MCRC硫磺回收装置2.docx
《MCRC硫磺回收装置2.docx》由会员分享,可在线阅读,更多相关《MCRC硫磺回收装置2.docx(22页珍藏版)》请在冰豆网上搜索。
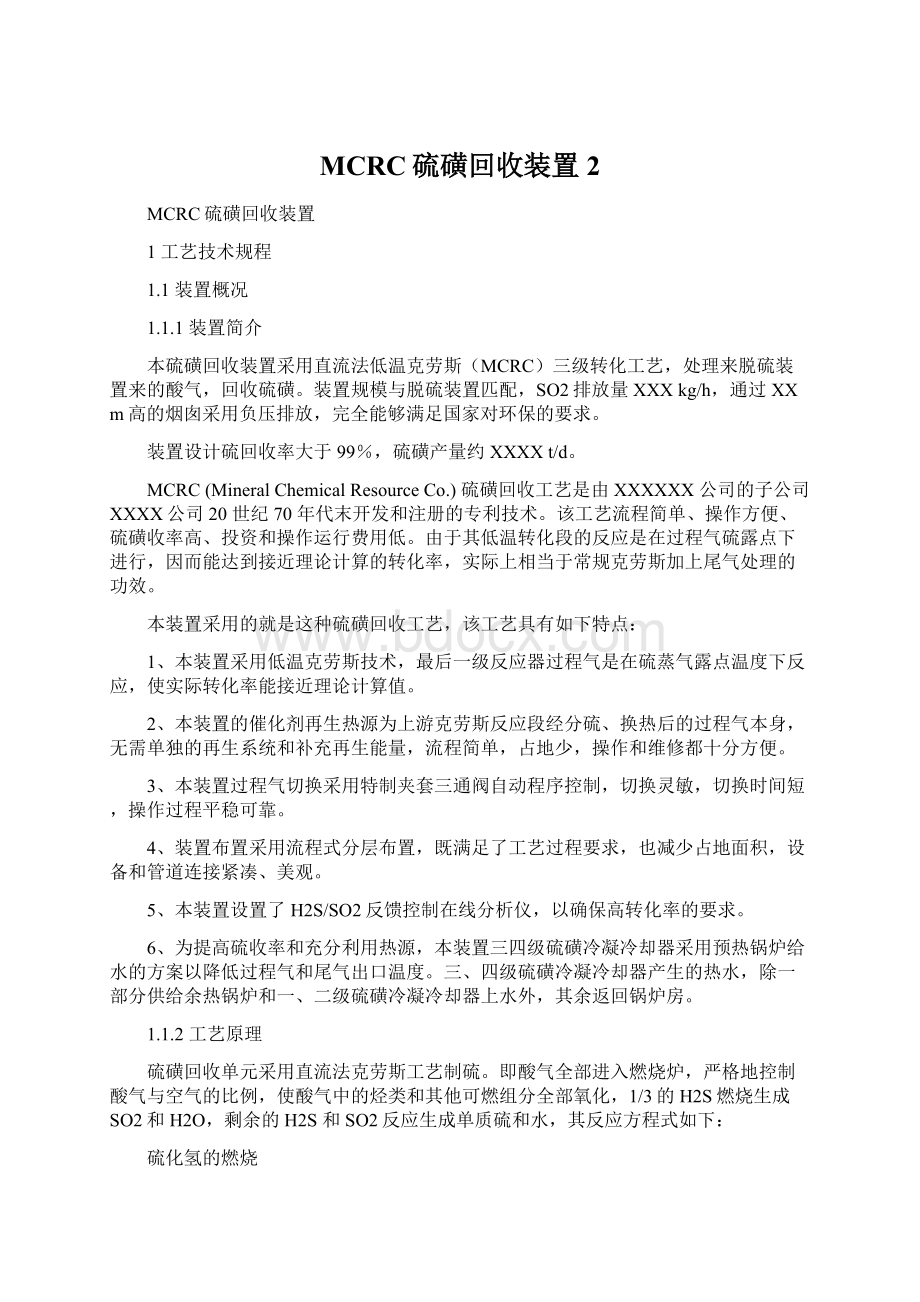
MCRC硫磺回收装置2
MCRC硫磺回收装置
1工艺技术规程
1.1装置概况
1.1.1装置简介
本硫磺回收装置采用直流法低温克劳斯(MCRC)三级转化工艺,处理来脱硫装置来的酸气,回收硫磺。
装置规模与脱硫装置匹配,SO2排放量XXXkg/h,通过XXm高的烟囱采用负压排放,完全能够满足国家对环保的要求。
装置设计硫回收率大于99%,硫磺产量约XXXXt/d。
MCRC(MineralChemicalResourceCo.)硫磺回收工艺是由XXXXXX公司的子公司XXXX公司20世纪70年代末开发和注册的专利技术。
该工艺流程简单、操作方便、硫磺收率高、投资和操作运行费用低。
由于其低温转化段的反应是在过程气硫露点下进行,因而能达到接近理论计算的转化率,实际上相当于常规克劳斯加上尾气处理的功效。
本装置采用的就是这种硫磺回收工艺,该工艺具有如下特点:
1、本装置采用低温克劳斯技术,最后一级反应器过程气是在硫蒸气露点温度下反应,使实际转化率能接近理论计算值。
2、本装置的催化剂再生热源为上游克劳斯反应段经分硫、换热后的过程气本身,无需单独的再生系统和补充再生能量,流程简单,占地少,操作和维修都十分方便。
3、本装置过程气切换采用特制夹套三通阀自动程序控制,切换灵敏,切换时间短,操作过程平稳可靠。
4、装置布置采用流程式分层布置,既满足了工艺过程要求,也减少占地面积,设备和管道连接紧凑、美观。
5、本装置设置了H2S/SO2反馈控制在线分析仪,以确保高转化率的要求。
6、为提高硫收率和充分利用热源,本装置三四级硫磺冷凝冷却器采用预热锅炉给水的方案以降低过程气和尾气出口温度。
三、四级硫磺冷凝冷却器产生的热水,除一部分供给余热锅炉和一、二级硫磺冷凝冷却器上水外,其余返回锅炉房。
1.1.2工艺原理
硫磺回收单元采用直流法克劳斯工艺制硫。
即酸气全部进入燃烧炉,严格地控制酸气与空气的比例,使酸气中的烃类和其他可燃组分全部氧化,1/3的H2S燃烧生成SO2和H2O,剩余的H2S和SO2反应生成单质硫和水,其反应方程式如下:
硫化氢的燃烧
烃类的燃烧
剩余的H2S与SO2的反应
反应放出的热量,在余热锅炉中产生0.5MPa(g)的饱和蒸汽而被利用。
硫在冷凝器中冷凝下来,出冷凝器的过程气,仍然有相当数量的H2S和SO2在进入反应器之前,与余热锅炉出来的过程气经过高温掺合阀混合,混合到有利于转化的温度,在装有催化剂的反应器内进行催化反应,经过三段催化后,硫磺收率达99%。
1.1.3生产流程说明
从80万方/日和50万方/日脱硫装置来的酸气,经系统汇合后,进入酸气分离器(D-1301),分离出酸水后的酸气进入主燃烧炉与从主风机送来的空气按一定配比在主燃烧炉内进行克劳斯反应,在主燃烧炉内约72.4%的H2S转化为元素硫。
