必学金属材料热处理轧制原理基本理论知识.docx
《必学金属材料热处理轧制原理基本理论知识.docx》由会员分享,可在线阅读,更多相关《必学金属材料热处理轧制原理基本理论知识.docx(60页珍藏版)》请在冰豆网上搜索。
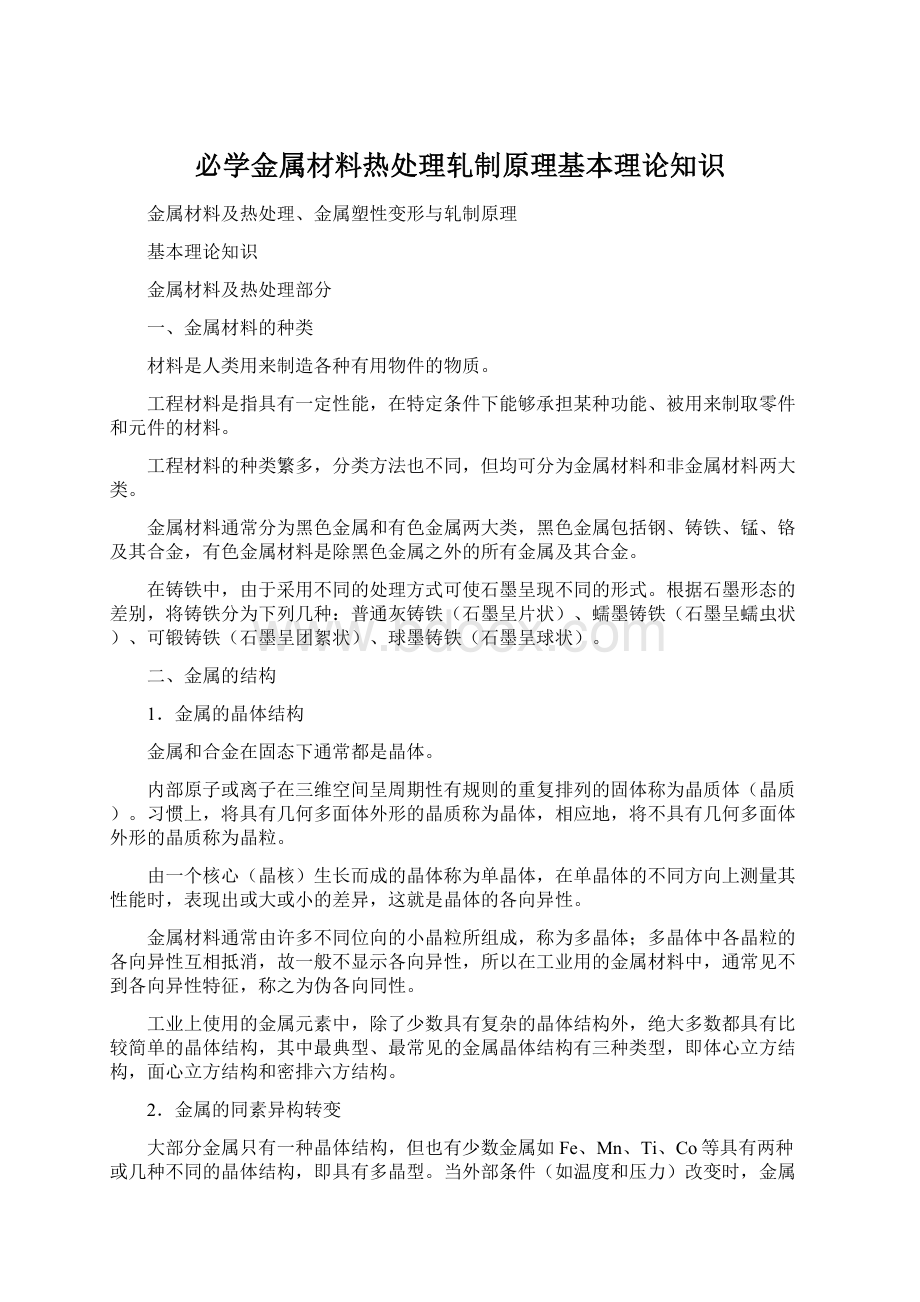
必学金属材料热处理轧制原理基本理论知识
金属材料及热处理、金属塑性变形与轧制原理
基本理论知识
金属材料及热处理部分
一、金属材料的种类
材料是人类用来制造各种有用物件的物质。
工程材料是指具有一定性能,在特定条件下能够承担某种功能、被用来制取零件和元件的材料。
工程材料的种类繁多,分类方法也不同,但均可分为金属材料和非金属材料两大类。
金属材料通常分为黑色金属和有色金属两大类,黑色金属包括钢、铸铁、锰、铬及其合金,有色金属材料是除黑色金属之外的所有金属及其合金。
在铸铁中,由于采用不同的处理方式可使石墨呈现不同的形式。
根据石墨形态的差别,将铸铁分为下列几种:
普通灰铸铁(石墨呈片状)、蠕墨铸铁(石墨呈蠕虫状)、可锻铸铁(石墨呈团絮状)、球墨铸铁(石墨呈球状)。
二、金属的结构
1.金属的晶体结构
金属和合金在固态下通常都是晶体。
内部原子或离子在三维空间呈周期性有规则的重复排列的固体称为晶质体(晶质)。
习惯上,将具有几何多面体外形的晶质称为晶体,相应地,将不具有几何多面体外形的晶质称为晶粒。
由一个核心(晶核)生长而成的晶体称为单晶体,在单晶体的不同方向上测量其性能时,表现出或大或小的差异,这就是晶体的各向异性。
金属材料通常由许多不同位向的小晶粒所组成,称为多晶体;多晶体中各晶粒的各向异性互相抵消,故一般不显示各向异性,所以在工业用的金属材料中,通常见不到各向异性特征,称之为伪各向同性。
工业上使用的金属元素中,除了少数具有复杂的晶体结构外,绝大多数都具有比较简单的晶体结构,其中最典型、最常见的金属晶体结构有三种类型,即体心立方结构,面心立方结构和密排六方结构。
2.金属的同素异构转变
大部分金属只有一种晶体结构,但也有少数金属如Fe、Mn、Ti、Co等具有两种或几种不同的晶体结构,即具有多晶型。
当外部条件(如温度和压力)改变时,金属可能由一种晶体结构转变成另一种晶体结构。
这种固态金属在不同温度下具有不同晶格的现象称为多晶型性或同素异晶性。
固态金属在一定温度下,其原子排列由一种晶格转变为另一种晶格的过程,称为多晶型转变,也称同素异晶(构)转变。
同素异晶(构)转变的产物称为同素异晶(构)体。
如纯铁的同素异构转变:
由于不同的晶体结构具有不同的致密度,因而发生同素异构转变时,必然引起体积和比容的变化,同时还会引起其它性能的变化。
3.实际金属的晶体结构
在实际应用的金属材料中,不但在结构上是多晶体,而且晶体内部总是不可避免地存在着一些原子偏离规则排列的不完整性区域,这就是晶体缺陷。
