热喷涂技术在炼油工业的应用.docx
《热喷涂技术在炼油工业的应用.docx》由会员分享,可在线阅读,更多相关《热喷涂技术在炼油工业的应用.docx(13页珍藏版)》请在冰豆网上搜索。
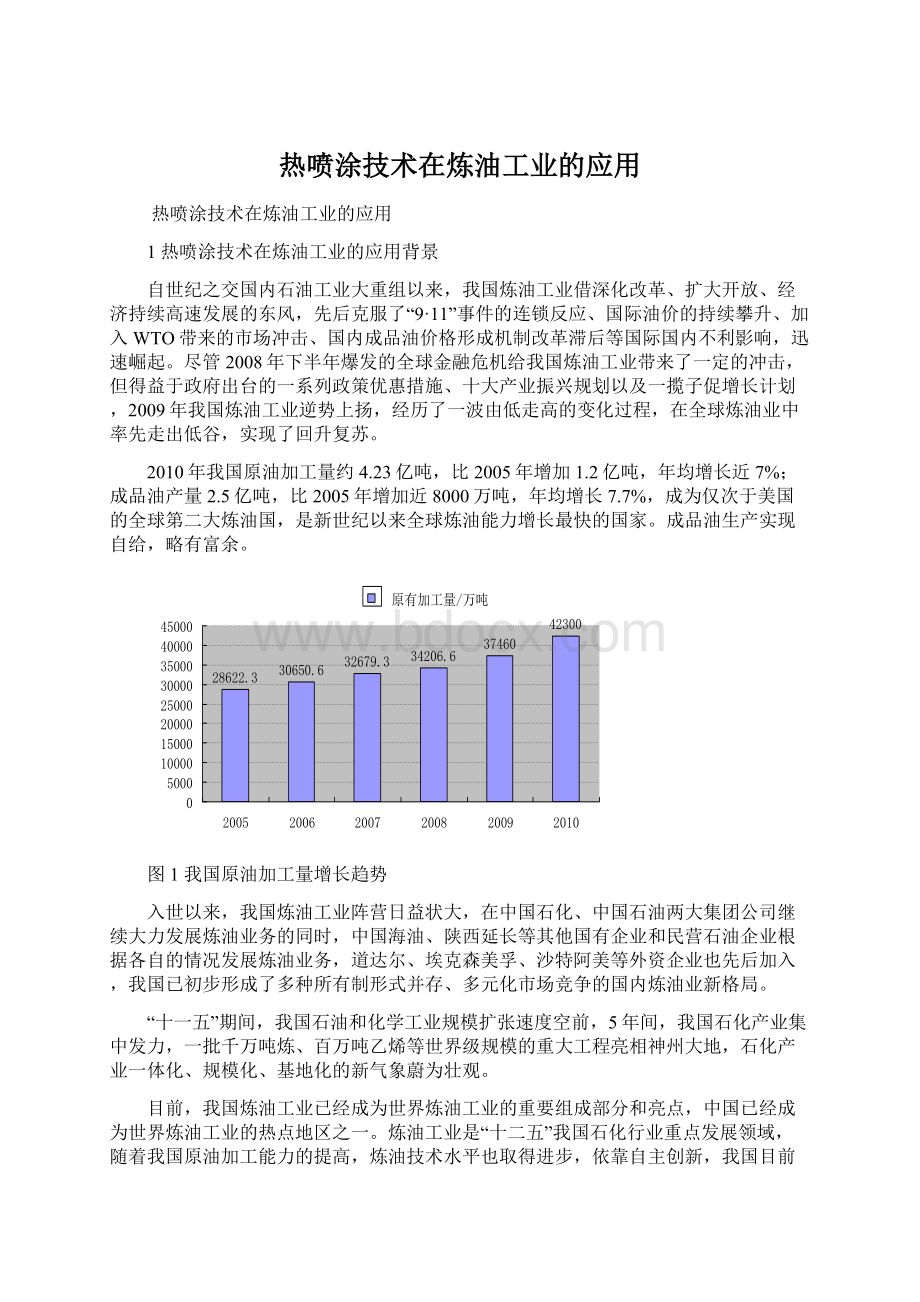
热喷涂技术在炼油工业的应用
热喷涂技术在炼油工业的应用
1热喷涂技术在炼油工业的应用背景
自世纪之交国内石油工业大重组以来,我国炼油工业借深化改革、扩大开放、经济持续高速发展的东风,先后克服了“9·11”事件的连锁反应、国际油价的持续攀升、加入WTO带来的市场冲击、国内成品油价格形成机制改革滞后等国际国内不利影响,迅速崛起。
尽管2008年下半年爆发的全球金融危机给我国炼油工业带来了一定的冲击,但得益于政府出台的一系列政策优惠措施、十大产业振兴规划以及一揽子促增长计划,2009年我国炼油工业逆势上扬,经历了一波由低走高的变化过程,在全球炼油业中率先走出低谷,实现了回升复苏。
2010年我国原油加工量约4.23亿吨,比2005年增加1.2亿吨,年均增长近7%;成品油产量2.5亿吨,比2005年增加近8000万吨,年均增长7.7%,成为仅次于美国的全球第二大炼油国,是新世纪以来全球炼油能力增长最快的国家。
成品油生产实现自给,略有富余。
图1我国原油加工量增长趋势
入世以来,我国炼油工业阵营日益状大,在中国石化、中国石油两大集团公司继续大力发展炼油业务的同时,中国海油、陕西延长等其他国有企业和民营石油企业根据各自的情况发展炼油业务,道达尔、埃克森美孚、沙特阿美等外资企业也先后加入,我国已初步形成了多种所有制形式并存、多元化市场竞争的国内炼油业新格局。
“十一五”期间,我国石油和化学工业规模扩张速度空前,5年间,我国石化产业集中发力,一批千万吨炼、百万吨乙烯等世界级规模的重大工程亮相神州大地,石化产业一体化、规模化、基地化的新气象蔚为壮观。
目前,我国炼油工业已经成为世界炼油工业的重要组成部分和亮点,中国已经成为世界炼油工业的热点地区之一。
炼油工业是“十二五”我国石化行业重点发展领域,随着我国原油加工能力的提高,炼油技术水平也取得进步,依靠自主创新,我国目前已经掌握了建设千万吨级炼厂的能力,一批批重大炼油不断投产。
“十二五”期间国内炼油能力将在现有基础上增加1.35亿吨/年,达到556亿吨/年,但根据炼油实际新增产能测算,2015年炼油能力将高达7.25亿吨左右。
表12010年后投产的炼油大项目
业主单位
建设地点
建设规模
中石油
彭州
1000万吨炼油项目
中石油
重庆
1000万吨炼油项目
中石油
葫芦岛
1000万吨炼油项目
中石油天津大港石化
天津
1500万吨扩建及新建项目
中石油
云南
1000万吨炼油项目
中石化科威特
广州南沙
1500万吨炼油项目
中石油
威海镆邪岛
1000万吨炼油项目
中俄东方石化
天津
1000万吨炼油项目
中石化
曹妃甸
