GB2商用车驾驶室外部凸出物.docx
《GB2商用车驾驶室外部凸出物.docx》由会员分享,可在线阅读,更多相关《GB2商用车驾驶室外部凸出物.docx(14页珍藏版)》请在冰豆网上搜索。
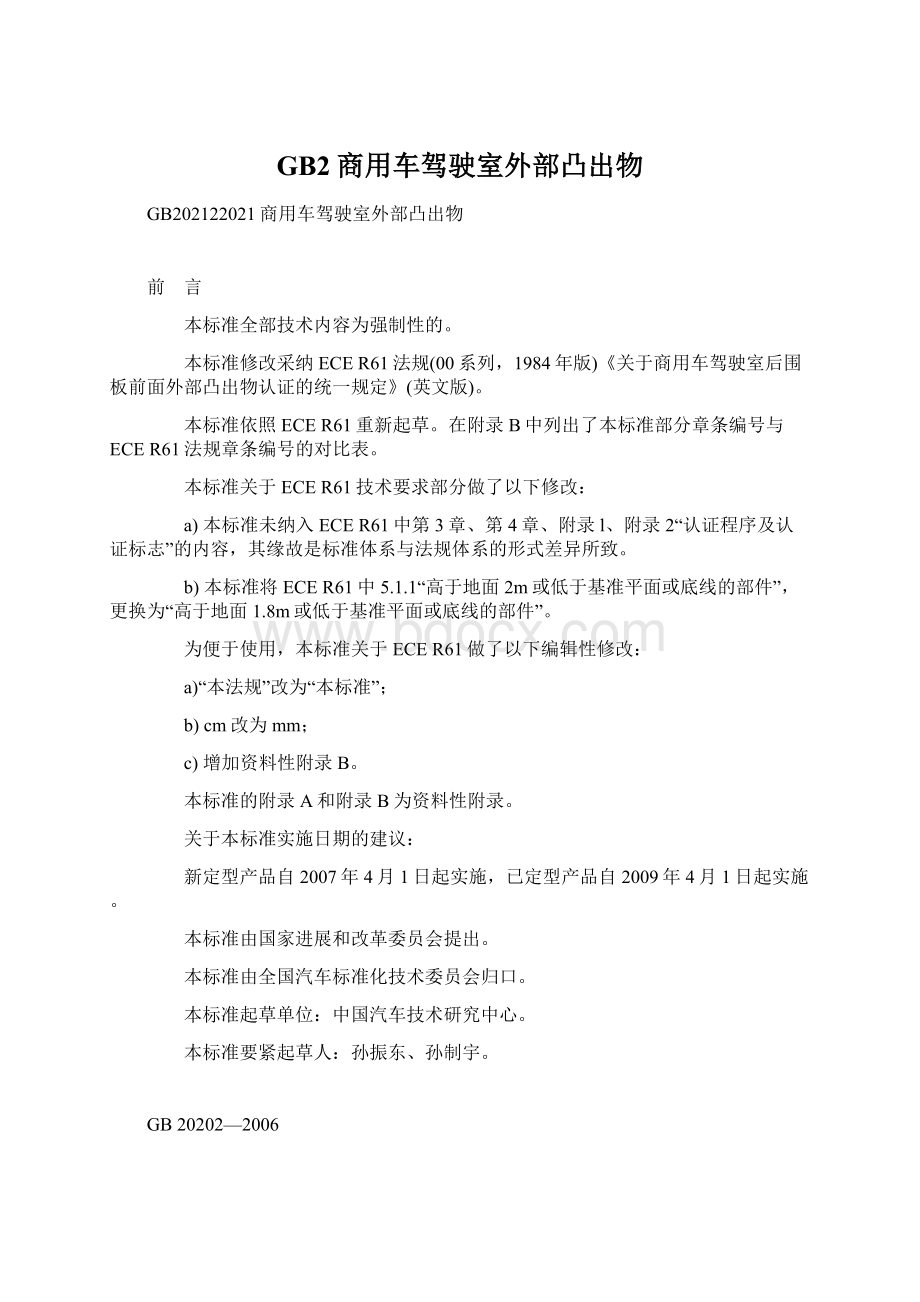
GB2商用车驾驶室外部凸出物
GB202122021商用车驾驶室外部凸出物
前 言
本标准全部技术内容为强制性的。
本标准修改采纳ECER61法规(00系列,1984年版)《关于商用车驾驶室后围板前面外部凸出物认证的统一规定》(英文版)。
本标准依照ECER61重新起草。
在附录B中列出了本标准部分章条编号与ECER61法规章条编号的对比表。
本标准关于ECER61技术要求部分做了以下修改:
a)本标准未纳入ECER61中第3章、第4章、附录l、附录2“认证程序及认证标志”的内容,其缘故是标准体系与法规体系的形式差异所致。
b)本标准将ECER61中5.1.1“高于地面2m或低于基准平面或底线的部件”,更换为“高于地面1.8m或低于基准平面或底线的部件”。
为便于使用,本标准关于ECER61做了以下编辑性修改:
a)“本法规”改为“本标准”;
b)cm改为mm;
c)增加资料性附录B。
本标准的附录A和附录B为资料性附录。
关于本标准实施日期的建议:
新定型产品自2007年4月1日起实施,已定型产品自2009年4月1日起实施。
本标准由国家进展和改革委员会提出。
本标准由全国汽车标准化技术委员会归口。
本标准起草单位:
中国汽车技术研究中心。
本标准要紧起草人:
孙振东、孙制宇。
GB20202—2006
商用车驾驶室外部凸出物
Thecabofcommericalvehicles—Externalprojections
1范畴
本标准规定了商用车驾驶室后围板之前的车身外部凸出物的术语、一样规定、专门规定及检验方法。
本标准适用于N类汽车。
但不适用于汽车外后视镜及外后视镜的连接件、天线和行李架。
2规范性引用文件
下列文件中的条款通过本标准的引用而成为本标准的条款。
凡是注日期的引用文件,其随后所有的修改单(不包括勘误的内容)或修订版均不适用于本标准,然而,鼓舞依照本标准达成协议的各方研究是否可使用这些文件的最新版本。
凡是不注日期的引用文件,其最新版本适用于本标准。
GBll566—1995轿车外部凸出物
3术语和定义
下列术语和定义适用于本标准。
3.1
外表面externalsurface
本标准3.3中所定义的驾驶室后围板之前的车身外部表面,不包括后围板本身,但包括前翼子板、前保险杠和前轮等。
3.2
驾驶室cab
构成驾驶员、乘员舱的车身,包括车门。
3.3
驾驶室后围板cabrearpanel
驾驶员和乘员舱外表面的最后面部分。
关于不能确定驾驶室后围板位置的,本标准认定位于驾驶员座椅R点向后500mm的横向垂直平面为驾驶室后围板,若驾驶员座椅位置可调剂,则调整到座椅的最后位置(见附录A)。
假如驾驶室内装有一排以上的座椅,则调整到最后位置的最后排乘员座椅靠背位置被认为是驾驶室后围板。
3.4
基准平面referenceplane
在车辆满载状态下,过前轮中心的水平面或离地高500mm的水平面,两平面中取其高度低的平面。
3.5
底线floorline
按下述方法确定的线:
