铸钢工艺.docx
《铸钢工艺.docx》由会员分享,可在线阅读,更多相关《铸钢工艺.docx(88页珍藏版)》请在冰豆网上搜索。
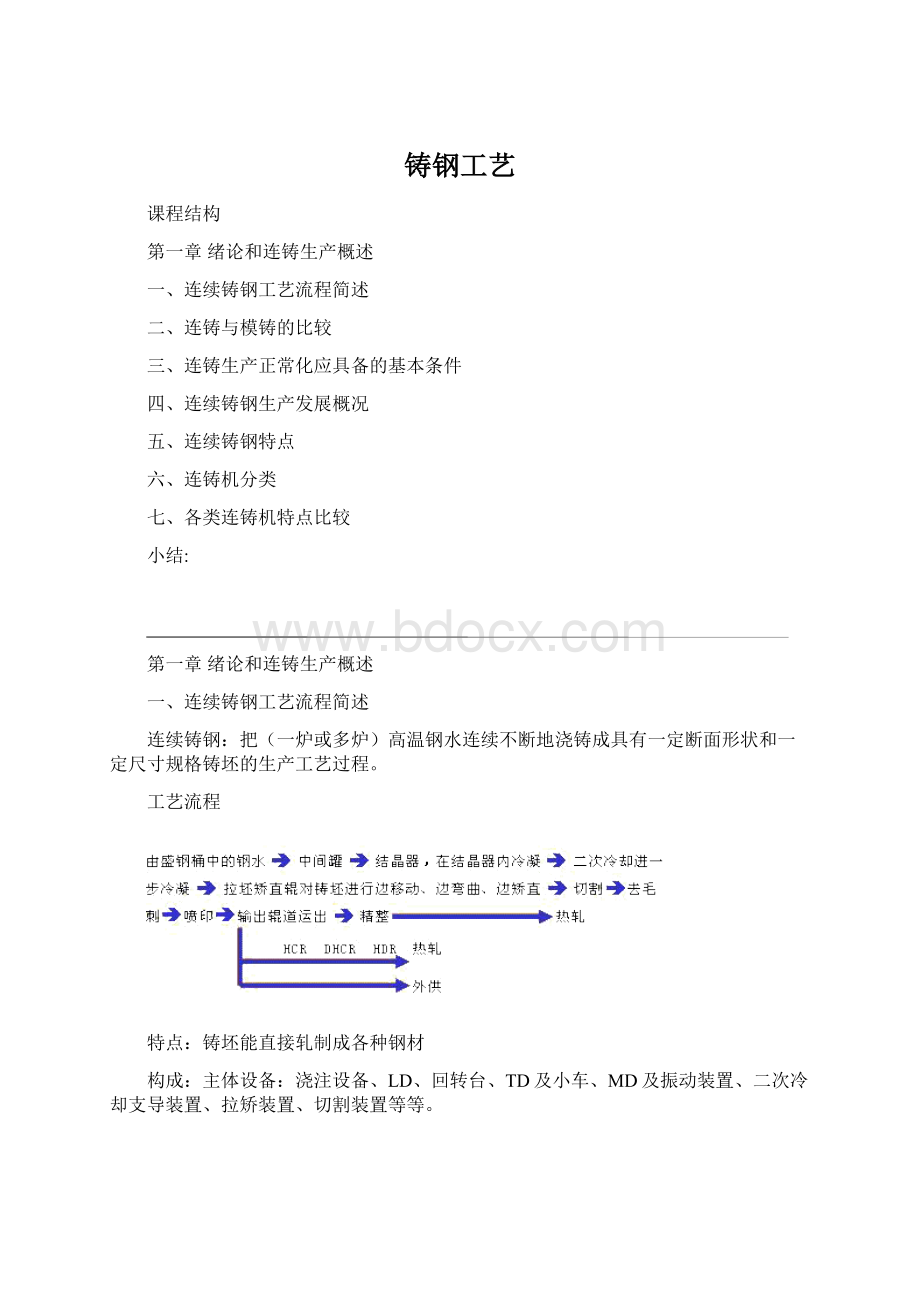
铸钢工艺
课程结构
第一章绪论和连铸生产概述
一、连续铸钢工艺流程简述
二、连铸与模铸的比较
三、连铸生产正常化应具备的基本条件
四、连续铸钢生产发展概况
五、连续铸钢特点
六、连铸机分类
七、各类连铸机特点比较
小结:
第一章绪论和连铸生产概述
一、连续铸钢工艺流程简述
连续铸钢:
把(一炉或多炉)高温钢水连续不断地浇铸成具有一定断面形状和一定尺寸规格铸坯的生产工艺过程。
工艺流程
特点:
铸坯能直接轧制成各种钢材
构成:
主体设备:
浇注设备、LD、回转台、TD及小车、MD及振动装置、二次冷却支导装置、拉矫装置、切割装置等等。
一台连铸机组成:
1)盛钢桶(盛钢桶支撑设备)2)中间包(中间包小车)3)结晶器(结晶器振动装置)4)二次冷却装置5)拉坯(娇直)装置6)切割装置(去毛刺装置)(喷印装置)7)铸坯运出装置等。
图1-1带有直线段多半径弧形连铸机1-盛钢桶;2-中间包;3-结晶器;4-二次冷却;5-拉矫装置;6-切割装置;7-运胚和检验装置
二、连铸和模铸的比较
1)模铸工艺流程简述
模铸:
按炉将盛在盛钢桶内的钢水注入到具有一定形状和尺寸的钢锭模中铸成钢锭的浇注工艺。
特点:
钢锭需经过初轧机轧制成钢坯,然后再进一步轧制成各种钢材。
2)连铸和模铸生产工艺比较图
连铸具有的优越性:
提高综合成材率;降低能耗;连铸产品的均一性高、质量好;易于实现机械化自动化。
三、连铸生产正常化应具备的基本条件
完好的设备状态-实现连铸生产正常化的根本保证;
完善的炼钢工艺-是连铸生产正常化的基础;
科学的管理-是保证连铸生产的连续性和稳定性;
高水平的人员素质-是搞好连铸生产的重要条件;
同步发展新工艺新技术-满足连铸生产发展的需要。
四、连续铸钢生产发展概况
五、连续铸钢特点
(1)简化了钢坯生产的工艺流程,节省大量投资,省去了模铸工艺中脱模、整模、均热及初轧等工作。
(2)提高了金属收得率和成材率。
(3)提高了钢坯质量。
(4)改善了劳动强度,提高了劳动生产率,而且有助于铸钢生产的连续化和自动化。
(5)节约能量消耗。
六、连铸机分类
各类连铸机机型简图
七、各类连铸机特点比较
小结
在钢铁工业史上,钢坯一直是用模铸法生产出钢锭后经开坯而成。
这种不连续的生产方式,工序复杂、效率低、金属损失大,成了钢铁生产的一个限制环节,严重阻碍了钢铁生产的发展。
连铸工艺的出现,无疑是浇注技术的重大突破和飞跃,最终使钢铁生产连续化和自动化。
用连铸工艺代替模铸工艺的发展形势已经成为当代钢铁工业的主要技术特征和发展方向。
第二章钢水浇注的基础理论
一、钢液的结晶过程
二、连铸坯的凝固
三、铸坯在二冷区的凝固和传热
四、连铸坯的凝固结构及控制
