连铸用耐火材料.docx
《连铸用耐火材料.docx》由会员分享,可在线阅读,更多相关《连铸用耐火材料.docx(24页珍藏版)》请在冰豆网上搜索。
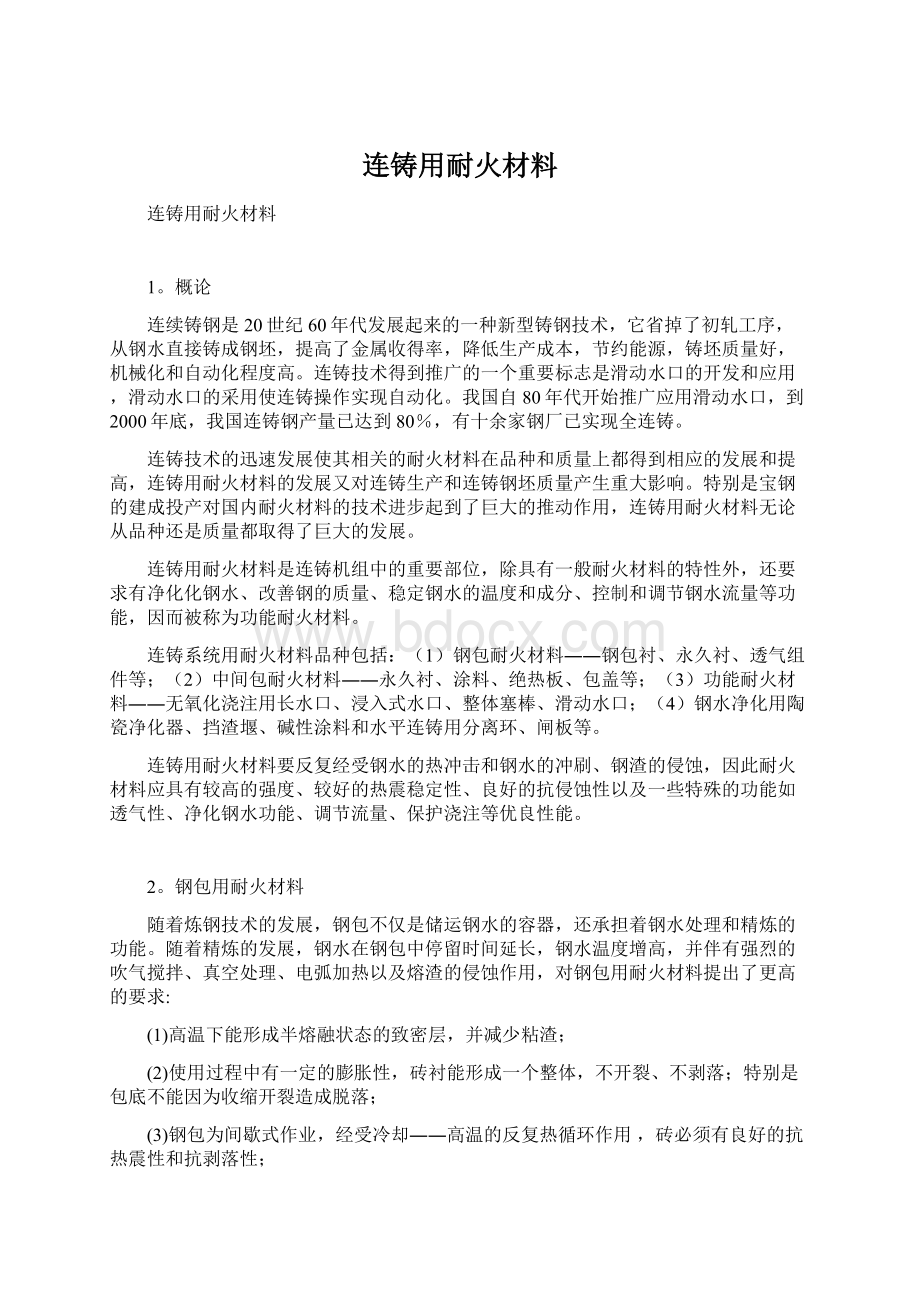
连铸用耐火材料
连铸用耐火材料
1。
概论
连续铸钢是20世纪60年代发展起来的一种新型铸钢技术,它省掉了初轧工序,从钢水直接铸成钢坯,提高了金属收得率,降低生产成本,节约能源,铸坯质量好,机械化和自动化程度高。
连铸技术得到推广的一个重要标志是滑动水口的开发和应用,滑动水口的采用使连铸操作实现自动化。
我国自80年代开始推广应用滑动水口,到2000年底,我国连铸钢产量已达到80%,有十余家钢厂已实现全连铸。
连铸技术的迅速发展使其相关的耐火材料在品种和质量上都得到相应的发展和提高,连铸用耐火材料的发展又对连铸生产和连铸钢坯质量产生重大影响。
特别是宝钢的建成投产对国内耐火材料的技术进步起到了巨大的推动作用,连铸用耐火材料无论从品种还是质量都取得了巨大的发展。
连铸用耐火材料是连铸机组中的重要部位,除具有一般耐火材料的特性外,还要求有净化化钢水、改善钢的质量、稳定钢水的温度和成分、控制和调节钢水流量等功能,因而被称为功能耐火材料。
连铸系统用耐火材料品种包括:
(1)钢包耐火材料――钢包衬、永久衬、透气组件等;
(2)中间包耐火材料――永久衬、涂料、绝热板、包盖等;(3)功能耐火材料――无氧化浇注用长水口、浸入式水口、整体塞棒、滑动水口;(4)钢水净化用陶瓷净化器、挡渣堰、碱性涂料和水平连铸用分离环、闸板等。
连铸用耐火材料要反复经受钢水的热冲击和钢水的冲刷、钢渣的侵蚀,因此耐火材料应具有较高的强度、较好的热震稳定性、良好的抗侵蚀性以及一些特殊的功能如透气性、净化钢水功能、调节流量、保护浇注等优良性能。
2。
钢包用耐火材料
随着炼钢技术的发展,钢包不仅是储运钢水的容器,还承担着钢水处理和精炼的功能。
随着精炼的发展,钢水在钢包中停留时间延长,钢水温度增高,并伴有强烈的吹气搅拌、真空处理、电弧加热以及熔渣的侵蚀作用,对钢包用耐火材料提出了更高的要求:
(1)高温下能形成半熔融状态的致密层,并减少粘渣;
(2)使用过程中有一定的膨胀性,砖衬能形成一个整体,不开裂、不剥落;特别是包底不能因为收缩开裂造成脱落;
(3)钢包为间歇式作业,经受冷却――高温的反复热循环作用,砖必须有良好的抗热震性和抗剥落性;
(4)为保持钢水的洁净度,要求钢包有良好的抗侵蚀性,高温下耐火材料尽量少熔入钢水;
(5)从经济角度出发,要求钢包衬有良好的施工性能且价格适当。
包衬用耐火材料已从定形制品向不定形材料发展。
包衬用材料
永久衬用耐火材料
钢包一般采用三层砌筑结构即隔热层、永久层和工作层。
绝热层一般采用轻质粘土砖、硅酸铝纤维毡或轻质浇注料砌筑。
而永久层目前普遍采整体打结的方式,材质有水玻璃结合的铝镁浇注料、低水泥或超低水泥高铝浇注料。