1000万吨炼油项目
中石化天津石化
天津
1250万吨扩建项目
中石化洛阳石化
洛阳
350万吨改扩建
中石化石家庄炼化
石家庄
500万吨改扩建项目
连实德中沙合资
大连双岛湾
1000万吨炼油项目
然而在我国的炼油工业中,由于加工设备中存在着一系列腐蚀、冲蚀以及腐蚀-冲蚀协同作用,常造成设备损伤,严重影响设备的安全运行。
随着加工原油含硫、含氮、酸值及含盐量升高,更加重了原油加工设备的腐蚀。
我国每年炼油工业中因磨损和腐蚀造成直接经济损失就达数亿元,迫切需要提高石油石化工业中开采和加工设备的耐磨性和耐蚀性。
热喷涂技术是表面工程中重要的表面处理技术,它是指在保持零件本体材料原有性能的基础上,通过在其表面制备一层具有优越性能的覆盖层,赋予零件表面耐磨损、耐腐蚀、耐高温、抗氧化、抗疲劳等多种性能。
采用热喷涂技术的最大优势是能够以多种方法制备出优于本体材料性能的表面功能薄层,其厚度仅为结构尺寸的几十分之一,却使零件具有了比本体材料更高的耐磨性、抗腐蚀性和耐高温等性能。
即使采用性能优异的贵重、稀有元素,也不会显著增加成本。
此外,热喷涂技术还能直接针对许多贵重零部件的失效原因,实行局部表面强化、修复、预保护,以达到延长使用寿命或重新恢复使用价值的目的。
热喷涂技术已经被广泛应用于炼油工业中设备的制造和修复。
2热喷涂技术在石油石化行业中炼油厂应用现状
目前热喷涂技术作为表面工程技术的重要部分现,已应用在炼油工业的烟气轮机、压缩机、工业炉、塔器、罐、管道阀类等.等设备的制造和修复当中。
2.1烟气轮机叶片
炼油厂的催化裂化装置,一般采用烟气轮机回收系统。
但由于烟气轮机是在带有固体催化剂微粒及有腐蚀介质的高温烟气流下工作,其动、静叶片等零部件易受冲蚀,其使用寿命只有2-12个月。
而采用等离子喷涂技术在动、静叶片表面喷涂合金粉末,可提高动、静叶片的抗冲蚀和磨损性能,从而延长烟气轮机的使用寿命。
长岭炼油化工厂设备研究所的叶菊英等人,采用采用激光熔覆Ni基高温合金恢复尺寸,等离子喷涂技术在动、静叶片表面喷涂CoCrW高温合金粉末,涂层总厚度150-200μm,涂层应用于济南炼油厂含高粉尘(平均浓度345.3mg/m3)及严重硫腐蚀(硫含量达30~44.5kg/h)的烟机,连续运行8424h后停机检查,叶片完好无损。
对烟机采用涂层防护后,4平均每小时节电5000kW,效益十分显著。
广州石化炼油厂YLII-6000B烟机热喷涂涂层叶片在实际运行18288h后,叶片涂层情况良好。
2MCL-806乙烯裂解压缩机Ⅱ、Ⅲ级进气叶片,由于进气口被异物撞击,造成叶片进气边缘严重损伤。
采用采用激光熔覆Ni基高温合金恢复尺寸,修复装机后,机组正常运行,满足各项性能指标。
图2-1无锡苏威热喷涂科技有限公司烟气轮机叶片超音速火焰喷涂WC-CO涂层
2.2压缩机部件
压缩机叶轮轴主轴长期经受烟气的腐蚀、冲蚀及磨损作用,表面有多孔及疏松的腐蚀层。
