SIMATIC S7.docx
《SIMATIC S7.docx》由会员分享,可在线阅读,更多相关《SIMATIC S7.docx(13页珍藏版)》请在冰豆网上搜索。
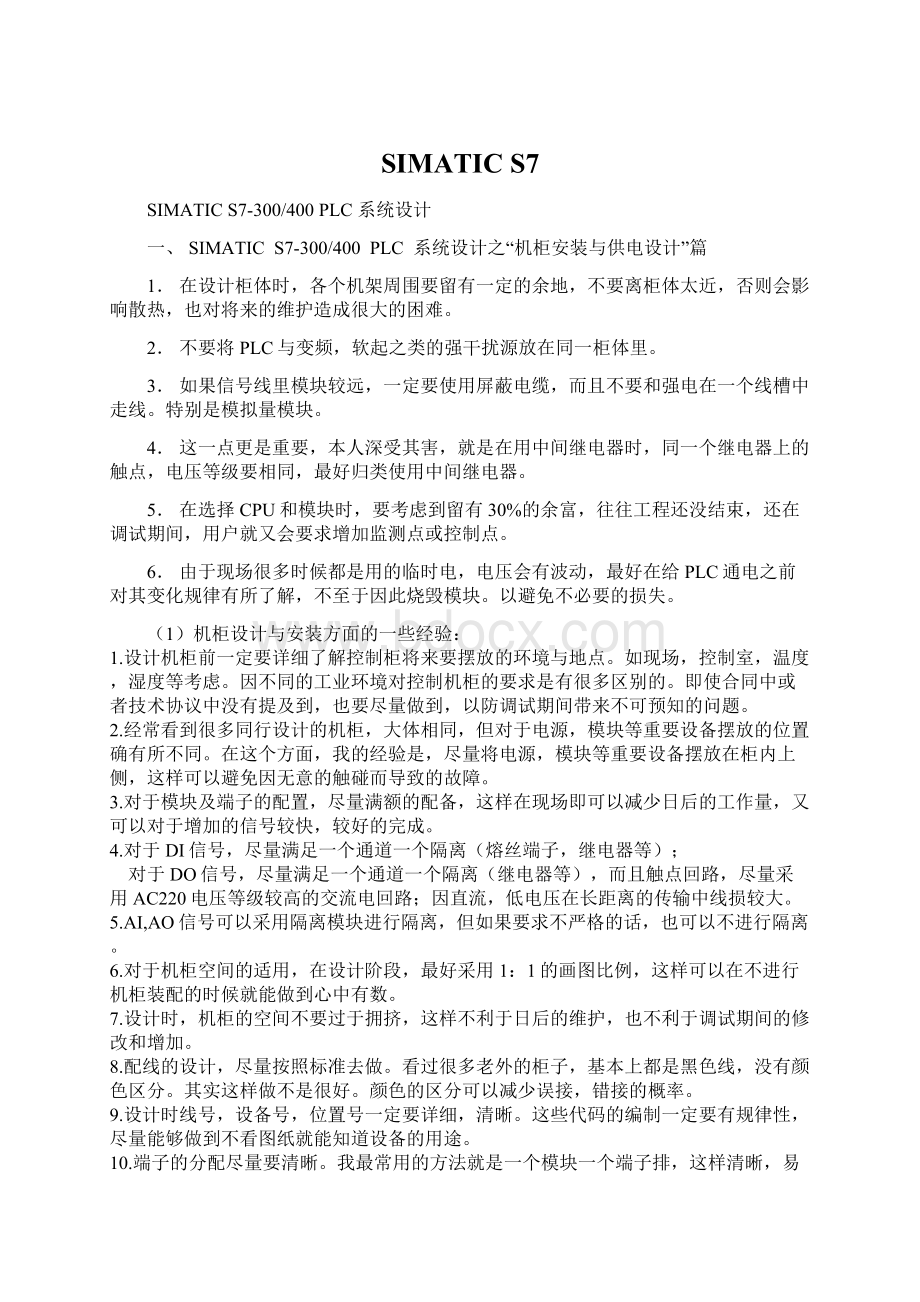
SIMATICS7
SIMATICS7-300/400PLC系统设计
一、SIMATIC S7-300/400 PLC 系统设计之“机柜安装与供电设计”篇
1.在设计柜体时,各个机架周围要留有一定的余地,不要离柜体太近,否则会影响散热,也对将来的维护造成很大的困难。
2.不要将PLC与变频,软起之类的强干扰源放在同一柜体里。
3.如果信号线里模块较远,一定要使用屏蔽电缆,而且不要和强电在一个线槽中走线。
特别是模拟量模块。
4.这一点更是重要,本人深受其害,就是在用中间继电器时,同一个继电器上的触点,电压等级要相同,最好归类使用中间继电器。
5.在选择CPU和模块时,要考虑到留有30%的余富,往往工程还没结束,还在调试期间,用户就又会要求增加监测点或控制点。
6.由于现场很多时候都是用的临时电,电压会有波动,最好在给PLC通电之前对其变化规律有所了解,不至于因此烧毁模块。
以避免不必要的损失。
(1)机柜设计与安装方面的一些经验:
1.设计机柜前一定要详细了解控制柜将来要摆放的环境与地点。
如现场,控制室,温度,湿度等考虑。
因不同的工业环境对控制机柜的要求是有很多区别的。
即使合同中或者技术协议中没有提及到,也要尽量做到,以防调试期间带来不可预知的问题。
2.经常看到很多同行设计的机柜,大体相同,但对于电源,模块等重要设备摆放的位置确有所不同。
在这个方面,我的经验是,尽量将电源,模块等重要设备摆放在柜内上侧,这样可以避免因无意的触碰而导致的故障。
3.对于模块及端子的配置,尽量满额的配备,这样在现场即可以减少日后的工作量,又可以对于增加的信号较快,较好的完成。
4.对于DI信号,尽量满足一个通道一个隔离(熔丝端子,继电器等);
对于DO信号,尽量满足一个通道一个隔离(继电器等),而且触点回路,尽量采用AC220电压等级较高的交流电回路;因直流,低电压在长距离的传输中线损较大。
5.AI,AO信号可以采用隔离模块进行隔离,但如果要求不严格的话,也可以不进行隔离。
6.对于机柜空间的适用,在设计阶段,最好采用1:
1的画图比例,这样可以在不进行机柜装配的时候就能做到心中有数。
7.设计时,机柜的空间不要过于拥挤,这样不利于日后的维护,也不利于调试期间的修改和增加。
8.配线的设计,尽量按照标准去做。
看过很多老外的柜子,基本上都是黑色线,没有颜色区分。
其实这样做不是很好。
颜色的区分可以减少误接,错接的概率。
9.设计时线号,设备号,位置号一定要详细,清晰。
这些代码的编制一定要有规律性,尽量能够做到不看图纸就能知道设备的用途。
10.端子的分配尽量要清晰。
我最常用的方法就是一个模块一个端子排,这样清晰,易记,对于日后的调试很有益处。
11.对于电气回路的保护一定要做,而且设计也要规范。
比如应该使用6A的断路器,为了图便宜,设计10A的断路器。
12.机柜内常规的设备,如照明,风扇,插座等设备尽量配齐。
13.保护地与工作地(信号地)尽量要做到分开设计。
这样如果现场是提供一个地,那就将保护地,工作地短接即可;如果现场提供2个地,那就可以分开接。
14.设计I/O分配的时候,尽量考虑现场设备一组电缆集中在一个机柜当中,这样会给施工单位带来很大的方便。
(2)现场施工部分考虑
1.规定底座必不可少;
2.电缆铺设要严格按照标准。
尽量适用屏蔽电缆;防爆区一定要使用本安电缆。
且安全隔离
3。
交流直流尽量分开;
4.现场仪表的供电要有保护;
5.汇线槽要考虑现场电缆的走向,避免一个汇线槽走过多的电缆;
6.机柜要设计电缆固定支架;
7.信号电缆,通讯电缆要严格与动力电缆分开。
屏蔽层接地。
(3)信号分配
1.I/O信号分配要考虑类型,尽量保证同一模块同一类型的信号。
如电流2线,4线尽量不要混接到同一模块。
2.DI,DO模块尽量摆放在同一机柜内。
比如一个电机(2反馈+1故障+1远程+2命令),这样一组电缆一个机柜,现场施工较为方便。
3.尽量避免柜间电缆。
4.同一类型设备,尽量不在同一模块上。
比如一个汽包水位测量可能有3组信号,这样的话,如果3组信号集中在一个模块上,一旦模块出现问题,那这3组信号都会受到影响。
分散设计,降低风险。
5.I/O信号表尽量包含所有信息。
这样一劳永逸。
一张表搞定一切。
(4)网络组件
1.如果允许,单独设计一个网络通讯柜,这样可以更多的避免人为及电气干扰;
2.供电如果有2路,尽量都采用;
3.交换机要预留一部分接口;
4.光纤的安装时注意不要小于90度;
5.光纤接头方向不要搞错;
6.预留光纤盒的安装位置;
谈一点抗干扰以外的话题:
本人在工作中发现,好多机柜生产商的配线工并不了解可编程控制器的最基本的东西,因此在300,400系列里,由于前连接器和前面板上的编号和组态后输入,输出的通道编号并不一致,因此很不方便。
本人是这样处理的,出模块接线图时以前连接器的编号为准,在编程时以系统的默认的通道编号为准,在符号表里把两者的对应关系表达出来。
另外在编线号时还是建议以被控对象为中心来编,因为更多的异常都是控制对象反映出来的,这样通过异常的对象找相应的输入,输出点,比反过来找效率更高一些。
首先说下低压部分的,我们的用电设备大多是水泵,在抽屉排布时最好最好将同种水泵的回路分布在不同的配电柜,这样一般既能平衡负荷分布,也能保证出现故障时至少有一台同种水泵能够工作。
还有就是不管是否提前设计了预留,最后配盘时也尽可能的再预留出两三个电源回路来。
因为我不止一次遇到最后施工时业主临时增加用电设备。
