热电厂锅炉燃烧控制系统设计精品.docx
《热电厂锅炉燃烧控制系统设计精品.docx》由会员分享,可在线阅读,更多相关《热电厂锅炉燃烧控制系统设计精品.docx(32页珍藏版)》请在冰豆网上搜索。
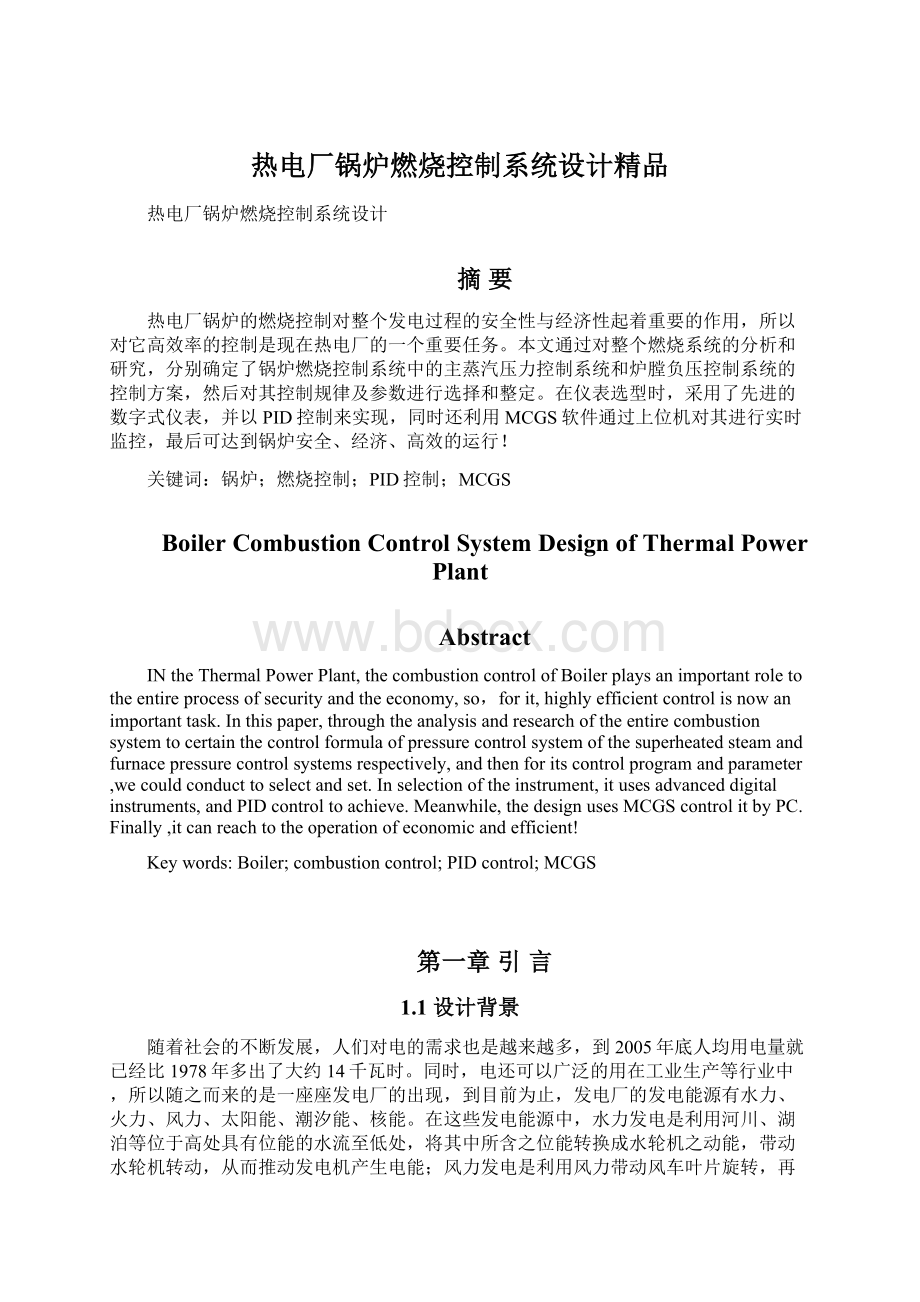
热电厂锅炉燃烧控制系统设计精品
热电厂锅炉燃烧控制系统设计
摘要
热电厂锅炉的燃烧控制对整个发电过程的安全性与经济性起着重要的作用,所以对它高效率的控制是现在热电厂的一个重要任务。
本文通过对整个燃烧系统的分析和研究,分别确定了锅炉燃烧控制系统中的主蒸汽压力控制系统和炉膛负压控制系统的控制方案,然后对其控制规律及参数进行选择和整定。
在仪表选型时,采用了先进的数字式仪表,并以PID控制来实现,同时还利用MCGS软件通过上位机对其进行实时监控,最后可达到锅炉安全、经济、高效的运行!