永久衬的施工是在隔热层砌筑完后,在其表面粘一层牛皮纸以防吸浆,然后放上胎模浇注永久层,永久层施工一般采用振动成型,为改善施工条件、减轻劳动强度,我厂开发了钢包永久衬用自流浇注料,取得了较好的使用效果。
包壁用耐火材料
我国在80年代钢包普遍采用高铝砖和叶蜡石砖,随着连铸的发展,钢水在钢包内停留的时间延长,砖衬出现熔损、剥落,寿命降低。
为提高包衬寿命,减少渣的侵蚀,开发了在Al2O3-SiO2系材料中引入MgO的Al2O3-SiO2-MgO系材料,利用MgO与Al2O3高温下生成镁铝尖晶石,且产生一定的膨胀作用,具有极好抗侵蚀和抗渣渗透性。
同时MA尖晶石可与渣中的FeO反应形成铁铝尖晶FeO+MgO•Al2O3≒MgO+FeAl2O4;过量的FeO与MgO形成固溶体,提高了渣的粘度,减少了渣的侵蚀与渗透。
水玻璃结合不烧砖
水玻璃结合铝镁砖骨料采用一级矾土,细粉用特级矾土粉和一级镁砂粉,采用水玻璃作结合剂,机压成型后经低温热处理即为成品.该产品在模铸的大、中型钢包上使用,取得了较好的使用效果。
为提高铝镁砖的抗侵蚀性,在不烧铝镁砖的基础上添加石墨制成的不玻璃结合铝镁碳砖,在中小型模铸钢包上使用,寿命达到50~100次,因其价格低廉,在中小钢厂得到推广。
树脂结合铝镁碳砖和镁铝碳砖
树脂结合铝镁碳砖原料采用特级矾土熟料、高铝刚玉和镁铝尖晶石等作骨料,添加镁砂细粉、磷片石墨、碳化硅及氧化铝粉,用树脂作结合剂经高压成型,低温热处理。
该产品具有强度高、抗侵蚀性好、抗剥落性好、抗热震性和不粘渣等优点。
在大型连铸钢包上使用,寿命达到50~100次;特别是在LF-VD精炼炉上得到应用。
树脂结合镁铝碳砖与铝镁碳砖生产工艺基本相同,主要原料是在镁砂中添加预合成的镁铝尖晶石,利用两者在高温下线膨胀系数差别较大的特性,来缓冲因温度变化产生的热应力,减轻热剥落;添加炭素材料,高温下形成碳网结构,有效地阻止熔渣的侵蚀和渗透。
镁铝碳砖有较好的抗侵蚀性,适用高碱度渣及LF精炼包等更苛刻的条件。
目前国内大中型钢包包壁普遍采用树脂结合的铝镁碳砖和镁铝碳砖,已经满足了钢厂的需要。
LF(电弧加热钢包精炼)法及LFV(真空电弧加热钢包精炼)法钢水温度更高、熔渣碱度大、加之吹气搅拌以及真空或还原气氛,耐火材料要承受化学反应与熔损、高温真空下的挥发、熔渣的侵蚀以及热冲击和机械冲刷,要求耐火材料的强度要高、热震稳定性好、抗渣侵蚀性好。
精炼炉包壁采用铝镁碳砖或镁铝碳砖,使用寿命普遍达到50炉以上;在真空冶炼的情况下,使用镁钙碳砖的效果要优于铝镁碳砖。
ASEA-SKF(电弧加热电磁搅拌精炼)法冶炼,耐火材料要经受电极电弧的强烈辐射、高碱度高温熔渣的强烈侵蚀与溶解、高温真空下的还原、电磁搅拌和包底吹氩所造成强烈冲刷和磨损以及内衬温度的急剧变化。
