延迟焦化基础能耗计算.docx
《延迟焦化基础能耗计算.docx》由会员分享,可在线阅读,更多相关《延迟焦化基础能耗计算.docx(17页珍藏版)》请在冰豆网上搜索。
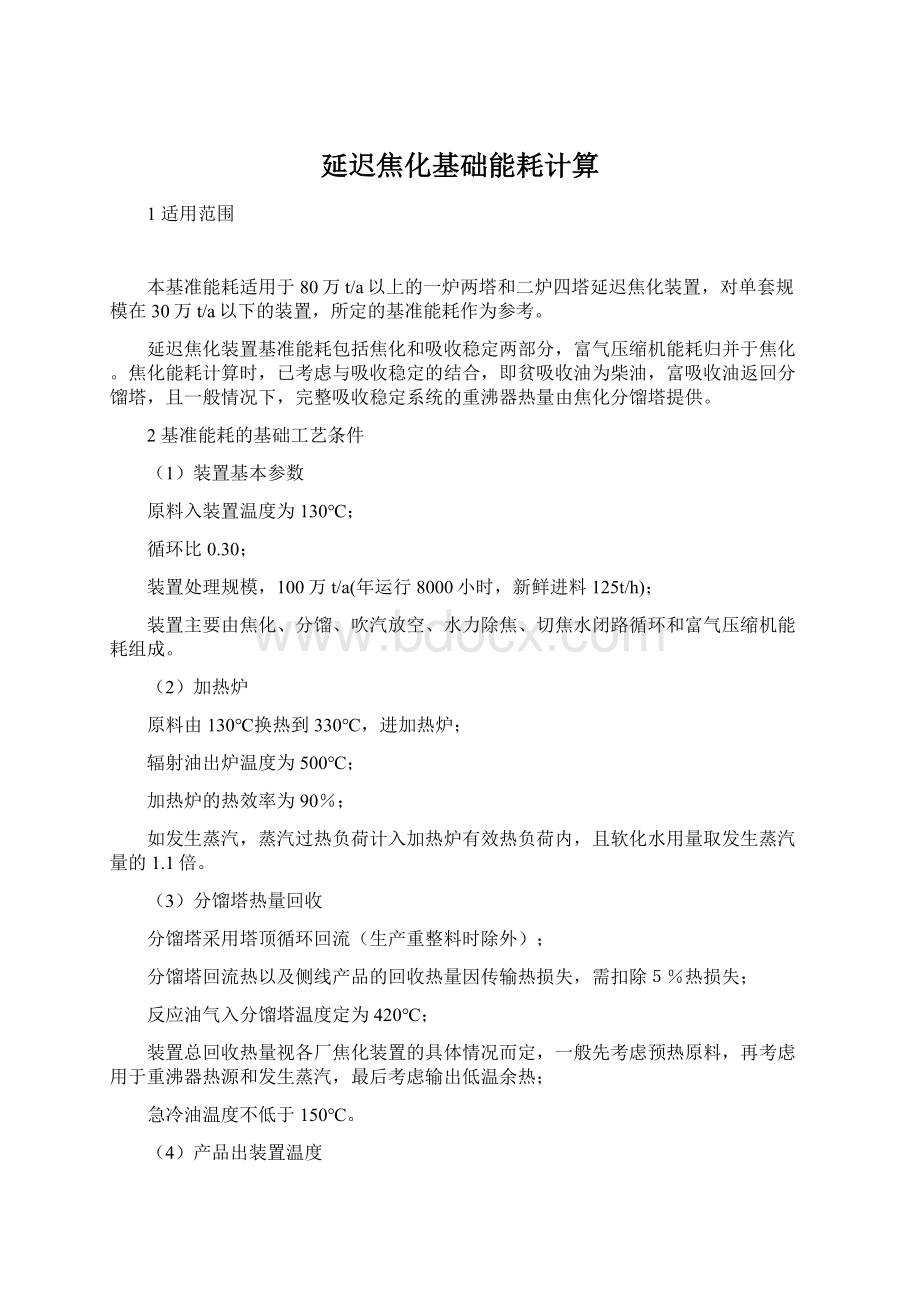
延迟焦化基础能耗计算
1适用范围
本基准能耗适用于80万t/a以上的一炉两塔和二炉四塔延迟焦化装置,对单套规模在30万t/a以下的装置,所定的基准能耗作为参考。
延迟焦化装置基准能耗包括焦化和吸收稳定两部分,富气压缩机能耗归并于焦化。
焦化能耗计算时,已考虑与吸收稳定的结合,即贫吸收油为柴油,富吸收油返回分馏塔,且一般情况下,完整吸收稳定系统的重沸器热量由焦化分馏塔提供。
2基准能耗的基础工艺条件
(1)装置基本参数
原料入装置温度为130℃;
循环比0.30;
装置处理规模,100万t/a(年运行8000小时,新鲜进料125t/h);
装置主要由焦化、分馏、吹汽放空、水力除焦、切焦水闭路循环和富气压缩机能耗组成。
(2)加热炉
原料由130℃换热到330℃,进加热炉;
辐射油出炉温度为500℃;
加热炉的热效率为90%;
如发生蒸汽,蒸汽过热负荷计入加热炉有效热负荷内,且软化水用量取发生蒸汽量的1.1倍。
(3)分馏塔热量回收
分馏塔采用塔顶循环回流(生产重整料时除外);
分馏塔回流热以及侧线产品的回收热量因传输热损失,需扣除5%热损失;
反应油气入分馏塔温度定为420℃;
装置总回收热量视各厂焦化装置的具体情况而定,一般先考虑预热原料,再考虑用于重沸器热源和发生蒸汽,最后考虑输出低温余热;
急冷油温度不低于150℃。
(4)产品出装置温度
富气40℃;汽油40℃;柴油50℃;蜡油90℃;渣油130℃。
(5)装置用汽
注汽量按新鲜进料的1.5m%;
吹汽、吹扫与伴热用汽(1.0MPa)为20kg/t。
(6)装置用电
泵均以电力驱动考虑,不考虑汽泵;
单程焦化的用电为120MJ/t(不包括富气压缩机耗电和吸收稳定系统耗电),不同循环比另加修正项43.1R(R为循环比,单位为MJ/t)。
(7)装置用水
新鲜水用量:
17kg/t新鲜进料;
机泵冷却用循环水;
产品冷却或物流冷却温度在80℃以上,用空冷,电耗已计入装置电耗。
冷却温度在80℃以下使用水冷,水温升10℃。
3正向法基准能耗
3.1物料平衡
根据原料油评价或生产实际确定物料平衡,物料平衡见表1。
表1物料平衡
项目
收率,m%
富气
8.65
汽油
13.41
柴油
28.00
蜡油
18.54
焦炭
29.70
外甩油+损失
1.70
合计
100
3.2加热炉有效热负荷及燃料消耗计算
油品进炉温度330℃;
油品出炉温度500℃;
油品有效热负荷Q1816.4MJ/t;
加热炉热效率0.9;
加热炉燃料用量21.67kg/t;
3.3分馏塔和换热系统计算
分馏塔用Process模拟程序进行优化;换热物流数据分别见表2、表3,换热系统用窄点技术超目标程序优化。
表2热物流数据
物流名称
起始温度℃
终止温度℃
流量t/h
热量kW
塔顶油气
108
40
31.053
3447
顶循
128
88
166.492
4200
柴油回流
228
170
136.245
5554
柴油
170
60
51.000
3448
中段回流
315
245
89.604
4837
轻蜡油
348
80
17.800
3310
重蜡油
376
255
40.180
3874
重蜡油
255
80
22.855
2565
循环油
360
270