根据晶体缺陷的几何形态特征,可以将它们分为:
点缺陷、线缺陷和面缺陷三类。
三、金属材料的性能
金属材料的性能与其化学成分、内部组织结构之间有着极其密切的关系。
金属材料的性能可以大致分为:
使用性能和工艺性能。
金属材料的使用性能是指为保证机械零件或工具正常工作,材料应具备的性能,它包括力学性能(也称机械性能)、物理性能和化学性能等。
使用性能决定了材料的应用范围、安全可靠性与使用寿命。
金属材料在加工或使用过程中,都是要承受外力作用的,当外力超过某一限度时,金属就会发生变形,甚至断裂。
作用在金属材料上的外力也叫作载荷。
根据载荷的性质可分为静载荷、冲击载荷和交变载荷等。
金属抵抗外力作用的能力,称为力学性能,或者说金属材料的力学性能是指材料在外加载荷作用时所表现出来的性能。
常用的力学性能指标有:
强度、塑性、硬度、冲击韧性、疲劳强度等。
工艺性能是指在制造机械零件或工具的过程中,金属材料适应各种冷热加工的性能,它包括铸造性能、压力加工性能、焊接性能、切削加工性能以及热处理性能等。
1.强度和塑性
金属受到载荷作用后,其变形和破坏过程一般是:
弹性变形→弹性变形加塑性变形→断裂。
弹性变形是指载荷全部卸除后,可完全恢复的变形;塑性变形是指在载荷去除后,材料中仍残留下来的永久变形。
强度是指金属材料在静载荷作用下,抵抗永久变形和断裂的能力。
由于载荷的作用方式有拉伸、压缩、弯曲、剪切等形式,所以强度也分为抗拉强度、抗压强度、抗弯强度、抗剪强度等。
手册与规范上所标出的材料的强度一般都是通过金属拉伸试验来测定。
塑性是指金属材料在断裂前发生永久变形的能力,通常用金属断裂时的最大相对塑性变形来表示。
金属的塑性指标也是通过拉伸试验测得的。
图1所示为低碳钢拉伸试验时记录的拉伸曲线(力-延伸曲线)。
由图可见,当载荷不大于FP时,拉伸曲线OP为一直线,即试样的延伸与载荷成正比关系,试样处于符合虎克定律的弹性变形(弹性延伸或比例延伸)阶段,当载荷大于Fp而小于Fs时,试样的延伸与载荷已不再成正比关系,拉伸曲线不成直线,但试样仍处于弹性变形阶段,即这时如果去除载荷,试样便恢复原状。
图1拉伸曲线图
载荷超过Fs后,除弹性延伸外,试样开始产生塑性延伸变形。
当载荷达到Fe时,在拉伸曲线上出现水平或锯齿形的线段,这表明在载荷不增加甚至减少的情况下,试样仍继续变形,这种现象称为“屈服”。
屈服现象过后,延伸量又随载荷的增加而逐渐增大,整个试样发生均匀而显著的塑性变形。
当载荷增加到某一最大值Fm(最大力)后,试样的局部截面开始急剧缩小,出现了“颈缩”现象。
以后的变形主要集中在颈缩部分。
由于颈部附近试样截面积急剧减小,载荷也逐渐降低。
当达到Fk时,试样在颈缩处断裂。
工业上使用的金属材料,多数是没有屈服现象的,其拉伸曲线如图1b、c所示。
图中b是塑性材料的拉伸曲线,如退火铝合金、调质处理的合金钢等;c图是低塑性材料的拉伸曲线图,它没有屈服现象,也不产生缩颈,断裂前载荷并不减小,如高碳钢、某些合金钢、球墨铸铁等。
