第六章压铸件缺陷的产生及控制.docx
《第六章压铸件缺陷的产生及控制.docx》由会员分享,可在线阅读,更多相关《第六章压铸件缺陷的产生及控制.docx(24页珍藏版)》请在冰豆网上搜索。
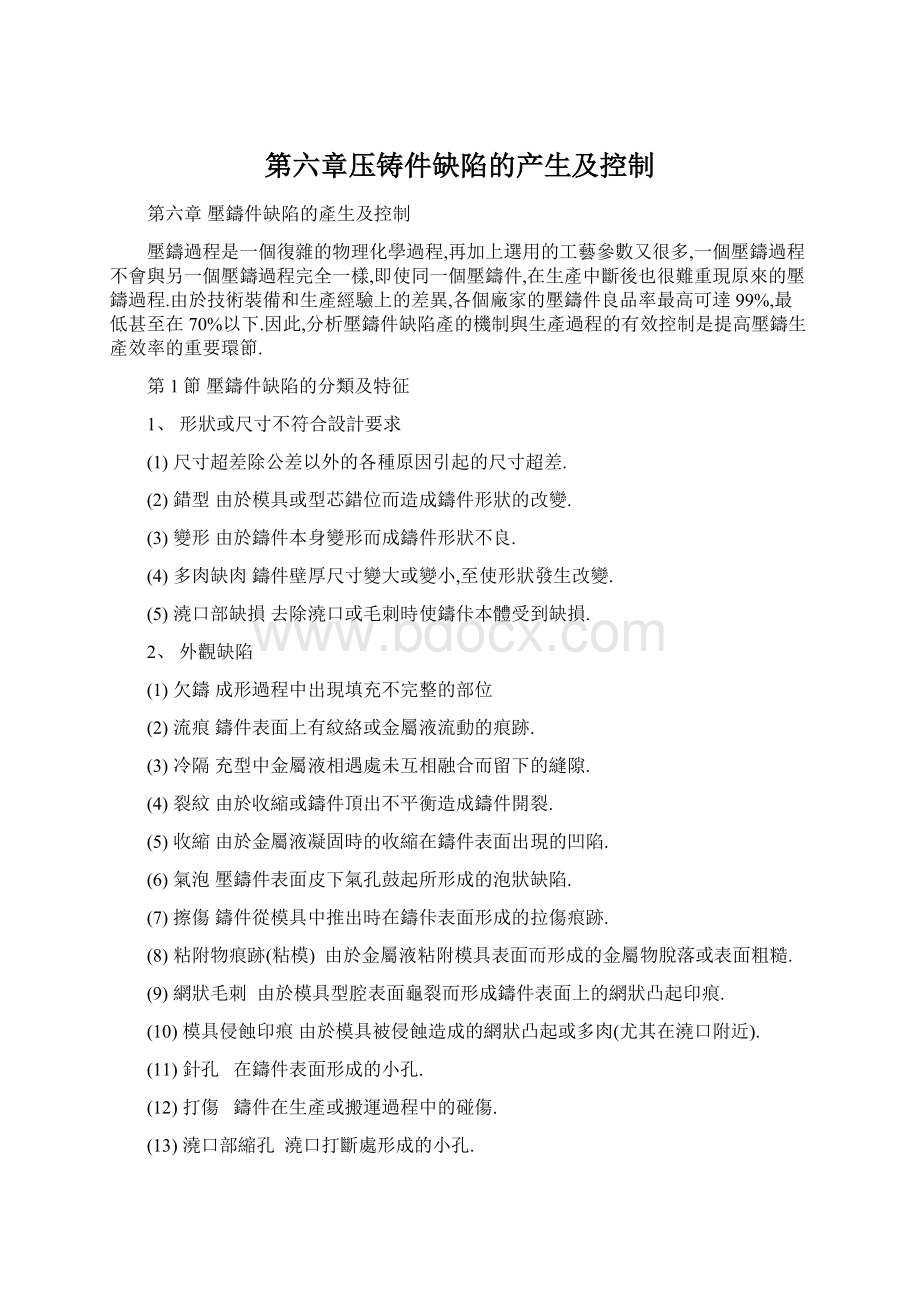
第六章压铸件缺陷的产生及控制
第六章壓鑄件缺陷的產生及控制
壓鑄過程是一個復雜的物理化學過程,再加上選用的工藝參數又很多,一個壓鑄過程不會與另一個壓鑄過程完全一樣,即使同一個壓鑄件,在生產中斷後也很難重現原來的壓鑄過程.由於技術裝備和生產經驗上的差異,各個廠家的壓鑄件良品率最高可達99%,最低甚至在70%以下.因此,分析壓鑄件缺陷產的機制與生產過程的有效控制是提高壓鑄生產效率的重要環節.
