我国造船工艺创新发展三十年doc.docx
《我国造船工艺创新发展三十年doc.docx》由会员分享,可在线阅读,更多相关《我国造船工艺创新发展三十年doc.docx(9页珍藏版)》请在冰豆网上搜索。
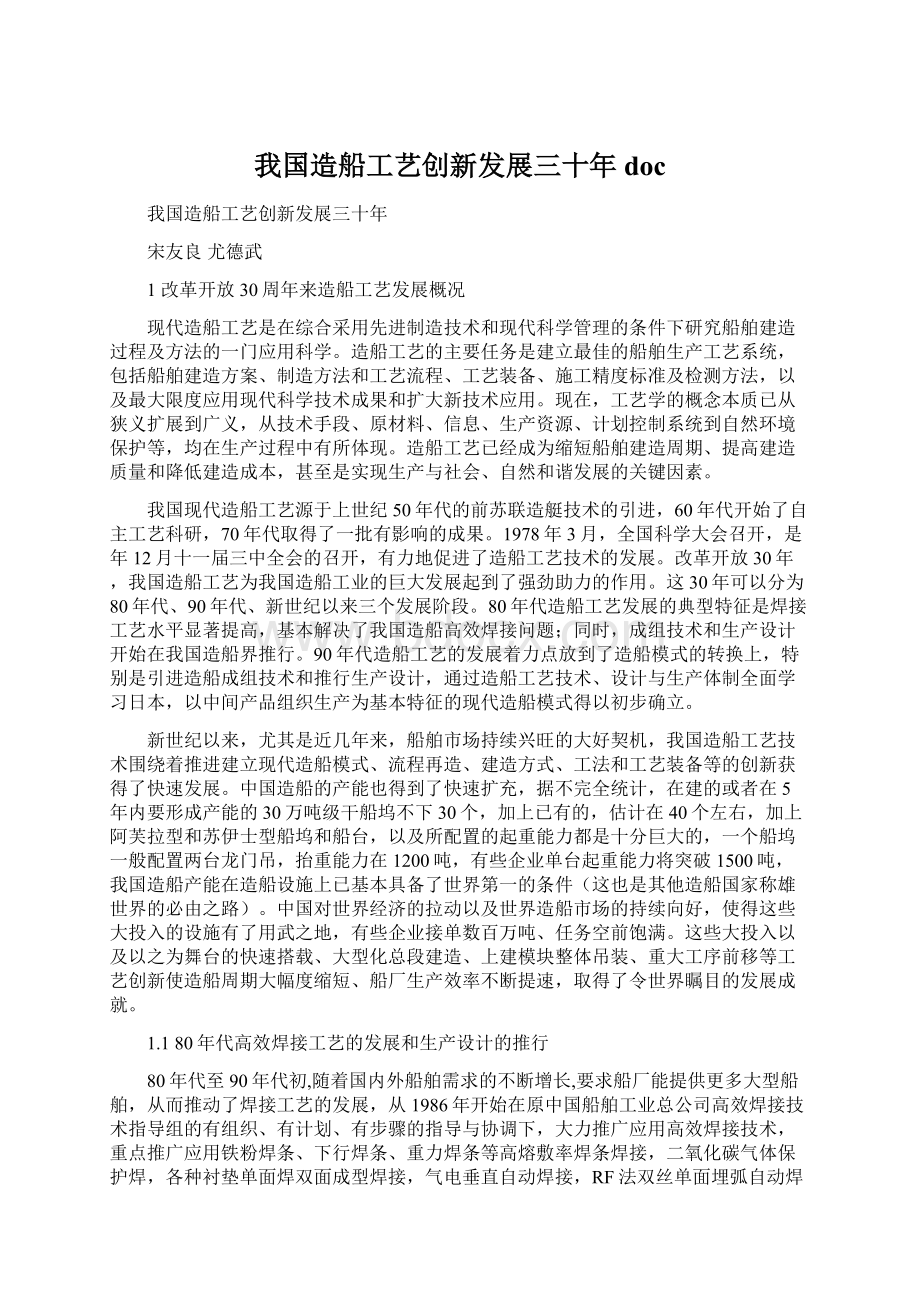
我国造船工艺创新发展三十年doc
我国造船工艺创新发展三十年
宋友良尤德武
1改革开放30周年来造船工艺发展概况
现代造船工艺是在综合采用先进制造技术和现代科学管理的条件下研究船舶建造过程及方法的一门应用科学。
造船工艺的主要任务是建立最佳的船舶生产工艺系统,包括船舶建造方案、制造方法和工艺流程、工艺装备、施工精度标准及检测方法,以及最大限度应用现代科学技术成果和扩大新技术应用。
现在,工艺学的概念本质已从狭义扩展到广义,从技术手段、原材料、信息、生产资源、计划控制系统到自然环境保护等,均在生产过程中有所体现。
造船工艺已经成为缩短船舶建造周期、提高建造质量和降低建造成本,甚至是实现生产与社会、自然和谐发展的关键因素。
我国现代造船工艺源于上世纪50年代的前苏联造艇技术的引进,60年代开始了自主工艺科研,70年代取得了一批有影响的成果。
1978年3月,全国科学大会召开,是年12月十一届三中全会的召开,有力地促进了造船工艺技术的发展。
改革开放30年,我国造船工艺为我国造船工业的巨大发展起到了强劲助力的作用。
这30年可以分为80年代、90年代、新世纪以来三个发展阶段。
80年代造船工艺发展的典型特征是焊接工艺水平显著提高,基本解决了我国造船高效焊接问题;同时,成组技术和生产设计开始在我国造船界推行。
90年代造船工艺的发展着力点放到了造船模式的转换上,特别是引进造船成组技术和推行生产设计,通过造船工艺技术、设计与生产体制全面学习日本,以中间产品组织生产为基本特征的现代造船模式得以初步确立。
新世纪以来,尤其是近几年来,船舶市场持续兴旺的大好契机,我国造船工艺技术围绕着推进建立现代造船模式、流程再造、建造方式、工法和工艺装备等的创新获得了快速发展。
中国造船的产能也得到了快速扩充,据不完全统计,在建的或者在5年内要形成产能的30万吨级干船坞不下30个,加上已有的,估计在40个左右,加上阿芙拉型和苏伊士型船坞和船台,以及所配置的起重能力都是十分巨大的,一个船坞一般配置两台龙门吊,抬重能力在1200吨,有些企业单台起重能力将突破1500吨,我国造船产能在造船设施上已基本具备了世界第一的条件(这也是其他造船国家称雄世界的必由之路)。
中国对世界经济的拉动以及世界造船市场的持续向好,使得这些大投入的设施有了用武之地,有些企业接单数百万吨、任务空前饱满。
这些大投入以及以之为舞台的快速搭载、大型化总段建造、上建模块整体吊装、重大工序前移等工艺创新使造船周期大幅度缩短、船厂生产效率不断提速,取得了令世界瞩目的发展成就。
1.180年代高效焊接工艺的发展和生产设计的推行
