数控等离子下料切割实用工艺.docx
《数控等离子下料切割实用工艺.docx》由会员分享,可在线阅读,更多相关《数控等离子下料切割实用工艺.docx(12页珍藏版)》请在冰豆网上搜索。
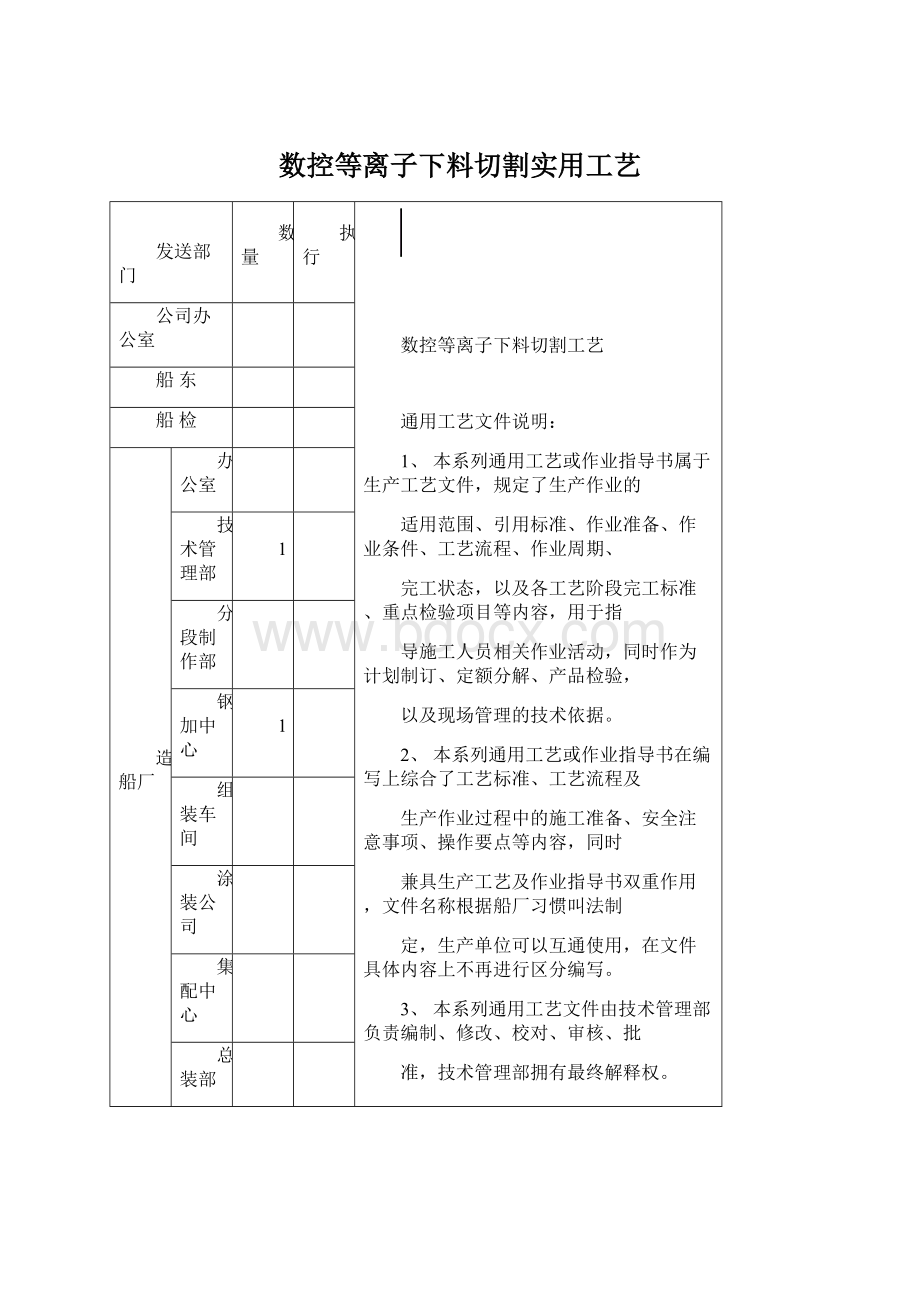
数控等离子下料切割实用工艺
发送部门
数量
执行
数控等离子下料切割工艺
通用工艺文件说明:
1、本系列通用工艺或作业指导书属于生产工艺文件,规定了生产作业的
适用范围、引用标准、作业准备、作业条件、工艺流程、作业周期、
完工状态,以及各工艺阶段完工标准、重点检验项目等内容,用于指
导施工人员相关作业活动,同时作为计划制订、定额分解、产品检验,
以及现场管理的技术依据。
2、本系列通用工艺或作业指导书在编写上综合了工艺标准、工艺流程及
生产作业过程中的施工准备、安全注意事项、操作要点等内容,同时
兼具生产工艺及作业指导书双重作用,文件名称根据船厂习惯叫法制
定,生产单位可以互通使用,在文件具体内容上不再进行区分编写。
3、本系列通用工艺文件由技术管理部负责编制、修改、校对、审核、批
准,技术管理部拥有最终解释权。
公司办公室
船东
船检
造船厂
办公室
技术管理部
1
分段制作部
钢加中心
1
组装车间
涂装公司
集配中心
总装部
建造车间
舾装项目部
机装车间
甲舾车间
管加工中心
电装车间
生产管理部
安防中心
设计所
1
质量保证部
经济计划部
物资供应部
生产保障部
安全保卫部
备注:
标记
修改
审核
批准
日期
项目
签名
日期
船舶建造通用工艺
造船厂技术管理部技术工艺科
编制
版本
0版
校对
共14页
封面
审核
批准
1适用范围………………………………………………………………………………………1
2引用标准………………………………………………………………………………………1
3术语和定义……………………………………………………………………………………1
4施工准备………………………………………………………………………………………1
5人员要求………………………………………………………………………………………1
6安全要求………………………………………………………………………………………2
7设计要求………………………………………………………………………………………2
8工艺要求………………………………………………………………………………………3
9工艺流程………………………………………………………………………………………5
9.1钢板吊运上台………………………………………………………………………………5
9.2核对信息……………………………………………………………………………………5
9.3外观检查……………………………………………………………………………………6
9.4数控切割……………………………………………………………………………………6
9.5号料…………………………………………………………………………………………6
9.6分类码放……………………………………………………………………………………6
9.7完工处理……………………………………………………………………………………7