我国在SKF炉内衬高侵蚀区采用电熔再结合镁砖及镁铬砖,低侵蚀区采用高铝砖,平均寿命达到30炉左右。
欧洲普遍采用镁白云石砖,寿命在20~30炉。
表1优质钢包衬砖
铝镁尖晶石碳砖
铝镁碳砖
镁铝碳砖
镁碳砖
PN-SPC1
PN-SPC2
PN-AMC
PN-MAC
PN-MT10
PN-MT14
Al2O3%≥
60
70
65
15
MgO%≥
15
10
10
70
78
74
C%≥
7
7
7
8
10
14
显气孔率%≤
10
10
11
10
5
4
体积密度g/cm3≥
耐压强度MPa≥
80
85
60
55
50
40
重烧线变化%
(1550×3h)≥
0~+
+~+
+0~+
+~+
高温抗折强度MPa≥
(1400℃×,埋炭)
6
6
7
6
8
包衬用浇注料
80年代,国内中小钢包采用水玻璃结合的铝镁浇注料,以一级高铝矾土作骨料,添加镁砂细粉,用不玻璃作结合剂,外加氟硅酸钠作促凝剂,在中小钢厂模铸钢包上使用平均寿命达到60~80次,基本满足了模铸生产的需要。
但随着连铸的发展,浇钢时间延长,浇钢温度提高,水玻璃结合的铝镁浇注料其抗侵蚀性、抗剥落性已不能满足生产的需要。
在90年代,又开发了低水泥、超低水泥结合的尖晶石质浇注料,其品种有适应中小钢厂使用的矾土尖晶石浇注料、适应大型钢包和精炼需要的刚玉尖晶石浇注料。
矾土尖晶石浇注料是以特级矾土为骨料,添加预合成的尖晶石,利用尖晶石抗侵蚀性好和热震稳定性好的特点,同时适量添加镁砂在更高的温度下与矾土颗粒继续反应生成尖晶石,伴随着持续性的膨胀有利于保持高温下的体积稳定性;采用SiO2超微粉和MgO与水形成凝聚结合以及合适的减少剂,实现低水分下有较好的流动性和较高的强度,具有较好的抗侵蚀性和抗剥落性。
矾土基尖晶石浇注料在国内中小型连铸钢包上使用寿命达到100炉以上。
随着大型钢包连铸及精炼的发展,普通的铝镁浇注料已不能满足使用寿命的要求,在此基础上又开发了刚玉尖晶石浇注料,降低水泥用量,合理控制MgO含量,调整尖晶石含量;具有更好的抗侵蚀、抗渗透以及抗剥落性,在宝钢、首钢、武钢等钢厂大型连铸钢包上使用寿命均超过150次,且使用过程中没有大的裂纹和剥落现象。
表2钢包浇注料理化指标
项目
铝镁浇注料
矾土尖晶石浇注料
刚玉尖晶石浇注料
Al2O3%≥
68
72
88
MgO%≥
12
10
7
SiO2%≥
10
8
体积密度g/cm3≥
耐压强度110℃×24h
Mpa1100℃×3h
1550℃×3h
23
60
70
65
70
80
80
60
110
抗折强度110℃×24h
MPa1100℃×3h
1550℃×3h
6
9
5
8
11
8
8
12
线变化率%1550℃×3h
+
+~+
++
渣线用耐火材料
钢包渣线区处于高碱度炉渣侵蚀、剧烈的温度变化、钢水的机械冲刷、以及长时间精炼条件下真空挥发、电磁搅拌、电弧辐射等苛刻条件,损毁十分严重,因此自九十年代以来抗侵蚀性好、热震稳定性优良的优质镁碳砖就成为钢包渣线部位的首选材料。
