wh/kg左右。
对于这一性能的提高,日产已在2009年7月举行的“09年先进技术说明会”上做过介绍,而此次还公开了降低成本的部分进展。
据日本新能源及产业技术综合开发机构(NEDO)调查,车用锂离子充电电池的价格2009年为10万日元/kWh。
LEAF所配电池的容量为24kWh,因此粗略换算的话为240万日元。
不过,日产解说员在此次发布会上介绍说:
“如果以200万日元的价格来销售(电池组)的话仍会有很高的收益性”。
200万日元/24kWh也就是8.3万日元/kWh。
如果说这一价格仍能有高利润的话,成本上就要大大低于8.3万日元/kWh。
日产在这一方面从未放松努力,争取在2015年降至3万~4万日元/kWh。
采用锰类正极和层压构造
电池组成本的降低带来了良好的量产效果,其中日产采用的电池材料和电池单元构造也做出了巨大贡献。
日产的锂离子充电电池的特点是采用了锰(Mn)类正极(锰酸锂,LiMn2O4)和层压构造。
笔记本电脑等使用的是正极采用钴(Co)类材料(钴酸锂,LiCoO2)的电池类型。
锰的价格比钴便宜,而且价格变动也较少。
正极材料在锂离子充电电池的成本中占有较高比例,因此锰类材料在成本方面有利。
另外,锰类材料为尖晶石构造,即使锂在充电时从正极脱离,基本构造也会保留完好,因此稳定性较高,耐久性及安全性出色(图5)。
而钴类及3元类〔Li(Ni-Co-Mn)O2〕材料则是对锂进行三明治式层叠的层状构造,因此当锂脱离后容易变得不稳定。
图5:
尖晶石构造和层状构造的充电放示意图
尖晶石构造的锰类(LiMn2O4)正极在充电时即使锂脱离也会维持稳定构造,而层状构造的话容易变得不稳定。
锰类材料虽然成本低且稳定性高,但却存在能量密度低于钴类及3元类材料的课题。
这一课题通过采用简单的层压型以有效利用空间来解决。
普通锂离子充电电池大多卷绕着带状电极及隔膜收放在圆筒形及方形的外壳内,而层压型则层叠多个电极及隔膜封入铝层合薄膜中。
“与圆筒形相比层压型的部件数量少2~3成,因此可控制成本”(日产)。
LEAF配备的锂离子充电池以4个层压型电池单元为1组制造模块,通过嵌入48个这样的模块形成电池组。
发布会上展示的电池组是开发最终阶段的产品,因此与已量产的产品略有不同(图6)。
量产产品新导入了为使电极及隔膜不在内部移动而进行固定的构造。
其原因在于层压部分中形成了大量层叠薄型电极及隔膜的构造,如果这些电极及隔膜移动,导致电极间的距离出现不均的话,发电及充电时的反应条件就会发生变化。
图6:
电池组的构造
在钢制机壳中嵌入48个电池模块(a)。
在电池模块中放入了4个电池单元,因此按48×4计算,电池单元的总数为192个。
容量为24kWh,最大输出功率为90kW,总电压为360V。
外形尺寸为1570×1190×260mm。
重量约为280kg。
展示的电池组与实车配备的产品略有不同。
实车配备的电池组在电池单元的周围套上了画框形状的树脂部件,可结实地固定住(b)。
为此,通过加深在模块上面设计的凹坑形状来稳稳按住电池单元,并像画框一样用树脂部件将层压型电池单元的周边围起来的做法,来把电池单元结实地固定住。
而且“还在层压部分中加入了板材,形成了内部层叠体不会移动的构造”(日产)。
通过这一手段,电池的性能得到稳定,而且耐久性也有所提高。
电池的劣化程度“还要看使用情况,估计电池容量5年减少2成,10年减少3成”(日产)。
重量约280kg
电池组的重量达到约280kg。
与本田在“飞度(FIT)”及“INSIGHT”上配备的混合动力系统(整体约60kg)相比相当重。
不过,这也受到了电池组成为底盘一部分的很大影响。
电池组的外装由钢板制成,为了提高侧面冲撞时的安全性,在内部设置了横梁(图7)。
“电池组不仅可保护电池单元免受来自外部的冲击,而且还具有提高车身整体强度的作用”(门田)。
图7:
保护电池组的车身构造
为了在受到冲撞等冲击时也可防止电池组发生变形或破损,采用了与发动机车不同的车身构造。
另外还通过在电池组内部设置横梁等措施,作为车身构造的一部分为提高耐冲击性做出了贡献。
为了保护柔软、强度低的层压型电池单元,日产除了电池单元本身之外,还在模块、电池组及车身上采取措施,以综合性手段确保了电池的冲撞安全性,而电池组也为提高车身的耐冲撞性做出了贡献。
通过分布绕组抑制振动
接下来说一下马达。
日产为LEAF开发的是永久磁铁式同步马达,这是一款在转子内部插入多个强磁力钕铁硼(Nd-Fe-B)类烧结磁铁的IPM(InteriorPermanentMagnet,内嵌永久磁铁式)马达(图8)。
图8:
马达
开发了效率出色的EV专用IPM马达。
最大输出功率为80kW(这时的转速为2730~9800rpm),最大扭矩为280N·m(这时的转速为0~2730rpm)。
卷线方式采用分布绕组,减小了顿转扭矩,此外还为实现轻量化采用了铝合金机壳。
为了放大扭矩,与减速比约为8的减速器连接。
IPM马达与其他马达相比效率高,并可实现小型轻量化。
这些因素将对持续行驶距离带来影响。
此外还具备“对控制的响应性出色,从而可实现顺畅行驶”(日产)的特点。
虽然因使用钕磁铁而成本较高,但日产为了重视持续行驶距离和行驶性能,最终选择了IPM马达。
转子和定子均由层叠硅钢板构成。
层叠厚度为200mm左右,直径为300mm左右。
马达的重量包括铝(Al)合金机壳在内不到60kg。
顺便提一下,逆变器的重量为15kg出头。
卷线的绕线方式采用分布绕组。
虽然与集中绕组相比铜损略高,效率下降,但由于顿转扭矩(CoggingTorque)较小,因此具有可降低行驶时的振动的优点。
日产与专业厂商共同开发了绕线机。
制造时最费力的是线圈端部(从定子两端露出的卷线部分)的处理。
线圈端部需要压扁进行紧凑成型,但压扁方法不适的话可能会有损绝缘性,因此要加以注意。
该马达与减速比约为8的减速器连接,对马达扭矩进行放大。
最大效率达到95%
在最大效率方面,逆变器和马达合计高达95%,而且在市区实际行驶时的效率也很出色。
比如,“USLA4模式下的平均效率达到90%左右”(日产)。
最大输出功率为80kW,该数值可基本认为是恒定输出功率。
“锂离子充电电池的输出功率为90kW,因此将效率估计为90%,以大约80kW来转动马达”(日产)。
LEAF还设想作为出租车来使用,马达估计采用了可承受40万km行驶距离的设计。
不过,嵌入逆变器的电子部件没有如此长的寿命。
冷却采用水冷方式,以冷却水的温度保持在60℃以下为标准来控制马达。
比如,当马达内部快要达到使磁铁的磁力下降(退磁)的温度时,会通过降低输出功率来防止温度上升超过60℃。