0726 第04章 程序分析3布置与经路分析2ok.docx
《0726 第04章 程序分析3布置与经路分析2ok.docx》由会员分享,可在线阅读,更多相关《0726 第04章 程序分析3布置与经路分析2ok.docx(27页珍藏版)》请在冰豆网上搜索。
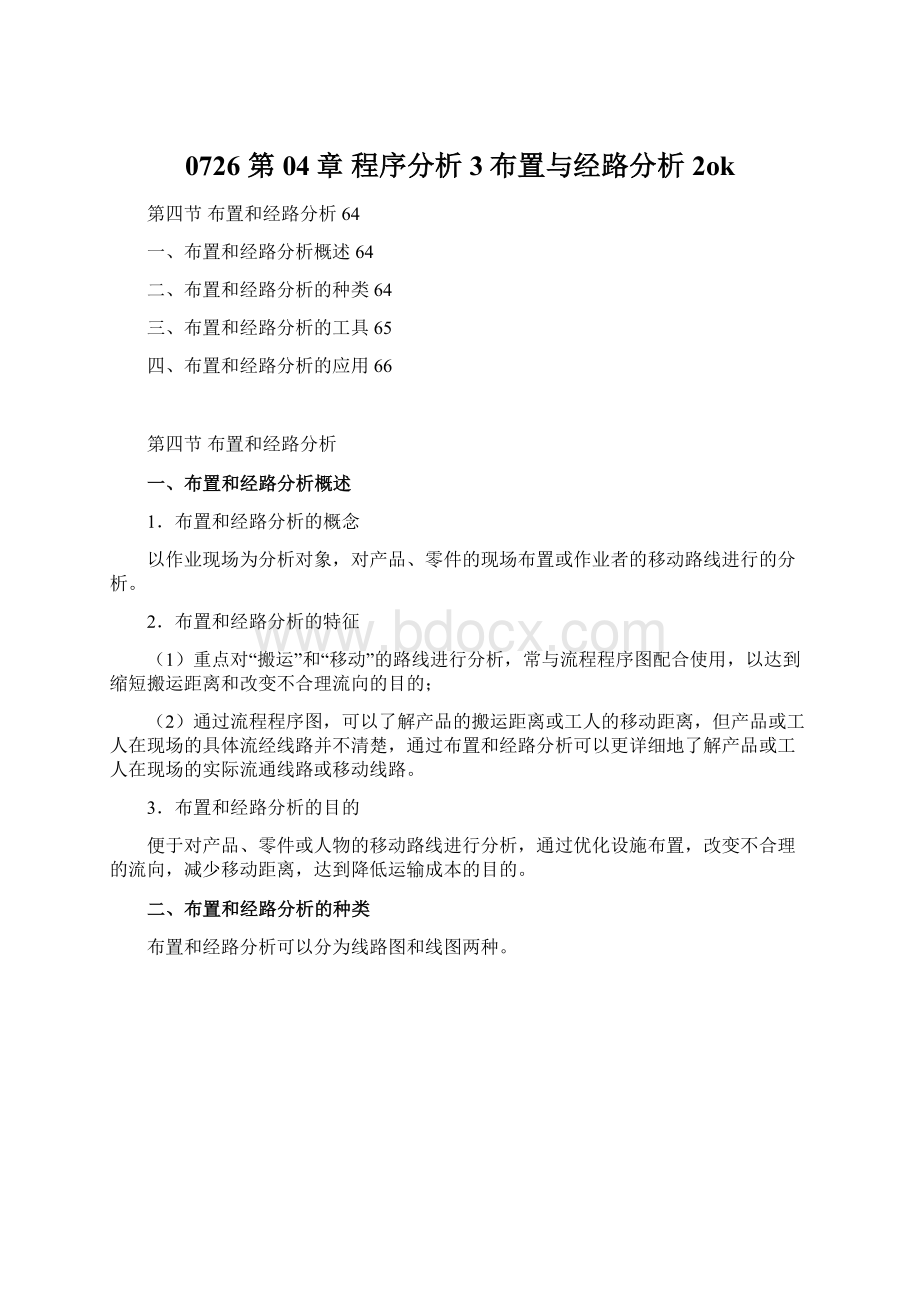
0726第04章程序分析3布置与经路分析2ok
第四节布置和经路分析64
一、布置和经路分析概述64
二、布置和经路分析的种类64
三、布置和经路分析的工具65
四、布置和经路分析的应用66
第四节布置和经路分析
一、布置和经路分析概述
1.布置和经路分析的概念
以作业现场为分析对象,对产品、零件的现场布置或作业者的移动路线进行的分析。
2.布置和经路分析的特征
(1)重点对“搬运”和“移动”的路线进行分析,常与流程程序图配合使用,以达到缩短搬运距离和改变不合理流向的目的;
(2)通过流程程序图,可以了解产品的搬运距离或工人的移动距离,但产品或工人在现场的具体流经线路并不清楚,通过布置和经路分析可以更详细地了解产品或工人在现场的实际流通线路或移动线路。
3.布置和经路分析的目的
便于对产品、零件或人物的移动路线进行分析,通过优化设施布置,改变不合理的流向,减少移动距离,达到降低运输成本的目的。
二、布置和经路分析的种类
布置和经路分析可以分为线路图和线图两种。
1.线路图
线路图是依比例缩小绘制的工厂简图或车间平面布置图。
它将机器、工作台、运行路线等的相互位置一一绘制于图上,以图示方式表明产品或工人的实际流通线路。
绘制线路图时,首先应按比例绘出工作地的平面布置图,然后将流程程序图中表示加工、检查、搬运、储存等的工序用规定的符号标示在线路图中,并用线条将这些符号连接起来。
注意在线与线的交叉处,应用半圆型线避开,如果在制品数量较多,则可采用实线、虚线、点划线或用不同颜色的线条将其区别开来,如果产品或零件要进行立体移动,则宜利用如图4-28所示的空间图来表示。
2.线图
是按比例绘制的平面布置图模型。
用线条表示并度量工人或物料在一系列活动中所移动的路线。
线图是线路图的一种特殊形式,是完全按比例绘制的线路图。