1)强度指标
根据拉伸曲线上各特殊点的载荷与试样原横截面积的关系,可以测得材料的强度指标。
金属材料的强度,常用应力来表示。
材料在受力F作用时,材料内部产生同等大小的抵抗力(称为内力)。
材料单位横截面积上的内力称为应力,即:
式中R——应力,N/mm2,1N/mm2=1MPa;
F——材料内部产生的内力,一般与外力大小相等,可用外力代替,N;
S——受力面积,mm2。
(1)屈服强度(Re)——旧标准中用“屈服极限
”表示
屈服强度是指当金属材料呈现屈服现象时,在试验期间发生塑性变形而力不增加时的应力。
对于拉伸试验时有明显屈服现象(呈现不连续屈服)的金属材料,其屈服强度包括上屈服强度(ReH)和下屈服强度(ReL),如图2所示。
图2不同类型曲线上的上屈服强度(ReH)和下屈服强度(ReL)
A.上屈服强度(ReH)
上屈服强度是试样发生屈服而力首次下降前的最高应力,其值等于试样发生屈服而力首次下降前的最高试验力与试样原始横截面积之比。
式中FeH——试样发生屈服而力首次下降前的最高试验力,N。
B.下屈服强度(ReL)
下屈服强度是在屈服期间不计初始瞬时效应时的最低应力,其值等于试样屈服期间不计初始瞬时效应时的最低试验力与试样原始横截面积之比。
式中FeL——试样屈服期间不计初始瞬时效应时的最低试验力,N。
(2)抗拉强度(Rm)——旧标准中用“
”表示
抗拉强度是与最大力(Fm)相对应的应力。
式中Fm——试样在拉断前所承受的最大试验力。
抗拉强度是材料对最大均匀变形的抵抗能力,是材料在拉伸条件下所能承受的最大应力值,它是设计和选材的主要依据之一,也是材料的重要机械性能指标。
2)塑性指标
衡量金属塑性好坏的主要指标是断后伸长率和断面收缩率,金属的断后伸长率和断面收缩率越大,其塑性越好。
(1)断后伸长率(A)——旧标准中用“延伸率或伸长率δ”表示
试样在拉断后,其标距部分内所增加的长度与原始标距长度之比的百分率称为断后伸长率。
式中L0——试样原始标距;
Lu——拉断后试样标距。
(2)断面收缩率(Z)——旧标准中用“ψ”表示
试样在拉断后,其断裂处横截面积的缩减量与原始横截面积的比值的百分率称为断面收缩率。
式中Su——试样断裂后的最小横截面积。
2.硬度
硬度是衡量金属材料软硬程度的一种性能指标,在金属材料制成的半成品或成品的质量检验中,硬度是标志产品质量的重要依据。
硬度的试验方法很多,基本可分为压入法和刻划法两大类。
在压入法中,根据加载速度不同又可分为静载压入法和动载压入法(弹性回跳法)。
在静载压入法中根据载荷、压头和表示方法的不同,又分为布氏硬度、洛氏硬度、维氏硬度和显微硬度等多种。
同一种材料用不同的试验方法测得的硬度值是不同的,但可进行换算。
硬度值的物理意义随试验方法的不同而不同。
