轴流压缩机制造过程质量验收检验大纲中石化.docx
《轴流压缩机制造过程质量验收检验大纲中石化.docx》由会员分享,可在线阅读,更多相关《轴流压缩机制造过程质量验收检验大纲中石化.docx(11页珍藏版)》请在冰豆网上搜索。
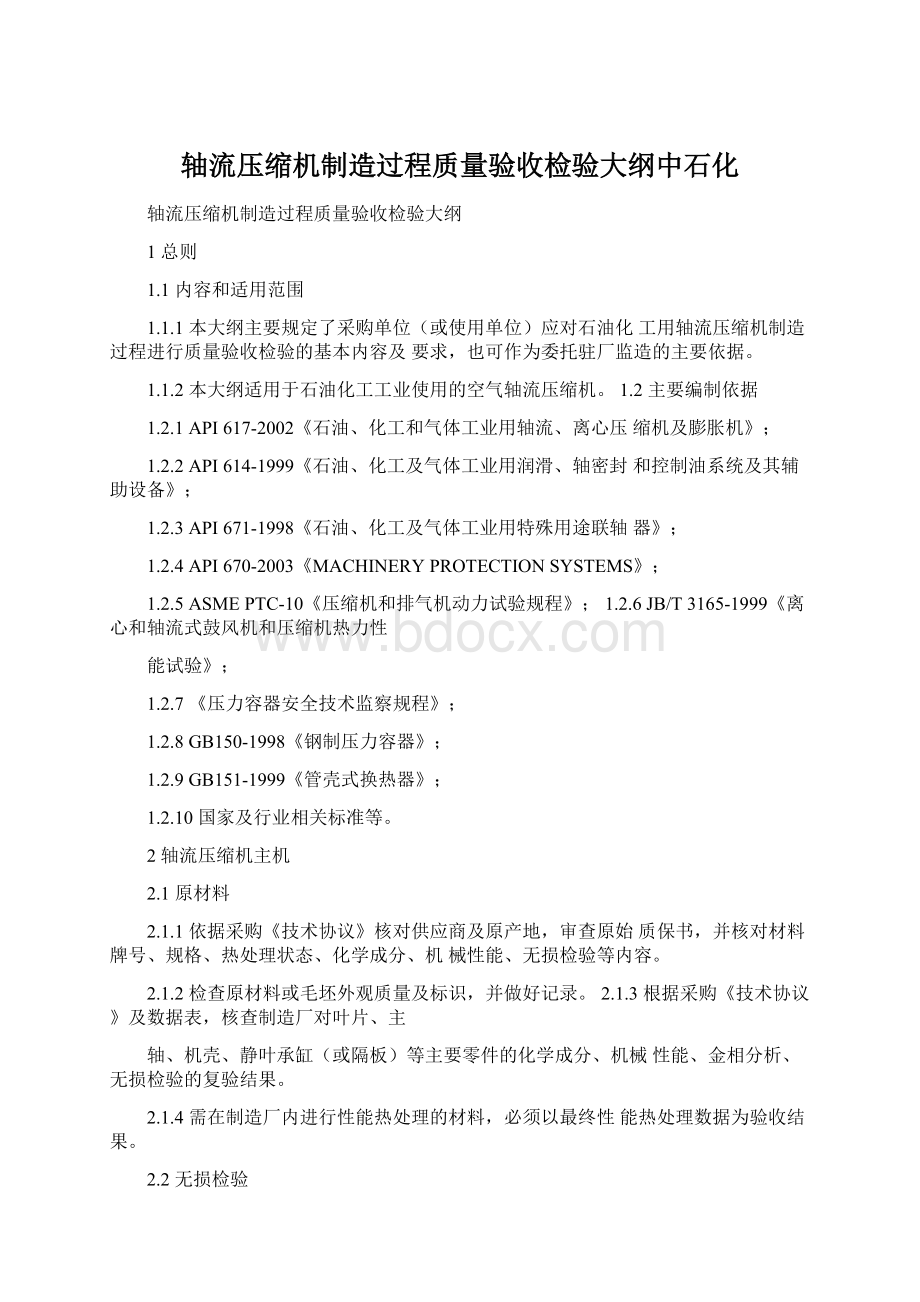
轴流压缩机制造过程质量验收检验大纲中石化
轴流压缩机制造过程质量验收检验大纲
1总则
1.1内容和适用范围
1.1.1本大纲主要规定了采购单位(或使用单位)应对石油化工用轴流压缩机制造过程进行质量验收检验的基本内容及要求,也可作为委托驻厂监造的主要依据。
1.1.2本大纲适用于石油化工工业使用的空气轴流压缩机。
1.2主要编制依据
1.2.1API617-2002《石油、化工和气体工业用轴流、离心压缩机及膨胀机》;
1.2.2API614-1999《石油、化工及气体工业用润滑、轴密封和控制油系统及其辅助设备》;
1.2.3API671-1998《石油、化工及气体工业用特殊用途联轴器》;
1.2.4API670-2003《MACHINERYPROTECTIONSYSTEMS》;
1.2.5ASMEPTC-10《压缩机和排气机动力试验规程》;1.2.6JB/T3165-1999《离心和轴流式鼓风机和压缩机热力性
能试验》;
1.2.7《压力容器安全技术监察规程》;
1.2.8GB150-1998《钢制压力容器》;
1.2.9GB151-1999《管壳式换热器》;
1.2.10国家及行业相关标准等。
2轴流压缩机主机
2.1原材料
2.1.1依据采购《技术协议》核对供应商及原产地,审查原始质保书,并核对材料牌号、规格、热处理状态、化学成分、机械性能、无损检验等内容。
2.1.2检查原材料或毛坯外观质量及标识,并做好记录。
2.1.3根据采购《技术协议》及数据表,核查制造厂对叶片、主
轴、机壳、静叶承缸(或隔板)等主要零件的化学成分、机械性能、金相分析、无损检验的复验结果。
2.1.4需在制造厂内进行性能热处理的材料,必须以最终性能热处理数据为验收结果。
2.2无损检验
2.2.1无损检验验收按采购《技术协议》有关规定。
2.2.2叶片:
2.2.2.1动叶片粗加工后应进行超声波检查;
2.2.2.2动、静叶片精加工后应进行磁粉检查;
2.2.3主轴:
2.2.3.1主轴毛坯粗加工后应进行超声波检查;
2.2.3.2主轴精加工后应进行磁粉检查。
2.2.4机壳
2.2.4.1铸钢机壳毛坯粗加工后应对中分面进行着色检查;2.2.4.2机壳应力集中处应进行磁粉检查;
2.2.4.3机壳上平衡管对接焊缝应进行射线检查。
2.2.5静叶承缸(隔板):
2.2.5.1静叶承缸(隔板)应力集中出应进行磁粉或着色检查。
2.3消应力处理
2.3.1按制造厂工艺规定验收;
2.3.2主轴半精加工后应进行消应力处理,并进行残余应力检查。
主轴的热稳定性试验按JB/T9021-1999规定;
2.3.3焊接隔板焊后应及时进行消应力处理,对于Cr-Mo钢类材料,焊前应进行预热,焊后应及时进行消氢、消应力处理;
2.3.4机壳、静叶承缸粗加工后应进行消应力处理;
2.3.5铸造轴承座清砂后应进行消应力处理;
2.3.6公用底座焊后应进行消应力处理。
2.4几何尺寸
2.4.1按制造厂施工图纸及工艺要求验收;
2.4.2叶根尺寸应逐一进行检查;
2.4.3主轴与联轴器、轴承配合尺寸应进行检查;
2.4.4转子轴向定位才尺寸及跳动应进行检查;
2.4.5机壳、静叶承缸(隔板)水平中分面自由贴合间隙应进行检查。
2.5外观检查
2.5.1叶片、主轴、静叶承缸(隔板)、机壳等应进行有效标识;
2.5.2所有零部件应进行毛刺和清洁度检查,合格后才能转入总装工序。
2.6其它检查
2.6.1转子残磁≤5高斯,机械电跳动量≤6.4μm;
2.6.2动叶片应进行测频,其避开裕度不得小于10%;
2.6.3轴承座应进行煤油渗漏检查。
2.7转子超速试验
2.7.1超速试验转速应不低于最大连续转速的1.05倍,且持续时间不小于1分钟;
2.7.2超速试验后应检查叶片外圆直径的变化,且应符合施工图规定。
2.8转子动平衡试验
2.8.1低速动平衡试验按制造厂施工图及工艺规定;
2.8.2高速动平衡试验应在超速试验后进行,其试验转速应为轴流压缩机的最大连续转速,且振动≤1.0mm/s.