绘制线图时,首先找到一个画有方格的软质木板或图纸,将与研究对象相关的机器、工作台、库房、各工作点以及可能影响移动线路的门、柱隔墙等均按一定的比例剪成硬纸片,然后用图钉按照实际位置钉于软质木板或图纸上,再用一段长线,从图钉钉子起点开始,即第一道工序开始,按照实际加工顺序,依次绕过各点,直至完成最后一道工序为止,最后,将这些线段取下来,测量其长度,并按一定的比例扩大,这样就较准确地测量出该产品或该零件的实际移动距离。
如果同一工作区域内有两个以上的产品或零件在移动,则可用不同颜色的线条来区别表示。
包含线条越多的区域,表示活动越频繁。
图4-29、图4-30是线图的结构形式。
图4-29绕成线图的情形
图4-30线图举例
三、布置和经路分析的工具
布置和经路分析的工具仍然是“5W1H”以及“ECRS”四大原则。
在进行具体分析时,可参考表4-17的内容来辅助思考。
表4-17线路图和线图改善分析表
内容
平面移动
移动距离能否缩小
移动路线是否采用了“—”“L”“U”字形等简单形式或成封闭系统
有没有相向流动
通道和路面状况是否良好
立体移动
高度能否降低
上下移动次数能否减少
是否使用起重设备
厂房设备配置是否合理
物流路线配置是否合理
运输方法是否恰当
运输通道、起重设备、行车路线、作业面积、标识是否符合要求
设备配置是否与工艺路线相适应
占地面积、摆放方向(与通道及采光的关系)是否恰当
车间办公室及检查工序的位置是否合适
四、布置和经路分析的应用
例1:
某汽车制造公司发动机装配所需的螺栓、螺帽都是从外面采购,经检查合格后,接收入库。
分析该汽车制造公司现行外购零件接收与检验流程,了解运输路线,提出改善方案。
1.现状调查
(1)外购件接收、检验与入库线路如图4-31所示。
图4-31外购件接收、检验线路图
(2)外购件接收与检验流程程序如图4-32所示。
流程程序图:
人员/物料/设备型
图号:
作图表的对象:
成箱的汽车发动机连接件,螺栓、螺帽的接收入库
方法:
现行方法
地点:
接收库房
制表人:
日期:
审定人:
日期
统计表
活动
现行的
改良的
节约
操作O
5
搬运
10
等待D
6
检查□
3
储存
1
距离/m
59.5
说明
数量/箱
距离/m
时间/min
符号
备注
O
D
□
1从货车卸下,置于滑板上
1.5
10
·
2人
2从滑板上滑向堆垛处
10
8
·
3堆垛
15
·
2人
4等待启封
—
6
·
5卸箱垛、启封箱子、取出票据
—
7
.·
1人
