毕业设计数控车床四工位回转刀架机电系统设计.docx
《毕业设计数控车床四工位回转刀架机电系统设计.docx》由会员分享,可在线阅读,更多相关《毕业设计数控车床四工位回转刀架机电系统设计.docx(19页珍藏版)》请在冰豆网上搜索。
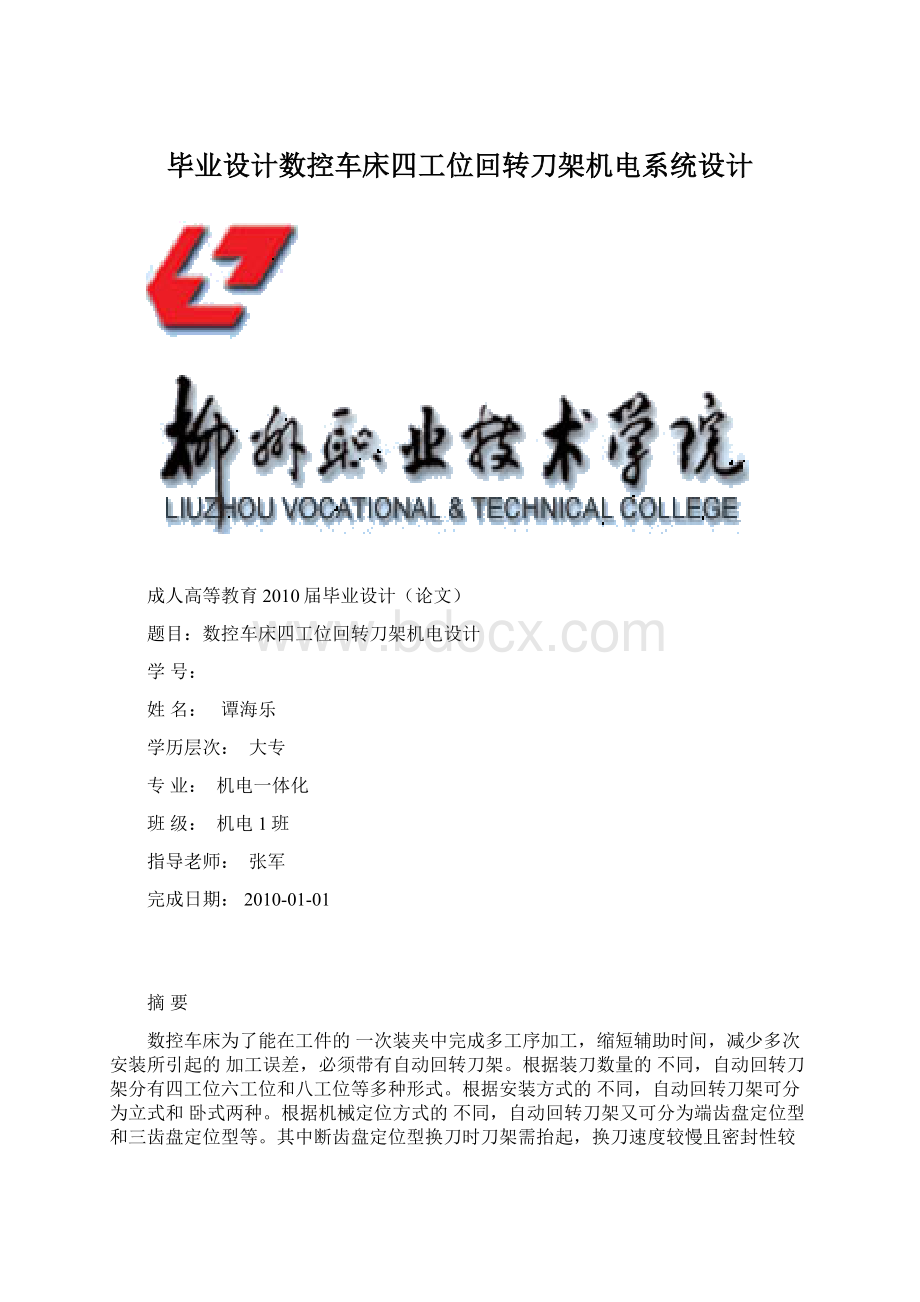
毕业设计数控车床四工位回转刀架机电系统设计
成人高等教育2010届毕业设计(论文)
题目:
数控车床四工位回转刀架机电设计
学号:
姓名:
谭海乐
学历层次:
大专
专业:
机电一体化
班级:
机电1班
指导老师:
张军
完成日期:
2010-01-01
摘要
数控车床为了能在工件的一次装夹中完成多工序加工,缩短辅助时间,减少多次安装所引起的加工误差,必须带有自动回转刀架。
根据装刀数量的不同,自动回转刀架分有四工位六工位和八工位等多种形式。
根据安装方式的不同,自动回转刀架可分为立式和卧式两种。
根据机械定位方式的不同,自动回转刀架又可分为端齿盘定位型和三齿盘定位型等。
其中断齿盘定位型换刀时刀架需抬起,换刀速度较慢且密封性较差,但其结构较简单。
三齿盘定位型又叫免抬型,其特点是换刀时刀架不抬起,因此换刀时速度快且密封性好,但其结构较复杂。
自动回转刀架在结构上必须具有良好的强度和刚性,以承受粗加工时的切削抗力。
为了保证转位具有高的重复定位精度,自动回转刀架还要选择可靠的定位方案和合理的定位结构。
自动回转刀架自动换刀时由控制系统和驱动电路来实现。
关键词:
自动回转刀架,蜗轮蜗杆副,机电系统
Abstract
CNClatheworkordertobeabletocompleteafixtureinmanyprocessesprocessingaidstoreducetime,reduceinstallationtimeandagaincausedbyprocessingerrors,wemustturnwithautomatictool.Installedinaccordancewiththenumberofdifferentknives,automaticrevolvingturretatpositionfourofsixandeight-stationworkspacesandotherforms.Accordingtothedifferentinstallationmethods,automaticrotarytoolcanbedividedintotwotypesofverticalandhorizontal.Positioningmeansaccordingtothedifferentmechanical,automaticrotarytoolsetcanbedividedintoclientpositioningtoothandthreeteeth,suchasdisk-basedpositioning.Theinterruptionoftoothplate-typetoolchangepositiontobeliftedwhenthetoolcarrier,toolchangeaslowandpoorsealing,butitsrelativelysimplestructure.Tridentateknowndisk-basedlocation-freelift-type,characterizedbyATCwhenthetoolisnotlifted,sowhenthetoolchangeisfastandgoodseal,butitsmorecomplicate
