2191420mm螺旋焊管机组报价书1.docx
《2191420mm螺旋焊管机组报价书1.docx》由会员分享,可在线阅读,更多相关《2191420mm螺旋焊管机组报价书1.docx(28页珍藏版)》请在冰豆网上搜索。
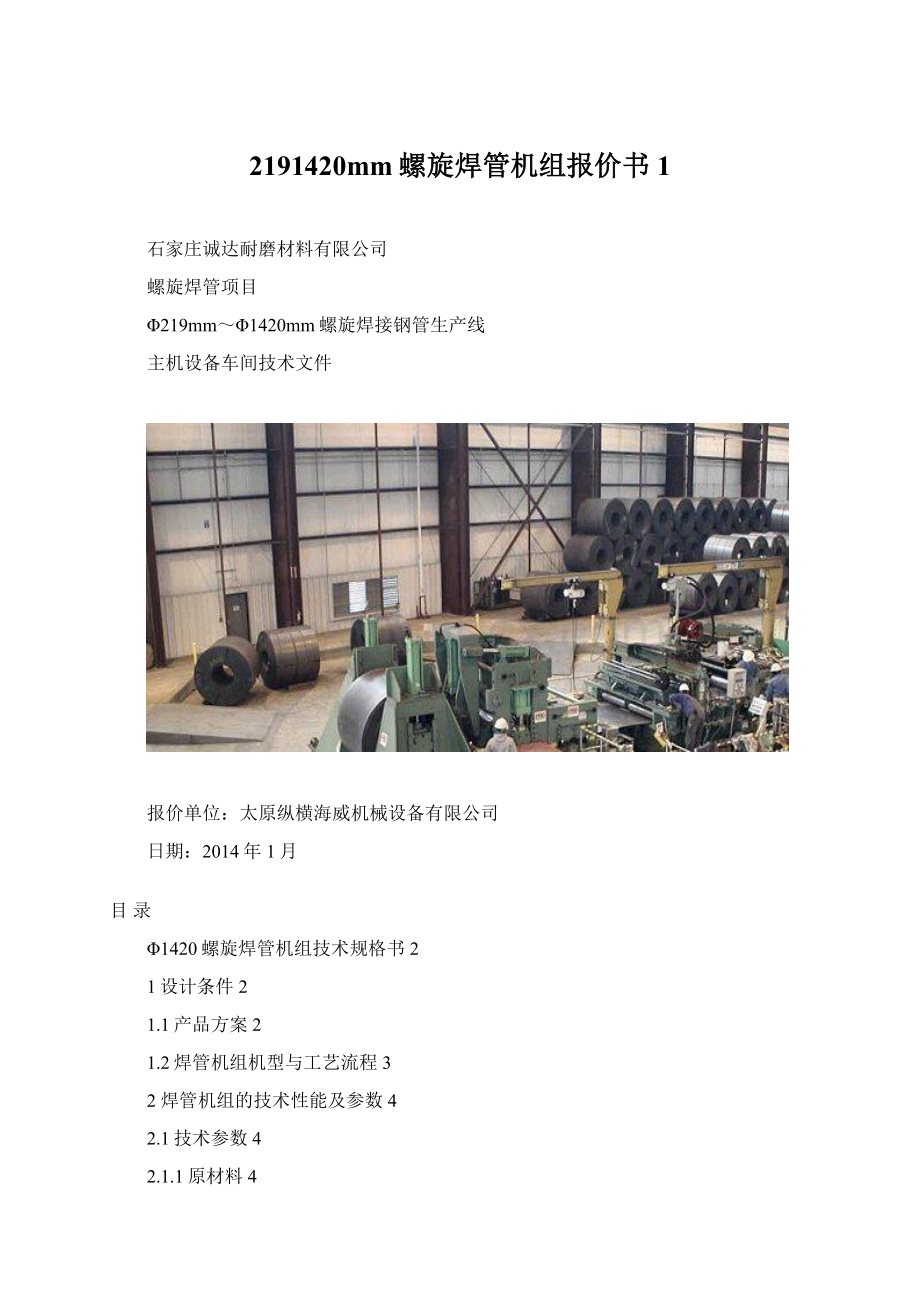
2191420mm螺旋焊管机组报价书1
石家庄诚达耐磨材料有限公司
螺旋焊管项目
Φ219mm~Φ1420mm螺旋焊接钢管生产线
主机设备车间技术文件
报价单位:
太原纵横海威机械设备有限公司
日期:
2014年1月
目录
Φ1420螺旋焊管机组技术规格书2
1设计条件2
1.1产品方案2
1.2焊管机组机型与工艺流程3
2焊管机组的技术性能及参数4
2.1技术参数4
2.1.1原材料4
2.1.2焊接5
2.1.3成品5
2.2机组主要设备表5
2.3控制系统7
2.3.1系统工作条件7
2.3.2控制系统结构及特点7
2.3.3控制系统各主要用电设备的电压等级8
2.3.4系统设备构成8
2.3.5操作方式9
2.4液压系统9
2.5润滑部分11
2.6机组非标设备:
11
2.6.1上卷车11
2.6.2开卷机11
2.6.3拆头机12
2.6.4夹送辊13
2.6.5矫平机14
2.6.6液压立辊15
2.6.7切割对焊装置10
2.6.8铣边机17
2.6.9递送机18
2.6.10预弯装置19
2.6.11导板装置19
2.6.12成型机20
2.6.13内焊装置22
2.6.14外焊装置22
2.6.15前桥23
2.6.16后桥23
2.6.17飞切机24
2.6.18收集台架24
2.6.19板面清扫装置24
3设备清单与价格25
4设备的供货周期27
5设备的包装、运输27
5.1设备的包装27
5.2设备的运输27
6设备的安装与调试27
7质量承诺及服务项目27
Φ1420mm螺旋焊管机组技术规格书
1设计条件
本项目拟新建一条Φ219~Φ1420mm螺旋焊管生产线。
生产线生产的钢管可以满足国家低压流体输送管(SY/T5037-2000)规定的要求。
1.1产品方案
本项目可直接生产管径为Φ219~Φ1420mm的双面螺旋埋弧焊接焊管,产品符合桩管及流体管标准。
产品标准:
GB/T3091-2001;SY/T5037-2000;
螺旋埋弧焊管生产线的产品能力见表1:
表1Φ1420螺旋焊管机组生产的焊管规格
钢管外径
(mm)
壁厚
(mm)
材质
壁厚
(mm)
材质
备注
219
5~14
Q235
5~12
Q345
508
5~14
Q235
5~12
Q345
600
5~14
Q235
5~12
Q345
711
5~18
Q235
6~14
Q345
762
6~18
Q235
6~16
Q345
813
6~18
Q235
6~16
Q345
914
8~18
Q235
8~18
Q345
1016
8~18
Q235
8~18
Q345
1168
8~18
Q235
8~18
Q345
1219
8~18
Q235
8~18
Q345
1420
8~18
Q235
8~18
