压力铸造连杆零件成型工艺分析.docx
《压力铸造连杆零件成型工艺分析.docx》由会员分享,可在线阅读,更多相关《压力铸造连杆零件成型工艺分析.docx(7页珍藏版)》请在冰豆网上搜索。
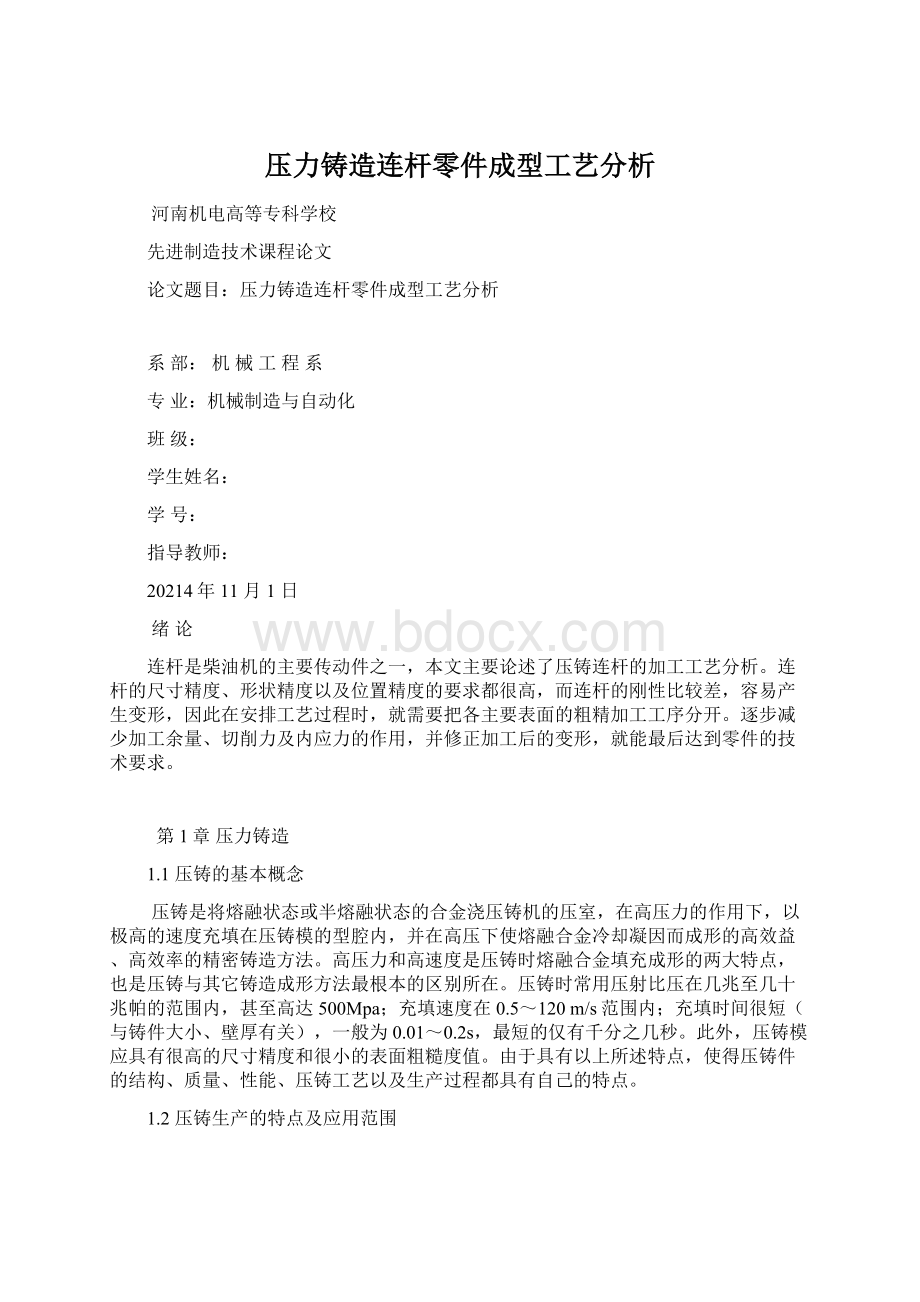
压力铸造连杆零件成型工艺分析
河南机电高等专科学校
先进制造技术课程论文
论文题目:
压力铸造连杆零件成型工艺分析
系部:
机械工程系
专业:
机械制造与自动化
班级:
学生姓名:
学号:
指导教师:
20214年11月1日
绪论
连杆是柴油机的主要传动件之一,本文主要论述了压铸连杆的加工工艺分析。
连杆的尺寸精度、形状精度以及位置精度的要求都很高,而连杆的刚性比较差,容易产生变形,因此在安排工艺过程时,就需要把各主要表面的粗精加工工序分开。
逐步减少加工余量、切削力及内应力的作用,并修正加工后的变形,就能最后达到零件的技术要求。
第1章压力铸造
1.1压铸的基本概念
压铸是将熔融状态或半熔融状态的合金浇压铸机的压室,在高压力的作用下,以极高的速度充填在压铸模的型腔内,并在高压下使熔融合金冷却凝因而成形的高效益、高效率的精密铸造方法。
高压力和高速度是压铸时熔融合金填充成形的两大特点,也是压铸与其它铸造成形方法最根本的区别所在。
压铸时常用压射比压在几兆至几十兆帕的范围内,甚至高达500Mpa;充填速度在0.5~120m/s范围内;充填时间很短(与铸件大小、壁厚有关),一般为0.01~0.2s,最短的仅有千分之几秒。
此外,压铸模应具有很高的尺寸精度和很小的表面粗糙度值。
由于具有以上所述特点,使得压铸件的结构、质量、性能、压铸工艺以及生产过程都具有自己的特点。
1.2压铸生产的特点及应用范围
1.2.1压铸的优缺点
(1)铸件的尺寸精度和表面粗糙度要求很高
铸件的尺寸精度为IT12~IT11;表面粗糙度Ra一般3.2~0.8μm,最低达0.4μm。
因此,一般压铸件可以不经过机械加工或仅是个别部位加工即可使用。
(2)铸件的强度和表面硬度较高
由于压铸模的激冷作用,又在压力下结晶,因此,压铸件表面晶粒较细,组织致密,所以表面层的硬度和强度都比较高。
压铸件得抗拉强度一般比砂型铸件高25%~30%,但伸长率较低。
(3)可以压铸形状复杂的薄壁铸件
由于压铸件形成过程始终是在压力作用下充填和凝固的,对于轮廓峰谷、凸凹、窄槽等都能清晰地压铸出来。
压铸出的最小壁厚:
锌合金为0.3mm;铝合金为0.5mm。
铸出孔的最小直径为0.7mm。
铸出螺纹最小螺距0.75mm。
对于形状复杂,难以或不能用切削加工制造的零件。