structure.
Automaticrotarytoolinthestructuremusthavegoodstrengthandrigiditytobeartheroughatthetimeofcuttingresistance.Inordertoensureahightranspositionoftherepeatpositioningaccuracy,automaticrotarytoolholderofthepositionwouldalsoliketochooseareliableandreasonablepositioningprogramstructure.RotaryToolAutomaticToolChangerautomaticallybythecontrolsystemandthedrivecircuittoachieve.
Keywords:
automaticrotarytool,viceworm,Electromechanicalsystem
目录
第1章绪论2
1.1课题综述2
1.1.1科学意义和应用前景2
1.1.2设计思路3
第2章总体结构设计4
1.1减速传动机构的设计4
1.2上刀体锁紧与精定位机构的设计4
1.3刀架抬起机构的设计4
第3章自动回转刀架的工作原理5
第4章主要传动部件的设计计算8
1.1蜗杆副的设计计算8
1.2螺杆的设计计算12
第5章电气控制部分设计13
1.1硬件电路设计13
1.2控制软件设计15
致谢17
参考文献18
数控车床四工位回转刀架机电系统设计
第一章
第1节绪论
1.1综述
1.1.1科学意义和应用前景
自动换刀系统是数控机床的重要组成部分。
刀具夹持元件的结构特性及它与机床主轴的联结方式,将直接影响机床的加工性能。
刀库结构形式及刀具交换装置的工作方式,则会影响机床的换刀效率。
自动换刀系统本身及相关结构的复杂程度,又会对整机的成本造价产生直接影响。
从换刀系统发展的历史来看,1956年日本富士通研究成功数控转塔式冲床,美国IBM公司同期也研制成功了“APT”(刀具程序控制装置)。
1958年美国K&T公司研制出带ATC(自动刀具交换装置)的加工中心。
1967年出现了FMS(柔性制造系统)。
1978年以后,加工中心迅速发展,带有ATC装置,可实现多种工序加工的机床,步入了机床发展的黄金时代。
1983年国际标准化组织制定了数控刀具锥柄的国际标准,自动换刀系统便形成了统一的结构模式。
目前国内外数控机床自动换刀系统中,刀具、辅具多采用锥柄结构,刀柄与机床主轴的联结、刀具的夹紧放松机构及驱动方式几乎都采用同一种结构模式。
在这种模式中,机床主轴常采用空心的带有长拉杆、碟形弹簧组的结构形式,由液压或气动装置提供动力,实现夹紧放松刀柄的动作。
利用这种机构夹持刀具进行数控加工的最大问题是,它不能同时获得高的夹持刚度和刀具振摆精度,而且主轴结构复杂,主轴轴向尺寸过大,加上它的液压驱动装置及刀具辅具锥柄的制造成本,使得自动换刀系统的造价在机床整机中占有较大的比重。
据有关资料介绍,在刀具采用锥柄夹头、侧压夹头以及弹簧夹头夹紧性能的对比实验中,采用弹簧夹头夹持刀具是唯一可同时获得高的夹持刚度和振摆精度的理想元件。
采用这种夹持元件,刀具或刀具辅具可作成圆柱柄,其制造成本低,精度易保证,这对大容量刀库降低刀具辅具的制造成本,意义更为显著。
在现代数控机床上亦有采用弹簧夹头作为刀具的夹持元件,但机床的主轴结构、驱动方式仍然采用与上述锥柄刀具完全相同的结构形式。