再说说I/O分站,我觉得应该尽可能的少做分站,能合的就合。
水处理工程有很多在线检测仪表,在设计分站时最好考虑好仪表的位置,再合理分布就地机柜和分站模块。
1是熟悉设备工艺情况,了解每一个细节,如需不需要走总线网络,只有熟悉设备才可以设计出适合的程序。
2对于市电质量不是很好情况,使用好一点的外接开关电源如菲尼克斯的,输出DC24V给CPU模块,可以不需要使用西门子PS电源模块。
尽量不使用直接接入AC220V的PS电源模块。
3安装的STEP7需要装有仿真软件,做好程序后使用仿真软件仿真很方便,集成安装winccflex,此软件也可以仿真运行,方便离线调试程序,即做好STEP7程序后,再做一个针对于此程序调试的winccflex程序。
4.根据工艺设备情况选择合适的硬件,I/O点数做适当的富余,方便以后扩展,对于PLC输出点,负载很小,动作不是很频繁,可以直接使用输出点带动负载,如果负载大,动作频繁的话,建议输出点控制中间继电器,中间继电器控制负载,可有效延长特别是继电器输出点的使用寿命。
尽量使用输入输出都是DC24V的模块,安全。
5.程序设计如果是顺序控制的,先根据工艺动作画出控制的顺序功能图,根据功能图来设计,做出来的程序就条例清晰,程序设计的效率就高,且不容易出错。
在程序编辑过程中,尽量使用FB,FC,块来做程序,块内程序尽量使用局域变量做,不使用全局变量,方便以后移植,尽量使用数据块数据,不使用M点。
6.系统外围如电机控制主电路,使用电机断路器加接触器,淘汰以前使用的熔断器或普通断路器加接触器加热继电器模式,尽量使用断路器来代替熔断器。
在以往的工程中经常发现业主为了省钱,省掉了中间继电器,信号隔离器,在调试过程中发现有时由于没有加中间继电器,负载为电磁阀,通过DO模块后,DO模块有压降,最后真正加在负载上的电压达不到电磁阀工作电压,而使电磁阀无法正常工作。
发现问题后再去加中间继电器,影响了工程的正常调试。
工业现场各种设备比较多,电缆比较多,有时调试时安装公司无意间接错线的情况下,出现烧模块的现象。
还有模块24VDC和220VAC不能混用,比如现场用24VDC模块来检测集中和分散,但在选择开关上又有220AC电的情况下,由于不细心接错线很容易产生220AC电源串到24VDC模块上,产生烧坏模块的现象。
所以工业现场尽量说服业主在DI/DO模块,AI/AO模块上加上中间继电器和信号隔离器,防止烧模块的现象发生,保证设备的安全可靠运行。
SIEMENS推荐的配电方式如下图所示:
从上图可以看出,PE和和机柜的接地母线是接在一起的。
同时机柜的机壳也是和接地母线接在一起的。
对于31XC和312IFM来说24V的M是和接地母线连接在一起的,别的CPU是可以通过接地滑块实现参考电位接地或者浮动接地。
从图中也可以看出交流模块,直流隔离模块、直流非隔离模块的电源是分开的。
这样的好处我觉得是可以隔离干扰.
