深孔钻镗床床设计实习报告.docx
《深孔钻镗床床设计实习报告.docx》由会员分享,可在线阅读,更多相关《深孔钻镗床床设计实习报告.docx(14页珍藏版)》请在冰豆网上搜索。
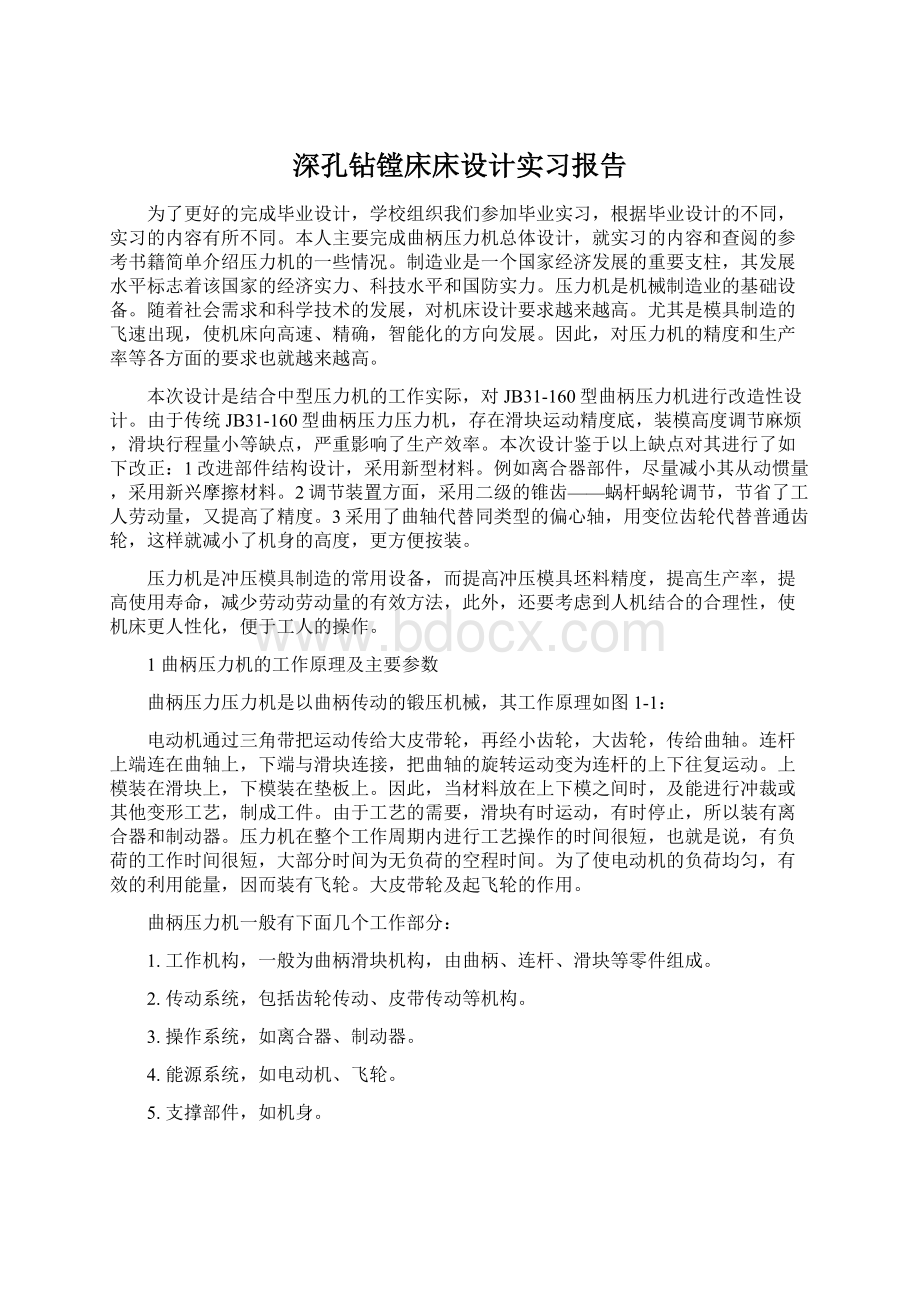
深孔钻镗床床设计实习报告
为了更好的完成毕业设计,学校组织我们参加毕业实习,根据毕业设计的不同,实习的内容有所不同。
本人主要完成曲柄压力机总体设计,就实习的内容和查阅的参考书籍简单介绍压力机的一些情况。
制造业是一个国家经济发展的重要支柱,其发展水平标志着该国家的经济实力、科技水平和国防实力。
压力机是机械制造业的基础设备。
随着社会需求和科学技术的发展,对机床设计要求越来越高。
尤其是模具制造的飞速出现,使机床向高速、精确,智能化的方向发展。
因此,对压力机的精度和生产率等各方面的要求也就越来越高。
本次设计是结合中型压力机的工作实际,对JB31-160型曲柄压力机进行改造性设计。
由于传统JB31-160型曲柄压力压力机,存在滑块运动精度底,装模高度调节麻烦,滑块行程量小等缺点,严重影响了生产效率。
本次设计鉴于以上缺点对其进行了如下改正:
1改进部件结构设计,采用新型材料。
例如离合器部件,尽量减小其从动惯量,采用新兴摩擦材料。
2调节装置方面,采用二级的锥齿——蜗杆蜗轮调节,节省了工人劳动量,又提高了精度。
3采用了曲轴代替同类型的偏心轴,用变位齿轮代替普通齿轮,这样就减小了机身的高度,更方便按装。
压力机是冲压模具制造的常用设备,而提高冲压模具坯料精度,提高生产率,提高使用寿命,减少劳动劳动量的有效方法,此外,还要考虑到人机结合的合理性,使机床更人性化,便于工人的操作。
1曲柄压力机的工作原理及主要参数
曲柄压力压力机是以曲柄传动的锻压机械,其工作原理如图1-1:
电动机通过三角带把运动传给大皮带轮,再经小齿轮,大齿轮,传给曲轴。
连杆上端连在曲轴上,下端与滑块连接,把曲轴的旋转运动变为连杆的上下往复运动。
上模装在滑块上,下模装在垫板上。
因此,当材料放在上下模之间时,及能进行冲裁或其他变形工艺,制成工件。
由于工艺的需要,滑块有时运动,有时停止,所以装有离合器和制动器。
压力机在整个工作周期内进行工艺操作的时间很短,也就是说,有负荷的工作时间很短,大部分时间为无负荷的空程时间。
为了使电动机的负荷均匀,有效的利用能量,因而装有飞轮。
大皮带轮及起飞轮的作用。
曲柄压力机一般有下面几个工作部分:
1.工作机构,一般为曲柄滑块机构,由曲柄、连杆、滑块等零件组成。
2.传动系统,包括齿轮传动、皮带传动等机构。
3.操作系统,如离合器、制动器。
4.能源系统,如电动机、飞轮。
5.支撑部件,如机身。
图1-1曲柄压力机传动示意图
上述除了的基本部分以外,还有多种辅助系统与装置,如润滑系统、保护装置以及气垫等。
曲柄压力机的主要参数和型号
一、曲柄压力机的主要参数
1.公称压力:
160吨
2.滑块行程:
200毫米
3.滑块每分次数:
32
4.最大装模高度:
450毫米
5.装模高度调节量:
200毫米
6.导轨间距离:
880毫米
7.滑块底面尺寸:
700毫米
8.工作台尺寸:
800毫米
二、曲柄压力机的型号
JA31—160型
J—机械压力机(第一类锻压机)
A—次要参数与基本型号不同的第一变型
3—第三列
闭式单点压力机
1—第一组
160—公称压力(×10千牛)
2电动机和飞轮的设计
一、封闭高度调节装置电动机功率的计算方法
在稳定负载下,电动机在单位时间内所做的有用功,除以传动系统的效率,便是电动机所需的功率。
写成公式为:
(千牛)(10-1)
式中N—电动机所需的功率(千瓦)
N‘—电动机每分钟所做的有用功;
η—传动系统的机械效率;
上式中102是单位换算常数,表示功率1千瓦相当102公斤·米/秒。
1.电动机通过传动系统提升滑块时,每秒中内所做的有用功为:
N‘=Gv(10-2)
式中G—滑块部件重量
v—滑块的调节速度(米/秒)
二、封闭高度调节装置传动系统的机械效率
传动系统的机械效率主要包括:
(1)导轨与滑块相对滑动的效率η1。
(2)调节螺杆传动效率η2。
(3)调节螺母与套筒端面之间相对滑动的效率η3。
(4)皮带、齿轮传动效率η4。
除了以上几方面的摩擦损失之外,轴承处还有摩擦损失,但因调节装置多采用滚动轴承,效率较高,所以可忽律。
因此,封闭高度调节装置传动系统的机械效率为:
(10-3)
多数曲柄压力机封闭高度调节装置传动系统的机械效率在0.02~0.03之间。
2.电动机功率计算
将式(10-2)代入式(10-1)中,得:
(10-4)
调节电动机可采用一般封闭式鼠笼型电动机。
电动机的同步转速根据传动级数和传动类型而定,在实际生产过程中,为了减少曲轴压力机的零件品种和规格,实现部件通用化,常常将吨位接近的曲柄压力机采用相同的调节电动机,传动系统的某些零件亦相互通用。
2.2主电动机的功率和飞轮的计算原理
一、曲柄压力机主传动为什么采用飞轮
在曲柄压力机的工作过程中,由于冲压时所需要的能量很大,而作用时间却很短,如果按冲压时所需的功率选取电动机,则所要求的电动机的功率很大。
但压力机的冲压过程很短,必然造成浪费,为了解决这一矛盾,所以在传动系统中加上一个飞轮,滑块不工作时,电动机带动飞轮旋转,使它储存能量,而在冲压工件是的短暂时间里,主要靠飞轮降低转速释放能量,所释放的能量为:
(公斤·米)
式中J—飞轮转动惯量;
ω1—冲压工件开始是飞轮的角速度;
ω2—冲压工件后飞轮的角速度。
飞轮释放能量后,角速度由ω1降到ω2,但这时工件已冲压完毕,飞轮的负载减小,于是电动机带动飞轮加速旋转,使它在冲压下一个工件前恢复到原来的角速度ω1。
采用飞轮后,冲压工件时所需的大部分能量不直接由电动机提供,所以,电动机的功率大大减小。
凡是具有短期的高峰负载和较长期空载相互交替特点的机械,一般都采用飞轮;负载均匀的机械没有必要采用飞轮。
二、曲柄压力机主传动电动机和飞轮的计算原理
1.电动机功率计算原理
曲柄压力机传动系统中装有飞轮之后,电动机的负载平稳许多,但仍是有变化的,所以确定电动机的功率也要注意一些问题,通常如下确定电动机:
(1)电动机的过载条件。
冲压工件时电动机扭矩上升,如果超过它的最大容许扭矩,电动机就可能停下,着就是过载条件的限制。
(2)电动机发热条件。
冲压工件时电动机的负载增加,电流上升,电动机的损耗变为热能,使其温度上升,冲压过后,负载变小,相应的转化为热能的耗损也减小。
电动机运行一段时间后,电动机的温度达到一稳定状态。
电动机的温升应在允许的范围之内,否则,电动机就会损坏,这是工作时发热条件的限制。
此外,有由于曲柄压力机有较大的飞轮,加速飞轮使其达到额定转速,需要一定的功率,如电动机的额定功率不足,就会引起电动机的启动电流过大和启动时间过长,使电动机温升过高而损坏,所以还应核算启动时间,视其是否在允许范围之内。
这就是启动时发热条件的限制。
在通常情况下,冲压作用时间很短,短时过载还不致使电动机停下来,因此,一般按工作时发热条件来解决电动机功率。
曲柄压力机主传动电动机的负载虽然是不均匀的,但是从发热条件来看,可以折合成某一恒定的功率N,如果所选用的电动机的额定功率大于或等于N,那么从发热条件看是能够满足要求的。
因此带飞轮传动的电动机功率计算,归结为如何确定折合功率N。
当电动机的负载波动较小,飞轮的能量较大时,这时折合功率N,接近于压力机一个周期的平均功率Nm。
当电动机的负载波动较大,飞轮的能量较小时,这时的折合功率N与平均功率Nm差距较大。
折合功率N与平均功率Nm的关系可用下式表示:
式中K—折合功率N与平均功率Nm的比值,K>1。
平均功率Nm为压力机一个工作周期内,电动机所做的功初以工作周期的时间;在此期间压力机所消耗的能量就等于电动机所做的功。
式中E—一个工作周期内压力机所消耗的能量(公斤·米);
E‘—工作行程时消耗的能量;
E‘‘—非工作行程时消耗的能量;
t—一个工作周期的时间。
因此,
(千瓦)
K的数值随压力机的具体情况而定,一般K在1.15~1.6范围内。
2.飞轮计算原理
曲柄压力机工作行程时所需的能量,主要靠飞轮降低转速释放能量来供给,如果这时忽略电动机所输出的能量,那么所设计的飞轮必须满足以下关系:
式中E‘—工作行程是消耗的能量。
3.电动机启动时间的核算
电动机的功率应满足启动时发热时发热条件的要求,通常需核算启动时间,视其是否小于允许值。
电动机启动时tg用下式计算:
(秒)
式中J—飞轮的转动半径
λg-电动机启动力矩与额定力矩之比;
Ne—电动机额定功率(千瓦);
ne—电动机额定转速(转/分);
i---电动机轴到飞轮轴的传动比。
对于鼠笼式电动机,允许启动时间为15秒;对于对于高速转速差率电动机,允许启动时间为20秒。
当电动机功率和飞轮的转动惯量确定之后,可根据压力机传动系统的布置情况来拟定飞轮结构尺寸。
飞轮最大直径D2要受轮缘线速度的限制:
ν=πD2ne/60i≤[v](米/秒)
飞轮的材料为铸铁时,
=40(米/秒)。
综合以上内容,曲柄压力机主传动电动机功率和飞轮尺寸的计算方法大致如下:
(1)确定压力机一个工作周期的时间t和所消耗的能量E。
(2)计算平均功率
。
(3)选择电动机类型,并拟定K值和折合功率N=KNn。
(4)查电动机手册,选出额定功率Ne与N接近的电动机,重新算出K值(
);并查出。
(5)计算不均匀系数
。
(6)计算飞轮应具有的能量
。
(7)核算电动机的启动时间。
(8)根据压力机的布置情况和飞轮应具有的动能来拟定飞轮的尺寸。
3带传动的介绍
一、皮带传动工作原理
曲柄压力机上的皮带传动,它由小皮带轮、三角带、大皮带、(即飞轮)和电动机滑等组成,是传动系统的第一级,工作时,电动机的转速通过皮带的传递进行减速并将动力传递给齿轮,使齿轮带动曲柄连杆滑块完成冲压工作。
皮带传动为什么可以起到所说的作用呢?
这是电动机安装在滑轨上,小皮带轮喝大皮带轮之间的距离可以调节,因而可使皮带紧紧压在皮带轮上,当电动机启动时,主动皮带轮旋转,它通过皮带喝皮带轮之间的摩擦传递动力,同时,又通过皮带使从动轮转动。
如果忽略皮带与皮带轮之间的滑动,那么,皮带与皮带轮接触面上任何一点的线速度是相等的,它的数值是:
(米/秒)
式中
-主动轮和从动轮的转速;
,
-主动轮和从动轮的计算直径。
所以
即:
传动比
由上式可知,经过皮带传动不仅可以传递动力,而且可以改变转速。
皮带传动喝齿轮传动都可以传递动力和运动,但齿轮传动是靠牙齿啮合来进行工作的,而皮带传动是靠摩擦进行工作的。
因此,在分析皮带传动工作原理的时候,必须紧紧抓住这个特殊性,并注意以下两个问题:
1.弹性滑动
皮带张紧在皮带轮上,当不传递动力时,皮带上下两边的拉力相等,都等于so,这个力称为出拉力;当传递动力时,由于皮带与皮带轮之间的摩擦的作用,皮带两边的拉力发生了变化,皮带在进入主传动时一边蓓拉的更紧,拉力由so增加到s1皮带在离开主动轮的一边有所放松,拉力由s1减小到s2,拉力大的一边叫紧边,拉力小的一边叫松边。
力s1,s2喝从动轮所需传递的扭矩M2,功率N有以下关系:
两式中
,
-皮带紧边和松边的拉力;
-皮带的速度(米/秒)
102-由公斤•米/秒化成千瓦的折算数
从上述两式可以看出,为了M2,紧边和松边必须存在拉力差s1-s2,差值称为有效拉力。
我们知道,皮带有弹性,在紧边和松边不同的拉力作用下,必然引起不同的伸长量,当皮带从紧边绕过皮带轮到松边的过程中,皮带渐渐缩短,当皮带从松边到紧边的过程中,皮带渐渐伸长。
皮带在皮带轮上的微量伸缩,造成皮带和皮带轮的少量局部滑动,此滑动称为弹性滑动,是皮带传动中不可避免的现象。
显然,由于弹性滑动的存在,皮带速度必然低于主动轮上的圆周速度,所以从动轮的实际转速n2’小于式(4—2)算得的理论值n2.同时,由于弹性滑动量是随所传递的圆周力P的变化而变化的,而实际生产中,外载荷难免会有变化,因此P是不断变化的,这也造成弹性滑动量的变化,并引起从动轮的实际转速n2’不仅小于理论转速,且不稳定,造成传动比I的不稳定。
1.打滑
由式(4-3)和(4-4)可知,随着外载荷的增加,有效力P和弹性滑动也跟着增加。
当传递外载荷所需的有效圆周力P增大到超过某一极限值时,滑动量迅速增加,皮带喝皮带轮之间发生全滑动,皮带传动失效,这种现像称为打滑。
打滑时,皮带发热,磨损严重,这是正常工作所不允许的,为了克服打滑,必须增大皮带与皮带轮之间的摩擦力。
增加出拉力s0和包角а都能使摩擦力增大。
然而,对于每种截面型号的皮带,s0是有一定的推荐值的,s0不能过大,否则会降低皮带的使用寿命,使轴和轴承的受力情况变坏,包角也不可能增加太多,因为它受大、小皮带轮直径和中心矩等结构的的限制。
当长的时间以后,还会出现疲劳破坏,即开始时局部地方皮带运转相的线与胶脱离,造成松散现象,然后使皮带诼渐失去工作能力,甚至在松散处断开,此时必须更换新皮带。
从以上介绍可知,皮带传动结构简单,制造和维护比较容易,可以在距离较远的两轴之间传递运动和动力,能够缓和冲击喝振动,超载时又能自动打滑,可以保护其他的零件不受损坏,因此获得了广泛的应用。
但是,因为它的传动比不稳定,所以在要求严格保持传动比的地方不能采用皮带传动。
4齿轮和轴的确定
一、齿轮的介绍
由于齿轮传动能传递较大的扭矩,又具有结构紧凑、工作可靠和寿命较长等优点,因此齿轮得到了广泛的应用,齿轮传动一般会遇到:
齿面磨损、牙齿折断、倒牙、齿面麻点和振动、噪音等。
根据这些情况,对于曲柄压力机的齿轮传动提出下面两点基本要求:
1.足够的承载能力。
要尽可能缩小齿轮的尺寸,采用常用的材料,又要保证能承受外载荷的作用,并且有足够的寿命。
2.必要的传动平稳性。
齿轮在传动过程中产生的噪音和振动要在允许范围之内,不能过大。
齿轮在应用的过程中对精度有下面的要求:
1.运动精度
为了准确的传递运动,要求主动齿轮转过一个角度,从动齿轮按传动比关系准确的转过相应的角度,但由于制造的误差,使从动齿轮不能按传动比关系准确地转过相应的角度。
但为了满足使用要求,规定齿轮一转的过程中回转角误差绝对值的最大值不超过一定限度。
2.工作平稳性精度
为了减小齿轮传动的躁声和振动,必须将齿轮在一转中的瞬时传动比的变化限制在一定的范围之内,也就是要求齿轮每转中回转角误差多次反复变化的数值小。
3.接触精度
在齿轮的使用过程中要使齿轮的齿面有足够的接触面积,不可是齿轮局部接触。
4.齿侧间隙
互相啮合的一对牙齿,在非工作面沿齿廓法线方向留有一定的间隙Cn,这是为了避免安装、制造不准确,以及工作时温度变化和弹性变化而造成牙齿卡住,同时还可以利用它储存润滑油,改善齿面的摩擦条件。
总之,为了保证齿轮传动有良好的性能,必须对齿轮的运动精度、工作平稳性、接触精度和齿轮侧隙有一定的要求,但这,四方面的要求也不能够平均对待,具体工作条件不同,每个方面的要求也不一样。
5离合器的确定
曲柄压力机上的离合器的形式很多,按工作情况分干式和湿式两种。
干式离合器和制动器的摩擦面露在空气中,而湿式离合器则放在油里。
按其摩擦面的形状,又可有圆盘式,浮点式和圆锥式等型式。
目前常用的是圆盘式摩擦离合器—制动器。
气动圆盘式离合器—制动器,左端是离合器,右端是制动器,他们之间用推杆刚性连锁。
离合器的主要部分包括大皮带轮,离合器内尺圈,主动摩擦片,汽缸,活塞和推杆等。
从动部分包括带小齿轮的传动轴,从动摩片,离合器外尺圈,以及制动器外尺圈和摩擦片等。
接合件是主动摩擦片和从动摩擦片。
操作系统由汽缸,活塞和压缩空气控制系统等组成。
它的工作过程如下:
电磁空气分配阀通电开启后,压缩空气进入离合器汽缸,向右推动活塞,推杆向右移动,压缩制动弹簧,于是制动器松开,离合器主、从动摩擦片压紧,大皮带轮便可带动从动轴转动;电磁空气分配阀断电后,离合器气缸与大气相同,在制动弹簧作用下,推杆推动活塞向左移动,离合器脱开,制动器的摩擦片被压紧,产生制动作用,从而迫使从动部分停止运动。