2.9机壳水压试验
2.9.1机壳水压试验可根据压力不同分腔进行,试验压力应为最大设计压力的1.5倍,保压时间≥30min,且无渗漏。
2.10装配检查
2.10.1按施工图纸及制造厂工艺规定验收;
2.10.2进入装配的所有零部件应进行清洁度检查;
2.10.3机壳与静叶承缸(隔板)应进行同心度检查;
2.10.4转子与机壳应进行同心度检查;
2.10.5转子与静止部件应进行间隙检查;
2.10.6转子与径向轴承应进行径向间隙检查,转子与推力轴承应进行轴向间隙检查;转子轴向应进行窜动量检查;
2.10.7导向块应进行装配间隙检查;
2.10.8静叶调节系统应进行静态模拟试验检查。
2.11其它外购件
2.11.1联轴器、轴承、液力偶合器、静叶调节伺服机构等型号、原产地及供应商应与采购《技术协议》规定一致;
2.11.2测温、测振、转速探头等主要监控仪表型号及原产地应与采购《技术协议》规定一致;
2.12机械运转试验
2.12.1试验前应进行一下检查:
2.12.1.1试验润滑油过滤精度应≤10μm;
2.12.1.2压缩机轴承应进行油温度检查;
2.12.1.3测验监测仪表数量基本要求:
测振探头前、后轴径各2个,测温探头前后径向轴承各2个,推力轴承主、辅推力面各2个,轴位移探头1个,转速表1个。
2.12.2运转试验:
2.12.2.1升速速率应为10%最大连续转速;
2.12.2.2最大连续转速稳定运行至少4h;
2.12.2.3转子未过滤波的双振幅≤25.4μm;,轴承温度≤85℃,回油温升≤28℃。
2.12.3试验后应记录压缩机惰走时间和临界转速;
2.12.4试验后应进行压缩机解体检查,转子与轴承、静止部件不允许有异常磨损及摩擦。
2.13气动热力性能试验
2.13.1按采购《技术协议》规定进行;
2.13.2试验介质采用空气;
2.13.3在额定转速下,其额定点流量、额定点压力(或能量头)不允许有负偏差、额定点功率偏差应不大于额定功率的104%。
3辅机
3.1润滑油及动力油系统
3.1.1核对油系统PID图;
3.1.2油箱、高位油箱、油管道、油管道法兰、阀门等主要部件和构件原材料应与采购《技术协议》规定一致;
3.1.3主辅油泵、双联过滤器、油冷却器调节阀及监控仪表等主要外购件供应商、原产地、技术规格应与采购《技术协议》规定一致;
3.1.4油管路焊接应采用对接焊形式,且必须采用氩弧焊打底;
3.1.5油箱、高位油箱、油管路应进行酸洗钝化处理,并进行外观及清洁度检查;
3.1.6动力油站管路应进行压力试验,试验压力为设计压力的1.5倍,保压时间≥15min。
3.2油站运转试验
3.2.1试验用油清洁度应符合相关标准规定;
3.2.2主、辅油泵(如为电机驱动)启动及运转应正常;
3.2.3双联油过滤器、油冷却器手动切换时油压变化应符合相关规定;
3.2.4运转试验1h后,用100目滤网进行检查,无硬质颗粒为清洁度合格。
3.3入口过滤网、消音器、导流栅
3.3.1其供应商、主要原材料、结构型式、技术参数、安装尺寸应与采购《技术协议》及施工图规定一致;
3.3.2承压部件无损探伤比例及验收级别按施工图或采购《技术协议》规定;
4机组总装
4.1压缩机与驱动机载公用底座上应进行冷态预对中,压缩机与驱动机转子的中心线偏差应符合施工图或工艺规定;