即使产量小,通常也采用压铸生产,尤其当采用其它铸造方法或其它金属成形工艺难以制造时,采用压铸生产最为适宜。
(4)生产效率极高
在所有的铸造方法中,压铸是一种生产率最高的方法。
这主要是由于压铸过程的特点决定的,且随着生产工艺过程的机械化、自动化程度进一步发展而提高。
一般冷压室压铸机平均每班可压铸600~700次,热室压铸机可压铸3000~7000次,适合于大批量的生产。
每一次操作循环一般为10s~1min,并且可以实现一模多腔的工艺,其产量增倍。
与其他铸造方法比较,压铸还节约甚至完全省去了零件的机械加工工时和设备。
(5)可省略装配操作和简化制造程序
压铸生产时,可嵌铸其他金属或非金属材料零件以提高压铸件得局部强度,满足某些特殊要求(如耐磨性、绝缘性、导磁性等),以及改善铸件结构的工艺性。
压铸既可获得形状复杂、精度高、尺寸稳定、互换性好的零件,又可以镶嵌压铸,代替某些部件的装配和简化制造工序,改善压铸件得工作性能,并且节能降耗。
任何一种工艺方法都不是十全十美的。
压铸也尚存一些缺点有待解决,主要是:
(1)压铸件表层有气孔
这是由于液态合金充型速度极快,型腔中的气体很难完全排除,常以气孔形式存留在铸件中。
因此,一般压铸件不能进行热处理,也不宜在高温条件下工作。
这是由于加热温度高的时候,气孔内的气体膨胀,导致压铸件表面鼓包,影响质量与外观。
同样,也不希望进行机械加工,以免铸件表面显露气孔。
(2)压铸合金类别和牌号有所限制
目前只适用于锌、铝、镁合金的压铸。
对于钢铁材料,由于其熔点高,压铸模使用寿命短,故目前钢铁材料压铸难于实际生产。
但近年来,正在研究试验半固态金属铸新工艺,将为钢铁材料压铸开辟新的途径。
至于某一种合金类别中,仅限于几种牌号可以进行压铸,这是由于压铸时的激冷、产生剧烈收缩、成形的充填条件等的原因造成的。
(3)压铸的生产准备费用较高
这是由于压铸机的成本高,压铸模加工周期长、成本高。
如国产的J111型1250kN通用压铸机,大约10~12万美元/台;一般的压铸模制造费2~10万元/具,进口模具价格更昂贵。
由于压铸机生产效率高,故压铸工艺只适用于大批量的生产。
第2章连杆
2.1连杆的作用
连杆的作用是将活塞承受的力传给曲轴,并使活塞的往复运动转变为曲轴的旋转运动。
连杆由连杆体、连杆盖、连杆螺栓和连杆轴瓦等零件组成,连杆体与连杆盖分为连杆小头、杆身和连杆大头。
连杆小头用来安装活塞销,以连接活塞。
杆身通常做成“工”或“H”形断面,以求在满足强度和刚度要求的前提下减少质量。
连杆大头与曲轴的连杆轴颈相连。
一般做成分开式,与杆身切开的一半称为连杆盖,二者靠连杆螺栓连接为一体。
