基于车辆动力学的四驱车的1档传动比优化设计.docx
《基于车辆动力学的四驱车的1档传动比优化设计.docx》由会员分享,可在线阅读,更多相关《基于车辆动力学的四驱车的1档传动比优化设计.docx(14页珍藏版)》请在冰豆网上搜索。
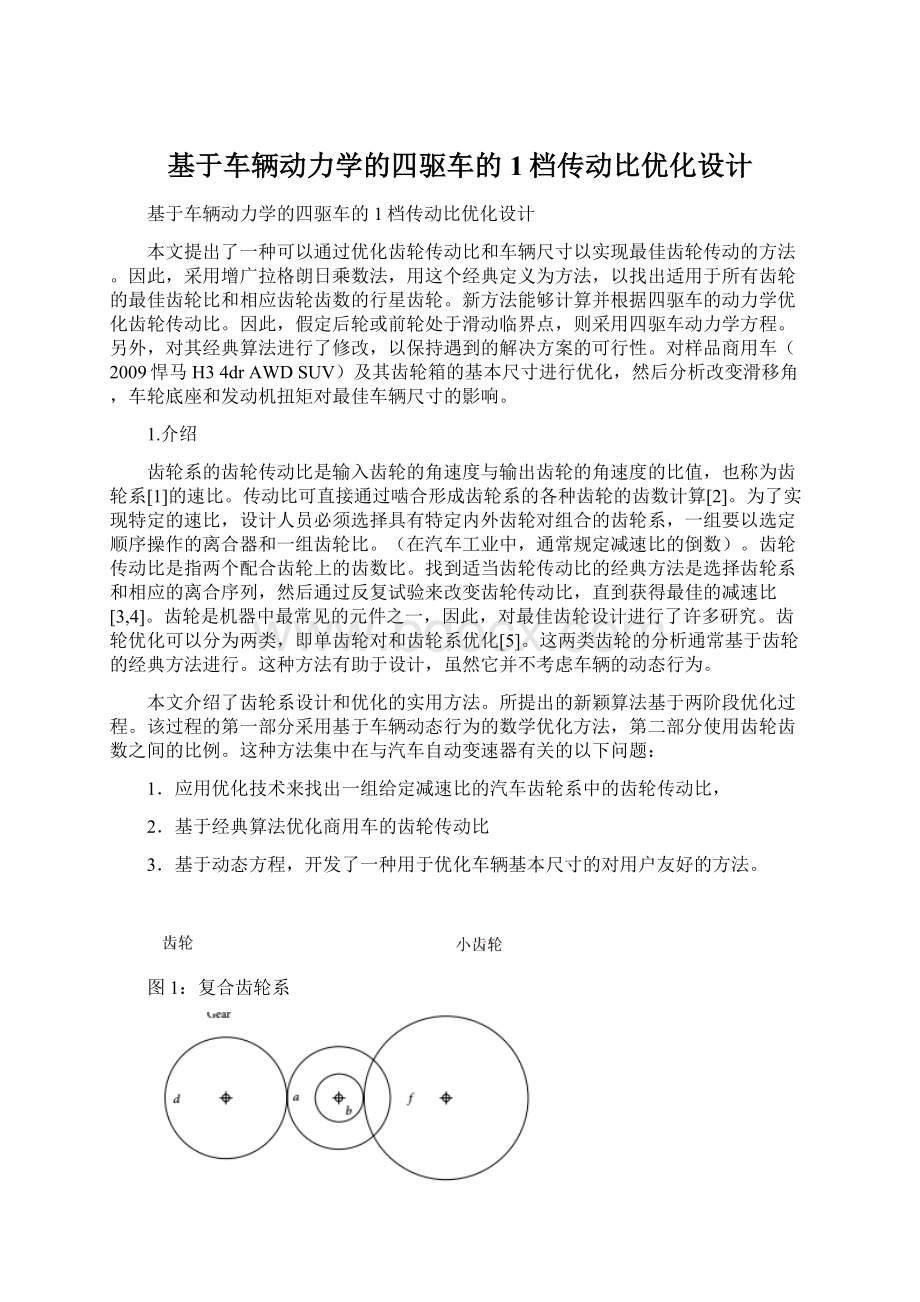
基于车辆动力学的四驱车的1档传动比优化设计
基于车辆动力学的四驱车的1档传动比优化设计
本文提出了一种可以通过优化齿轮传动比和车辆尺寸以实现最佳齿轮传动的方法。
因此,采用增广拉格朗日乘数法,用这个经典定义为方法,以找出适用于所有齿轮的最佳齿轮比和相应齿轮齿数的行星齿轮。
新方法能够计算并根据四驱车的动力学优化齿轮传动比。
因此,假定后轮或前轮处于滑动临界点,则采用四驱车动力学方程。
另外,对其经典算法进行了修改,以保持遇到的解决方案的可行性。
对样品商用车(2009悍马H34drAWDSUV)及其齿轮箱的基本尺寸进行优化,然后分析改变滑移角,车轮底座和发动机扭矩对最佳车辆尺寸的影响。
1.介绍
齿轮系的齿轮传动比是输入齿轮的角速度与输出齿轮的角速度的比值,也称为齿轮系[1]的速比。
传动比可直接通过啮合形成齿轮系的各种齿轮的齿数计算[2]。
为了实现特定的速比,设计人员必须选择具有特定内外齿轮对组合的齿轮系,一组要以选定顺序操作的离合器和一组齿轮比。
(在汽车工业中,通常规定减速比的倒数)。
齿轮传动比是指两个配合齿轮上的齿数比。
找到适当齿轮传动比的经典方法是选择齿轮系和相应的离合序列,然后通过反复试验来改变齿轮传动比,直到获得最佳的减速比[3,4]。
齿轮是机器中最常见的元件之一,因此,对最佳齿轮设计进行了许多研究。
齿轮优化可以分为两类,即单齿轮对和齿轮系优化[5]。
这两类齿轮的分析通常基于齿轮的经典方法进行。
这种方法有助于设计,虽然它并不考虑车辆的动态行为。
本文介绍了齿轮系设计和优化的实用方法。
所提出的新颖算法基于两阶段优化过程。
该过程的第一部分采用基于车辆动态行为的数学优化方法,第二部分使用齿轮齿数之间的比例。
这种方法集中在与汽车自动变速器有关的以下问题:
1.应用优化技术来找出一组给定减速比的汽车齿轮系中的齿轮传动比,
2.基于经典算法优化商用车的齿轮传动比
3.基于动态方程,开发了一种用于优化车辆基本尺寸的对用户友好的方法。
图1:
复合齿轮系
图2:
2D车辆模型的演示。
2.齿轮系经典设计
为了找到所需的总传动比,复合齿轮系包含两对齿轮d-a和b-f(图1)。
输入和输出齿轮之间所需的齿轮比itot,w0和wi分别显示为输出齿轮和输入齿轮的角速度,n表示每个齿轮上的齿数。
(1)
2.1经典齿轮传动比优化。
在增广拉格朗日乘数法中,目标函数是计算齿轮d,a,b和f的齿数,以便找到齿轮比itot。
每个齿轮的最小齿数假定在12到60之间。
目标比率,itrg,假定为1/6.93,函数表示如下:
(2)
换句话说,该过程将计算四个变量的最佳值,这将使目标比率itrg和可用齿轮比itot之间的平方差最小化。
目标函数表示为实际和目标传动比之间的平方差。
齿轮系问题的另一种解决方案是由差分进化算法建立起来的。
通过应用表1和表2中提到的明确列举[12-14],发现这些解决方案是全局最优的。
在本文中,2009年悍马H34drSUV的遗传算法已经解决了这个问题。
表1:
齿轮比问题的替代方案
3.WD车辆动态齿轮比
通过应用动力学方程得到动态变速比如下[15,16]:
(3)
Ff和Fr分别是前后牵引力。
m,车辆质量,a,是加速度,FRR是滚动阻力,w是车辆重量,θ是道路坡度,Fa是空气动力,Nf是前反作用力,Nr是后反作用力,hA是气动力的高度,h是重心高度力,l是轮底,a和b分别是c.g到前轮和后轮的距离。
(4)
(5)
根据图2,定义了后牵引力与前牵引力的和为总牵引。
表2:
齿轮系问题的最优解
还有:
(6)
(7)
(8)
(9)
fr是滚动阻力系数,通过公式(4)—(9)得出下列公式:
(10)
(11)
在四驱车辆中,前轴和后轴的车轮转矩按一定比率r分布,r由前后轴转矩的比值得到。
假设后轮处于临界滑动点,则表达的是四驱车辆的齿轮传动比的表达式。
根据图2,总的牵引力是:
(12)
通过将前轴和后轴的牵引力的比值除以相同的前后齿轮传动比来获得:
(13)
将(5)带入(13)得到:
(14)
当后轮胎处于滑动点时,(14)可以写成:
(15)
μp是道路摩擦系数
在本文中,车辆速度被认为等于零,这发生在最大道路坡度和轮胎滑移点的相交临界值。
忽略(10)中Δ的项和其在(12)中的替换,则可以得到:
(16)
将(8)代入(16)并根据N=Wcosθ,则可以获得:
(17)
(18)
将(16)代入(15)中,最大牵引力计算为:
(19)
齿轮传动比(n)的方程表示为:
(20)
其中nd为差动比,Te为电机转矩,rw为轮胎半径。
另外,将(12)代入(13)中,后齿轮传动比(nlr)可得:
(21)
另一方面,假设前轮处于临界滑移点,可以获得四驱车辆的齿轮传动比的表达式。
根据(5)和(13),总牵引力可以写为:
(22)
当前轮胎处于滑移点时,最大牵引力可计算为:
(23)
图3:
前轮胎或后轮胎处于滑移点时的齿轮比及其误差。
因此,用最大牵引力代替,可以表示为
(24)
最后,前齿轮比表示为
(25)
动态变速比结果进行了两种比较。
首先,比较包括20个样本车在内的车辆人数,如齿轮比。
其次,执行该方法来评估动态齿轮比。
方法之间的差异相互比较。
这个想法是表明即使是70%的动态形式,在二手车都用于商用车的情况下,仍然表现得比古典的要好。
将第一动力传动比与第一代经典齿轮比(nl,实数)的值进行比较,对于汽车厂使用的20辆样车,这种比较如图3所示。
传统的方法不考虑轮胎滑移以及前轮胎或后轮滑移呈现不同的行为并使计算与现实更相似的事实。
因此,动态齿轮比比传统齿轮比好得多。
此外,经典齿轮比与动态齿轮比之间的差异如图3所示。
第一档齿轮比应约在4到6之间以在轮胎中产生更多扭矩。
表2中提出的齿轮比不是车辆比例,它们用于呈现经典的齿轮比计算方法。
第二车辆齿轮比和其他齿轮比减小以减少发动机转矩。
图3的齿轮比与表2中给出的比率不同,尽管在计算车辆经典齿轮比中使用相同的方法。
为了优化不同路面坡度的齿轮比,为了获得2009年悍马H34drSUV的最佳基本尺寸,应分析齿轮比参数的影响。
在图4-6中研究了基本车辆尺寸变化如摩擦系数,滚动阻力系数和重量分布评估的影响。
在每个参数中齿轮比误差约为零左右的情况下,这些图用于确定优化参数的界限。
此外,图4-6表示改变参数的影响,例如:
车辆高度,μp和fr在齿轮比上。
此外,它将指示如何改变这些参数将改变传动比,并提供最佳传动比,这是指参数误差在零附近的点,以提高齿轮箱的效率。
图4:
后/前档比与路面摩擦显示系数的关系。
3.1。
道路摩擦系数道路摩擦变化系数对动态传动比有影响。
它与传统齿轮比的误差如图4所示。
如图4所示,增加道路摩擦系数将减小经典齿轮比与动态齿轮比之间的差异。
换句话说,前后齿轮比和道路摩擦系数之间存在直接的关系。
图5:
后/前齿轮比误差与车辆高度的关系c.g..
3.2。
车辆高度c.g.车辆例如高度变化对动态齿轮比有影响。
经典传动比发生的误差如图5所示。
高度增加了正面模式的经典和动态齿轮比之间的差异。
相反,这种差异将减少重新调整。
因此,前后齿轮比具有相反的作用。
3.3。
滚动阻力摩擦。
滚动阻力(有时称为滚动摩擦或滚动阻力)是当轮胎在表面上滚动时抵抗运动的力。
主要是由非弹性效应造成的;也就是说,当去除压力时,并不能恢复对象的变形所需的所有能量。
滚动阻力是作为速度的函数表示的
(26)
图6显示,提高滚动阻力系数降低了传统齿轮比和动态齿轮比之间的差异。
此外,增加滚动阻力增加前齿轮比。
图6:
后/前齿轮比与滚动阻力误差的关系。
4.
遗传算法优化
目前使用演化方法来解决优化问题有着越来越大的趋势。
作为最受欢迎的演化算法的遗传算法在研究研究中有广泛的应用[17-19]。
在前轮或后轮处于滑移点的情况下,第一动力传动比使用9个设计变量,以提出适当的变速比设计模型。
优化的结果是指定车辆的基本尺寸,最佳道路坡度,1档和齿轮系,使可用经典齿轮比,nl,rea实际和动态齿轮比之间的平方差最小化,nl,f,or,r遗传算法开始于多种解决方案,称为群体。
这些解决方案由基因染色体串表示[20,21]。
他们是从一群解决方案中获取的,用于创造新的人口,认为新的人口比原来的人口更好。
另一个终端遗传算法是变异率。
变量运算符改变字符串的整数部分。
每个弦的突变与初始目标函数(可用的经典齿轮比,nl,实数和动态齿轮比nl,f,or,r)之间的平方差成比例,其被选择以适合突变率(图7)。
该运算符可以提供群体中不存在的解决方案,以补偿由于交叉路口不足导致的有价值信息的损失。
在本文中,研究了GA算法中确定收敛反应精度和速度的突变率。
这里开发的代码包括人口数量,迭代次数,成本函数值,突变率等不同项目的大量探索。
因此,迭代的最小值和收敛速度非常重要。
为了探索突变率的影响,采用了3.7的经典齿轮比。
突变率为0,1%,4%,6%和15%。
早期收敛发生没有任何突变率,GA算法不能满足所有可能的约束值。
对于1%突变的情况,单个位变化并且实现更好的适应度函数的机会增加。
当突变等于零时,45代可获得最佳适应度函数。
然而,突变率的值为1%时,100代可获得适当的适应度函数。
如上所述,突变率值的增强增加了人群中各种个体的概率。
基于该解释,突变率应选择4%至6%,这是尝试和错误获得的。
在本文中,动态齿轮比方程通过图8所示的遗传算法进行了优化,目标函数如(27)所示,它是可用经典齿轮比nl,实数之间的平方差,和动态齿轮比,nl,f,or,r。
这种优化导致车辆参数的益处,如表3中列出的车轮底座和倾斜角度。
提供了4WD车辆的最佳传动比情况还需要引入在特定边界内约束的随机选择的变量。
这些变量及其带通过(28)表示:
4.1。
应用遗传算法(GA)。
齿轮比优化中的人口规模代表了人口中的个人人数。
通常较大的人口数量增加初始人口中存在的变异量,并且需要更多的健身评估。
在这种情况下,人口大小为20,容易获得优异的溶液。
当然,较小的人口数量将会减少几代人,计算时间将会减少。
如图9和图10所示,可以看出,在足够数量的世代(约50代)之后,良好(最佳)解的轨迹以及人口平均的轨迹收敛于最终解。
应用遗传算法优化2009年悍马H34dr的基本尺寸得出最佳数据,以获得最合适的齿轮比。
在设计车辆时,建议在表4中提到的2009年悍马H34dr的最佳尺寸,以获得最佳的动态性能。
(27)
(28)
图7:
遗传算法算子
5.结果与讨论
将从遗传算法获得的齿轮比的结果与针对悍马H34dr报道的常规方法的结果进行比较。
这项研究证实了戈弗雷和巴布的结果。
该程序能够为可选的不同约束找到优秀的结果,并且可以考虑许多参数。
在经典形式中,为了找到所需的总传动比,复合齿轮系包含两对齿轮。
第二目标函数表示为实际和所需传动比之间的平方误差。
这个优化引入了一个变速箱
从动态齿轮比获得并提供适当的齿轮比。
戈弗雷模型基于常规齿轮比计算,其利用经典齿轮比来确定齿轮齿。
该模型与精密齿轮齿的动力学模型进行比较。
表5表示通过Godfrey和Babu[3]获得的结果证实的牙齿数。
在优化设计中研究道路坡度角,以引入与环境兼容的最佳比例,特别是使车辆在适当的条件下运行。
图11给出了通过不同路面的前后滑动模式的最佳传动比,这意味着具有平均路面坡度的不同城市需要特定的变速箱和齿轮比。
图8:
遗传算法图。
图9:
当后轮处于滑模式时,总体性能的演变=20。
图10:
当前轮处于滑模式时,人口的性能演变=20。
图11:
不同道路的最佳前后齿轮比倾斜角度
6.结论
在本文中,已经考虑了与汽车齿轮比有关的两个问题。
首先,提出了传统的试错法,通过发现满足几何约束条件的齿轮齿数组合来计算齿轮比。
其次,借助于车辆的动态参数来计算动态齿轮比。
然后,将传统的齿轮比设计与现有结果进行比较,显示出这种研究对商用车的优越性。
然后,开发出一种新的方法来计算具有将动态齿轮比和经典齿轮比之间的差最小化的趋势的第一齿轮比。
因此,用于计算齿轮比的动力学方程已被夸大,以研究用于优化样车(2009悍马H34dr)的基本尺寸的第一档。
所提出的方法还用于评估车辆的最佳尺寸以实现经典和动态齿轮比的最小差异。
还得出结论,由于c.g.的影响,更多的道路坡度产生低的第一档。
高度。
结果也与戈弗雷和巴布报道的结果进行比较[3]。
比较结果显示了本研究的可靠性。
所提出的算法与传统算法相比具有很高的灵活性。
它更适应于获得动态约束非常重要的最佳传动比。
此外,本文指出了改变参数的影响,如c.g.车辆高度,up和fr齿轮比。
在每个参数中齿轮比误差大约为零的情况下,所示的图表用于确定优化参数的界限。
此外,前后齿轮比的方程式表明,车轮底座长度和发动机扭矩的两个参数对于达到适当的性能起着重要的作用。
7.参考文献
【1】J.J.Uicker,G.R.Pennock,andJ.E.Shigley,TheoryofMachinesandMechanisms,OxfordUniversityPress,2003.
【2】B.Paul,KinematicsandDynamicsofPlanarMachinery,PrenticeHall,NewYork,NY,USA,1979.
【3】C.GodfreyandB.V.Babu,NewOptimizationTechniquesinEngineering,Springer,NewYork,NY,USA,2004.
【4】K.DebandM.Goyal,“Optimizingengineeringdesignsusingacombinedgeneticsearch,”inProceedingsofthe7thInternationalConferenceonGeneticAlgorithms,pp.521–528,1997.
【5】S.PrayoonratandD.Walton,“Practicalapproachtooptimumgeartraindesign,”Computer-AidedDesign,vol.20,no.2,pp.8392,1988.
【6】E.Sandgren,“Nonlinearintegeranddiscreteprogramminginmechanicaldesign,”inProceedingsoftheASMEDesignTechnologyConference,pp.95–105,Kissimme,Fla,USA,September1988.
【7】J.C.FuandL.Wang,“Arandom-discretizationbasedMonteCarlosamplingmethodanditsapplications,”MethodologyandComputinginAppliedProbability,vol.4,pp.5–25,2002.
【8】H.T.LohandP.Y.Papalambros,“Asequentiallinearizationapproachforsolvingmixed-discretenonlineardesignoptimizationproblems,”JournalofMechanisms,Transmissions,andAutomationinDesign,vol.113,no.3,pp.325–334,1991.
【9】Y.WangandW.J.Zhang,“Stochasticvibrationmodelofgeartransmissionsystemsconsideringspeed-dependentrandomerrors,”NonlinearDynamics,vol.17,no.2,pp.187–203,1998.
【10】C.-H.Hsu,K.-T.Lam,andY.-L.Lin,“Automaticsynthesisofdisplacementgraphsforplanetarygeartrains,”MathematicalandComputerModelling,vol.19,no.11,pp.67–81,1994.
【11】B.K.KannanandS.N.Kramer,“Anaugmentedlagrangemultiplierbasedmethodformixedintegerdiscretecontinuousoptimizationanditsapplicationstomechanicaldesign,”JournalofMechanicalDesign,vol.116,no.2,pp.405–411,1994.
【12】K.DebandM.Goyal,“Aflexibleoptimizationprocedureformechanicalcomponentdesignbasedongeneticadaptivesearch,”JournalofMechanicalDesign,vol.120,no.2,pp.162–164,1998.
【13】E.Sandgren,“Nonlinearintegeranddiscreteprogramminginmechnicaldesignoptimization,”JournalofMechanisms,Transmissions,andAutomationinDesign,vol.112,no.2,pp.223–229,1990.
【14】J.F.Fu,R.G.Fenton,andW.L.Cleghorn,“Amixedintegerdiscretecontinuousprogrammingmethodanditsapplicationtoengineeringdesignoptimization,”EngineeringOptimization,
vol.17,pp.263–280,1991.
【15】D.CrollaandB.Mashadi,VehiclePowertrainSystems,JohnWiley&Sons,NewYork,NY,USA,2011.
【16】R.G.Pennock,J.J.Uicker,andJ.E.Shigley,TheoryofMachinesandMechanisms,OxfordUniversityPress,NewYork,NY,USA,2009.
【17】C.-H.KoandS.-F.Wang,“Precastproductionschedulingusingmulti-objectivegeneticalgorithms,”ExpertSystemswithApplications,vol.38,no.7,pp.8293–8302,2011.AdvancesinMechanicalEngineering9
【18】A.KaurandA.K.Bakhshi,“Changeinoptimumgeneticalgorithmsolutionwithchangingbanddiscontinuitiesandbandwidthsofelectricallyconductingcopolymers,”ChemicalPhysics,vol.369,no.2-3,pp.122–125,2010.
【19】R.L.HauptandS.E.Haupt,PracticalGeneticAlgorithms,JohnWiley&Sons,NewYork,NY,USA,2004.
【20】J.D.Dyer,R.J.Hartfield,G.V.Dozier,andJ.E.Burkhalter,“Aerospacedesignoptimizationusingasteadystatereal-codedgeneticalgorithm,”AppliedMathematicsandComputation,vol.
218,no.9,pp.4710–4730,2012.
【21】M.SalehiandR.Tavakkoli-Moghaddam,“Applicationofgeneticalgorithmtocomputer-aidedprocessplanninginpreliminaryanddetailedplanning,”EngineeringApplicationsofArtificialIntelligence,vol.22,no.8,pp.1179–1187,2009.