天津市亚博炼油化工工程有限公司DA220-73压缩机叶轮轴主轴全长2306mm,轴套外直径为Φ180mm,叶轮最大直径Φ525mm,要求修复后在转速高达4400r·min-1时轴颈全长及动平衡支点跳动允差为0.01mm,叶轮外径跳动允差0.2mm。
因其在高温、高速及重载下工作,涂层与基体必须有良好的冶金结合,发生变形不能用机械方法矫正,喷焊工艺必须严格控制变形。
采用Ni-Cr-Si镍基合金进行喷焊修复和表面强化,经机械加工后达到各项要求,使用效果良好。
常州石油化工厂在石油压缩机活塞杆上的喷焊,其使用寿命延长5倍。
图2-2铁岭永兴热喷涂有限公司压缩机叶轮轴喷焊Ni-Cr-Si镍基合金修复
2.3容器、塔、罐、管道等的防腐
石油石化炼油工业中容器、管道和仓的防腐可采用电弧喷涂铝、锌、不锈钢等涂层防腐或采用火焰喷塑防腐。
中国石化上海石油化工股份有限公司采取对炼厂储罐喷铝层加封闭涂层的防腐措施一年后开罐检查,发现石脑油储罐、酸性水储罐和污油储罐的底部以及酸性水储罐罐壁的防腐层上有很多小鼓泡,是已破裂的小鼓泡里面充满了白色粉末,白色粉末为铝的化合物。
除此之外,其他部位的防腐层完好,光亮如初。
产品油储罐和污油储罐壁喷铝防腐层厚度几乎没有变化,氧化铝钝化膜也没有受到破坏。
铲除已失效的封闭涂层加喷铝层,然后进行喷砂处理,分2次涂装,戮结力强、韧性好和不加导电剂的有机环氧涂料,再分3次涂装相应的致密性好(添加了云母片)、不加导电剂、粘结力和韧性好的有机环氧涂料。
一年之后检查修复的内防腐涂层,发现涂层表面光亮如新。
北京燕山石化工程公司对大连西太平洋石油化工有限公司常减压蒸馏装置1000万t/a扩能改造工程中减压塔改造,减压塔EL20170mm以上部分原喷铝层打掉并重新喷涂锌铝层,原油泵Pol/A引油装置一次开车成功,减压塔处理量和各抽出口流量、馏分达到设计要求。
美国路易斯安娜炼油厂高76.2m的点火架,1951年喷涂0.25mm厚的锌涂层,在石油化工区的腐蚀气氛下,涂层至今完好无损。
杜邦、联合化工、壳牌等公司在反应发生器内壁已大量使用线材喷涂不锈钢、司太立合金、钼和钛合金。
采用等离子喷涂、超音速火焰喷涂、电弧喷涂均可解决油田用各种锅炉管道的腐蚀和冲蚀问题,但由于成本、工艺等因素限制了等离子喷涂和超音速火焰喷涂的应用。
美国采用电弧喷涂45CT线材(43%Cr,0.1%Fe,4%Ti,其余为Ni),喷涂部位包括下部炉区的熔体底部区域、沸腾器过渡区、过热器管、端部拱形部分和沸腾器管。
最初一年的检查表明,这种涂层不剥落、不老化。
26个月后对涂层进行检查,均未发生剥落,根据目前实际应用结果,这种涂层可保证锅炉管道在7-10年内安全运行。
可见,采用电弧喷涂涂层是解决锅炉管道腐蚀和冲蚀问题的有效方法。
大型石油化工装置,特别是高分子塑料原料的储存料仓,均采用不锈钢或铝合金制造,以防对高分子原材料的污染。