连杆轴瓦安装在连杆大头孔座中,与曲轴上的连杆轴颈装和在一起,是发动机中最重要的配合副之一。
常用的减磨合金主要有白合金、铜铅合金和铝基合金。
2.2连杆的结构特点
连杆是汽车发动机中的主要传动部件之一,它在柴油机中,把作用于活塞顶面的膨胀的压力传递给曲轴,又受曲轴的驱动而带动活塞压缩气缸中的气体。
连杆在工作中承受着急剧变化的动载荷。
连杆由连杆体及连杆盖两部分组成。
连杆体及连杆盖上的大头孔用螺栓和螺母与曲轴装在一起。
为了减少磨损和便于维修,连杆的大头孔内装有薄壁金属轴瓦。
轴瓦有钢质的底,底的内表面浇有一层耐磨巴氏合金轴瓦金属。
连杆小头用活塞销与活塞连接。
小头孔内压入青铜衬套,以减少小头孔与活塞销的磨损,同时便于在磨损后进行修理和更换。
在发动机工作过程中,连杆受膨胀气体交变压力的作用和惯性力的作用,连杆除应具有足够的强度和刚度外,还应尽量减小连杆自身的质量,以减小惯性力的作用。
连杆杆身一般都采用从大头到小头逐步变小的工字型截面形状。
为了保证发动机运转均衡,同一发动机中各连杆的质量不能相差太大,因此,在连杆部件的大、小头两端设置了去不平衡质量的凸块,以便在称量后切除不平衡质量。
连杆大、小头两端对称分布在连杆中截面的两侧。
考虑到装夹、安放、搬运等要求,连杆大、小头的厚度相等(基本尺寸相同)。
在连杆小头的顶端设有油孔(或油槽),发动机工作时,依靠曲轴的高速转动,把气缸体下部的润滑油飞溅到小头顶端的油孔内,以润滑连杆小头衬套与活塞销之间的摆动运动副。
连杆的作用是把活塞和曲轴联接起来,使活塞的往复直线运动变为曲柄的回转运动,以输出动力。
因此,连杆的加工精度将直接影响柴油机的性能,而工艺的选择又是直接影响精度的主要因素。
反映连杆精度的参数主要有5个:
(1)连杆大端中心面和小端中心面相对连杆杆身中心面的对称度;
(2)连杆大、小头孔中心距尺寸精度;
(3)连杆大、小头孔平行度;
(4)连杆大、小头孔尺寸精度、形状精度;
(5)连杆大头螺栓孔与接合面的垂直度。
2.3连杆的主要损坏形式
连杆的主要损坏形式是疲劳断裂和过量变形。
通常疲劳断裂的部位是在连杆上的三个高应力区域。
连杆的工作条件要求连杆具有较高的强度和抗疲劳性能;又要求具有足够的钢性和韧性。
传统连杆加工工艺中其材料一般采用45钢、40Cr或40MnB等调质钢,硬度更高,因此,以德国汽车企业生产的新型连杆材料如C70S6高碳微合金非调质钢、SPLITASCO系列锻钢、FRACTIM锻钢和S53CV-FS锻钢等(以上均为德国din标准)。
合金钢虽具有很高强度,但对应力集中很敏感。
所以,在连杆外形、过度圆角等方面需严格要求,还应注意表面加工质量以提高疲劳强度,否则高强度合金钢的应用并不能达到预期效果。