酸水收集到酸水压送罐中,利用氮气定期压至脱硫装置酸水回流罐中。
自主燃烧炉出来的高温过程气经余热锅炉(E-1301)冷却到320℃后进入一级硫磺冷凝冷却器(E-1302)冷却,分离出液硫后的过程气和余热锅炉(E-1301)的650℃的过程气通过高温掺合阀混合至280℃,混合后的过程气进入一级反应器(R-1301)进行常规克劳斯反应,生成元素硫,同时过程气中CS2和COS充分水解。
(下面为便于叙述,假设二级反应器(R-1302)处于再生态而三级反应器R-1303处于吸附态)从一级反应器出来的过程气经气/气换热器(E-1303)后进入二级硫磺冷凝冷却器(E-1304)冷却至170℃,分离出液硫后的过程气经气-气换热器E-1303和从一级反应器出来的过程气换热至269℃后进入二级反应器(R-1302),在二级反应器(R-1302)中,上一周期吸附在催化剂上的液硫逐渐汽化,从而使催化剂除硫再生,并进行常规克劳斯反应。
自二级反应器(R-1302)来的过程气经三级硫磺冷凝冷却器(E-1305)冷却除硫后,不经再热直接进入三级反应器(R-1303),进行低温克劳斯反应。
自三级反应器(R-1303)出来的过程气进入四级硫磺冷凝冷却器(E-1306),冷却分离出液硫后进入液硫捕集器(D-1302),从捕集器出来的尾气送入尾气焚烧炉(H-1304)焚烧,焚烧后的废气进入尾气烟囱排放。
本装置低温克劳斯段的二、三级反应器和两台硫磺冷凝冷却器通过三个三通切换阀程序控制,自动切换操作。
各级硫磺冷凝冷却器及捕集器分出的液硫通过相应的液硫封流出,汇集后自流入硫磺成型装置的液硫池。
余热锅炉和一、二级硫磺冷凝冷却器产生0.5MPa(g)的低压饱和蒸汽,进入工厂蒸汽系统。
1.1.4工艺原理流程图
1.2工艺指标
1.2.1进料酸气条件
进入本装置的酸气为脱硫装置产生的酸气,酸气进料条件如下:
温度:
40℃
压力:
170kPa(a)
流量:
54.358kmol/h1217.62m3/h
组成:
见下表
组分
mol%
C1
0.359
C2
0.000
H2S
84.946
CO2
10.532
H2O
4.161
N2
0.002
合计
100.000
1.2.2产品硫磺质量
本装置的产品为液体硫磺,其质量符合国家标准GB2449-92《工业硫磺及其试验方法》中的优等品质量指标。
1.2.3硫磺回收单元正常操作主要参数表
1、硫磺回收装置DCS系统操作参数表
序号
过程对象
刻度范围
设定点
报警
调节器作用
H/HH
L/LL
1
酸气总管温度
0~100
2
空气总管温度
0~150
3
燃料气温度
0~100
4
主燃烧炉温度
0~1600
5
主燃烧炉温度
0~1600
1400
1000
6
掺合阀出口温度
0~600
253
反作用
7
掺合阀出口温度
0~600
8
余热锅炉出口温度
0~600
9
一级冷凝冷却器出口温度
0~300
10
一级反应器温度
0~600
11
一级反应器温度
0~600
12
一级反应器温度
0~600
13
一级反应器出口温度
0~600
14
气/气换热器出口温度
0~600
15
二级冷凝冷却器入口温度
0~600
16
二级冷凝冷却器出口温度
0~300
17
KV-1301入口温度
0~600
18
二级反应器入口温度
0~600
19
二级反应器温度
0~600
20
二级反应器温度
0~600
21
二级反应器温度
0~600
22
二级反应器出口温度
0~600
23
三级冷凝冷却器过程气出口温度
0~250
127
反作用
24
三级冷凝冷却器给水出口温度
0~250
149.3
反作用
25
三级反应器入口温度
0~250
26
三级反应器入口温度
0~600
27
三级反应器入口温度
0~600
28
三级反应器温度
0~600
29
三级反应器温度
0~600
30
三级反应器温度
0~600
31
三级反应器出口温度
0~600
32
四级冷凝冷却器过程气出口温度
0~250
127
反作用
33
四级冷凝冷却器给水出口温度
0~250
150
反作用
34
锅炉给水空冷后温度
0~250
120
反作用
35
锅炉给水空冷前温度
0~250
36
液硫捕集器出口温度
0~250
37
液硫捕集器入口温度
0~250
38
尾气灼烧炉温度
0~1600
1200
反作用
39
尾气灼烧炉温度
0~1600
40
风机K-1301/A出口压力
0~0.16
0.09
反作用
41
风机K-1301/B出口压力
0~0.16
0.09
反作用
42
酸气总管压力
0~0.16
0.06
43
空气总管压力
0~0.16
44
燃料气压力
0~0.6
44
调压后锅炉水压力
0~1.66
0.9
45
系统来锅炉给水压力
0~1.6
45
至系统蒸气压力
0~1.0
0.58
反作用
46
风机K-1301/A入口流量
0~4000
2900
反作用
47
风机K-1301/B入口流量
0~4000
2900
反作用
48
酸气总管流量
0~2000
49
主燃烧炉80%空气流量
0~4000
2300
反作用
50
主燃烧炉20%空气流量
0~1000
577
反作用
51
至系统除氧水流量
0~4000
52
进主燃烧炉燃料气流量
0~100
反作用
53
进主燃烧炉低压蒸气流量
0~300
54
自系统来锅炉给水流量
0~10000
55
灼烧炉燃料气流量
0~200
反作用
56
去系统蒸气流量
0~5000
57
酸水压送罐液位
0~100
50
80
20
58
余热锅炉液位
0~100
50
80
40
正作用
59
一级冷凝冷却器液位
0~100
50
80
20
正作用
60
一级冷凝冷却器液位
0~100
61
二级冷凝冷却器液位
0~100
50
80
20
正作用
62
二级冷凝冷却器液位
0~100
50
80
20
63
尾气中SO2含量
0~1
0.05
0.2
64
尾气中H2S含量
0~250
0.1
0.4
65
H2S-2SO2
0
正作用
2、硫磺回收装置ESD系统操作参数表
序号
过程对象
刻度范围
设定点
报警/联锁
调节器作用
H/HH
L/LL
1
酸气总管流量
0~2000
1393
2
主燃烧炉80%空气流量
0~4000
2307
3
主燃烧炉20%空气流量
0~1000
577
4
酸气分离器液位
0~100
50
90
10
5
酸气分离器液位
0~100
50
90
10
6
余热锅炉液位
0~100
50
20
7
余热锅炉液位
0~100
50
20
8
余热锅炉液位
0~100
50
20
9
空气总管压力
0~0.16
0.12
10
空气总管压力
0~0.16
0.12
3、组分分析及取样点
组分分析及及取样地点一览表
序号
取样地点
分析项目
分析次数
1
进装置酸气
H2S烃类含量全分析
每天一次
2
一、二、三级反应器进口
H2S、SO2含量
每天一次
3
捕集器出口
H2S、SO2含量及其比例
四小时一次
4
烟道
H2S含量分析
每天一次
5
烟道
SO2含量分析
每天一次
2单体设备操作
2.1主然烧炉的空气流量控制
在主燃烧室里给酸气配给恰当比例的空气量,是装置操作中重要的一环,为了尽可能提高硫磺的回收率,必须保证H2S/SO2的比例为2/1,配给的空气总量按燃烧H2S总量的1/3和完全燃烧酸气中的烃类和其它可燃化合物的量来计。
本装置的进料酸气可燃组分只有H2S和少量烃类(主要是CH4),所以炉-1301所需的理论空气量可按下式计算:
风气比:
式中:
Q酸:
进H-1301的酸气量m3/h
Q空:
进H-1301的酸气量m3/h
YH2S:
酸气中H2S的含量(V%)
YCH4:
酸气中的CH4含量(V%)
R:
风气比
到主燃烧的空气流率是通过空气供给线上的二路调节阀来进行控制。
第一、第二路调节阀设计通过能力分别为主然烧炉空气总量的80%和20%,第一路比例调节,它跟踪酸气流量的变化保持空气、酸气的一定比例,第二路由安装在尾气管线上的H2S/SO2在线分析仪反馈的信号调节。
它随进料酸气组成的变化而变化。
2.2余热锅炉和硫磺冷凝器的操作
正常生产期间,余热锅炉产生158℃,0.5MPa的饱和蒸汽。
蒸汽量为2954kg/h。
一级冷凝器产生相同条件的饱和蒸汽480kg/h。
二级冷凝器产生相同条件饱和蒸汽200kg/h,三、四级冷凝器不产生蒸汽,进出三、四级冷凝器的都是锅炉水,水量分别为5621kg/h、1176kg/h。
为了防止余热锅炉和硫冷凝器固体物积累,锅炉水要不断通过排污罐排污。
排污水量应达到蒸发量的5%,以防止过量的不溶解物累积。
2.3催化转化器的操作
一、二、三级反应器入口温度控制,应使过程气得到转化的最佳效果,设计值为
一级反应器入口温度280℃出口温度326.5℃
二级反应器入口温度269℃出口温度289.8℃
三级反应器入口温度127℃出口温度157.2℃
反应器入口和出口气体温差,标志着催化转化发生的程度。
一旦发现温差下降时,应临时提高反应器入口温度,这样硫将从催化剂表面被除去,但是催化剂表面硫太多,多数原因是催化剂变质。
但是如果催化剂积炭,则只有在停工期间才能排除,所以在正常操作期间要控制好配给的空气量,避免催化剂积炭。
2.4催化剂的再生
2.4.1硫酸盐的脱除
在操作过程中由于硫催化剂和过程气中SO2、SO3、O2的作用,催化剂中氧化铝和氧化铁会转化成硫酸盐,这些硫酸盐占据了催化剂表面活性中心,降低了催化剂的活性。
硫酸盐的生成反应:
(1)
(2)
在操作过程中,催化剂表面的生成的硫酸盐的量并不是无限增加,因生成的硫酸盐能与过程气中的硫化氢反应,重新生成三氧化二铝。
还原反应:
硫酸盐的生成取决于反应
(1)、
(2)、(3)的化学平衡状态,改变平衡条件,即提高H2S浓度和床层温度,可促使硫酸铝重新转化成氧化铝。
因此,硫酸盐的还原操作是:
将一级转化器入口温度提高到300℃左右,二级转化器入口温度提高到比一般操作温度高30℃~50℃,维持12-24小时,除去催化剂表面吸附的元素硫,然后调节过程气中的H2S/SO2分子比值为2.5或更高,维持24-36小时,再将温度和H2S/SO2分子比值恢复到正常操作条件,即可观察到催化剂活性恢复。
但是在进行硫酸盐还原操作期间,由于温度和H2S/SO2分子比例改变,将引起硫化氢转化率下降,尾气中含硫化合物浓度显著上升,因此,必须采取相应的措施。
2.4.2除硫
装置正常操作期间,硫磺积聚在催化剂的孔隙中,一旦发现反应器的温差明显下降时,最大可能的原因就是积硫。
为从催化剂床层除硫,反应器进出口温度应比正常时增加大约30℃以上,这个周期至少要24小时。
2.5尾气灼烧炉的燃料气控制
尾气灼烧炉是在有过量空气存在下,用燃料气把尾气加热到一定温度后使其中含硫化合物都转化成SO2,灼烧温度为550℃~600℃,正常耗燃料气约111m3/h,配给空气量为1666m3/h。
当硫磺回收装置产量变化时,燃料气由温度调节控制,改变其进炉的量,以保证灼烧温度。
2.6硫磺回收装置主要控制回路描述
2.6.1TIC-1306回路:
为余热锅炉出口高温掺和温度调节回路。
通过余热锅炉前后过程气的掺和,使过程气温度稳定在253℃最佳克劳斯反应温度值上。
2.6.2FIQ-1303及FIC-1305比值调节回路:
为主燃烧炉80%空气的比值回路,用主酸气量乘比值系数(经过化验分析确定,一般为2左右),减去20%空气需求(可外部给定),作为给定值。
通过DCS系统中的PID调节功能将满足下式:
FIQ-1303×K-Q1=FIQ-1305
式中:
K为分析数据,初值为1.989;
Q1可设定为577,或者为FIQ-1307测量值。
2.6.3AIC-1301及FIC-1307串级调节回路:
AIC-1301为主环调节,FIC-1307为副环调节。
在比值控制回路中所减去的Q1值(正常为20%)应作为副环回路的给定值,用在线2:
1分析仪的调节值与副环回路串级。
目的在于使尾气中H2S和SO2的比值达到2:
1最佳的克劳斯反应状态。
由于过程反应时间原因,主环为采样调节。
初步定为80s时间内,调节15s。
在2:
1分析仪检测准确和酸气量一定时,串级调节回路使用最佳。
2.6.4LIC-1306调节回路:
为余热锅炉的上水调节,当锅炉液位低到35%(LIA-1304/1305/1306三选二)时,ESD系统将关闭硫磺回收装置。
2.6.5LIC-1307调节回路:
为一级冷凝冷却器液位调节,当液位低于35%时,DCS系统发出报警信号。
2.6.6LIC-1309调节回路:
为二级冷凝冷却器液位调节,当液位低于35%时,DCS系统发出报警信号。
2.6.7TIC-1325调节回路:
为三级冷凝冷却器出口温度调节,当TI-1326的温度低于175℃(绝压0.9MPa下水的饱和蒸汽温度)时,HS-1325选择TIC-1325,当TI-1326的温度高于159℃时,HS-1325选择TIC-1326。
2.6.8TIC-1335调节回路:
为四级冷凝冷却器出口温度调节,当TI-1336的温度低于175℃(绝压0.9MPa下水的饱和蒸汽温度)时,HS-1335选择TIC-1335,当TI-1336的温度高于159℃时,HS-1335选择TIC-1336。
2.6.9TIC-1342及FIC-1313串级控制回路:
TIC-1342为主环,FIC-1313为副环。
控制尾气焚烧炉温度在600℃,使反应过剩的H2S完全烧成SO2排入大气。
采用进炉燃气流量串级方式能较快的达到温度控制的效果。
为了防止后段温度过热,当后段温度TI-1343大于600℃,切断焚烧炉燃料气进口阀。
3开工规程
3.1开车前的准备工作
开车前的准备工作,概括起来主要工作项目有检查、机械试运转,空气吹扫、水洗、仪表的检查、耐火材料烘干、催化剂的装填、气密性试验。
3.1.1检查
开车前应对装置的每个部分都要严格按工艺、设备和仪表等的检查要求进行仔细检查。
检查内容包括:
1、塔、罐与反应器的检查
1)内部构件是否安装完整。
2)化学药品、干燥剂、催化剂、瓷球等填料是否填装完毕。
2、运转设备的检查
1)检查润滑油加入量是否合适。
2)能够进行手动盘车的设备必须盘车检查。
3)检查电动机的旋转方向是否正确。
4)检查电动机脱车时的空载试车,直到电动机的温度稳定,确保电动机轴不发生过热现象。
5)带上负载进行试车。
6)检查机、泵的报警,紧急停车系统是否正常。
3、管路系统的检查
1)准备好冲洗操作中所需要的所有垫片、法兰、短管、盲板、临时连接件及各种有关工具。
2)必要时隔断或拆除调节阀、疏水器和粗滤器等进行冲洗操作、冲洗后复原。
3)检查各种阀门的开关情况,检查所有8字盲板到位情况。
4、仪表系统的检查
1)在安装仪表部件前应用仪表风吹扫所有输送与调节系统用风管线。