小结:
第二章钢水浇注的基础理论
一、钢液的结晶过程
结晶:
是从金属学的原理出发,研究金属熔体中晶核的形成和长大,以及由此而产生的结晶组织。
凝固:
是从传热原理出发,研究铸坯不同部位的凝固过程,凝固速度以及伴随发生的物化现象。
1.钢水结晶凝固的必要条件-必须过冷、且须有结晶核心
理论结晶温度(T液、TL、Tm);实际结晶温度(Tn、T);“过冷”现象;过冷度:
ΔT=(T液-T);结晶潜热(Lf):
钢水在由液相转变为固相时,系统的自由能(ΔG)也随之变化(见图-1):
图-1 液、固态金属自由能与温度的关系 图-2
2.晶核的形成与晶体的长大
(一)晶核的形成
金属结晶时,由于结晶条件不同,将出现两种不同的形核方式,即:
1、自发形核-均质形核
2、非均质形核(异质形核)。
1、自发形核(均质形核):
结晶时直接从熔体中产生晶核(这一过程只有引起系统自由能降低才能自发进行)
其中GA:
为A相体积自由能;σ为A、B两相界面能GB:
为B相体积自由能;
形成新相晶核自由能变化为:
自由能(ΔG)与晶核半径(r临)的关系:
1.r临与过冷度的关系:
2.r<r临:
ΔG增加,晶核不能长大;
3.r>r临:
ΔG降低,晶核能够长大;
4.r=r临:
晶核的长大和溶解处于平衡;
5.r=r临与临界形核功的关系:
图2-1自由能与晶核半径关系
结论是:
在一定温度下,任何大于临界半径的晶核趋向于长大,小于临界半径晶核趋向消失。
同时,要形成稳定的晶核,必须有过冷度和与过冷度相适应的液相能量起伏。
过冷度越大,临界半径(r临)值就减小,临界形核功(ΔG*)也随之减小,形核就越容易且稳定。
也就是说能量涨落是晶核形成的动力学条件。
均质形核时的形核率与过冷度的关系
均质形核需要有0.2Tf的过冷度
形核率与过冷度的关系
2、非均质(异质)形核:
(借助于存在熔体中的异相固体而形核的过程)
1)非均质形核理论
如在一个平面的夹杂物上形成一个半球缺的固体晶核(图2-2)。
晶核与液体、固体有三个交界面,处于平衡时有:
2-6
式中:
σ为界面张力;θ表示晶体在夹杂物表面的润湿倾角。
得到:
图2-2在平面上形成球冠晶核
2)非均质形核功ΔG非*与均质形核功ΔG*的关系
由(2-8)式可知:
非均质形核功与均质形核功相差(2-3cosθ+cos3θ)/4
其中 ①当θ=1800,cos1800=0,晶体独立于液体中,形核功与均质形核相同;
②当θ=00,cos00=1,ΔG非*=0,液体中质点已是一个晶核,不需任何过冷度就可形核;
③当0<θ<1800,依附于外来质点形成晶核。
式中看到:
非均质形核的有效性决定于润湿角θ。
θ越小,形核功就越小,就易形核。
非均质形核所需的能量起伏,相起伏和过冷度远远低于均质形核,且临界形核功较小和能在较小的过冷度下具有较高的形核率。
3)均质形核和非均质形核的形核率与过冷度的关系
非均质形核的过冷度比均质形核大为减少,约为0.02Tm
