PLC自动配料运输机系统设计.docx
《PLC自动配料运输机系统设计.docx》由会员分享,可在线阅读,更多相关《PLC自动配料运输机系统设计.docx(16页珍藏版)》请在冰豆网上搜索。
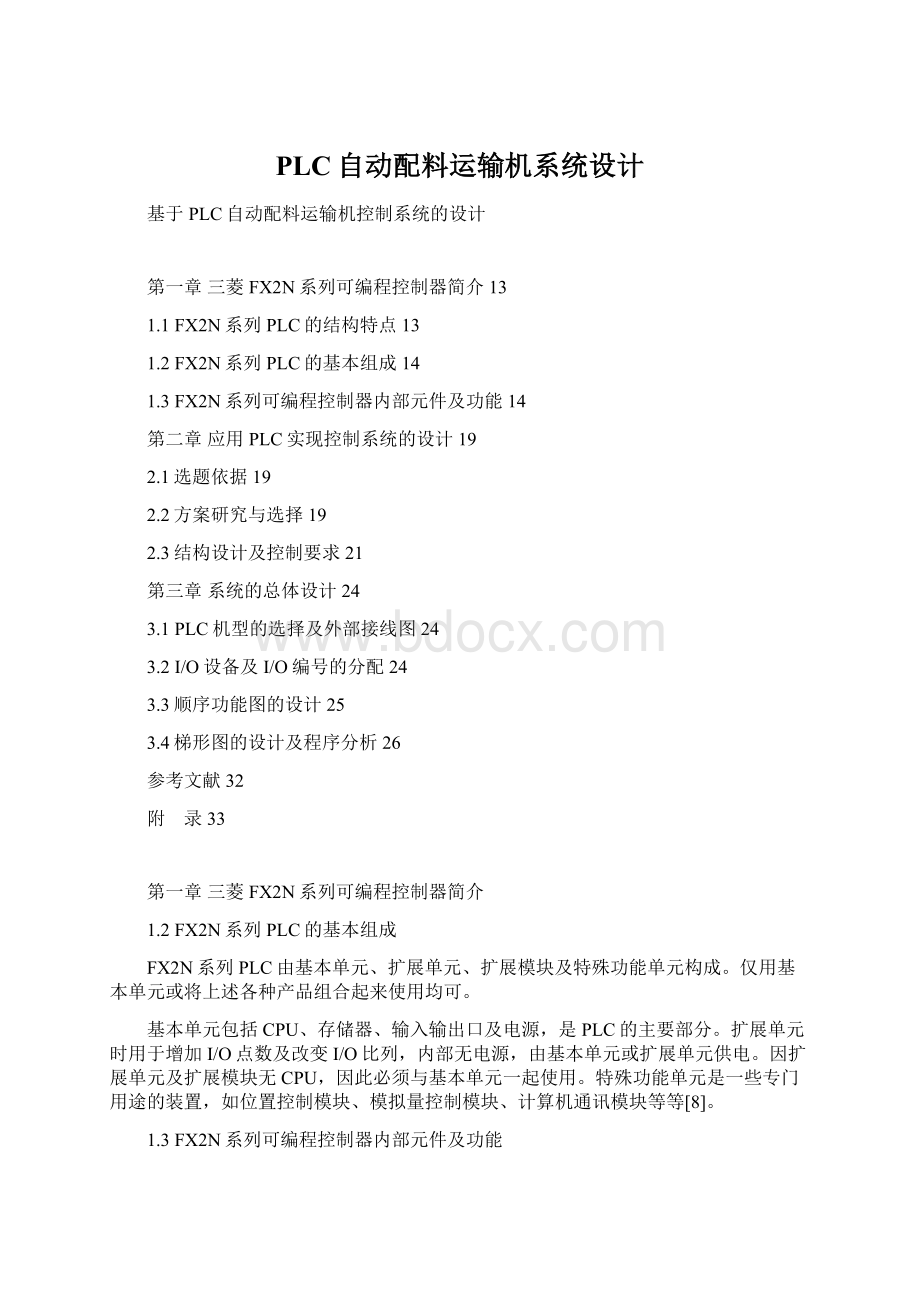
PLC自动配料运输机系统设计
基于PLC自动配料运输机控制系统的设计
第一章三菱FX2N系列可编程控制器简介13
1.1FX2N系列PLC的结构特点13
1.2FX2N系列PLC的基本组成14
1.3FX2N系列可编程控制器内部元件及功能14
第二章应用PLC实现控制系统的设计19
2.1选题依据19
2.2方案研究与选择19
2.3结构设计及控制要求21
第三章系统的总体设计24
3.1PLC机型的选择及外部接线图24
3.2I/O设备及I/O编号的分配24
3.3顺序功能图的设计25
3.4梯形图的设计及程序分析26
参考文献32
附 录33
第一章三菱FX2N系列可编程控制器简介
1.2FX2N系列PLC的基本组成
FX2N系列PLC由基本单元、扩展单元、扩展模块及特殊功能单元构成。
仅用基本单元或将上述各种产品组合起来使用均可。
基本单元包括CPU、存储器、输入输出口及电源,是PLC的主要部分。
扩展单元时用于增加I/O点数及改变I/O比列,内部无电源,由基本单元或扩展单元供电。
因扩展单元及扩展模块无CPU,因此必须与基本单元一起使用。
特殊功能单元是一些专门用途的装置,如位置控制模块、模拟量控制模块、计算机通讯模块等等[8]。
1.3FX2N系列可编程控制器内部元件及功能
FX系列产品,它内部的编程元件,也就是支持该机型编程语言的软元件,按通俗叫法分别称为继电器、定时器、计数器等,但它们与真实元件有很大的差别,一般称它们为“软继电器”。
这些编程用的继电器,它的工作线圈没有工作电压等级、功耗大小和电磁惯性等问题;触点没有数量限制、没有机械磨损和电蚀等问题。
它在不同的指令操作下,其工作状态可以无记忆,也可以有记忆,还可以作脉冲数字元件使用。
一般情况下,X代表输入继电器,Y代表输出继电器,M代表辅助继电器,SPM代表专用辅助继电器,T代表定时器,C代表计数器,S代表状态继电器,D代表数据寄存器,MOV代表传输等。
1.输入继电器(X)
PLC的输入端子是从外部开关接受信号的窗口,PLC内部与输入端子连接的输入继电器X是用光电隔离的电子继电器,它们的编号与接线端子编号一致(按八进制输入),线圈的吸合或释放只取决于PLC外部触点的状态。
内部有常开/常闭两种触点供编程时随时使用,且使用次数不限。
输入电路的时间常数一般小于10ms。
各基本单元都是八进制输入的地址,输入为X000~X007,X010~X017,X020~X027。
它们一般位于机器的上端。
2.输出继电器(Y)
PLC的输出端子是向外部负载输出信号的窗口。
输出继电器的线圈由程序控制,输出继电器的外部输出主触点接到PLC的输出端子上供外部负载使用,其余常开/常闭触点供内部程序使用。
输出继电器的电子常开/常闭触点使用次数不限。
输出电路的时间常数是固定的。
各基本单元都是八进制输出,输出为Y000~Y007,Y010~Y017,Y020~Y027。
它们一般位于机器的下端。
3.辅助继电器(M)