第3章压力铸造连杆工艺分析
3.1铸造连杆工艺分析
采用铸造连杆有4个优点:
1.与锻造连杆相比设计的灵活性比较大;2.改善了连杆的机加工性能;3.铸造连杆的尺寸比较接近连杆的成品尺寸;4.在使用上能满足可靠性要求。
(1)经济效果
由于珠光体可锻铸铁连杆具有优异的机加工性能,因此铸造连杆的成本比锻造连杆要低得多,另外,铸造连杆的可靠性和多用性表明它在其它车发动机上也具有潜力。
(2)材料
铸造连杆的材料为珠光体可锻铸铁,其平均化学成分为:
2.6%C、1.4%SI、0.42%Mn,其余为Fe。
热处理后的机械性能:
最小的抗拉强度为689N/mm2、最小屈服强度为551N/mm2、延伸率为2%;布氏硬度为249~269。
(3)工艺过程
选择合适的废钢、铁合金和回炉料,利用冲天炉熔化,铁水出炉温度为1482℃。
将铁水转入电炉内搅拌并过热,然后倒入浇包内浇筑。
每个铸型可铸几支连杆。
铸件在铸型中充分冷却后进行落砂处理,将所得铸件装入比较小的箱内旋转,以去除粘附在铸件上的型砂。
(4)退火
铸态下的连杆为白口组织,碳全都以碳化物Fe3C的形式存在。
将连杆堆放在退火盘内,由提升机构升起,并用推杆推入炉内,在可控气氛、以辐射管加热的退火炉中退火。
分度机构带动炉内连杆向前移动,以便下一批连杆入炉。
在退火过程中,连杆被加热至954℃保温18h。
出炉后,连杆在空气中以极快的冷却速度通过上临界温度,获得一种致密的珠光体组织和均匀分布的二次石墨。
(5)淬火
将退火后的连杆放入另一个炉子里重新加热至870℃,并充分保温,是基体组织奥氏体化。
随即将连杆放入油中淬火,形成马氏体基体。
然后再将连杆加热至620~604℃,并保温3~4h进行回火。
附图中黑色团絮状物为石墨,它大大地改善了材料的加工性能。
经退火、淬火并回火的连杆基体组织为回火马氏体。
(6)检验和质量控制
在退火、淬火和回火之后,对连杆进行连续检查,以保证获得所要求的组织和硬度。
将热处理后的连杆重新加热至480℃并进行模压,从而保证其平直度满足图纸技术要求。
将铸件移至三工位切除工序上,切除三个浇冒口并清理飞边毛刺。
随后对铸件进行喷丸处理。
并进行磁力探伤、声频检查、超声波探伤和X射线检查。
(7)机加工
机加工工序包括磨削连杆大头和小头两侧的平面、镗内孔、钻两个螺栓孔和分开连杆大头孔,形成与曲轴相配的轴承盖。
珠光体可锻铸铁基体中的回火石墨颗粒可是切屑破裂,同时由于石墨的润滑作用,减少了切削负载,从而加工过程中允许使用较高的切削速度和进刀量,提高了刀具的切削寿命,也节省了去除刀具上切屑瘤的时间。