Q345
注:
该表可做为设备能力的考核依据。
螺旋埋弧焊管成品定尺:
812.5m
代表钢号:
Q235;Q345
品种:
桩管、流体管、结构管等
1.2焊管机组机型与工艺流程简述
成型方式:
前摆螺旋上卷式,三辊成型五辊外控可调定径成型法。
焊接方式:
内双丝,外双丝双面埋弧焊接。
成型工艺:
前摆式断续生产;
带钢中心定位
工艺流程:
开卷→直头→夹送矫平→立辊对中→剪切板尾、板头→前后卷对接焊→立辊对中→粗铣边→立辊对中→精铣边→板面清扫→板边除锈→立辊对中→递送→预弯及导板→立辊→成型→内焊→外焊→飞切→拨出→落管→清渣→检查补焊→X光探伤→水压试验→超声波检查→平头倒棱→收集→入库
工艺流程简述:
从开卷到定尺切断拨出为螺旋焊管形成的整个流程,此机组承担着将钢板转化生产成螺旋焊管的任务,是整个工艺流程的主体部分,在整个过程中只有在前一卷料料尾与后一卷料料头对接时才需要将机组停下来,对接完成后再继续生产,所以此机组具有连续性强,各工序配合紧密的特点。
首先将带钢卷用行车吊至开卷机的支承辊上,由左右锥头将钢卷夹紧,并可通过操作按钮将钢卷准确移至所要求的递送线中心,然后操作铲刀靠紧钢卷,启动支承辊电机使钢卷旋转,在铲刀的配合下将带钢头打开,并初步直头后送往夹送矫平机。
带头进入夹送辊后,夹送辊压下并将带钢向前送进,通过矫平辊将带钢矫平,带钢继续向前,由一对立辊保证带钢处于递送中心线上,经过剪切对焊装置将板头不规则部分切掉以便顺利进入递送机,在此位置,前一卷带钢的尾部和后一卷带钢的头部完成对接埋弧焊,然后经过粗铣边机把带钢的边缘铣平,消除带钢边缘不齐对成型的影响,经过粗铣边后带钢进入精铣边机,在带钢厚度大于12mm时,为了保证焊接质量良好,熔池深度足够,需要经过精铣边机在钢带的边缘铣出上下倒角以利于成型后的焊接,经过精铣边后的带钢继续向前进入递送机,递送机为螺焊机组的总动力源,用于产生成型力及克服各种阻力,如成型阻力,开卷阻力,矫平阻力,剪切阻力等,将带钢送入成型器,通过成型器的1#、2#、3#成型辊强制钢板变形形成钢管,通过4#、5#、6#、7#成型辊对初步成型的钢管强制定径产生符合尺寸规格的螺旋管,在成型的同时将互相接触的两个边缘,即螺旋管产生的缝隙处,通过林肯埋弧焊机分别从内壁和外壁进行焊接形成螺旋焊管,在后桥上设有自动定尺及钢管切割装置,在生产过程中将钢管按要求的长度切断,拨出,保证机组生产的连续进行。
根据成型理论,在螺旋焊管的生产过程中,不同的板宽、板厚适合生产的钢管直径也有所不同,其基本对应关系如下公式所示:
cosα=B/πDm
其中:
α为成型角
B为钢板宽度
Dm为钢管的中径,Dm=D(钢管外径)-t(钢板厚度)
在实际生产时,可先根据上述的公式计算出所需要的成型角,然后根据计算值调整前桥至合适的位置,调整成型辊至适当的角度,再开始生产。
2焊管机组的技术性能及参数
2.1技术参数
Ø原材料:
原料状态:
热轧钢卷,具有原始轧制边缘
钢卷外径:
Φ1200~2200mm
钢卷内径:
Φ610~760mm
钢板宽度:
650~1500mm
钢卷厚度:
5~18mm
钢卷材质:
Q235B,Q345B