6置于手推车
1
4
·
2人
7推向收货台
9
3
·
1人
8从手推车上卸下
1
10
·
2人
9置箱于工作台
1
2
·
2人
10从箱中取出纸盒,启封检查
·
1人
11重新装箱
—
4
·
1人
12置箱于手推车上
1
2
·
2人
13待运
—
5
·
14运向检查工作台
16.5
3
·
1人
15待检
5
·
箱在车上
16从箱和盒中取出螺栓、螺帽
1
2
·
检查员1人
17对照图纸检查,然后复原
3
·
19等待搬运工
—
5
·
箱在车上
20推至点数工作台
9
5
·
1人
21等待点数
—
4
箱在车上
22从箱和盒中取出螺栓、螺帽
—
2
·
仓库工1人
23在工作台上点数及复原
5
·
24等待搬运工
—
5
·
箱在车上
25运至分配点
4.5
5
·
1人
26存放
4
·
共计
59.5
120
5
10
6
3
1
图4-32现行外购件检验、点数流程程序图
2.现行布置存在的问题
通过对图4-31的分析,发现现行布置存在以下问题:
(1)搬运、等待和检查次数较多。
从图4-31中的统计分析得知,汽车发动机连接螺栓、螺帽接收工作共有5次加工、10次搬运、6次等待、3次检查和1次储存,搬运、等待和检查次数较多。
(2)运输时间长。
从图4-31可知,零件箱经过了多次运输,最后才运到零件架上,运输距离共59.5m,运输时间120min。
3.制订改善方案
针对现存的问题,运用“5W1H”技术,“ECRS”四大原则和改进分析表4-18进行分析,得出改善方案如下:
表4-18改进分析表
问
答
第3工序堆垛,第5工序卸箱,既然要卸箱为什么需要先码起来
因为卸车比办理接收快,为避免在地上到处都是箱子,只好码起来。
第6工序置于手推车上,第8工序从手推车上卸下,既然要从手推车上卸下,为什么还要放在手推车上去
因为收货台距离卸货处有一定的距离
第11工序为何要重新装箱
因为需要运到下工序去对照图纸进行质量检查,所以需要重新装箱
第20工序为何要推至点数工作台
为了进行数量检验
为何接收、检验和点数要分开
因为接收、检查、点数的地方离得远
为何接收、检查、点数的地方离得那么远
现行布局就是这样
有无更好的办法
有
能将接收、检查、点数合并吗
能
为什么接收物品要绕一圈才能放到零件架上
因为零件架的入口设在检验台那边
能将门设立在接收货物处吗?