在抗侵蚀方面,选用大结晶镁砂,同时添加较高的抗浸润性好的石墨,采用高压成型,为防止石墨的氧化,添加金属铝、金属硅、铝镁合金、碳化硼、硼化锆等材料,其作用主要是在较低的温度下比碳先氧化,同时生成致密的保护层避免碳的进一步氧化,从而提高了镁碳砖的抗侵蚀性。
目前国内钢包渣线部位普遍采用MT14A、MT14B镁碳砖砌筑,使用寿命一般在60~70次左右,精炼包渣线寿命在30次左右,个别钢厂已实现渣线与包壁同步。
表3镁碳砖的理化指标
项目
指标
MT-10A
MT-10B
MT-10C
MT-14A
MT-14B
MT-14C
MT-18A
MT-18b
MT-18C
MgO%≥
80
78
76
76
74
74
72
70
70
C%≥
10
10
10
14
14
14
18
18
18
显气孔率,%≤
4
5
6
4
5
6
3
4
5
体积密度g/cm3≥
常温耐压强度MPa≥
40
35
30
40
35
25
40
35
25
高温抗折强度(1400℃×30min)MPa≥
6
5
4
12
8
5
10
7
4
抗氧化性
提供实测资料
包底用耐火材料
钢包包底不仅要承受钢水的静压力,还要承受来自钢水的巨大冲击,由于反复热特循环产生裂纹,炉渣渗透造成结构剥落,以及冲击与包底砖之间接缝处的侵蚀,以致钢水侵入接缝,损毁更为严重;以及来自浇钢过程中钢流的冲刷和吹氩形成的涡流,对包底材料均产生不利的影响。
目前国内包底是采用不烧铝镁碳砖或尖晶石浇注料,铝镁碳砖采取立砌,以增加包底厚度同时可减少包底砖脱落,冲击区砖厚度加大或使用预制大砖以提高包底寿命。
通常包底砖均不能与包壁同步,需中途更换一次或两次包底砖,个别厂家采取铝镁碳砖平砌立砌相结合的办法或砖砌与浇注料相结合的办法来延长包底寿命,有些厂家已实现包底与包壁同步。
3.包底透气砖
炉外精炼其主要功能是脱气、脱氧、脱碳、合金化、去除夹杂物、以及均匀钢水温度和化学成分等。
其主要方法为搅拌技术,最常用为吹氩搅拌。
吹氩方法有上吹法和底吹法。
上吹法使用吹氩喷枪,其材料一般为低水泥刚玉-碳化硅质浇注料,上吹法安全系数高,但喷枪寿命短,耐火材料消耗高,且吹氩效果不如底吹好,随着连铸技术的发展,上吹法已很少使用。
底吹法是在钢包底部安装透气砖,通过透气砖向钢包内吹入氩气,来达到钢水搅拌的目的,促进了精炼中化学反应的完全,降低了钢水中的有害成分,降低了钢坯中气体、非金属夹杂,均匀了钢水成分,缩短了冶炼时间,提高了经济效益。
因透气砖使用条件苛刻,透气砖应具备良好的透气性、优良的抗侵蚀性、足够的强度、抗钢水渗透性好、具有良好的抗热冲击性在反复吹氩时不开裂不剥落、安装简单、安全可靠。
透气砖的结构类型有:
弥散型、直通孔式、直通狭缝式、镶嵌式、迷宫式、组合式。
透气砖损毁的主要因素有:
气体、熔体对透气砖的高速冲刷造成熔蚀或生成低熔物造成的局部堵塞;透气砖在热压下变质,使透气减小不能通气而停用;高温熔体通过孔隙渗入砖体或套砖与砖本体之间造成严重蚀损;因热震造成的损坏剥落。
透气砖主要材质有:
刚玉质、铬刚玉质、高铝质和镁质等。
提高透气砖寿命的主要措施:
选择高抗冲刷、耐热震的材料;改进透气砖结构;透气砖合理安装;快速更换系统;增设安全报警装置;主气体管路的维修。
4.滑动水口
早期的钢包铸钢控制是靠塞棒来实现的,但塞棒存在使用寿命低,安全性差,消耗大等诸多问题,现在已被滑动水口所取代。
滑动水口位于钢包的外部,起钢水流量的控制调节作用,它不受钢水搅拌、熔剂喷入和钢水停留时间的影响,且操作方便,采用滑动水口易实现浇注操作自动化,消除钢水、渣的停留时间以及浇注时间对流量控制的影响。
滑动水口装置与塞棒系统比较其优点如下:
(1)装置安装在钢包外部,装卸方便、浇注安全可靠,能实现浇注自动化;
(2)钢包烘烤时间短,预热温度高,钢水温降少;
(3)能准确控制钢水的浇注速度,有利于提高钢的质量;
(4)钢包周转快,间歇时间短,受急冷急热的影响小,能延长钢包寿命,降低耐火材料消耗。
滑动水口的结构形式包括:
机械装置部分;驱动部分(手动与液压)。
其运动方式有两种:
直线往复式――当滑板作直线往复运动时,调节滑动板与固定板之间的流钢孔来控制钢流。
回转式――滑动板作旋转运动,以调节流钢孔大小和控制钢水流量。
滑动水口中的滑板直接控制钢水流量,为改善钢的质量,防止结瘤堵塞,使浇注系统易于实现自动化,板坯连铸机多采用双层式滑动机构。
滑板则是决定滑动水口功能的关键部分,由于滑板反复接触高温钢水,蚀损严重,使用条件苛刻。
要求滑板有高强度、抗侵蚀、抗剥落等良好性能,在浇注过程中保证滑动面之间不能漏钢水,滑板必须具有以下性能:
(1)滑动面应光滑、平整度≤;
(2)机械强度高;(3)耐钢水和熔渣的侵蚀能力强;(4)不易附着钢水;(5)有良好的热震稳定性,保证使用中不会从裂纹中漏钢。
钢包中的滑动水口主要包括上下座砖、上下水口、上下滑板几部分,其密封主要在上水口与上滑板、下滑板与下水口相连接处用火泥,上下滑板之间靠滑板的平整度来密封。
浇注过程中,一般每浇一炉或几炉后,必须更换下滑板和下水口,并重新安装,以保证使用的安全。
滑板砖
滑板是连铸生产中控制钢水流量的关键部件,其性能的好坏直接决定着生产的安全和正常进行。
影响滑板使用有以下几个方面:
(1)由于热震引起的铸孔周围的龟裂和碎裂。
在高温钢水与耐火材料接触时都要产生微小的裂纹,因此提高滑板材料的热震稳定性以及限制裂纹的扩展所采取的措施就极为重要;
(2)钢水和熔渣侵蚀和冲刷。
滑板的抗侵蚀和冲刷能力将明显影响其使用寿命。
侵蚀主要来自钢水中的Mn、MnO、FeO、CaO等成分与滑板中的SiO2等杂质成分引起的,减少滑板中的SiO2有利于提高抗侵蚀性,增加碳能有效阻止钢水及氧化物的渗透和反应,添加防氧化剂可有效防止碳的氧化。