均质形核和非均质形核的形核率与过冷度的关系
主要原因:
1.模壁(结晶器壁);2.活性质点;3.非活性质点。
均质和非均质形核都是在一定条件下自由能降低的过程,所以它们都是自发的过程。
4)晶核的长大
晶核长大-是原子或原子团按一定规律向晶核表面不断堆积的过程,也就是相界面向液相推移的过程。
生长方式-树枝状
成因:
一般晶体散热是在散热最快的地方优先生长,由于棱角比其他地方导热性好,所以棱角方向长大速度快。
而铁为立方晶格,呈正六面体结构,从八个角长成为菱锥体的尖端,就构成了树枝晶主轴,然后在主轴侧面长出分叉-二次轴、三次轴直至相遇,形成晶粒。
形核速率(N)、晶核长大(V)与过冷度关系
影响冷却速度最重要的因素是凝固方法
二、连铸坯的凝固
连铸坯冷凝过程,实质上是一个强制传热、尽快地加速钢液冷凝过程。
1.凝固特点:
1)钢液的过热:
即从浇注温度冷却到钢的液相线温度所释放出的热量;
2)结晶潜热:
即完成从液相到固相转变的过程中所放出的热量;
3)钢坯的显热:
即钢从固相线温度冷却到室温所放出的热量;
连铸坯冷却示意图
连铸坯的冷凝是由结晶器一冷、二冷、三冷完成,使坯壳在边运行、边放热、边凝固的过程,将产生以下特点:
1)可形成很长的液相穴
2)坯壳固-液两相区的凝固前沿晶体强度和塑性都很小
3)金属将发生的δ→γ→α相变
结论:
增加高温脆性,易产生裂纹
2.钢液在结晶器内的凝固
目的:
迅速带走钢液大量的热,使铸坯尽快形成均匀且具有一定厚度的坯壳,以抵抗钢液的静压力,保证铸坯在拉出结晶器时有足够的强度,而不致发生拉漏事故。
(1)结晶器内坯壳的形成分为:
1)弯月面区
2)紧密接触区
3)气隙区
1)弯月面区
①形成:
注入到结晶器内的钢液由于表面张力的作用在表面上很快形成了一层具有弹性簿膜性能的弯月面。
②性能:
能抵抗剪切力。
随着结晶器的振动,向弯月面下输送钢液而形成新的固体坯壳弯月面的作用决定于曲率半径。
③影响因素:
夹杂物(如Al2O3)
④措施:
采用保护渣浇注
钢液与铜壁弯月面的形成
2)紧密接触区
①形成:
初生坯壳在钢液静压力的作用下被推向结晶器铜壁并与之紧密接触而形成。
②传热方式:
传导传热。
图2-6铸坯表面组织的形成
a—坯壳与铜壁紧密接触;b—坯壳产生气隙
3)气隙区
①形成:
坯壳凝固到一定厚度时,发生δ→γ的相变,引起坯壳收缩,牵引坯壳向内弯曲脱离铜壁,而形成。
特别在角部区域,由于二维传热,坯壳凝固最快,最早收缩而首先形成。
②特性;在钢液静压力的作用下处于气隙形成和消失的动态平衡过程中。
③传热方式:
辐射和对流;
④影响结果:
传热减慢,凝固速度降低,坯壳减薄,强度降低,在钢液静压力的作用下,坯壳将发生变形,另外在角部由于气隙的产生,推迟凝固,使角部坯壳最簿,易产生裂纹和拉漏。
图2-7 结晶器内气隙的形成过程 图2-8 横向气隙形成
(二)坯壳的生长规律
服从:
凝固平方根定律