至于是否要设置单独信号接地母线,从图中没有看到,很多图纸中也没有看到。
真正的做到3相5线制应该对于防止干扰应该很帮助,我在一个现场见过所有的AI/AO都没有加保险丝端子,很多DI都没有加继电器隔离.当时感觉这样做不怕出问题吗?
对方的工程师说他们运行5年,几乎很少出问题.他们的接地做的非常好.现场供电也是三相五线制.施工的时候也很注意,基本上杜绝了N线带电的情况.
我记得以前的项目很多的都是24V的M端与机壳都是连接在一起的。
以前也在机柜这边做过处理,把24V的M和机柜隔离,但是往往24V要给现场仪表供电,因为现场仪表的问题,所以也不能保证M端与大地隔离。
大家都是如何做的呢?
再谈一下如何制作机柜接线图,怎么样才能让接线工人最容易接线呢?
以前看过老外的图纸,图纸很标准,包括图例、安装、等电位连接、详细的通讯原理图、详细的配电图、机柜布置图,甚至每个输入/输出详细接线都画了出来,包括与继电器连接的线号,与端子连接的线号都详细的作了标注.这样的图纸内容很多,但很多都是标准化的,很多应该是用AUTOCAD 电气版或者EPLAN自动生成的。
前面讨论了很多了,个人觉得有几点比较重要:
1,标准化以及可移植性,也就是说这次所做的设计、改进、创意都要很容易的可以移植到下一个项目。
2,有规律可循,比图图纸的页码,电器元件的命名以及IO点的地址等等都要很有规律性。
一个设备或一个大的系统可能分为好几个部分,那么每个部分的K1固定是电机的接触器,Q1固定式电机的过流保护,图纸里第一至第五页是xx...io地址,如果一个部分有类似的结果,比如左右时一样的,那么io地址可以命名一部分是200.x,一部分是300.x,除了200和300这个大的方面不一样,后面的应该都一样。
这样做可以给调试人员和维护人员极大的方便。
印象很深的是有的项目电器元件的名字后面的数字就是图纸上的页码,这样在查阅图纸的时候非常方便。
3,现在的变频器和其他元件功能都很强大,但是个人觉得300/400的PLC的处理能力已经完全足够,所以最好把绝大部分的工作都交给PLC,让变频器和其他元件傻瓜化。
这样维护人员需要适应新系统的时间将大大缩短,因为他只要搞清楚PLC程序就可以了。
见过国外项目,把本应在PLC完成的任务交给CUVC的自由功能块,结果为了搞清楚他的工作方式,我要把变频器的几十个bxx一个个搞清楚,用功能块画出来。
我想客户不见得也可以画出来吧。
个人觉得这样的系统可维护性太差!
4,给每个站的电源用保险丝隔离起来。
现在的300/400系统很多事分布式IO,但是很多系统这些远程模块以及人机界面的电源是从一个地方来的,也就是说24v电源都是连在一起的,曾经出现过调试过程中有工人接线的时候把230Vac的电源误碰到一个远程模块的电源,导致整个系统全部烧毁的悲剧。
而另外一次也发生同样的问题,但是损失却小得多,因为那次的系统全部模块的电源都有一个2A的保险丝隔
针对工程项目,我一般是按如下步骤考虑:
1、系统方案设计:
(1)首先我要明确解项目工艺和要求
(2)在满足工艺要求的前提下,我会考虑几种方案,比如:
我是用300+200模式还是用300+ET200模式,通讯用以太网模式还是PROFIBUS模式,还是MODBUS模式。
。
。
(3)根据工程预算,结合客户要求,确定最佳方案
2、系统设计
(1)首先根据工艺控制要求和DI、DO、AI、AO点数,预留20%~30%余量,确定PLC类型和模块数量;
(2)确定HMI使用触摸屏还是PC,使用组太王还是WINCC、INTOUCH、IFX。
。
。
,并确定网络通讯协议
(3)选型其他低压电器
(4)设计 :
做控制系统图、控制柜图等等
(5)程序编写和初步模拟调试
3、安装
(1)指导安装,尤其注意经常出问题或容易干扰的地方
(2)动力、控制电缆分开敷设
(3)电气安装要符合国家低压电气安装和验收规范
4、调试
(1)我一般先把系统调通,保证HMI和PLC、PLC和PLC之间通讯正常
(2)再着重调试PLC程序,先保证局部运行没问题
(3)再整体调试,保证整个系统按工艺流程运行
(4)最后调试HMI
5、工程考核、验收和移交
6、后续跟踪和问题处理也要作好
主要就这么多
讲讲设计裕量的问题。
很多合同里都有这么一条,保证系统I/O点要有10%-20%的裕量,那么在实践中这些设计裕量起到其应有的作用了吗,还是就是浪费了?
根据这些年来我有心观察的结果,95%以上是浪费了的。
当我们留出了足够的I/O点,因为柜体空间紧张,没有把信号线放到输入、输出的端子上,这些点就基本被埋没了;即使花了代价,把备用的I/O都放到了端子上,却发现电源有问题了,不是同一组电源。
电压等级不同了;虽然把中继引到端子了,却发现要加几个接触器,没空间了,柜内的负载电源容量也不够了;等等。
所以,没有经过系统规划的设计裕量就是白白浪费的,对于一个成熟稳定的系统,刻意去增加系统的设计裕量是毫无意义的,相反只能证明你对系统的不熟悉。
我的一些设计方案:
(我涉及到的都是一些生产线类的控制。
)
首先,我不喜欢使用那种集中控制的方案,CPU+一堆DIO,AIO的方案。
(除非是独立的设备,s7-200程序空间不够,或IO点数不够。
只能采用s7-300)
原因是:
现场布线太麻烦了。
例如:
一个CPU柜+两个(十二台变频器)驱动柜,进出线缆(辅助电源、现场IO、传感器、触摸屏、电机电缆)两捆直径200毫米。
你还要担心不可预见的接错线问题、EMC问题...。
既然西门子s7-300支持Profibus,干嘛不好好利用?
一、把变频器从驱动柜中拿出来(取消集中放置的驱动柜),根据现场工艺要求(单独或几台)安置在最接近电机处,为它设计一个IP5x的箱体(空间:
变频器+空开+380/220隔离变压器+AC/DC辅助电源+散热风机+IO接线端子+插座[变频器调试用])。
这样带来的好处是:
1、把变频器-电机电缆长度降到最短,大大减少了EMC干扰问题。
我有的设计可做到距离短于一米。
2、由于交货前已经完成电机接线、调试。
现场免去接线、布线的麻烦。
3、既然Profibus是分布式IO(驱动装置也是IO),而西门子的驱动装置绝大部分支持BiCo技术,那么就应该充分利用它。
一般说来,电机+传动距离现场操作者不会太远(2-3米?
)。
那么就把现场的按钮(急停除外)、指示灯(甚至和该点传动相关的传感器)、电磁阀连接到变频器IO端子(这个连接并不是去控制变频器的!
)每一台变频器至少提供6个Di、3个Do、各2个AiAo。
它们全部可以通过DP网络由s7-300读取和控制。
这样一来又减少了一大部分布线的烦恼。
(一般说来,现场的控制面板是嵌在设备上的)
二、如果可以把PLC取出来和触摸屏集成在一个柜(箱)里(由于上述原因,IO线已经没有几根了)。
PLC和触摸屏共用一个隔离辅助电源,仪表、指示灯用另外一个隔离电源。
三、做好DP电缆的屏蔽、防护。
按照生产线的布置,设计镀锌管防护。
里面只有一根DP通讯电缆、一根等电位电缆、重要的控制线束(急停之类)。
四、如果所有驱动柜(箱)呈一字排开,距离又不是太远,可以考虑采用供电母排。
按驱动容量分布,选择中点供电接入(母排电容量仅是总容量的一半)。
使用母排的好处是:
现场母排安置,插头(自带空开)一插就完成所有的装置供电。
要点:
不使用零线。
只有地线。
五、驱动的控制;西门子的驱动装置一般都内置多个PID控制器,应该好好利用。
做成一些局部反馈的PID环节,减轻PLC的处理负荷。
也就是说,传感器的反馈可以介入局部PID控制,同时PLC还能通过DP读取当前状态。
六、编程,组态一般选用PPO2 4PKW 6PZD就够了。
对驱动的同时启动、停止,用PLC的同步命令。
读取变频器的Di只需要一个PZD字,Do只能利用控制字中不用的位(当然可以利用自由功能块扩展功能),Aio只需要自己定义哪个PZD字段即可。
七、尽量充分利用触摸屏内置的运算功能、数值转换、限制功能、配方存储功能、密码保护功能,降低PLC的运算负荷。
只要DP网络不是特别远,DP通讯速率完全可以跑到12M。
这种方案的好处是:
生产线可以模块化设计。
现场安装实现了Profibus的初衷。
一天完成接线(就是布镀锌管、DP接线、插头)。
从现实出发:
1.往往合同签订的时候,设计方很难拿出一个成型的方案出来,都是一个初期的设计,这个时候统计的点数自然也只是一个大体的数量。
而在实际操作中,往往会增加一些设备,这个时候设计初期的备用量就会大派用场了。
当然如果过多的设计备用设备和备用点,当然就如版主所说,毫无意义。
2.但换一个角度看,还有另外一种原因导致备用点的浪费。
客户的技术水平有限,有的时候培训又不到位,仅仅是使用而已。
而此时对于后续的简单增加设备等不敢去随意尝试,同样也是为了保证系统运行的稳定性不敢轻易的修改系统中的任何一个程序(中国客户很多都是这样的心里)。
这个也导致大量的备用点的浪费。
而合同就是合同,文本格式,而且谁也不会承认自己的技术能力问题。
因此都是按照常规的要求制定合同而已。
3.如果设计方是我的话,我会毫不犹豫的设计中留有备用余量(当然要在一个合理的范围内)。
根据我这些年的实际经验看,这些备用余量是会给我在调试过程中带来很多的便利。
当然这些备用余量也不会完全都用尽的。
二、SIMATIC S7-300/400 PLC 系统设计之“系统接地及抗干扰”篇
我工作的地方是钢厂,工作时发现环境的干扰也会影响PLC的正常运行,有一次因为电磁干扰都发生了事故。
在这里交流一下:
几种干扰:
PLC控制系统的干扰源与一般影响工业控制设备的干扰源一样,大都产生在电流或电压剧烈变化的地方,这些电荷剧烈移动的部位就是干扰源。
有共模干扰和差模干扰。
共模干扰是信号对地的电位差,主要由电网串入、地电位差及空间电磁辐射在信号线上感应的共态(同方向)电压迭加所形成。
共模电压通过不对称电路可转换成差模电压,直接影响测控信号,造成元器件损坏(这就是一些系统I/O模件损坏率较高的主要原因),这种共模干扰可为直流、交流。
差模干扰是指作用于信号两极间的干扰电压,主要由空间电磁场在信号间耦合感应及由不平衡电路转换共模干扰所形成的电压,这种干扰叠加在信号上,直接影响测量与控制精度。
来自空间辐射电磁场干扰:
由电力网络、电气设备的暂态过程、雷电、无线电广播、电视、雷达、高频感应加热设备等产生的,通常称为辐射干扰。
影响主要通过两条路径:
一是直接对PLC内部的辐射,由电路感应产生干扰;而是对PLC通信内网络的辐射,由通信线路的感应引入干扰。
辐射干扰与现场设备布置及设备所产生的电磁场大小,特别是频率有关,一般通过设置屏蔽电缆和PLC局部屏蔽及高压泄放元件进行保护。