大庆石油化工总厂三期工程引进的ABS装置,一改过去连同料仓引进的做法,而是采用在碳钢件表面热喷涂铝的方法制造ABS粉料料仓,既保证了ABS粉料料仓的质量,又节省投资46.4%。
如果用不锈钢材料制造ABS粉料料仓,总价约为875万元,而采用碳钢件热喷涂铝技术后其总价约为469万元,节约资金406万元。
存放油田三次采油所用聚合物的容器,也可采用热喷涂铝或不锈钢的方法,防止对聚合物的污染。
2.4油浆泵
油浆泵是石油化工催化裂化装置系统中一个关键设备,负责油浆输送及排放,工况条件恶劣。
油浆中催化剂浓度高达10mg/L,正常工作温度365—375℃,有时达390℃,工作压力10MPa,转速3000r/min,油浆中含有1%以下的S及其他有害杂质。
由工况分析看出,油浆泵上作时受到流体冲蚀与低温热腐蚀的交互作用,油浆中的S与其他杂质(V、K、Na等)对流通道内的静、动零件产生低温热腐蚀,其生成的疏松腐蚀产物被含有催化剂颗粒(一般为很硬的硅酸铝)的油浆冲蚀掉,如此循环往复,使有关零部件逐渐变薄,输出效率不断下降,最终导致油浆泵失效。
目前该类国产油浆泵一般工作寿命都不长,短的仅几百小时,长的约为3000h左右,不足一个周期,严重影响整个催化裂化装置系统的正常运转。
现在一般采用增加备用泵的办法来解决,但这样不仅给维修造成许多困难,而且给生产造成重大经济损失。
采用等离子喷涂NiCr-CrC防护涂层可以提高其冲蚀抗力及耐蚀性能,延长油浆泵使用寿命。
1996年8月,广州石油化工总厂采用等离子喷涂工艺在催化裂化装置用250PY100型油浆泵(P-309/l))上喷涂NiCr-CrC防护涂层(表2-1),1997年5月此泵投人生产运行,经过3710h实际使用后,进行现场分检.对此泵运行情况十分满意。
对喷涂零件的解体检查,叶轮档套、叶轮含叶轮密封环、泵体含泵体密封环均完好无损,无冲蚀现象,泵盖含泵体密封环中泵体密封环完好,仅泵盖靠密封环侧导流翼有麻点冲蚀现象,该台油浆泵仍在继续使用中。
作为对比,工厂在同一班组完全相同的工况下安排另一台无喷徐层的同型号油浆泵,在运行285Oh后泵体和泵盖的导流翼全部冲蚀掉.叶轮密封环严重冲蚀,几近报废。
为此,该厂于1998年l月至又采用该涂层先后喷涂了4台油浆泵(共5台),为无涂层油浆泵寿命的2-3倍。
表2-1250PY100油浆泵喷涂零件一览表
序号
名称
数量/件
材料
喷涂部位
1
叶轮
1
ZG1Cr13
除轴孔外所有表面
2
叶轮密封环
2
40Cr
工作面
3
泵体密封环
2
40Cr
工作面
4
轴套
2
40Cr
除轴孔外所有表面
5
底套
2
40Cr
6
端封轴套
2
40Cr
7
泵体
1
ZG1Cr13
内滚道易损部位
8
泵盖
1
ZG1Cr13
内滚道易损部位
天津市亚博炼油化工工程有限公司对250PY100油浆泵受损的部位(气蚀冲蚀沟深达3mm)用Ni-Cr-Si合金进行表面喷焊修复,2000年5月修复使用,取得良好效果。