10标准作业周期…………………………………………………………………………………7
11参考资料………………………………………………………………………………………7
附件1……………………………………………………………………………………………8
1适用范围
本工艺规定了数控等离子切割机开工前的作业准备、人员要求、工艺要求、精度控制方法及自检项目等内容。
本工艺适用于船厂钢板的干式等离子数控下料切割工作,其它数控切割机的钢板切割,以及铝合金板材等材质的数控切割工作也可参照使用。
2引用标准
CB/T4000-2005中国造船质量标准
3术语和定义
等离子弧切割:
利用高温等离子弧的热量使工件切口处的金属局部融化,并借助高速等离子束排除熔融金属以形成切口的一种加工方法;
4施工准备
4.1工具设备
4.1.1盒尺、盘尺等测量工具;
4.1.2撬棍、记号笔等定位、号料工具;
4.1.3手持切割、打磨工具;
4.1.4U盘等数据存储工具。
4.2技术准备
4.2.1根据生产计划,提前向设计所拷贝数切程序,准备数切小样及数切套图,并检查数切小样及数切套图是否一致,如有差别,及时向设计反馈进行确认修改,检查无误后,将数切套图裁减为单板数切小样,分发到号料人员,同时将数切程序拷贝到各数切机;
4.2.2确保数切机安全可靠运行,切割前重点检查数切机精度校验记录表(附件1),确保数切机具有可靠的精度保障;
4.2.3根据生产计划,切割主管人员提前到板材发放处进行登记,并由板材发放人员检查待切割板材准备情况,如有缺漏,立即向上工序反馈,如存在板材代用情况,切割主管必须在钢板预处理后,及时将代用信息书写在钢板上,要求清晰、易见;
4.2.4确保切割平台安全可靠,无废料等杂物,同时保证数切机气压、电源正常可靠。
5人员要求
5.1施工人员应接受过数切机操作、保养培训,并能够熟练使用;
5.2施工人员应熟知本工艺,或在熟知本工艺的人员带领下施工;
5.3施工人员必须持证上岗;
5.4施工人员必须严格遵守工艺纪律和现场安全操作规程。
6安全要求
6.1安全帽、三防鞋、防尘口罩等劳防用品必须穿戴齐全;
6.2切割工作场地周围不得有可燃物品和危险物品;
6.3作业过程中要十分注意防电击防护;
6.4上料及下料过程中远离起重设施,注意防砸及防摔;
6.5切割完毕后要及时切断电源和气源;
6.6必须保证施工人员进行过安全培训。
7设计要求
7.1设计部根据车间工艺要求,配合施工人员定期做出数切样板,适用于每台等离子数控切割机,以便工作人员校验切割机精度。
7.2设计在对数切构件进行放样时,需在构件边缘处增加切割补偿量,坡口切割件按设备规定补偿量进行修正,直口切割件按下表执行:
(所有补偿量均需长期跟踪统计不断修正)
直口切割补偿量参照表
板厚t
喷咀型号
单边切割补偿量
<10mm
220439
1.5mm
≥10mm
220632
2.5mm
7.3数切小样,必须保证每张板材上,至少有一个数切构件有长、宽、对角线等平面尺寸数据,留有数据的数切构件,尽量选择形状规则、尺寸最大的进行标注。
7.4由于数切平台隔板间距100mm,因此对于小于300mm的构件应保持相互连接,防止切割后掉落。
7.5设计人员在做数切预拼图时,应标明距切割起弧点最近的拼板口处具体尺寸,以便现场施工人员对板材进行准确定位。
横向接口定位示意图
纵向接口定位示意图
7.6带有变坡口的构件,在构件坡口改变的切割边处做出100mm标记,保证施工人员切割坡口的准确性。
坡口分界线示意图
7.7为防止切割变形,对于不规则且数量较大的板材时(例如曲形细长类零件),施工人员应在构件之间留连接点,切割完成后切开。
8工艺要求
8.1所有数切机必须定期进行精度校验,同时需要在切割运行过正中,随时进行切割、画线精度检查,做好测量精度记录(附件1)。
位置线偏差
项目
标准范围
允许极限
构件位置线、对合线、检查线
≤2
≤3
切割线及切割尺寸偏差
项目
标准范围
允许极限
备注
长度
±2
±3
宽度
±1.5
±2.5
对角线
±2
±3
曲线外形
±1.5
±2.5
直线度
≤4m
≤1
≤1.2
指零件的直线边缘,按直线长度计算。
>4m,且≤8m
≤1.2
≤1.5
>8m
≤2
≤2.5
坡口及过渡偏差
项目
标准范围
允许极限
备注
坡口面角度θ
±2°
±4°
坡口深度d
±1.5°
±2°
过渡段长度l
±0.5d
±d
按相应船级社规范要求,l可取3d、4d或5d
8.2施工人员必须定期(至少6个月一次)对数切机运行轨道进行直度和平度的检测,以防轨道变形或下沉后对数切机的切割精度造成影响;
8.3施工人员每天必须对数切机进行大方精度校验,具体方法为:
对平台上要切割的板材进行喷粉画线,画出板尺最大矩形,并测量长、宽、对角线尺寸,对照精度要求(见表《切割线及切割尺寸偏差》)调整数据切机,直至满足精度要求为止;
大方检验示意图
8.4施工人员必须在交接班时,首先对数切机进行小方检验,小方检验主要检验切割精度、画线精度、切割与画线匹配精度三个方面,具体方法为:
:
根据切割机划线嘴头横向和纵向坐标尺寸,画300mmX300mm正方形,再切出400mm*400mm方板,然后分别测量矩形板尺寸、画线尺寸,以及切割边距划线边的尺寸。
小方检验示意图
8.5数切过程中,必须时刻观察切割件状态,并且根据数切小样,对每张板件上的标有尺寸的构件进行精度检验,发现问题即使调整。
9工艺流程
工艺流程示意图
9.1钢板吊运上台
起重人员根据车间切割计划,将所需要的钢板吊运至切割平台,要求钢板摆放时,长边基本平行于轨道,两张钢板并排摆放时,利用撬杠使两张钢板尽量紧密帖合,以便在切割过程中增加排尘效果。
为加快作业进度,可以在钢板切割过程中进行另一端钢板吊装摆放工作。
9.2核对信息
钢板切割前,数切人员必须首先核对待切割钢板的材质、规格、尺寸、数量是否与数切程序一致,如发现问题,首先检查钢板上有无代用说明,如无代用说明,必须向切割主管汇报,确认无误后,方可进行切割。
另外,出于船级社对钢板可跟踪要求,数切人员在进行信息核对时,必须将待切割钢板炉号(船级+炉号+钢板号)与数切小样上所标的数切并编号进行对应记录,切割完成后,立即将该记录反馈给信息标注人员,并由信息标注人员将该记录写在数切小样的统一位置,以便后期对钢板进行跟踪。
9.3外观检查