电源的干扰:
电网内部的变化,入开关操作浪涌、大型电力设备起停、交直流传动装置引起的谐波、电网短路暂态冲击等,都通过输电线路传到电源原边。
PLC电源通常采用隔离电源,但其机构及制造工艺因素使其隔离性并不理想。
实际上,由于分布参数特别是分布电容的存在,绝对隔离是不可能的。
信号线引入的干扰:
一是通过变送器供电电源或共用信号仪表的供电电源串入的电网干扰,这往往被忽视;二是信号线受空间电磁辐射感应的干扰,即信号线上的外部感应干扰,这是很严重的。
由信号引入干扰会引起I/O信号工作异常和测量精度大大降低,严重时将引起元器件损伤。
对于隔离性能差的系统,还将导致信号间互相干扰,引起共地系统总线回流,造成逻辑数据变化、误动和死机。
PLC控制系统因信号引入干扰造成I/O模件损坏数相当严重。
抗干扰措施
1、采用性能优良的电源,抑制电网引入的干扰
2、电缆选择的敖设:
不同类型的信号分别由不同电缆传输,信号电缆应按传输信号种类分层敖设,严禁用同一电缆的不同导线同时传送动力电源和信号,避免信号线与动力电缆靠近平行敖设,以减少电磁干扰。
3、正确选择接地点,完善接地系统
对于抗干扰措施我觉得可以从以下两个方面如手:
一、在系统设计阶段,可以从硬件和软件两方面考虑
1 对于硬件措施,可以采用屏蔽,滤波,电源调整与保护,隔离,采用模块式结构 等方面入手
2 对于软件措施,可以采用故障诊断,信号保护和恢复,设置警戒时钟,加强对程序的检查和校验,对程序及动态数据进行后备等方面进行考虑
二、在系统安装阶段,可以在电源和地线接线,输出端子的接线,电缆的敷设按照规范进行施工,从而保证得到理想的抗干扰效果
关于模拟信号接地问题一般处理如下:
对隔离输入模板,.摸板参考地Mana与CPU的电源地M没有电连接。
因此Mana与M有电位差时,必须采用隔离输入模板。
但是,如果电位差超过Eiso,则必须建立Mana与M之间的连接。
对SIEMENS的模板,Eiso=75VDC或60VAC。
对非隔离输入模板,则必须建立Mana与M之间的连接。
为抑止信号地M-与Mana之间的共模干扰,不同传感器的接地方式不同,限于篇幅以及图解困难,难以细说。
一般原则是,建立信号地与模板的地、模板地与(CPU)系统地的连接。
如果有干扰环流,则将取消模板地与系统地的连接,让模拟地悬浮。
另外,屏蔽推荐双端接地,如果有干扰环流,则改为单端
三、SIMATIC S7-300/400 PLC 系统设计之“网络架构及通讯优化”篇
在生产线的自动化控制中,都有多站点的问题,根据不同的设计要求和工厂环境选择适合的通讯方式,能大量的节约电缆和铺设成本。
通讯方式对维护也是很方便的。
profibus适合速率12M以下,不加中继器的情况下最多带32个站点,距离不超过1000M,不过距离长了速率也要下调才能保证通讯的正常。
工业以太网的速率为10M和100M,通讯数据量为8K,两个站点间距离可达3000M,适用于大量数据的传输和长距离通讯。
MPI和串口通讯,主要用在编程和与串口设备通讯,最大距离都是50M。
个人感觉profibus用的更广一点,基本上每个厂家都支持,可以用于不同厂商设备的通讯控制,在应用的时候初用者一定要注意程序一些组织块一定要下载,如OB82、OB85、OB86、OB87、OB121、OB122和总线末端要加有源终端,否侧容易出现局部从站的故障导致整个网络的瘫痪或因个别站点出现停电、维修、故障时导致全网通信故障。
其它感觉就没什么了,很好用的。
工业以太网现在用的也比较多了,西门子的产品基本上都有支持工业以太网的模块了,上个月做的一个项目用到ET200M和KTP的屏,就有都有支持工业以太网的型号。
在末来,各厂商都支持工业以太网的产品后,应用应该会更好。
对于S7-300/400系统的通讯接口和通讯优化方面,个人觉得应该注意以下几个方面:
首先在进行系统网络架构设计时,在网络协议的选择上,对于S7-300/400系列可以优先考虑使用西门内部专有协议(不公开协议),如ISO-ON-TCP,S7,Profinet等来保证系统的通讯的稳定性
另外在系统接口预留上也一定要考虑与第三方系统的的通讯兼容性,如基于以太网TCP/I