第1節壓鑄件缺陷的分類及特征
1、形狀或尺寸不符合設計要求
(1)尺寸超差除公差以外的各種原因引起的尺寸超差.
(2)錯型由於模具或型芯錯位而造成鑄件形狀的改變.
(3)變形由於鑄件本身變形而成鑄件形狀不良.
(4)多肉缺肉鑄件壁厚尺寸變大或變小,至使形狀發生改變.
(5)澆口部缺損去除澆口或毛刺時使鑄佧本體受到缺損.
2、外觀缺陷
(1)欠鑄成形過程中出現填充不完整的部位
(2)流痕鑄件表面上有紋絡或金屬液流動的痕跡.
(3)冷隔充型中金屬液相遇處未互相融合而留下的縫隙.
(4)裂紋由於收縮或鑄件頂出不平衡造成鑄件開裂.
(5)收縮由於金屬液凝固時的收縮在鑄件表面出現的凹陷.
(6)氣泡壓鑄件表面皮下氣孔鼓起所形成的泡狀缺陷.
(7)擦傷鑄件從模具中推出時在鑄佧表面形成的拉傷痕跡.
(8)粘附物痕跡(粘模)由於金屬液粘附模具表面而形成的金屬物脫落或表面粗糙.
(9)網狀毛刺由於模具型腔表面龜裂而形成鑄件表面上的網狀凸起印痕.
(10)模具侵蝕印痕由於模具被侵蝕造成的網狀凸起或多肉(尤其在澆口附近).
(11)針孔在鑄件表面形成的小孔.
(12)打傷鑄件在生產或搬運過程中的碰傷.
(13)澆口部縮孔澆口打斷處形成的小孔.
3、內部缺陷
(1)縮孔由於凝固時的收縮在鑄件內部產的孔洞.
(2)气孔卷入铸件内部的气体所形成的孔洞.
(3)疏鬆鑄件內部出現粗大的海綿狀组织.
(4)厚壁中心部的針孔在壁較厚部位的中心處產生的球狀小孔.
4、材質缺陷
(1)硬質點鑄件內部存的高硬度的顆粒,此會影響切削加工.
(2)化學成分超差化學成分超過標準或使用了另外的材料.
(3)氧化夾雜氧化物混入鑄件中.
5、其它缺陷
(1)理化性能不良強度、耐蝕性等理化性能未達到規定標準.
(2)氣密性不良(耐壓不良)鑄件內若加壓,壓力發生泄漏.
(3)鑲嵌件遺漏壓鑄時,鑄件上忘記嵌入鑲嵌件.
第二節產生缺陷的原因及措施
表6-1~表6-5分別列出了缺陷的名稱、產生的原因及相應的措施.防止各种缺陷產生的措施應依次實施,且待結果確認以後,再實行下一個措施.
