12m客车车架结构设计及分析.docx
《12m客车车架结构设计及分析.docx》由会员分享,可在线阅读,更多相关《12m客车车架结构设计及分析.docx(17页珍藏版)》请在冰豆网上搜索。
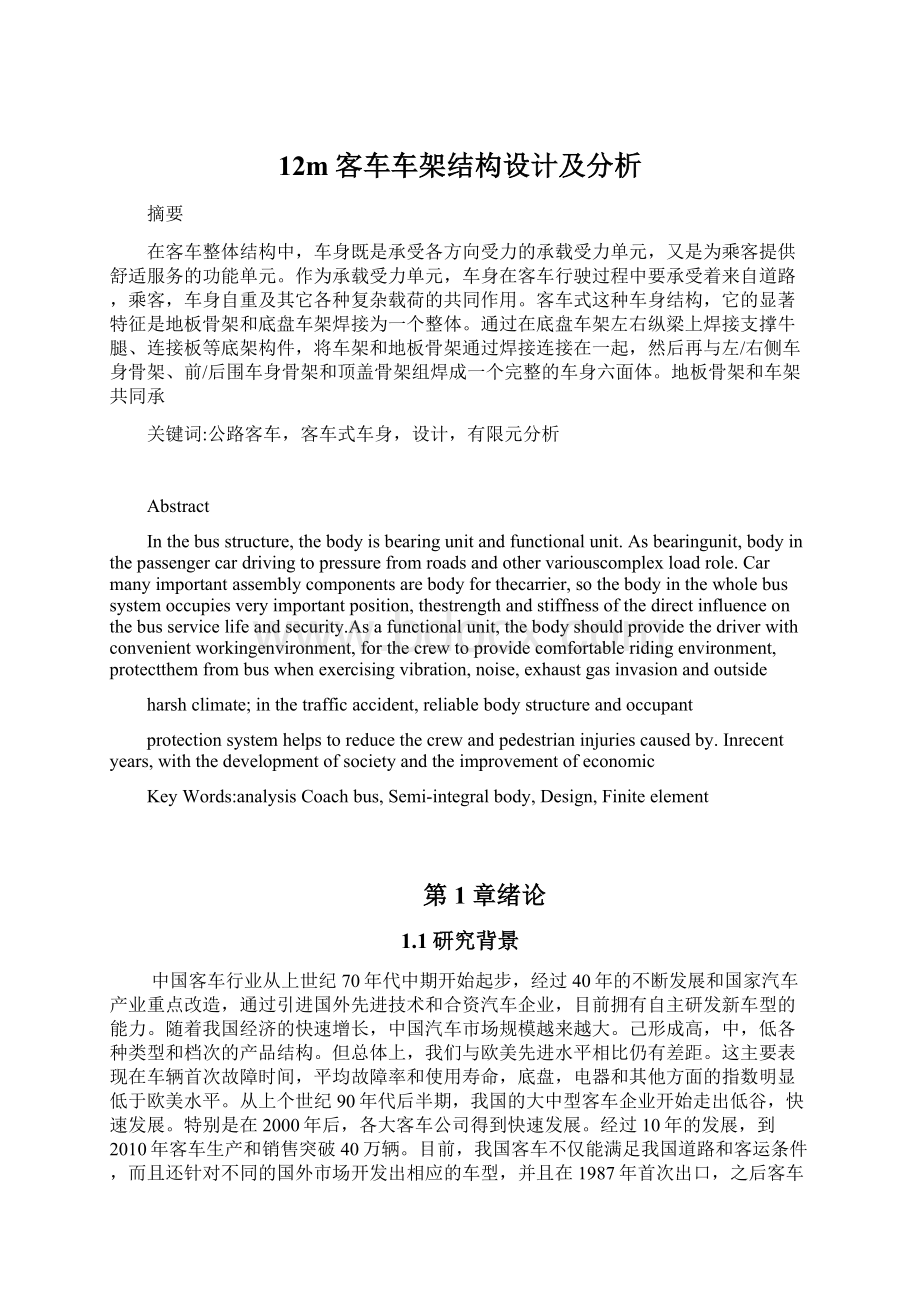
12m客车车架结构设计及分析
摘要
在客车整体结构中,车身既是承受各方向受力的承载受力单元,又是为乘客提供舒适服务的功能单元。
作为承载受力单元,车身在客车行驶过程中要承受着来自道路,乘客,车身自重及其它各种复杂载荷的共同作用。
客车式这种车身结构,它的显著特征是地板骨架和底盘车架焊接为一个整体。
通过在底盘车架左右纵梁上焊接支撑牛腿、连接板等底架构件,将车架和地板骨架通过焊接连接在一起,然后再与左/右侧车身骨架、前/后围车身骨架和顶盖骨架组焊成一个完整的车身六面体。
地板骨架和车架共同承
关键词:
公路客车,客车式车身,设计,有限元分析
Abstract
Inthebusstructure,thebodyisbearingunitandfunctionalunit.Asbearingunit,bodyinthepassengercardrivingtopressurefromroadsandothervariouscomplexloadrole.Carmanyimportantassemblycomponentsarebodyforthecarrier,sothebodyinthewholebussystemoccupiesveryimportantposition,thestrengthandstiffnessofthedirectinfluenceonthebusservicelifeandsecurity.Asafunctionalunit,thebodyshouldprovidethedriverwithconvenientworkingenvironment,forthecrewtoprovidecomfortableridingenvironment,protectthemfrombuswhenexercisingvibration,noise,exhaustgasinvasionandoutside
harshclimate;inthetrafficaccident,reliablebodystructureandoccupant
protectionsystemhelpstoreducethecrewandpedestrianinjuriescausedby.Inrecentyears,withthedevelopmentofsocietyandtheimprovementofeconomic
KeyWords:
analysisCoachbus,Semi-integralbody,Design,Finiteelement
第1章绪论
1.1研究背景
中国客车行业从上世纪70年代中期开始起步,经过40年的不断发展和国家汽车产业重点改造,通过引进国外先进技术和合资汽车企业,目前拥有自主研发新车型的能力。
随着我国经济的快速增长,中国汽车市场规模越来越大。
己形成高,中,低各种类型和档次的产品结构。
但总体上,我们与欧美先进水平相比仍有差距。
这主要表现在车辆首次故障时间,平均故障率和使用寿命,底盘,电器和其他方面的指数明显低于欧美水平。