115.861
8189
表3冷物流数据
物流名称
起始温度℃
终止温度℃
流量t/h
热量kW
原料油
130
330
125.000
17895
富吸收油
51
120
17.278
732
循环油
270
330
37.500
1823
解吸塔重沸物流
178
205
112.536
3722
稳定塔重沸物流
221
228
154.667
2675
优化后,该换热系统的窄点温差是23.6℃,平均传热温差为41.9℃,冷却负荷12577kW,热物流开始冷却时的平均温度为158.2℃,130℃以下的冷却负荷为10940kW,80℃以下的冷却负荷为2606kW。
冷热综合曲线见图1。
图1换热系统冷热综合曲线
3.4装置新鲜水、循环水、蒸汽、软化水及用量
(1)新鲜水用量17kg/t。
(2)循环水用量
80℃以下冷却负荷消耗循环水为224t/h,接触冷却塔顶消耗循环水折为连续量是11t/h,泵冷却耗循环水40t/h,故循环水耗量为(224+11+40)/125=2.2t/t。
(3)蒸汽用量
炉注汽(3.5MPa) 15kg/t;
吹汽、吹扫与伴热用汽(1.0MPa) 20kg/t;
合计35kg/t。
3.5富气压缩机能耗
(1)富气压缩机由中压蒸汽背压机驱动
富气压缩机能耗为8.3EL/Q,MJ/t;
式中:
EL—富气压缩机耗电,kW;
Q—装置实际处理量,t/h。
(2)富气压缩机由1.0MPa凝汽机驱动
富气压缩机能耗22.3EL/Q+20,MJ/t;
(3)富气压缩机耗电估计
EL=1.26(Yg+YL)Q
式中:
Yg—干气收率,m%;
YL—液化石油气收率,m%。
3.6装置基准能耗
(1)燃料E1=907.2MJ/t。
(2)蒸汽消耗量35kg/t;
蒸汽能耗E2=0.015×88+0.02*76=2.84×104kcal/t=118.9MJ/t。
(3)循环水能耗E3=2.2×0.1=0.22×104kcal/t=9.21MJ/t。
(4)新鲜水能耗E4=0.017×0.17=0.003×104kcal/t=0.12MJ/t。
(5)用电能耗E5=120+43.1*0.3=132.9MJ/t。
(6)富气压缩机能耗(采用中压背压透平) E6=8.3×1.26(Yg+YL)=90.5MJ/t。
(7)热输出8189kW,计入能耗E7=-235.8MJ/t。
(8)基准能耗Eo=E1+E2+E3+E4+E5+E6+E7=1023.0MJ/t。
4反向法基准能耗
反向法的基准能耗计算公式如下:
EB=
Ei
式中:
E1~E10分别见下述。
表4延迟焦化装置基准能耗计算所需数据
序号
项目
符 号
单位
1
原料
新鲜进料量
Q
t/h
新鲜进料分子量
MC
2
产品收率
干气
YF
m%
液化气
YL
m%
汽油
YG
m%
柴油
YLO
m%
蜡油
YCGO
m%
焦炭
YCK
m%
3
循环比
R
加热炉效率
η
(小数)
注汽率
Rw
m%
成套规模(一炉两塔)
S
万t/a
富气压缩机采用背压透平
有完整的吸收稳定系统
低温余热未回收
4.1化学焓差能耗E1(MJ/t)
E1=24158
MC—原料平均分子量,若有该数据按实际数据输入,若无该数据按下式估算,
MC=42.97exp(2.10×10-4T-7.79D+2.09×10-3TD)T1.26D4.98
Mp—产品平均分子量;
Mp=(YCGO+YLO+YG+YL+YF)/(2.86×10-3YCGO+5×10-3YLO+0.01YG+0.02YL