(3)滑板材料在滑动中磨损,特别是当滑板有一定的损伤,凝固的钢在滑动时引起的滑动面磨损尤其严重。
因此应提高滑板强度,另外还要使滑板保持较低的气孔率和平滑的表面,以减少钢水的贯通和渗透。
采用高压成型和真空油浸是提高强度和降低气孔率的有效途径。
烧成铝碳滑板
烧成铝碳滑板是以氧化铝原料如板状刚玉、电熔刚玉、莫来石、特级矾土等为主要原料,引入碳素材料如磷片石墨、碳黑、沥青、活性碳等,并添加其它少量材料如金属硅、金属铝、碳化硅、碳化硼等,以酚醛树脂作结合剂,经配料、混合,高压成型,在1300~1500℃的还原气氛中烧成,再经油浸碳化处理,最后对工作面进行磨光,用钢带在滑板外围打箍,并在非工作面粘贴石棉板和马口铁后,就成为滑板成品。
铝碳滑板基本生产工艺是:
氧化铝原料(刚玉、矾土熟料)经破碎筛分后按一定颗粒级配进行配料,加入湿碾机或高速混练机中混合3~5分钟,加入酚醛树脂结合剂,混匀后再加入石墨、防氧化剂(金属硅、碳化硅、碳化硼、金属铝等)、氧化铝细粉,混合10~30分钟出料。
成型采用630吨以上高吨位压砖机,按照砖的形状、尺寸,精确称量物料,需要复合的要分别称量两种物料的重量,称量好的料加入到模具内,成型到规定尺寸,每块砖要测量外形尺寸、平整度、对角线尺寸,每班要抽查10%的单重,每一车砖要检测气孔率、体积密度,凡发现不合格现象必须报废并查找原因。
成型后的砖坯一般需经自然干燥后才能入干燥器,砖坯在干燥器内按一定的升温曲线进行干燥,干燥后的砖坯经过检查后合格的半成品才能装窑。
烧成采用梭式窑、倒焰窑、隧道窑等烧成设备,滑板的烧成采用还原气氛,需要砌匣钵,装入滑板后用炭粒保护,烧成温度在1300~1500℃。
烧成后滑板要进行油浸,油浸采用立式或卧式真空-加压油浸装置,滑板经预热后放入油浸罐内,密封后抽真空至真空度133Pa以下,充入预热到200℃左右的中温沥青,沥青被吸入到滑板的开口气孔中,为了让沥青更多地进入到滑板的气孔中,对罐内进行加压,压力达到~,经一定时间的浸渍后既可卸压,抽出沥青,取出滑板。
有些滑板需要干馏处理,使沥青碳化,以防止使用过程中粘连或污染环境,热处理温度一般在500℃左右;浸油或热处理后的滑板需对表面沥青进行清理。
为了提高滑板的使用性,防止裂纹的产生和扩大,要用钢带对滑板周边打箍。
为了提高滑板在开拉过程中的灵活性,防止从滑动面之间漏钢,滑动面要在磨床上进行加工,要求平整度小于。
磨制后的滑板经检验合格后,要在背面粘贴石棉垫和马口铁,其作用主要是减少通过滑板传递到滑动机构上热量,防止烧毁机构。
滑板生产中需注意的事项:
(1)配料要严格按比例称量,细粉要混均匀,配混合粉时,添加剂要加在物料中间,经混合机搅拌的混合粉要抽查其化学成分是否均匀;
(2)经湿碾机或高速混练机混合的物料要控制其温度,以防止物料温度过高或过低影响混料效果和成型性。