在整个生产过程中,从原材料验收,铸造生产工艺过程的控制到产品的最后检验都必须保证严格的质量管理。
(8)铸造连杆应力分析
铸造连杆的重新设计是以应力分析、疲劳试验和发动机耐久性试验以及铸造和机加工工艺要求为基础进行的。
首先对比锻造连杆和铸造连杆的应力分析,确定静态应力分析中所用的载荷,这一数值可由发动机制造厂家提供的有关资料中计算出来。
连杆的实验数据为拉为8.9~40kN,压力为40~71KN。
上述拉力和压力作用下得到的脆漆图样示出了应力集中区。
为了获得应力的绝对值,将应变片粘附于该应力集中区并重复加载。
应力分析结果表明,最大交变应力位于杆身、连杆小头凸缘部及曲柄端凸缘上的螺母和螺栓头座部分。
将应力值标在改进的古德曼应为图上,用于指导设计和估算耐久性。
(9)该劳性能试验
试验在液压拉伸压Vii;疲劳试验机上以4910r/min的转速和445kN的载荷对连杆进行轴向交变应力试验,以确定其疲劳性能。
根据在设计载荷下获俘的最小疲劳寿命和用Weibu11分析法得出的高载荷下平均疲劳寿命进行连杆设计。
为了进一步检验连杆的疲劳特性,可将铸选连杆装在各种汽车发动机上,在带有测功器的试验台上以一定的转速和负荷迸行试验,根据试脸进行最后设计。
(10)更改原设计
根据应力分析、疲劳试验和铸造试验结果,对连杆的原设计进行了改进,即在连杆应力比较小的区域减薄铸件,而在应力比较大的区域增厚铸件.从而减小了连杆的重量。
另外连杆腹部的工字截面带有一定的斜度,以此获得所要求的凝固顺序,即远离冒口的部位宪凝固,因而保证了在受力最大的部位具有十分健全的组织。
其它特点如下:
尽量保持铸件的截面厚度均匀、采取冒口补缩和冷却筋,从而提高了铸造性能并保证了铸件的内在质量。
参考文献
[1]田雁晨,天宝善,王文广等.编著.《金属压铸模设计技巧与实例》.2006年3月.化学工业出版社
[2]汪恺.主编.《机械工业基础标准应用手册》.2001年6月.机械工业出版社
[3]王启平.主编.《机械制造工艺学》第5版.2005年8月.哈尔滨工业大学出版社
[4]刘越.机械制造技术.化学工业出版社.2001年
[5]姜敏凤.工程材料及热成型工艺.北京.高等教育出版社.2003年
[6]顾崇衍.机械制造工艺学.陕西.科技技术出版社.1981年
[7]陈于萍.周兆元.互换性与测量技术基础.北京.机械工业出版社.2004年
[8]杨裕国.编.《压铸工艺与模具设计》.1997年.机械工业出版社
[9]黄健求.主编.《机械制造技术基础》.2005年11月.机械工业出版社
[10]张耀宸.机械加工工艺设计实用手册【M】.北京.航空工业出版社.1993年
[11]顾崇衍.机械制造工艺学.陕西.科技技术出版社.1981年