80年代至90年代初,随着国内外船舶需求的不断增长,要求船厂能提供更多大型船舶,从而推动了焊接工艺的发展,从1986年开始在原中国船舶工业总公司高效焊接技术指导组的有组织、有计划、有步骤的指导与协调下,大力推广应用高效焊接技术,重点推广应用铁粉焊条、下行焊条、重力焊条等高熔敷率焊条焊接,二氧化碳气体保护焊,各种衬垫单面焊双面成型焊接,气电垂直自动焊接,RF法双丝单面埋弧自动焊接,熔咀电渣焊接等高效焊接新工艺、新技术和新装备,基本解决了我国造船高效焊接问题,焊接质量和效率得到了很大提高。
1982年上海船厂引进了挪威TTS平面分段流水线;1985年沪东造船厂在生产线上采用船舶工艺研究所设计制造的双丝埋弧自动焊机,实施压力架式的FCB(焊剂铜垫法)双丝单面埋弧自动焊接工艺,1988年又自行设计研制焊剂垫装置,配置进口双丝埋弧焊机实施RF法焊接工艺,提高焊接效率3~4倍;1990年和1991年,江南造船厂相继解决了LPG船等高强度钢、特种钢的焊接工艺难题。
80年代,通过与日本造船业的技术合作,我国大连造船厂、新港船厂、沪东船厂、广州船厂等开始推行生产设计和电算化,将造船的工艺流程和工人在现场施工中需要思考解决的造船工艺问题搬到设计阶段由技术人员来解决,生产设计理念和方法的引入,开创了我国造船生产设计的先河,由此揭开了我国造船模式转换的序幕。
1.290年代造船模式转换
1990年,原中国船舶工业总公司针对建造出口船严重脱期,导致违约罚款的被动局面,召开了“第一次缩短造船周期”会议,要求全行业千方百计缩短造船周期,重点在贯彻全系统、全过程、全方位的“超前准备”。
同时,原中国船舶工业总公司组织了“缩短造船周期的对策”课题研究,得出“缩短造船周期的根本对策是建立现代造船模式”这一正确结论,由此拉开了我国造船模式由传统向现代转换的进程。
广州船厂在80年代中期在全国率先引进日本IHI公司的造船模式,而后,参照《造船成组技术》理论不断改进,并按成组技术原理新建了我国第一个现代化管子车间。
1995年,原中国船舶工业总公司召开了“第二次缩短造船周期”会议,会议主题由强调“超前准备”转移到以空前的行政力度部署推进实施现代造船模式。
会上,“生产设计、成组技术指导组”提出转变造船体制的措施,主要是建立符合成组技术原理按中间产品导向的作业组织,实现造船全过程的生产设计,编制壳舾涂一体化的造船计划,运用编码系统和托盘集配技术等。
1996年,原中国船舶工业总公司调动我国造船界各路精英,成立由国家科技部下达的“现代造船模式研究”课题组,采用软科学与硬技术相结合的方式,分设“国外先进造船技术跟踪”、“船体分道建造”、“船舶区域涂装”、“船舶建造精度控制”、“船舶机械化、自动化焊接”、“船体曲板加工”等11个研究专题,1999年结题,通过课题研究和示范应用,基本完成了我国造船模式现代化转型的历史任务,确立了以中间产品组织生产为基本特征的总装造船模式,从而为即将到来的21世纪造船工业的大发展作了理念、方法上的准备,也为造船工艺大发展开创了广阔的空间。