式中 δ-坯壳厚度,mm;
K-凝固系数,mm/min1/2;
t:
凝固时间(min)
L:
结晶器有效长度(㎜)
V:
拉坯速度(㎜/min)
保证铸坯出结晶器下口厚度的措施:
1)K值的选择
2)结晶器操作
3)保护渣的选择
(三)钢液在结晶器内凝固的影响因素
1)结晶器中钢液的散热,分为水平和垂直方向(垂直方向的散热较小,可忽略不计)
3)由于气隙的热阻最大,因而是结晶器传热的限制性环节。
显然要改善结晶器的传热,就得减少气隙。
A结晶器设计参数对传热的影响
(1)锥度的影响(作用:
良好的接触,以减小气隙,增加热流,加速结晶器内坯壳的生长,要点;结晶器内部形状应与坯壳的冷却收缩相适应。
铸坯线收缩量可根据ΔL=βΔT来确定);
(2)长度的影响(作用:
上部-热量输出,下部-支撑);
(3)材质的影响(要求:
导热性好,抗热疲劳,强度高,高温下膨胀小,不易变形);
(4)内表面形状的影响(传热面积);
B.操作因素对结晶器传热的影响
这一节内容包括:
(1)冷却强度的影响
(2)冷却水质的影响
(3)结晶器润滑的影响
(4)拉速的影响
(5)钢液过热度的影响
(6)钢液成分的影响
(1)冷却强度的影响(要点;冷却水应保证迅速地将钢液凝固所放出的热量带走,使铜壁冷面上没有热的积累,以防止结晶器发生永久变形)
①强制对流:
热流与铜壁温度呈线性关系,水流速增加,热流增大。
②水沸腾:
靠近铜壁表面过热的水层中,有水蒸气生成并产生沸腾此时传热不取决于水流速,而主要取决于铜壁表面的过热和水的压力。
③膜态沸腾:
温度超过某一极限值时,靠近铜壁表面的水形成蒸汽膜,热阻增大,热流减小。
改善结晶器传热:
1.水缝中的水速大于6米/秒;
2.控制进水与出水温差在5~6℃
3.结构合理
结晶器铜壁与水的界面状态和热流的关系
(2)冷却水质的影响-对热流影响,控制水质,应用软水。
(3)结晶器润滑的影响-减小拉坯阻力、改善传热。
(菜子油作用:
高温下裂解为碳氢化合物;保护渣:
高温下形成渣膜)
(4)拉速的影响-高拉速,能增加结晶器导出的平均热流,但使单位质量的钢液从结晶器中导出的热量减少,致使坯壳减薄。
(5)钢液过热度的影响-过热度对结晶器热流、铜板温度无关,而与出结晶器坯壳的表面温度有关,影响坯壳强度。
(6)钢液成分的影响-主要是钢中碳含量对热流、坯壳收缩、偏析的影响。
从影响结晶器凝固传热的因素可知,结晶器是一个复杂的传热系统。
了解结晶器导出热流的大小和变化,以及它与坯壳生长厚度的关系,可作为调整结晶器热工状态的依据,使结晶器工作最佳化。
图2-9钢中含碳量与热流的关系
三、铸坯在二冷区的凝固和传热
作用:
对出结晶器一次冷却后的铸坯内部仍为高温钢液进行二次喷水冷却,使其逐渐完全凝固。
关联:
产量、质量
1.二冷区的凝固传热
A:
铸坯凝固传热机理:
水冷→形成温度→梯度产生传热动力
B:
传热方式与比例:
(1)纯辐射25%;