表6-1形狀尺寸不良
缺陷名稱
原 因
措 施
錯
誤
操
作
圖紙尺寸誤標
(1)建立圖紙檢查制度
(2)完善圖紙管理
模具尺寸檢查方法不當
(1)試壓鑄時進行充分檢查,尤其是曲接處的壁厚要作斷面切開檢查
(2)實行兩次檢查制度
模具維修失誤
(1)確認修理部位以及與之相關的部位是否正確
(2)修模後,試壓鑄檢查
尺
寸
超
差
尺
寸
超
差
模具或模具裝配不良
1)檢查模具裝配情況
2)檢查螺釘鬆動情況
3)檢查嵌入的型腔和模套之間的平行度
檢查分型面是否平行貼合模框和所嵌型腔之間的配合間隙是否適當
型芯彎曲
1)定期檢查型芯是否變形
2)使用模具時要充分預熱,並且嚴格按工藝規程進行操作
3)對澆口方案及型芯型腔能否冷卻等鑄造方案重新進行論證.
4)針對鑄件的收縮情況對鑄件形狀進行改動
5)改進模具的材料或硬度
模具衝蝕
1)修復模具被衝蝕的部分
2)改進澆口位置,模具結構或鑄造方案
3)改進模具的材料或硬度
收縮引起的尺寸變化
1)檢查澆注溫度,循環時間,保壓時間及模具溫度等參數是否正確,並嚴格遵守工藝規程.
2)檢查金屬液化學成分是否合格
3)如果是由於局部過熱成局部收縮,可調節該部分的冷卻水量或改變澆口位置和金屬液成分等
模具強度不足
1)提高模具強度
2)改進模具設計
3)改進鑄件結構
錯
型
導柱鬆動
檢查導柱和導套之間的磨損情況,如果間隙過大應更換
所嵌型腔與模套配合不良
檢查型腔與模套的間隙並應符合要求
滑塊和導軌配合不良
1)檢查滑塊和導軌間的間隙,並應符合要求
2)檢查楔緊塊和滑塊的配合,是否良好
3)檢查滑塊和導軌的潤滑情況
4)研討並改進滑動部分的材料和硬度
模具裝配調配不良
檢查模具裝配部份的平行度
壓
射
跑
水
、
鑄
孔
隔
層
加
厚
模具鎖緊不完全
1)調整導柱和導套的配合使動定模完全貼合,如果配合不好,則修理相抵的部份
2)壓鑄機合型力不夠,造成鑄件飛邊過大,則要調節合型力
3)清理分型,面去掉飛邊毛刺.
4)檢查並修整型芯和型腔分型面的表面,使平面度、表面粗糙度、凹凸部分的嵌合呈良好狀態,以不產生飛邊為準
5)調整滑塊和導軌的間隙
6)檢查滑和鎖緊塊的磨損情況,並進行修理
壓射力不合適
1)調低壓射力或用較大的衝來降低壓鑄比壓
2)減小衝頭速度
注:
采取1)或2)對策時,必須保證不能出現流痕或欠鑄的缺陷.經險表明,選用大噸位的壓鑄機要好些
變型
變
型
鑄件壁厚變化突然
修改鑄件形狀以使鑄件壁厚均勻或壁厚變化平緩
由於應力集中造成收縮不平衡
1)適當詷鑄圓角
2)分析並改進鑄件結構
3)采用加強筋,改變鑄件結構以使應力均勻分布
型腔表面有倒色或拋光不充分
1)檢查並按要求修復拔模斜度
2)雙具側壁進行拋光,消除倒勾,使鑄件頂出順利
推杆強度不夠
1)使用大一點的推杆
2)增加推杆數量
鑄件推出不平衡
檢查並調整推杆位置或增加推杆以使鑄件推出平穩
壓鑄工藝不佳
1)嚴格按工藝操作
2)分析壓鑄參數,調低過高的壓鑄壓力,加大過熱部分的冷卻水量,使鑄件溫度均衡
模具熱平衡不良
1)分析並改進脫模劑的種類、噴涂量、噴涂位置和方法等
2)有必要的話,可為頂出鑄件設置加強筋或凸臺
鑄
件
殘
缺
鑄件某一部分粘在型腔上
1)修足拔模斜度
2)去掉模具表面的劃痕並進行拋光
3)分析並改進冷卻方法,溢渣包和澆口設計以便於模具的溫度平衡
4)設置加強筋使鑄件在熱狀態時有足夠的強度.
