实践报告.docx
《实践报告.docx》由会员分享,可在线阅读,更多相关《实践报告.docx(15页珍藏版)》请在冰豆网上搜索。
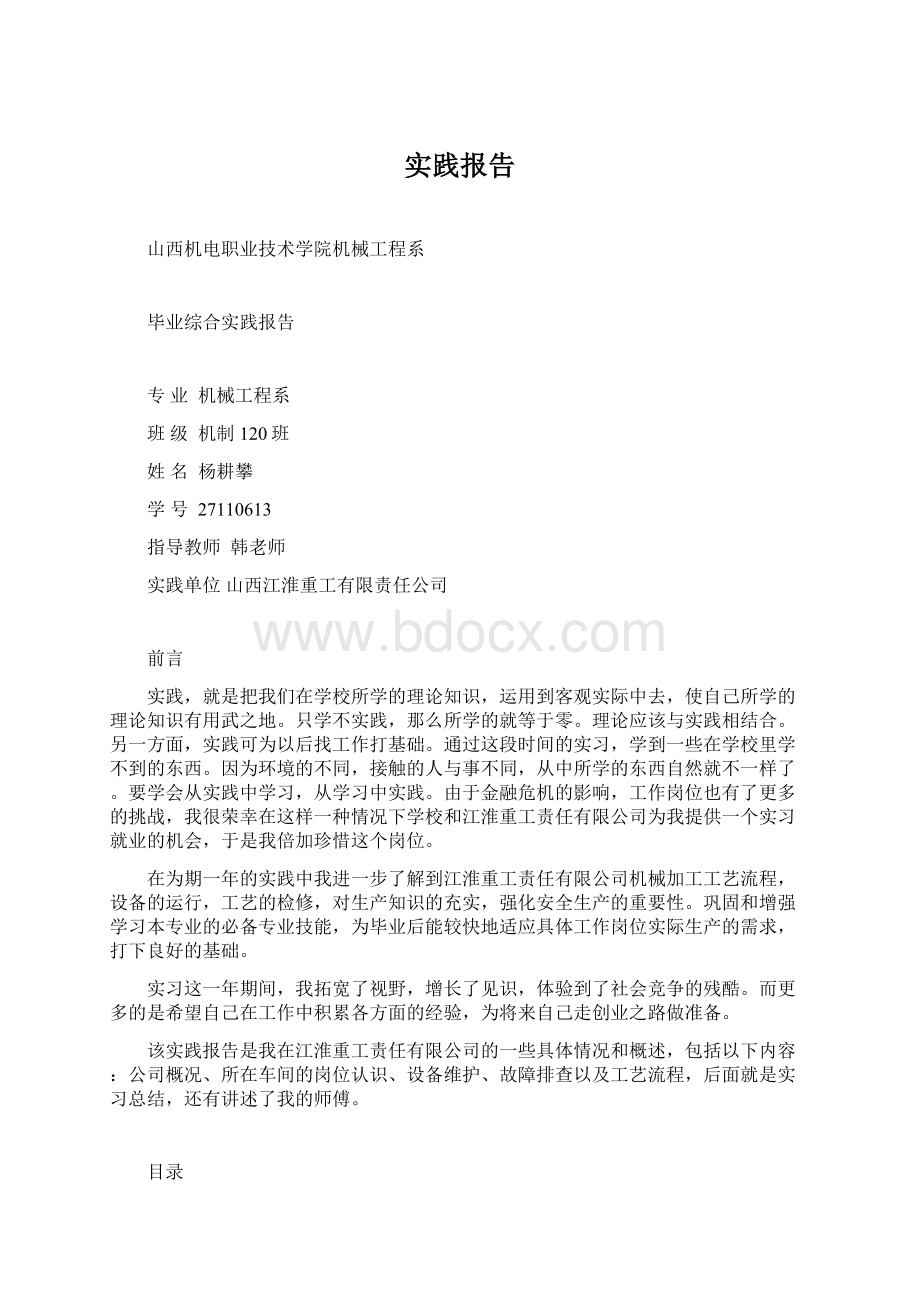
实践报告
山西机电职业技术学院机械工程系
毕业综合实践报告
专业机械工程系
班级机制120班
姓名杨耕攀
学号27110613
指导教师韩老师
实践单位山西江淮重工有限责任公司
前言
实践,就是把我们在学校所学的理论知识,运用到客观实际中去,使自己所学的理论知识有用武之地。
只学不实践,那么所学的就等于零。
理论应该与实践相结合。
另一方面,实践可为以后找工作打基础。
通过这段时间的实习,学到一些在学校里学不到的东西。
因为环境的不同,接触的人与事不同,从中所学的东西自然就不一样了。
要学会从实践中学习,从学习中实践。
由于金融危机的影响,工作岗位也有了更多的挑战,我很荣幸在这样一种情况下学校和江淮重工责任有限公司为我提供一个实习就业的机会,于是我倍加珍惜这个岗位。
在为期一年的实践中我进一步了解到江淮重工责任有限公司机械加工工艺流程,设备的运行,工艺的检修,对生产知识的充实,强化安全生产的重要性。
巩固和增强学习本专业的必备专业技能,为毕业后能较快地适应具体工作岗位实际生产的需求,打下良好的基础。
实习这一年期间,我拓宽了视野,增长了见识,体验到了社会竞争的残酷。
而更多的是希望自己在工作中积累各方面的经验,为将来自己走创业之路做准备。
该实践报告是我在江淮重工责任有限公司的一些具体情况和概述,包括以下内容:
公司概况、所在车间的岗位认识、设备维护、故障排查以及工艺流程,后面就是实习总结,还有讲述了我的师傅。
目录
第1章了解企业概况……………………4
第2章岗位认识…………………………13
第3章机床的维护………………………25
第4章心得体会…………………………27
第1章了解企业概况
1.1企业全称、地址、性质
企业全称:
山西江淮重工有限责任公司
企业地址:
地处山西省晋城市经济技术开发区内
企业性质:
国有企业
1.2企业历史
山西晋城江淮工贸有限公司,始建于1966年。
历经四十多年发展,已成为拥有铸造、机械加工、焊接、工模具设计与制造、表面处理、热处理等多种生产能力,集科研、设计、生产为一体的综合性企业。
公司目前产品涉及船舶、汽车、煤炭、核电、风电等行业机械配套设备、太阳能、建筑材料等多个领域,并积极向石油钻探、民爆产业延伸。
企业分新老两区,新厂区位于晋城市经济开发区内,老区位于泽州县,自八十年代中期,工厂实施产业结构调整,经国家批准,在“七五”、“八五”期间,共投入资金8千余万元进行技术改造,引进美国、德国、日本等国先进机械加工设备,现已形成完整的机械加工、有色金属铸造、金属表面处理及热处理、工模具制造、理化、计量及测试等综合性的加工生产企业。
1.3企业规模
工厂占地面积56万平方米,固定资产净值1亿1千余万元。
生产设备1036台(套),下设8个分厂。
公司现有员工2000余人,其中各类专业技术人员425人,高级专业技术人员50余人。
拥有固定资产5亿多元,占地面积80余万平方米,主要生产设备1000余台(套),公司具有精密及普通机械加工、铸造、表面处理、热处理等多种加工能力,并具有先进的计量检测设备和理化分析设备。
现公司拥有数控车床及数控车削中心48台,数控加工中心及数控镗铣床42台,电加工设备25台,铝合金压差铸造生产线两条,另有50T-500T液压机十余台,各种冲床、剪板机、数控等离子切割机、高压水射流切割机、卷板机、氩弧焊、CO2保护焊、大型喷沙、抛丸、喷漆等生产设备。
计量理化方面有三座标测量机两台,等离子光谱分析仪,高精度测长仪,无损探伤等检测设备。
公司近年来,通过对生产线进行全面技术改造,引进世界先进国家的新设备、新工艺、新技术,建成了企业独特的铸造、机械加工、焊接、工模具设计与制造、表面处理、热处理等多条生产线,并具有先进的计量检测和理化分析手段,大大提高了企业的市场竞争能力。
公司于1996年通过了GB/T19001–2000质量管理体系认证,并于2006年取得了GB/T24001–1996环境管理体系认证和GB/T2800–2001职业健康安全管理体系认证。
公司在高强度铝合金压差铸造技术领域处于国内领先水平,拥有大、中、小三条铸造生产线,年生产能力1000吨以上,最大铸件可达6000千克,最大直径1米,最大高度2.2米,可完成各种不同规格、形体各异的大型薄壁铸件生产。
机械加工能力优势突出,拥有各类数控加工设备200余台(套),其中从瑞士、德国进口的各类大型数控加工设备30余台(套)。
“摩擦材料分厂”是山西晋城江淮工贸有限公司下属的经济独立核算单位。
始建于1991年3月,专门从事摩擦材料制品的研发与生产。
现生产占地面积2016平方米,固定资产1000余万元,生产设备100余台(套),其中有蔡氏试验机、定速试验机、万能试验机、理化分析室等20余台(套)。
有十余位高、中级科技、试验人员专门从事摩擦材料研发和试制。
组建了多条现代生产线,形成了年产汽车盘式制动刹车片100万套,鼓式制动刹车蹄总成50万套,工业制动器摩擦材料2000余吨的生产能力,产品有无石棉低金属、无石棉非金属两大系列。
并通过国家权威产品技术检测部门的“台架试验”“军爵”牌刹车片系列产品与辆多家车桥底盘厂配套。
公司生产的“军爵”牌摩擦材料产品。
现分为无石棉低金属、无石棉非金属汽车及工业用制动衬片两大系列产品,并广泛应用于汽车、石油钻机、火车、船舶、风力发电机、冶金、采矿、能源、化工、港口、码头、建筑、国防等行业的各式起重机、连铸连轧机械的安全制动产品。
先后被中国摩擦密封材料协会评为“国家推荐品牌产品”、“扶优推强信得过产品”,被山西省技术监督局评为“山西省著名商标”,山西省名牌产品协会评为“山西省用户满意产品”,产品获得了自营进出口权。
产品又先后被中国摩擦密封材料协会评为“国家推荐品牌产品”、“扶优推强信得过产品”。
在二000年的招标中实现了与河南省焦作制动器股份有限公司及瑞塞尔合资公司等主机厂全面配套。
产品随主机设备出口至二十余个国家和地区。
二000年通过GB/T9002—1994质量体系谁并获得了自营进出口权。
我厂为“中国摩擦材料协会”正式会员单位。
1.4企业产品
公司自行研制开发生产的“神力”牌太阳能热水器畅销国内二十多个省市,其中“神力”集成式太阳能热水器拥有国家专利。
多年来,优质的售后服务为公司的发展赢得了良好的信誉。
公司拥有的塑钢门窗生产线,是民品发展的又一大亮点。
其加工生产的产品远销省内外。
无论在工业厂房建筑、还是在民用住宅方面,产品都占有一席之地。
公司七分厂现拥有高、精、尖数控机床和高精密加工中心,其加工设备先进、加工手段齐全,公司依托军工优势,技术力量雄厚、管理理念超前,集产品开发、设计、制造为一体,在晋城地区机械加工行业中首屈一指,在华北地区同行中也名列前茅,适合新型产品的研制开发和所有定型产品的批量加工和流水作业。
从ф10mm–ф800mm的多种规格和系列的新概念数控车削中心和ф1000mm、ф1250mm五米数控车床能使工件在一次装夹下,便可完成车、铣、钻加工,大大节省了机加辅助时间,又为客户尽可能地降低了机加成本。
五轴联动的数控镗铣加工中心和能够进行五面体加工的定梁龙门数控铣床适合于各种箱式结构件和大型复杂零件的加工,专为煤机、矿机、汽车等行业打造精品。
数控立、卧铣削加工中心配置刀库,特别适用于铸造模具、塑料模头等具有复杂形状零件的精密加工。
高精度慢走丝、精密电火花成型机、线切割机床又能为高硬度模具的批量加工提供强有力的保障。
数控水切割机床、ф3150mm落地车床等特种设备又能为用户提供众多加工服务。
江淮重工作为中国船舶重工集团公司的骨干企业之一,将以创建中国最大国际一流船舶集团为目标,依托集团公司在国际国内的优势地位,以团结务实、求实创新的精神,牢固树立“诚信为本顾客至上”的经营思想,致力于打造顾客满意的一流产品,不断加强科技创新,提升生产能力,完善品质控制,优化管理模式,依靠雄厚的技术、先进的设备、科学的管理、优质的服务、良好的信誉,赢得了广大用户和协作单位的尊重和好评。
千帆竞发、百舸争流,公司将始终秉持强烈的进取精神,坚持诚实守信、合作共赢、互惠互利理念靠一流的技术、优质的服务、良好的信誉,又有各界同仁的鼎力相助,山西江淮重工有限公司必将走向强大与辉煌。
1.5企业发展规划
山西江淮重工有限责任公司早规划、早准备,在认真总结“十一五”期间所取得成绩的基础上,全面分析了公司目前在发展中所面临的形势,提出了2010年及“十二五”发展的目标和思路,对公司现有生产格局进行重新规划设计,整合两个生产厂区的资源,力争到2015年公司经济总量达到10亿元以上,真正实现大中型机械装备制造企业的战略转型目标,并制定了公司《2010年及“十二五”发展规划》。
江淮重工在制定《2010年及“十二·五”发展规划》时,认真学习了集团公司总经理李长印指示精神,对公司下一步的重点工作进行了安排部署。
公司各单位正精心组织好今年冲刺全年目标的工作,想方设法克服困难,努力完成年初制订的产值增长计划,确保年度生产经营目标全面完成。
公司还对预研生产项目、节能减排以及基础设施改造、风电制动器生产线建设、核电认证、流动资金筹集等工作,进行了详细周密的安排部署。
企业文化
公司愿景(发展目标):
创建一流企业
公司精神:
自强、自信、求实、求精
价值观:
强企报国,奉献社会
管理理念:
严、精、细、新
工作作风:
思、真、实
用人理念:
知人善用、人尽其才
营销服务理念:
你把要求给我,我把满意给你
质量理念:
做精品、追求零缺陷
安全理念:
预防为主,警钟长鸣
公司QEO方针:
遵章守法重达标,全员意识要提高
以诚取信求满意,预防为主降能耗
安全生产人为本,持续改进创绩效
1.6企业动态
1.6.1公司组织“迎新春、庆元旦”职工长跑健身赛活动
12月30日,虽然是隆冬季节,玉龙潭公园内彩旗飘扬、热闹非凡,江淮重工“迎新春、庆元旦”职工长跑健身赛活动在此举行。
长跑比赛共分青年组和中年组,有四百多名职工参加了长跑比赛活动。
公司领导郜光明、聂秋社、夏靖立也来到活动现场为大家鼓劲加油,并分别为获得一、二、三等奖的选手颁发了奖品。
公司领导希望通过今天举行迎新年长跑健身活动,全体员工能够快乐工作、健康生活,继续发扬江淮人不畏艰险、顽强拼搏的优良传统,进一步增强凝聚力和战斗力,继续谱写江淮重工持续平稳发展的新篇章。
1.6.2江淮重工精心绘制公司发展蓝图
山西江淮重工有限责任公司早规划、早准备,在认真总结“十一五”期间所取得成绩的基础上,全面分析了公司目前在发展中所面临的形势,提出了2010年及“十二五”发展的目标和思路,对公司现有生产格局进行重新规划设计,整合两个生产厂区的资源,力争到2015年公司经济总量达到10亿元以上,真正实现大中型机械装备制造企业的战略转型目标,并制定了公司《2010年及“十二五”发展规划》。
江淮重工在制定《2010年及“十二五”发展规划》时,认真学习了集团公司总经理李长印指示精神,对公司下一步的重点工作进行了安排部署。
公司各单位正精心组织好今年冲刺全年目标的工作,想方设法克服困难,努力完成年初制订的产值增长计划,确保年度生产经营目标全面完成。
公司还对预研生产项目、节能减排以及基础设施改造、风电制动器生产线建设、核电认证、流动资金筹集等工作,进行了详细周密的安排部署。
1.6.3公司召开液压支柱生产专项会
2009年12月4日,公司召开了液压支柱生产专项会议。
公司领导郜光明、赵中庆,总质量师郭沁明、副总工程师田军文和液压支柱主要生产分厂领导及相关单位负责人参加了会议。
会议主要总结梳理了液压支柱从试制攻关和两个批次批产过程中取得经验和亟待完善的工作,共同探讨下一阶段生产需要解决的问题。
会议就技术工艺向细腻化转换、生产组织由调度管理向计划管理转变、严格过程质量控制、生产能力提升、生产效率提高和降低成本等进一步达成了共识,明确了质量过程控制的六项具体措施。
党委书记郜光明强调指出:
通过对液压支柱现场管理模式、质量过程控制、细化技术工艺、成本控制、能力提升、挖掘潜力等方面的研讨,明确了今后工作的改进方向,必须用科学的管理办法,不断完善管理体制机制,为2010年液压支柱上规模、上水平、做强做大液压支柱打好基础。
1.6.4江淮重工对人事劳资管理人员进行培训
近日,山西江淮重工有限责任公司邀请人力资源管理方面的专家,对公司人事劳资管理人员就组织行为学、人力资源管理。
劳动力市场、劳动与社会保险政策等内容进行了专门的培训,旨在提高全体人员在现代企业管理制度下的业务能力和水平
2009年12月21日—22日,中国船舶重工集团公司召开2010年工作(视频)座谈会,公司领导郜光明、聂秋社、赵中庆、宋维炉、夏靖立以及相关部门主要领导在我公司分会场参加了会议。
集团公司党组书记、总经理李长印在会上对2009年的工作进行了概要总结;提出了2010年“把握大势、强化创新、调整结构、持续发展”的工作总体方针和2010年生产经营的主要经济指标;明确了2010年的重点工作。
围绕李长印总经理的讲话精神,参加会议的各成员单位进行了认真的讨论,部分成员单位领导在会议上进行了发言。
对照座谈会上李长印总经理提出的新“十六字方针”和2010年各项工作的要求,我公司对2010年的总体工作安排也进行了认真的研究讨论,确保在2010年战略转型发展第二阶段的起步开局之年,各项经济指标能够顺利实现,企业经营管理水平进一步提升。
第2章岗位认识
2.1工作岗位位置图
2.2普通车工岗位的情况
1.职业定义
车工属于生产设备操作人员类中的机械冷加工人员,其定义为:
操作车床,进行工件旋转表面切削加工的人员。
车工是用车床加工的一种方法。
2.适用范围
车床主要用于加工各种回转表面,如内、外圆柱面,圆锥面,成形回转表面及端面等.车床还能加工螺纹面。
若使用孔加工刀具(如钻头、铰刀等),还可加工内圆表面。
车床在一般机器制造厂的金属切削机床中所占的比重最大,约占机床总台数的30%。
3.知识要求
基础理论知识;机械加工基础知识;钳工基础知识;电工知识;安全文明生产与环境保护知识;质量管理知识;相关法律、法规知识。
1)仔细研究和详细了解各种车床的零件,部件,机构和它们之间的相互关系。
以便正确使用车床和排除故障。
并熟悉车床各加油孔。
2)正确使用车床的附件以及工具,刀具和量具,熟悉它们的构造和保养。
3)熟悉图纸和工艺。
并能按图纸和工艺的要求加工零件。
4)掌握有关车削工件的计算。
5)了解常用金属材料性能及热处理知识。
6)正确组识自己的工件位置(工件堆放,粗精分开放)
7)收得如何节约原材料和提高劳动生产率。
保证产品质量,降低成本。
8)能查阅有关技术手册。
2.3技能要求
1.基本素质要求
(1)具有较强的计算能力和空间感、形体知觉及色觉;手指、手臂灵活,动作协调。
(2)具有职业道德基本知识,并遵守本职业的职业守则。
(3)最低学历为初中毕业。
2.车工的作业环境为:
室内,常温
本要求按照初级、中级、高级、技师和高级技师依次递进,高级别包括低级别的要求。
3.工艺准备
(1)能够读图与绘图,
(2)能够制定加工工艺,(3)能够正确定位、夹紧工件,(4)能够正确选择并安装刀具,(5)能够对设备进行调整、维护及保养,(6)能够编制数控机床的程序。
2.4机床及其他设备的应用
2.4.1机械加工工艺过程介绍
在生产过程中,那些与有原材料转变为产品直接相关的过程称为工艺过程。
它包括毛坯制造、零件加工、热处理、质量检验和机器装配等。
而为保证工艺过程正常进行所需要的刀具、夹具制造,机床调整维修等则属于辅助过程。
在工艺过程中,以机械加工方法按一定顺序逐步地改变毛坯形状、尺寸、相对位置和性能等,直至成为合格零件的那部分过程称为机械加工工艺过程。
技术人员根据产品数量、设备条件和工人素质等情况,确定采用的工艺过程,并将有关内容写成工艺文件,这种文件就称工艺规程。
为了便于工艺规程的编制、执行和生产组织管理,需要把工艺过程划分为不同层次的单元。
它们是工序、安装、工位、工步和走刀。
其中工序是工艺过程中的基本单元。
零件的机械加工工艺过程由若干个工序组成。
在一个工序中可能包含有一个或几个安装,每一个安装可能包含一个或几个工位,每一个工位可能包含一个或几个工步,每一个工步可能包括一个或几个走刀。
1)工序一个或一组工人,在一个工作地或一台机床上对一个或同时对几个工件连续完成的那一部分工艺过程称为工序。
划分工序的依据是工作地点是否变化和工作过程是否连续。
例如,在车床上加工一批轴,既可以对每一根轴连续地进行粗加工和精加工,也可以先对整批轴进行粗加工,然后再依次对它们进行精加工。
在第一种情形下,加工只包括一个工序;而在第二种情形下,由于加工过程的连续性中断,虽然加工是在同一台机床上进行的,但却成为两个工序。
工序是组成工艺过程的基本单元,也是生产计划的基本单元。
2)安装在机械加工工序中,使工件在机床上或在夹具中占据某一正确位置并被夹紧的过程,称为装夹。
有时,工件在机床上需经过多次装夹才能完成一个工序的工作内容。
安装是指工件经过一次装夹后所完成的那部分工序内容。
例如,在车床上加工轴,先从一端加工出部分表面,然后调头再加工另一端,这时的工序内容就包括两个安装。
3)工位采用转位(或移位)夹具、回转工作台或在多轴机床上加工时,工件在机床上一次装夹后,要经过若干个位置依次进行加工,工件在机床上所占据的每一个位置上所完成的那一部分工序就称为工位。
简单来说,工件相对于机床或刀具每占据一个加工位置所完成的那部分工序内容,称为工位。
为了减少因多次装夹而带来的装夹误差和时间损失,常采用各种回转工作台、回转夹具或移动夹具,使工件在一次装夹中,先后处于几个不同的位置进行加工。
操作者在上下料工位Ⅰ处装上工件,当该工件依次通过钻孔工位Ⅱ、扩孔工位Ⅲ后,即可在一次装夹后把四个阶梯孔在两个位置加工完毕。
这样,既减少了装夹次数,又因各工位的加工与装卸是同时进行的,从而节约安装时间使生产率可以大提高。
4)工步在加工表面不变,加工工具不变的条件下,所连续完成的那一部分工序内容称为工步。
生产中也常称为“进给”。
整个工艺过程由若干个工序组成。
每一个工序可包括一个工步或几个工步。
每一个工步通常包括一个工作行程,也可包括几个工作行程。
为了提高生产率,用几把刀具同时加工几个加工表面的工步,称为复合工步,也可以看作一个工步,例如,组合钻床加工多孔箱体孔。
5)走刀加工刀具在加工表面上加工一次所完成的工步部分称为走刀。
例如轴类零件如果要切去的金属层很厚,则需分几次切削,这时每切削一次就称为一次走刀。
因此在切削速度和进给量不变的前提下刀具完成一次进给运动称为一次走刀。
2.4.2加工精度的基本概念
对零件制造的基本要求就是要做到多、快、好、省。
其中“好”的含义包括不断提高零件的质量,提高其使用效能与使用寿命,最大限度地消灭废品,降低次品率,提高零件的合格率。
因为零件的质量直接影响着机器的性能、寿命、效率、可靠性等指标,是保证机器质量的基础,而零件的制造质量,是依靠其毛坯的制造方法、机械加工、热处理以及表面处理等工艺来保证的。
因此,在零件制造的各个环节都要始终把保证质量放在首位。
衡量零件的加丁质量的指标有两大类:
一是机械加工精度,二是机械加工表面质量。
1.加工精度和加工误差
加工精度是指零件加工后的实际几何参数(尺寸、形状和位置)与图纸规定的理想几何参数符合的程度。
这种相符合的程度越高,加工精度也越高。
所谓理想几何参数,对于尺寸而言,就是零件的公差带中心;对于表面形状而言,就是绝对准确的圆柱面、平面、圆锥面等;对表面位置而言,就是绝对的平行、垂直、同轴和一定的角度等。
在加工中,由于各种因素的影响,实际上不可能将零件的每一个几何参数加工得与理想几何参数完全相符,总会产生一些偏离。
这种偏离,就是加工误差。
实际上,从多快好省的全面观点出发,也没有必要将零件的尺寸、形状和位置加工得绝对精确。
因此,只要能保证零件在机器中的功能,则加工时允许零件的几何参数存在一定的加工误差。
只要零件的加上误差不超出零件图上按零件的设计要求所规定的公差,就可以说保证了零件的加工精度要求。
由此可见,“加工精度”和“加工误差”这两个概念是从两个侧面来评定零件几何参数这个同一事物的。
加工精度的低和高是通过加工误差的大和小来表示的。