中国石油兰州石化公司机械厂在油浆泵受损的部位喷焊Ni6O硬质合金,达到效果,目前该厂制造的油浆泵全部应用了此项技术。
2.5阀类
2.5.1滑阀
滑阀是催化裂化装置的重要部件,其工作参数为:
质量流量1209600kg/h,流体密度560kg/m3,入口压力284kPa,压差62kPa,内件工作温度为774℃。
滑阀出现故障的主要原因是阀件的严重磨损。
在催化裂化装置的反应-再生系统中,待生滑阀的介质为待生催化剂与重馏分油气,这时的催化剂是待生催化剂,表面附有焦炭。
这种附有焦炭的待生催化剂进入再生器后,在沸腾状态下将附在催化剂表面的焦炭烧掉,使催化剂恢复活性,再经淹流斗、管道和再生单动滑阀进入反应器下部,再次参加催化裂化反应。
在这个过程中待生与再生单动滑阀都要经受携带催化剂粒子的高温流体的冲刷腐蚀、磨粒磨损与热腐蚀作用,其中再生滑阀经受的温度达700℃。
根据计算,流过滑阀的催化剂粒子的流速可达6.6m/s,发生冲刷腐蚀磨损的临界速度为2.7m/s。
显然在阀的工作状态,阀体部件经受着严重的冲刷腐蚀磨损。
此外还应考虑到有重馏分油气的高温腐蚀与高温氧化作用。
基于上述工况分析并结合TAPCOinternational公司的有关技术文件,天津市亚博炼油化工工程有限公司在2000年5月对炼油装置区已受到严重腐蚀磨损的待生与再生滑阀的表面用Co-Cr-W系钴基合金进行热喷涂修复和表面强化,修复后使用直到2004年。
2.5.2阀杆
催化裂化装置中的再生阀和待生阀的阀杆表面一般采用渗氮热处理,虽然表面硬度提高不少(≥HRC60),但是仍具有局限性,往往不能满足高速、重载、高温和腐蚀介质的严重腐蚀等条件下的要求,特别是高温吹扫蒸汽的吹扫,对阀杆表面而言无疑提出了更高的要求。
阀杆的寿命严重制约了产品的生产和发展,经过生产中的多次探索和实验,采用镍基合金粉末加碳化钨粉末,运用表面喷焊新工艺替代表面氮化热处理工艺,对阀杆表面实施喷焊新工艺,提高了阀杆寿命,满足了生产和装置的要求。
以双动滑阀阀杆为例,此阀安装在催化裂化装置中的添料涵内,涵内有高温、高速的催化剂颗粒吹扫阀杆表面,阀杆的表面磨损、腐蚀和冲刷十分严重。
如抚顺公司石油二厂、独山子炼油厂和茂名石化公司炼油厂,就先后出现过阀杆被冲蚀断裂现象,造成了经济损失。
表1列出了炼油催化剂的质量分数。
表2-2 炼油催化剂成份含量指标
催化剂
质量分数/%
典型质量分数/%
Al2O3
≥28
35
Na2O
≤0.35
0.32
Fe2O3
≤0.50
0.30
SO4-2
≤2.5
1.8
表2-3 阀杆接触部位催化剂速度和密度
名 称
线速度v/(m·s-1)
密度ρ/(kg·m-1)
再生塞阀上阀杆
6
625
待生塞阀
11
47.9
单动滑阀阀杆
3-4
500-600
双动滑阀阀杆
100
4
从表1和表2可以看出催化裂化装置中阀杆表面的工况条件十分恶劣,介质比较复杂,阀杆要克服Fe2O3、Al2O3和SO4-2等多种因素的腐蚀,同时阀杆还要克服催化剂颗粒以100m/s线速度的冲刷。