(2)喷雾水滴蒸发33%;
(3)喷淋水加热25%;
(4)辊子与铸坯的接触传导17%。
要点:
要提高二冷区的传热效率,获得最大的凝固速度,就必须尽可能地改善喷雾水滴与铸坯表面之间的热交换。
图2-11铸坯而冷传热方式示意图
2.二冷区凝固传热的影响因素
①铸坯表面温度(Ts)-与二冷水关系:
A:
Ts<300℃-热流随Ts增加而增加
B:
300℃C:
Ts>800℃-热流与表面温度无关,而随喷水强度增加,热流增大。
在二冷区铸坯表面温度仍在1000~1200℃,为此应通过改善喷雾水滴状况来提高传热效率。
图2-12铸坯表面温度与热流关系不同喷水强度
②水流密度(是指铸坯在单位时间单位面积上所 接受的冷却水量)
传热系数(αk)与水流密度(W)关系:
αk=A*W
A:
为常数
总的趋势水流密度增加,传热系数也增大
图2-13传热系数与水流密度的关系
③水滴速度-增加水速,可提高冷却效率
④水滴直径-水滴越细,传热系数越高
⑤喷嘴的布置
图2-15板坯在二冷区冷却水喷嘴布置方式图 2-14两种喷嘴对传热系数的影响
3.二冷区凝固坯壳的生长(服从于凝固平方根定律)
比水量:
是通过二冷区单位质量铸坯所接受的水量(L/kg)。
确定依据:
钢种、断面、拉速、冷却指数(I)
图2-16小方坯的凝固系数与冷却强度的关系 图2-17板坯的凝固系数与冷却强度的关系
4.铸坯的液相穴深度-是指铸坯从结晶器钢液面开始到铸坯中心液相完全凝固点的长度
液相穴深度可根据凝固平方根定律计算:
铸坯的液相穴深度与铸坯厚度、拉坯深度和冷却强度有关。
当拉坯速度为最大拉速时,所计算出的液相穴深度为连铸机的冶金长度。
连铸铸坯液相穴示意图
四、连铸坯的凝固结构及控制
1.连铸坯的凝固结构
(1)细小等轴晶带
(2)柱状晶带
(3)中心等轴晶带
图2-19连铸坯凝固结构示意图
图2-18连铸板坯凝固组织结构 1-中心等轴晶;2-柱状晶带;3-细小等轴晶率
(1)细小等轴晶带(激冷层)
①形成:
较大的过冷度,钢液的形核速率大大超过了晶核的长大速率。
②性质:
不同取向的细小等轴晶。
③影响因素:
钢水温度;
④控制:
浇注温度,冷却条件。
(2)柱状晶带
①形成:
坯壳收缩产生气隙,热阻增加,钢液的形核速率低于晶核的长大速率。
②性质:
排列整齐,平行于散热方向,具有定向性,对弧形连铸机,柱状晶的生长具有不对称性。
③影响因素:
坯壳与结晶器壁间气隙。
④控制:
浇注温度,冷却条件。
(3)中心等轴晶带
①形成:
柱状晶的不断发展,散热越来越膜,于是整个截面的温度逐渐变得均匀。
当中心钢液过冷到熔点以下时,就在整个残留的钢液中同时出现晶核而凝固。
②性质:
粗大,无规则排列。
③控制:
浇注温度,冷却条件。
2.“小钢锭”结构
1)形成:
柱状晶不均匀生长而产生“凝固桥”。
2)影响因素:
二冷区不均匀的冷却。
3)性质:
铸坯中心疏松或缩孔,中心偏析。
4)控制:
二冷区铸坯均匀冷却、低过热度浇注、电磁搅拌等措施。
“小钢锭”结构示意图
连铸坯凝固特点:
连铸坯:
除了头尾以外,铸坯在长度方向上结构比较均匀。
就各结晶带而言,连铸坯由于受结晶器通水冷却,其激冷层比模铸钢锭要厚,晶粒更细,而且还可以得到没有侧枝的细柱状晶。
由于二冷区喷水冷却,铸坯内外温度梯度大,而使柱状晶比模铸钢锭发达,并容易形成穿晶成“小钢锭”结构,在凝固桥下部有中心缩孔和中心疏松形成。
由于柱状晶带宽,故与模铸钢锭比较,中心等轴晶带要窄得多。
连铸坯组织比钢锭致密。
小结:
本章讲的是钢水浇注成铸坯,必须要经过结晶和凝固,而此过程则必须使钢水得到过冷度。
过冷度越大则系统自由能差也就越大,形核越容易,晶粒越细。
连铸坯的凝固是一个热量的传输过程,要经过结晶器、二冷及辐射三个冷却区的互相联系的收缩阶段,由于冷却条件不同,如冷却水、温度、拉速成分等,都将影响铸坯的内、外质量。
通过本章学习,知道其中的原委而加以防止、改进。
课程结构
第三章 连铸设备
一、钢包、运载设备
二、中间包及其运载设备
三、结晶器
四、结晶器振动装置
小结:
第三章 连铸设备
一、钢包、运载设备
1.钢包
①钢包的作用及功能
②钢包容量的确定
③钢包形状的确定
④钢包的结构
⑤钢包耐火材料
⑥钢包滑动水口
⑦钢包长水口
钢包构造示意图
1.渣嘴;2.外壳;3.吊轴;4.支撑座;5.保温层;6.保护层;7.工作层;8.腰箍;9.倾翻机构
①钢包的作用及功能
作用:
具有盛装、运载、精炼、浇注钢水、倾翻、倒渣及落地放置。
②钢包容量的确定
确定原则:
容纳额定钢液量和约3%的炉渣及有10%左右的富余。
③钢包形状的确定
钢包的直径与高度之比-0.9~1.1。
锥度-10%~15%(大型钢包底应向水口方向倾斜3%~5%)
钢包外形(深粗比)-1~1.2
图3-1钢包各部位尺寸
④钢包的结构
(1)外壳;
(2)加强箍;(3)耳轴;(4)溢渣口;(5)注钢口;(6)透气口;(7)倾翻装置;(8)支座;(9)氩气配管
图3-2 钢包结构
1-包壳;2-耳轴;3-支撑座;4保温层;5-永久层;6-工作层;7-腰箍;8-倾翻吊环
⑤钢包耐火材料
(1)内衬结构-保温层、永久层和工作层组成;
(2)钢包耐火材料的工作环境。
1)承受的钢水温度比模铸钢包高。
2)钢水在钢包内的停留时间延长。
3)钢包内衬在高温真空下自身挥发和经受钢水的搅动作用。
4)内衬在承接钢水时受到的冲击作用。
5)熔渣对内衬的侵蚀。
(3)对钢包内衬的要求
1)耐高温,能经受高温钢水长时间作用而不熔融软化。
2)耐热冲击,能反复承受钢水的装、出而不开裂剥落。
3)耐熔渣的侵蚀,能承受熔渣和熔渣碱度变化对内衬的侵蚀作用。
4)具有足够的高温机械强度,能承受钢水的搅动和冲刷作用。
5)内衬具有一定的膨胀性,在高温钢水作用下,内衬之间紧密接触而成为一个整体。
(4)内衬的材质:
黏土砖、高铝砖、蜡石砖、锆石英砖、镁碳砖┉