关键词:
锅炉;燃烧控制;PID控制;MCGS
BoilerCombustionControlSystemDesignofThermalPowerPlant
Abstract
INtheThermalPowerPlant,thecombustioncontrolofBoilerplaysanimportantroletotheentireprocessofsecurityandtheeconomy,so,forit,highlyefficientcontrolisnowanimportanttask.Inthispaper,throughtheanalysisandresearchoftheentirecombustionsystemtocertainthecontrolformulaofpressurecontrolsystemofthesuperheatedsteamandfurnacepressurecontrolsystemsrespectively,andthenforitscontrolprogramandparameter,wecouldconducttoselectandset.Inselectionoftheinstrument,itusesadvanceddigitalinstruments,andPIDcontroltoachieve.Meanwhile,thedesignusesMCGScontrolitbyPC.Finally,itcanreachtotheoperationofeconomicandefficient!
Keywords:
Boiler;combustioncontrol;PIDcontrol;MCGS
第一章引言
1.1设计背景
随着社会的不断发展,人们对电的需求也是越来越多,到2005年底人均用电量就已经比1978年多出了大约14千瓦时。
同时,电还可以广泛的用在工业生产等行业中,所以随之而来的是一座座发电厂的出现,到目前为止,发电厂的发电能源有水力、火力、风力、太阳能、潮汐能、核能。
在这些发电能源中,水力发电是利用河川、湖泊等位于高处具有位能的水流至低处,将其中所含之位能转换成水轮机之动能,带动水轮机转动,从而推动发电机产生电能;风力发电是利用风力带动风车叶片旋转,再透过增速机将旋转的速度提升,来促使发电机发电;核能发电利用核反应堆中核裂变所释放出的热能进行发电的方式,它与火力发电极其相似,只是以核反应堆及蒸汽发生器来代替火力发电的锅炉,以核裂变能代替矿物燃料的化学能;太阳能发电是利用光电效应发电的,当光照在半导体p-n结上,形成新的空穴-电子对,在p-n结电场的作用下,空穴由n区流向p区,电子由p区流向n区,接通电路后就形成电流;而火电厂是利用煤、石油、天然气作为燃料生产电能的工厂,它的基本生产过程是:
燃料在锅炉中燃烧加热水使之成蒸汽,将燃料的化学能转变成热能,蒸汽压力推动汽轮机旋转,热能转换成机械能,然后汽轮机带动发电机旋转,将机械能转变成电能。
在所有发电方式中,火力发电是历史最久的,也是最重要的一种,且火力发电在近几年还是主流的,因为我国的经济状况决定了我国采用什么样的能源措施。
火力发电厂其分类有:
按燃料分,燃煤发电厂,燃油发电厂,燃气发电厂,余热发电厂,以垃圾及工业废料为燃料的发电厂;按蒸汽压力和温度分,中低压发电厂(3.92MPa,450度),高压发电厂(9.9MPa,540度),超高压发电厂(13.83MPa,540度),亚临界压力发电厂(16.77MPa,540度),超临界压力发电厂(22.11MPa,550度);按原动机分,凝气式汽轮机发电厂,燃气轮机发电厂,内燃机发电厂,蒸汽—燃汽轮机发电厂等;按输出能源分,凝汽式发电厂(只发电),热电厂(发电兼供热);按发电厂装机容量分,小容量发电厂(100MW以下),中容量发电厂(100-250MW),大中容量发电厂(250-1000MW),大容量发电厂(1000MW以上);我国目前最大的火电厂:
浙江北仑港电厂,装机容量300万KW(即3000MW),5台60万KW(600MW)机组。
1.2设计目的
目前,在我国电力能源结构中燃煤电厂的发电量占总发电量的80%以上,即使到2020年,燃煤电厂的发电量仍将占70%以上。
煤燃烧排放的SO2和NOx以及粉尘仍已成为大气主要污染源,所以要努力提高能源利用率,尽可能减少煤炭消耗,减少温室气体和SO2的排放。
在火力发电行业中,原有的小机组锅炉由于燃烧效率低、环境污染大的缘故已经逐步被淘汰,这在很大程度上加快了国内火电设备的更新换代,拉动火电设备市场需求。
国内火电市场的主力机型已由2005年之前的30万千瓦机组为主,逐渐向60万千瓦及以上过渡。
由于机组的功率增大了,所以使它安全、稳定的运行也相对变的更加重要了,因为锅炉安全、稳定运行才能保证整个发电过程的经济性、高效性。
这便是该设计的主要目的!