例如,压入法的硬度值是金属材料抵抗更硬物体压入其表面的能力,也可以说是金属表面抵抗变形的能力;刻划法的硬度值表示金属表面抵抗局部断裂的能力;而回跳法硬度值则代表金属弹性变形功的大小。
因此,硬度值实际上不是一个单纯的物理量,它是表征材料的弹性、塑性、形变强化、强度和韧性等一系列不同物理量组合的一种综合性指标。
一般认为硬度是金属表面抵抗局部压入变形或刻划破裂的能力。
生产上常用的硬度测量方法是压入法。
因为它能测量所有金属材料的硬度,而且设备简单、操作方便、迅速,不损坏工件,适于成批检验,还可在一定条件下根据硬度大致推算出材料的强度值。
1)布氏硬度
布氏硬度试验是在规定试验力F的作用下,将一个直径为D的硬质合金球压入被测试件表面,并停留一定时间,使塑性变形稳定后,再卸除试验力,测量被测试金属表面上所形成的压痕直径d,以压痕的单位面积所承受的平均试验力作为被测试金属的布氏硬度值,用符号HBW表示。
当所加试验力F和硬质合金球直径D选定后,硬度值只与压痕直径d有关。
d越大,说明金属材料对压痕的抵抗力越低,即布氏硬度值越小,材料越软;反之,d越小,布氏硬度值越大,材料越硬。
2)洛氏硬度
洛氏硬度试验法是目前工厂中应用最广泛的试验方法之一。
和布氏硬度一样,也是一种压入硬度试验。
试验时,将压头在规定的试验力作用下分两步压入被测金属表面,经规定保持时间后,卸除主试验力,测量在初试验力下压痕残余深度h,以此残余压痕深度来表示硬度的高低。
普通洛氏硬度试验时使用金刚石圆锥和1.5875mm、3.175mm球三种压头,采用的试验力有60kg、100kg、150kg三种,它们共有九种组合,对应于洛氏硬度的九个标尺;表面洛氏硬度试验时使用120°金刚石圆锥和1.5875mm硬质合金球两种,采用15kg、30kg、45kg三种试验力,共有六种组合,对应于表面洛氏硬度的六个标尺。
洛氏硬度试验法的优点是操作简便、迅速,压痕较小故可在工件表面或较簿的金属上进行试验,并适用于大量生产中的成品检查,测试的硬度范围大,适于各种软、硬材料。
但是,因为压痕小,对于内部组织和硬度不均匀的材料,硬度值波动较大。
3)维氏硬度
维氏硬度试验是将一个顶角为136°的金刚石正四棱锥压头,在规定试验力作用下,压入试件表面,保持一定时间后卸除试验力,然后根据压痕对角线长度来确定试件硬度。
所得的硬度值用符号HV表示。
3.冲击性能
以很大速度作用于工件上的载荷称为冲击载荷。
许多机器零件在工作时都要受到冲击载荷的作用,如火车的起动、刹车以及速度突然改变时,都会受到冲击,刹车愈猛、起动愈猛,冲击力也就越大。
还有一些机械本身就是利用冲击能量来工作的,如锻锤、冲床、凿岩机、铆钉枪等。
制造这类零件所用的材料不能单用在静载荷作用下的指标来衡量,而必须考虑材料抵抗冲击载荷的能力。
金属材料的冲击性能通过夏比摆锤冲击试验来测定。