1.3新世纪以来的大发展
新世纪以来,我国造船工业和世界船舶工业一同保持了高度繁荣,中国造船工业“世界第一”的国家战赂驱动着我国造船领域极为广泛地创新,造船工艺技术进入快速发展通道。
(1)建立现代造船模式的推进工作有力助推了造船工艺的发展
原国防科工委为加快建立现代造船模式的步伐,提升船舶制造技术水平,增强产业国际竞争力,推动我国船舶工业持续、快速、协调、健康发展,于2004年发布《关于加快建立现代造船模式的指导意见》,着重提出了推行分段总组造船法、发展单元组装、预舾装和模块化技术、发展精度造船和先进涂装技术以及加强船坞(台)总装工艺方法研究等相关制造技术是推进建立现代造船模式支撑技术。
2006年,将加快建立现代造船模式提升到我国船舶工业实现做大做强目标的重要战略举措的高度,发布了《全面建立现代造船模式行动纲要(2006-2010年)》,明确提出加强总装造船工法研究与应用,包括总装造船工法的研究、全面推行分段总组建造法、大力推广精度造船、先进舾装和先进涂装技术等。
其间,通过“十五”高科技船舶科研渠道,下达了“现代造船模式的应用研究”项目,由两大造船集团所属骨干企业参加,共同开展了以中间产品为导向的涉及管理体制、总装流程、生产设计、生产技术准备、舾装件的设计与管理托盘化等8个方面的应用研究,2006年完成了项目验收。
近两年来,围绕上述的研究成果和应用实例编制了一系列设计、管理和作业指导书,向全国推广。
(2)新的生产设计理念和方法实现壳舾涂一体化设计
新世纪之初,上海外高桥造船有限公司投产并迅速发展,取得骄人业绩,也为我国造船业贡献了新的理念和经验,其中,引进消化吸收韩国生产设计理念和方法,为实现壳、舾、涂一体化设计提供了方式和途经。
在生产设计之前,需要整理新船所有的船厂惯例和标准,即SDP(ShipbuildingDesignPractice),SDP涵盖了建造流程、生产设备与设施的能力、各部门工作职责以及国标、厂标等,还包括具体的设计标准和方法,如船体设计的套料和钢材管理、切割、成型、坡口、校正、焊接、装配等工艺标准和方法。
通过SDP设计使设计过程简单化、标准化,最大限度地规范设计行为。
在研究船体分道建造流程的基础上,完成模拟船体分段的组立过程设计,即DAP(DetailAssemblyProcedure),从小组立开始到一个分段大组立结束,组立的基准面、重量、上下层组立关系,组立场地或区域全部表示清楚,以指导船体生产设计。
DAP设计:
满足作业场地、设施要求;充分考虑到分段组立过程中工艺,如搬运、堆放等;为工人施工提供良好的作业环境;为实行高效焊接方法和提高焊接质量提供便利;有利于实行先行舾装,特别是提前完成结构化舾装;最大限度扩大中小组立,使大组立胎架时间最短;分段组立过程的精度控制点,在各组立阶段需要得到控制;分段吊马利用本身船体结构来处理,最大限度减少在外板上设置吊马;各阶段所用的脚手架马板全部在中小组立阶段完成等。
在研究舾装生产流程的基础上,完成WSD(WorkSequenceDiagram),指导舾装生产设计,包括单元、托盘的划分。
各区域的预舾装、单元组装、涂装设计和工艺要点是WSD设计的重中之重,按照各区域中小组立、分段、总段、坞内及码头不同阶段,分别规定结构舾装件、铁舾件、管舾件、电舾件、主要设备和基座的安装阶段和技术要求,由此,生产设计时按照WSD的策划来划分托盘,同时建立于作业阶段、区域、类型的任务包。
(3)工法的引入产生巨大的生命力
韩国船厂高度重视工法技术研究,将其视为船厂竞争力的核心要素,一般都设有专门的工法部门,主要任务是开展各船型建造工法策划、新工法研究与创新等。
所谓工法,是船厂工程师和生产者在生产实践中共同探索、不断改进而形成的自己独特的新工艺、新技术、新设施、新工作方法,可有效促进生产效率提高和成本下降。
外高桥造船公司率先引入工法概念,成立工法技术室,负责承担公司生产流程与布局研究、各种新船型的建造方案研究、新工艺新技术新材料应用研究和推广实施,编制和发布各船的核心建造工法,全公司工装的开发以及收集、整理和研究国内外工法情报。
近几来年,外高桥造船公司通过学习国内外先进工法技术,并结合企业自身实际广泛开展工法研究和工法创新工作,形成了一批工法新成果并得到应用,产生了巨大的生命力,不仅为公司降本增效和提高综合争力作出了巨大贡献,而且在国内造船业产生深远影响。
目前,我国主要造船企业,不管其所有制和隶属关系,均引入了工法概念,很多企业还设立了专门机构,负责学习和研究工法技术,源源不断地进行工艺方法的创新,极大地提高了生产效率、缩短了建造周期和降低了造船成本,也改善了工人的作业条件和环境。
2壳、舾、涂工艺创新
改革开放30年来造船工艺的创新和快速发展,大大扩展和丰富了造船工艺技术的内涵。
随着船市持续火爆和国内外众多资金涌入造船业,在船舶工业大发展带动下,造船工艺和工装也进入快速发展通道,各种新技术、新装备也应运而生。
2.1建造方式和船体建造工艺
(1)建造方式的发展
新世纪以来围绕船厂核心资源能率最大化和快速造船这个核心,以中间产品为导向组织生产的原则和方法在建造方式上,借助造船设施扩充的有利条件获得了空前的发展。
分段总组建造法。
零件切割加工后增加了部件中小组立工序,然后集配后送平、曲两个分段大组立,在分段舾装和涂装后实施分段平地总组,即进行总段建造和总段舾装,在船坞(台)仅进行总段搭载。
这一作业主流程已经成为我国大型造船企业(包括两大集团骨干造船企业和地方新兴造船企业)的主流,己基本摒弃过去船坞(台)进行分段塔式建造方式。
一坞多造的串并联建造方式。
一次排楞工艺、不同船型间的互补通用坞墩布置工艺、坞墩专用工装、横向串联造船的起浮转向工艺、纵向串联落墩的定位工艺及进出坞工艺等都获得了突破,并不断取得新的发展,如外高桥造船公司的双岛建造法,大连船舶重工集团的湿法两段(三段)建造法等,大大地缩短了船坞周期,一年内开坞门的次数(批次)成为衡量造船能力的主要指标。
快速搭载的相关工艺。