+5.56×10-2YF)
式中:
YCGO—蜡油产率,m%;
YLO—柴油产率,m%;
YG—汽油产率,m%;
YL—液化气产率,m%;
YF—干气产率,m%。
T=T50,即原料油恩氏蒸馏50%点温度,K;
D—原料油比重,d15.615.6。
4.2加热炉散热与排烟能耗E2(MJ/t)
E2=628(1+R)(1/η-1)
式中:
R—循环比;
η—加热炉效率(对单面辐射炉取0.87,对双面辐射炉取0.90)。
4.3装置电耗E3(MJ/t)
E3=120+43.1R
4.4蒸汽能耗E4(MJ/t)
E4=63.6+6.3RW
4.5富气压缩机能耗E5(MJ/t)
(1)富气压缩机由中压蒸汽背压机(背压汽1.0MPa)驱动
E5=8.3EL/Q
式中:
EL—富气压缩机耗电,kW。
一般应使用富气压缩机的耗电估计式的计算功率值,如果实际功率值比计算值小,则使用实测值;
Q—装置实际处理量,t/h。
(2)富气压缩机由1.0MPa凝汽机驱动
E5=22.3EL/Q+20
(3)富气压缩机耗电估计
EL=1.26(YF+YL)Q
4.6工艺利用与回收环节的散热能耗E6(MJ/t)
E6=397S-0..5
式中:
S—装置对应一炉两塔的设计规模,万t/a。
如装置二炉四塔总规模100万t/a,则对应一炉两塔的规模为50万t/a,S等于50。
4.7装置排弃能耗E7(MJ/t)
E7=11.50YF+6.88YL+6.55YG+0.477YLO+0.574YCGO+28.73Rw+2.763YCK-6.7(1+R)+15
式中:
YCK—焦炭产率,m%;
Rw—对新鲜进料的注汽率,m%。
4.8装置排弃能消耗的循环水和新鲜水能耗E8(MJ/t)
E8=9.33
4.9吸收稳定系统能耗E9(MJ/t)
(1)有带重沸器的完整吸收稳定系统E9=230MJ/t;
(2)不带重沸器的简单吸收系统E9=25MJ/t。
4.10装置输出低温余热所降低的能耗E10(MJ/t)
(1)当装置所能输出的低温余热全部利用时:
E10=-(5.95YF+4.22YL+2.83YG+0.79YLO+0.78YCGO+3.06Rw)
(2)当装置低温余热无法利用时:
E10=0
(3)当装置低温余热部分利用时,严格按新修订的《炼油厂能量消耗与评价方法》计算低温余热利用所降低的能耗值,该种情况的能耗降低值不可能超过第一种情况。
5基准能耗的校正
在装置负荷率与设计能力相差较多时,需对计算所得到的基准能耗进行近似校正。
θ=(0.3E2+0.48E3+E4+E6+E8)/EB
EC=(1-θ)EB+θ*EB/L=EB(1-θ+θ/L)
式中:
EC—近似的校正后的能耗,MJ/t;
L—装置负荷率(小数);
θ—焦化装置固定能耗(不包括吸收稳定系统)占总能耗的比例。
6建议的能耗评价指标及应用
即使对同一类装置但各个不同的装置,由于具体的原料、产品、规模等差别很大,应达到的能耗目标是不同的,因此,建议用能耗因数EF并结合装置与本基准能耗设定的条件对比,分析评价各装置的能量利用水平
EF=实际能耗/校正后的基准能耗
EF值愈大,说明装置的实际能耗与基准能耗的差距愈大,能量利用水平愈低,节能潜力愈大,EF值愈接近1,表示能量利用水平愈高。
7生产装置标定数据能耗校核方法
以某厂焦化装置的标定数据为例,进行计算,物料平衡见表5。
装置标定循环比γ=0.487,注水量占新鲜进料百分比为4.23%。
表5某焦化装置标定原始数据
项目
入方
出方
收率
减压渣油
kg/h
t/d
kg/h
t/d
