工艺决策技术.docx
《工艺决策技术.docx》由会员分享,可在线阅读,更多相关《工艺决策技术.docx(45页珍藏版)》请在冰豆网上搜索。
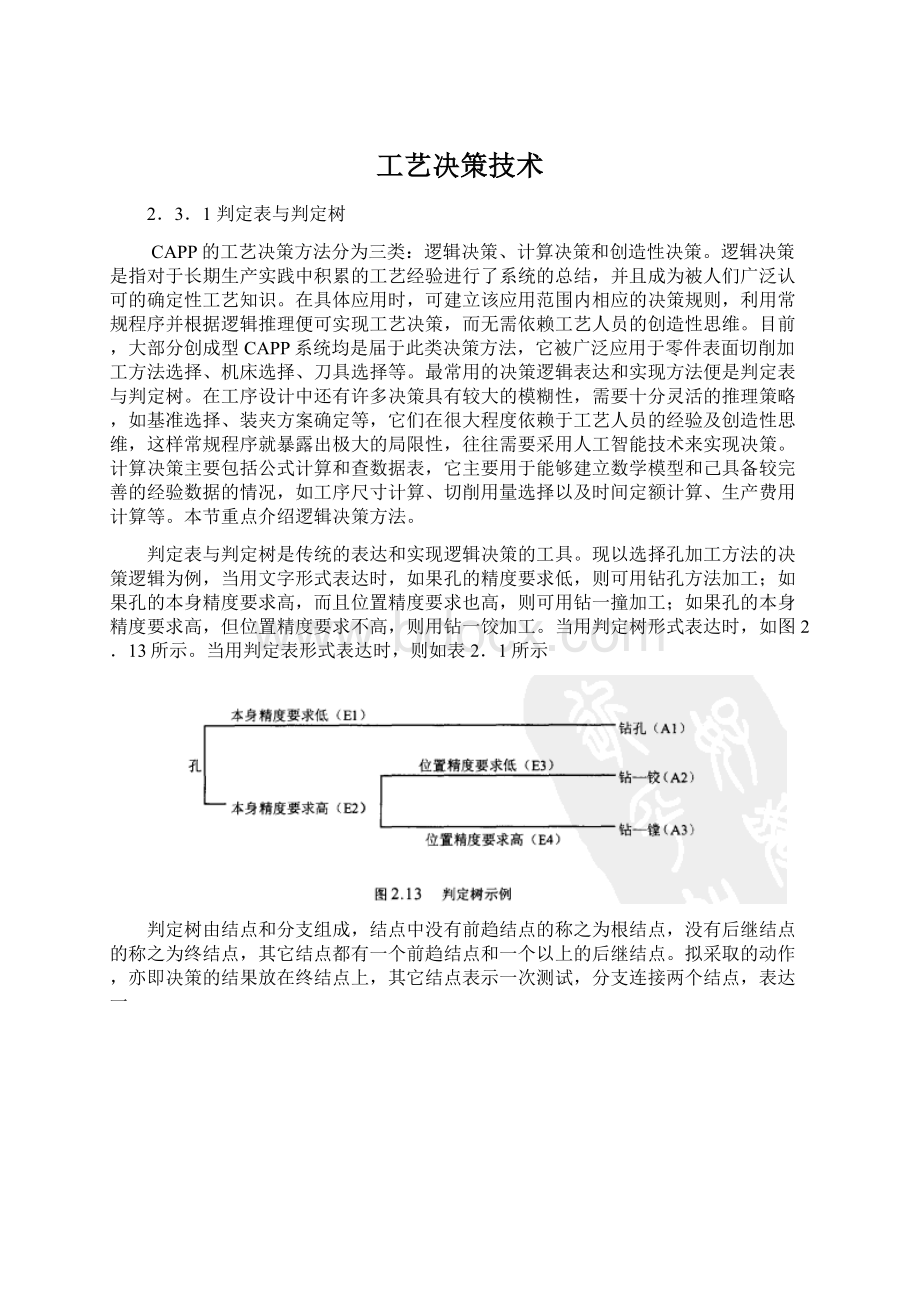
工艺决策技术
2.3.1判定表与判定树
CAPP的工艺决策方法分为三类:
逻辑决策、计算决策和创造性决策。
逻辑决策是指对于长期生产实践中积累的工艺经验进行了系统的总结,并且成为被人们广泛认可的确定性工艺知识。
在具体应用时,可建立该应用范围内相应的决策规则,利用常规程序并根据逻辑推理便可实现工艺决策,而无需依赖工艺人员的创造性思维。
目前,大部分创成型CAPP系统均是届于此类决策方法,它被广泛应用于零件表面切削加工方法选择、机床选择、刀具选择等。
最常用的决策逻辑表达和实现方法便是判定表与判定树。
在工序设计中还有许多决策具有较大的模糊性,需要十分灵活的推理策略,如基准选择、装夹方案确定等,它们在很大程度依赖于工艺人员的经验及创造性思维,这样常规程序就暴露出极大的局限性,往往需要采用人工智能技术来实现决策。
计算决策主要包括公式计算和查数据表,它主要用于能够建立数学模型和己具备较完善的经验数据的情况,如工序尺寸计算、切削用量选择以及时间定额计算、生产费用计算等。
本节重点介绍逻辑决策方法。
判定表与判定树是传统的表达和实现逻辑决策的工具。
现以选择孔加工方法的决策逻辑为例,当用文字形式表达时,如果孔的精度要求低,则可用钻孔方法加工;如果孔的本身精度要求高,而且位置精度要求也高,则可用钻一撞加工;如果孔的本身精度要求高,但位置精度要求不高,则用钻一饺加工。
当用判定树形式表达时,如图2.13所示。
当用判定表形式表达时,则如表2.1所示
判定树由结点和分支组成,结点中没有前趋结点的称之为根结点,没有后继结点的称之为终结点,其它结点都有一个前趋结点和一个以上的后继结点。