采用扩大分段总组范围等方式来实现快速搭载,将若干分段总组成非环行总段进行船体建造,实施大型总段吊装,促进坞内装焊接、舾装作业前移,减少坞内工作量,达到快速搭载的目的。
如机舱双层半立体总组、货舱底部分段全宽型总组、横隔舱与甲板进行总组等。
先进工装为快速搭载助力,如分段总组和总段搭载时的箱式胎架、活络支墩、液压顶升设备以及专门开发的特殊支撑等先进工装可实现分段(总段)的快速定位和吊车的快速松钩。
上建整体吊装。
国内多家船厂实现了上层建筑整体吊装,上建吊装前已达到较高的结构完整性,完成了封舱件安装、管线安装、各层甲板设备安装、内舾装施工及主体外表涂装等作业结束,有的甚至可通电通水。
上海船厂实现了异地定点制造,从而腾出了船台附近宝贵的总组场地,避免与船台搭载争资源,使得船台周期屡创记录。
精度控制水平显著提高。
我国三大主力船型分段无余量拼板制造率达到70%以上,分段无余量上船台(进坞)率均达到95%以上,精度控制为快速建造和快速搭载创造了必要条件。
(2)船体建造的机械化、自动化
——高效焊接技术
改革开发以来,我国广大造船焊接科技人员一直致力于造船焊接工艺方法的多样化,目前已有40多种造船焊接工艺方法并获得有关船级社认可。
高效焊接技术除了在散货船、油船、集装箱船等主力船型上应用之外,还在液化天然气船(LNG)、液化石油气船(LPG)、大型集装箱船、海洋浮式生产储油船(FPSO)、超大型油船(VLCC)、滚装船、水翼船等高技术、高附加值船舶上获得广泛应用。
我国造船业焊接高效化率目前已达到90%以上。
船舶高效焊条、CO2气体保护实心焊丝、CO2气体保护药芯焊丝、单面焊衬垫、CO2气体保护电弧焊、多丝埋弧焊机、逆变焊机、气电垂直自动焊机、横向自动焊机、自动平角焊机、双丝MAG焊机等已全面推广应用,并先后实现了国产化。
我国船厂焊接设备结构比例逐步调整,至新世纪头五年,基本淘汰了耗能大、效率低的旋转式直流焊机,增长迅速的半自动CO2气体保护焊机已成为船厂的主要焊接设备,其量大面广为推广高效焊接工艺奠定了装备条件。
我国高效节能型焊接设备应用率达95%以上。
与此同时,上海船舶工艺研究所改革开发以来,几十年与船厂密切合作,连续不断地开发了CO2气体保护半自动焊接电源、便携式逆变TIG焊机、气体保护自动角焊机、双丝气体保护自动角焊机、双丝MAG自动焊机、管子机器人自动焊接流水线等自动焊接新工艺新设备,使船厂在制造平面分段和平直立体分段的焊缝时均可以实现机械化和自动化焊接。
——切割技术
自动化热切割技术在造船行业内经历改革开放30年来的持续发展,如今已全面进入一个崭新的阶段,数控火焰切割、数控等离子弧切割、数控激光切割、数控管子相贯线切割、机器人型材自动切割等先进自动化热切割技术先后在我国造船行业获得应用,从根本上解决了困扰船舶建造周期中的钢板下料切割的瓶颈。
——T型材自动装焊流水线
T型材自动装焊流水线已经实现国产化,并在我国新建的大型船厂安装使用。