第二章热电厂的生产工艺及单元机组的自动控制系统
2.1热电厂的生产工艺
热电厂既为火力发电厂,火力发电(thermalpower,thermoelectricitypowergeneration)是利用煤、石油、天然气等固体、液体、气体燃料燃烧时产生的热能,通过发电动力装置(包括电厂锅炉、汽轮机和发电机及其辅助装置)转换成电能的一种发电方式。
它的工作原理:
由锅炉产生蒸汽,然后送入到汽轮机,汽轮机的转动带动发电机发电。
汽轮机的排气进入到一个叫凝汽器的冷端设备,凝结成水,由凝结水泵送往给水泵,再进入锅炉。
这样就为一个循环。
热电厂的三大主要设备是锅炉、汽轮机、发电机。
锅炉用燃料燃烧放出的热能将水加热成具有一定压力和温度的蒸汽,然后蒸汽沿管道进入汽轮机膨胀做功,带动发电机一起高速旋转,从而发电。
整个过程中存在三种能量转换过程,在锅炉中燃料的化学能转换成热能,在汽轮机中将热能转换成机械能,在发电机中将机械能转换成电能。
以下是热电厂生产工艺流程图:
图1.1热电厂生产工艺流程图
2.2锅炉系统的组成及工作原理
锅炉是由“锅”和“炉”两部分组成。
“锅”就是汽水系统,由省煤器、汽包、下降管、水冷壁、过热器及再热气等设备组成。
它的任务是水吸热变成蒸汽,最后再变成一定参数的过热蒸汽。
其过程是:
给水由给水泵打入省煤器以后,逐渐吸热,温度升高的给水进入汽包,经由下降管进入水冷壁中循环吸热,并蒸发为饱和蒸汽:
饱和蒸汽再汽包中经分离、清洗后,引入过热器,逐渐过热到规定温度,成为合格的过热蒸汽,然后送往汽轮机;过热蒸汽在汽轮机高压缸中膨胀做功后,气温、气压均下降,在高压缸出口由导管将蒸汽引入锅炉再热器中第二次再过热成为高温再热蒸汽,然后再送往汽轮机中,低压缸中继续膨胀做功。
图1.2煤粉锅炉及辅助设备示意图
“炉”就是锅炉的燃烧系统,由炉膛、烟道、喷燃器及空气预热器等组成。
其过程是:
送风机将空气送入空气预热器中吸收烟气的热量并送进热风段,然后分成两股:
一股送给制粉系统作为一次风携带煤粉送入喷燃器。
另一股作为二次风直接送往喷燃器。
煤粉与一、二次风经喷燃器喷入炉膛进行燃烧放热,并将热量以辐射方式传给炉膛四周的水冷壁等辐射受热面;燃烧产生的高温烟气则沿烟道流经过热器、再热器、省煤器和空气预热器等设备。
将热量主要以对流方式传给它们。
在传热过程中,烟气温度不断将低,最后由引风机送入烟囱。
2.3热电厂单元机组的自动控制系统
在热电厂中,以单位机组为控制对象,可以讨论的控制系统有:
锅炉汽包水位控制系统、燃烧过程控制系统以及过热蒸汽温度控制系统,过热蒸汽温度控制又包括过热蒸汽温度控制和再热蒸汽温度控制。
2.3.1锅炉汽包水位控制系统
汽包水位是锅炉运行的重要指标,保持水位在一定的范围内是保证锅炉安全运行的首要条件。
在该汽包水位的控制系统中,被控变量是汽包水位,操纵变量是给水量。
它主要是保持汽包内部的物料平衡,使给水量适应锅炉的蒸汽量,维持汽包中水位在工艺允许的范围内。
水位过高、过低,都会给锅炉及蒸汽用户的安全操作带来不利的影响。
首先,水位过高,会影响汽包内的汽水分离,饱和蒸汽将会带水过多,导致过热器管结垢并损坏,使过热蒸汽的温度下降。
以此过热蒸汽带动汽轮机,则将因蒸汽带液损坏气轮机的叶片,造成运行的安全事故。
然而,水位过低,则因汽包内的水量减少,而负荷很大,加快水的汽化速度,若不及时加以控制,将有可能使汽包内水全部汽化;尤其是大型锅炉,水在汽包内的停留时间极短,从而导致水冷壁烧坏,甚至引起爆炸。
所以,保持汽包水位在工艺允许的范围内是锅炉正常运行的重要指标!