冬季需采取保温措施或对物料加热,夏季要尽量降低室温度,最好能保持在25℃左右。
(3)成型时压力要先轻后重,中间排气,避免层裂;经常检查底盖板的弯曲度,防止滑板变形造成废品;(4)严格控制烧成过程中的升温曲线,特别是含氧化锆的产品,升降温时必须严格控制防止出现裂纹;(5)滑板磨制时必须严格控制平行度和平整度;(6)滑板在搬运或加工过程中要轻拿轻放,在固定或打箍时要用木锤或橡皮锤轻轻敲打,严禁用铁锤。
滑板在使用中需注意的事项:
(1)滑板运到使用现场后要先放在烘干房中预热;
(2)滑板安装时,与水口接触面火泥要抹匀,不准用铁锤敲打;(3)安装后要检查弹簧的压力,并对机构进行推拉,以检查开闭情况;(4)使用中要注意滑板的开拉情况,多次使用的滑板,要检查滑动面的裂纹、侵蚀、拉毛情况;在检查中发现有夹钢现象时严禁再次使用;(5)尽量减少烧氧对滑板的影响。
铝锆碳滑板
影响滑板长时间使用的主要因素是各种裂纹的形成。
为提高滑板的使用寿命就必须进一步提高其抗热震稳定性,降低材料的热膨胀系数是最有效的途径。
用进一步增加滑板中的碳含量来降低热膨胀系数是不可取的,因为这也增加了碳氧化的危险,从而可降低其抗冲刷和抗侵蚀性能。
增加原料中的SiO2量即增加莫来石含量也可以降低热膨胀系数,但同样使抗侵蚀性下降。
ZrO2在升温和降温的过程中伴有较大体积变化,这种可逆的体积变化可有效抵消材料内的热应力,热震稳定性大大提高。
锆莫来石在较低的温度下的热膨胀与莫来石是相同的,但在1000~1500℃的高温下的热膨胀率明显低于莫来石。
所以,滑板配料中引入锆莫来石料可以使滑板的抗热震性明显提高,特别是在高温下的热波动中很不容易产生裂纹。
另外,ZrO2具有优良的抗侵蚀性,使得含锆莫来石的滑板的抗侵蚀性优于含莫来石的滑板。
可以说,铝锆碳滑板是目前性能最优的滑板。
铝锆碳滑板制造工艺与铝碳滑板的主要差别在于有锆莫来石取代了莫来石,其加入量在7~45%之间,过少则显示不出优良的抗热震性和抗渣性,若过多,滑板的抗侵蚀性不理想。
铝锆碳滑板的热膨胀系数低、弹性模量小,因而其抗热震性大大提高,但是引入锆莫来石可能会降低制品的冷态和热态强度。
另一类滑板,配料中引入锆刚玉料。
锆刚玉料含Al2O370~90%,ZrO22~30%,主晶相是刚玉和斜锆石,显微结构呈现出单斜ZrO2分散在刚玉晶粒的晶界上。
这种锆刚玉料是用工业氧化铝和氧化锆原料,采用电熔法或烧结法合成,价格较锆莫来石贵。
目前有些厂直接添加ZrO2来制作铝锆碳滑板,也取得了较好的使用效果。
低碳滑板
在浇注超低碳钢、合金钢、高氧钢等钢种时,就要采用低碳滑板或无碳滑板。
其品种主要有碳含量低于5%的铝碳、铝锆碳滑板或不含碳的刚玉质、刚玉莫来石质滑板。
碱性滑板