从上个世纪90年代后半期,我国的大中型客车企业开始走出低谷,快速发展。
特别是在2000年后,各大客车公司得到快速发展。
经过10年的发展,到2010年客车生产和销售突破40万辆。
目前,我国客车不仅能满足我国道路和客运条件,而且还针对不同的国外市场开发出相应的车型,并且在1987年首次出口,之后客车出口不断增加,到2003我国国内客车实现批量出口。
但此时出口行为仍然只有少数个体企业和小批量的行为。
从2004到2005的出口市场似乎正在积蓄能量,从2006开始,我国客车出口显示完整的爆炸性增长,从2006至2007年客车出口总量保持2位数增长。
出口金额超过2004年近10倍,单车出口价格也实现了
翻番。
在2008和2009年客车市场因全球宏观经济的影响有所下滑,但出口市场的绝对数量的影响比较小。
2008全球金融危机后,随着国外稳定的高端客户不断增加,产品附加值的不断增加,中国客车出口己经进入了良陛发展的轨道。
2010年,中国客车出口的20194辆,出口金额达到187959.4万元。
如今,我国国产客车的档次、配置水平不断提高,很多客车上采用了许多轿车上的技术。
例如在动力总成方面采用大功率低排放发动机
1.2研究意义
研究中所取得的数据为我厂以后车辆的设计提供了理论依据,对我公司以后产品的开发有很大的帮助作用。
研究中所使用的设计方法和模型简化方法可为客车企业的现代化设计的规范化提供一定的参考,对提高我国国产客车的设计水平、缩短开发周期和节约设计成本具有积极的意义。
本课题研究所取得的成果己经被我厂采用,对我厂提高产品的设计水平,降低成本,增强市场竞争力起到了很好的促进作用。
1.3UG技术的发展概况
UG技术即计算机辅助设计,是使用计算机和图形设备帮助设计师工作。
现在,国内大型制造型企业己普遍实施了UG系统,取代手工作业,一些大型汽车企业的UG应用水平也接近国际先进水平。
但由于我国UG软件自主研发术水平与发达国家之间存在巨大的差距,国内一些研究机构和公司推出的UG系列软件得不到更广泛的应用,市场占有率低,尤其在UG系统集成方面还是刚刚起步。
随着我国市场化程度的加深,市场竞争的加剧,迫使汽车企业必须改变传统的设计、制造、管理、销售模式,来提升企业竞争力和市场应变能力。
可以说,实施UG系统是最有效的方式之一。
我国从上世纪70年代开始研究推广计算机辅助设计技术,并取得了良好的经济效益。
UG技术在车身开发中的应用,使原来的旧模式有了彻底的改
观。
设计人员通过与UG系统的交互,将自己脑中的概念模式转化为清晰的视觉模式—几何实体,易于优化和改进,提高了工作效率和设计质量。
1.4客车车身技术的研究现状
大型客车按车身承载形式不同分类共有三种:
一种是非承载式车身,第二种是本课题研究的客车车身,第三种是全承载车身。
全承载式车身的主要问题是:
由于底架是由很多直线小型矩形管构成格栅式结构,工艺复杂,工装投入大,企业的生产工艺必须作重大调整,生产过程焊接工作量巨大,生产效率低,增加成本,较适用于豪华大客车。
欧洲大型客车档次高,生产批量很小,售价昂贵,此种析架式全承载车身对他们来说是比较合适的,而现阶段在国内却很难普及推广。
在客车行业发展初期,客车生产厂家将客车车身用紧固螺栓通过非金属垫板和货车底盘连接在一起,这种车身结构称为非承载式结构。
这种非承载式结构的好处是可以在同一个底盘上面安装不同的客车车身,但此种结构没能很好的利用客车车身骨架的承载作用,因此这种形式的客车整备质量比较较大,油耗也比较高。
为了客车车身的轻量化设计,并兼顾客车车身与底盘
的匹配,我们将底盘车架横梁加宽并与客车车身侧围骨架焊接在一起,使底盘和车身骨架组合成一个完整的整体,车身骨架也承担一部分车辆载荷,此种结构称为客车式结构。
现阶段,我国绝大部分客车为此种客车式结构。
但这种客车式结构仍保留了重量比较大的底盘车架,这使车辆轻量化设计受到了很大限制。
为了进一步减轻客车车身自重以及使车身结构更合理,我们可改用重量较小,而刚度却比较大的全承载式客车车身来取代笨重的车架。
这种车架具有两贯通式纵梁和一些与客车车身等宽的横梁,这与车身骨架形成一个刚性的空间全承载系统。
从而使客车车身的各部件都参与承载,使各部件承载时相互关联、协调。
这能充分发挥材料的最大强度,使整车车身重
量比较小而刚度、强度比较大。
1.5本论文的研究内容及目标
1、进行客车式车身的总体方案设计。
2,应用UG三维软件对此款车身骨架进行三维建模。
3、按照总布置方案,建立前后桥轴荷受力模型,进行此款车辆的前后桥轴荷分配的计算。
并对此款客车式车身在理论上进行受力分析和强度校核。
4、对此款车身骨架进行有限元分析。
5、对此款样车进行各项性能试验,通过检验证明了此款样车满足了我国相关的国家标准。
通过这一课题的研究,我们利用客车式车身技术构建了一种12米客车车身,并对车此身进行有限元分析。
通过理论计算分析此车身是否满足强
度刚度要求。
并通过试验检验此款客车式客车车身的可靠性。
第2章车身的总体设计
2.1车身的总体设计方案
本车型车身的设计方案为:
一种三段式底架的长途大客车客车车身。
他包括:
底架、地板骨架、左侧骨架、右侧骨架、前围骨架、后围骨架和顶盖骨架七部分组成此款客车式车身的骨架结构如下:
底架和地板骨架,前后围骨架,左右侧骨架及顶骨架形成一个整体承载载荷的框架。
通过各个连结点,整车骨架形成若干个封闭环结构「“一」。
车身骨架结构布置图见图2.lo
图2.1车身骨架结构布置方案
2.2车辆布置形式
本车型的布置形式如下表2.1所示:
表2.1车型布置形式
2.3车身主要尺寸的确定
1、车身长度
本车型是一款12米级长度车型,考虑到制造误差,整车完成后长度不大
于12米,此车车身长度设计为12000mmo
2、轴距、前悬和后悬
根据本车型轴荷分配的要求,以及《GB7258-2004机动车运行安全技术条件》的规定,确定本车型轴距为6100mm。
根据法规要求及本车运行环境所需的接近角和离去角以及前后轴荷分配的要求,确定本车型的前悬为1940mm,后悬为2755mm。
3、车高、车宽和前后轮轮距
根据《GB1589-2004道路外廓尺寸、轴荷及质量限值》(客车最高不超过3200mm最宽不超过2500mm,并考虑到车身外形的协调美观;车辆总高设计为2500mm。
车辆总宽设计为2520mm(确定车宽时,应在满足法规要求的前提下,尽量加大,从而使座椅在满足宽度440~的情况下,有足够的过道宽度。
还应考虑到制造误差,使车辆制作出来后车宽不大于法规要求。
)。
此车型的车身主要尺寸见下表2.20
2.4车辆质量参数的确定
车辆质量参数确定时首先要考虑能满足国家法规要求,因法规要求比较低容易满足。
车辆质量参数确定时还要参考其他厂家同类产品质量参数以及本厂其他相同长度车型。
为了满足载客量,同时又要降低燃油消耗量,所以车辆的最大总质量尽量加大,但车辆自重尽量减小。
1、车辆的总质量Ma和前后桥的选择
根据此车乘客区长度尺寸可以计算出此车最大载客量为39人(具体计算方法见后面章节)。
乘客每人按65千克计算,乘客重量为65X39=2535千克。
车辆整备质量的估算:
根据底盘上自制件以及所选各总成件和电器件等所有部件质量的总和约为4000千克;综合考虑我厂的工艺保障能力及技术突破水平,车身部分的总质量可控制在4550千克内;可以确定车辆整备质量Mo=8550千克。
2535千克+8550千克=11085千克
根据以上计算进行前后桥的选择。
前桥:
选用东风4.2T车桥,其型号为30JS20E-00005,其理论承载重量为4200千克,因此可以确定此车前桥的承载能力为MI}4200千克,我们取3800千克。
后桥:
选用东风8T后桥,其型号为24BRS15M-00005,其理论承载重量为8000千克,我们取7800千克。
由以上可以得出此车辆最大总质量11600千克。
2、轮胎的选择
根据车辆最大总质量以及所选的车桥,我们选用佳通9822.5轮胎,此轮胎理论承载能力单胎时每胎为2240千克,双胎时每胎为2120千克。
此车轮胎总的承载能力为12960千克。
综合以上所述,此款车辆最大总质量确定为Ma=11600千克。
2.5车辆主要性能参数的确定
1、动力性能参数见下表2.3
2、燃油经济性参数
等速90km/h百公里油耗毛18L/100km;
3、制动性能参数见下表2.4
表2.4制动性能参数
4,最小转弯直径Dmin
本车最小转弯直径Dmin-14米。
5、通过性参数
此车最小离地间隙在后桥中间位置处,最小离地间隙为
现在大部分客车接近角在8}-13。
之间,离去角在7~140
220mm。
第3章客车车身UG建模
UG是法国达索公司大型高端计算机辅助设计/制造/工程集成应用软件,在全球计算机辅助设计/制造/工程领导。
随着产品生命周期管理(产品生命周期管理)协作解决方案,是一个非常重要的组成部分,它可以帮助制造商设计自己的新产品,它可以支持从生产项目的早期阶段,具体的设计,分析,仿真,组件保持在所有的工业设计过程。
UG是汽车工业的事实标准,
在欧洲,亚洲和北美国最大汽车制造商的核心设计系统。
在造型,车身和发动机设计具有独特的优势,适合各种车辆设计和制造提供了一个端到端解决方案。
3.1客车式长途客车车身底架建模
本车型底架建模共分为三个设计单元即:
C1)前段底架总成;C2}中段底架总成(行李舱区,析架结构);C3)
后段底架总成具体布置见下图3.lo
这种三段式底架的前段为槽形的两大梁,中间部分为析架结构(此处为行李舱区),后段也为槽形的两大梁,因后端安装发动机,载荷较大,所以此处大梁断面比前段大梁尺寸大。
根据客车车型和承载情况的不同,中间析架结构部分采用不同截面尺寸的型钢组焊成一个框架结构。
这个框架结构通过铆接或焊接同前后段大梁固定在一起。
如果是钢板弹簧悬架,中间析架部分一般不会超过悬架安装区域;但如果是气囊悬架,为了尽量增大行李舱容积,部分底盘的中间析架可能超出悬架安装区域。
只有驾驶员操纵区域和发动机
安装区域采用比较短的槽形大梁。
这种结构被普遍用于长途大客车和旅游客车。
