首秦2号高炉定量化停开炉操作实践.docx
《首秦2号高炉定量化停开炉操作实践.docx》由会员分享,可在线阅读,更多相关《首秦2号高炉定量化停开炉操作实践.docx(17页珍藏版)》请在冰豆网上搜索。
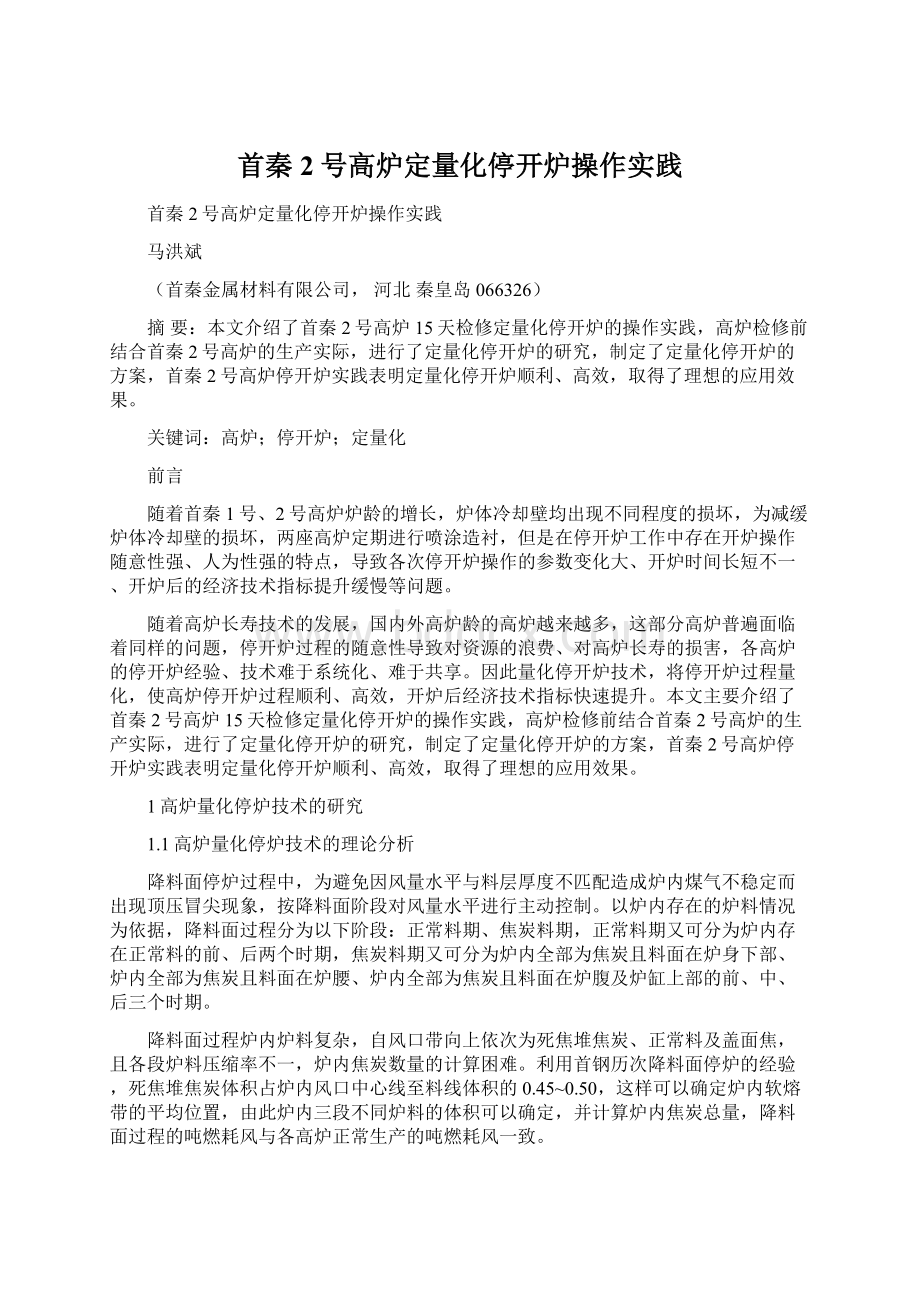
首秦2号高炉定量化停开炉操作实践
首秦2号高炉定量化停开炉操作实践
马洪斌
(首秦金属材料有限公司,河北秦皇岛066326)
摘要:
本文介绍了首秦2号高炉15天检修定量化停开炉的操作实践,高炉检修前结合首秦2号高炉的生产实际,进行了定量化停开炉的研究,制定了定量化停开炉的方案,首秦2号高炉停开炉实践表明定量化停开炉顺利、高效,取得了理想的应用效果。
关键词:
高炉;停开炉;定量化
前言
随着首秦1号、2号高炉炉龄的增长,炉体冷却壁均出现不同程度的损坏,为减缓炉体冷却壁的损坏,两座高炉定期进行喷涂造衬,但是在停开炉工作中存在开炉操作随意性强、人为性强的特点,导致各次停开炉操作的参数变化大、开炉时间长短不一、开炉后的经济技术指标提升缓慢等问题。
随着高炉长寿技术的发展,国内外高炉龄的高炉越来越多,这部分高炉普遍面临着同样的问题,停开炉过程的随意性导致对资源的浪费、对高炉长寿的损害,各高炉的停开炉经验、技术难于系统化、难于共享。
因此量化停开炉技术,将停开炉过程量化,使高炉停开炉过程顺利、高效,开炉后经济技术指标快速提升。
本文主要介绍了首秦2号高炉15天检修定量化停开炉的操作实践,高炉检修前结合首秦2号高炉的生产实际,进行了定量化停开炉的研究,制定了定量化停开炉的方案,首秦2号高炉停开炉实践表明定量化停开炉顺利、高效,取得了理想的应用效果。
1高炉量化停炉技术的研究
1.1高炉量化停炉技术的理论分析
降料面停炉过程中,为避免因风量水平与料层厚度不匹配造成炉内煤气不稳定而出现顶压冒尖现象,按降料面阶段对风量水平进行主动控制。
以炉内存在的炉料情况为依据,降料面过程分为以下阶段:
正常料期、焦炭料期,正常料期又可分为炉内存在正常料的前、后两个时期,焦炭料期又可分为炉内全部为焦炭且料面在炉身下部、炉内全部为焦炭且料面在炉腰、炉内全部为焦炭且料面在炉腹及炉缸上部的前、中、后三个时期。
降料面过程炉内炉料复杂,自风口带向上依次为死焦堆焦炭、正常料及盖面焦,且各段炉料压缩率不一,炉内焦炭数量的计算困难。
利用首钢历次降料面停炉的经验,死焦堆焦炭体积占炉内风口中心线至料线体积的0.45~0.50,这样可以确定炉内软熔带的平均位置,由此炉内三段不同炉料的体积可以确定,并计算炉内焦炭总量,降料面过程的吨燃耗风与各高炉正常生产的吨燃耗风一致。
结合软熔带位置,料面位置的计算分为:
耗焦量小于正常料的焦炭量,炉内存在软熔带,通过耗焦量计算正常料减少的体积,从而得到料面位置;耗焦量大于正常料的焦炭量,炉内软熔带消失,通过耗焦量计算炉料减少的体积,从而得到料面位置。
