8精馏岗位操作规程.docx
《8精馏岗位操作规程.docx》由会员分享,可在线阅读,更多相关《8精馏岗位操作规程.docx(19页珍藏版)》请在冰豆网上搜索。
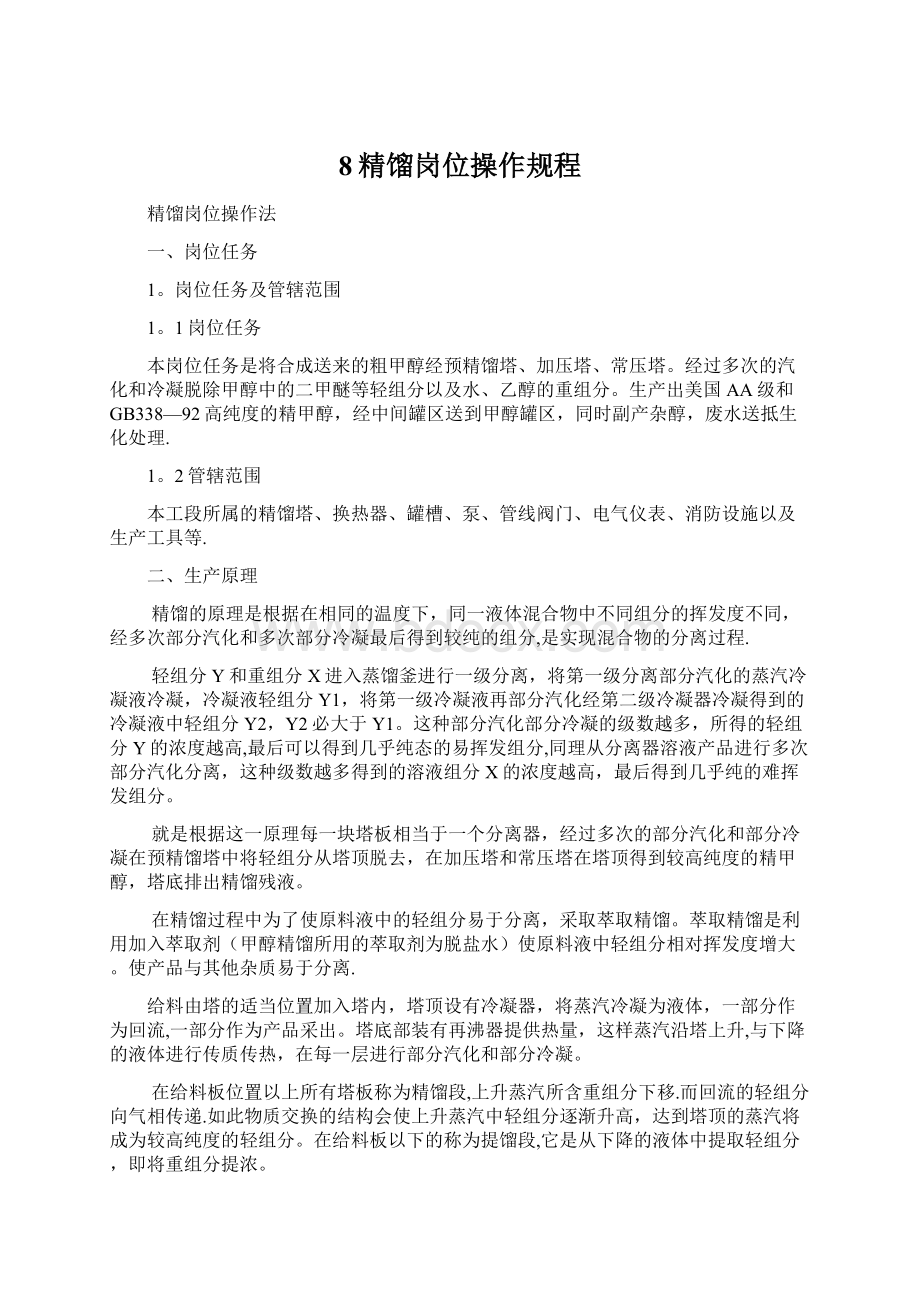
8精馏岗位操作规程
精馏岗位操作法
一、岗位任务
1。
岗位任务及管辖范围
1。
1岗位任务
本岗位任务是将合成送来的粗甲醇经预精馏塔、加压塔、常压塔。
经过多次的汽化和冷凝脱除甲醇中的二甲醚等轻组分以及水、乙醇的重组分。
生产出美国AA级和GB338—92高纯度的精甲醇,经中间罐区送到甲醇罐区,同时副产杂醇,废水送抵生化处理.
