铝储罐的焊接工艺设计.docx
《铝储罐的焊接工艺设计.docx》由会员分享,可在线阅读,更多相关《铝储罐的焊接工艺设计.docx(27页珍藏版)》请在冰豆网上搜索。
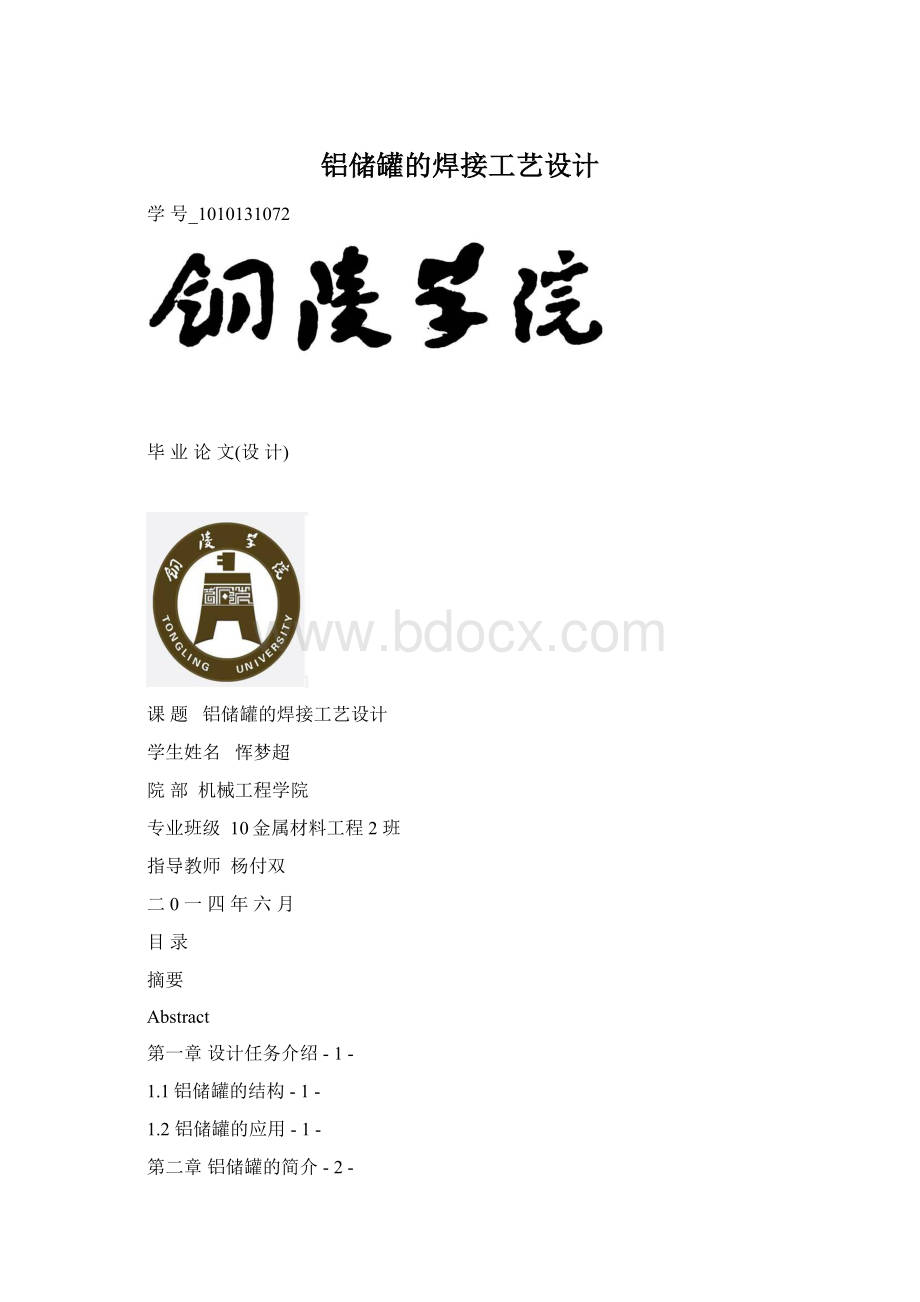
铝储罐的焊接工艺设计
学号_1010131072
毕业论文(设计)
课题铝储罐的焊接工艺设计
学生姓名恽梦超
院部机械工程学院
专业班级10金属材料工程2班
指导教师杨付双
二0一四年六月
目录
摘要
Abstract
第一章设计任务介绍-1-
1.1铝储罐的结构-1-
1.2铝储罐的应用-1-
第二章铝储罐的简介-2-
2.1铝储罐的介绍-2-
2.2铝储罐的结构特点-2-
2.2.1球型容器的特点-2-
2.2.2圆筒型容器的特点-2-
2.3材料的介绍-2-
第三章选用焊接方法的比较-3-
3.1TIG焊-3-
3.1.1焊接原理-3-
3.1.2焊接工艺-3-
3.2MIG焊-4-
3.2.1焊接原理-4-
3.2.2焊接工艺-6-
3.3焊接方法的选用-6-
第四章焊接缺陷及解决方法-7-
4.1焊缝气孔-7-
4.1.1气孔的成分-7-
4.1.2氢的来源-7-
4.1.3气孔的预防-7-
4.2焊接裂纹-8-
4.2.1焊接裂纹的性质-8-
4.2.2裂纹特征-8-
4.2.3焊接裂纹的危害-8-
4.2.4焊接裂纹的影响因素及防治措施-8-
第五章铝储罐的焊接制造工艺设计-11-
5.1焊接工艺设计-11-
5.1.1.备料-11-
5.1.2.焊接设备及焊接材料的选用-11-
5.1.3.焊前准备-12-
5.1.4.工艺装备的准备-14-
5.1.5.组装与焊接-16-
5.2铝储罐的焊后检验-21-
5.3焊后处理-21-
结论-22-
参考文献-23-
致谢-24-
铝储罐的焊接工艺设计
摘要
与其他金属相比较,铝及铝合金具有独特的和优异的物理特性、化学特性、力学特性及工艺特性,能适应现代科技及高新工程发展的需要,广泛地应用于制造各类工业产品。
目前,铝及铝合金的焊接技术已经有了长足的进步。
铝及铝合金焊接结构已成为我国民用及军工产品上的重要组成部分。
本次设计的铝储罐用来储存的是98%的浓硝酸,因此对铝储罐具有较高的要求。
首先,本文介绍了铝储罐的结构及应用并对铝储罐进行了简单的介绍,然后对焊接方法的选用进行了比较分析并对铝储罐中可能出现的缺陷提出解决方法。
最后从铝储罐的结构工艺、焊接工艺、铝储罐的焊后检验及焊后处理这四个方面着重介绍铝储罐的制造工艺。
关键词:
焊接缺陷;结构工艺;焊接工艺;检验;焊后处理
Designofweldingprocessof aluminum tank
Abstract
Comparedwithothermetals,uniqueandphysicalproperties,excellentchemicalproperties,mechanicalpropertiesandprocessingpropertiesofaluminumandaluminumalloywith,canadapttotheneedsofthedevelopmentofmodernscienceandtechnologyandhigh-techprojects,iswidelyusedinmanufacturingallkindsofindustrialproducts.Atpresent,aluminumandaluminumalloyweldingtechnologyhasbecomeanimportantpartofourcivilandmilitaryproductsonthealuminumanaluminumalloywelding.
Thedesignofthe aluminum tank usedtostore is 98%concentratednitricacid, soithashigh requirements onaluminum tank. Firstofall, thispaper introducesthe structureand applicationofaluminum andaluminum tank to tank areintroduced, Thenhascarriedonthe comparativeanalysis andproposesthesolutionstothepossibledefectsinthe aluminum tank on selectionofwelding method . Finalinspectionfromthe technologyofweldingstructure, aluminumtank process, aluminumtankafterweldingandafterweldingtreatmentofthesefouraspectsemphaticallyintroducesthemanufacturingprocessofaluminumtank.