2.3.2锅炉燃烧过程控制系统
锅炉燃烧控制系统由主蒸汽压力控制系统和炉膛压力控制系统组成,它的控制任务是使燃料流量随蒸汽负荷的变化而变化,当燃料流量变化时,空气流量也要随之变化以维持最佳风煤比,保证锅炉燃烧的经济性;在炉膛压力控制系统中,炉膛负压主要是受引风量的变化而变化的,所以通过改变引风量来使炉膛负压保持在-20Pa左右,从而使锅炉安全的运行!
在热电厂中每台锅炉燃烧过程的具体控制任务与制粉系统、燃烧方式以及锅炉的运行方式有着密切的关系。
2.3.3过热蒸汽温度控制系统
蒸汽过热系统包括一级过热器、减温器、二级过热器。
控制任务是使过热器出口温度维持在允许范围内,并保护过热器使管壁温度不超过允许的工作温度。
过热蒸汽温度过高或过低,对锅炉运行和蒸汽用户设备都是不利的。
过热蒸汽温度过高,过热器容易损坏,汽轮机也因内部过度的热膨胀而严重影响安全运行;过热蒸汽温度过低,一方面使设备的效率降低,同时使汽轮机后几级的蒸汽湿度增加,引起叶片磨损。
所以必须把过热器出口蒸汽的温度控制在规定的范围内,并保证管壁温度控制在规定的范围内。
过热蒸汽温度控制的系统常采用减温水流量作为操纵变量,但由于控制通道的时间常数及纯滞后均较大,组成单回路控制系统往往不能满足生产的要求,因此要采用以减温器出口温度为副参数的串级控制系统,这样可以提高对过热蒸汽温度的控制质量。
第三章锅炉燃烧控制系统设计
3.1锅炉燃烧控制系统的任务
锅炉燃烧系统的控制与燃料种类、燃烧设备以及锅炉形式等有密切关系。
现侧重以燃煤锅炉来讨论燃烧过程的控制。
燃烧过程的控制基本要求由三个:
第一、保证出口蒸汽压力稳定,能按负荷要求自动增减燃料量;
第二、燃烧良好,供气适宜,既要防止由于空气不足使烟囱冒黑烟,也不要因空气过量而增加热量损失;
第三、保证锅炉安全运行。
在该控制系统中,可选用的操纵变量也由3个:
燃料量、送风量和引风量。
组成的燃烧系统的控制方案要满足燃烧所产生的热量,适应蒸汽负荷的需要;使燃料与空气量之间保持一定的比值,保证燃烧的经济性和锅炉的安全运行;使引风量与送风量相适应,保持炉膛一定的负压,以免负压太小,甚至为正,造成炉膛内热烟气往外冒出,影响设备和工作人员的安全;如果负压过大,会使大量冷空气漏进炉内,从而使热量损失增加。
此外,还需防止燃烧嘴背压太高时脱火,燃
烧嘴背压太低时回火的危险。
3.2锅炉燃烧控制系统的组成
锅炉燃烧控制系统由主蒸汽压力控制系统和炉膛负压控制系统。
主蒸汽压力控制系统又包含燃料控制系统和送风控制系统,由于这两个控制系统是紧密联系的,所以一般不将它们分开讨论;在炉膛负压控制系统中,送风量对炉膛压力的影响很小,炉膛压力主要是靠引风机来调节的,所以有时它也被称为引风控制系统。
在整个锅炉燃烧控制系统中,蒸汽压力的变化表示锅炉蒸汽的产生量与负荷的耗汽量不相适应,因此必须相应的而改变燃料的供应量,以改变锅炉蒸汽的产量。
当燃料改变时,必须相应的改变送风量,使燃料量与空气量相适应,保证燃烧过程有较高的经济性。
同时,当送风量改变时,也应该相应的改变引风量,从而使得炉膛压力保持在-20Pa左右。
3.2.1主蒸汽压力控制系统
本炉采用中间储仓式制粉系统,其特点是制粉系统出力的变化并不直接影响锅炉的负荷。
当锅炉负荷发生变动时,是通过改变给粉机转速进行的。
当锅炉负荷变化,调节给粉机转速时,给粉量的增减应缓慢进行,调节范围不易太大。
若转速过高,不但会因煤粉浓度过大堵塞一次风管,而且容易使给粉机超负荷。