1。
2管辖范围
本工段所属的精馏塔、换热器、罐槽、泵、管线阀门、电气仪表、消防设施以及生产工具等.
二、生产原理
精馏的原理是根据在相同的温度下,同一液体混合物中不同组分的挥发度不同,经多次部分汽化和多次部分冷凝最后得到较纯的组分,是实现混合物的分离过程.
轻组分Y和重组分X进入蒸馏釜进行一级分离,将第一级分离部分汽化的蒸汽冷凝液冷凝,冷凝液轻组分Y1,将第一级冷凝液再部分汽化经第二级冷凝器冷凝得到的冷凝液中轻组分Y2,Y2必大于Y1。
这种部分汽化部分冷凝的级数越多,所得的轻组分Y的浓度越高,最后可以得到几乎纯态的易挥发组分,同理从分离器溶液产品进行多次部分汽化分离,这种级数越多得到的溶液组分X的浓度越高,最后得到几乎纯的难挥发组分。
就是根据这一原理每一块塔板相当于一个分离器,经过多次的部分汽化和部分冷凝在预精馏塔中将轻组分从塔顶脱去,在加压塔和常压塔在塔顶得到较高纯度的精甲醇,塔底排出精馏残液。
在精馏过程中为了使原料液中的轻组分易于分离,采取萃取精馏。
萃取精馏是利用加入萃取剂(甲醇精馏所用的萃取剂为脱盐水)使原料液中轻组分相对挥发度增大。
使产品与其他杂质易于分离.
给料由塔的适当位置加入塔内,塔顶设有冷凝器,将蒸汽冷凝为液体,一部分作为回流,一部分作为产品采出。
塔底部装有再沸器提供热量,这样蒸汽沿塔上升,与下降的液体进行传质传热,在每一层进行部分汽化和部分冷凝。
在给料板位置以上所有塔板称为精馏段,上升蒸汽所含重组分下移.而回流的轻组分向气相传递.如此物质交换的结构会使上升蒸汽中轻组分逐渐升高,达到塔顶的蒸汽将成为较高纯度的轻组分。
在给料板以下的称为提馏段,它是从下降的液体中提取轻组分,即将重组分提浓。
精馏塔的操作就是控制塔的物料平衡(F=D+W)。
热量平衡(Q入=Q出+Q损)和气液平衡Yi=KiXi。
根据塔的给料量,给塔釜一定的热量,建立热量平衡,随之达到一定的溶液平衡,然后用物料平衡为正常的调节手段,控制热量平衡和气液平衡的稳定。
三、工艺流程
来自甲醇合成的工段的粗甲醇,温度40℃,压力0。
5MPa,通过粗甲醇缓冲槽(F40501),流量为16766。
31㎏/h,经粗甲醇预热器(C40510)与来自加压塔回流罐的精甲醇进行换热达到60℃后进入预精馏塔(E40501).按照缓冲槽(F40501)的液位控制LICA-40501调节多余的粗甲醇进入粗甲醇贮槽(F40511)以做备用。
为中和产品中的少量有机酸,用固体NaOH在配碱槽(F40506)配制5﹪碱液,流至碱液槽(F40507),再用碱液泵(J40506)沿入口管线向预塔内加入碱液约25㎏/h。
控制塔釜内液体PH=8~9范围内。
从预塔(E40501)塔顶出来的气体温度75℃,压力0。
05MPa,经预塔冷凝器Ⅰ(C40502)和预塔冷凝器Ⅱ(C40503)用循环水分级冷凝后,温度降到40℃冷凝下来的液体收集在预塔回流槽(F40508)内,通过预塔回流泵(J40509)加压后从预塔进入预塔内,预塔再沸器的热源为0.5MPa的低压蒸汽。
预塔冷凝器Ⅱ(C40503)中不凝气、预塔(E40501)塔顶少量排放气和各塔顶部安全阀排放气体均通入排放槽(F40504)用软水吸收后送至40米高度放空.回收的甲醇自流入地下槽.经液下泵打入粗甲醇槽(F40511)从预塔底出来的脱除轻组分的预后甲醇,温度为85℃用预后泵(J40501)送入加压塔(E40502)加压精馏塔的操作压力为0。
6MPa,塔底热源为0.5MPa低压蒸汽加热的再沸器(C40504).使塔釜物料维持在134℃,从甲醇加压塔顶出口的蒸汽在常压塔再沸器(E40507)中冷凝,释放出的热量使塔釜温度达到121℃,用来加热常压塔(E40503)中的物料。