GB/T229-1984中规定衡量材料冲击性能的另一指标是冲击韧度(冲击韧性)ak,按GB/T10623-89《金属材料力学性能试验术语》的解释,冲击韧度是试样缺口底部单位横截面积上的冲击吸收功,单位为J/cm2。
现行标准中已不再提及该指标。
4.疲劳
许多机械零件如轴、齿轮、弹簧、滚动轴承、轧辊等都是在重复或交变应力作用下工作的。
所谓重复应力,是指材料所受的应力只是量的变化,即由小变大,再由大变小;所谓交变应力,是指材料所受的应力的大小和方向随时间作周期性变化。
承受重复或交变应力的零件,在工作过程中,往往在工作应力低于其屈服强度的情况下发生断裂。
这种断裂称为疲劳断裂。
疲劳断裂与静载荷作用下的断裂不同,无论是脆性材料还是韧性材料,疲劳断裂都是突然发生的,事先没有明显的塑性变形,很难事先观察到,因此具有很大的危险性,常常造成严重的事故。
疲劳断裂是一个裂纹发生和发展的过程,由于材料质量或加工过程中造成的缺陷(裂纹、夹杂、划痕等),在局部造成应力集中,超过屈服强度而形成微裂纹。
在重复或交变应力作用下,这些裂纹不断扩展,使材料承受载荷的有效面积不断减小,当减小到不能承受外加载荷作用时,便产生突然断裂。
大量实验证明,金属材料所受的最大交变应力越大,则断裂前所经受的应力循环次数N(疲劳寿命)越少;反之,最大交变应力越小,疲劳寿命N越大。
疲劳强度是指材料在无限多次交变载荷作用而不会产生破坏的最大应力,称为疲劳强度或疲劳极限。
5.金属材料的物理性能
金属材料的物理性能是指金属材料在重力、温度、电磁等物理作用下表现出的性能,包括密度、熔点、导电性、导热性、热膨胀性和导磁性等。
6.全属材料的化学性能
金属材料的化学性能是指金属材料抵抗周围介质侵蚀的能力,包括耐腐蚀性和热稳定性等。
耐腐蚀性是指金属材料在常温下,抵抗周围介质(氧气、水蒸汽及其它化学介质)侵蚀的能力。
7.金属材料的工艺性能
工艺性能是指零件制造过程中各种冷热加工工艺对材料性能的要求,它包括铸造性能、压力加工性能、焊接性能、切削加工性能和热处理性能等。
金属材料的工艺性能对于保证产品质量、降低成本、提高生产效率有着重大的作用。
四、纯金属的结晶
金属由液态转变为固态的过程称为凝固,由于凝固后的固态金属通常是晶体,所以又将这一转变过程称之为结晶。
无论是非金属还是金属,在结晶时均遵循着相同的规律,即结晶过程是形核与长大的过程。
当液态金属过冷至理论结晶温度以下的实际结晶温度时,晶核并未立即出生,而是经过一定时间后才开始出现第一批晶核。
结晶开始前的这段停留时间称为孕育期。
随着时间的推移,已形成的晶核不断长大;与此同时,液态金属中又产生第二批晶核,依次类推,原有的晶核不断长大,同时又不断产生新的第三批、第四批…晶核,就这样液态金属中不断形核,不断长大,使液态金属越来越少,直到各个晶粒相互接触,液态金属耗尽,结晶过程便告结束。
由一个晶核长成的小晶体,就是一个晶粒。
晶粒的大小对金属的机械性能有很大的影响。