頂杆痕跡過深
(1)鑄件冷卻時間不夠
(2)部份壁過厚
1)模具需充分冷卻
2)延長保壓時間和冷卻時間,待充分凝固後再推出
3)改變鑄件形狀使壁厚均勻或者改變推杆位置
由於留有殘屑造成鑄件缺肉
(1)模具清理不乾凈
(2)鑲塊或滑塊配合不好
(3)表面狀況較差
1)把模具表面和滑塊處的殘渣清除徹底後再壓鑄
2)減小鑲塊和模具的配合間隙
3)降低表面粗糙度,改善型腔表面狀況,以殘屑不粘在模具上
4)改善滑塊和導軌的配合
缺肉
破損
表面存在倒勾或粘模
1)修理倒勾或粘模部位
2)分析並改進澆口位軒和冷卻方法
3)分析並改進脫模劑和壓鑄工藝
多
肉
(1)模具型腔斷裂
(2)型芯斷裂
(3)型腔衝蝕
(4)型腔腐蝕
(5)推杆過短
1)修模(焊補、磨削)
2)更換型芯
3)修模
4)修模
5)更換並調整推杆的長度
澆
口
部
破
裂
(1)澆口、渣包和鑄佧結合部位設計不合理
(2)去澆口方向不當
(3)去澆口方法不當
1)在澆口,渣包和型腔連接處倒角.
2)改變澆口的位置和設計
3)改變去掉澆口的方向
4)分析並改進去澆口的方法
欠
鑄
(1)鑄造條件不合適(模具溫度,澆注溫度,壓鑄循環等)
(2)壓鑄機參數不合適(壓射速度,壓力等)
(3)鑄件形狀不合適(壁厚,形狀等)
(4)模具設計不合理(分型,線內澆口,橫澆道,溢渣包,排氣道的位置和尺寸等)
1)調整鑄造條件,提高模具溫度和澆注溫度
2)詷整壓鑄機的工藝參數:
壓射速度、壓射壓力、慢壓射和快壓射的轉換位置、料筒尺寸等
3)分析並改進模具設計、澆口的位置和尺寸、提供足夠的排氣道和溢渣包
4)改變鑄件的工藝結構以獲得合適的壁厚和形狀
流
痕
1)調整鑄造條件,提高模具溫度和澆注溫度,減少脫模劑噴涂量
2)研討模具設計,提供足夠的排氣道和溢渣包,尤其注意金屬液的流向
3)通過噴丸等方法改善表面粗糙度,改變模具表面附近的金屬液流向
4)調整壓鑄機的工藝參數,提高壓射速度和壓鑄壓力.
5)選擇合適的鋁合金
冷
隔
1)同欠鑄的措施1)~4)
2)選擇凝固範圍較寬的鋁合金
3)注意金屬液中的氧化夾雜
縮
裂
压铸工艺、铸件结构、合金成分、澆口設計不合理
1)提高模具溫度,必要時提高澆注溫度
2)縮短凝固時間
3)減少脫模劑用量
4)優化鑄件結構,使鑄件壁厚均勻
5)倒棱或加大圓角半徑
6)不使用極薄的壁厚
7)改變壓射條件以獲得好的流態
8)改進澆口設計使充填更充分
9)檢查鋁合金的化學成分,尤其注意含鐵量
開模推出等造成的機械裂紋
(1)推出裝置或推出方法不當
(2)壓鑄機、模具、滑塊等精度不良
(3)推出時間不合適
(4)鑄件結構不合理
(5)鑄造合金質量差
1)去掉型腔表面的倒勾,修復拔模斜度
2)詷整模具溫度和凝固時間
3)倒棱或加大圓角半徑
4)拋光模具表面
5)調整推出等待時間
6)檢查推出是否平衡
7)加大推杆的尺寸
8)分析並改進澆口設計以獲得好的流態
9)檢查鋁合金的化學萬分是否合適
10)檢查模具裝配、動定模配合是否良好
壓射時由於模具或滑塊鬆動造成的裂紋
(1)合模力不夠
(2)模具中心和壓鑄機中心不吻合
(3)模具精度差或裝配不良
(4)模具強度不夠或型芯強度不夠
1)選擇合適的壓鑄機
2)調整模具的受力中心
3)降低壓鑄壓力
4)修理滑塊和楔緊塊配合處
5)檢查模具和滑塊的平面度和平行度
6)檢查壓鑄機動、定型板的平面芭
7)檢查模具設計是否合理以保證在壓鑄壓力下模具不發生變形
8)調整合模機構
收
縮
(1)壓鑄工藝不合理尤其是模具溫度過高
(2)鑄件結構不合理尤其是壁厚變化突然
1)調整壓鑄工藝:
降低模溫,降低澆注溫度,減少脫模劑噴涂量
2)防止鑄壁厚變化突然
3)倒棱或加大圓角半徑
4)減少鋁合金中雜質含量
5)調整模具的溫度,鑄件的形狀,壓射速度和金屬液流動狀態,以使熱中心處於厚壁的中心
6)改進澆口使流態更佳
7)改變工藝使流態更佳
氣
泡
(1)壓鑄工藝不合理,尤其是模溫過高
(2)鑄件結構不合理
(3)鑄件表面存在氣體
1)降低模具表面溫度
2)調整凝固時間
3)改進模具設計以便獲得好的流態,特別是保證足夠大的溢渣包和排氣道
4)調整模具溫度,壓射速度和金屬液流動狀態或改變鑄件的形狀,以便實現熱中心能夠處於厚壁部位
擦
傷
(1)模具維修不徹底
(2)壓鑄工藝鑄件結構不合理
1)對模具表面進行充分拋光
2)去掉型壁上存在的倒勾
3)增加拔模斜度
4)倒棱或加大圓角半徑
5)沿脫模方向拋光模具型腔表面
6)更換脫模劑或噴足脫模劑
7)降低模具表面溫度
8)去除模具表面的熱裂紋
9)去掉粘在模具表面的鋁屑
粘
附
物
痕
跡
(粘模)
(1)模具和澆口設計及鑄件結構不合理
(2)模具維修不良
1)增加內澆口厚度
2)修理澆口的位置和方向
3)加強粘模部位的冷卻
4)選擇合適的脫模劑,充分噴涂
5)調整鐵含量
6)調整壓射速度
7)改變鑄件結構以使充型良好
8)經常去除粘附在型腔表面的鋁屑
網
狀
毛
刺
(1)不適當的鑄造條件
(2)模具材料的強度或硬度不夠
(3)模具冷卻不良
(4)模具的熱循環和熱衝擊
1)從模具型腔表面去除熱裂紋
2)充分拋光模具表面
3)優化模具冷卻系統
4)研討模具材料的拉伸強度和硬度,選擇合適的模具材料
5)縮小模具工作溫度和澆注溫度之間的溫差,防止熱衝擊的產生
6)開始壓鑄前要對模具充分預熱
7)盡量避免冷卻水泄漏進入模具的表面
模
具
侵
蝕
印
痕
(1)模具和澆口設計及鑄條件不合理
(2)模具維修不良
1)調整內澆口厚度
2)改變內澆口位置
3)改變內澆口處金屬液流入的方向或其與型腔的連接方法
4)提供更在的圓角半徑和在澆口附近加大拔模斜度
5)對澆口和被衝刷部位進行充分冷卻
6)修理模具被侵蝕的部位(焊接,研磨,拋光,表面處理等)
釘
孔
(
鑄
件
表
面
)
(1)鑄造條件不適當
(2)壓射條件不適當
(3)飛邊毛刺太多
(4)模具設計不合理
(5)排氣不暢
1)提高模具溫度
2)減少脫模劑噴涂量
3)提高壓鑄壓力
4)改進模具設計,使充填狀態良好
5)提供足夠的排氣道
6)調整壓射參數
7)防止產生金屬飛濺和飛邊毛刺
打
傷
不適當的碼放,搬運和裝箱
1)在碼放、搬運、裝箱過程中要小心輕放