取一个顶角为30°的圆锥体(自行确定锥高,锥顶向上,锥轴与水平面垂直),使其沿一满载车辆的车身外表面滚动以便连续接触车身外表面的最低位置,这些接触点几何轨迹确实是底线。
确定底线时,不考虑排气管、车轮和装在车身下面的功能机械元件,例如起重器支撑点,在拖曳或抛锚情形下使用的悬挂装置或连接件。
在不改变位置的情形下,车轮拱形别处的间隙可假想成填平后所形成的光滑外表面。
确定底线时,应考虑前保险杠。
就某一车型,底线轨迹可能在前保险杠的端头或前保险杠下面的车身板件上。
假如同时有两个或两个以上的接触点,应取最低的接触点来确定底线。
3.6圆角半径radiusOfcurvature
最接近零件的圆形的圆弧半径。
4一样规定
4.1在汽车空载,车门、车窗及各种盖板处于关闭状态时,下列车身外表面零部件不受本标准限制:
4.1.1高于地面1.8m或低于基准平面或底线的部件;
4.1.2在静止状态下,不能被直径100mm的球体所触及的部件;
4.1.3在低于基准平面的区域内,落在两个垂直平面之间的部件,仍受本标准限制。
这两个垂直平面是触及到车身外表面的平面和此平面向车辆内部平移80mm的平面。
4.2车身“外表面”不得有任何直截了当朝外可能伤及行人和骑自行车及摩托车者的部分。
4.3本标准第5章中所述的车身零件不得有任何直截了当朝外的尖锐部分,以及由于其形状、尺寸、朝向、硬度等在碰撞事故中可能增加刮伤、撞伤的危险性或加重被撞者伤势的外部凸出部分。
4.4车身外表面凸出零件的材料硬度不超过邵尔A硬度60HA时,凸出零件圆角半径可小于第5章的规定。
5专门规定
5.1装饰件、商用符号、商用标记的字母和数字
5.1.1装饰件、商用符号、商用标记的字母和数字的圆角半径不得小于2.5mm。
本规定不适用于凸出表面高度不大于5mm的部件,但这些部件直截了当朝外边缘应是钝角。
5.1.2对凸出支承面超过10mm的装饰件、商用符号、商用标记的字母和数字,在大致平行于其安装面的平面内,从任何方向对其凸出的最高点施加100N的外力时,其应能收缩、脱落或弯曲。
在施加100N的外力时,使用一个直径不大于50mm的平端压头,如若不可能,应采纳等效方法。
在装饰件缩进、脱落或弯曲之后,剩余部分凸出高度不得大于10mm,同时不能有任何尖角、锐边或刃口。
5.2前照灯遮光板和灯圈
5.2.1前照灯承诺装凸出的遮光板和灯圈,但相关于前照灯透光玻璃外表面的凸出高度不应超过30mm,圆角半径不得小于2.5mm。
5.2.2可收缩式前照灯,在工作和收缩位置,都应符合5.2.1的规定。
5.2.35.2.1的规定不适用于埋在车身内或伸出车身外的前照灯,但车身要符合4.2的规定。
5.3格栅
格栅的圆角半径:
格栅缝隙宽度大于40mm时,圆角半径不得小于2.5mm;格栅缝隙宽度大于25mm小于40mm时,圆角半径不得小于1mm;格栅缝隙宽度小于25mm时,圆角半径不得小于0.5mm。
5.4风窗刮水器和前照灯刮水器
5.4.1风窗刮水器和前照灯刮水器的转轴应装有爱护罩,爱护罩圆角半径不得小于2.5mm,在离最高凸出点不大于6.5mm处测量时,转轴爱护罩表面面积不得小于150mm2。
5.4.2风窗和前照灯洗涤器喷嘴的圆角半径不得小于2.5mm,凸出高度小于5mm的部分的朝外边缘应是钝角。
5.5爱护装置(前保险杠)
5.5.1前保险杠的两端应沿车身外表面弯曲。