最大卷重:
30T
月牙弯:
≤10/10mm/m
原料塔形:
单侧≤30mm
错层≤15mm
Ø焊接:
采用双面埋弧自动焊接
焊接方式:
内二丝,外双丝埋弧自动焊接
焊接电源:
内双丝:
Ⅰ丝DC-1500
Ⅱ丝AC-1200
外双丝:
Ⅰ丝DC-1500
Ⅱ丝AC-1200
焊接速度:
0.8~2.2m/min
递送速度:
0.6~2.8m/min
Ø成品参数:
钢管直径:
Ф219mm~Ф1420mm
钢管壁厚:
5~18mm
钢管材质:
普通碳素钢,低合金钢,
Q235B,Q345B
螺旋角:
40°~75°
钢管长度:
8~12.5m
Ø机组参数:
年产量:
3~8万吨(三班制)
机组占地面积:
见平面布置图
Ø能源参数:
装机容量:
~600KW
(不含天车,照明等车间其他公辅设施用电)
电源:
三相四线制电压:
380V
频率:
50Hz
控制电压:
220V
压缩空气:
压力:
0.4~0.7MPa
流量:
1.5M3/Min
水源:
压力:
0.3~0.5MPa
流量:
2M3/min
2.2机组主要设备表
序号
名称
数量
备注
1
开卷机
1
2
直头机
1
3
夹送矫平机
1
两辊夹送,七辊矫平
4
电动立辊
3
5
剪切对焊装置
1
6
粗铣边机
1
带碎屑输送
7
精铣边机
1
带碎屑输送
8
板面清扫装置
1
9
手动立辊
1
10
递送机
1
11
预弯机及导板装置
1
12
成型机
1
13
前桥
1
14
内焊装置
1
15
外焊装置
1
装于扶正器上
16
后桥
1
含落管器
17
飞切小车
1
18
主机电控系统
1
19
主机液压系统
1
外购配套设备
用户自备
20
焊机DC-1500
2
美国林肯公司
21
焊机AC-1200
2
美国林肯公司
22
对焊焊头
2
美国林肯公司
电源与内焊共用
23
焊剂处理设备
1
国内配套
24
焊剂输送及回收装置
2
国内配套
25
等离子切割机
1
国内配套
26
X光探伤设备
1
国内配套
27
离线超声波检测设备
1
国内配套
28
焊缝激光跟踪系统
1
国内配套(可选)
✧注:
车间风,水,电能源由买方提供。
电源到控制柜电缆由买方提供,控制柜到设备的配线由买方提供。
设备基础及安装用垫铁由买方负责。
2.3控制系统
本套技术方案主要描述本机组对电气传动及自动化控制系统的技术要求,并给出该项目的电气传动及自动化控制系统的技术设计方案,具有成熟、先进、可靠的特点,整套设备维护、检修简便。
Ø系统工作条件
现场条件:
安装:
户内安装
储藏温度:
-40℃~+65℃
工作温度:
电机:
0℃~+40℃
电机高温地点:
0℃~+65℃
控制设备:
0℃~+40℃
操作设备:
0℃~+40℃
交流电源基本条件:
电压波动:
±10%最大
频率波动:
Max±3%
相间平衡差异:
Max±2%
交流频率:
50Hz
系统进线电源:
380V,50Hz,3相4线
电压等级:
低压380V,3相4线
控制电压DC24V,AC220V(单相)
Ø控制系统结构及特点