2)認真細致地從壓鑄機上取下鑄件
澆
口
部
縮
孔
(1)模具狀況不良
(2)鑄造條件和澆口設計不當
1)在澆口部進行充分冷卻
2)減小澆口厚度
3)提高壓鑄壓力
4)提高金屬液質量
5)防止產生金屬液飛濺和飛邊毛刺
6)延長凝固時間,直到澆口完全凝固為止
縮
鬆
(1)厚壁處金屬液供應量不足
(2)壁厚變化突然
1)改進模具設計,並重點檢查澆口厚度,寬度和位置,還要變更排氣道溢渣包的位置和尺寸
2)改變壓射和充填時間
3)提高壓鑄壓力
4)降低產生縮鬆處模具表面的溫度
5)研討冷卻的位置和方法
6)在產生縮鬆的地方加一個型芯
7)盡量使鑄件壁厚均勻一致
氣
孔
由型腔內的空氣或脫模劑產生的氣體所致
1)變更鑄造方案(改變澆品的位置,尺寸,溢渣包排氣道等,或者改變分型面)
2)調整壓射和充填時間
3)提高壓鑄壓力
4)在產生氣孔的地方增加型芯
5)更換脫模劑
6)減少脫模劑噴涂量
7)調整鑄件壁厚,使其盡量均勻
8)調整快壓射和慢壓射的轉換位置
由合金液中的氣體所致
1)減少合金液中氣體和氧化物含量
2)控制和管理好回爐料,以免混入油污臟物
疏
鬆
(1)金屬液充填不充分
(2)混入氧化膜
1)壓射室中的金屬液需平穩流動,防止金屬液被氧化
2)不斷地去掉坩堝中的氧化膜
3)研討模具設計,使金屬液充填狀態良好
4)調整壓射速度和充填時間,保證金屬液充填充分
5)減少脫模劑噴涂量
6)研討模具溫度是否適宜
厚壁中心處的針孔
(1)壓鑄比壓不足
(2)模具設計不合理
1)合模完整,減少飛邊毛刺
2)防止金屬液飛濺,跑水
3)改進模具設計
非
金
屬
性
硬
質
點
氧化夾雜
1)將坩堝內的氧化膜徹底清除掉
2)澆注時避免帶入爐渣
3)將澆瓢和熔煉工具清理乾凈
4)鑄鐵坩堝要涂覆合適的涂料
5)使用石墨坩堝
混入了金屬液和耐火磚的反應物
1)選擇合適的耐火磚(例如:
高鋁耐火磚等)
2)定期更換熔煉爐的耐火材料
混入了金屬液與涂覆層的反應物
使用不與金屬液發生化學反應的涂
混入非金屬雜質
1)用脫氧劑進行充分地脫氧處理
2)選擇合適的脫氧劑
3)用優質的硅原料
4)保證足夠的鎮靜時間
外來雜質
1)管理好原料,回爐料,防止混入異物
2)防止加爐料粘染油,砂或臟物
3)修爐後避免砂漿耐火磚粉混入金屬液
4)把熔煉坩堝和工具上的氧化物,灰塵去除乾凈
5)把熔煉間,廠房,場地等清掃乾凈
金
屬
性
硬
質
點
混入了未溶解的硅
1)熔煉時不要使用粉狀硅
2)在調整鋁合金的化學萬分時,不要直接加入金屬硅(用鎢硅中間合金)
3)應保證較長的時間和高的溫度以硅全部溶解
混有發達的初晶硅結晶化合物
1)熔煉後保溫溫度應保持恆定
2)注意金屬液中的雜質含量,盡可能減少使初晶硅長大的雜質含量
混入金屬間化合物
1)熔煉後保溫溫度應保持恆定
2)注意控制合金成分中雜質含量
3)對鋁水進行高溫處理,高熔點的金屬間化合物溶解
復合性硬質點
金屬液和耐火材料或鑄鐵坩堝的反應物進入合金中
1)不要使用低鋁的耐火材料,因為它极易和鋁合金發生反應
2)不要鑄鐵坩堝和金屬液表面接觸地方的氧化物長期附著在坩堝上