采用这种结构模式,在实际数控加工中,尤其是在需要超高速主轴、主轴的径向、轴向尺寸都很小、没有足够的换刀空间的微细加工场合中实现自动换刀将会是很困难的,如果实施自动换刀那将使机床成本大幅度提高。
如在CNC控制磨削球面铣刀的数控磨削机床上,直接由高速电机驱动主轴,使用小直径盘形砂轮和指形砂轮加工球面铣刀,换刀空间很小,在这种条件下,将难以实现自动换刀。
国外最新研制的内圆磨床上采用的弹簧夹头自动换刀装置售价昂贵。
随着机械加工业的发展,制造行业对于带有自动换刀系统的高效高性能加工中心的需求量越来越大。
在现有的各种类型的加工中心中,传统结构的自动换刀系统的造价在机床整机造价中总是占着很大比重,这是加工中心价格居高不下、应用不普遍的重要原因。
如果把自动换刀系统的设计制造从现有加工中心的制造模式中分离出来,把它作为加工中心的标准件或附件组织专门化的生产,同时由于该项技术的应用简化了机床主轴结构、采用弹簧夹头和外驱动机械手等关键技术、采用圆柱柄刀具和辅具,这不仅使数控机床工作性能有所提高,而且使得由它配套构成的加工中心的总体造价大幅度下降。
低造价高性能的加工中心将会被中小厂广泛接收,这样必将给自动换刀系统生产厂商和加工中心制造厂商带来巨大的经济效益
数控标准是制造业信息化发展的一种趋势。
数控技术诞生后的50年间的信息交换都是基于ISO6983标准,即采用G,M代码描述如何(how)加工,其本质特征是面向加工过程,显然,他已越来越不能满足现代数控技术高速发展的需要。
为此,国际上正在研究和制定一种新的CNC系统标准ISO14649(STEP-NC),其目的是提供一种不依赖于具体系统的中性机制,能够描述产品整个生命周期内的统一数据模型,从而实现整个制造过程,乃至各个工业领域产品信息的标准化。
STEP-NC的出现可能是数控技术领域的一次革命,对于数控技术的发展乃至整个制造业,将产生深远的影响。
首先,STEP-NC提出一种崭新的制造理念,传统的制造理念中,NC加工程序都集中在单个计算机上。
而在新标准下,NC程序可以分散在互联网上,这正是数控技术开放式、网络化发展的方向。
其次,STEP-NC数控系统还可大大减少加工图纸(约75%)、加工程序编制时间(约35%)和加工时间(约50%)。
目前,欧美国家非常重视STEP-NC的研究,欧洲发起了STEP-NC的IMS计划(1999.1.1~2001.12.31)。
参加这项计划的有来自欧洲和日本的20个CAD/CAM/CAPP/CNC用户、厂商和学术机构。
美国的STEPTools公司是全球范围内制造业数据交换软件的开发者,他已经开发了用作数控机床加工信息交换的超级模型(SuperModel),其目标是用统一的规范描述所有加工过程。
目前这种新的数据交换格式已经在配备了SIEMENS、FIDIA以及欧洲OSACA-NC数控系统的原型样机上进行了验证。
1.1.2设计思路
本设计采用三相异步交流电机驱动,控制部分设计主要采用plc控制包括收信和发信电路两部分。
设计好自动回转刀架的机械结构和电器控制电路后,就可以编制刀架自动转位的控制软件。
通过此次设计,不仅是对四年学习生活的一个总结,更是对今后继续学习的一次锻炼。
在学习了四年的基础课、专业课之后,通过这次课题的考验,除了要求掌握好本专业的课程外,还要求对本专业相关的知识有足够的认识。
这次设计就要用到机械设计相关知识,不仅是对自己的一次考验,更是对自己所学知识的一个补充。
逐步锻炼自己独立完成工作的能力,以适应今后真正的考验。