切割人员在核对完信息以后,必须对钢板外观进行检查,重点检查有无麻点板、夹层和夹渣情况,发现问题及时向切割主管反馈。
9.4数控切割
9.4.1在切割过程中,切割人员必须及时清除板材费料,以免在切割时发生变形使板材发生移位,导致构件切割精度产生偏差;
9.4.2带有结构位置线的板材在数切喷粉画线时,若无特殊情况必须一次完成画线工作。
如中途出现停车情况,必须由原点起车直到停车点处再重新开始喷粉画线;
9.4.3切割完毕后,首先应对钢材切割面进行检查,其切割面应无裂纹、夹渣和氧化铁等缺陷,检查方式为外观检查;其次,应该对板件上标有尺寸的零件进行尺寸检查,并将检查结果填写在数切小样上,如发现问题,必须重新校验数切机精度;
9.4.4切割后零件的外观质量应作为常规项目进行检查,如切割后零件的外形尺寸、断面光洁度、槽沟、断口垂直度、坡口角度、钝边高度、局部缺口、毛刺和残留氧化物等缺陷必须消除。
9.5信息标注
9.5.1切割后完成后,信息标注人员根据数切小样,用油漆笔将构件编号、坡口信息、过渡信息、加工信息等所有数切小样上的字符,全部清晰书写到数切零件上,禁止连笔、简写,尤其注意区分“5、S”“2、Z”之类容易混淆的字符书写,书写字符时,禁止使用油漆刷进行书写。
9.5.2信息标注结束后,按照数切小样进行互检,确保零件各种信息清晰准确。
9.5.3对有余料的板材应标清余料号,并注明其余料用途,方便施工人员对余料进行整理,余料上的信息字体应大于零件信息,起到醒目作用,同时必须将钢板炉号(船级+炉号+钢板号)清晰的标在余料及数切小样上。
9.6分类码放
9.6.1施工人员利用磁吊将带有编号的零件按照分段和工序流向(工序流向参见《港船重工零件编码原则》),放到不同的托盘里;
9.6.2切割后的余料单独存放到专门的区域,并区分二次利用余料与非二次利用余料,以便进行区分处理;
9.6.3将切割剩余的废料,用磁吊放到指定的地点,整齐摆放到废料托盘里.过长的废料应进行截短。
9.7完工处理
板材切割工作完毕后,将数切小样以及零件精度检查表交由切割主管进行归档,以利于以后复查,并通知起重人员进行下一轮钢板吊运上台工作。
10标准作业周期
10.1按最小人员投入,每台数控切割机每天安排数切人员1人,号料人员2人,分类码放人员2人,每天每台数控切割机可平均完成钢板切割数量6片。
10.2以上标准作业周期为平均周期,同时必须保证起重上板、下台人员配合充足,对于具体情况还要参考板厚,切割长度等因素影响。
11参考资料
<1>《船舶切割工》
附件1:
数切机精度校验记录表
数切机精度校验记录表
ACCURACYCALIBRATIONOFDIGITALCONTROLCUTTINGMACHINE
数切机编号日期记录单号
MachineNO.Date:
RecordNo.:
项目
类型
标准
极限
实测
记录人
时间
大方
长
±2
±3
宽
±1.5
±2.5
对角线
±2
±3
小方
切割边
±1.5
±2.5
画线边
±1.5
±2.5
边匹配
±1
±1.5
小方
切割边
±1.5
±2.5
画线边
±1.5
±2.5
边匹配
±1
±1.5
小方
切割边
±1.5
±2.5
画线边
±1.5
±2.5
边匹配
±1
±1.5