拟采取的动作,亦即决策的结果放在终结点上,其它结点表示一次测试,分支连接两个结点,表达一
个条件是否满足。
若满足,测试就沿分支向前传送,以实现逻辑“与”(AND)的关系;若不满足,则转向出发节点的另一分支,以实现逻辑“或”(oR)的关系。
这样,从根结点到终结点的任一条路径都表达了一条决策规则。
判定树很容易改写为程序流程框图。
图2.14是图2.13所示判定树对应的流程框图。
判定表是由四部分组成(见表2.1),双横线的上部两个区域是条件,其中左上区是条件说明,右上区是满足这些条件的各种可能的组合,表中用T表示满足所在行的条件。
双横线的下部是结果(动作),其中左下区是各种可能的行动,右下区是条件组合下采取的行动,用V表示。
由此可见,判定表右部的每一列就是一条决策规则。
判定表的条件之间是“与”的关系,行动之间也是“与”的关系。
判定表可通过分解(分成若干子表)、合并(几个表合为一表)以及连接等方法,描述多层次联系的复杂决策逻辑。
判定表的逻辑关系表达比判定树更清晰,而且格式紧凑。
判定表可以先转换成判定树,再写成程序。
2.3.2工艺决策及推理机
1.工艺决策知识及其表示
工艺设计是一项复杂的多层次、、多任务的决策过程(图2.15。
),而且其工艺决策涉及的面较广,影响工艺决策的因素也比较多,实际应用中的不确定性也较大。
国内的研究习惯上把工艺决策分为加工方法决策和加工J帧序决策,而国外把刀具轨迹、加工过程的计算机模拟等也作为智能CAPP决策的一部分。
通常工艺决策中的知识包括选择型决策逻辑(如毛坯类型及其尺寸的选择,加工方法的选择,机床及工、夹、量具选择,切削用量的选择等),规划型决策逻辑(如工艺路线安排、工序中加工步骤的确定等),以及加工方法知识(如加工能力、加工限度、预加工要求等)这些知识适合用产生式规则表达。
2.工艺推理过程‘.