第二章
第1节总体结构设计
1.1减速传动机构的设计
普通的三相异步电动机因转速太快,不能直接驱动刀架进行换刀,必须经过适当的减速。
根据立式转位刀架的结构特点,采用蜗杆副减速是最佳选择。
蜗杆副传动可以改变运动的方向,获得较大的传动比,保证传动精度和平稳性,并且具有自锁功能,还可以实现整个装置的小型化。
1.2上刀体锁紧与精定位机构的设计
由于刀具直接安装在上刀体上,所以上刀体要承受全部的切削力,其锁紧与定位的精度将直接影响工件的加工精度。
本设计上刀体的锁紧与定位机构选用端面齿盘,将上刀体和下刀体的配合面加工成梯形端面齿。
当刀架处于锁紧状态时,上下端面齿相互咬合,这时上刀体不能绕刀架的中心轴转动;换刀时电动机正传,抬起机构使上刀体抬起,等上下端面齿脱开后,上刀体才可以绕刀架中心轴转动,完成转位动作。
1.3刀架抬起机构的设计
要想使上,下刀体的两个端面齿脱离,就必须设计合适的机构使上刀体抬起。
本设计选用螺杆-螺母副,在上刀体内部加工出内螺纹,当电动机通过蜗杆-蜗轮带动蜗杆绕中心轴转动时,作为螺母的上刀体要么转动,要么上下移动。
当刀架处于锁紧状态时,上刀体与下刀体的端面齿相互咬合,因为这时上刀体不能与螺杆一起转动,所以螺杆的转动会使上刀体向上移动。
当端面齿脱离咬合时,上刀体就与螺杆一同转动。
设计螺杆时要求选择适当的螺距,以便当螺杆转动一定角度时,使得上刀体与下刀体的端面齿能够完全脱离咬合状态。
传动结构见总装配图。
第三章
第1节自动回转刀架的工作原理
自动回转刀架的换刀流程图如下图1所示
图2表示自动回转刀架在换刀过程中有关销的位置。
其中上部的圆柱销2和下部的反靠销6起着重要的作用。
当刀架处于锁紧状态时,两销的情况如图a所示,此时反靠销6落在反靠圆盘7的十字槽内,上刀体4的端面齿和下刀体的端面齿处于咬合状态
需要换刀时,控制系统发出刀架转位信号,三相异步电动机正向旋转,通过蜗杆副带动螺杆正向转动,与蜗杆配合的上刀体4逐渐抬起,上刀体4与下刀体之间的端面齿慢慢脱开;于此同时,上盖圆盘1也随着螺杆正向转动(上盖圆盘1通过圆柱销与螺杆连接)当转过约170时,上盖圆盘1直槽的另一端转到圆柱销2的正上方,由于弹簧3的作用,圆柱销2落入直槽内,于是上盖圆盘1就通过圆柱销2使得上刀体4转动起来(此时端面齿已经完全脱开)如图b所示
上盖圆盘1,圆柱销2以及上刀体4在正转的过程中,反靠销6能够从反靠圆盘7中十字槽的左侧斜坡滑出,而不影响上刀体4寻找刀位时的正向转动,如图c所示
上刀体4带动磁铁转到需要的刀位时,发信盘上对应的霍尔元件输出低电平信号,控制系统收到后,立即控制刀架电动机反转,上盖圆盘1通过圆柱销2带动上上刀体4开始反转,反靠销6马上就会落入反靠圆盘7的十字槽内,至此。
完成粗定位,如图d所示。
此时,反靠销6从反靠圆盘7的十字槽内爬不上来,于是上刀体4停止转动,开始下降,而上盖圆盘1继续反转,其直槽的左侧斜坡将圆柱销2的头部压入上刀体4的销孔内,之后,上盖圆盘1的下表面开始与圆柱销2的头部滑动。
在此期间,上,下刀体的端面齿逐渐咬合,实现精定位。
当蜗杆转动产生轴向位移,压缩弹簧,套筒的外圆压缩开关使刀架电动机停转,整个换刀过程结束。
由于蜗杆副有自锁功能,所以刀架可以稳定的工作。
图1自动换刀流程
ab
cd
图2刀架转位过程中销的位置
a)换刀开始时,圆柱销2与上盖圆盘1可以相对滑动。
b)上刀体4完全抬起后,圆柱销2落入上盖圆盘1的槽内,上盖圆盘1将带动圆柱销2及上刀体一起转动。