常压塔再沸器出口的精甲醇冷凝液进入加压塔回流槽(F40502),一部分由加压塔回流泵(J40502)经加压塔回流槽(F40502)流量控制(FIC40512)下送加压塔做回流;另一部分做为成品甲醇,成品甲醇首先经过粗甲醇预热器(C40510)冷却再经过精甲醇冷却器(C40505)冷却大约40℃送往精甲醇中间槽(F40510)。
控制加压塔的液面,使过剩产物在134℃下进入常压(E40503),常压塔(E40503)在107℃和0.03MPa压力条件下,由加压塔产物冷凝再沸。
离开常压塔顶的温度约为65℃,在常压塔顶冷凝器(C40506)中冷却到40℃后送到常压塔回流槽(F40503),在流量控制下再用常压塔回流泵(J40503)将回流液送至塔顶,回流液流量由流量计(FIC-40513)控制,其余部分作为精甲醇产品送至精甲醇中间贮槽(F40510)。
精甲醇经过分析合格后,通过精甲醇(J40507)送到成品罐区贮存.常压塔底的产物是残液,含有微量的甲醇和高沸物。
为防止高沸点杂醇混入到产品中,在常压(E40503)下塔有杂醇采出口,温度约为85℃,压力约为0.035MPa,经杂醇冷却器(C40509)冷却到40℃后靠静压送到杂醇贮(F40509),再通过杂醇泵(J40510)送到综合罐区。
从常压塔(E40503)底部排出的废水温度107℃,压力0.045MPa,甲醇含量≤0。
4%经残液冷却器(C40508)冷却到40℃由残液泵(J40504)送往水处理装置生化处理.
排放的污甲醇排到地下槽(F40505)经液下泵(J40505)送到粗甲醇贮槽(F40511).
开车或事故状态下,经分析精甲醇中间槽(F40510A/B)内不合格的精甲醇通过精甲醇泵(J40507A/B)送到粗甲醇贮槽(F40511)同时甲醇缓冲槽(F40501)的液位靠从粗甲醇贮槽(F40511)进出粗甲醇的流量来控制。
四、正常生产调节
生产时工艺调节原则:
精馏主要操作是维持系统的物料平衡、热量平衡和汽液平衡,物料平衡掌握的好,汽液接触得好,传质效率高。
塔的温度和压力是控制热量平衡的基础。
三者互相影响,因此,一切调节都必须缓慢的逐步的进行,在进行下一步调节前,必须待上一步调节显现效果后才能进行。
否则会使工况紊乱,调节困难达不到预期效果。
4.1给料量的调节
4。
1.1每次调节流量变化幅度小于1m3/h
4。
1.2当粗甲醇槽(F40511)液位下降较快时,要迅速查找原因,若因合成来料不足可减量生产。
4。
1。
3当进料含水多时,塔釜温度也较高但要用回流量和回流液温度等手段来保证E40502,E40503塔顶温度正常.
4.1。
4加减给料量的同时要向塔釜加减蒸汽量,应遵循以下原则:
4.1。
4.1预塔(E40501)加给料量时应先加蒸汽量后加给料量,减量时应先减给料量后减蒸汽量以保证轻组分脱除干净。
4。
1.4.2加压塔(E40502)常压塔(E40503)应先加给料量再加回流量后加蒸汽量.减量时应减蒸汽量再减给料量后减回流量。
这样才能保证两塔的塔顶产品质量.
4。
1。
5加减给料量时,碱液量也随之调整,保证塔底的PH=7~9。
4。
1.6随时注意合成工况及F40511的库存,有预见性的进行工况调节,控制好入料量是保证的前提,是稳定精馏操作的基础。
4。
2温度的调节
4。
2.1蒸汽量增大塔温上升,对重组分上移,影响甲醇的质量,同时蒸汽加入量过大,上升气速过快,有可能造成液泛,因此精馏塔升温应小于1℃/次
4.2。
2蒸汽量加入量减少,塔温下降,轻组份下移,对于预塔(E40501)来说可能将轻组分带到后面产品塔,造成产品的KMnO4试验和水溶性试验不合格。
4。
3回流的调节
当回流不足,塔温上升重组分上移,影响精甲醇的产品质量,这时就应减少采出,增加回流。
尤其是在产品质量不合格时应增大回流量.
4。
4压力调节
4.4.1压力对系统的影响非常大。
对E40501来讲压力增大,影响不凝气的排放,压力升高一方面对安全不利;另一方面,压力升高使不凝气不能顺利排放,带入下面几个塔,影响精甲醇的酸度和水溶性试验。
预塔塔顶控制在62~65℃,塔底温度为76~79℃,压力150KPa,回流比为25~30。
E40501压力控制可通过FV40509开启度,E40502、E40503冷却水量及再沸器C40501蒸汽加入量调节。
4。
4。
2对E40502来讲,压力若不足,塔顶甲醇蒸汽量下降,影响常压塔再沸器E40507的供热量,导致常压塔底温度下降,废水含量超标。
故加压塔塔顶控制在112~115℃,压力为550KPa,塔釜温度为127~130℃,压力为820KPa。
压力调节是通过E40502塔斧蒸汽加入量及PG40544、回流量的大小及温度来调节塔压.
4。
4。
3对常压塔E40503来讲,压力不足有可能引起负压,使设备受到损害;压力过高,使甲醇在塔底的分压增高,造成塔底废水水含量超标.常压塔塔顶温度保持在63~65℃,压力为常压,塔釜温度为112~115℃,压力为170KPa。
常压塔E40503的压力调节是通过C40506冷却水量、回流量、回流温度共同作用实现,一般常压塔回流比控制在2~3。
4。
5液位调节
4。
5.1塔釜液位给定太低,造成釜液蒸发过大,釜温升高,釜液停留时间较短,影响换热效果;塔釜液位给定太高,液位高至再沸器回流口,液相阻力增大,不仅会影响甲醇汽液的热循环,还容易造成液泛,导致传质、传热效果差.故各塔液位应保持在60%~90%.
4。
5。
2E40502、E40503回流槽液位,
开车初期,为了使生产出的不合格甲醇回流液尽快置换,回流槽液位可给定20%,分析产品合格后,液位在给定30%。
正常生产时,回流槽应有足够的合格甲醇以供回流及调节工况,回流槽给定30%,投自动。
当液位自动调节阀故障失灵时,应关闭前后切断阀,用旁路阀控制,现场液位应尽量稳定,同时通知仪表工处理。
五、开车前的准备
5。
1离心泵的开车
5.1。
1启动前的安全检查与停车
5。
1。
1.1确认泵护罩牢固
5。
1.1。
2手动盘车,转动灵活无摩擦声.
5。
1。
1。
3检查润滑油位和冷却水是否正常.
5。
1。
1。
4确认槽内液位正常,打开泵的入口阀。
5。
1.1.5对泵做排气处理。
5。
1.1。
6确认压力表根部阀打开.
5。
1.1.7打开泵的冲洗、密封水.
5。
1.2开泵
5。
1。
2。
1关闭泵的进出口倒淋阀。
5。
1.2。
2启动泵,观察泵轴转向无误。
5.1.2。
3待泵出口压力开压后,打开泵出口阀,调整压力指标。
5.1。
2。
4运行5分钟,待无异常现象方准离开,并记录开泵时间。
5。
1。
3停泵
5.1.3.1关闭泵出口阀。
5.1。
3。
2按下停泵按钮。
5.1.3。
3关泵入口阀。
5。
1。
3。
4排净泵内液体,关闭倒淋阀。
5。
1。
3。
5关闭密封水上水阀。
5.1。
4倒泵
按开泵步骤开启备用泵,泵运行正常后按停泵步骤停原运行泵,应注意两人配合,防止流量大幅度波动。
5。
2柱塞泵的开车
5。
2。
1启动前的安全检查及准备工作
5。
2.1.1确认泵防护罩完好.
5.2。
1.2检查润滑油位是否正常。
5。
2。
1.3检查打开压力表根部阀。
5。
2.1.4确认安全阀好用.
5.2。
1。
5检查槽内液位是否正常。
5。
2。
1.6将泵的行程调至最小。
5。
2。
2开泵
5。
2.2.1打开泵入口阀.
5.2。
2.2打开泵近路阀。
5。
2。
2.3启动泵.
5。
2。
2。
4打开泵出口阀。
5。
2.2。
5关闭泵近路阀。
5.2.2.6逐渐调大活塞行程,使泵流量达到正常。
5.2。
3停泵
5。
2.3。
1逐渐将活塞行程调至最小。
5.2.3。
2按下停车按钮。
5。
2。
3。
3关泵出口阀。
5.2。
4倒泵
5。
2。
4.1按正常开泵步骤开启备用泵。
5.2。
4.2将原运行泵的行程调小,同时将备用泵的行程调大。
5.2。
4。
3按正常停泵步骤停原运行泵。
5。
2.5离心泵运行时应注意的事项:
a)经常注意压力表、电流表的读数是否正常,发现异常情况应查明原因及时消除。
b)经常观察润滑油标,使油量保持在规定范围内,定期检查油质,发现有变化应立即按规定牌号及时更换.
c)经常观察润滑油,油封及冷却水的供应情况.发现情况及时处理。
d)经常检查离心泵和电动机地脚螺栓的紧固情况,泵体和轴泵的温度及泵运行时的声音等。
e)对结构复杂和自动化程度较高的离心泵必须按有关的操作规程进行启动、维护和停车,在没有科学根据和经过实验证明之前,不得随便改变操作方法。
5。
3离心泵常见故障及处理方法
序号
故障现象
原因分析
处理方法
1
泵不起压
1、泵内有空气
2、旋转方向不对
3、入口压头过低
1、排气
2、调整旋转方向
3、降低安装高度
2
流量不足
1、吸入式排出阻力过大
2、叶轮阻塞
3、泵漏气
1、疏通吸入排出管
2、清理叶轮
3、加强泵体密封
3
电流过大
1、填料压的过紧
2、流量过大
3、轴承损坏
1、松填料压盖
2、减小流量
3、更换轴承
4
轴承过热
1、泵与电机轴承不同心
2、轴承缺油
3、转速过高
4、流量过大
5、断冷却水
1、调整同心度
2、补油
3、降低转速
4、减少流量
5、加冷却水
5
泵体震动
1、地脚螺栓松动
2、泵与电机轴承不同心
3、泵汽蚀
4、叶轮损坏严重
1、拧紧地脚螺栓
2、调整同心度
3、降低物料温度
4、更换叶轮
6
流量波动
1、入口滤网不畅
2、介质温度过高
3、槽液位太低
1、清理滤网
2、降低介质温度
3、向槽内补液或停泵
7
泵内异常响声
1、泵内有异物
2、汽蚀
3、泵漏气
1、拆检,清理异物
2、降低介质温度
3、加强密封
六、开车步骤
6.1原始开车准备
开车前,整个系统根据要求均需化学处理:
一是金属表面钝化,除去金属表面上有催化活性作用的金属粒子的活性。
二是脱脂,脱除塔、换热器、槽、罐及其它精馏设备上的防锈油,以免它污染产品或在低温下凝结在塔内件上影响塔板效率和正常操作.三是杀灭余留活性中心,如果不将其活性杀灭,投料后聚合垢会很快生产,运行周期会大幅缩短。
系统清洗结束后,如有可能,再用水作介质对有关的泵、调节阀和切断阀做试运行,并对流量计、液位计等仪表进行校验.
在试运行时,应反复清洗泵入口侧的过滤器,以防异物进入泵体,损坏叶轮,还应注意观察贮罐液位,避免泵抽空.