化學成分超差
化學元素超過標準
1)認真嚴格地實行工藝管理,技術管理和質量管理
2)制定爐料的化學成分標準
3)鑄鐵坩堝,熔煉工具和澆瓢上涂刷合格的涂料
4)避免把鑄鐵鑲嵌件熔化掉
氧
化
夾
雜
1)在鑄造過程中金屬液被氧化
2)混入了金屬液表面的氧化膜
1)減少脫模劑的噴涂量
2)減少衝頭油的用量
3)經常要去除金屬液表面的氧化膜,並且注意不要把氧化物舀入澆瓢中
4)熔融金屬液平穩地澆入壓射室中
表6-5其它缺陷
缺陷名稱
原因
措施
理化性能不良
(1)化學成分不合格
(2)鑄造方案不適當
(3)充填條件不適當
1)選擇成分合格的鋁合金並將雜質含量控制在適當的範圍內
2)研討模具設計,壓鑄工藝和充填條件並做適當的調整
氣密性
不良(耐壓不良)
(1)合金材料不適當
(2)化學成分不合格
(3)模具設計不合理
(4)壓鑄工藝不適當
(5)充填條件不適當
1)研討合金材料並選擇最佳的一種
2)選擇化學成分和雜質含量均合格的材料
3)研討模具設計,壓鑄工藝和充填條件並做適當的調整
4)如有可能,對鑄件形狀加以改進
5)采用新的鑄造方法
鑲嵌件遺漏
操作者疏忽大意
1)制定作業指導書和操作規程
2)對操作者進行嚴格的教育訓練
第三節宜安壓鑄缺陷特點及解決辦法
EP-EY發熱板前段時期經機械加工後,廢品率較高,最高的廢品率達到98%,而廢品中最主要的廢品原因為氣孔占報廢率的80%,其次為夾渣占15%~30%,彎形及露發熱管的現象也比較嚴重.這些質量問題都是由於我們在實際生產過程中,沒有嚴格執行工藝規程的結果.近段時期,在消除主要廢品原因氣孔的情況下,又出現了較嚴重的流紋現象,這也是由於一些設備因素及工藝因素所造成的.下面將首先分析氣孔現象.
(1)氣孔產生的主要原因
(1)澆口位置選擇和導流形狀不當,導致金屬液進入型腔產生正面撞擊和產生旋渦.
(2)澆道形狀設計不良.
(3)壓鑄充滿度不夠.
(4)內澆口速度太高,產生湍流.
(5)模具型腔位置太深.
(6)涂料過多,充前未燃盡.
(7)機械加工量餘量太大.
分析:
1.粗煉不完全,除氣不底.
在精煉除氣時,沒有將精煉除氣劑壓入爐爐底部並做緩慢移動.
精煉劑,除氣劑的加入量沒有按一定的規定,對原材料選用熔煉時沒有分類.精煉除氣工作不細緻底了事.
2.原材料中帶入氣體
所選用的原材料(鋁錠)中本身存有氣體.由於在熔煉過程中沒有按照適當的配比,加入回爐料,其回爐料在加入前沒有進行預熱處理,回爐料含有水分,油漬,污漬等,如果在煉過程中不進行正確的精煉除氣,就有可能造成產品氣孔而使產品報廢.
3.保溫爐精煉效果不明顯.
因為保溫爐的溫度只適合於壓鑄溫度.而我們所要求的精煉除氣的最佳溫度為680~720ºC.所以在保溫爐中做精煉除氣,不會有很好的效果,但也會起到一定的作用,相對減少鋁液中的氣體含量.
4.保溫爐末加覆蓋劑
在壓鑄過程中,保溫爐長時間與大氣接觸,壓鑄過程中經常要噴脫模劑,其車間濕度較高,空氣中的水氣含量較多.鋁合金溶液又極易吸氣,如果沒有保護措施,鋁合金液在保溫過程中吸收大量的水分及氣體,而使鋁液中的含氣量增加.