流水线不仅提高了装焊效率,而且通过在焊接区域下面横梁建立拉伸应用的方法来防止横梁的焊接变形,保证装焊质量。
——数控水火弯板和曲板成形
广船国际与上海交大开发成功的数控水火弯板机已投入使用,突破了复杂曲面外板水火加工成形技术。
上海船舶工艺研究所也与外高桥造船公司合作研发数控板材线加热曲板成形自动化装备,其应用软件能与Tribon船体建造系统软件匹配,能根据Tribon输出的目标形状,进行最佳加热路径规划,直接输出数控指令,以控制高频感应头的扫描速度、温度等参数,能够实现大型船用板材线加热自动化加工成形。
另外,国内科研机构和有关厂家已经研发成功并投入使用的船体加工新工艺新装备还有数控肋骨冷弯机、型材自动化加工生产线、部件装焊生产线、纵骨生产线、拼板自动焊接、平面分段流水线等机械化、自动化装备和设施,极大地提高了生产效率和建造质量。
2.2船舶舾装工艺
(1)区域舾装
改革开发以来,我国船舶舾装工艺由传统舾装、预舾装发展为区域舾装。
80年代伴随着综合放样技术的引入,预舾装开始取代完全先船体后舾装的传统舾装。
预舾装将传统的码头、船内的舾装作业提前到分段、总段上船台(入坞)前进行,实现高空作业平地做,外场作业内场做,仰装作业俯装做,减少码头、船内多工种的混合作业,大大提高了生产效率,缩短了造船周期。
90年代末期随着现代造船模式转换的深入,区域舾装得以推行。
区域舾装即按船舶区域进行舾装,包括按船舶区域进行设计,进行船舶区域内舾装件的综合布置,按船舶区域划分绘制舾装安装图、零件图,并尽可能地进行舾装单元设计和托盘化设计,编制区域托盘管理表,施工部门(一般为综合施工组织)按照区域进行舾装作业。
区域内的舾装件尽可能被设计为各种单元,这些单元单独进行制造或组装,然后在该区域船体建造的分段阶段、或总段阶段进行安装,这样舾装与船体建造实现了平行作业,船体与舾装分道建造、有序组合,使作业效率大幅度提高,作业环境得到很大改善,作业质量也有了保证。
目前,我国三大主力船型上船台(进坞)前管子预装率和铁舾件预装率都在85%左右。
2000年以来,特别是引入工法技术概念和先进的生产设计方法(WSD设计),一些先行舾装工艺不断推出,一些重大的工序前移对缩短周期、改善作业条件起到了重要支撑作用。
如沪东中华造船集团将轴舵系镗孔提前到分段阶段;外高桥造船公司在半岛起浮前镗孔塞轴,下一步再提前到总段阶段,大大缩短了坞内工作量;上船公司3500TEU船的集装箱导架、箱脚、货舱风机、风管、管系、铁舾件全部实现分段预装,带缆桩、弦墙栏杆、导缆滚轮、锚绞设备等实现了总段预装,机舱区域实现了环型总段单元及模块安装,从而刷新船台周期新记录。
舾装单元(模块)组装不断增加,外高桥造船公司等一些先进企业一般一条船有60-80个单元(模块),还设置了专门的单元(模块)组装场地,广船国际还将管子、设备单元(模块)的附件一并进行统筹设计,实现机舱底部全单元化设计,其中管子单元的组装量占到全船管子的35%以上。