能
(1)对接收、检查、点数工序进行了合并;
(2)在接收台的对面开了一个门直接进入库房。
改进后零件接收入库的方法是:
箱子从送货车上卸下后沿滑板直接滑到手推车上,送到开箱处,操作工人直接在手推车上打开箱子,取出送货单,将送货单以及货物运到收货台,等待片刻,打开箱子,将零件从箱子中取出,放到工作台上,检验员对照送货单进行数量和质量检查,检查完毕后,再将零件放回纸盒重新装箱,最后再将零件运入仓库,放置于货架上。
改进后,外购螺栓、螺帽接收、检验和入库流程程序如图4-33所示,运输路线如图4-34所示。
流程程序图:
人员/物料/设备型
图号:
页号:
总页数
总计
图号:
作图表的对象:
成箱的发动机连接件、螺栓、螺帽的接收入库
方法:
改良方法
地点:
接收库房
制表人:
日期:
审定人:
日期
活动
现行方法
改良方法
节约
操作O
5
3
2
搬运
10
5
5
等待D
6
2
4
检查□
3
1
2
储存
1
1
0
距离/m
59.5
28.5
27
说明
数量/箱
距离/m
时间/min
符号
备注
O
D
□
1从货车卸下,置于滑板上
1.5
10
·
2人
2从滑板直接滑向手推车
10
8
·
3推至启箱处
·
4启封箱子、取出票据
—
7
·
1人
5推向收货台
9
3
·
1人
6等待卸车
—
5
·
7从箱中取出纸盒,打开
·
1人
8将螺栓、螺帽置于工作台上
1
2
·
检查员1人
9对照图纸检查以及点数,然后复原
8
·
10等待搬运工
—
5
·
箱在车上
11运至分配点
3
4
·
1人
12存放
4
·
共计
28.5
52
3
5
2
1
1
图4-33改进后外购件检查和点数流程程序图
图4-34改进后外购件检查和点数线路图
4.改进效果
从图4-33的统计表可知,改进后操作次数从原来的5次减少为3次,搬运从原来的10次减少为5次,等待从原来的6次减少2次,检查从原来的3次减少为1次,运输距离从59.5m减为28.5m。
通过改进,获得了较大的效果。
例如2:
某微型汽车制造公司汽缸盖生产线设施布置及物流情况分析改进
1.现状调研
(1)生产概况。
缸体车间共有429名员工,其中一线工人341人,整个车间长94m,宽35m。
布置了两条生产线,一条缸体生产线和一条缸盖生产线,缸体和缸盖均是汽车发动机上的主要零件,年产量20万件。
(2)缸盖生产设施布置简图如图4-35所示。
图4-35缸盖生产线设施布置简图
(2)缸盖加工流程程序如图4-36。
流程程序图:
人员/物料/设备型
图号:
页号:
总页数
统计
地点:
缸体车间编号02对象:
:
缸盖加工
操作人:
日期:
方法:
现行方法
制表人:
日期:
审定人:
日期:
活动
现行方法
改良方法
节约
操作O
26
搬运
32
等待D
12
检查□
5
贮存
2
距离/m
2455.2
说明
距离/m
时间/s
符号
备注
O
D
□
1储存
·
2编号
·
3至铣床
4
·
4铣盖沿面
8.8
·
5搬运到下工序
2.5
·
6粗铣底面
34
·
7搬运到下工序
2.0
·
8钻工艺孔
42
·
9搬运到下工序
3
·
10铣顶面、两侧面,精铣底面
174
·
11搬运到下工序
3.2
·
12铣开档面
98
·
13搬运到下工序
10
·
14铣前后圆弧面
81
·
15搬运到下工序
6
·
16加工缸体定位销孔、螺栓过孔
52
·
17搬运到下工序
10
·
18钻前端盖紧固螺栓孔、摇臂轴孔
63
·
19搬运到下工序
5.4
·
20钻摇臂安装孔、油盖紧固孔
121
·
21运到下工序
3.2
·
22钻铰堵塞孔、10个过孔
61
·
23运到下工序