4.2公用底座上的机组配管应进行检查,油管路焊接应采用对接焊形式,且必须采用氩弧焊打底;回油总管应沿回油方向水平倾斜。
5涂装与发运
5.1防锈、涂装按采购《技术协议》规定,其中主机涂装质量应确保12个月,备用转子及其它备件涂装质量应确保18个月;
5.2共用接口必须用金属盲板封口,且盲板厚度应为3mm以上;
5.3压缩机转向标识、铭牌应固定在压缩机壳体醒目位置;5.4装箱及出厂文件应进行检查。
6轴流压缩机驻厂监造主要控制点
序
号
零部件
及工序
名称
监造内容
文件见证点(R)
现场见证点(W)
停止
点
(H)
1
主轴
1.化学成分
R
2.机械性能
R
3.无损检验
W
4.热处理
R
5.热稳定性试验
R
6.残余应力测定
R
7.尺寸外观检查
W
、
2
动叶片
1.化学成分
R
2.机械性能
R
3.金相检验
R
4.无损检验
R
W
5.尺寸及外观检查
W
6.测频
R
7.喷涂质量检查
W
3
转子
1.机械电跳量检查
W
2.叶片安装质量检查
W
3.联轴器安装检查
W
4.跳动
W
5.超速试验
H
6.高速动平衡试验
H
4
静叶承
缸
1.化学成分
R
2.机械性能
R
3.水平中分面间隙、螺栓孔对
中检查
W
4.外观尺寸及清洁度检查
W
5
调节缸
1.化学成分
R
2.机械性能
R
3.焊接质量
W
4.外观、尺寸及清洁度检查
W
6
进口圈
扩压器
1.化学成分
R
2.机械性能
R
3.水平中分面间隙检查
W
4.外观、尺寸及清洁度
W
7
静叶片
1.化学成分
R
2.机械性能
R
3.金相检验
R
4.无损检验
R
5.尺寸及外观检查
W
6.喷涂质量
W
8
机壳
1.化学成分
R
2.机械性能
R
3.水平中分面间隙、螺栓孔对
中检查
W
4.无损检验
R
5.水压试验
H
6.外观、尺寸及清洁度检查
W
9
公用底
座
1.焊后消应力处理
R
2.安装尺寸及外观检查
W
10
总装
1.静叶与静叶承缸安装质量检查
R
W
2.静叶转动角度试验
R
W
3.动、静部件找同心、校水平
R
W
4.轴瓦间隙
R
W
5.通流部分间隙测量
R
W
11
机械运
转试验
1.升速
R
H
2.超速试验
R
H
、
、
3.稳定
运行
a.轴承温度
R
H
b.振动
R
H
c.轴位移
R
H
d.噪音
R
H
12
机械运
转后拆
检
1.迷宫密封部位检查
H
2.轴承部位检查
H
13
入口过滤器、
消音器
导流栅
1.供应商核对、结构型式、技
术参数核对
R
2.主要部件材料核对
R
3.安装尺寸
W
14
油系统
1.油冷却器管束、过滤器壳体油管道等原材料检查
R
W
2.清洁度及外观检查
W
3.油过滤器、油冷却器水压试
验
W
4.油箱、高位油箱渗漏检查
W
5.油路系统水压试验
W
6.油管酸洗处理
W
7.油系统运转试验
H
15
其它外
购件
1.联轴器、轴承、齿轮箱、电机等型号、原产地、质保书检查
R
W
2.监控仪表的合格证检查
R
W
16
涂装与
发运
1.涂装检查
W
2.共用接口封闭检查
W
3.转向标识及铭牌检查
W
4.专用工具检查
W
5.装箱及出厂文件检查
R
W
7附则
7.1本大纲由中国石油化工集团公司物资装备部组织编写,上海众深设备科技有限公司负责起草。
7.2本大纲有中国石油化工集团公司物质装备部负责解释。