大连船舶重工集团组建了以管子加工、附件配套和单元组装为主体的舾装公司,其中单元制作中心是为满足总段舾装和船台(坞)舾装的需要而设置的具有创新意义的生产单位,将原来需要在船上或者分段上零散装配的管子、舾装件、设备等在平地上,按照船舶结构和分段的要求,进行组装,形成符合分段、总段和船台(坞)阶段安装的中间产品。
托盘管理水平不断提高。
托盘管理成为区域舾装的基本物流方式,依托生产设计对不同阶段/区域的舾装内容而编制的托盘管理表,进行舾装件的集配,按照作业阶段/区域送托到作业现场,使得整个舾装作业的物流组织科学、有序。
也有部分造船企业已将舾装件的托盘集配从总装造船生产作业中剥离出来,集中到配套企业(管子工厂或舾装公司)制造,由配套企业按照总装厂作业阶段/区域直接供托,实现生产、配送一体化,并向标准单元(模块)供应商发展。
(2)管件族制造
这几年我国配合新的造船基地建设而建设了多个专业化、自动化的管子生产线,管子制造不仅按照成组技术原理实现了管件族制造,而且实现了制造过程的自动化,并且部分自动化设备实现了国产化。
如上海船舶工艺研究所研制开发了我国首套船舶管子数字化柔性生产线,经上海江南船舶管业有限公司的实地现场试用,全套装备技术性能和各项技术指标接近国际先进水平。
这套装备由“管子定长切割”、“机器人管子—法兰自动焊接”、“管子—法兰点装”三部分设备组成,作业时,三大部分设备按生产流程有机联动,实现船舶管子从落料到管子成品的全过程自动化流水生产。
2.3船舶涂装工艺
——钢材预处理自动流水线
改革开发之初,我国造船工业为适应走出国门的需要,开始建设钢材预处理自动流水线,经过30年的发展已全面普及,实现钢材运输、矫正、除锈、涂漆、烘干等工序的自动流水作业。
——分段涂装
我国骨干船厂新世纪以来都建设了大型分段涂装厂房,一般都是几喷几涂,而且全部实现国产化装备,达到环保要求。
最近,中船龙穴造船基地建成符合IMO“PSPC”标准要求的涂装工场,该涂装工场由油漆车间、喷砂车间、冲水车间等组成,除配有先进的喷砂、喷漆等设备外,还装备分体风冷组合式除湿机、有机废气处理设备。
——跟踪补涂
由外高桥造船公司首先实施的分段涂装前跟踪补涂工艺,主要针对钢材经切割加工、小组立(部件)、中组立(片体)、大组立(分段)等施工阶段的建造过程中,因切割、冷热加工、壳舾装配、焊接、打磨、火工、吊运等造船车间底漆的局部区域破损,按照谁损坏谁修补的原则,而进行的表面清理与车间底漆修补。
这一工艺目前得到了推广应用,大大减少了二次表面处理的工作量,提高了涂装房的使用效率,缩短了涂装周期,降低了涂装成本。
——应对IMO“PSPC”标准
2006年12月8日MSC82会议通过了MSC.215(82)决议和MSC.216(82)决议,通过了IMO《所有类型船舶专用海水压载舱和散货船双弦侧处所保护涂层性能标准》(PSPC),规定在2008年7月1日及以后签定建造合同的,或无建造合同,在2009年1月1日以后安放龙骨或处于类似建造阶段的,或在2012年7月1日以后交船的船舶上实施。