本套系统是在充分考虑机组的生产工艺特点及PLC,HMI控制系统的硬件、软件发展趋势的前提下、遵照系统工作可靠、设备稳定实用、技术先进的原则,采用了控制系统PLC,HMI(HumanMachineInterface)(电气传动—自动化仪表—电控系统)三合一的设计方案。
•机组速度自动控制:
机组的速度给定及控制分手动及自动控制。
手动控制时,由操作工在辅助操作台上人为给定及控制;
自动控制时,由机组的自动化控制系统PLC,根据机组控制工艺要求、由操作工在主操作台HMI人机画面输入设定参数,各单机的速度给定值由PLC传输给相应的交直流变频装置,实现机组的速度自动控制。
•顺序控制:
机组各设备的顺序控制,由操作人员在操作台上进行操作,再由PLC根据工艺要求进行联锁后,输出给各设备的执行机构进行顺序控制。
·介质系统控制:
介质系统的各阀组的控制。
由自动化控制PLC根据机组各设备的联锁要求进行控制。
Ø控制系统各主要用电设备的电压等级
PLC电源AC220V
PLC信号输入DC24V
PLC信号输出DC24V(驱动信号灯)
PLC信号输出DC24V(驱动中间继电器)
非调速电动机AC380V
液压电磁阀DC24V/AC220V
信号灯DC24V/AC220V
Ø系统设备构成
控制台柜
主要由操作台、交直流传动控制柜、PLC柜、辅助控制柜等组成;
操作台配有数显表、设备操作按钮、控制电源开关的合/分闸及HMI系统;
PLC柜用于安装设备控制系统的PLC;
直流传动控制柜用于安装系统的全数字直流调速装置。
辅助控制柜用于安装系统的辅助设备的控制回路元件。
机旁控制箱/按钮盒
现场设备主要由现场检测元件及机旁控制箱/按钮盒组成。
·控制箱:
在操作平台上设置有现场控制箱,主要用于在操作平台上控制设备启动、停止。
面板上安装有相应的控制按钮和信号灯。
·按钮盒:
在现场还设有一些设备的启动、停止,面板上安装有操作控制按钮和信号灯。
·接线盒:
为方便现场检测元件所接电缆的铺设,在现场设备还设有就近接线盒。
Ø操作方式
本套系统的操作方式为两种方式:
机旁控制方式、集中控制方式。
机旁控制方式是指通过操作安装在设备附近的按钮盒上按钮达到每个单独系统设备自己独立工作或停止的操作方式,这种操作方式应用于设备调试、设备发生故障检修及系统的日常检修时,为非正常日常操作方式。
集中操作方式是指通过PLC系统,通过操作安装于操作室内的操作台或柜面的元件达到让远程设备根据一定的连锁条件运行或停止的操作方式,为正常日常操作方式。
Ø元件选择:
感应器和继电器选用LG产品
PLC选用日本三菱系列产品
直流调速器选用英国欧陆系列产品
交流变频调速器选用日本富士系列产品
2.4液压系统
液压系统采用先进成熟的液压技术,机组液压系统由液压站、液压阀组和液压管路组成,控制在线执行元件的操作。
阀组全部采用集成块阀组。
系统设有独立循环过滤冷却装置,回油管路设置回油过滤器。
本机组全线共设3个液压站。
主机前桥液压站一套,递送机液压系统一套,后桥液压系统一套。
主机前桥液压系统用来操作前桥摆动,开卷机,夹送矫平等前桥上的液压执行元件。
由液压泵站,集成块阀组,配管系统组成。
✦液压泵站:
泵站组成:
由泵源、主油箱、冷却器、电源接线盒、回油滤清器、吸油过滤器等组成。