工艺过程设计的目标是产生工艺规程,而同一零件可以采用不同的加工方法达到设计要求,因而同一零件的工艺规程又可以不同。
故工艺推理不宜采用目标驱动模式(反向推理策略),而适宜采用数据驱动模式(正向推理策略),即从零件的毛坯开始(此时工艺规程为空),根据零件的基本信息调用工艺决策知识逐步形成工艺规程,最终完成工艺设计任务。
图2.16所示是工艺推理的基本过程。
3。
基于框架的推理控制
根据工艺推理过程的特点,本节介绍一种面向加工表面对象的多级推理方式,一个框架表示一个加工表面对象,整个框架构成了完整的零件加工表面对象树。
在推理过程中,系统自顶向下搜索,遍历每个节点。
这种推理方式是以框架推理为主导,规则推理为核心,其它推理为辅的复合型推理模型,见图;2。
17。
推理系统在工、艺决策过程的控制下,驱动框架推理对每个框架进行识别和处理,并根据—汇needed侧面随时调用规则推理和辅助推理,完成工艺设计及工艺决策等相关任务,生成零件的加工工艺信息链(见图2.18,其中每个节点用一个框架描述),以便生成工艺卡、工序图及NC加工指令等时使用。
2.3.3工序决策
1.零件信息的分析与理解
工序决策是工序设计的重要内容。
它首先要对零件信息进行分析与理解,也就是对零件切削表面进行识别,包括对其几何形状、尺寸公差、结构工艺性、技术要求等信息的分析研究。
这些在人工设计中是由工艺员读图来完成的,可是在计算机辅助工序设计中成了一项关键技术。
因为需要以计算机内部能够识别及处理的方式来描述零件信息,而且要能被CAPP系统所接收。
处理的方式与描述的方式是紧密相关的,基于特征的产品建模技术的发展为零件工艺信息的计算机描述及处理提供了有效的途径。
在特征与零件切削表面之间可以建立内在的联系,“形面要素”、“形体要素”、“加工特征”等实质上均可看作是对零件切削表面自身的信息以及各表面之间的组织关系的一种表达。
如果在零件信息的描述中采用了基于特征的方法,显然在工序决策时就能比较容易地根据特征识别结果来确认零件切削表面的信息,这正是当前CAPP系统普遍采用的一种方法。
2.各切削表面加工方法的选择
加工方法选择实际上是将零件信息与企业的资源进行匹配的过程。
同一种加工方法在不同的工作条件下所能达到的精度会有所不同。
如果细心操作、精心调整,选择相应的切削用量,就可能得到较高的精度,但往往却会花费较多时间,增加了生产成本,因此,这里所指的精度是在正常的机床、刀具、工人等工作条件下,以合适的工时消耗所能达到的加工精度。
表2.2表示了对于孔这样一种典型切削表面来说,各种加工方法可达到的精度(Jr)及表面粗糙度(及。
)。
零件是由许多表面组成的,往往包含多种典型的切削表面(即加工特征),如外围、孔、槽、平面、成形表面等等。
对于每一种典型切削表面均可列出类似于表2.2的各种加工方法所能达到的精度及表面粗糙度。
因此,在识别或理解了零件切削表面的信息后,便可以根据具体情况,从表2.2或其它相应的表中选择最合适的加工方法。
图2.19是外旋转表面加工链网络图,图2.20是孔加工链网络图,它们是选择典型加工方法的一种表达方法,从加工链网络图中可以看出达到同一加工要求可以有不同的加工链。
在选择加工方法时,根据企业当时的资源(人、财、物、技术)条件的约束,寻求满足T、Q、C为目标的最优的加工链。
同样,对于其它各种典型切削表面,均可以图2.19、图2.20的方式列出其可能选择的典型加工方法,从图中亦可看出,加工方法的选择需要一系列的逻辑决策。
典型的加工方法是指在分析、总结企业内各种生产工艺方法、各种生产经验和各种与加工有关的规范后,提出的带有指导意义的加工过程,它可以随着生产设备的更新、生产工艺的发展,甚至操作工人的改变而有所改变,还可能受到企业自身特点的影响,所以具有较大的灵活性;再者,上述加工方法的选择并不等同于“是非”选择,有的准则是模糊的,常会出现模棱两可的情况,这就是工序设计的非一致性。
这些特点在计算机辅助工序决策时应该考虑到的。