这一标准涉及分段表面处理和涂装、表面缺陷处理、涂装前表面可溶性盐限制、灰尘、涂层厚度、合拢后的表面处理要求、涂层检查人员的资质要求、涂层的合格预试验和验证要求等多方面内容,对我国新造船的周期和成本带来重大影响。
我国船舶工业采取了积极的应对工作,中船集团成立推进小组,上海船舶工艺研究所受有关方面委托牵头组织开展了应对PSPC一揽子工艺对策研究,包括推进模拟实施和编制检验人员培训教材及实施培训;725所研究、设计、建设完成我国自己的符合PSPC附件1《船舶专用海水压载舱和散货船双弦侧处所保护涂层的资格实验程序》要求的验证试验室,制作了我国自己的模拟压载舱状况加速试验装置——模拟压载舱状况试验舱和冷凝试验舱,为涂层性能检测和验证试验提供了技术条件;中船龙穴建设了完全符合PSPC要求的分段涂装厂房。
大连船舶重工集团、广船国际等其他造船企业均通过对产品船的盐份/粗糙度/表面清洁度/涂层破损率进行了测试和统计分析,掌握了基础数据和测试方法,采取了设计、生产和管理方面的相应对策。
3造船工艺技术发展展望
我国造船业在改革开放之初,较早地融入到国际市场之中,经过30多年来的发展,特别是新世纪以来的大发展,奠定了我国造船大国的地位和基础,并正在向造船强国迈进,造船工艺在不断吸收国外先进技术的同时,大力进行自我创新,内涵不断得到丰富,新成果不断涌现,为我国造船业做大做强所做的贡献也越来越大,成为我国造船业核心竞争力的重要组成部分。
未来几年,我国造船业将成为世界第一,这其中除了继续加大投入之外,要想在激烈的国内外竞争中拨得头筹,造船工艺技术的不断创新无疑将起到关键性作用。
有专家提出我国造船业改革开放以来的发展可谓第一次现代化,尽管取得了巨大的成就,但仍处在第一次现代化的水平,而世界造船工业的发展已经进入第二次现代化的范畴,因此,我国造船工业的发展在较长时间内仍然处于第一次现代化的阶段,同时又必须叠加进第二次现代化的部分内容。
造船工艺的发展,一方面,要继续深化船体分道建造、区域舾装和区域涂装的工艺创新,围绕快速、高效造船,研发和推行巨型总段、大型单元、舾装单元(模块)生产线、激光或电感应加热外板成形、曲面分段流水线、船体结构机器人群焊接以及工序前移(并行)等工艺创新,加速向壳舾涂一体化的集成制造迈进。
同时,面对未来船市的不确定因素,我们又必须抓紧考虑造船工艺发展的战略转型。
要研发和攻克高端船舶(大型水面舰船、豪华游轮、巨型船舶、LNG船、特种舰船、大型先进海工产品等)的特殊建造工艺;要发展绿色造船工艺,减少建造过程的物资和能源消耗以及污染排放,如船体装焊的自动化、高效焊接技术、绿色涂装技术等,实现造船直接劳动者的健康作业以及造船生产与社会、自然和生态的和谐发展;要发展数字化造船,进行三维建模,在设计时以船厂的3D环境生成工艺过程虚拟仿真、作业计划、机器人操作、NC模拟和CALS物流系统等,生产前实施建造过程的CAE,获取相关的技术数据和管理数据;要研发造船的智能化,包括智能化设计系统和智能