Keywords:
Weldingdefects;Structureprocess;Weldingtechnology;Test;Afterweldingtreatment
插图清单
图1-1罐体的结构示意图……………………………………………………………………..1
图3-1短路过程和电流以及电压波形………………………………………………………..5
图3-2大滴过渡示意图………………………………………………………………………..5
图3-3喷射过渡示意图………………………………………………………………………..6
图4-1焊缝成形系数对焊缝热裂的影响……………………………………………………..9
图5-1坡口形式及尺寸………………………………………………………………………..13
图5-2焊接试板、引弧板和引出板与筒节的组装情况……………………………………..17
图5-3焊丝直径、焊接电流、送丝速度之间的关系………………………………………..19
图5-4合适的电弧电压与焊接电流的配合…………………………………………………...19
表格清单
表3-1钨极许用电流…………………………………………………………………….…..4
表5-1焊丝型号……………………………………………………………………………..11
表5-2铝储罐坡口化学清洗的工艺参数…………………………………………………..14
表5-3EB-10TN型可调式焊接滚轮架的技术参数......................................................15
表5-4自动MIG焊焊接参数……………………………………………………………....20
表5-5半自动MIG焊焊接参数…………………………………………………………....21
第一章设计任务介绍
1.1铝储罐的结构
设计的铝储罐最重要的组成部分是封头、筒体、接管、人孔等。
其中筒体部分又分为3节,并且每1节是由两块厚度为6mm的工业纯铝1060板材经过焊制而成的。
位于两端的封头则是由厚度为8mm的工业纯铝1060板材经压制而成的【1】。
容器容积为4m³,储罐的结构如图1-1所示。
图1-1罐体的结构示意图
1.2铝储罐的应用
主要用于98%的浓硝酸(HNO3)在常温常压下的贮存。
第二章铝储罐的简介
2.1铝储罐的介绍
铝储罐是变形铝合金在容器工业中的应用,由于用的材料是变形铝合金,其具有良好的抗腐蚀性、无吸附性和能防止碎裂,因此,在化工行业中可用于储存不宜散装的化学试剂【2】。
2.2铝储罐的结构特点
在化工行业中通常是用圆筒型容器或球型容器来盛装介质。
2.2.1球型容器的特点
承压能力较强为球型容器的最大特点,如果容器使用同样的材料并且板材厚度一样,则圆筒型容器承受压力的能力要比球型容器低2倍。
由于球型容器的壳体呈球面,制作比较麻烦,且成本比较高,并且由于本次铝储罐设计的工作条件是在正常的温度和压力下,因此,不应该使用球型容器【1】。
2.2.2圆筒型容器的特点
圆筒型容器承受压力的能力相对较好,制造工艺相对简单,安装方便,成本相对较低,因此设计选用圆筒型卧式的型式,见图1-1
2.3材料的介绍
1060工业纯铝的耐蚀性、表面处理特性、加工性较强且强度较小,通常是在日用品及电器上使用较多。
但是随着1060工业纯铝中杂质物Fe、Si的减少,其耐蚀性会得到改善,通过阳极处理之后,1060工业纯铝的表面会变得非常光亮,常用于工业罐体、化学、反射板等【2】。