%
富气
91767
2202.4
5800
139.20
6.32
汽油
12492
229.80
13.61
柴油
26458
634.99
28.83
冷蜡油
5777
138.65
6.30
热蜡油
16348
392.35
17.81
焦炭
23970
575.28
26.12
外甩油+损失
922
22.13
1.01
合计
91767
2202.40
100.00
7.1燃料用量计算(见表6)
表6燃料用量计算
项目
炉301
炉302
合计
对流油品入炉温度,℃
255
255
对流油品出炉温度,℃
334
330
对流油品进、出口焓差,kJ/kg
226.2
214.2
对流油品有效热负荷MJ/t
111.56
108.56
Q1=220.1
注水入炉温度,℃
175
100
注水量,kg/t
20.92
21.41
注水热负荷,MJ/t
57.2
65.25
Q2=122.5
过热蒸汽入炉温度,℃
190
190
过热蒸汽出炉温度℃
312
275
过热蒸汽流量kg/t
59.93
80.9
过热蒸汽热负荷MJ/t
16.82
16.21
Q3=33.0
辐射油品入炉温度℃
391
391
辐射油品出炉温度℃
495
495
辐射油品流量kg/t
728.9
758.2
辐射油品进、出口焓差kJ/kg
414.1
414.1
辐射油品有效热负荷MJ/t
301.8
313.97
Q4=615.8
加热炉总热负荷MJ/t
487.4
504.0
Q=991.4
炉实际热效率%
89.35
89.12
理论燃料量kg/t
13.03
13.51
热空气入炉热量MJ/t
28.12
-
热空气入炉热量折合燃料量kg/t
0.6
-
加热炉燃料总量kg/t
25.94
7.2核算装置热流提供的热量
分馏塔回流取热情况见表7。
总回流取热量减去冷回流负荷75.1MJ/t,得装置回流提供的总热量为414.6MJ/t。
表7分馏塔回流取热情况
项目
返塔温度℃
出塔温度℃
流量kg/t
取热量MJ/t
取热比例%
塔顶循环
47
174
539.1
167.6
34.2
十六层回流
49
240
160.8
77.8
15.9
十三层回流
198
240
263.0
31.25
6.4
冷回流
39
127
143.2
75.1
15.3
中段
255
326
646.9
137.9
28.2
合计
489.7
侧线馏出油热量情况见表8。
表8侧线馏出油回收热量情况
项目
流量kg/t
初温℃
终温℃
热量MJ/t
柴油
288.3
240
49
136.27
蜡油
62.95
357
198
28.81
合计
165.08
以上两项合计热流提供的热量为579.7MJ/t。
7.3核算装置回收的热量
发生蒸汽的热量
装置发生1.2MPa蒸汽12.924t/h,折合140.8kg/t,
则需要热量=140.8×(666.8-175)=6.9245×104kcal/t=289.9MJ/t。
预热除氧水热量
161.76×(175-100)=1.2132×104kcal/t=50.8MJ/t。
预热低温电站软化水热量(从46℃加热至130℃)为223.6MJ/t。
以上3项总计回收热量为564.3MJ/t。
7.4装置单耗
(1)蒸汽耗量
焦炭塔吹汽、试压、伴热、吹扫用汽3.56t/h,折合38.8kg/t;
焦炭塔汽封为1t/h,折合10.9kg/t;
耗汽总量为4.56t/h,折合49.7kg/t;
剩余蒸汽量为140.8-49.7=91.1kg/t。