一般在常温下,金属的晶粒越细小,强度和硬度越高,同时塑性韧性也越好。
细化晶粒对于提高金属材料的常温机械性能作用很大,这种通过细化晶粒来提高材料强度的方法称为细晶强化。
五、二元合金的相结构
1.合金
合金是指由两种或两种以上的金属或金属与非金属组成的具有金属特性的物质,如黄铜是由铜和锌组成的合金、钢铁是由铁和碳组成的合金。
合金具有较高的强度、硬度及某些优异的物理化学性能和工艺性能,而且价格低廉,所以它比纯金属得到了更广泛的应用。
2.组元
组成合金最基本的、独立的物质叫做组元,简称为元。
一般说来,组元就是组成合金的元素,但也可以是稳定的化合物。
例如,黄铜的组元是铜和锌,青铜的组元是铜和锡,碳钢的组元是铁和碳或者是铁和金属化合物(Fe3C)。
3.相
合金中具有相同的结构、成分和性能,并以界面相互分开的组成部分称为相。
如纯金属在固态时为一个相(固相),在熔点以上为另一个相(液相),在熔点时为固液两相共存,两相之间有界面(相界)分开。
又如铁碳合金在常温时的组成相有两个:
铁素体相和渗碳体相。
由一种固相组成的合金称为单相合金,由几种不同固相组成的合金称为多相合金。
4.组织
合金的组织为合金中相的综合,即合金中不同形状、大小、数量和分布的相,相互组合而成的综合体,或说组织就是相的机械混合物。
如含碳0.77%的铁碳合金经缓慢冷却到室温时,其组织为铁素体相和Fe3C相组成的两相组织,称为珠光体组织。
5.固溶体
一种组元均匀地溶解在另一组元中而形成的均匀固相称为固溶体。
形成固溶体时,由于溶剂晶格发生畸变,导致塑性变形抗力增加,固溶体的强度、硬度提高,这种现象称为固溶强化。
6.合金相图
合金相图是表示合金系中合金的状态与成分、温度间关系的图解,简称相图或称状态图。
相图是在极缓慢冷却、接近平衡条件下测绘的,故又称平衡图。
对二元合金系来说,通常用横坐标表示合金成分,纵坐标表示温度。
在成分和温度坐标平面上的任一点称为表象点。
一个表象点的坐标值表示一个合金的成分和温度。
7.杠杆定律
在合金的结晶过程中,随着结晶过程的进行,合金中各个相的成分及其相对含量都在不断地发生着变化。
对于某一具体合金来说,不但要了解相的成分,还需要了解相的相对含量。
利用“杠杆定律”就能确定任何成分的合金在任何温度下处于平衡状态的两个相的成分和相对含量。
(1)两平衡相及其成分的确定
如图3a所示的Cu-Ni二元相图中,要确定合金Ⅰ冷却到温度t1时合金的组成相及其成分,可通过温度t1作一水平线,分别与液相线和固相线交于a、b两点,表示合金Ⅰ在温度为t1时,是由液相(L)和固相(
)所组成,a、b两点在成分坐标轴上的投影CL和Cα即是液固两相的成分。
(2)两平衡相相对质量的确定
设图3a中合金Ⅰ的总质量为1,当温度为t1时,液相的质量为WL,固相质量为Wα。
总质量等于液相和固相的质量之和,即
总含镍量等于液固两相含镍量之和,即