3.编排合理的加工顺序
t1)基准的选择加工顺序是指工序的先后排列。
它与加工质量、生产率和经济性密切相关,安排加工顺序首先要考虑的因素就是工艺基准面,零件在加工时所用的工艺基准称为定位基准,定位基准是指零件在机床上加工时,它们被用来决定零件相对于刀具的位置。
根据该基准面是否被加工过,定位基准又可分为粗基准和精基准。
前者是指没有加工过的毛坯面被用作定位基准;后者是指已加工过的表面被用作定位基冶。
当然,定位基准的选择是要遵循一定的原则的。
一般来说,定位基准的选择原则可简要归纳为:
1)定位基准应与设计基准重合。
2)安装面与导向面应选择尺寸大者。
3)便于夹紧,在加工过程中稳定可靠。
零件是由许多表面组成的,往往包括多种典型的切削表面(即加工特征),例如外圆、孔、槽、平面、成形表面等。
对于每一种典型切削表面均可列出类似于表4—2的各种加工方法所能达到的精度及表面粗糙度。
因此,在识别或理解了零件切削表面的信息后,便可以根据具体情况,从表4—2或其他相应的表中选择最合适的加工方法。
图4。
7是外旋转表面加工链网络图,图4—8是孔加工链网络图,它们是选择典型加工方法的一种表达方法,从加工链网络图中可以看出达到同一加工要求可以有不同的加工链。
在选择加工方法时,根据企业当时的资源(人、财、物、技术)条件的约束,寻求满足(T、Q、C)为目标的最优的加工链。
同样,对于其他各种典型切削表面,均可以图4—7、图4。
8的方式列出其可能选择的典型加工方法,从图中亦可看出,加工方法的选择需要一系列的逻辑决策。
典型的加工方法是指在分析、总结企业内各种生产工艺方法、各种生产经验和各种与加工有关的规范后,提出的带有指导意义的加工过程,它可以随着生产设备的更新、生产工艺的发展,甚至操作工人的改变而有所改变,还可能受到企业自身特点的影响,所以具有较大的灵活性;再者,上述加工方法的选择并不等同于“是”或“非”选择,有的准则是模糊的,常会出现模棱两可的情况,这就是工序设计的非一致性。
这些特点在计算机辅助工序决策时应该考虑到。
3.编排合理的加工顺序
(1)基淮的选择加工J顷序是指工序的先后排列,它与加工质量、生产率和经济性密切相关。
安排加工J顺序首先要考虑的因素就是工艺基准面,零件在加工时所用的工艺基准称为定位基难,定位基准是指零件在机床上加工时,被用来决定零件相对于刀具的位置的基准。
根据该基准面是否被加工过,定位基准又可分为粗基准和精基准。
前者是指没有加工过的毛
以上这些选择原则必须在实际应用中根据具体情况灵活掌握。
有些原则,如定位基准与设计基准重合原则和基准单一原则,有时会发生矛盾,这时,必须凭借工艺知识,综合考虑实际加工的多方面因素,作出合理优化的选择。
制订加工顺序时,总是先安排精基准面的加工;然后采用精基准面定位来加工其他表面。
如果有多个精基准,则必须在他们被使用之前加工完毕。
可见,选定粗、精基准,使得加工顺序的安排具有了一个基本轮廓。
(2)主要加工表面的安排零件的主要加工表面一般都是指精度或表面质量要求比较高的表面,它们的加工好坏对整个零件的质量关系较大,往往它们的加工工序也较多。
因此,一般应以考虑主要表面的加工顺序为主干,再将其它表面的加工适当穿
插其间。
例如,箱体零件中,主轴孔、孔系和底平面一般是主要表面,所以应首先考虑他们的加工顺序。
而其它的,如固定用的通孔和螺纹孔、端面和侧面,则可以适当安排,端面和侧面就可与底面、顶面安排同一次装夹中进行加工;通孔、螺纹孔则可与主轴孔安排在同一次装夹中进行加工。
在上述加工表面的安排中,通常应考虑“先面后孔”、“先粗后精”的排序原则。
例如,固定用的通孔及螺纹孔的加工一般安排在它们所附着的平面加工完之后;又如,主轴孔的精度和表面质量的要求比较高,所以其粗精加工应该分开,主轴孔的精加工应安排在最后(手铰或精膛一浮动经)。
(3)热处理工序与辅助工序的安排热处理工序可分为四类:
一类是为了改善切削性能而进行的,如正火、调质及退火等,这类热处理工序应安排在切削加工之前;第二类是为了消除内应力而进行的,如时效处理,应安排在粗加工之后精加工之前;第三类是为了得到预期的物理机械特性,如渗碳、渗氮、淬火等,这类热处理工序应安排在粗加工、半精加工之后精加工之前。
表面淬火后,一般只能进行磨削加工;第四类是为了使表面耐磨耐腐蚀或美观,如镀铬、发兰等,一般都放在最后工序。
辅助工序包括去毛刺、清洗、退磁及检验等。
它们一般安排在关键工序的前后、转换车间的前后、加工阶段的前后(粗加工完精加工前或者精加工后精密加工前),或者零件全部加工完毕后。
加工顺序的安排是一个比较复杂的问题。
特别是对于普通机床,人为因素的影响大,灵活性也大,更应利用长期生产实践所积累的经验,结合具体情况,灵活掌握上述原则。
4.选择加工机床和相关的工艺装备
加工机床的选择,对工序的加工质量、生产率和经济性都有很大影响。
在进行机床选择时,一般调出CAPP系统内预先建立的机床数据库,它提供机床规格及平均经济加工精度信息,使其与零件所选择的加工方法信息相比较,然后作出决策。
一般可先按零件及其加工方法的要求作出初选,然后再根据选得的切削用量计算出切削力、切削功率进行校核,有的系统还可根据PPS(生产过程计划)对机床利用率情况进行适当的调整。
工艺装备(刀具、夹具、量具)的选择与机床的选择有些类似,即同样需要根据零件信息和选择的加工方法信息去和预先建立在工装数据库中的信息相比较,然后作出决策。
当没有现成的通用工装可利用时,CAPP系统就应提出专用工装设计的要求。
在机械加工中,零件、机床、刀具与夹具组成的工艺系统,是一个相互联系、相互影响的整体,因此,CAPP系统的决策机制应努力反映这种联系,并帮助工艺员得到从全局上比较优化的决策结果。
2.3.4工艺尺寸确定
工艺尺寸确定包含了加工余量的选择、工序间尺寸和公差的确定等内容。
从机械制造工艺学的角度来看,加工余量值及工序间尺寸公差值对于机械加工的质量、生产率、成本均会产生影响,而且三者间还会互相影响。
11加工余量的选择、
加工余量由三部分组成:
(1)上一工序的加工精度,它包括上一工序的加工尺寸公差(可由公差表中查得)和上一工序的位置精度(根据具体情况计算)。
(2)上一工序的表面质量,因为上一工序加工后遗留下来的表面粗糙度和表面缺陷厚度(也可查表获得)应包含在本工序的余量中。
(3)本工序的安装误差,它包含定位误差和夹紧误差(可以根据具体情况计算或考查阅有关的资料获得)。
各工序问余量之和便成为该表面的总余量。
余量的组成部分中,既有系统误差,也有随机误差。
在计算加工余量时可用概率法来综合分析,用分析计算法确定加工余量必须占有充分的资料及统计数据,计算也复杂。
所以除了特别重要关键零件或大批量生产的少数情况外,目前大多数工厂采用查表与经验相结合的方法。
查表法是根据企业多年来积累的资料,整理而得到的用于各种加工方法的加工余量表格,根据当前的加工方法、加工精度等直接从表格中查出工序间余量推荐值,它比较方便迅速i实用。
有些工厂还将余量确定表纳入工厂标准之内。
但正因为表格是通用的,无法考虑具体情况,因此查得的余量值往往与实际情况有些距离,而且通用表格的整理本身也是一件非常不容易的事,基于这两个原因,由一些有经验的工程技术人员或工人根据经验对查表所得值进行修正,或者直接进行确定,这是目前大多数工厂仍在采用的方法。
现举例说明查表法确定加工余量的过程。
假设一个外围表面的工艺过程为粗车一半精车一淬火一粗磨一精磨一研磨。
查阅工序手册得到:
研磨余量为0.01mm,精磨余量为0.1mm,粗磨余量为0.3mm,半精车余量为1.Imln,粗车余量为4.5mm。
相加后
得总余量是6.01mm,可圆整为6mm,而把粗车余量定为4.49mm。
2。
工序间尺寸的计算
一般采用“由后往前”的办法。
先按零件图的要求,确定最终工序的尺寸及公差,再按选定的加工余量推算出前一道工序的尺寸,而公差则是按本工序加工方法的精度来给出。
当工序设计中存在基准转换(工艺基准与设计基准不重合)时,就需要进行工序尺寸换算,对于位置尺寸关系比较复杂的零件,这种换算也比较复杂。