顶温控制的原则是既要保护炉顶设备,又要避免大量冷却水落至料面与炽热的焦炭反应生成H2,实现安全降料面,温度控制范围一般在250~350℃。
降料面过程中对于各打水管流量的调整要抓住顶温变化趋势,及时、微量调整,对于风量、风温下降引起的顶温下降要同时减少各打水管流量,对于渣皮脱落并覆盖在料面上引起的单方向顶温下降可不对打水管流量进行调整。
降料面过程前期的顶压突然升高现象多是由于炉内煤气分布不稳定,炉内产生了气流、管道,与风量水平匹配的高顶压有利于稳定炉内煤气,减少顶压的波动。
降料面过程中除非因各种原因导致O2混入炉内上部空间,否则在料面降至炉腹前,炉内发生爆震的可能性极小。
为了停气时的高炉安全及减少停气操作时煤气流速突然增大对炉内料柱的冲击,料面降至炉腰位置,逐步降低顶压。
降料面过程使用高风温有利于提高炉缸的热度,促进炉墙脱落渣皮的熔化、渗透,但高风温的使用提高了顶温控制的难度,且由于下部煤气体积的增加,对于减少降料面过程的煤气不稳定现象也是不利的,风温的使用范围一般在800℃~1000℃,在炉顶打水能力满足要求的基础上,随着对降料面过程中煤气控制能力的增强,可提高风温使用水平。
1)正常料期。
按降料面阶段对风量水平主动控制,避免因风量水平与料层厚度不匹配造成炉内煤气不稳定,基本原则是炉内存在正常料的情况下,风量可按较高水平控制,正常料前期按全风量的88%~92%控制,正常料后期按全风量的78%~82%控制,正常料前期与后期的划分依据料柱高度确定。
降料面过程的出渣出铁是料面能否降至风口以下的关键,第一次出铁安排在耗风量达到正常料所需耗风量的25%~30%时出铁,控制出铁量在炉内正常料生成铁水量的40%~50%,即使铁口未喷也堵口。
2)焦炭料期。
风量控制的基本原则是炉内只剩焦炭后,对风量水平严格控制,防止出现气流、管道,焦炭料前期按全风量的68%~72%控制,焦炭料中期按全风量的48%~52%控制,焦炭料后期按全风量的38%~42%控制。
回收煤气能够控制环境污染,创造经济效益,但降料面过程后期焦炭料层已经很薄,如何使吹入的热风全部与焦炭燃烧而不残留氧气,如何使煤气成分中H2含量不超标,为此要求降料面过程煤气稳定,在焦炭料层很薄的情况下不出现气流、管道,同时将顶温控制在适当水平,但H2%>8%、O2%>0.8%时或料面位置进入炉腹时必须停气。
停气时炉顶压力瞬间大幅下降,导致炉内下部的高温煤气瞬间加速向上运动,在打水量无法及时调整的情况下,炉顶温度快速上升,超过了高炉煤气的着火温度,使高炉煤气在放散阀处点燃,这严重影响降料面停炉时的高炉安全,停气前减风至0.30~0.35kg/cm2,打开炉顶放散阀,然后再将风量加至规定的水平。
在多个风口见空之后,安排第二次出铁,由于降料面期间铁口深度下降的影响,第二次出铁仅有少量铁水排出,但大部分炉渣能够排出。
若要求实现料面的大幅沉降,则要力争保持正常的铁口深度,若对料面沉降的幅度无要求,则出净预留的渣铁后,料面可以实现沉降至风口下沿的目的。