PLC内有很多的辅助继电器,其线圈与输出继电器一样,由PLC内各软元件的触点驱动。
辅助继电器也称中间继电器,它没有向外的任何联系,只供内部编程使用。
它的电子常开/常闭触点使用次数不受限制。
但是,这些触点不能直接驱动外部负载,外部负载的驱动必须通过输出继电器来实现。
如下图2-1中的M300,它只起到一个自锁的功能。
在FX2N中普遍途采用M0~M499,共500点辅助继电器,其地址号按十进制编号。
辅助继电器中还有一些特殊的辅助继电器,如掉电继电器、保持继电器等,在这里就不一一介绍了。
图2-1断电保持功能
4.状态器(S)
状态器S与步进梯形图指令STL一起使用,用于顺序控制的程序编程。
当不对S使用STL指令时,其作用相当于普通辅助继电器M。
无断电保持功能的通用状态器为S0~499,共500点。
其中,S0~S9用于顺序功能图的初始状态;S10~S19用于自动回原点程序的顺序功能图;S20~S499为通用状态器。
有断电保持功能的通用状态器为S500~S899,共400点。
状态器S900~S999用于外部故障诊断的输出(又称为报警器)。
5.定时器(T)
在PLC内的定时器是根据时钟脉冲的累积形式,当所计时间达到设定值时,其输出触点动作,时钟脉冲有1ms、10ms、100ms。
定时器可以用用户程序存储器内的常数K作为设定值,也可以用数据寄存器(D)的内容作为设定值。
在后一种情况下,一般使用有掉电保护功能的数据寄存器。
即使如此,若备用电池电压降低时,定时器或计数器往往会发生误动作。
定时器通道范围如下:
100ms定时器T0~T199,共200点,设定值:
0.1~3276.7秒;
10ms定时器T200~TT245,共46点,设定值:
0.01~327.67秒;
1ms积算定时器T245~T249,共4点,设定值:
0.001~32.767秒;
100ms积算定时器T250~T255,共6点,设定值:
0.1~3276.7秒;
定时器指令符号及应用如下图2-2所示:
图2-2通用定时器
当定时器线圈T200的驱动输入X000接通时,T200的当前值计数器对10ms的时钟脉冲进行累积计数,当前值与设定值K123相等时,定时器的输出接点动作,即输出触点是在驱动线圈后的1.23秒(10×123ms=1.23s)时才动作,当T200触点吸合后,Y000就有输出。
当驱动输入X000断开或发生停电时,定时器就复位,输出触点也复位。
每个定时器只有一个输入,它与常规定时器一样,线圈通电时,开始计时;断电时,自动复位,不保存中间数值。
定时器有两个数据寄存器,一个为设定值寄存器,另一个是现时值寄存器,编程时,由用户设定累积值。
如果是积算定时器,它的符号接线如下图2-3所示:
图2-3积算定时器
定时器线圈T250的驱动输入X001接通时,T250的当前值计数器对100ms的时钟脉冲进行累积计数,当该值与设定值K345相等时,定时器的输出触点动作。
在计数过程中,即使输入X001在接通或复电时,计数继续进行,其累积时间为34.5s(100ms×345=34.5s)时触点动作。
当复位输入X002接通,定时器就复位,输出触点也复位。
6.计数器(C)
FX2N中的16位增计数器,是16位二进制加法计数器,它是在计数信号的上升沿进行计数,它有两个输入,一个用于复位,一个用于计数。
每一个计数脉冲上升沿使原来的数值1,当现时值减到零时停止计数,同时触点闭合。
直到复位控制信号的上升沿输入时,触点才断开,设定值又写入,再又进入计数状态。
其设定值在K1~K32767范围内有效。
设定值K0与K1含义相同,即在第一次计数时,其输出触点就动作。
通用计数器的通道号:
C0~C99,共100点。
保持用计数器的通道号:
C100~C199,共100点。
通用与掉电保持用的计数器点数分配,可由参数设置而随意更改。
举个例子,如图2-4所示:
图2-4计时器工作过程
由计数输入X011每次驱动C0线圈时,计数器的当前值加1。
当第10次执行线圈指令时,计数器C0的输出触点即动作。
之后即使计数器输入X011再动作,计数器的当前值保持不变。
当复位输入X010接通(ON)时,执行RST指令,计数器的当前值为0,输出接点也复位。
应注意的是,计数器C100~C199,即使发生停电,当前值与输出触点的动作状态或复位状态也能保持。
7.数据寄存器(D)
数据寄存器是计算机必不可少的元件,用于存放各种数据。
FX2N中每一个数据寄存器都是16bit(最高位为正、负符号位),也可用两个数据寄存器合并起来存储32bit数据(最高位为正、负符号位)。
(1)通用数据寄存器D通道分配D0~D199,共200点。
只要不写入其他数据,已写入的数据不会变化。
但是,由RUN→STOP时,全部数据均清零。
(若特殊辅助继电器M8033已被驱动,则数据不被清零)。
(2)停电保持用寄存器通道分配D200~D511,共312点,或D200~D999,共800点(由机器的具体型号定)。
基本上同通用数据寄存器。
除非改写,否则原有数据不会丢失,不论电源接通与否,PLC运行与否,其内容也不变化。
然而在二台PLC作点对的通信时,D490~D509被用作通信操作。
(3)特殊功能寄存器通道分配D8000~D8255(共256点)。
它用来监控可编程控制器的运行状态,如电池电压、扫描时间、正在动作的状态的编号等,其在电源接通时被清零,随后被系统程序写入初始值[6]。
第二章应用PLC实现控制系统的设计
2.1选题依据
可编程逻辑控制器(PLC)是20世纪70年代发展起来的一种新型工业自动控制设备。
它集自动化技术、计算机技术和通信技术为一体,是一种专门用于工业生产过程控制的现场设备。
目前,PLC始终处于工业自动化控制领域的主战场,为各种自动化控制设备提供非常可靠的控制应用。
主要原因在它能为自动化控制应用提供安全可靠和比较完善的解决方案,适合当前工业企业对自动化的需要。
由于控制对象的复杂性,使用环境的特殊性和运行的长期连续性,使PLC在设计上有自己明显的特点:
可靠性高,适应性广,具有通信功能,编程方便,结构模块化。
在现代集散控制系统中,PLC已成为一种重要的基本控制单元,在工业控制领域中应用前景极其广泛[6]。
本文主要在原有混液装置系统上的改进,结合皮带运输机控制系统,构造出新的控制系统,即自动配料皮带运输机控制系统,采用三菱公司FX2N系列PLC来实现自动配料皮带运输机系统的控制,该系统能够提供均匀、无杂色、无结块、品质均一的干混料,同时可运送散状物料,现场安装和维修都很方便,理检查时也一目了然,且能适应高温度、高粉尘、有冲击和连续振动的工作条件,不受恶劣环境的影响。
该系统有着广阔的应用空间,被广泛应用在煤炭、电厂、钢铁企业、水泥、粮食、烟草、食品及轻工业的生产线。
2.2方案研究与选择
本次设计主要是围绕液体混料装置及皮带运输机方面的研究,综合运用其控制功能。
1.皮带运输机的控制系统
在建材、化工、食品、机械、钢铁、冶金、煤矿等工业生产中广泛使用皮带运输机运送原料或物品。
图3-1为某原料皮带运输机的示意图。
原料从料斗经过PD-1、PD-2两台皮带运输机送出。
从料斗向PD-2供料由电磁阀YV控制,PD-1和PD-2分别由电动机M1和M2驱动。
该控制系统主要考虑的是传送带的启动和停止。
在启动时,对其进行一些要求:
为了避免在前段皮带上造成物料堆积,要求逆物料方向按一定的流动方向按一定的时间间隔顺序启动。
同样,在停止时,为了使运输皮带上不残留物料,要求顺物料流动方向按一定时间间隔顺序停止[5]。
图3-1原料皮带运输机控制示意图
2.物料混合装置控制系统
图3-2为水泥、粮食、烟草、食品等轻工业生产线的混料装置,阀A、B、C为电磁阀,用于控制管路。
线圈通电时,打开管路;线圈断电后,关闭管路。
高、中、低三个料位传感器被淹没时为ON。
系统初始状态为电动机停止,所有阀门关闭,装置内没有物料,高、中、低三个传感器处于OFF状态。
控制要求为按下启动按钮后,打开A阀,物料A流入;当中传感器被淹变为ON时,A阀关闭,B阀打开,B物料流入容器;当高位传感器被淹没变为ON时,
图3-2物料混合装置系统示意图
B阀关闭,搅拌电机开始运行,开始搅动物料,8s后停止搅拌,打开C阀放出均
匀的混合物料;当料位下降到露出低位传感器(传感器有ON变为OFF)时,开始计时,3s后关闭C阀(以确保容器放空)系统回到初始状态,系统运行完一个完整的周期。
此时,系统应检测在刚过的运行周期里是否发出了停止信号,如果已发出,则系统停止在初始状态等待下一次启动信号,否则系统继续运行。
也就是说,按下此类系统的停止要求不应马上停止。
而应该等回到初始状态运行完这个周期再停止。
这生产工艺所必须要求的[11]。
2.3结构设计及控制要求
根据皮带运输机控制及混液装置系统的工控原理,从中提取一部分元件,综合运用,构造出新的PLC控制系统,即自动配料皮带运输机控制系统。
1.系统的基本构成
(1)自动配料系统
由一个混料容器,三个料位传感器,进料阀A,进料阀B及放料阀C,一台搅拌电机组成。
(2)皮带传送系统
包括3条个传送带PD-1、PD-2、PD-3,传送带均由步进电机驱动,共使用了3台步进电机。
(3)控制系统
该系统的全部控制功能由一台三菱FX2N-16MR型可编程控制器实现,用于控制进料、搅拌、放料、皮带运转、停止等工作过程。
2.系统的工作原理
图3-3为自动配料皮带运输机系统的设计原理图,SL1、SL2、SL3、分别为高、中、低料位传感器,料位淹没时接通,物料A、B有进料电磁阀Y4、Y5控制、混料由出料电磁阀Y6控制,M0为搅拌电机,三条传送带PD-1、PD-2、PD-3分别由接触器M1、M2、M3控制。
控制要求如下:
(1)初始状态
自动配料混合装置处于OFF状态,搅拌电动机停止,所以阀门关闭,装置内没有物料,上、中、下三个液位传感器处于OFF状态;皮带运输机由电动机控制,现处于停止状态。
(2)启动操作
图3-3动配料皮带运输机控制系统原理图
按下启动按钮SB1,装置开始按以下规律运行:
a.物料A电磁阀打开,物料A流入容器。
当料位到达中料位传感器SL2时,SL2接通,关闭物料A电磁阀,打开物料B电磁阀,物料B开始流入容器。
b.当容器料位到达高料位传感器SL1时,SL1接通,关闭物料B电磁阀,搅拌电机M0启动,开始搅匀物料。
c.搅拌电机工作8s后停止搅动,在开启放料电磁阀C之前,为了避免在前段传送带上造成物料堆积,依次间隔2s启动传送带电动机M3、M2、M1,分别带动传送带PD-3、PD-2、PD-1运转。
d.当皮带PD-1运转起来2s后,放料电磁阀C打开,开始放出混合物料。
e.当容器料位下降到低料位传感器SL3时,SL3由接通变为断开,开始计时,3s后关闭放料电磁阀C。
f.在关闭放料电磁阀C的同时,为了使传送带上不残留物料,依次间隔2s停止传动带M1、M2、M3电动机,传送带PD-1、PD-2、PD-3停止运转,系统开始执行下一个循环周期。
(3)停止操作
按下停止按钮SB2后,在当前的混合、放料、输送操作处理完毕后,才停止运行(停在初始状态上)
第三章系统的总体设计
3.1PLC机型的选择及外部接线图
图4-1自动配料皮带运输机PLC外部接线图
根据对自动配料皮带运输机控制要求的分析,可确定输入信号由启动、停止按钮SB1、SB2,物料传感器SL1、SL2、SL3共计5点输入;输出信号为搅拌电机接触器M0、传动带接触器M1、传送带接触器M2、传送带接触器M3,进料电磁阀A、进料电磁阀B、放料电磁阀C,共计7点。
综合上述分析系统要求,考虑到系统的经济型和技术指标,可选用三菱公司的FX2N系列PLC,机型为FX2N-16MR。
该机基本单元有有8个开关量输入点,8个开关量输出点,能够满足系统控制要求。
据此可作出自动配料皮带运输机控制系统的输入、输出分配,如外部接线图4-1所示。
3.2I/O设备及I/O编号的分配
如表4-1所示为控制系统的I/0分配表。
表4-1PLC的I/O分配表
输入设备
输入点编号
输出设备
输出点编号
启动按钮SB1
X0
搅拌电机接触器M0
Y0
停止按钮SB2
X1
传送带接触器M1
Y1
高料位传感器SL1
X2
传送带接触器M2
Y2
中料位传感器SL2
X3
传送带接触器M3
Y3
低料位传感器SL3
X4
进料电磁阀A
Y4
进料电磁阀B
Y5
放料电磁阀C
Y6
3.3顺序功能图的设计
由题目给出的控制要求,可以把顺序功能图划分为12步,连同初始步共13
步。
每一步驱动相关的负载,设计思路同STL顺序功能图一样,图4-2给出了用
M代表步的顺序功能图。
需要注意的是M7步的转换条件是料位露出下传感器,也就是X4由ON变为OFF,所以转换条件应该是X4,下面是与顺序功能图对应的梯形图4-3。
图中X0为启动信号,X1为停止信号,如果启保停辅助继电器M20为ON,M0为ON后能马上状态转移,系统继续工作;如果M20为OFF,M0为ON后不能转移,系统停在初始步。
编写梯形图时,必须把所有能够使M为ON的条件全部考虑到,比如M0电路,M20为活动步情况下,T8为ON将会使M0为ON,所以将M12、T8的常开触点串联作为M0的启动电路。
可编程程控制器开始运行时应将M0置ON,否则系统无法正常运行,故将M20的常开触点与上述的电路并联,并联后还应并联上M0的自保触点。
M0后续步M1为ON应将M0线圈断开,所以后续步M1的常闭触点与M0的线圈串联。
对于传动带的启动,为了避免在前段运输皮带上造成物料堆积,要求逆物料流动方向按一定时间间隔顺序启动PD-3、PD-2、PD-1,停止时,为了使运输皮带上不残留物料,要求顺物料流动方向按一定时间间隔顺序启动PD-1、PD-2、PD-3,M7、M8两步都驱动负载Y6,为避免双线圈输出,用M7、M8的常开触点并联集中驱动Y2。
具体的程序分析过程见4.4节。
以M为编程软件的顺序功能图和S为编程软件的顺序功能图一样,一般情
图4-2自动配料皮带运输机的顺序功能图
况下,每一步为ON时都要驱动一定得负载,条件不满足活动步不转移。
在状态转移过程中,相邻两步的状态同时为ON一个周期,对那些不能同时接通的外部负载(如正反接触器),为了保证安全,必须在外部设置硬件互锁。
3.4梯形图的设计及过程分析
该控制系统的梯形图程序如图4-3所示。
1.采用基本逻辑指令编程
根据控制要求编写的梯形图如图所示,下面分析其工作过程:
(1)初始状态
当系统投入运行时,自动配料装置处于OFF状态,搅拌电动机停止,所以阀门关闭,装置内没有物料,上、中、下三个料位传感器处于OFF状态;皮带运输机由电动机控制,现处于停止状态;
(2)启动操作
按下启动按钮X0,M20接通并自保,同时使并联在第2行及串联在第3行的M20动合触点闭合,此时M0接通并自保,第3行串联的动合触点M0接通(为开启进料电磁阀A做准备)及串联在第12行的M0动断触点断开(切断执行皮带停止运转系统),同时M1接通并自保,使串联在第4行的M1动合触点闭合(为开启进料电磁阀B做准备)及串联在第2行的M1动断触点断开(切断初始步系统),同时时Y4接通,物料A电磁阀打开,物料流入容器。
a.料位上升到中料位
当料位上升到中料位时,X3动作,M2接通并自保,使串联在第5行的M2
图4-3自动配料皮带运输机控制系统梯形图
动合触点闭合(为搅拌启动作准备)及串联在第3行的M2动断触点断开(切断进料A系统),同时Y5接通,进料电磁阀B开启,物料B流入容器。
b.料位上升到高料位
当料位上升到高料位时,X2动作,M3接通并自保,使串联在第6行的M3动合触点闭合(为皮带3启动做准备)及串联在第4行的M3动断触点断开(切断进料B系统),同时Y0接通,搅拌电机运转,T0接通开始计时。
c.依次间隔启动传送带M3、M2、M1电动机
当定时器T0计时8s过后,串联在第6行定时器T0的动合触点闭合,M4接通并自保,使串联在第7行的M4动合触点闭合(为皮带2启动作准备)及串联在第5行的M4动断触点断开(切断搅拌物料系统),同时Y3接通,皮带PD-3开始运转,定时器T1接通开始计时,2s过后,串联在第7行的定时器T1的动合触点闭合,M5接通并自保,使串联在第8行的M5动合触点闭合(为皮带PD-1启动作准备),同时Y2接通,皮带PD-2开始运转,定时器T2接通开始计时,2s过后,串联在第8行的定时器T2的动合触点闭合,M6接通并自保,使串联在第9行M6的动合触点闭合(为开启放料阀作准备),同时Y1接通,皮带PD-1开始运转,定时器T3接通开始计时。