所以,保证和提高加工精度的问题,实际上就是限制和减小加工误差的问题。
2.获得加工精度的方法
加工精度可以分为尺寸精度、形状精度和位置精度。
因此,加工精度的高、低是以尺寸公差、形状公差和位置公差来衡量的。
1)获得零件尺寸精度的方法
(1)试切法这种方法就是通过试切、测量、调整、再试切,反复进行直到被加工尺寸达到要求为止。
例如,在车床亡车削外圆时,首先在工件端部试切一小段,然后停车、退刀,用外卡钳或游标卡尺测量其直径,再调整切削深度,之后再切削。
经多次试切,直到尺寸达到要求时再车出整个表面来。
这种方法能达到较高的加工精度,但它的效率低,对操作者的技术水平要求高,主要适用于单件小批生产。
(2)调整法这种方法是先调整好刀具和工件在机床上的相对位置,并在——批零件的加工过程中保持这个位置不变,以此保证被加工尺寸的精度。
工件的加工精度很大程度上取决于调整精度,调整好之后,能自动保证加工精度,大大缩短了加工所需的辅助时间,因此生产率高。
这种方法广泛用于各类半白动、自动机床和自动线卜,适用于成批、大量生产。
(3)定尺寸刀具法这种方法是用刀具的相应尺寸和形状来保证被加工部位的尺寸和形状。
例如,钻孔、铰孔、拉孔、镗孔、攻螺纹和铣槽等。
这种方法的加工精度主要由刀具本身的精度来保证。
由于可以提高刀具制造精度,因此用尺寸刀具加工能达到相当高的加工精度,同时又避免了试切过程,生产率较高。
其主要缺点是刀具的制造复杂和耗费较大,使用的尺寸范围受到一定的限制。
此法适用于各种生产规模中的孔、螺纹和成形表面的加工。
(4)自动控制法这种方法是用度量装置、进给机构和控制系统构成加工过程的自动循环,即自动完成加工巾的切削、度量、补偿调整等一系列工作,当工件达到要求的尺寸时,机床自动退刀停止加工。
此法适用于成批和大量生产。
2.5机床介绍
机床,用来制造机器零件的设备通称为金属切削机床,简称机床。
普通车床,为是最广泛的车床种类,因为其主轴是水平放置,所以又名卧式车床。
普通车床的主要部件有:
主轴箱、进给箱、溜板箱、刀架、尾架、光杠、丝杠和床身。
普通车床通过配备各种专用刀具,可完成内外圆加工、钻孔、车螺纹、切断车槽、端面加工、车外圆、钻中心孔、车孔,铰孔、车圆锥、车成形面、滚花、盘绕弹簧等加工程序。
车床是主要用车刀对旋转的工件进行车削加工的机床。
在车床上还可用钻头、扩孔钻、铰刀、丝锥、板牙和滚花工具等进行相应的加工。
车床主要用于加工轴、盘、套和其他具有回转表面的工件,是机械制造和修配工厂中使用最广的一类机床。
古代的车床是靠手拉或脚踏,通过绳索使工件旋转,并手持刀具而进行切削的。
1797年,英国机械发明家莫兹利创制了用丝杠传动刀架的现代车床,并于1800年采用交换齿轮,可改变进给速度和被加工螺纹的螺距。
1817年,另一位英国人罗伯茨采用了四级带轮和背轮机构来改变主轴转速。
为了提高机械化自动化程度,1845年,美国的菲奇发明转塔车床;1848年,美国又出现回轮车床;1873年,美国的斯潘塞制成一台单轴自动车床,不久他又制成三轴自动车床;20世纪初出现了由单独电机驱动的带有齿轮变速箱的车床。
第一次世界大战后,由于军火、汽车和其他机械工业的需要,各种高效自动车床和专门化车床迅速发展。
为了提高小批量工件的生产率,40年代末,带液压仿形装置的车床得到推广,与此同时,多刀车床也得到发展。
50年代中,发展了带穿孔卡、插销