6。
2原始开车
(1)煮塔
在已做好开车前的准备工作,系统已经经过清洗并已作过试运行的情况下煮塔。
向预塔回流槽(F40508)、加压塔回流槽(F40502)、常压塔回流槽(F40503)加软水液位在90%左右(留有配碱空间).向槽内加药,配制煮塔溶液,配制标准如下:
水(m3):
1
NaOH(㎏):
2~3
Na3PO4.12H2O(㎏):
2~3
配制好溶液搅拌均匀启动回流泵向塔内加料,塔釜液位50﹪停回流泵,开冷却水,开再沸器蒸气缓慢加温,三塔关闭采出,当塔釜液位开始下降,启动回流泵向塔内打循环,,加压塔压力控制在0。
35~0。
4MPa,其余两塔常压操作,热水循环过程中检查各塔采出排放是否畅通,加热循环36小时,后排放,排放液通过临时管线引到合成东侧地沟。
向回流槽加清水用回流泵向塔内打水清洗,直到排放水颜色和入口水相同为止。
(2)系统置换
如不及时投料,则应排净塔全部积水,然后再充如入氮气置换整个系统,直至取样分析气体中的氧气≤0。
5﹪为止.置换以后,应保证精甲醇采出管线、精甲醇贮槽、粗甲醇贮槽及其他有关的管线内均无积水。
置换过程中,应特别小心,控制系统压力不得超过操作压力,而且升降压也不能过快,以免损坏塔板。
6。
3开车准备工作
(1)检查设备具备开车条件,并联系电气、仪表人员检查所有电器、仪表具备开车条件、各泵送电、盘车、试车,工艺配合各调节阀调试完毕。
(2)系统试气密合格,氮气置换合格氧气≤0。
5﹪。
(3)工艺检查循环水、脱盐水、0。
5MPa低压蒸汽、氮气等接至界区并具备开车条件。
(4)关闭各塔、槽、泵、管道导淋及低点放净,关闭各放空阀、取样阀、各氮气充压阀。
(5)打开各压力表的根部阀,检查压力表、温度表完好。
(6)打开C40502、C40503、C40506、C40508、C40509、上水回水阀,并调整好开度.
(7)打开各调节阀流量表前后切断阀,关闭付线阀、控制室人员将阀位手动打至关闭位置.
(8)碱液槽配置好碱液,排放槽建立30﹪液位。
(9)检查关闭合成直接进料阀和进料总阀,冷凝液总阀。
(10)F40511接受合成来的粗甲醇、且达10﹪~15﹪液位.
6。
4开车
6。
4。
1预塔开车
接受合成来的粗甲醇,启动粗甲醇泵J40508经流量计FIC40506向预塔进料。
启动碱泵(J40506)向塔(E40501)加碱液使塔釜PH=7~9.当E40501液面达到50﹪时控制进料,先将C40501暖管控制人员缓慢通入蒸汽升温。
应加强联系注意配合,保持LICA40503液位稳定,并在80﹪投自动.将C40501投入使用.当塔压力上升时将PIC40506投自动将不凝气经过排放槽高空排放。
当预塔回流槽液位达30﹪时,开启预塔回流泵(J40509)向塔内打回流。
在液位30﹪时将LICA40507投自动,根据回流液的温度调节C40502,C40503,的冷却水流量,控制回流比25~30﹪.
6.4.2加压塔开车及常压塔开车
加压塔(E40502)必须和常压塔(E40503)同时开车.这样加压塔顶蒸汽才能冷却常压塔的再沸器才能有热源。
当预塔建立正常的回流后开启预塔给料泵(J40501)向加压塔进料,当液位建立50﹪时缓慢打开再沸器(C40504)蒸汽,将再沸器(C40504)投入使用,加压塔(E40502)塔底缓慢升温并将液位到达80﹪时投自动,建立常压塔液位,待常压塔液位达80﹪时投自动,从常压塔排出的残液不能送往生化,应送至地下槽(F40505).当地下槽液位达到80﹪时开液下泵,保持液位在30﹪~60﹪。
此时应调整各塔的进料量,保持各塔液位稳定,忌顾此失彼,稳定原则,从前到后,逐步稳定。
调整加压塔压力0.55MPa。
塔釜温度132℃,待加压塔回流槽建立30﹪液位启动加压塔回流泵(J40502)将冷凝液全部回流到塔顶.当液位超出设计值时采出甲醇到粗甲醇槽(F40511).当S40509分析两次合格后,加压塔采出产品到精甲醇槽(F40510)。
常压塔回流槽液位30﹪时启动常压塔回流泵.向塔内打回流,当液位超出设计值时,采出塔顶产品到粗甲醇贮槽,当S40510取样两次分析合格后,采出精甲醇到精甲醇贮槽(F40510)。
七、停车步骤
7。
1长期停车
当接到车间停车的指令后,停止向预塔进料,停碱液泵,关闭入粗甲醇预热器总阀。
停止加压塔、常压塔的采出,将塔顶采出切换到粗甲醇槽(F40511).关闭预再沸器(C40501)加压塔再沸器(C40504)的蒸汽总阀,视情况各阀打到手动位置,各塔进行充氮气保护,待各回流槽无液位时停回流泵,注意加压塔回流泵不得抽空。
手动控制预塔、加压塔、常压塔采出当预塔液面到5﹪~10﹪.加压塔、常压塔液面为0后。
各塔、回流槽打开导淋排放,通过低点导淋排放到地下槽(F40505)由液下泵打到粗甲醇贮槽.关闭塔入料和采出阀,充氮气保护,不得出现负压。
关闭循环水总阀,视综合罐区情况停精甲醇泵,视合成情况停止接收粗甲醇.