1.2高炉量化停炉技术的操作要点
停炉过程两个阶段:
正常料期、焦炭料期,正常料期又可分为炉内存在正常料的前、后两个时期,焦炭料期又可分为炉内全部为焦炭且料面在炉身下部、炉内全部为焦炭且料面在炉腰、炉内全部为焦炭且料面在炉腹及炉缸上部的前、中、后三个时期。
1)正常料期。
正常料期为炉内存在正常料的时期,正常料前期与后期的划分依据料柱高度确定,正常料前期对应的料柱高度占正常料料柱高度的60%~65%。
①炉内存在正常料的情况下,风量按较高水平控制,正常料前期按全风量的88%~92%控制,正常料后期按全风量的78%~82%控制。
②第一次出铁安排在耗风量达到正常料所需耗风量的25%~30%时出铁,控制出铁量在炉内正常料生成铁水量的40%~50%,即使铁口未喷也堵口。
2)焦炭料期。
焦炭料期为炉内正常料与软熔带已经消失、只剩焦炭的时期,焦炭料前、中、后期分别为炉内全部为焦炭且料面在炉身下部、炉内全部为焦炭且料面在炉腰、炉内全部为焦炭且料面在炉腹及炉缸上部的三个时期。
①炉内只剩焦炭后,对风量水平严格控制,防止出现气流、管道,焦炭料前期按全风量的68%~72%控制,焦炭料中期按全风量的48%~52%控制,焦炭料后期按全风量的38%~42%控制。
②料面位置进入炉腹时必须停气,停气前减风至0.30~0.35kg/cm2,打开炉顶放散阀,然后再将风量加至规定的水平(全风量的38%~42%)。
③全部风口数10%~20%的风口见空之后,安排第二次出铁,出净预留的渣铁后,料面沉降至风口下沿。
2高炉量化开炉技术的研究
2.1高炉量化开炉技术的理论分析
高炉开炉过程中,随着风口前焦炭的燃烧,回旋区逐步成型,炉料由下而上逐步加热、下降。
随自身热度的上升,炉料发生物理化学的变化,软熔带逐步成型、上移,炉内上部块状带发生炉料的预热、间接还原,炉料软熔、滴落后,铁水开始形成,铁水透过死焦堆下降至炉缸底部。
在开炉过程中软熔带的稳定成型是最关键的阶段,第一次出铁是否顺利直接关系开炉的快慢,由此,将开炉过程划分为三个阶段:
软熔带成型阶段、出渣出铁适应阶段及矿批、负荷加重阶段,由此明确开炉过程中各阶段的重点工作及定量化原则。
加风曲线是开炉技术的核心,因为其涉及炉缸初始煤气形态、热制度、开炉过程的快慢等,加风曲线确定后,实际风速可以通过掌握捅开风口的时机来控制,确保实际风速不过分偏离正常生产期间的范围,以形成稳定的风口回旋区、防止回旋区形状畸变。
软熔带形成前,炉内压差水平低,实际风速较正常水平偏高,软熔带开始形成后随着压差的提高,实际风速回落至正常水平以下,若软熔带成型后实际风速仍过分偏离正常范围,则必须对其进行控制,防止损坏风口等冷却设备。
高炉送风前期,炉内适当快速加风,软熔带成型期间,风量以稳定为主,第一次出铁后,较送风前期,加风幅度适当降低、加风间隔适当拉长,以实现在风量水平平稳上升过程中对炉内热制度的稳定控制。