这种离合器-制动器的从动摩擦片。
使用铜基粉末冶金材料。
离合器或制动器脱开时,摩擦面之间的间隙为0.5毫米左右。
摩擦材料过渡摩损后,需要从新调整间隙。
调整时,只要松开右端制动器上的锁紧螺钉和圆螺母,扳动螺旋,即可调整间隙。
6机身的介绍
机身是曲柄压力机的一个重要部件,工作机构和传动系统等都安装在它的上面,压力机工作时,承受工作载荷。
在整台机器中机身的重量及加工量都很大。
以闭式压力机为例,机身约为压力机总重量的40~60%,加工量约为压力机总加工量的30%。
因此,机身对于压力机的使用性能、生产工件的质量、机器的重量和加工量都有较大的影响。
机身的结构随压力机的用途和传动类型而定。
按机身的外型特点,可分为开式和闭式两类,中型和大型压力机广泛采用闭式机身,闭式机身可分做成整体式和组合式。
公称压力大于160吨的压力机,由于采用整体机身时加工和运输不方便,多采用组合机身。
图6-1如下:
图6-1组合机身
组合机身由上梁,左右立柱和工作台四大件,以及将此四大件连成一体的四根拉紧螺栓组成。
为了防止四大件的相对错位,保证精确定位,在各个接合面的左右和前后方向都设置了圆形和长方形定位销。
拉紧螺栓一般穿过上横梁,但有些压力机为了缩小拉紧螺栓的长度,拉紧螺栓不穿过上横梁,而靠四个螺母卡在横梁里面,并从横梁的专用窗来进行安装。
刚度对机身的压力机都很重要,压力机在工作过程中,因受载荷使机身发生弹性形变。
机身所受载荷与其弹性变形量的比值,成为机身刚度,它表明机身的抗变形能力。
压力机受载荷时不仅机身有弹性变形,曲柄滑块机构也有弹性变形,这些部件弹性变形的结果,使压力机的封闭高度增加,滑块所受载荷与封闭高度增加量的比值,称为压力机刚度,它表示压力机抗变形能力,用下式表示:
(吨/毫米)
式中P-压力机滑块所承受的载荷(吨);
-压力机总弹性变形(毫米)。
压力机的刚度直接影响模具的寿命、工件的质量和机器的能量消耗。
闭式板料冲压机滑块的许用挠度[fk],数值与滑块的宽度成正比,即:
B(毫米)
式中B-为滑块宽度(毫米)。
闭式压力机工作台的许用挠度[ft],其数值与工作台的跨度成正比,即:
L(毫米)
式中L-工作台跨度。
提高机身刚度的办法有:
1.采用高弹性模数的材料。
2.改变机身结构。
如在开式机身上装设拉杆或采用闭式组合机身。
强度也要着重计算;
7传动系统布置及设计
一、传动系统的布置方式
传动系统的作用是把电动机的能量传给曲轴滑块机构,并对电动机的转速进行减速,使滑块获得所需的行程次数。
曲柄压力机的传动系统有三个比较突出的问题需在设计之前加以分析和确定,以便使整个压力机能达到结构紧凑,维修方便,性能良好和外型美观。
传动系统的布置方式包括三方面:
1)采用上传动,还是采用下传动?
2)主轴和传动轴垂直与压力机正面,还是平行与正面?
3)齿轮放在压力机机身之内,还是压力机之外?
单边驱动还是双边驱动?
分述如下:
1.压力机的传动系统可至于工作台之上,也可至于工作台之下。
前者叫上传动,后者叫下传动。
下传动的优点是:
(1)压力机的重心低,运动平稳,能减少振动和躁声,劳动条件好;
(2)压力机地面高度较小,易于高度较矮的厂房;
(3)从结构上看,有增加滑块高度和导轨长度的可能性,因而能提高滑块的运动精度,延长模具的寿命,改善工件的质量;
(4)由于拉杆承受工作变形力,故机身的立柱和上梁的受力情况得到改善。
下传动的缺点是:
(1)压力机平面尺寸较大,而总高度和传动相差不多,故压力机总重量比上传动的约大10~20%,造价也较高。
(2)传动系统置于地坑之中,检修传动不见时,不便于使用车间的桥式吊车。
拉延垫夹在传动不见和底坐之间,维修不方便,且地坑深,基础较大,造价也高。
因此是否采用下传动结构,需经全面的技术经济比较之后才能确定。
现有的通用压力机采用上下传动较多,下传动较少。
通常认为在旧车间内添置大型压力机时,由于车间高度受到限制,采用下传动的优点才比较明显。
2.压力机传动系统的安放形式有垂直于压力机正面的也有平行于压力机正面的,旧式通用压力机多采用平行于压力机正面的安放形式。
这种布置,曲轴和传动轴比较长,受力点与支撑轴承的距离比较大,受力条件恶化。
压力机平面尺寸较大,外形不够美观,近代大中型通用压力机愈来愈多地采用垂直于压力机正面的安放形式,(特别是广泛采用偏心齿轮结构之后),甚至有些小型开式压力机也改用这种结构。
3.齿轮可以放在机身之外,也可以放在机身之内,前一种形式,齿轮工作条件差,机器外形不美观,但安装维修方便;后一种形式,齿轮工作条件好,外形较美观。
如将齿轮侵入油池中,则大大降低齿轮传动的噪音。
但安装维修较困难。
近年来,许多压力机制造厂家倾向后一种形式。
齿轮传动也可设计成单边传动或双边传动,采用后一种形式,可以缩小小齿轮的尺寸,但加工装配比较困难(两边的齿轮必须精确加工,装配时要保证对称,否则可能发生运动不同步的情形)。
二、传动级数和各级速比分配
压力机的传动级数与电动机的转速和滑块没分钟的行程次数有关。
行程次数有关。
行程次数低,总速比大,传动级数应多些,否则每级的速比过大,结构不紧凑;行程次数高时,总速比小,传动级数可少些。
现有压力机传动系统的级数一般不超过四级。
行程次数在70次/分以上的用单级传动,70~30次/分的用两级传动,30~10次/分的用三级传动,10次/分以下的采用四级传动。
采用低速电动机可以减少总速比和传动级数,但,着类电动机的外形尺寸较大,成本较高(与同功率的高速电动机比较),因此,不一定合适。
通常,两级或两级以上的传动系统采用同步转速为1500或1000转/分的电动机,单级传动系统一般采用1000转/分的电动机,行程次数小于80次/分的单级传动才采用750转/分的电动机。
各传动级数的速比分配恰当。
通常三角带传动的速比不超过6~8,齿轮传动不超过7~9。
速比分配时,要保证飞轮有适当的转速,也要注意布置的尽可能紧凑,美观和长,短,高尺寸比例恰当。
通用压力机的飞轮的转速常取300~400转/分,左右,因为转速太低,会使飞轮的作用大大削弱;转速太高,会使飞轮轴上的离合器发热严重,造成离合器和轴承的损坏。
三、确定离合器和制动器的安装位置
单级传动压力机的离合器和制动器只能至于曲轴上。
采用刚性离合器的压力机,离合器应至于曲柄上,这是因为刚性离合器不宜在高速下工作,而曲轴的转速较底,故离合器置于曲轴上比较合适。
在此情况下,制动器必然也置于曲轴上。
采用磨察离合器时,对于具有两级和两级以上传动的压力机,离合器可至于转速较低的曲轴上,也可置于中间传动轴上。
从压力机能量消耗来看,当磨察离合器安装在低速轴上时,加速压力机从动部分所需要的功和离合器接合时所消耗的磨察功都比较小,因而能量消耗也较少。
从离合工作条件来看,低速轴上的离合器的磨察系数较小,故离合器工作条件较好。
但是低速轴上的离合器需要传递较大的扭距,因而结构尺寸较大。
此外,从传动系统的布置来看,闭式通用压力机的传动系统今年来多封闭在机身之内,并用偏心齿轮,致使离合器不变安装在曲轴上,通常只好置于转速较高的传动轴上。
因此,摩擦离合器的合适位置应视机械的具体情况而定。
一般来说,行程次数较高的压力机(如热模锻压力机)离合器最好安装在曲轴上,因为这样可以利用大齿轮的飞轮作用,能量损失小,离合器的工作条件也较好,行程次数较低的压力机(如中