若转速过低,则在炉膛温度不太高的情况下,由于浓度不足,着火不稳,容易发生熄火。
给粉机的转速控制在300~800r/min的范围内。
调整给粉机转速的同时,应注意调整送、引风量,保持汽压和汽温的稳定。
增加负荷时,先增加风量,随之增加给粉量;减负荷时,先减少给粉量,随之减少风量,并使同层给粉机的下粉量一致,以便于配风。
当外界负荷变化而需要调节锅炉出力时,随着燃料量的改变,锅炉的风量也需要作出相应的调节。
在锅炉运行中,实际进入炉内的空气不可能全部与燃料接触并发生完全反应。
为了减少化学不完全燃烧热损失和烟气热损失,获得良好的燃烧效率,实际送入炉内的空气量通常比理论计算空气量多一些,两者之比称为过量空气系数α。
过量空气系数的控制是通过烟气分析仪测量烟气中的O2成分来实现的。
由于目前普遍采用氧量计,过量空气系数α与烟气中O2含量关系如式3-1所示:
(3-1)
式中O2—烟气中的含氧量,%;
α—过量空气系数。
因此运行人员可直接根据氧量表的数值来控制送入炉膛内空气量,而不必换算过量空气系数。
从运行经济来看,在一定范围内,随着炉膛内过量空气系数的增大,可以改善燃料与空气的接触和混合,有利于完全燃烧,使化学不完全燃烧损失降低。
但是,当过量空气系数过大时,则因炉膛温度降低和烟气流速加快使燃烧时间缩短,可能使不完全燃烧损失反而增加,而烟气热损失则总是随着过量空气系数的增大而增加的。
所以,过量空气系数过大时,锅炉总的热损失就要增加,与此同时,还将使送、引风机的电耗增大。
合理的过量空气系数应使各项热损失之和为最小。
从锅炉工作的安全性来看,炉内过量空气系数过小,会使燃料燃烧不完全,造成烟气中含有较多的未燃尽炭黑和一氧化碳可燃气体等,在尾部烟道可能发生可燃物在燃烧。
由于灰分在还原性气体中熔点降低,易引起炉内结渣以及高温硫腐蚀等不良后果。
过大的过量空气系数使煤粉炉受热面管子和引风机叶片的磨损加剧,影响设备的使用寿命。
此外,过量空气系数增大时,由于过剩氧的相应增加,将使燃料中的硫形成三氧化硫,烟气露点也相应提高,从而使空气预热器发生腐蚀。
同时,烟气中的氧化氮也将增多,影响排放指标。
总之送风量过大或过小都会给锅炉的安全运行带来不良的影响。
锅炉总风量的调节是通过改变送风机的出力来实现的。
本炉所使用的送风机为轴流风机,通过改变风机动叶角度来调节风量。
在锅炉的风量控制中除了改变总风量外,一、二次风的配合调节也是十分重要的。
一、二次风的风量分配应根据它们所起的作用进行调节。
一次风量应已能满足进入炉膛的分粉混合物挥发燃烧及固体焦炭的氧化需要为原则,二次风量不仅应满足燃烧需要,而且还应起到补充一次风末段空气量不足的作用。
此外,二次风应能与进入炉膛的可燃物充分混合,这就需要较大的二次风速,对高温火焰起到搅拌混合的作用,以强化燃烧。
当两台风机均运行时,在调节风量的过程中,通常应同时改变两台风机的风量,并注意观察电动机的电流以及风机出口压和风量是否同步变化,并防止轴流风机进入不稳定区域运行。
风量调节时,还应通过炉膛出口氧量的变化,来判定是否已满足需要。
高负荷情况下,还应注意防止电动机的电流。
3.2.2炉膛压力控制系统
炉膛压力是反应燃烧工况稳定与否的重要参数。
炉内燃烧工况一旦发生变化,炉膛压力将迅速发生相应的变化。
当锅炉的燃烧系统发生故障时,最先将在炉膛压力的变化上反应出来,而后才是蒸汽参数的一系列变化。
因此,监视和控制炉膛压力,对于保证炉内燃烧工况的稳定具有及其重要的意义。
炉膛负压过大,将会增加炉膛和烟道的漏风,锅炉在低负荷或燃烧工况不稳的情况下运行时,便有可能由于漏入冷风而造成燃烧恶化,甚至发生锅炉熄灭。
反之,若炉膛压力偏正,则炉膛内的高温火焰就有可能外喷,不但影响环境卫生还将造成设备损坏或引起人身事故。
运行中引起炉膛负压波动的主要原因是燃烧工况的变化。
为了使炉内燃烧连续进行,必须不间断的向炉膛供给燃料燃烧所需的空气,并将燃烧后产生的烟气及时排走。
在燃烧产生烟气及其排放的过程中,如果排出炉膛的烟气量等于燃烧产生的烟气量,则进、出炉膛的物质保持平衡,此时炉膛负压就相对保持不变。
若上述平衡遭到破坏,则炉膛负压就要发生变化。
例如在引风量未变时,增加送风量,就会使炉膛出现正压。
运行中即使送、引风量保持不变,由于燃烧工况总有小量的变化,故炉膛压力总是波动的。
当燃烧不稳时,炉膛压力将产生剧烈的波动,炉膛风压表相应作大幅度的剧烈晃动。
运行经验表明:
当炉膛压力发生剧烈波动时,往往是熄火的预兆,这时必须加强监视炉内燃烧工况,分析原因,并及时进行调整和处理。
炉膛压力通常是通过改变引风机的出力来调节的。
引风机的风量调节方法要求和送风机基本相同。
3.3锅炉燃烧控制系统中被控变量的选择
被控变量的选择是控制系统设计的核心问题,选择得正确与否,会直接关系到生产的稳定操作、产品产量和质量的提高以及生产安全与劳动条件的改善等。
如果被控变量选择不当,不论采用何种仪表,组成什么样的控制系统,都不能达到预期的控制效果,满足不了生产的技术要求。
为此,自控设计人员必须深入生产实际,进行调查研究,只有在熟悉生产工艺的基础上才能正确的选择相互被控变量。
在锅炉燃烧控制系统中包含两个控制系统:
主蒸汽压力控制系统和炉膛压力控制系统,而主蒸汽压力又由主蒸汽压力与燃料流量构成的燃料控制系统和燃料流量与空气流量构成的送风控制系统组成;炉膛压力的变化主要是由引风量的调节来实现的,所以有时,也可以把炉膛压力控制系统称为引风控制系统。
如果想要对该系统进行高效、精确的控制,首先得依次对这三个子控制系统进行被控变量的选择。
在燃料控制系统中,要完成的任务是使燃料流量的变化要随着蒸汽负荷的变化而变化,所以很明显的可以看出在该系统中,被控变量是蒸汽压力(负荷),操纵变量是燃料量;在送风控制系统中,要求保持合理的风、煤配合,才能使锅炉经济的燃烧,所以该控制系统的被控变量是烟气成分,操纵变量是送风量;在引风控制系统中,主要的目的是使炉膛负压能够保持在一定的范围内,从而保证锅炉的安全运行,所以它的控制变量是炉膛负压,操纵变量是引风量。
3.4锅炉燃烧控制系统控制方案的确定
3.4.1主蒸汽压力控制系统方案的确定
蒸汽压力的主要扰动是蒸汽负荷的变化与燃料量的波动。
当蒸汽负荷及燃料量波动较小时,可以采用蒸汽压力来控制燃料量的单回路控制系统,系统方框图如下:
图3.1蒸汽压力控制燃料量的单回路控制系统方框图
但是,从上图我们明显的可以看出:
当燃料流量波动较大时,等到主蒸汽压力控制器感受到这样的偏差去控制调节阀时,燃料量已不是原来的流量了,所以对它的控制总是存在着一定的偏差和滞后的。
所以,要对燃料流量设置一个调节器,让它对干扰进行快速的控制,这便构成了一个串级控制系统。
图3.2蒸汽压力控制燃料量的串级控制系统方框图
当燃料量改变时,必须相应的改变送风量,使燃料量与空气量的比值达到一个最优比以保证锅炉燃烧的经济性。
在这里,不管燃料量还是送风量都应该是可控制的,所以采用的是双闭环比值控制系统,它在提降量上也是很方便的,只要缓慢的改变主流量的给定值,就可以提降主流量,同时副变量也就跟踪提降,并保持两者比值不变。
在该系统中空气量是随着燃料量变化的,所以燃料量是主流量,空气流量是副流量。
图3.3双闭环比值控制系统方框图
通过上述的分析,得到了燃烧过程的基本控制控制方案如下
图3.4燃烧过程的基本控制方案
为了使锅炉能够充分且完全的燃烧:
在蒸汽量要求增加时,应先加大空气量,后加大燃料量;在蒸汽量要求减小时,应先减燃料量,后减空气量。
完成该逻辑提降量是依靠系统中设置的两个选择器:
高选择器HS,低选择器LS。
如图3.5所示。
在正常工况下,即系统处于稳定状态时,蒸汽压力控制器的输出Ip等于燃料流量变送器输出I1,也等于空气流量变送器的输出呈上空气过剩系数K后的值I2。
高、低选择器的两个输入端信号是相等的,整个系统犹如不加选择器时的串级和比值控制组合的系统进行工作。
当系统进行提量时,随着蒸汽量的增加,蒸汽压力减少,压力控制器的输出Ip增加(根据串级控制系统的要求,压力控制器应选用反作用式控制器),这个增加了的信号不被低选器选中,而被高选器选中,它直接改变空气流量控制器的
图3.4燃烧过程的改进控制方案
给定值,命令空气量增加,也就使I2开始增加。
因此时I2这一过程保证在增加燃料量前。
先加大空气量,使燃烧完全。
整个提量过程直至Ip=I1=I2时,系统又恢复到正常工况时的稳定状态。
在系统降量时,蒸汽压力增加,蒸汽压力控制器的输出减少,因而它被低选器选中,作为燃料流量控制器的给定值而命令燃料降量。
燃料降低,经变送器的测量信号为高选器选中,作为空气流量控制器的给定值,命令空气降量,降量过程直至Ip=I1=I2,系统又恢复到稳定状态。
这样就实现了提量时先提空气量,后提燃料量,降量时先降燃料量,后降空气量的逻辑要求。
前面介绍的锅炉燃烧过程的燃料与空气比值控制存在两个不足之处。
首先不能保证两者的最优比,这是由于流量测量的误差以及燃料的质量(水分、灰分等)的变化所造成的。
另外,锅炉负荷不同时,两者的最优比也应有所不同。
为此,要有一个检验燃料与空气适宜配比的指标,作为送风量的校正信号。
通常用烟气中的氧含量作为送风量的校正信号。
锅炉的热效率(经济燃烧)最简便的检测方法,是用烟气中的氧含量来表示。
根据燃烧方程式,可以计算出燃料完全燃烧时所需的氧量,从而可以得出所需的空气量,成为理论空气量QT。
但是,实际上完全燃烧所需的空气量QP要超过理论空气量QT,即需要一定的过剩空气量。
当过剩空气量增多时,不仅使炉膛温度下降,而且也使最重要的烟气热损失增加。
因此,对不同的燃料,过剩空气量都有一个最优值,即所谓最经济燃烧,如图3.5所示。
对于煤粉燃料,最优过剩空气量约为8%~15%。
过剩空气量常用过剩空气系数α来表示,即实际空气量QP与理论空气量QT之比:
(3-2)
因此,α为衡量经济燃烧的一种指标。
α很难直接测量,但与烟气中氧含量有直接关系,可用近似式表示:
(3-3)
式中AO为烟气中的氧含量。
图3.5过剩空气量与能量损失的关系
图3.6示出了过剩空气量烟气中氧含量及锅炉效率之间的关系。
从图中可看出,与锅炉最高效率对应的α在1.08~1.15,AO的最优值为(1.6%~3%)O2。
图3.6过剩空气量与O2及锅炉效率间的关系
根据上述可知,只要在图3.2的控制方案中,对进风量用烟气氧含量加以校正,就可构成图3.5所示的烟气中氧含量的闭环控制方案,在此烟气氧含量的闭环控制方
图3.7烟气中氧含量的闭环控制方案
案中,只要把氧含量成分控制器的给定值,按正常负荷下烟气氧含量的最优值设定,就能使过剩空气