开炉热制度的制定关系到能否对炉内进行充分的加热及是否因炉温过高造成炉前出铁工作困难,热制度涉及开炉料与加风曲线等因素,是多种因素综合作用的结果。
炉内送风后,焦炭燃烧产生的热量及风温带入炉内的热量对炉墙、死焦堆及料柱进行加热,加热至正常生产时的热度水平,随着炉内软熔带的最终成型,炉内上部块状料带的逐步升温加热,及上部块状带间接还原的正常进行,炉内热制度最终进入一个热度平稳阶段,这一阶段的标志就是顶温水平上升至一定水平后,上下波动但总体水平稳定,这一阶段大致在送风后加入的正常料经过预热、间接还原到达软熔带位置时出现,此后热制度进入稳定期,最终铁水温度由开炉料、风量水平及装料制度等因素决定。
为减少开炉过程中的影响因素,装料制度在开炉过程中尽量不予调整,这需要装料制度适度超前,既确保开炉过程中炉内上部两边开的煤气分布,也照顾风量水平接近正常时对煤气分布的控制,确保不出现气流、管道。
装料制度与正常生产的装料制度模式保持一致,避免开炉后对装料制度的大幅度调整影响高炉经济技术指标的快速提升,焦炭布料与正常生产完全一致,对矿石布料适当往中间环带集中,开炉后可以根据炉内煤气分布的实际表现,将矿石摊开,稳定煤气分布、提高煤气利用率。
根据停炉时间的长短等因素,装炉料中的正常料焦炭负荷可以适当偏低,以补充高炉送风后炉内温度场重建需要的热量,高炉装炉料中正常料焦炭负荷2.6、全炉焦比3.0t/t,但送风后加入的后续正常料,经历了在炉内上部的预热、间接还原,适当提高后续正常料的焦炭负荷是必要的,后续正常料的焦炭负荷基本决定了开炉过程中处于稳定期的热度水平。
开炉过程中捅开风口后要间隔一定的时间再加风,使该风口前的焦炭燃烧释放热量,形成稳定的回旋区,使堆积在风口前的渣铁渗透下去,加风的幅度不要太大,此时该风口上部的软熔带位置处于上移的过程,加风幅度太大易造成对软熔带的破坏,加风后要维持此风量一定的时间,使增大的炉腹煤气寻找合适的通路,使料柱的运动适应增大的炉腹煤气量。
开炉过程中的透气性指数与上部装料制度、下部热制度、渣铁在软熔带以下的滞留量、渗透能力等存在较强的相关性,随历次开炉条件的变化,开炉过程中的透气性指数可能存在差别,评价透气性指数是否合适的标准应该是炉内下料是否顺畅,压量关系是否平稳,不宜过分苛求透气性指数的大小。
1)软熔带的成型阶段。
高炉送风后,风口前堆积的焦炭被点燃,随着焦炭的燃烧,炉内从风口前开始,进行着热量的向外传递,逐步完成炉内温度场的重建,伴随着软熔带的形成、块状带的预热、炉缸死焦堆的初步加热等过程,其中软熔带成型是开炉的最关键阶段,能否在炉料与煤气的逆流运动中建立稳定的软熔带关系到开炉是否顺利。
利用经验定义软熔带开始成型的时间,软熔带在炉内的平均高度大致在炉腰与炉身交界处,正常料由炉身进入炉腰后,软熔带开始成型,以正常料下降进入炉腰的时间做为软熔带开始成型的时间,该时间通过耗风量可以计算得出。
同样,利用经验定义软熔带成型终了的时间,软熔带成型终了的标志就是炉顶温度开始明显爬升,此时炉内温度场重建基本完成,软熔带成型终了后,随着炉缸热度的增加继续上移,但变型幅度已经相对较小。
高炉开炉采用堵风口(送风风口数占总风口数的55%~65%)的方式,避免了开炉之后的再次停风,但对于开炉过程中软熔带的均匀成型是不利的。
高炉初始送风风量按风压0.55~0.65kg/cm2控制,防止送风初期压差过高将料柱顶住而无法下降,焦炭点燃、回旋区形成后,可以抓紧时机捅风口加风,在软熔带成型前尽量加大风量,一则可以加速软熔带的成型,二则伴随着风量的加大,必然需要及早捅开更多的风口,由此可以尽量减少软熔带的不均匀程度,高炉软熔带开始成型前风量达到全风水平的45%~50%。
在软熔带开始成型至成型终了阶段,风量以稳定为主、可适度小幅加风,防止风量的大幅度增加破坏软熔带的重建,软熔带重建完成至第一次出铁前可以适量加风。
2)出渣出铁的适应阶段。
铁水、炉渣能否顺利流出取决于:
一是铁水的物理热、[Si]%及炉渣的物理热、碱度、Al2O3%,这由开炉料所决定;二是铁水、炉渣下降过程中流经的死焦堆的热度,铁水、炉渣下降时是否会因为热量不足造成铁水、炉渣凝结,这由开炉料及死焦堆的受热方式所决定;三是铁口孔道大小、渣铁沟准备情况等炉前因素。
因此,按时出渣、出铁的关键还在于炉内的开炉料,炉前处于辅助地位。
开炉料中空焦内夹入正常料,使铁水能够及早生成、及早下降到铁口区,铁水凝固点低,可有效对炉缸死焦堆、铁口区加热,促使渣铁顺利下降到铁口区。
开炉料配加锰矿、萤石,保证铁水[Mn]%达到0.8%~1.0%,在正常料内配加硅石、灰石,提高渣铁比、降低炉渣Al2O3%至14.5%~15.0%,控制炉渣碱度在1.05,确保炉渣的良好流动能力。
降料面停炉时控制打水量,开炉前对炉缸死焦堆覆盖的压火料、喷涂反弹料、渣皮等进行清理,停风时间大于7天,清理炉缸死焦堆,降低炉缸的亏热状态。
铁口埋设吹氧枪,使铁口前焦炭燃烧,加热铁口区,有利于消除在铁口区渣铁的凝结。
这些措施都为开炉后第一次出铁的顺利奠定了基础。
高炉开炉过程中第一次出铁时间的确定至关重要,第一次出铁过早,没有一定的铁水下达到炉缸,并且开炉第一次出铁希望渣铁量尽量大些,使炉内料柱在铁后能更加松动,关键是渣铁量大有利于炉前出铁的组织。
炉内从软熔带成型开始,陆续有铁水的生成,但由于开炉前期风量水平较小,正常料移动进入软熔带区间的动作缓慢,第一次出铁的时间确定在软熔带成型后的5批料之后,这样炉缸积存了一定的铁水量,即使一定量的铁水滞留在死焦堆中,仍然有大量的铁水可以到达炉缸下部,经铁口排出。
3)矿批、负荷的加重阶段。
随着对高炉大修、中修开炉过程的不断深入研究与实践,高炉开炉过程呈现越来越快的趋势,但高炉开炉不只是炉内恢复至全风、重负荷的过程,更是磨合高炉系统设备,使高炉各部位消除热应力的过程,过短的开炉过程易使炭砖、冷却壁、炉壳等无法及时消除热应力,给高炉长寿埋下隐患,从历次高炉开炉经验看,48~56h的开炉进程对于中修开炉是适宜的,对于时间更长的停炉,开炉进程要相应延长,切不可盲目追求高炉的快速恢复,而给高炉长寿埋下隐患。
第一次出铁后,相比软熔带成型前的加风曲线,加风幅度适当降低、加风间隔适当拉长,加风间隔可按5~7h为一个风量稳定阶段的原则进行,以实现在风量水平上升过程中对炉内热制度的稳定控制。
在开炉过程中的矿批、负荷加重阶段,尽量保持稳定的焦炭层厚度,负荷的加重主要通过加重矿批的方式,矿批接近正常水平后,可减轻焦批、继续加重焦炭负荷,平均焦炭负荷加重幅度在0.3~0.4,平均间隔在5~7h,焦炭负荷加重幅度随着炉内负荷水平的加重而逐步减小,与加风相互间隔,防止因加风与加负荷同步造成的炉温波动幅度加大。
第一次出铁后,在炉内风量水平未达到全风量70%的情况下,铁次间隔按炉内下料批数组织,主要是考虑炉前工作的难度,尽量保持一定的铁水流量,风量达到全风量70%以后,可按正常间隔(25~30min)组织炉前出铁。
第一次出铁铁水物理热低,渣铁走残铁沟,待渣铁温度上升,渣铁能够进行分离后,渣铁走小坑进行分离,之后每次铁后捅小坑,防止小坑及大沟铸死,直至风量达到全风量的70%,出铁过程中防止渣铁沟结盖,铁后及时清理渣铁沟,确保按时出铁,不影响开炉进度。
开炉过程中铁水温度的控制是难点,随着装料制度中矿石布料的摊开,开炉第一次出铁的铁水物理热在1300℃以上;送风后装入的正常料在经过一个冶炼周期后产生的铁水物理热达到1400℃以上;在现有的开炉装料制度下,风量达到全风的80%、料速达到6批/小时后,铁水物理热达到1500℃以上。
但铁水[Si]%受加风曲线的影响较多,铁水[Si]%基本情况:
第一次出铁铁水[Si]%控制在1.5~2.0%;焦炭负荷3.0的炉料产生的铁水[Si]%控制在1.0%~1.5%,焦炭负荷3.5的炉料产生的铁水[Si]%控制在0.8~1.0%,焦炭负荷4.0的炉料产生的铁水[Si]%控制在0.6%~0.8%,随着焦炭负荷的加重,将铁水[Si]%降至0.4%~0.6%,并根据渣铁流动能力,适时停加锰矿、萤石。
2.2高炉量化开炉技术的操作要点
开炉过程三个阶段:
软熔带的成型阶段、出渣出铁的适应阶段及矿批、负荷的加重阶段。
1)软熔带的成型阶段。
定义正常料下降进入炉腰的时间为软熔带开始成型的时间,炉顶温度明显爬升至80℃的时间为软熔带成型终了的时间,两者之间的阶段为软熔带的成型阶段。
①高炉堵风口送风,堵风口数占总风口数的35%~45%,避免开炉之后再次停风,初始送风风量按风压0.55~0.65kg/cm2控制,焦炭点燃、回旋区形成后,捅风口加风,软熔带开始成型前风量达到全风水平的45%~50%。
②在软熔带开始成型至成型终了的时间段内,风量在全风水平的45%~50%。
2)出渣出铁的适应阶段。
软熔带成型终了后,炉内再下降5批料,进行第一次出铁,但第一次出铁时铁口都难开,适应第一次出铁的阶段为出渣出铁的适应阶段。
①开炉料中空焦内由上至下分别间隔2个、3个、5个空焦夹入3个正常料,使铁水能够及早生成、及早下降到铁口区。
②开炉料配加锰矿、萤石,铁水[Mn]%达到0.8%~1.0%,在正常料内配加硅石、灰石,提高渣铁比、降低炉渣Al2O3%至14.5%~15.0%,控制炉渣碱度在1.05,确保炉渣的良好流动能力。
③第一次出铁时,风量在全风水平的50%~55%,第一次出铁后,风量加到全风水平的60%~65%。
3)矿批、负荷的加重阶段。
矿批、负荷加重至正常水平(负荷4.5~5.0)的阶段为矿批、负荷的加重阶段。
①开炉进程为48~56h,不可盲目追求高炉的快速恢复而给高炉长寿埋下隐患。
②加风间隔按5~7h为一个风量稳定阶段进行,平均加风幅度为全风水平的5%~7%,以实现在风量水平上升过程中对炉内热制度的稳定控制。
③前期保持稳定的焦炭层厚度,负荷的加重主要通过加重矿批的方式,矿批达到正常水平后,减轻焦批、继续加重焦炭负荷,平均焦炭负荷加重幅度在0.3~0.4,平均间隔在5~7h,与加风相互间隔。
④第一次出铁后,在风量水平未达到全风量70%的情况下,铁次间隔按炉内下料批数(5批)组织,风量达到全风量70%以后,按正常间隔(25~30min)组织炉前出铁。
第一次出铁铁水物理热低,渣铁走残铁沟,待渣铁温度上升,渣铁能够进行分离后,渣铁走小坑进行分离。
⑤第一次出铁铁水[Si]%控制在1.5%~2.0%;焦炭负荷3.0的炉料产生的铁水[Si]%控制在1.0%~1.5%,焦炭负荷3.5的炉料产生的铁水[Si]%控制在0.8%~1.0%,焦炭负荷4.0的炉料产生的铁水[Si]%控制在0.6%~0.8%,随着焦炭负荷的加重,将铁水[Si]%降至0.4%~0.6%。
3高炉量化停开炉技术的应用方案
3.1高炉量化停炉技术的应用方案
2012年9月,首秦2号高炉降料面至风口带,停炉进行15天计划检修,对炉内炉喉钢瓦下沿至炉腹部位进行喷涂造衬。
停炉前,以停炉技术的定量化原则为基础,结合高炉停炉的具体条件,计算、规划了降料面停炉过程中各阶段的节点、控制原则,细化了降料面停炉过程的各项参数。
表1高炉降料面停炉定量化控制参数
风口至料线体积
1487m3
正常料批数
16批
吨燃耗风
2810m3/t
正常料产生的铁水量
368t
正常料的焦炭量
210t
第一次出铁时耗风量
18万m3
盖面焦的焦炭量
64t
软熔带消失时耗风量
77万m3
软熔带至风口的焦炭量
464t
停气时耗风量
149万m3
总焦炭量
738t
降料面总耗风量
207万m3
表2高炉降料面停炉定量化操作参数
项目
料线
m
风量m3/min
风温
℃
顶压
kg/cm2
耗风
万m3
耗时
h
正常料前期
1.4~10.0
3400
950
1.75
42
2.2
正常料后期
12.0~15.0
3050
900
1.56
32
1.8
焦炭料前期
12.9~15.3
2650
850
1.37
39
2.5
焦炭料中期
15.3~18.2
1900
850
0.98~0.25
44
2.8
焦炭量后期
18.2~22.1
1500
800
停气
50
5.7
3.2高炉量化开炉技术的应用方案
3.2.1软熔带成型阶段
1)软熔带成型标志。
以正常料下降进入炉腰的时间作为软熔带开始成型的时间,计算得出软熔带开始成型时间:
送风6h。
以炉顶温度显著爬升至80℃的时间作为软熔带成型终了的时间,此时炉内软熔带重建基本完成,之后,软熔带主要存在位置的上移。
2)加风原则。
①加风在料尺自由活动及压量关系平稳的前提下进行。
②风温用全(800~1000℃,≯1000℃),在软熔带开始成型前尽可能提高风量,加速焦炭燃烧,迅速提高炉内热度,促进软熔带的均匀成型。
③软熔带开始成型至软熔带成型终了期间,尽量维持压量关系的稳定,防止因风量水平突然大幅增加,破坏软熔带的均匀稳定成型。
④合理高风速,风速不宜偏离正常范围太多,避免过高风速导致风口回旋区畸变,炉缸初始煤气分布不均,软熔带难以均匀稳定成型。
⑤炉顶温度显著爬升至80℃,软熔带成型终了时,视情况,风温降至800~900℃。
3)加风步骤。
送风开16个风口,用放风阀控制,风压0.6kg/cm2左右,坚决控制≯0.8kg/cm2,风量1200m3/min。
送风4h,16个风口全亮,料尺自由活动,煤气成分取样合格后,将煤气引到干法除尘箱体入口阀前和荒煤气管道末端放散管。
送风5h,荒煤气管道末端温度达到45℃后给箱体送气。
送气手续完毕,风量逐步加至1600m3/min。
4)矿批、负荷调整。
送风2h,风量稳定在1200m3/min,矿批不动,负荷2.8t/t。
3.2.2出渣出铁适应阶段
1)出铁控制。
第一次出铁时间:
软熔带成型后生成的渣铁下达至炉缸,在风眼工作良好的情况下,第一次出铁的时间确定在软熔带成型终了的5批料之后,铁量80t左右,第一次出铁时间:
送风12h。
第一次出铁安排:
南场,走残铁眼。
视渣铁分离情况,临时定是否走小坑。
出铁间隔按计算铁量80吨组织。
2)加风原则。
①第一次出铁正常后可逐步加风。
②软熔带稳定成型后,高炉压差升高,送风后加入的正常料产生的渣铁下达炉缸后,炉温大幅转热,风速下降,控制风速在210~230m/s范围。
③加风在料尺自由活动及压量关系平稳前提下进行,每次加风幅度≯0.1kg/cm2,风量≯100m3/min,加风间隔≮0.5h。
3)加风步骤。
第一次出铁正常后,逐步加风至2200m3/min。
送风18h,捅开5#、18#风口(18个风口),逐步加风至2500m3/min。
4)矿批、负荷调整。
风量达到2200m3/min,加矿批2t(矿批25t),负荷3.0t/t。
风量达到2500m3/min,加矿批3t(矿批28t),负荷3.2t/t。
3.2.3矿批、负荷加重阶段
1)出铁控制。
风量稳定在2800m3/min以上,渣铁流动性良好,南、北场轮流出铁,出