要使装置正常运行,提高阀杆的使用寿命是非常重要的。
选择镍基合金粉末加碳化钨粉末实施氧-乙炔火焰喷焊工艺,零件基材为OCr14Ni14W2Mo(与实际零件材料相同),要提高其表面喷焊层硬度、耐磨和耐腐蚀等性能,应该选熔点低于基体金属,合金与基体结合强度高的镍基自熔性合金粉末。
同时要求在粉末中加入硼、硅元素,使得能自行脱氧还原造渣,形成牢固的焊层。
硼的作用是弥散强化,硼除极少数溶于镍的奥氏体中外,大部分以Ni3B等金属间化合物的形式弥散分布于合金中。
再加入适量的铬,则生成Cr2B、CrB等硬质颗粒,运用表面喷焊新工艺替代表面氮化热处理工艺,解决了表面加工技术,工效提高2倍以上,提高阀杆使用寿命1-2倍,经济效益显著,经过安装在松源炼油厂实践考核效果良好。
兰州炼油化工机械厂Φ1100mm/Φ60Omm电液待生塞阀表面喷焊镍基硬质合金以起到耐冲刷的作用,取得了较好的社会效益及经济效益。
2.5.3耐环烷酸腐蚀阀门
原油的环烷酸在低温时腐蚀性不强,在180-400℃时腐蚀随温度的升高而增加。
在较高温度下,环烷酸不仅与铁直接作用产生腐蚀,还能与腐蚀产物硫化亚铁反应,生成可溶于油的环烷酸铁。
当环烷酸与腐蚀产物反应时,不但破坏了具有一定保护作用的硫化亚铁膜,同时游离出的硫化氢又进一步腐蚀金属。
因此,在阀门密封面上,凡是保护膜被破坏的地方,就会暴露出新的金属表面,而使腐蚀继续进行。
锦西炼油化工总厂自加工辽河原油后,由于原油环烷酸值逐年增加,设备腐蚀情况愈来愈严重。
虽然采取了防护措施,解决了一些关键装置的腐蚀问题,但阀门密封面的腐蚀问题仍较突出。
阀门密封面受环烷酸腐蚀后,关闭不严,影响装置长期正常运行。
1995年3月-1996年3月,仅酚精练2套装置因设备和工艺管线的腐蚀泄漏就停车19次,给生产造成了重大损失。
常用阀门密封面堆焊材料的耐腐蚀性生产运行情况表明,Z41Y及Z41H不同口径的阀门密封面耐环烷酸腐蚀性能均不理想。
加工含环烷酸原油时,酸腐蚀主要发生在常减压蒸馏装置高温部位的阀门密封面,减粘装置和蜡油溶剂装置的阀门密封面酸腐蚀也很严重。
系统的低温部位是指塔顶上部和塔顶冷凝冷却系统。
低温腐蚀与原油中所含的氯盐和硫化物有关。
有水存在时,氯盐在一定温度下水解成HCl,原油在加工过程中硫化物分解生成H2S。
低温部位防止HCl-H2S-H2O对阀门密封面的腐蚀可以由选用合适的堆焊材料解决,也可以采用工艺措施缓解。
原油的酸性越高,对阀门密封面腐蚀越重,其特性表现为均匀腐蚀。
低硫高酸原油的腐蚀性比高硫高酸原油腐蚀性强,高流速介质也使腐蚀加剧。
原油中所含的碱性水会形成环烷酸钠,加速阀门密封面的腐蚀。
锦西炼油化工总厂采用SF-5T堆焊铁基Cr-Mn-B加Mo、W和V等强化元素,代替D547Mo和HS111,从1993-1998年5月,使用SF-5T焊条堆焊Z41H、Z41Y-16I、Z41Y-20P及Z41Y-16R等系列阀门密封面共600余台,阀门运行1年,仍可继续使用。