第三章选用焊接方法的比较
除了CO2气体保护焊以外,可以用来对铝及铝合金进行焊接的方法有很多,然而每一种焊接方法都在特定的场合有着各自的应用。
本次设计主要考虑惰性气体保护焊,TIG焊和MIG焊都属于惰性气体保护焊,铝及铝合金的焊接通常是用这两种焊接方法【3】【4】。
3.1TIG焊
3.1.1焊接原理
钨极氩弧焊的焊接是采用脉冲交流电源、直流电源、交流电源、变极性方波脉冲交流电源。
下面主要介绍直流电源和交流电源【2】【5】【6】。
(1)直流电源
直流电源分为直流正接和直流反接,当采用直流正接焊接铝及铝合金时。
钨极的电子发射能力很强,可以发射出大量的电子流,在电场的作用下,钨极发射出来的高能量的电子流以高速冲击焊件并且将全部的能量交付给焊件,使其深熔,进而形成了深而窄的焊缝。
但是由于电子自身的质量很小,电子流对焊件的冲击不能破除焊件表面的氧化膜。
此外虽正离子流奔向钨极,使其发热,但是由于钨极自身具有冷却功能,因而钨极不致于过热烧坏。
直流反接的接法与正接相反,这种焊接的方法具有阴极清理的作用,但是由于焊接时钨极已不具有自身冷却功能,钨极会发生过热甚至是熔化,从而使得在操作中不得不限制焊接电流的大小并且反接时电弧的稳定性较差,使焊接的效率变低。
(2)交流电源
为了使焊接工艺具有阴极清理的同时也不致使钨极过热,所以采用交流钨极氩弧焊。
交流电流的极性是周期变化的,在任何周期中,半波相当于直流反接,半波相当于直流正接。
在正接的过程中钨极不致于过热,因此可以承载较大的焊接电流,有利于电弧的稳定性,容许的可焊接厚度也随着增加,在反接的过程中具有阴极清理作用,可以去除焊件的表面氧化膜,确保焊缝的良好成形。
3.1.2焊接工艺
(1)钨极
铝及铝合金钨极氩弧焊的选材主要有铈钨、锆钨、钍钨、纯钨等。
钨的熔点为3400度。
是目前为止最好的一种不熔化的电极材料,具有非常强的电子发射能力。
纯钨电极的熔点高并且不易熔化和挥发,但是电子发射能力不是很高,同时载流的能力也比较低,抗铝污染性能比较较差,因此现在基本很少使用。
钍钨电极中含有氧化钍,电子的发射能力比较强,允许的电流密度也比较大,寿命加长,同时还具有易引弧,抗铝污染性较好,电弧稳定的特点,但是由于价格比较高和具有微量的放射性,导致应用范围得到限制。
锆钨的电极含有1%左右的氧化锆,具有强的载流能力,抗铝污染性,能够保持电极端部的形状,不容易产生焊缝夹钨。
铈钨是我国工业部门广泛采用的电极,具有放射性小,抗氧化性好,化学稳定性好、能允许的电流密度大、烧损率低、逸出功低、弧长长、电弧稳定等优异的特点。
一定直径的钨极有相应的极限电流,若超过极限电流则会出现钨极过热、熔化甚至蒸发,引起电弧不稳定、焊缝夹钨等问题。
如下表3-1所示:
钨极许用的电流。
表3-1钨极许用电流
电极直径
电流/A
交流/A
正接(电极-)
反接(+)
纯钨
钍钨、铈钨
纯钨
铈钨、钍钨
纯钨
钍钨、铈钨
0.5
2~20
2~20
—
—
2~15
2~15
1.0
10~75
10~75
—
—
15~55
15~70
1.6
40~130
60~150
10~20
10~20
45~90
60~125
2.0
75~180
100~200
15~25
15~25
65~125
85~160
2.5
130~230
160~250
17~30
17~30
80~140
120~210
3.2
160~310
225~330
20~35
20~35