2.9
·
24加工排气、螺栓孔
56
·
25运至外车间
1200
600
·
…
1200
·
26运回本车间
1200
600
…
…
27精铰气门阀座
161
·
1.5
·
28清洗
·
29水漏试验
17
·
30运到下工序
1.5
·
31油漏试验
65
·
合计
2455.2
3433.8
图4-36缸盖加工流程程序图
2.统计分析
从图4-36统计表可知,整个缸盖加工总加工次数为26次,搬运次数为32次,等待次数为12次,搬运距离为2455.2m,加工时间为3433.8s。
3.现行布置存在的问题
(1)搬运距离太长。
该缸盖生产线是由国内各机床厂填平补齐、单机组合成的一条生产线,设计不合理,制造精度低,生产线上各机床能力不匹配,存在严重的不合拍现象。
而且,该生产线已经使用了近10年,设备陈旧、老化,其中的孔加工设备已基本不能正常加工。
因此,缸盖在该生产线上完成面加工后,需要运至1200m以外的外车间进行孔加工,然后再运回本车间进行余下工序的加工,从而造成每生产一件缸盖,在车间外的运输距离就长达2400m。
在车间内的运输距离由两部分组成:
一部分是生产线上各工序间的正常运输距离,有115m;另一部分是由于工序安排不合理或设备布置不合理造成零件往返运输距离为120m。
每生产一件缸盖,所必须完成的辅助运输距离为2520m,是生产线实际运输距离的22倍。
年产20万件缸盖,则每年用于辅助运输缸盖的距离高达20万件×2520m=504000km。
(2)在制品数量多。
由于车间内外搬运距离长,不仅造成了人力、物力的大量浪费,而且还造成了车间内部在制品的大量积压。
现场发现,有些工序在制品积压高达200件。
(3)加工辅助时间长,劳动强度大,耗费资源多。
缸盖生产共有35道工序,在缸盖车间要进行27道工序的加工。
各工序间的运输靠上、下工序操作者双手搬运,上工序加工完成之后,操作者将工件放于地面上堆垛,下工序操作者再从地面上取工件后进行加工,直至所有工序加工完毕。
为了完成每道工序的加工,需要取、放工件各1次,弯腰2次。
我们用秒表测时发现,每取一次工件的时间为8s,每放一次工件的时间为6s,完成一件缸盖的加工,花费在取、放零件上的时间总共为14s/道工序×35道工序=490s。
如果日产量为440件,则在缸盖的加工过程中每天用于取、放零件的时间总共为490s/件×440件=59.8h,如果时间利用率为0.9,工人每天制度工作时间为8h,则每天需要59.8h×0.9÷8h/人=8.3人专门从事加工过程中取、放零件工作,而且每个操作工人每天平均需要弯腰2次/件×440件=880次,极易造成工人身心疲劳,影响生产效率的提高。
4.提出改进方案
通过对现存问题的分析,运用“5W1H”技术和“ECRS”四大原则,提出改善方案如下:
(1)在原缸盖生产线上新增添了必要的孔加工设备;
(2)重新布置了清洗机的位置;
(3)在车间内部零件的运输采用滚柱运输带,靠机械动力来传送工件,改进后缸盖生产线的设施布置如图4-37所示。
图4-37改进后缸盖生产线设施布置简图
5.改进效果
(1)缩短了运输距离。
改进后生产线长度只有77m,宽13m,共有设备36台,两班制工作,每年可减少车间外的运输距离为480000km。
(2)减少了人员,降低了成本。
改进前生产线上有员工121人,改进后实行两班制工作,只需要100名员工,工人平均每人工资9100元/年,年节约人力成本19万元。
(3)降低了工人的劳动强度。
由于实行了流水线作业,操作过程中,勿需工人频繁弯腰,每年每个工人可少弯腰22万次(年有效工作时间按254天计算),大大地降低了工人的劳动强度;