SF-5T堆焊合金耐冲蚀,耐氧化,热态组织稳定,堆焊工艺性好,价格较低,其耐环烷酸腐蚀的特点,使之成为辽河、胜利等油田原油加工装置首选的阀门密封面堆焊材料。
中国石油锦州石化分公司研制了2种堆焊合金,定名为“抗烷1号和抗烷3号”,耐蚀性试验性能良好。
经考虑闸板与阀座密封副必需的硬度差要求后,选取“抗烷1号”和“抗烷3号”分别作为阀座和闸板密封面的堆焊材料。
在减压蜡油输送管线内受环烷酸腐蚀最剧烈的减三线泵出口阀下端处挂片对比性能试验,油品温度为270-330℃,酸值为3-4mgKOH/g,时间为180天,与其同时进行挂片对比试验的还有司特立合金试件。
挂片对比性能试验的结果是“抗烷1号”和“抗烷3号”的耐蚀性能良好,优于司特立合金。
该公司2套常减压装置内的减二线泵出入口处安装研制的高温耐蚀闸阀作工业应用试验。
闸阀口径为DN200mm和DN250mm,压力等级为PN40MPa。
阀门在装置中使用一个生产周期(2年)后,于1999年4月装置停产检修期间解体,对闸板和阀座进行清洗,其外表光亮,无点蚀,但有减薄现象。
经内部清理后组装,检验合格,可继续使用。
2.5.4耐腐蚀耐磨球阀
对于工作在温度达540℃,压力达140MPa的含有腐蚀性砂浆的管道中的金属座球阀,应用超音速火焰喷涂WC-Co涂层、Cr2C3-NiCr涂层、Fe-Cr-Ni-Mo涂层或WC-Ni涂层,可大幅度改善球阀的耐腐蚀和耐冲蚀性能,提高使用可靠性和寿命。
图2-3无锡苏威热喷涂科技有限公司硬面球阀表面喷涂硬质合金碳钨
2.6工业炉
2.6.1 加热炉
加热炉中燃烧器的工作温度一般为850℃以下,炉管的温度也是十分高的,制氢炉的炉管温度高达1000℃,并承受一定压力同时接触腐蚀性介质,工作环境十分恶劣;乙烯裂解炉炉管的工作环境恶劣,炉膛烟气温度在1000℃左右,炉管外壁温度1050-1100℃,管内介质温度900℃左右,炉管管壁处在管内烃类渗碳,管内外氧化硫化及高温环境下,同时又承受内压、自重、温差及开停车所引起的疲劳、热冲击等复杂的应力作用。
加热炉的一些炉管配件,如翅片管与钉头管的高温部位操作温度为500-700℃(低温部位为500℃以下)。
这些环境应用热障涂层,提高高温腐蚀性和热效率。
2.6.2 造气炉
大庆石油化工总厂二厂丁辛醇车间的造气炉操作温度1355℃。
其迎火面要求有耐高温层,背衬要求有保温作用的保温层。
2.6.3 加氢反应器
热壁加氢反应器的工作温度较高,为320-420℃,大量的烃类分子的裂解,氧化物转化为氨,硫化物转化为硫化氢的过程使加氢反应器处在苛刻的条件下运行。
因此反应器材料即要求能抵抗高温,又要抵抗高温环境中的氢蚀能力和抵抗氨、硫化氢及其化合物的高温腐蚀能力。