国内引进和开发的豪华客车大部分都采用这种结构。
这种结构便于设计制造,并且增大了行李舱的容积,但这种结构前后段纵梁与中间析架的连接比较复杂,工艺难度比较大。
1、前段底架总成建模
前段底架的左右纵梁采用截面为190x70x6的槽形16Mn钢。
由于本车型采用前2后4空气悬架,因此前段底架总成设计不仅要考虑底架和前桥的装配关系,还要考虑此车转向机和两个前气囊的的安装。
前段底架第一横梁位置(底架前悬)由整车前悬尺寸,仪表台尺寸和转向管柱位置确定。
前段底架左右纵梁之间由三个横梁相连。
左右纵梁与三个横梁组成两个封闭方框。
第一横梁在前段底架最前端,为拖车横梁。
由于位置所限,此车型拖车横梁与左右纵梁的连接方式为用螺栓与左右纵梁上下翼面连接在一起。
这种连接方式可以增加左右纵梁的抗扭刚度,但同时也容易产生约束扭转集中应力,造成左右纵梁的上下翼面出现比较大集中应力。
但因此款车型为客车式车身,底架与车身骨架共同承受车身载荷,所以可以采用。
第二横梁和左右两
纵梁的下翼面和腹板同时连接在一起。
这种横梁与左右纵梁的连接方式同时具有刚性抗弯和柔性抗扭的这两种特点,是这种客车底架横梁和左右纵梁的所有连接方式中最好的一种。
横梁与左右纵梁连接时,横梁与左右纵梁的连接部分产生最大的应力,因此为了避免横梁两端局部区域产生很大的连接负荷应力,第二横梁两端与纵梁连接部分的断面尺寸很大,以增大连接区域减小连接负荷应力集中。
第三横梁与左右纵梁的连接方式与前面所讲第二横梁
相同。
因为此车为前2后4空气气囊悬架。
悬架处为高负荷区。
为增加此处纵梁强度,通过连接型钢将此处前段底架纵梁与中段底架纵梁连接起来,并在连接型钢外面增加加强钢板。
连接型钢和加强钢板与纵梁的连接方式为塞焊。
两纵梁的最后端为车辆仓体的前端。
底架前段模型见图3.20
2、中段底架建模
中段底架是用横截面为160x60x5的型钢作为两纵梁,用横截面70x40x3,40x40x3,40x30x3,40x40x2等型钢组焊成析架结构。
用以增加此析架结构的强度和刚度在矩形方框的各个角部位设计有加强角两纵梁的前端为车内乘客过道前端台阶处,两纵梁的后端为车内后排五人椅前台阶处。
中段底架具体布置见图3.30
3、后段底架总成建模
后段底架总成分为两部分:
一部分是后桥处底架,另一部分是发动机处底架。
后桥处底架左右纵梁采用横截面为180x70x6的槽形16Mn钢。
因为此车为前2后4空气气囊悬架。
悬架处为高负荷区。
为增加此处纵梁强度,通过连接型钢将此处前段底架纵梁与中段底架纵梁连接起来,并在连接型钢外面增加加强钢板。
后桥处第一横梁在空气悬架前方靠近空气悬架处,第二横梁在空气悬架后方靠近空气悬架处。
第一横梁,第二横梁与左右侧纵梁组成一个封闭的方框结构,增加了后桥处底架的强度。
本车型地板骨架建模分为
1、前悬地板骨架建模
前悬段地板骨架由40x40x2.0,40x40x3.0;40x30x1.5等截面的型钢焊接而成。
第一格栅与第二格栅前后位置由乘客门位置确定。
第一格栅与乘客门前立柱对齐并焊接在一起。
第二格栅与乘客门后立柱对齐并焊接在一起。
在第一格栅上有三根连接梁与前围骨架焊接在一起。
第二格栅与乘客门后立柱和司机窗后立柱及顶骨架上此处的横梁组成一个封闭环以增加客车整体强度。
此车装壁挂式导游椅。
因此需在乘客门后立面上预留导游椅固定板。
为了使导游椅不影响乘客上下车,我们在乘客门后立面上预留导游椅凹台,在凹台后立面上预留固定板,使导游椅安装后尽量不占用乘客过道。
第三格栅为驾驶区与乘客区分界处。
第三格栅前为驾驶区,第三格栅后为乘客区。
在左右侧乘客区前端分别焊接乘客隔栏固定板以固定隔栏。
前悬地板骨架建模见下图3.7。
2、中间地板骨架建模
中间地板骨架在前后两车桥之间,他由四个格栅和其他连接梁组成。
四个格栅分别是前桥后格栅,后桥前格栅以及中间两个行李仓的前桥后格栅的位置由轮胎到挡泥板的距离确定。
此格栅位置要求既要尽量向前靠用以增大行李仓容积又要保证车辆行驶时轮胎不与此格栅干涉。
基于以上两点要求,此格栅位置定在与前桥中心相距610mm处。
后桥前格栅的位置确定方法与前桥后格栅的位置确定方法一样。
因此后桥前格栅的位置定在与后桥中心相距610mm处。
中间行李仓前格栅位置的确定。
因此车油箱放在前轮后第一个仓中,因此中间行李仓前格栅位置只要保证此格栅前的空间能放开油箱即可。
中间行李仓后格栅位置的确定。
因此格栅前后都为行李仓,因此此格栅位置确定时,考虑此格栅前后两个行李仓门大小的统一性。
己利于车间工人的施
工。
中间两个格栅与底架上的格栅前后位置一致,形成封闭析架结构,此种结构既降低骨架重量,又能保证骨架强度。
在两格栅之间,上部用纵向小截面型钢连接,下部用小型钢组成的三角框连接,此框同时与底架连接在一起,这使车身整个下部骨架组成一个完整的空间框,增加了骨架的强度。
中间地
3、后段地板骨架建模
后段地板骨架建模时需注意骨架不与发动机干涉,注意预留变速箱和发动机检修口。
后段地板骨架建模见下图3.90
3.2左侧骨架总成建模
左侧骨架位于车身左侧,它由边窗立柱,两根贯通纵梁,仓门立柱和若干斜支撑以及连接型钢组焊而成。
左侧骨架厚度分为两部分,分界点为侧窗下60X40X2P异型材贯通纵梁。
此纵梁以下骨架厚度SOmm,此纵梁以上骨架厚度为40mm。
在侧窗下贯通纵梁下方,行李仓上部是一SOXSOX2P的异型材贯通纵梁,此贯通纵梁与地板骨架上格栅焊接在一起。
为了便于施工与采购,边窗中间三块玻璃尺寸大小一样。
同时为了骨架的良好承载性,边窗立柱与地板骨架在前后轮处的格栅位置尽量对齐以形成封闭环。
在边窗下纵梁
与行李仓上纵梁之间用立柱与斜撑连接两纵梁。
左侧骨架总成建模见下图3.10。
图3.11为左侧骨架和底架及地板骨架配合在一起时位置关系。
第四章车身结构有限元分析
4.1车身模型的简化
客车式客车的骨架主要是由矩形梁构成,另外还有一部分异形梁,槽钢梁和钢板等构成。
各个梁之间大多采用焊接的方式连接在一起。
在不影响应力和变形的条件下,在建模的过程中我们采取了一些简化措施
1、将空间中的曲面梁简化为直梁,例如将前后围左右侧及顶盖骨架上曲面立柱简化为若干个直梁,这种简化对整个车身结构的计算影响很小。
2、将有厚度的梁简化为无厚度的梁,在计算时再约束梁的厚度。
3、忽略车身蒙皮。
车身蒙皮大多数是焊接在骨架上,少数是铆接在骨架上,因此他对车身骨架的强度具有加强作用。
这样计算的结果将更加安全可靠。
4.2车辆载荷工况分析
4.2.1水平弯曲工况分析
水平弯曲工况下,此款客车式客车车身骨架所承受的载荷主要是由车身骨架、底架、底盘、座椅、乘员、空调系统及车身各种附件的重量产生的。
根据车辆上各总成的质量的分布的空间位置将他们换算成为节点载荷,放置在其所在位置的薄壁梁的节点位置上「<6-}0}0
1)、载荷处理
本文中,载荷可分为底盘各总成质量、车身骨架质量、车身附件质量和乘客质量等。
底盘各总成质量可均匀分布到底架上的各对应的薄壁梁单元上;车身骨架质量可分布到骨架各个骨架型钢的几何形心上;车身附件的质量根据其质心所在的位置可均匀分布在相对应空间位置的节点上,使之成为这些相应节点上的集中载荷。
乘员重量(按65千克/人计算)载荷均匀分布到骨架的各对应的薄壁梁单元上。
2)、约束处理
边界条件是约束此车两后轮位置处节点的全部自由度以及两前轮位置处节点的3个转动自由度和2个平动自由度,释放一个平动自由度UX。
其计算结果如下图4.1所示。
由上图可以看出在水平弯曲工况下,底架的最大应力为后悬架前,截面突变处可以达到165MPa,前悬架处应力也比较大,在100-140MPa之间,底架其余位置一般较高处在50-60MPa之间,大部分区域在30MPa以下;顶骨架最大应力在第一横梁处,其应力值为70MPa左右,其余位置应力较高处出现在中部的横梁的中间部位以及横梁与两侧纵梁的连接部位,其应力值为50-60MPa之间;左右侧骨架的最大应力为70MPa左右,出现在中部两侧窗立柱,斜支撑以及窗下沿以及行李仓门上横梁的中段位置,其余位置应力较高处的应力值一般为50-60MPa。
地板骨架应力较大处在地板骨架与底架连接
部分,其应力值一般在80MPa以下,其余部分都较小。
此款客车骨架型钢材料为Q235和Q345钢,底架型钢和槽钢材料为16Mn钢。
Q235钢的屈服强度为235MPa,Q345钢的屈服强度为345MPa,16Mn钢的屈服强度为280-350MPa。
而此款客车水平弯曲工况下的最大应力值为165MPa,这种工况下安全系数为1.7-2.2。
安全储备系数比较高,满足车辆安全要求。
4.2.2紧急制动工况分析
紧急制动工况计算时主要考虑客车在满载的状态下以最大制动加速度0.758制动时,地面产生的制动力对整个车身产生的影响。
由于此款客车采用前2后4空气气囊悬架,空气气囊只能承受竖直方向的作用力,而对于纵向和横向的作用力则需要通过推力杆传递到底盘车架上。
这种情况下,推力杆及推力杆支座将会承受比较大的力,因此它们必须具有足够大的强度
1)、载荷处理
紧急制动工况下的载荷处理方法与水平弯曲工况下的载荷处理方法相同。
2)约束处理
本文中采取约束两前轮装配位置处节点的所有三个平动自由度,并约束两后轮装配位置处的节点的垂直自由度以及纵向自由度,释放其他自由度。
其计算结果见下图4.20
由图4.2我们可以看出在紧急制动工况下,由于制动轴荷发生转移,整车质心位置的变化较大,前悬处所受载荷将大大增加。
底架最大应力发生在车架前段与中段的连接处,其应力值为251MPa;前悬架处的横梁位置的应
力值为90-1OOMPa,后悬架处的应力值比较小;顶骨架的最大应力发生在顶横梁与两侧的纵梁的连接处,其应力值为100MPa左右,其余部位应力值比较小在50-70MPa之间;左右侧骨架的最大应力发生在两侧窗立柱的根部位置,其应力值在130-150MPa之间,其余部分的应力值在100MPa以下;地板骨架最大的应力发生在地板骨架格栅的斜支撑型钢处,其应力值为150MPa,地板骨架其余部位应力都比较小。
由以上结果可以看出在紧急制动工况下,此款车的最大应