5.5.2前保险杠上的元件所有朝外的刚性表面的圆角半径不得小于5mm。
5.5.3牵引钩和绞盘不能凸出前保险杠的前表面。
绞盘在非工作状态下,且绞盘上盖有圆角半径不小于2.5mm的爱护罩时,绞盘能够凸出前保险杠的前表面。
5.5.45.5.2的规定不适用于保险杠上的镶嵌件或安装在保险杠上凸出高度小于5mm的零部件,但凸出高度小于5mm的零部件的边缘应是钝角。
关于安装在保险杠上的其他零部件和本标准其他条款所提及的零部件,本标准第5章的规定应是适用的。
5.6车门、行李箱、发动机罩、通风口、把手的手柄、铰链和按钮
5.6.1车门、行李箱、发动机罩、通风口的按钮凸出高度不应超过30mm,把手和发动机罩盖锁扣凸出高度不应超过70mm,其他零件凸出高度不应超过50mm。
圆角半径均不得小于2.5mm。
5.6.2假如侧门手柄是旋转式手柄,则应满足下述任一要求:
5.6.2.1如手柄在与车门表面平行的方向上旋转,手柄的端头必须朝向后方且向车门板弯曲并安置在爱护套内或嵌在凹槽中。
5.6.2.2不与车门表面平行的任何方向上向外转动的手柄,在关闭位置时,手柄的端头应朝后或朝下并安置在爱护套内或嵌在凹槽中。
不符合上述规定但满足下列规定的手柄仍可同意:
a)手柄有独立的回位机构;
b)若同位机构损坏,手柄凸出表面不应超过15mm;
c)手柄处于打开位置,手柄圆角半径不得小于2.5mm(本规定不适用于手柄开到最大位置,凸出高度小于5mm,朝外边缘是钝角的手柄);
d)手柄端部表面积在离最外凸出点不大于6.5mm处测量时,不得小于150mm2。
5.7踏步板
踏步板边缘应是圆角。
5.8侧面空气和雨水导流板与车窗玻璃防污空气导流板
侧面空气和雨水导流板与车窗玻璃防污空气导流板直截了当朝向别处的边缘,圆角半径不得小于1mm。
5.9金属板件的边缘
金属板件的边缘应向车身内部方向翻边,且翻边至边缘可不能被一直径为100mm的球体所触及;或金属板件的边缘加装圆角半径不得小于2.5mm的爱护罩。
5.10车轮螺母、轮毂罩盖和爱护装置
5.10.1车轮螺母、轮毂罩盖和爱护装置不能有任何蝶形凸出物。
5.10.2当汽车直线行驶时,位于车轮旋转轴线水平面以上的车轮零件(轮胎除外),不得凸出车轮以上的车身围板边缘在水平面上的垂直投影。
然而,因功能要求,覆盖车轮螺母和轮毂的爱护装置不得不凸出时,必须保证:
凸出部分的圆角半径不得小于5mm且凸出量不得大于30mm。
5.10.3若螺栓或螺母凸出轮胎(过车轮旋转轴线的水平面以上的轮胎部分)外表面的投影,则应安装符合5.10.2规定的爱护装置。
5.11起重器支承架和排气管
5.11.1起重器支承架和排气管凸出底线的垂直投影或凸出基准平面与车身外表面相交部分的垂直投影的距离不应超过l0mm。
5.11.2不符合5.11.1的规定,然而排气管的末端边缘是圆形且圆角半径不小于2.5mm时,排气管能够凸出10mm以上。
6检验方法
6.1装在车身外表面上的零件凸出部分尺寸的测量方法
6.1.1装在车身凸形表面上的零件的凸出部分尺寸能够直截了当测量或参照此零件在安装位置时的截面图纸来测定。
6.1.2除装在车身凸形表面上的零件,其他安装在车身上的零件的凸出部分尺寸不能直截了当测量,而是用一个直径为100mm的球体在其上连续滚动,测量基准线(基准线指过首末球体位置球心的直线。