150~190
150~250
4.0
275~450
350~480
35~50
35~50
180~260
240~350
5.0
400~625
500~675
50~70
50~70
240~350
330~460
6.3
550~675
650~950
65~100
65~100
300~450
430~575
3.2MIG焊
3.2.1焊接原理
电弧是在焊丝电极与工件之间并且在氩气的保护下产生的强烈持久的放电现象,电弧将电能转化成热能然后用于熔化焊丝及工件。
一般焊丝的熔化的热能来自三个区,分别为阴极区、弧柱区和阳极区的产热以及焊丝自身的电阻产生的热量但是其中焊丝的电阻发热和弧柱区的产热对焊丝的加热和熔化所起得作用不是很大。
主要使焊丝受热和熔化的热源来自阴极区和阳极区。
这两个电极区的产热主要与电极材料的种类、电流大小以及保护气体氩有关。
但是MIG焊一般不采用直流正接和交流电流【2】【5】【6】。
MIG焊中一个重要的部分是熔滴过渡,其形式有下列三种,即短路过渡、大滴过渡和喷射过渡
(1)短路过渡
短路过渡一般在电压较低,电流较小时,这时候的焊丝熔滴在未脱离焊丝端头前即与熔池发生直接接触,在电弧瞬间熄灭,熔滴由于受到液态金属的表面张力和短路电流产生的电磁力的共同作用下会被拉入熔池,然后焊丝端头会与熔池完全脱离开来,电弧重新得到引燃,准备下一次的短路过渡。
短路过渡的发生频率可达到每秒20~200次,图3-1为短路过渡过程和相应的电流和电压波形。
图3-1短路过度过程和电流以及电压波形
(2)大滴过渡
大滴过渡是在所使用的平均电流等于或者高于短路过渡时并且熔滴直径大于焊丝直径的情况下才称为大滴。
大滴过渡在焊丝端头不停的摇摆,最后因为质量太大,表面张力支持不住,在重力的作用下滴落到熔池。
如图3-2,频率为每秒钟过渡的几个大滴,称为大滴过渡,因为其过程很不稳定、焊接成形差、容易产生很大的飞溅以及未熔合、未焊透或者焊缝余高过大,所以在焊接过程中一般限制使用大滴过渡形式。
图3-2大滴过度示意图
(3)喷射过渡
喷射过渡是在进一步加大电流时,电弧力也随之加大,熔滴尺寸越来越小,当电流加大到某个值时,焊丝直径会与熔滴尺寸非常接近。
在由大滴到小滴的转变时的电流称为临界电流。
此时电弧的形态和熔滴过渡的特点发生明显的变化,弧柱呈钟罩型,小滴变成球状。
喷射过渡分为两种过渡,第一种为射滴过渡,是在电弧力的作用下,熔滴即沿轴向高速射向熔池。
这种过渡飞溅不大,焊缝成形比较良好,熔透形状呈弧形。
另一种为射流过渡,其在电流仍进一步加大时,直到临界点以上熔滴尺寸变的更小仅为焊丝直径的1/5到1/3,弧柱呈锥状,细小的熔滴沿着焊丝的顶端一个接着一个地以束状液流方式射进熔池。
这种过渡形式焊丝和工件不会短路,没有飞溅,电弧非常的稳定。
两者的过程如图3-3所示:
图3-3喷射过渡示意图
a)射滴过渡b)射流过渡
3.2.2焊接工艺
(1)保护气体的选择
在使用MIG焊时,通常是使用氩气或氦气作为保护气体。
在通常情况下,优先选用氩气进行MIG焊焊接。
(2)接头形式的选择
铝及铝合金的焊接工艺、熔滴过渡方式、焊件位置、焊件的尺寸决定了接头形式和其相关的尺寸
在单面焊接时,若零件的厚度小于6mm,通常情况下采用无坡口对接,若零件厚度大于6mm,我们可以采用V形坡口对接。
在对铝及铝合金进行焊接时,为了防止产生未熔合的现象,V形坡口的角度一般小于90°。
零件钝边和对接间隙的尺寸要根据熔滴过渡形式做出相应的改变,在射流过渡时,因为熔深较大,间隙应当较小而钝边应当加大;在短路过渡时,间隙应当较大,钝边应当较小。
3.3焊接方法的选用
从钨极许用电流和“阴极清理”作用两方面考虑,通常是用钨极氩弧焊。
氩弧焊电流稳定、热量集中、其焊缝组织致密、成形美观、强度和塑性高,并且工件变形小。
但是,由于钨极许用电流的限制,电弧的生产率比较低,熔透力比较小。
因此常用于板厚在6mm以下薄板的焊接。
熔化极氩弧焊(MIG)的热影响区小、电弧功率大、热量集中、生产率比钨极氩弧焊高三倍以上。
因此适用于焊接厚板结构,可用于50mm以下铝及铝合金板材的焊接,可不预热焊接30mm厚的铝板。
碳素钢和低合金钢的热导率和比热容均比铝及铝合金高两倍多。
奥氏体不锈钢的热导率比铝低十几倍。
在焊接过程中,有更多的热量消耗于金属的其他部位,为了提高焊接接头的质量,应当尽量采用功率大、能量集中的能源。
TIG焊与MIG焊相比较,MIG焊的最小加热面积为10-4cm2,最大功率密度为104~105w·cm-2,TIG焊的最小加热面积为10-3cm2,最大功率密度为1.5~104w·cm-2,因此选用MIG焊较好【6】【7】【8】【9】。
第四章焊接缺陷及解决方法
焊接接头的主要焊接缺陷是焊接裂纹和焊缝气孔【2】【3】。
4.1焊缝气孔
4.1.1气孔的成分
从焊缝孔隙直接提取并分析的结果证实,气孔的主要成分为氢。
因此,铝及铝合金焊缝气孔有时被称为氢气孔。
4.1.2氢的来源
惰性气体保护焊时的氢源很多,焊接时的填丝、母材和弧柱气氛是氢的三大载体。
由弧柱气氛方面引起的氢气孔的原因可能有:
(1)瓶装惰性气体中超标的氢和水分。
(2)因惰性气体管路和冷却水管路潮湿或不密封而混入弧柱气氛中的空气、潮气和水分。
资料表明,弧柱的氢源是不难识别、消除和防止。
铝材的氢源可能有:
(1)因铝材熔炼生产中除气不尽而使其本身含有固溶于其内的超标氢。
(2)铝材加工过程中粘附于其表面的油物、碳氢化合物或其他含氢的表面污染物。
(3)铝材表面的氧化膜及吸附的潮气和水分。
通过查阅相关资料,导致焊缝内生成气孔的主要因素是母材及填丝方面的氢源[2]。
4.1.3气孔的预防
预防气孔是一个复杂的难题。
查阅相关资料和书籍,可选用下列措施来预防气孔:
(1)母材及焊丝母材的氢含量和焊丝的氢含量应控制在每100g金属不超过0.4mL。
零件表面应该经机械清理或化学清洗,以去除油污及含水氧化膜。
零件清理或清洗后,用干燥、洁净、不起毛的织物或聚乙烯薄膜胶带将坡口及其临近区域覆盖好,防止其随后沾污。
必要时临焊前再用焊枪向坡口吹氩,吹除坡口内刮屑,然后施焊。
零件表面清洗后,存放待焊时间不超过4~24h,否则需再次清洗。
焊丝表层的氢污染危害比母材更大,因为其表面积的比值甚大。
因此,消除焊丝表层氢污染更为重要。
最好的办法是采用抛光的焊丝,其表面光滑、光洁、光亮,拆封后无需任何清理即可用于焊接。
(2)惰性气体采用的纯氩应符合国家标准:
φ(H2)<0.0001%;φ(H2O)<0.02%;φ(O2)<0.1%;露点:
不高于-55℃
(3)惰性气体管路管路应气密。
材料最好不要用塑料,因为有些塑料气密性差,最好采用不锈钢管,管路连接不用螺纹球头连接,而应采用焊接或钎焊连接。
管路端部与焊枪之间的柔性软管最好采用聚三氟氯乙烯塑料管,它的密封性相对于其他塑料管更好。
(4)焊枪结构由于焊枪结构内需接冷却水管,应确保其管接头不会漏水。