联解以上两式得:
上式与力学上的杠杆定律相似,其中以r为支点,杠杆两端质量与其臂长成反比,如图3b)所示,故称为杠杆定律。
图3杠杆定律及其力学比喻图
在图4中,虽然F~G点之间的合金均由
和β两相所组成,但是由于合金成分和结晶过程的变化,相的大小、数量和分布状况,即合金的组织差别很大,甚至完全不同。
如在F~M成分范围内,合金的组织为
+βⅡ,亚共晶合金的组织为
+βⅡ+(
+β),共晶合金完全为共晶组织(
+β),过共晶合金的组织为β+
Ⅱ+(
+β),在N~G点之间的合金组织为β+
Ⅱ。
其中的
、β、
Ⅱ、βⅡ及(
+β)在显微组织中均能清楚地区分开,是组成显微组织的独立部分,这种在显微组织中能清楚分辨的组成显微组织的独立部分称为组织组成物。
从相的本质看,它们都是由
和β两相所组成,所以
和β两相就是组成合金组织的基本相,称为合金的相组成物。
图4标记组织组成物的Pb-Sn合金相图
合金中的组织组成物或相组成物的相对含量,都可以用杠杆定律来计算。
例如图4中含锡量为30%的亚共晶合金在183℃共晶转变结束后,组织为
+(
+β),其相对含量分别为:
相组成物
和β的相对含量分别为:
8.二元合金相图遵循的规律
根据前几节对各种二元相图的分析,可以总结出二元合金相图一般具有以下规律:
(1)两个单相区只能相交于一点,而不能相交成一条线。
(2)两个单相区之间,应有一个两相区,且该两相区由近邻两个单相区的相所组成;两个两相区必定以单相区或三相共存线隔开。
即相邻相区的相数相差1(相区接触法则,点接触除外)。
(3)三相共存线是一条水平线,每一条水平线必定和三个两相区相邻,还分别和三个单相区成点接触,其中一点在线的中间,两点在两端。
(4)如果两个恒温转变中有两个相同的相,那么在这两条水平线之间,一定是由这两个相组成的两相区。
六、铁碳合金相图
碳钢和铸铁都是铁碳合金,是使用最广泛的金属材料。
1.铁碳合金的组元
铁与碳可以形成一系列的化合物,Fe3C、Fe2C、FeC等,每一个稳定的化合物都可以看成是一个组元,因此整个相图可以看成是由Fe-Fe3C、Fe3C-Fe2C、Fe2C-FeC以及FeC-C等四个二元相图所构成。
Fe3C中含碳量为6.69%,超过6.69%C的铁碳合金脆性很大,没有使用价值,所以工业上作用的铁碳合金中含碳量不超过5%,在Fe-Fe3C相图的成分范围内。
因此,我们在研究铁碳合金时,仅研究Fe-Fe3C部分。
后面讨论的铁碳相图实际上就是Fe-Fe3C相图,其组元是铁和渗碳体。
2.铁碳合金中的基本相
在Fe-Fe3C二元合金系中,存在多种成分不同的铁碳合金,它们在不同温度下的平衡组织是各不相同的,但是它们总是由几个基本相所组成。
在液态,铁和碳可以无限互溶。
在固态,由于铁碳合金的基本组元纯铁具有同素异构转变,可以形成体心立方晶格和面心立方晶格的两种同素异构体。