)与球心之间的最大距离,图1给出了使用本方法的示例。
用直径100mm的球体在其上连续滚动,将得到一系列的球体球心位置点Q1、Q2、Q3。
过首末球体位置的球心点Q1和Q3做一直线,Q1Q3线即是基准线。
从距最远的球心点Q2向Q1Q3作垂线Q2Q,则Q2Q即是被测的凸出高度h。
6.1.3关于把手,相关于过连接点的平面,测量凸出距离,图2给出了示例。
连接点L和点Q,测量凸出高度h。
6.2前照灯遮光板和灯圈的凸出部分的测量方法
从直径为100mm的球体的接触点水平测量前照灯外表面凸出部分,如图3所示。
直径100mm的球体与前照灯透光玻璃外表面相接于点L,同时该球外表面又与前照灯遮光板上部最凸出部分相接于点Q,点L和Q在纵向垂直平面的投影水平距离h即为凸出高度。
6.3格栅间隙的测量方法
格栅间隙指过直径为100mm的球体接触点且垂直于接触点连线的两平面之间的距离,图4和图5给出了使用本方法的示例。
用直径100mm的球体与格栅的两相邻元件接触,接触点分别为L、Q点。
点L和Q间的距离h即为格栅间隙。
单位为毫米
附录A
(资料性附录)
“H”点与实际靠背角确定程序和“R”点与设计靠背角关系验证程序
A.1定义
A.1.1乘坐位置“H”点:
是第A.3章所述的三维H点装置的躯干与大腿的理论旋转轴在纵向垂直平面内的标记点。
A.1.2“R”点或“乘坐基准点”:
指由车辆制造厂规定的基准点:
A.1.2.1相关于三维坐标系来确定;
A.1.2.2与躯干和大腿的旋转点(“H”点)的理论位置相同,座椅处于制造厂给定的每个座椅最低和最后的正常驾驶或乘坐位置。
A.1.3“座椅靠背角”:
指座椅靠背与铅垂方向的夹角。
A.1.4“实际靠背角”:
指第A.3章所述的三维H点装置的躯干线与过“H”点铅垂线之间的夹角。
A.1.5“设计靠背角”:
指由制造厂规定的:
A.1.5.1座椅处于制造厂给定的每个座椅最低和最后的正常驾驶或乘坐位置,确定的座椅靠背角;
A.1.5.2过“R”点的铅垂线与躯干线之间的夹角;
A.1.5.3理论上与实际靠背角相等。
A.2“H”点和实际靠背角的确定
A.2.1制造厂提供的每个座椅都应确定“H”点和实际靠背角。
假如认为同一排座椅是相同的(长条座椅、相同座椅等),每排座椅只需确定一个座椅的“H”点和“实际靠背角”。
第A.3章所述的三维H点装置安放在该排有代表性的位置上,该位置是:
A.2.1.1关于第一排:
驾驶员座椅;
A.2.1.2关于其他排:
某一外侧座椅。
A.2.2确定“H”点和实际靠背角时,座椅处于制造厂给定的每个座椅最低和最后的正常驾驶或乘坐位置。
若座椅靠背角是可调的,座椅靠背应在制造厂规定的位置锁止,制造厂没有规定任何位置,座椅靠背应在实际靠背角为25°的位置锁止。
A.3三维“H”点装置的描述
A.3.1三维H点装置的质量和外形与平均身高的成年男性的质量和外形相同,见图A.1和图A.2。
A.3.2三维H点装置包括:
A.3.2.1背板和座板,模拟人体的躯干和大腿,两者机械地铰接于“H”点处;
A.3.2.2小腿杆件在连接膝部的T形杆处与座板总成相连;
A.3.2.3模拟脚的部件,通过模拟踝部的部件与小腿杆件相连;
A.3.2.4此外,座板上装有水平仪以检验其横向定位。
A.3.3各个构件质量用适当的点代替相应构件的重心,三维H点装置的总质量大约是75.6kg。