c)上刀体4连续转动时,反靠销6可以从反靠圆盘7的槽左侧斜坡滑出。
d)找到刀位时,刀架电动机反转反靠销6反靠,上刀体停转,实现粗定位。
1.上盖圆盘2.圆柱销3.弹簧4.上刀体5.圆柱销6.反靠销
7.反靠圆盘
第四章
第1节主要传动部件的设计计算
1.1蜗杆副的设计计算
自动回转刀架的动力源时三相异步电动机,其中蜗杆与电动机直连,刀架转位时涡轮与上刀体直连。
已知电动机额定功率P1=90W,额定转速n1=1440r/min,上刀体设计转速n2=30r/min,则蜗杆副的传动比i=n1/n2 =1440/30=48.刀架从转位刀锁紧时,需要蜗杆反向,工作载荷不均匀,启动时冲击较大,今要求蜗杆副的使用寿命Lh=10000h。
1.1.1 蜗杆的选型
GB/T10085----1988推荐采用渐开线蜗杆(Z1蜗杆)和锥面包络蜗杆(ZK蜗杆)。
本设计采用结构简单,制造方便的渐开线型圆柱蜗杆(Z1型)。
1.1.2蜗杆副的材料
刀架中的蜗杆副传递的功率不大,但蜗杆转速较高,因此蜗杆的材料选择45钢,其螺旋齿面要求淬火,硬度为45~55HRC,以提高表面耐磨性;涡轮的转速较低,其材料主要考虑耐磨性,选用铸锡磷青铜ZcuSn10P1,采用金属模铸造。
1.1.3按齿面接触疲劳强度进行设计
刀架中的蜗杆副采用闭式传动,多因齿面胶合或点蚀而失效。
因此,在进行承载能力计算时,先按齿面接触疲劳强度进行设计,再按齿根弯曲疲劳强度进行校核。
按涡轮接触疲劳强度条件设计计算的公式为:
a≥
式中 a-------蜗杆副的传动中心距,单位为mm;
K-------载荷系数;
T2-------作用在涡轮上的转矩T,单位N.mm;
ZE-------弹性影响系数,单位为MPa;
Z--------接触系数
【
】----许用接触应力,单位为MPa;
从式中算出蜗杆副的中心距a之后,根据已知的传动比i=48,可以选择合适的中心距a值,以及相应的蜗杆,涡轮参数。
1)确定作用在蜗轮上的转矩T
设蜗杆头数z1=1,蜗杆副的传动效率取=0.8。
由电动机的额定功率P1=90W,可以算出涡轮传递的功率P2=P1,再由涡轮的转速n2=30r/min,求得作用在涡轮上的转矩:
T2=9.55P2/n2=9.55P1/n2=22920N.mm
2)确定载荷系数K
载荷系数K=KAKBKV.其中KA为使用系数,由于工作载荷分布步均匀,启动时冲击较大,因此取KA=1.15;K为齿向载荷分布系数,因工作载荷在启动和停止时有变化,故取KB=1.15;KV为动载系数,由于转速不高,冲击不大,可取KV=1.05,则载荷系数
K=KAKBKV=1.39
表1使用系数KA
工作类型
Ⅰ
Ⅱ
Ⅲ
载荷性质
均匀,无冲击
不均匀,小无冲击
不均匀,大无冲击
每小时起动次数
<25
25-50
>50
起动载荷
小
较大
大
KA
1
1.15
1.2
3)确定弹性影响系数ZE
铸锡磷青铜涡轮与钢蜗杆相配时,从参考文献中差得弹性影响系数ZE=160MPa
4)确定接触系数Zp
先假设蜗杆分度圆直径d1和传动中心距a的比值d1/a=0.35,可得系数ZP=2.9
5)确定许用接触力【
】
根据涡轮材料为铸锡磷青铜ZCuSn10P1,金属模铸造,蜗杆螺旋齿面硬度大于45HRC,涡轮的基本许用力【
】=268MPa,已知蜗杆为单头,涡轮每转一转时每个轮齿咬合的次数j=1;涡轮转速n=30r/min;蜗杆副的使用寿命L=10000h。
则应力循环次数
N=60jn2Lh=60×1×30×10000=1.8×107
寿命系数:
KHN=
=0.929