当操作环境较为潮湿,可先用加热过的氩气对气体管路进行吹通,以去除管壁上可能附着的水分。
也可采用试板进行氩弧焊接试验,要根据实际情况来定性检查惰性气体的露点、保护效果和纯度,同时也可以对气体管路和焊枪中的冷凝水进行清除。
(5)现场环境铝及铝合金焊接生产厂房内的环境温度不宜超过25℃,相对湿度不宜超过50%,尽量为焊接工作创造一个好的环境同时应保持现场整齐清洁。
在装配及焊接过程中操作人员身上的油污及手迹、汗迹含有碳氢化合物,也是氢源。
因此,在接触、加工、焊接时,必须穿戴白色衣、帽及手套,选择白色穿戴的目的即在于发现和消除其上的脏污。
此外,还应该多准备另外一幅白手套,专用于接触坡口及操作焊丝,而不能用于其他作业。
(6)设计设计时应选用对焊缝气孔敏感性较小的铝材,焊接时的可操作性较好或能实施自动焊的结构,以便于减少焊缝接头,同时还可以避免手工焊频繁引弧熄弧而引起的焊缝气孔。
此外,设计对焊缝余高的要求不必过高,如果过分突出焊缝会使液态焊缝金属内的气泡从上浮至逸出的距离增大而导致气泡来不及逸出焊缝以外。
4.2焊接裂纹
4.2.1焊接裂纹的性质
铝合金焊接裂纹的性质属于热裂纹,简称裂纹。
它们是在固相线温度附近的高温下沿晶界开裂的。
与黑色金属不同,铝合金很少出现冷裂纹。
4.2.2裂纹特征
铝合金焊接时产生的热裂纹有两种特征形式,其一为凝固裂纹或结晶裂纹,另一为液化裂纹。
4.2.3焊接裂纹的危害
焊接裂纹具有尖锐的两端,在焊接残余应力和工作应力的作用下,易产生严重的应力集中,裂纹极易扩展,常成为低应力下脆性断裂或疲劳断裂,应力腐蚀断裂的断裂源。
4.2.4焊接裂纹的影响因素及防治措施
4.2.4.1冶金因素
(1)预防焊接裂纹不如避免焊接裂纹,为此,选材设计时,必须避免选用热裂倾向大的材料,应优先选用或改用力学性能水平相当,但焊接性较好、热裂倾向小的材料。
(2)填充金属的牌号及其成分。
焊缝金属是由母材合金与填充金属熔合而成的。
填充金属的牌号与母材合金的牌号需适当配合,配合是否适当可导致不同的裂纹倾向,因此焊丝的选择应具备下列特性:
①焊丝熔入熔池后能提供大量的、流动性好的低熔点共晶体,以便及时愈合焊缝金属内可能产生的结晶裂纹。
②在熔合区或母材近缝区晶界液化状态临近结束前,在熔合线焊缝一侧的焊缝金属内应尚存足够数量的、流动性好的液态低熔点共晶体,其固相线温度应低于熔合区或母材近缝区晶界低熔点共晶体的固相线温度,以便前者能顺沿熔合线两侧晶间的液相通道流到熔合区或母材近缝区晶间,愈合可能产生的晶界液化裂纹。
4.2.4.2工艺因素
(1)焊缝成形。
焊缝成形系数φ(焊缝宽度、焊缝的实际厚度比)可以影响焊缝金属凝固裂纹的倾向,如图4-1所示。
φ值增大时,焊缝热裂倾向降低,但φ>7以后,由于焊缝截面过薄,热裂性降低。
φ值较小时,最后凝固的枝晶会和面因晶粒相生长而成为杂质严重析集的部位,最容易生成焊缝结晶裂纹。
图4-1焊缝成形系数对焊缝热裂的影响
由于铝材焊接性不良且本次的焊件厚度较大,因此,宜施行开坡口焊接,避免形成窄而深的焊缝。
(2)组织形态。
焊缝金属的晶粒愈粗大,柱状晶的方向性愈明显,则焊缝产生结晶裂纹的倾向亦愈大;母材近缝区晶粒愈粗大,晶界熔化愈明显,则该区产生液化裂纹的倾向亦愈大。
组织形态取决于焊接时的热输入。
提高焊接时的热输入,例如降低焊接速度,增大焊接电流,可降低焊缝金属产生结晶裂纹的倾向,但应注意,此举可能同时引起母材热影响区过热,晶界熔化,引发母材热影响区产生液化裂纹。
因此,在操作