主泵源功率:
37KW
油箱容积:
1.5M3
液压油型号:
N46#抗磨液压油
冷却方式:
水冷
✦阀组:
阀组采用集成块阀组,共4组。
分别控制前桥的不同设备的执行元件动作。
维护方便,简单。
✦液压配管:
液压配管为连接各液压阀组,阀组和液压站,阀组和执行元件所用的钢管,软管,接头等液压连接件。
液压配管管路全部采用热轧无缝钢管,耐压程度高,无泄漏。
液压配管配有专用的塑料管夹,防止管路由于高压产生的振动,安全可靠。
管路的铺设为明沟铺设,及在地面制作用于配管行走的沟槽,增加安全性。
递送机液压系统专门为递送机提供液压动力,保证递送机始终平稳可靠。
✦液压泵站:
泵站组成:
由泵源、主油箱、冷却器、电源接线盒、回油滤清器、吸油过滤器及蓄能器等组成。
油箱容积:
0.5M3
液压油型号:
N46#抗磨液压油
冷却方式:
水冷
✦阀组:
阀组采用集成块阀组,共1组。
用于控制递送机柱塞缸。
✦液压配管:
液压配管为连接各液压阀组,阀组和液压站,阀组和执行元件所用的钢管,软管,接头等液压连接件。
液压配管管路全部采用热轧无缝钢管,耐压程度高,无泄漏。
液压配管配有专用的塑料管夹,防止管路由于高压产生的振动,安全可靠。
管路的铺设为明沟铺设,及在地面制作用于配管行走的沟槽,增加安全性。
后桥液压系统为控制后桥微调和落管器等液压执行元件。
由一个液压泵站和两个阀组组成。
三套液压系统相互独立,保证了各液压执行元件的正常运行,在机组正常运行的过程当中,不用的液压站可以停止以节省能源。
液压元件:
液压阀选用国产合资力士乐产品。
(北京华德或上海华德)
电机采用江苏贝德产品。
2.5润滑部分
本机组减速箱采用稀油池润滑,确保机组的稳定可靠运行。
成型辊采用集中干油润滑系统。
2.6机组非标设备:
设备所有轴承选用国产哈、瓦、洛大厂产品。
2.6.1开卷机
用途:
支承悬挂钢卷
位置:
上卷车后移位置的两侧
技术参数及结构:
开卷机由夹卷锥头、活动支撑架,托辊及底座组成。
锥头为铸钢件,活动支撑架底座为焊接件,锥头升降由油缸完成。
托辊旋转由电机通过齿形链条传动。
锥头带制动器,防止由于故障停车时锥头倒转产生散卷。
可根据不同的钢卷调整制动力。
锥头带圆形护盘,防止塔形钢卷损伤设备。
护盘为耐磨材料。
活动支撑架移动方式:
液压油缸,采用特殊液压回路,浮动对中。
锥头的升降由液压油缸驱动,带单向阀自锁回路,保证工作时不会产生钢卷的掉落。
锥头形式:
斜锥型
最大承重:
30吨
活动支撑架开合范围:
650mm~1500mm(适应板宽)
活动支撑架升降范围:
φ1200~φ2200mm(适应钢卷外径)
锥头升降油缸:
φ180mm×800mm两件
锥头移动油缸:
φ120mm×700mm两件
托辊旋转电机:
AC电机11KW
托辊宽度:
500mm
托辊直径:
Φ330mm
托辊材质:
42CrMo
辊面硬度:
HRC48~52
2.6.2拆头机
用途:
配合上卷车托辊旋转、开卷机铲开钢卷头部,并将头部反弯
位置:
开卷机后,夹送轿平前
技术参数及结构:
本设备用于配合开卷机把带钢卷打开,对带钢卷的头部进行反弯,保证能顺利进入下道工序。
由铲刀、靠辊、导辊及支架等组成。
铲刀摆动由液压油缸驱动。
靠辊、导辊采用42CrMo优质合金钢制造。
铲刀采用高锰钢制造,支架为焊接件。
依靠铲头摆动和伸缩,可以完成对钢卷带头和帯尾的矫直功能。
矫直力量大,效果好。
铲刀收缩回位形成防板尾撞击装置,能够防止在帯尾钩形回弹时损伤设备。
主要技术参数:
适用钢板宽度:
650mm~1500mm
适用钢板厚度:
5~18mm
适用钢板材质:
Max.Q345B
铲刀摆动油缸:
φ150mm
直头方式:
液压
铲头硬度:
HRC58-62
直头支撑辊材质:
42CrMo
支撑辊辊径:
Φ220mm
2.6.3夹送矫平机
夹送矫平机由夹送辊装置和矫平辊装置组成。
主要用于把开卷机和铲头打开的带钢矫平后继续向下一道工序送进。
主牌坊采用了焊接式箱型结构,具有良好的刚性。
夹送辊装置
用途:
牵引钢板,送入矫平机。
本设备是带钢进入递送机前的动力源所在,在夹送辊的牵引下,带钢渐次通过矫平,导向辊,切割对焊等设备,最后到达递送机前。
位置:
拆头机后,矫平机前
技术参数及结构:
由夹送辊装配、机架及传动装置组成。
夹送上辊由液压油缸驱动控制上下动作。
机架采用焊接箱式结构件。
压下同步采用同步齿轮齿条机构。
传动采用交流电机减速机。
带离合器系统。
适应钢板宽度:
650~1500mm
适应钢板厚度:
5~18mm
夹送辊直径:
φ250mm
夹送轿平速度:
6m/min
夹送辊材质:
42CrMo
辊面硬度:
HRC52-55
夹送压下油缸:
φ180mm
夹送辊长度:
1550mm(有效宽度)
驱动电机功率:
AC30KW(与矫平共用)
矫平辊装置
用途:
矫平钢板。
位置:
夹送辊后,
技术参数及结构:
由矫平辊、机架、传动系统组成。
机架采用焊接件。
七辊主动/被动矫平。
上四下三,下辊固定,上辊由电动控制升降。
矫平传动采用直流调速系统,可实现全程主动矫平。
带离合器,必要时可以脱开实现全程被动矫平,节省能源。
上辊可摆动微调,实现上辊的开张度,保证了矫平效果。
矫平辊直径:
φ250mm
矫平辊材质:
60CrMoV优质冷轧轧辊钢
适应板宽:
650mm~1550mm
适应板厚:
Max18mm
矫平辊布置形式:
上四下三
传动输出方式:
硬齿面减速机万向轴输出
齿轮材质:
低速齿轮:
42CrMo表面淬火
高速齿轮:
20CrMnTi渗碳淬火
齿轮箱润滑方式:
内部强制循环稀油冷却
矫平辊压下方式:
AC电机驱动蜗轮丝杆压下
压下电机功率:
AC7.5KW
2.6.4电动立辊
用途:
定位钢板对准机组中心线
位置:
夹送矫平机后1套,切割对焊后1套,递送机前1套,铣边机中间1套
技术参数:
由左右立辊、电机减速机、传动丝杠和底座组成。
立辊对中采用AC电机驱动丝杆丝母。
立辊底座采用了焊接箱式结构,刚性好。
左右立辊各由一台AC电机驱动,可分别单独调整。
立辊座采用了U形卡入式结构,更滑丝母时只需从上吊起即可更换,方便快捷。
立辊调整带位移刻度,可根据不同规格的带钢选择调整位置。
立辊调整范围:
550~1550mm
立辊材质:
GCr15