(2)软化水耗量
机泵用端面冷却水为4.164t/h,折合45.38kg/t。
(3)循环水耗量
循环水耗量为91.77t/h,折合1000kg/t。
(4)新鲜水耗量
机泵冷却及生活用为10.83t/h,折合118.0kg/t。
(5)除氧水耗量
蒸汽发生器耗除氧水为12.924t/h,折合140.8kg/t;
炉注水耗除氧水为3.885t/h,折合42.34kg/t;
冷焦用除氧水为1.067t/h,折合11.63kg/t;
合计为17.876t/h,折合194.8kg/t。
(6)电耗量
电耗量(实测数据)980kW,折合10.68kWh/t。
(7)燃料油耗量
燃料油耗量=25.94kg/t。
7.5计算的装置能耗
蒸汽-0.0911×76=-6.924×104kcal/t=-289.9MJ/t;
循环水1.0×0.1=0.1×104kcal/t=4.187MJ/t;
软化水0.04538×0.25=0.011×104kcal/t=0.461MJ/t;
新鲜水0.118×0.17=0.02×104kcal/t=0.837MJ/t;
除氧水0.1948×9.2=1.792×104kcal/t=75.03MJ/t;
电10.68×0.28=2.99×104kcal/t=125.2MJ/t;
燃料25.94×104kcal/t=1086.1MJ/t;
渣油热进料6.6×104kcal/t=276.3MJ/t;
热蜡油输出-3.057×104kcal/t=-128MJ/t;
低温热输出-2.67×104kcal/t=-111.8MJ/t;
总计24.8×104kcal/t=1038MJ/t。
8反向法基准能耗计算举例
下面用实例说明反向法基准能耗计算方法的使用。
例:
某100万t/a延迟焦化装置数据总结(即反向法需要的数据)见表9:
表9延迟焦化装置基准能耗计算所需数据
序号
项目
单位
数值
1
原料
新鲜进料量
t/h
125
新鲜进料分子量
1000
2
产品收率
干气
m%
6.06
液化气
m%
2.59
汽油
m%
13.41
柴油
m%
28.0
蜡油
m%
18.54
焦炭
m%
29.7
3
循环比
0.3
加热炉效率
%
0.9
注汽率
m%
1.5
成套规模S(一炉两塔)
万t/a
50
富气压缩机采用背压透平
有完整的吸收稳定系统
低温余热未回收
表10延迟焦化装置基准能耗计算结果
序号
计算结果
序号
计算结果
1
E1=227.9
8
E8=9.33
2
E2=90.7
9
E9=230
3
E3=132.9
10
E10=0
4
E4=73.1
5
E5=90.5
EB=1241.3
6
E6=56.1
7
E7=330.8
表10计算结果表明:
该装置的焦化部分基准能耗为1011.3MJ/t(24.15kgEo/t),包括吸收稳定系统时,全装置的基准能耗为1241.3MJ/t(29.64kgEo/t),若80℃以上低温余热全部利用,将降为1115.4MJ/t。
附件 延迟焦化装置基准能耗
编制说明
基准能耗的确定通常有二种方法,一种是正向推算法,即从实物消耗的角度追踪,其优点是直观易懂,缺点是对各种影响因素,难于达到准确的修正。
正因如此,本正向基准能耗方法仅提供了一种思路。
另一种是反向推算法,即从排放于环境的能量进行计算。
对延迟焦化装置来说,反向推算法更简便一些,更易于对比查找差距。
如循环比不同的基准能耗修正,需要考虑5个方面的影响,加热炉燃料耗量变化、机泵耗电的变化、反应热的变化、低温余热的变化、富气压缩机功率的变化,这在反推法中均得到了较好的体现。