2)检查调节阀和各种流量计介质的流动方向是否正确。
3)检查各类仪器仪表的操作可靠性。
3.1.2机械试运转
在电动机脱车情况下的空载试运后,在进行空气吹扫作业时,完成对主风机的机械试车。
3.1.3空气吹扫
需要空气吹扫的管线有液硫管线,过程气管线以及相连接的设备,吹扫液硫管线和液封时要特别注意不要将杂质吹入内部。
吹扫步骤如下:
1、卸下调节阀和孔板;
2、卸下装置在冷凝冷却器和捕集器内的捕雾网;
3、吹扫设备和管线,直到吹扫空气干净为止;
4、吹扫完后,安装卸下的所有调节阀和孔板,并上紧吹扫系统所有的连接部分;
5、装上设备内拆除的捕雾网。
3.1.4水洗
用水冲洗的管线有余热锅炉和冷凝冷却器的给水管线和排污管线,蒸汽管线以及相连接的设备。
冲洗水用洁净水,冲洗步骤如下:
1、卸下孔板和流量计;
2、卸开用法兰连接的设备;
3、引入洁净水冲洗余热锅炉、冷凝冷却器以及相连接的管线,直到冲洗干净为止。
4、上紧连接设备的法兰,装上拆卸的孔板和流量计。
3.1.5仪表检查
首次开车前应全面检查和调试各控制回路,大修后的检查则着重在经过维修或更换的部分。
3.1.6耐火材料的烘干
烘炉是决定使用效果好坏的关键环节。
炉子施工完毕后,必须进行烘炉,以排出衬里中游离水和化学结合水,烘炉得当,可以提高设备使用寿命,否则,水分排除不通畅,会使耐火衬里产生裂纹,剥落甚至引起爆裂事故。
烘炉应在经过技术检验合格以及自然通风干燥七天以上,锅炉房应有蒸汽送出时才可进行。
1、烘炉前的检查
1)检查炉前有关阀门的严密性及开关的灵活性。
2)检查燃料气管道、酸气管道、空气管道是否严密。
3)热电偶及热工控制仪表是否准确无误。
2、烘炉步骤
1)暖炉:
向余热锅炉,冷凝冷却器供给软化水并保持正常水位。
打开余热锅炉和冷凝冷却器上部的排气阀,然后向余热锅炉和冷凝冷却器壳体内供给蒸汽,这点是十分重要的,如果余热锅炉和冷凝冷却器内的软水不处于沸腾状态,由于烟气温度较高则可能造成炉管和壳体的温差过大而损坏管板与管子连接部分,在烘炉期间,蒸汽从排气口喷出后,关闭排气阀,停止向壳体供给蒸汽,并注意操作余热锅炉、冷凝冷却器的上水排污、蒸汽的送出。
2)点火:
当余热锅炉和冷凝冷却器内的水达到沸腾温度后开始点火烘炉。
炉子的点火顺序为主燃烧炉、尾气灼烧炉。
点火前点火器需取出在大气中进行试验,点火前应全开空气管线上的阀门吹扫炉膛,吹扫时间不少于三分钟。
3)烘炉:
开始用点火嘴进行烘炉(烘主燃烧炉时,应在余热锅炉过程气出口加临时烟囱两个(高温和低温各1个)),调节好燃料气和空气的配比,观察燃烧情况,当点火嘴不能继续提高温度时,改用主火嘴。
4)降温:
烘炉完毕,应慢慢减少燃料气量,使炉子逐渐冷却下来,最后切断燃料气和空气,待炉子自然冷却两天后经火嘴注入空气,直到主燃烧炉、尾气灼烧炉可以进人为止。
5)检查耐火材料衬里的干燥情况,清除内部灰尘、铁屑和其它杂质。
3、烘炉注意事项
1)严格按升温曲线进行,烘炉曲线见热-3260、热-