工序尺寸计算常用尺寸链分析计算方法,工序尺寸计算的工作流程如图2.21所示。
在图2.2l中,第二阶段是建立尺寸树,并由此组成设计尺寸链与余量尺寸链。
第三阶段需进行尺寸校核,即校核设计尺寸公差能否得到保证。
第四阶段需进行余量校核,即校核最小余量是否小于或等于零,公差校核可按组成环公差叠加。
如上节所述,亦可按概率理论算出。
如校核不通过,则重新调整工序尺寸公差或余量值,当调整后校核仍迈不过时,则应显示出错信息,建议修改工序尺寸标注方法。
第五阶段,是用邻接矩阵来计算工序尺寸值。
2.3.5工艺参数决策
工艺参数,又称为切削参数,一般是指切削速度(v)、进给量(/)和切削深度(“”)。
这些参数值的选择对于加工时间、切削表面的质量、加工精度、机床的选择以及加工费用等会产生直接的影响,而且很多约束条件又是互相制约的。
所以,在进行工艺参数决策时,必须综合考虑多方面因素,努力求得各切削参数的优化组合。
在CAPP系统中常用的方法是预先建立适应本企业的切削用量数据库以供决策时使用。
目前,国外根据多年实验研究的积累,己出版了多种实用的机械加工数据手册,
包含了适用于不同的机床、刀具、零件材料、切削深度等条件的推荐的进给量和切削速度。
这是人类共同的宝贵财富,可以提供很好的借鉴。
同时,我国也由国家或有关部门推荐出版了各种机械加工手册、切削用量手册等,可以从中按需选取有关数据内容,做成数据库。
有些工厂以本厂实践经验为基础,收集厂内操作工人在实际生产中的经验数据,经过分析整理,相对于各种刀具的寿命值规定出相应的切削速度、切削深度和进给量,并据此做成切削用量数据库。
这种方法比较简便易行,但不够准确,局限性也比较大。
第4章交互型CAPP系统
本软件是为了配合《机械加工工艺手册(软件版)》而开发的计算机辅助工艺设计系统。
本系统由西安交通大学CAD/CAM研究所开发。
整个系统由两个CAPP子系统组成:
一为交互型CAPP系统;另一为变异型CAPP子系统。
由于工艺设计随企业的资源不同,加工工艺习惯不一样,操作人员的水平不同,设计的加工工艺过程不尽相同,即使在同一企业内,不同的工艺设计人员也可能设计出不同的加工工艺过程,工艺设计的质量在很大程度上取决于工艺设计人员的技术水平。
为了让用户更好地了解本系统并熟练地掌握使用系统,特编写本使用说明书,通过阅读本使用说明,您可以妓照使用说明提示的操作步骤,迅速了解和掌握本系统的使用,从而提高您编制工艺的效率。
4.1系统开发背景
随着科学技术的发展,为适应瞬息多变的市场需求及机械制造业信息化工程发展的需要,数字化系列手册(软件版)必将成为推动制造业信息化工程广泛深入开展的核心基础支撑环境之一。
为此,机械工业出版社在出版《机械设计手册(软件版)》的基础上,组织出版了其妹妹篇《机械加工工艺手册(软件版)》,它是国家“十五”电子出版物规划项目之一。
本软件是配合《机械加工工艺手册(软件版)》而研制的,本系统的原型是在企业已经使用的CAPP系统并证明其切实可用和使用效率较高的基础上,根据手册的需求精炼出的一个系统。
众所周知,开发和推广应用CAPP系统可缩短工艺规程设计和生产准备时间,加快零件的制造周期,降低零件的生产成本,并可以提高工艺设计文档的质量。
研制实用、可靠、运行效率高的CA卯系统已经成为机械制造业信息化工程的一个很重要的课题,而且一个具有智能导航的CAPP系统对工艺设计人员熟练程度的要求也比较低,即工艺经验较少的工艺人员也能借助于CAPP系统设计出高质量的工艺规程。
由于工艺设计的多变性和对具体企业资源的依赖性、针对性强等原因,通用CAPP的发展远远滞后于CAD、CAM、CAE等软件的发展及应用。
本产品以交互式CAPP为主,提供了针对企业的实际资源情况,建立适应本企业需求的工艺数据库(包括加工设备库、工装库、工时定额库、工艺术语库、切削用量库、材料库、毛坯库、工艺文件库等等)及实施CAPP的必须工具,力求减轻工艺人员的重复性劳动。