7。
2短期停车
停止预塔进料,关入工段总阀,将塔的采出切换到粗甲醇槽,停蒸汽阀,停止三塔的采出,停各泵,各塔、回流槽保持液位充氮气保压.
7。
3紧急停车
遇到爆炸着火,管道断裂,设备损坏严重,造成跑液漏气情况严重,人不能近前处理,或断水、断电、断蒸汽、断循环水、断仪表空气,应做紧急停车处理。
立即切断蒸汽入口阀,立即停泵,停各塔的采出,关闭各调压阀前后阀门。
迅速查明原因,或进行有效隔离防止事故的扩大或蔓延,各塔保持正压.
八、生产中不正常情况的判断及处理
现象
原因
处理方法
所有泵停车
停电
按紧急停车步骤处理
各塔超温,安全阀起跳
断循环水
按紧急停车步骤处理,
并联系相关工段
各塔温塔压陡降,塔釜液位陡升
断蒸汽
按紧急停车处理,联系锅炉.
各自调阀失灵,按气开、气闭动作
断仪表空气
将阀前阀后切断,手动操作或按紧急停车处理
塔釜温升高,压力上升,采出含水量增高
再沸器漏
无法正常生产,
按正常停车处理,检修
塔顶馏分不合格塔压超高釜液减少,回流槽液位上涨
进入液泛区
减少蒸汽量、加大回流、
加大采出,逐步调节
九、主要设备
序号
设备名称
规格型号
1
杂醇冷却器
换热面积:
4.3m2折流板间距:
23mm
设计压力:
管侧0.39MPa壳侧0.35MPa
最高工作压力:
管侧0.39MPa壳侧0。
04MPa
设计温度:
管侧60℃壳侧110℃
介质:
管侧冷却水壳侧杂醇
2
残液冷凝器
容器重量:
1710kg换热面积:
47。
8m2
折流板间距:
250mm
设计压力:
管侧0。
44MPa壳侧0.385MPa
最高工作压力:
管侧0。
4MP壳侧0.35MPa
设计温度:
管侧125℃壳侧50℃
介质:
管侧甲醇残壳侧冷却水
3
预塔冷凝器Ⅰ
容器重量:
3885kg换热面积:
120m2折流板间距:
300mm
设计压力:
管侧0.385MPa壳侧0。
055MPa
最高工作压力:
管侧0.35MPa壳侧0。
05MPa设计温度:
管侧50℃壳侧90℃
介质:
管侧冷却水壳侧甲醇
4
预塔冷凝器Ⅱ
容器重量:
780kg换热面积:
22。
5m2
折流板间距:
300mm
设计压力:
管侧0。
385MPa壳侧0。
03MPa
最高工作压力:
管侧0.35MPa壳侧0。
05MPa
设计温度:
管侧50℃壳侧70℃
介质:
管侧冷却水壳侧不凝气甲醇溶液
5
粗甲预热器
容器重量:
6280kg换热面积:
221m2折流板间距:
500mm
设计压力:
管侧0。
495MPa壳侧0.605MPa
最高工作压力:
管侧0。
45MPa壳侧0.55MPa
设计温度:
管侧80℃壳侧140℃
介质:
管侧粗甲醇壳侧精甲醇
6
常压塔冷凝器
容器重量:
13540kg换热面积:
501m2
折流板间距:
500mm
设计压力:
管侧0.39MPa壳侧0。
033MPa
最高工作压力:
管侧0.35MPa壳侧0。
03MPa
设计温度:
管侧60℃壳侧80℃
介质:
管侧冷却水壳侧甲醇蒸气/甲醇溶液
7
精甲冷却器
容器重量:
13572kg换热面积:
120。
7m2
折流板间距:
300mm
设计压力:
管侧0。
39MPa壳侧0.61MPa
最高工作压力:
管侧0.35MPa壳侧0。
55MPa
设计温度:
管侧60℃壳侧135℃
8
常