在浇注高氧钢、高锰钢、Ca处理钢、镇静钢等钢种时,由于钢水中的氧与滑板中的碳反应,因氧化失碳形成变质层,结构疏松,被钢水冲刷而损毁;滑板中的Al2O3与钢水中的FeO(MnO)反应生成低熔物造成化学侵蚀。
改进的方法是从提高抗侵蚀性和耐磨性入手,一方面提高MgO含量,同时改善配料中的颗粒组织,以增强高温强度。
碱性滑板的主要材质有镁质、镁尖晶石质以及镁锆质等。
表4高温烧成滑板理化指标
中间包三层式滑板
中间包多炉连浇时,由于浇注时间长,常出现中间包塞棒失控,采用滑动水口可有效避免事故的发生。
滑动水口安装在中间包底部,它不像塞棒那样长时间浸泡在钢水中。
中间包滑动水口结构与钢包不同,在连铸过程中,为使浸入式水口保持在同一浇注位置,上下板都是固定的,另加一块中间板来对钢水流量起控制和调节作用,因此中间包滑板采用三层式。
三层式滑板的特点是中间的滑动板不用火泥,用金属带嵌板进行固定,对控制裂纹的扩展起到良好的作用。
要严格检查滑动面的平行度。
中间滑板滑动面的不平行度不应超过。
浇注初期,为防止钢水在滑动水口的流钢道内冷凝,安装有塞棒或陶瓷溢流管,阻止冷钢液流入水口信道,保持钢水在中间包内形成必须的液面,并严防更换浸入式水口时,因钢水冷却在信道内凝结或非金属性夹杂物,堵塞信道。
但由于中间包的容量和受的钢水温度均与钢包有较大的差别。
且使用条件不同,对中间包滑动水口装置及其所用耐火材料的要求更高。
(1)耐火材料部件与熔渣不发生相互作用;
(2)中间包内钢水温度钢包内钢水温度40~80℃;
(3)中间包与滑动水口装置的耐火材料要预先加热到800℃以上;而钢包滑动水口装置的耐火材料在浇注开始前仅为100℃左右;
(4)浇注时中间包滑动水口装置,耐火材料使用一次的温差从开始的700~800℃至1520~1560℃(浇钢温度);而钢包滑动水口的耐火材料多次使用时,一个周期的温差则的100~400℃至1600~1670℃;
(5)中间包滑动水口装置在使用时要求有特定的功能:
吹氩、防止钢水在流道内凝结、防止结瘤,保证浇注顺利。
中间包滑板的材质一般采用低SiO2或无SiO2的铝锆碳滑板,镁尖晶石滑板。
不烧滑板
我国发展了一种工艺比较简单、成本较低,使用效果良好不烧滑板。
这种滑板的配料与烧成滑板相同,其原料可以是刚玉、莫来石、一级高铝熟料等,加入鳞片石墨,含碳量10~12%,另外加入碳化硅和硅粉。
这时加入SiC是重要的,其目的是提高滑板的中、高温强度和抗氧化性,有的滑板加入的SiC较多,所以亦称为Al2O3-SiC-C不烧滑板。
采用酚醛树脂作结合剂,成型、热处理及磨制后即为成品。
不烧滑板相对于烧成滑板来讲,在制造过程中不用烧成、油浸和干馏热处理,简化了生产工艺。
另外,有的滑板制成复合制品,在滑板的主要侵蚀部分即铸孔和滑动面采用刚玉、莫来石配料,其它部位采用二等高铝熟,这样可以大幅度降低成本,而对使用几乎没有影响。
不烧滑板相对于烧成滑板来讲,强度偏低、气孔率稍高。
但是使