交互型CAPP系统是通用CAPP系统中较容易实现的方案之一,按照不同类型的:
[艺需求,编制一个人机交互软件系统,工艺设计人员根据系统进程的提示,进行人机交互操作,操作人员在系统的提示引导下,回答工艺设计中的问题,对工艺过程进行决策及输入相应的内容,形成所需的工艺规程。
工艺人员在系统集成环境下,根据实际情况,一步步地完成工艺的编制。
因此这种CA卯系统工艺过程设计的质量对人的依赖性很大,且因人而异。
因而一个实用的交互型CAPP系统必须具有下列条件:
1)具有支持工艺决策、工艺参数选择的基于本企业资源的工艺数据库,它由工艺术语库、机床设备库、刀具库、夹具库、量具库、材料库、切削参数库、工时定额库等组成。
2)应有一个友好的人机界面,一个友好的人机界面必须具备下列功能。
①实时的人机交互,快速响应输入、输出,对操作人员有及时提示及智能引导功能,对输入内容能详细检查,对不正确的内容明确指出其错误性质,指出其修改的回溯点及回溯路径。
②对整个系统的组成应一目了然,能方便地调用各功能模块,并能快速无阻碍地进行切②界面布置合理,宜人悦目,整个系统要前后一致,规格统一,方便操作,用户掌握其·个模块交互操作,就能举一反三。
④用户记忆量最小。
⑤图文配合适当,既不令人眼花缭乱,又使人感到形象直观。
3)具有纠错、提示、引导和帮助功能。
4)数据查询与设计程序能方便地进行切换,杏询所得数据能白动地插入设计所需地点。
5)能方便地获取零件信息及工艺信息。
6)能方便地与通用图形系统链接,获取或绘制毛坯图及工序图。
4.2系统的体系结构4.2.1系统的总体结构
该系统以人机交互的方式来编制零件工艺。
工艺人员在系统集成环境下,根据实际情况步步地完成工艺的编制。
系统主要包括以下几个功能模块(图4.1):
1)零件信息检索
工艺人员在编制零件工艺时,首先就要进行零件信息检索。
在工艺人员输入零件图号后系统将检索零件信息数据库,并将检索出的零件信息显示出来,工艺人员可以编辑零件信息也可以交互地输入零件信息;如果没有检索到该零件,表示该零件信息没有建立,系统会给出提示。
2)零件信息输入
提供工艺人员一个交互输入零件信息的窗口。
工艺人员可根据零件的具体情况,输入诸如零件图号、零件名称、工艺路线号、产品、部件编号、材料牌号、毛坯类型、毛坯尺寸和设计者等基本信息。
3)交互式工艺编辑
提供工艺人员交互输入工艺内容和工步内容的窗口。
工艺人员可以很方便地添加、删除、插入和移动工序。
在工艺编辑过程中,工艺人员可以很方便地查询各种工艺数据,如机床、刀具、量具、工装和工艺参数等。
4)工艺设计过程管理
工艺编制完成后,应有一个工艺设计过程的管理过程。
在系统中为4个步骤,即审核、标准化、会签和批准。
5)工艺文件输出
系统主要输出两种工艺文件,即工艺卡和工序卡。
6)CAPP系统相关工具工艺设计过程管理分
本系统主要提供了工艺数据建立及其管理系统和工艺尺寸链的计算两种工具,用来建立适应本企业资源的工艺数据库及查询各种工艺数据和进行尺寸链的计算,尺寸链计算包括组成环的尺寸解算和封闭环的公差解算内部分。
系统工作流程如图4.2所示。
4.2.2系统的数据结构
系统在数据结构上,采用关系型数据库来存放数据。
零件信息、工艺信息、工步信息和其它工艺数据信息都存储在不同的二维数据表中,不同类型的数据表又存放在不同的数据库中。
此外,系统提供了用户自定义工艺数据库接口,用户可以根据自己单位的实际情况,定义自己的数据库,使系统具有了较好的适应性和可扩展性。
在设计过程中,需要系统提供的数据信息有:
U零件信息存放零件的基本信息,如零件图号、零件名称、材料牌号、部件编号、件数、毛坯类型和设计者等等。
工艺路线号、产品编号、
2)工艺信息存放工序的基本内容,如工艺路线号、工序代号、工序名称、工序描述、切削参数、工时和设备、工装等信息。
3)工步信息工步是对工序的更为详细的描述,包括工步代号、工步内容、工艺路线号切削参数、工时和设备、工装等信息。