(4)缩短了生产周期,在相同的工作时间内提高了生产产量;
(5)需要投资建立输送带和重新布置设备,但为今后发展的需要,这些投资是值得的。
例如3:
某发动机分厂装配车间设施布置分析研究
1.现状调查
(1)平面布置
该发动机装配车间是一个靠嘉陵江边,长100m的四层楼房。
其空间物流布置如图4-38所示。
一楼在公路平面以下,是清洗和包装场地;二楼与公路平面一致,是当天装配发动机所需的全部零部件的临时库房和分拣库房;三楼和四楼是发动机两条总装线。
由于历史的原因,装配车间距离机加工车间大约1000m。
当天发动机装配所需要的零部件都需要预先运到二楼临时库房,再分别由左、右两部电梯运到三楼或四楼总装配线进行装配。
左边电梯主要负责运送离合器壳体和产成品,右边的电梯主要负责运送其余所有零部件,装配完成后由左边电梯运到一楼,再前运到35m处的磨合车间进行“三漏”试验,试验完毕后返回一楼包装待运。
图4-38现行的物流路线和设施布置简图
2.统计分析
从图4-38可知,零件的物流路线太长,实际测量了发动机主要零件从二楼临时库房到三楼和四楼总装配线的运输距离如表4-19所示。
表4-19主要零件从二楼临时库房到装配线的距离
零件名
楼层
从二楼临时库房到总装配线距离/m
从总装配线线到磨合车间距离/m
平均距离/m
总平均距离/m
缸体
三楼
110
-
87.5
91.25
四楼
65
-
缸盖
三楼
85
-
77.5
四楼
70
-
曲轴
三楼
90
-
82.5
四楼
75
-
连杆
三楼
135
-
117.5
四楼
100
-
产成品
三楼
45
52
四楼
59
注:
1.三楼和四楼装配线的布置和起点不一样,零件运到三楼后,还需要前运几十米才能到达装配起点。
因此,运往三楼的距离比运往四楼的距离要长。
2.不同的零件由于在临时库房堆放的位置不同,运送总装线的位置也不同。
因此,距离有所不同。
3.现行布置存在的问题
从表4-19的统计数据可知,零件平均运上生产线的距离为91.25m,每台发动机由256个零件所组成,大小数量共计779个,重量达115kg。
假设手推车需要5次才能将一台发动机所需要的全部零件从二楼临时库房分别运到三楼和四楼装配现场,则装配每台发动机零件的运输距离为:
5次×91.25m/次=456.25m。
若日产发动机440台,则每天需要将零件从二楼临时库房运送到三楼或四楼总装配线的运输距离为440台×456.25m/台=200.75km。
将从发动机总装线下线的产成品,运往磨合车间的运输距离为440台×52m/台=22.88km。
若负责运送零件的工人平均每天的移动距离是10km,则每天需要200.75km÷10km/人=20人专门从事将零部件运送到总装线的工作;每天需要22.88÷10=2.3人专门从事将产成品运到磨合车间的工作。
每条生产线现有装配工人47人,两条装配线有操作工人94人,其中专门从事运输的工人就占22.3人,占生产线工人人数的23.7%。
通过以上分析,发现现行布置存在如下问题:
(1)零件从二楼临时库房运到装配线的距离太长,每天高达200.75km;
(2)产成品从装配线运到磨合车间的距离长,每天累计达22.88km;
(3)专门从事将零部件运送到总装线上的人多,达22.3人,是装配线实际操作工人的23.7%;
(4)专门从事将产成品运到磨合车间的工人有2.3人,是装配线实际操作人数的2.4%;
(5)运输工作量大,运输成本高。
因此,需要对现行的设施布置进行改进,应尽量避免空间运输和不必要的额外运输,将装配线布置在水平面上,并按直线、直角、U型、环型、山型或S型布置,使其占地面积最小,物流路线最短,运输成本最低。