d.放料电磁阀开启
当定时器T3计时2s过后,串联在第9行的定时器T3动合触点闭合,M7接通并自保,使串联在第10行的M7动合触点闭合(为清空容器作准备),同时Y6接通开始放料。
e.料位下降到低料位
当料位下降到低料位时,X4动作,M8接通并自保,使串联在第9行M8动断触点断开(暂时切断放料系统)及第12行的M8动合触点闭合(为关闭放料电磁阀作准备),同时Y6接通继续放料,定时器T4接通开始计时。
f.关闭放料电磁阀
当定时器T4计时3s过后,T4动合触点闭合,M9接通并自保,使串联在第10行的M9动断触点闭断开(切断放料系统),同时定时器T5开始计时。
g.依次间隔停止三条传送带M1、M2、M3电机
当定时器T5计时2s过后,串联在第13行的定时器T5动合触点闭合,M10接通,使串联在第8行的M10动断触点断开,M6、Y1、T3断电,所有的触点复位,皮带PD-1停止运转,同时定时器T6接通开始计时,2s过后,串联在第14行的M11接通,使串联在第7行的M11动断触点断开,M5、Y2、T2断电,所有的触点复位,皮带PD-2停止运转,同时定时器T7开始计时,2s过后,串联在第15行的M12接通,使串联在第6行的M12动断触点断开,M4、Y3、T1断电,所有的触点复位,皮带PD-3停止运转,同时串联在第2行的M12动合触点闭合(为下一次循环作准备)及定时器T8接通开始计时,2s过后,串联在第2行的定时器T8动合触点闭合,准备执行下一次循环周期。
(3)停止操作
按下停止按钮X1,M20断电,并联在第2行及串联在第3行的M20动合触点复位,即停止循环,若系统正在运行过程中,按下此类系统的停止按钮X1,其不应该立即停止,而应该等到等到回到初始状态运行完这个周期再停止。
这是生产工艺所必须要求的。
2.根据图4-3的梯形图程序编制的语句表(见附录)
参考文献
[1]陈立定.电气控制与可编程序控制器原理及应用.机械工业出版社,2005.198~201
[2]黄净.电气控制与可编程序控制器.北京:
机械工业出版社,2005.156~157
[3]方承远.工厂电气控制技术.北京:
机械工业出版社,2006.189~192
[4]范永胜,王岷.电气控制与PLC应用.北京:
中国电力出版社,2007.130~138
[5]杨长能,林小峰.可编程序控制器(PC)与实验指导.重庆大学出版社,1997.301~305
[6]何衍庆.可编程控制器原理及应用技巧.北京:
化学工业出版社,1998.251~252
[7]张万忠.可编程控制器应用技术.北京:
化学工业出版社,2001.151~156
[8]史国生.电气控制与可编程控制器技术.北京:
化学工业出版社,2001.94~95
[9]廖常初.PLC编程及应用.北京:
化学工业出版社,2001162~173
[10]路林吉,江龙康.可编程控制器原理及应用.北京:
清华大学出版社,2001.155~157
[11]江秀汉,汤楠.可编程控制器原理及应用.西安电子科技大学出社,2003.224~226
[12]张进秋,陈永利.可编程控制器原理与应用实例.机械工程出版社,2004.178~179
[13]孙同景,徐蹲.可编程序控制器应用基础.山东科学技术出版社,1996.45~46