表2铸锡磷青铜蜗轮的基本许用接触应力
蜗轮材料
铸造方法
蜗杆螺旋面的硬度
≤45HRC
>45HRC
铸锡磷青铜ZCuSn10P
砂模铸造
150
180
金属模铸造
220
268
铸锡锌铅青铜ZcuSn5Pb5Zn5
砂模铸造
113
135
金属模铸造
128
140
许用接触应力:
【
】=KHN【
】=0.929×268Mpa≈249Mpa
6)计算中心距a≥
将以上各参数代入式 ,求得中心距:
a≈48mm
取中心距a=50mm,已知蜗杆头数z1=1,设模数m=1.6mm,得直径d1=20mm,这时d1/a=0.4,可得接触系数Z’p=2.74。
因为Z’p1.1.4蜗杆和涡轮的主要计算参数和几何尺寸
由蜗杆和涡轮的基本尺寸和主要参数,算得蜗杆和涡轮的主要几何尺寸后,即可绘制蜗杆副的工作图了。
1)蜗杆参数及尺寸
头数z1=1,模数m=1.6mm,轴向齿距Pa=3.14×m=5.027mm,轴向齿厚sa=0.5m=2.514mm,分度圆直径d1=20mm,直径系数q=d1/m=12.5,分度圆导程脚r=Y=arctan(z1/q)=4°34ˊ26ˊˊ.取齿顶高系数ha=1,径向间隙系数c=0.2,则齿顶圆直径da1=d1+2ha×m=20mm+2×1×1.6mm=23.2mm,根圆直径df1=d1-2m(ha+c)=d1-2m(ha+c)=[20-2×1.6×(1+0.2)]mm=16.16mm
2)蜗轮参数与尺寸
齿数z2=48,模数m=1.6mm,分度圆直径为d2=mz2=1.6×48mm=76.8mm,变位系数x=[a-(d1+d2)/2]/m=[50-(20+76.8)/2]/1.6=1,蜗轮喉圆直径为da2=d2+2m(ha+x2)=83.2mm,涡轮齿根圆直径df2=d2-2m(ha-x2+c)=76.16mm
(5)校核蜗轮齿根弯曲疲劳强度,即校验下式是否成立:
≤[
]
式中
........涡轮齿根弯曲应力,单位为Mpa;
Yfa2 ..........涡轮齿形系数;
YB .........螺旋角影响系数
[
] .........涡轮的许用弯曲应力,单位为MPa
由蜗杆头数Z1=1,传动比i=48,可以算出涡轮齿数Z2=iz1=48
则涡轮的当量齿数:
ZV2=Z2/cos3r=48.46
根据涡轮变位系数x2=1和当量齿数ZV2=48.46,得齿形系数
Yfa2=1.95
旋转角影响系数;
YB=1-r/140°=0.967
根据涡轮的材料和制造方法,可得涡轮基本许用弯曲应力:
[
]‘=56MPa
涡轮的寿命系数:
KF=
=1.725
涡轮的许用弯曲应力:
[
]=40.6Mpa
将以上参数带入上式中,得涡轮齿根弯曲应力:
=37.4
可见,
< [
],涡轮齿根的弯曲强度满足要求。
表3蜗轮的基本许用弯曲应力
(单位:
Mpa)
蜗轮材料
铸造方法
单侧工作
双侧工作
铸锡青铜ZCuSn10P
砂模铸造
40
29
金属模铸造
56
40
铸锡锌铅青铜ZcuSn5Pb5Zn5
砂模铸造
26
22
金属模铸造
32
26
铸铝铁青铜ZcuAl10Fe3
砂模铸造
80
57
金属模铸造
90
64
HT150
砂模铸造
40
28
HT200
砂模铸造
48
34
1.2螺杆的设计计算
1.2.1螺距的确定
刀架转位时,要求蜗杆在转到约170°的情况下,上刀体的断面齿与下刀体的断面齿完全脱离;在锁紧的时候,要求上下端面齿的咬合深度达2mm.因此,螺杆的螺距P应满足P×170/360>2mm,即P>4.