但反向推算法的缺点是比较抽象。
1分馏塔和换热系统计算
在反向推算法中,不涉及分馏塔和换热系统的计算。
在正向推算中,对分馏塔采用process流程模拟软件进行模拟优化,在保证产品质量的同时,使分馏塔的过剩热尽量在较高的温度下取出。
根据上述模拟软件计算的物流数据,使用窄点技术的超目标程序对换热系统进行优化。
由于原料的换热终温已经确定为330℃,所以换热系统优化的目标是在满足原料换热的前提下,尽可能输出高温位的热量,即优先提供吸收稳定系统重沸器热量,剩余热量尽可能多产生1.0MPa蒸汽,最后提供低温余热(由60℃加热到100-120℃)。
在正向推算法中,仅向吸收稳定系统提供所需的重沸器热量后,换热系统的窄点温差为23.6℃,平均传热温差为41.9℃,热物流开始冷却时的平均温度为158.2℃,此时说明换热系统本身已达到优化状态,不可能再产生蒸汽而只可能输出低温余热。
2反应热的计算
反应热的计算通常采用分子膨胀法或燃烧热法,由于燃烧热法需要非常准确的物料平衡,实际过程中难于达到,所以对主要为吸热反应的过程常采用分子膨胀法计算反应热。
由于有关文献中,没有查到计算公式中的系数,故采用两个炼油企业的焦炭塔能量平衡后的反应热作为依据,推算出分子膨胀法的系数。
3加热炉散热与排烟能耗
这部分能耗的计算主要涉及到加热炉热负荷的确定。
进料温度换热到330℃后进加热炉加热到500℃,此段温度范围,按纯液相计算的焓差为136kcal/kg,考虑加热炉出口汽化率为20%,则焓差增大到140kcal/kg,再考虑10kcal/kg的反应热后,加热炉油品的总加热焓差为150kcal/kg。
焓差确定以后,就可以根据循环比和加热炉效率推算出加热炉散热与排烟所形成的能耗。
加热炉对流室仅预热空气。
4装置电耗
装置电耗指标不包括富气压缩机和吸收稳定系统,它主要以最新设计的4套焦化装置电耗数据为依据而定,并且仅对装置电耗影响最大的因素--循环比进行了修正。
循环比增大时,带来的电耗主要为:
循环油泵电耗增加、辐射油泵电耗增加、加热炉燃料单耗带来的加热炉风机电耗增加。
5蒸汽能耗
蒸汽能耗不包括富气压缩机和吸收稳定系统,它分为二部分,一是注汽量,为3.5MPa蒸汽,按新鲜进料的1.5m%确定;二是大吹汽、小吹汽、汽封、吹扫与伴热用汽,为1.0MPa蒸汽,按20kg/t计。
在正向法中,这二部分用汽直接形成能耗。
在反向法中,注汽形成的能耗主要已在排弃能中考虑(即分馏塔顶油气的热量),所以应予扣除。
扣除影响后,每吨3.5MPa中压蒸汽形成的能耗为15kg标油。
6富气压缩机能耗
富气压缩机的功率消耗是根据许多设计和统计数据而定,即每吨富气消耗功率90kWh。
一般应使用富气压缩机的耗电估计式的计算功率值,如果实际功率值比计算值小,说明富吸收油未返回分馏塔,这时应使用实测值。
有关计算式中的系数是根据压缩机的驱动形式不同而确定的,其中3.5MPa到1.0MPa的中压背压汽轮机汽耗量按16.5kg/kWh;1.0MPa凝汽机的汽耗量按7.35kg/kWh。
7工艺利用及回收散热能耗
由于反推法中,主要是从排弃能的角度计算能耗,此部分能耗用于推算加热炉燃料消耗中形成的散热能耗。
因此,对于一炉两塔的流程,正常运行时,一个焦炭塔处于除焦状态,而它的排弃能已计入装置排弃能中,故其散热损失不包括在内,当然密闭接触冷却系统的冷却及散热损失也排除在外(它是由焦炭的排弃能转换过来的)。
此部分散热包括的具体内容为: