大直径人工挖孔桩的安全技术措施.docx
《大直径人工挖孔桩的安全技术措施.docx》由会员分享,可在线阅读,更多相关《大直径人工挖孔桩的安全技术措施.docx(4页珍藏版)》请在冰豆网上搜索。
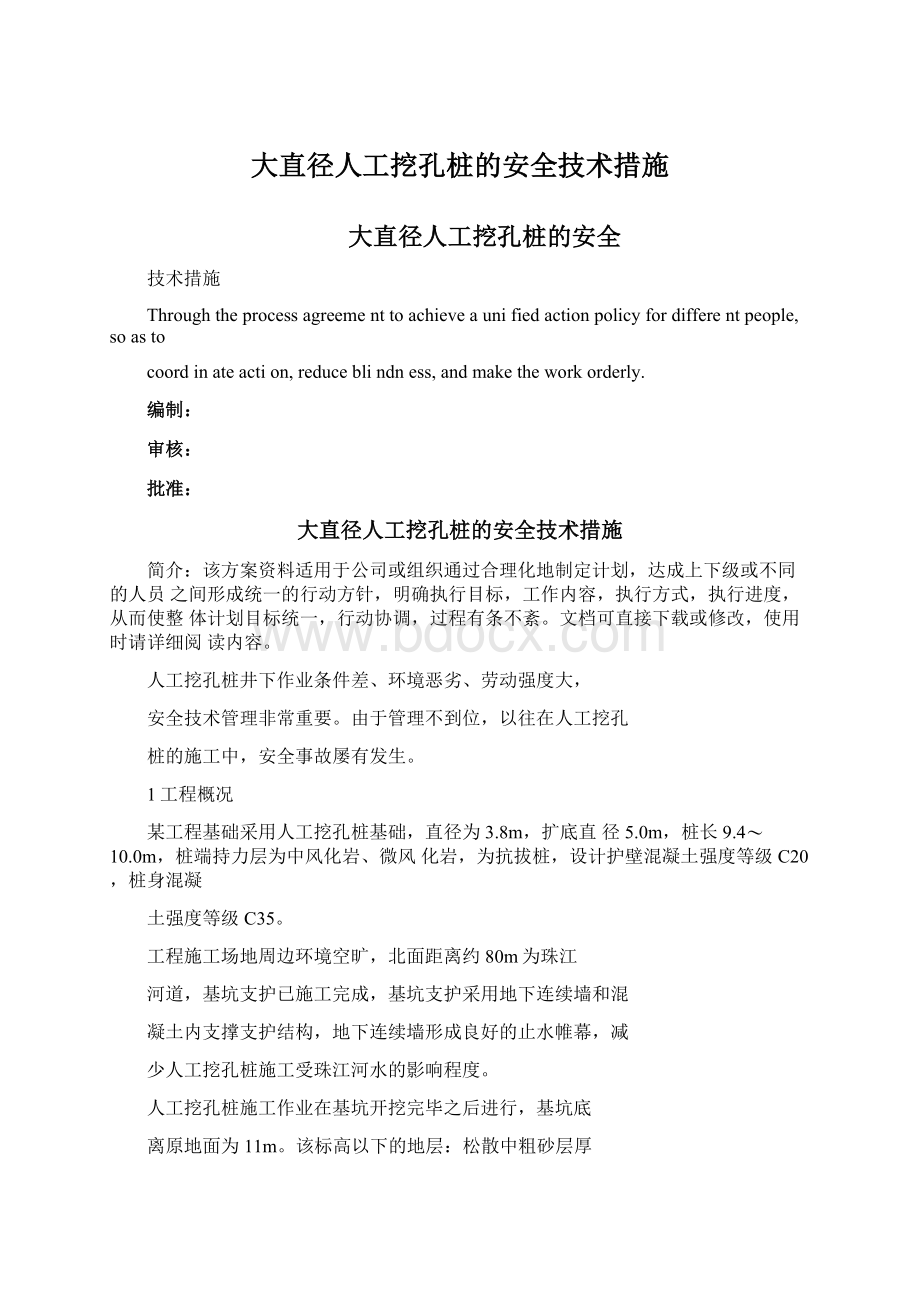
大直径人工挖孔桩的安全技术措施
大直径人工挖孔桩的安全
技术措施
Throughtheprocessagreementtoachieveaunifiedactionpolicyfordifferentpeople,soasto
coordinateaction,reduceblindness,andmaketheworkorderly.
编制:
审核:
批准:
大直径人工挖孔桩的安全技术措施
简介:
该方案资料适用于公司或组织通过合理化地制定计划,达成上下级或不同的人员之间形成统一的行动方针,明确执行目标,工作内容,执行方式,执行进度,从而使整体计划目标统一,行动协调,过程有条不紊。
文档可直接下载或修改,使用时请详细阅读内容。
人工挖孔桩井下作业条件差、环境恶劣、劳动强度大,
安全技术管理非常重要。
由于管理不到位,以往在人工挖孔
桩的施工中,安全事故屡有发生。
1工程概况
某工程基础采用人工挖孔桩基础,直径为3.8m,扩底直径5.0m,桩长9.4〜10.0m,桩端持力层为中风化岩、微风化岩,为抗拔桩,设计护壁混凝土强度等级C20,桩身混凝
土强度等级C35。
工程施工场地周边环境空旷,北面距离约80m为珠江
河道,基坑支护已施工完成,基坑支护采用地下连续墙和混
凝土内支撑支护结构,地下连续墙形成良好的止水帷幕,减
少人工挖孔桩施工受珠江河水的影响程度。
人工挖孔桩施工作业在基坑开挖完毕之后进行,基坑底
离原地面为11m。
该标高以下的地层:
松散中粗砂层厚
0.60〜5.10m;稍密中粗砂层厚0.75〜5.50m;中密中粗砂层厚0.73〜5.60m;粉质黏土(含粉细砂)层厚0.50〜1.90m;
全风化钙质和粉砂质泥岩层厚0.50〜1.40m;强风化钙质和
粉砂质泥岩层厚0.50〜7.80m;中等风化钙质和粉砂质泥岩
层厚0.50〜10.10m;微风化钙质和粉砂质泥岩层厚0.50〜
11.10m。
场地地下水属空隙潜水及基岩裂隙水,中粗砂层是
场区主要的富水层区。
该工程人工挖孔桩有以下特点。
1)桩直径较大(3.8m),采用人工挖孔桩,桩深入微风化
岩层和中风化岩层,成孔深度深,成孔过程需要密切配合护
壁施工。
2)挖孔取土石方量较大,且主要为碎石,挖掘主要由人
工采用铁锹,铁镐等工具施工。
3)挖孔桩底部微风化岩层面起伏较大。
4)挖孔桩需穿过强风化以及中、微风化岩层。
中、微风
化岩及孤石施工需要采用微差控制爆破技术爆破开挖,现场安全控制要求高。
5)桩深度范围内所涉及的土层较复杂,场地以下最深有约7m的强透水砂层存在,场地内的地下水与北边的珠江和河道存在水力联系,这种情况对于人工挖孔桩的施工存在着较大的危险性。
2安全技术措施
1)由于该工程的人工挖孔桩在基坑下挖桩作业,所以基坑周边应设置安全护栏和安全网围蔽,并搭设符合要求的人行梯。
桩口周边应设有1m高的护栏,周边挂符合使用要求的安全网。
停止挖桩的孔口必须全封蔽,且能安全承受2000kN的重力,或有1.2m高全围蔽的护栏。
2)当桩孔净距不足4.5m,应进行分批跳挖。
待第一批桩芯混凝土浇灌完毕后,才能开挖第二批桩。
每节护壁之间必须有50mm的搭接。
挖桩操作的桩孔,必须有钢爬梯挂至工作面,人员上下桩孔,不得用吊桶或直接利用护壁支撑上下;
不得使用麻绳和尼龙绳吊挂或脚踏井壁凸级上下;支承绞车的桥枋应细心检查,应有足够支承强度和刚度。
3)挖孔桩孔口,应设水平活动安全盖板,如图1所示。
图1人工挖孔桩安全防护示意图当吊桶提升到离
地面高1.8m左右(超过人高)时推活动盖板关闭孔口,手推
车推至盖板上,卸土后再开盖板下吊桶吊土,以防土块和工具掉入孔内伤人。
最上一节护壁比井口地面再高出25cm,
以防止地面水流入井孔内或脚踢杂物入孔内。
孔井口边1m
范围内不得有任何杂物,堆土应在孔井口边1.5m以外。
4)当桩孔挖深超过5m以上时,离桩底2m处必须设置半圆钢网挡板,提土上、下时,井下人员应站在挡板下方。
每天上岗时,孔口操作人员应检查绞车、缆绳、吊桶,发现有安全隐患的,须随时更换。
孔内上下传递材料、工具,严禁抛掷。
当吊送大物件、石块时,桩孔内人员应先行返上地面。
5)当孔深超10m,或桩径在0.8m内孔深超6m,或桩径在lm内孔深超8m时,应对桩孔内送气换气,风量不少
于25L/s。
桩下作业时,桩口人员不得离开,还应密切注视桩下动态,做好安全监控。
6)当孔底扩头可能会引起孔壁失稳时,必须采取相应的措施,经审批后方可施工;已扩底的桩孔,要及时浇灌桩身混凝土或封底,不能尽快浇灌混凝土的桩应暂时不扩底,以
防扩大头塌方。
7)当相距10m以内的邻桩正在浇灌混凝土或桩孔积水很深时,一般应暂停施工,人不准下孔。
随时加强对土壁涌水情况的观察,发现异常情况应及时采取处理措施。
采用潜水泵抽水时,孔中积水基本上抽干后,作业人员才能下至孔中进行挖土。
地下水丰富时,可将中间部位桩孔提前开挖,汇集附近的地下水,用潜水泵将水抽出,进行深井降水。
孔内必须设置应急软爬梯,供人员上下孔洞使用的电动葫芦、吊笼等应安全可靠并配有防坠落装置。
3对不利土层的安全技术措施
该工程遇到的不利土层是:
存在强透水的粗砂和砾砂层,场地东部和南部的砂层较厚。
砂层底部层底深度最深为
17.00m,即基坑底以下最深有约7m的强透水砂层存在,
并且场地内的地下水与北边的珠江和河道存在水力联系,这种情况对于人工挖孔桩的施工存在着较大的危险性。
对于场地内的降水,先施工外围(或迎水部位)的桩孔,每根间距大约为50m,这部分桩孔混凝土护壁完成后,桩孔先不浇筑桩
身混凝土,而将其作为排水井,以方便其他
孔位的施工。
成桩过程中在穿过砂层时,施工人员必须熟悉所挖孔的地质情况,勤检查,注意土层变化。
当遇到流沙、大量地下水等情况时,要立即采取有效防护措施,然后才能继续施工。
3.1处理方法
1)当砂层厚度小于2m时:
流砂情况较轻,缩短这一循环的开挖深度,将正常的
1m左右一段,缩短为0.3〜0.5m,以减少挖层孔壁的暴露时间,及时进行护壁混凝灌注。
当孔壁塌落,有泥砂流人而不能形成桩孔时,可用纺织袋土逐渐堆堵,形成桩孔的外壁,并保证内壁满足设计要求,混凝土应加速凝剂,加快凝同速
度。
如流砂情况较严重,采取下钢套筒。
以孔外径为直径,
可分成4〜6段圆弧,再加上适当的肋条,相互用螺栓或钢筋环扣连接,在开挖0.3〜0.5m,即可分片将套简装入,深入孔底不少于0.2m,插入上部混凝土护壁外侧不小于0.5m,
装后即支模浇注护壁混凝土。
若放入套筒后流砂仍上涌,可
采取突击挖出后即用混凝土封闭孔底的方法,待混凝土凝结后,将孔心部位的混凝土清凿以形成桩孔。
2)当砂层厚度超过2m时,沿桩四周做直径0.6m单重管旋喷桩,深度至强风化岩岩面,起到止水帷幕和支护固结砂层的作用。
3.2加高护壁就地堆土的具体措施
1)原土面加高之护壁,其构造按软弱土层护壁施工的要求,在护壁混凝土内增加构造筋和上下节护壁的拉结筋;其护壁外圈模板要求为正圆形,以免改变护壁的受力状态。
2)挖出之土方要就地堆放,四周堆土须均匀放置,要保证周边堆土不要高于桩口标高,保持桩口护壁高于堆土面150mm以上。
3)把原始点中心线和标高随着护壁加高而向上引测,并记在最高的护壁节上,以保证桩身的垂直度。
4)基坑内的设备要随着土面加工而变动,土方不得掩埋设施、设备,基坑内临时用电的电缆或电线要保证架空高度满足2.5m以上的规定。
5)保证基坑内排水系统的正常工作,不能让土方堵塞地
下水沟