立辊直径:
Φ200mm
传动丝杠直径:
Tr60mm
立辊表面硬度:
HRC52-58
调整电机功率:
2.2KW
2.6.5剪切对焊装置
用途:
切齐前一卷的板尾,切齐后一卷的板头,对正板头板尾,压紧后自动焊接
位置:
两电动立辊之间
技术参数和结构性能:
由液压剪切装置、车体托辊、板头板尾压紧装置,焊剂垫升降,及车体移动装置组成。
车体是焊接件框架结构,板头、板尾压紧方式采用液压。
焊接时焊剂垫升起靠紧焊缝,保证焊接效果。
焊剂垫升降采用液压。
车体可以沿着生产线方向移动,保证对缝准确无误。
移动装置采用液压驱动。
板头、板尾焊接方式:
采用双丝埋弧焊接,单面焊,双面成型。
焊机电源与内焊共用,自配两个焊机头。
适应钢板宽度:
650~1500mm
适应厚度:
5~18mm
切断方式:
液压剪切
焊接方式:
埋弧半自动焊接。
与内焊共用电源,由一个九挡开关切换。
可配双焊头,提高焊接速度。
小车移动:
液压驱动
小车移动缸径:
Φ125mm
压紧方式:
液压
压紧缸直径:
Φ140mm
压辊压下方式:
液压
压辊压下缸径:
Φ120mm
焊机垫升降方式:
液压
焊机垫升降缸直径:
Φ90mm
2.6.6铣边机
用途:
本设备共有两套。
一套用于铣齐钢板边部,利于对缝,一套用于铣坡口(板厚大于12.7mm),以利于焊接。
两套的结构形式一致,可配置不同的刀盘,实现不同的使用效果。
位置:
位于切割对焊及电动立辊后
技术参数及结构特点:
由导向辊,左右铣削装置,钢板压紧装置,铣削头移动装置,底座及碎屑输送收集装置组成。
铣削头由直流电机减速机通过齿形链传动,直流数字调速。
钢板机械压紧,铣削头整体移动方式为电动丝杆式。
铣削头可调整角度,以形成不同的边缘铣削形状。
铣刀转速可根据不同的材质,厚度等进行调整。
铣刀片为机加刀片,由紧定螺钉固定。
一片刀片可使用八个刀刃,更换方便,使用寿命长。
铣削头具有铣屑导向槽,铣下的钢板碎屑可沿此导向槽进入碎屑输送装置,由碎屑输送装置将其输出线外进行人工收集。
在钢板压紧辊和铣削头之间设有防碎屑飞溅装置,防止碎屑进入压辊和钢板之间,损坏压辊。
适应钢板宽度:
600~1550mm
适应钢板厚度:
5~18mm
铣刀盘直径:
φ600mm
铣削线速度:
140~170m/min
速度根据板宽,板厚,銑深度,自动调节
电机功率:
粗铣边机:
AC45Kw两台
精铣边机:
AC45KW两台
最大切削深度:
粗铣边机:
20mm(单边)
精铣边机:
10mm(单边)
切削后钢板宽度公差:
0~0.5mm
刀盘形式:
I型,Y型,X型
适应生产线速度:
0.5~3m/min
压紧辊:
整体式轴承辊
压紧辊润滑方式:
集中式干油润滑
轴承润滑方式:
集中式干油润滑
铣刀盘设计左右不一样的安装结构,保证在装配时不装错。
在铣边机位置布置悬臂小吊专门用于更换铣刀盘。
2.6.7递送机
用途:
牵引和递送钢板,是整个机组的动力源,用于克服开卷,矫平,切割对焊,成型等所需的摩擦力以及成型阻力。
位置:
在铣边机和立辊后
技术参数及结构性能特点:
由上下递送辊、左右牌坊和上、下辊传动装置组成。
左、右牌坊采