若在反应器内壁喷涂一层陶瓷热障涂层材料,不用在内壁堆焊奥氏体不锈钢耐蚀层,不仅可节省反应器用料、缩短制造周期,而且避免了对材料回火脆化的影响。
乌鲁木齐石油化工总厂炼油厂在立式加热炉上应用全陶瓷纤维衬里,炉墙外壁温度:
原加热炉炉墙面无破损处壁温为60℃左右,而破损部位高达80-90℃,墙面油漆被烤脱落,热损失较大。
用全陶瓷衬里后,炉壁温设计值为38.5℃,实际壁温与设计值相差不大,炉墙热损失由原4.2%降至2.5%,仅此一项每年就可节能1.4×109kJ,相当于节约标准燃油33.44t。
炉体重量大幅度减轻,原加热炉炉墙总重315.4t,其中耐火砖等非金属材料重284.4t,加热炉总重542.9t。
改用全陶瓷纤维衬里后,炉墙重70t,只有原炉墙重的1/6。
由于炉体重量减轻,故加热炉的抗震能力有所增强。
经济效益:
原挂砖结构墙体不仅钢材用量大,异型砖种类繁多,且结构复杂,施工难度大,按当时价格计算约为60万元,改用全陶纤衬里后,炉墙衬里结构简单,施工方便,炉墙厚度也较薄,材料耗费少,实际造价仅40万元。
热效率比较:
原加热炉燃料单耗为37.5kg/t,热效率为77.56%。
改用全陶纤衬里后,燃料单耗降至26.5kg/t,热效率提高到88.9%。
仅燃料每年节约151.8万元。
国内热障涂层技术刚刚起步,随着技术的不断发展,将会出现多种优质、耐火、隔热和节能的陶瓷材料,并将逐步取代一些老式的隔热结构。
2.7大型油缸活塞表面
液压油缸的柱塞长时间做往复运动,造成柱塞表面出现磨损使柱塞和密封圈的接触不均匀,如有外部的小颗粒粘到柱塞上,随着柱塞的运动带入密封内,造成柱塞表面拉伤。
化工设备常常要和酸、碱、盐等强腐蚀性介质接触;化工生产过程常常在高温、高压、高流速等强化条件下进行。
这些条件又强化了腐蚀作用,金属表面因受介质腐蚀产生溃疡、深洼、斑点等局部缺陷而损坏。
液压油中存在高硬质点,采用火焰喷涂镍包铝或铝包镍,这两种粉末完全可以满足柱塞表面的使用要求。
利用该方法历时4h,成功修复了修复了美国进口Φ300油缸柱塞表面产生的500mm×8mm×0.8mm两道轴向拉伤。
修复后使用效果良好,不但避免了大量漏油(每周漏油180kg左右)损失,而且节省了每班清理油污的人力。
该修复过程仅用4小时,是在停机维护情况下完成的,与拆下修复至少要一周时间相比,能减少对生产的影响。
而且修复费用少,此次修复总成本约500元左右。
表2-3热喷涂技术在炼油工业的应用简况表
产品
工况
喷涂工艺
涂层体系
性能与用途
相关企业
烟气轮机叶片
烟气的腐蚀、冲蚀及磨损
激光熔覆+
等离子喷涂
Ni基高温合金+CoCrW高温合金粉
恢复尺寸,防腐蚀,提高耐磨性能
长岭炼油化工厂设备研究所
济南炼油厂
广州石化炼油厂
无锡苏威热喷涂科技有限公司
压缩机叶轮轴/
活塞杆
烟气的腐蚀、冲蚀及磨损
喷焊
Ni-Cr-Si镍基合金
恢复尺寸和表面强化
天津亚博炼油化工工程有限公司
常州石油化工厂
铁岭永兴热