图A.2中的列表给出其各构件质量的说明。
A.3.4三维H点装置的躯干线是过背板和座板的连接点与颈和胸的理论连接点的直线(见图A.1)。
A.4三维“H”点装置的安装
三维H点装置按下列方式安装。
A.4.1车辆停放在水平面上,按A.2.2的规定调整座椅位置。
A.4.2在被检验的座椅上铺一块布以便安装三维H点装置。
A.4.3三维H点装置放在被检验的座椅上,其旋转轴与车辆纵向对称面垂直。
A.4.4三维H点装置的脚放在下述位置:
A.4.4.1前排座椅,使用来检验三维H点装置座板横向定位的水平仪指示水平。
A.4.4.2后排座椅,尽可能通过前排座椅的方式调整。
假如两脚落在地板不同的水平位置上,应以先与前排座椅接触的脚作为基准来放置另一只脚,使检验三维H点装置座板横向定位的水平仪指示水平。
A.4.4.3假如在中间座椅确定“H”点位置时,则两脚分别放在通道的两侧。
A.4.5放上大腿重块,调平检验三维H点装置座板横向定位的水平仪。
A.4.6通过三维H点装置的连接膝部的T形杆和背板向前旋转,把三维H点装置从座椅靠背上移开。
然后将背板向后倾到后限位块,把三维H点装置重新放在座椅上,三维H点装置背板重新放在座椅靠背上。
A.4.7对三维H点装置施加100N±10N的水平力两次,图A.2中的箭头表示力的作用点和方向。
A.4.8躯干重块放在左右两侧位置上,并调平三维H点装置的横向水平仪。
A.4.9使三维H点装置的横向水平仪保持水平,将三维H点装置背板向前旋转直到躯干重块在“H”点正上方,以便减小与座椅靠背的摩擦。
A.4.10轻轻向后移动三维H点装置的背板,安装操作就此完成。
三维H点装置的横向水平仪应水平,若不水平,重复上述程序。
A.5结果
A.5.1按A.4章要求安装完三维H点装置后,就确定了车辆座椅的“H”点和实际靠背角,实际靠背角是过“H”点的铅垂线和躯干线之间的倾角。
A.5.2测量“H”点在三维坐标系中的坐标和实际靠背角,同时与车辆制造厂提供的数据相比较。
A.6验证“R”点与“H”点的相对位置和设计靠背角与实际靠背角的关系
A.6.1符合A.5.2规定的“H”点和实际靠背角的测量结果与车辆制造厂提供的“R”点坐标和设计靠背角相比较。
A.6.2假如“H”点坐标位于水平与铅垂方向边长均为50mm且对角线交于“R”点的正方形内,同时实际靠背角偏离设计靠背角小于5°,关于上述乘坐位置,应认为“R”点与“H”点相对位置以及设计靠背角与实际靠背角关系满足要求。
A.6.2.1若符合A.6.2的规定,“R”点和设计靠背角可用于试验。
也能够调整三维H点装置使“H”点和“R”点一致,实际靠背角和设计靠背角一致。
A.6.3假如“H”点或实际靠背角不符合A.6.2的规定,则“H”点或实际靠背角再重新确定两次共3次)。
假如3次中有两次结果符合要求,则试验结果是满足要求的。
A.6.4假如3次操作中至少有两次结果不符合A.6.2的规定,则试验结果无效。
A.6.5假如处于A.6.4所述的情形,或由于车辆制造厂未提供有关“R”点位置或设计靠背角的数据,而使检验无法进行时,则应取3次测量结果的平均值用于本标准涉及“R”点或设计靠背角的所有场合。
附录B
(资料性附录)
本标准章条编号与ECER61章条编号对比
表B.1本标准章条编号与ECER61章条编号对比