碳溶于铁的这两种晶格,形成两种固溶体,它们是相图中的两个基本相,即铁素体和奥氏体。
此外,Fe3C(亦称渗碳体)也是Fe-Fe3C相图的基本相之一。
名称
铁素体(F)
奥氏体(A)
渗碳体(Fe3C)
类型
碳溶于
-Fe中形成的间隙固溶体
碳溶于γ-Fe中形成的间隙固溶体
铁与碳形成的稳定化合物
晶格
体心立方
面心立方
斜方晶格
含碳量
<0.0218%
0.77~2.11%
6.69%
外形
不规则外形晶粒
不规则外形晶粒
片、粒、网状
性能
塑性、韧性好,强度、硬度低
硬度低、塑性好
硬而脆
3.铁碳合金相图分析
图5铁碳合金相图
铁碳合金相图主要是由左上角的包晶转变、右边的共晶转变及左下角的共析转变三部分所构成。
相图中的特性线是各不同成分合金具有相同意义的临界点的连线。
1)铁碳合金相图中的特性点
特性点
温度/℃
碳的质量分数/%
特性点的含义
A
1538
0
纯铁的熔点
B
1495
0.53
包晶转变时液态合金的成分点
C
1148
4.30
共晶点
D
1227
6.69
渗碳体的熔点
E
1148
2.11
碳在γ-Fe中的最大溶解度点
F
1148
6.69
共晶渗碳体的成分点
G
912
0
α-Fe
γ-Fe同素异构转变点(A3)
H
1495
0.09
碳在δ-Fe中的最大溶解度点
J
1495
0.17
包晶点
K
727
6.69
共析渗碳体的成分点
M
770
0
纯铁的磁性转变点
N
1394
0
γ-Fe
δ-Fe同素异构转变点(A4)
O
770
≈0.5
0.5%C合金的磁性转变点
P
727
0.0218
碳在α-Fe中的最大溶解度点
S
727
0.77
共析点(A1)
Q
600
0.0057
600℃时碳在α-Fe中的溶解度点
2)铁碳合金相图中的特性线
特性线
特性线的含义
特性线
特性线的含义
ABCD
液相线
PQ
碳在铁素体中的溶解度线
AHJECF
固相线
ES(Acm)
碳在奥氏体中的溶解度线
NH
δ铁素体向奥氏体转变开始温度线,即碳在δ铁素体中的溶解度曲线
HJB
包晶转变线
ECF
共晶转变线
JN(A4)
δ铁素体向奥氏体转变终了温度线
PSK(A1)
共析转变线
GS(A3)
奥氏体向铁素体转变开始温度线
MO(A2)
铁素体的磁性转变线
GP
奥氏体向铁索体转变终了温度线
230℃水平线(A0)
渗碳体的磁性转变线
(1)三条等温转变线
相图中有三条水平线,表示三种等温转变:
包晶转变线、共晶转变线、共析转变线。
727℃的PSK线是共析转变线,S点为共析点。
凡含碳>0.0218%的铁碳合金缓慢冷却到727℃(A1)时均要发生共析转变:
共析转变的产物(F+Fe3C)称为珠光体,用“P”表示。
(2)三条固态转变线
GS线——含碳<0.77%的铁碳合金在冷却过程中,从奥氏体中析出铁素体的开始线,或在加热过程中铁素体转变成奥氏体的终了线,又称A3线。
ES线——碳