5.人為帶入氣體或帶入發氣量較高的物體.其具體表現在:
(a)把小量機油倒入保溫爐液表面.使之燃燒.以達到取火烤模的目的.
(b)澆粘鋁時,用澆機油,再伸入鋁液中.
(c)用澆不斷在鋁液中攪拌.
(d)在保溫爐中加鋁水時,運料色或澆色離鋁液表面的距離太高,直接帶入氣體.
6.模具設計不合理帶入氣體.
模具設計時,沒有選擇正確的澆注系統和排氣溢流系統.鋁液在充型時排氣不順暢或者說排氣受阻.而使鑄件產生氣孔.使用抽真空裝置,應經常檢查真空度,因為當真空度不高或沒有抽真空時,模具排氣受到限制,換言之,模具此時失去排氣效果.大部分產口將會產生氣孔.
7.模具變形時,會產生飛料.(也有說跑水),飛料後壓力受損.
鋁合金液在充型時,速度極快,鋁合金會產生急冷,液態處於型腔中的時間較短,前部分鋁合金液被飛出型腔後,後部分的鋁合金液還來不及補充就已被凝固,因此在鑄件中產生蜂窩狀的氣孔形狀,其氣孔最大尺寸有超過10mm的.
8.機器設備因素:
壓鑄設備在壓鑄過程中對產品成型以及獲得高質量的鑄件起著決定性的作用.一般情況,調試好的設備不要輕易更改工藝參數,如設備的壓力.合模鎖緊力,壓射速度,壓射起步時間等因素都有可能造成產品質量不合格.
(2)夾渣或夾雜產生的主要原因
(1)鋁合金,未精煉好,澆注時混入了氧化物.
(2)由鋁,鐵,錳,硅組成的復雜化合物,主要是由MnAI3在熔池較冷處形成,然後以MnAI3為核心使Fe析出,又有硅等參加反應形成化合物.
(3)游離硅混入物時,鋁硅合金含硅量高.鋁硅合金在半液態澆注,存在了游離硅.
分析:
1.熔煉過程精煉不完全.
鋁合金液中含有許多的氧化物,砂及渣點等雜質.精煉造渣過程非常重要.精煉劑加入量是否合適,打渣劑加入量是否符合比例要求,工作過程是否按工藝規程去做.扒渣是否完錢底等.
2.人為帶入渣質.
(a)用涂有石和機油的澆取鋁液.
(b)用臟的機油和石的混合物灑入鋁液表面取火烤模.
(c)衝模油的噴涂及質量.
上述三條中都含有石成分,石的熔點較高.很難在鋁液中熔化,產品成型後石在產品內經機加工後就可以看見色的石渣點.
(d)澆沒用氧化鋅涂料保護,其鐵的氧化物和其它氧化物被帶入產品中.
(e)取鋁淮時沒有將鋁合金液表成氧化物去掉,而被直接帶入模具型腔中.
(f)使用回用發熱管時,其發熱管表成的油漬,污漬和氧化物沒有清理乾凈,致使產品夾渣.
3.模具弄型腔表成的殘冷料或化物等雜質沒有清理乾凈.
4.料柄厚度太薄,帶入渣質等物.
(3)產品變形所產生的原因
1.模具溫度對產生的影響.當模具溫度過高時,產品成型頂出的強度不夠,被頂出的產品容易變形.具溫度超過一定值時.會產生粘模殃象.因而直接影響到產品的外觀及形狀.
2.脫模劑噴涂不均勻.噴涂模劑時同應根據模具的表面溫度.模具型腔各部位的復雜狀況及模具熱帶處等來決定的,有選擇地平模溫而均勻的噴涂脫模劑,是獲得理想產品外型的先決條.
3.頂出平面受力不一致.模具在壓鑄過程中,受熱溫度不一致.即具內存在熱節處,模具有內應力作用下產生變形,產品頂出時,頂出平面受力不一致,從而造成產品變形.
4.