⑥钢包滑动水口
作用:
是借助于盛钢桶外水口的滑动来控制钢流的开闭和调节钢流大小的控制装置。
组成:
由座砖、上水口砖、上滑板砖、下滑板砖和下水口。
(1)滑动水口耐火材料性能
工作环境:
使用中承受温度急变,钢液静压力,高温钢渣的冲刷和侵蚀。
材质:
应具有足够的高温强度、耐磨性好、耐冲刷、抗渣性好、热稳定性强的材料。
采用材质:
高铝质,莫来石刚玉质、刚玉质、镁质、铝碳质和铝锆碳质等。
图3-3 滑动水口耐火材料组成
1-座砖;2-上水口砖;3-上滑板砖;4-下滑板砖;5-下水口砖
(2)滑动水口工作原理
借助机械装置,采用液压或电动使滑板做往复直线或旋转运动,根据上、下滑板孔的相对位置,调节浇注钢水流量。
图3-4 滑动水口原理示意图
a-全开;b-半开;c-全闭
1-上水口;2-上滑板;3-下滑板;4-下水口
(3)滑动水口机构
结构组成:
图3-5 滑动水口机构
1-框架;2-上滑板套;3-下滑板套;4-盖形螺母;5-螺杆柱;6-弹簧;7-压套;8-压盖;9-垫圈;10-座砖;11-上水口;12-上滑板;13-下滑板14-下水口
(4)滑动水口开浇(自动)
1)填料法;
2)气烧法;
3)烧氧法。
(5)滑板润滑剂-石墨系、二硫化钙系和二硫化钼系
(6)滑动水口的损坏原因
1)钢液的热冲击;
2)钢液和钢渣的侵蚀;
3)滑板面反复加热;
4)粘钢;
5)节流浇注,钢流紊乱。
⑦钢包长水口
(1)长水口的作用:
保护钢流不受二次氧化,防止钢流飞溅以及敞开浇注的卷渣。
(2)长水口的材质:
熔融石英质和铝碳质。
(3)长水口的种类:
具有吹氩环的和具有透气材料的长水口。
钢包长水口结构图
(4)长水口安装装置
1)卡口型安装装置
2)液压型安装装置
3)叉型安装装置
图3-7 长水口保护装置
a-卡口型;b-液压型;c-叉型
1-钢包;2-氩气;3-钢水;4-中间包;5-浇注位置
2.钢包烘烤装置
烘烤介质(燃料介质及助燃介质)
2)助燃介质:
有压缩空气、鼓风气以及氧气
3)钢包烘烤装置的主要结构、组成
图3-8 立式钢包烘烤装置结构简图
1-钢包放置支架;2-钢包;3-烘烤盖板;4-烘烤介质管道;5-烘烤盖板支架及升降、回转机构;6-管道调节阀;7-鼓风机;8-烘烤装置支架
图3-9 卧式钢包烘烤装置结构简图
1-引风机(喷射排烟器);2-排烟压缩空气阀;3-住进风调节闸板;4-汽(油)阀;5-钢包放置支架;6-烘烤盖板;7-保焰烧嘴;8-点火;9-烘烤盖板移动底座;10-烧嘴;11-鼓风机;12-保焰燃烧阀;3-推车撬杠支杆;14-换热器;15-电器控制箱;16-轨道及底板
钢包烘烤装置的组件及作用
立式和卧式钢包烘烤装置的通用件及作用:
(1)烘烤烧嘴:
汇集和混合各种烘烤介质并喷射出烘烤火焰;
(2)烘烤盖板:
使钢包保温,减少烘烤热量的散失;
(3)鼓风机:
向烘烤烧嘴提供鼓风气助燃介质,并使烘烤火焰具有一定的喷射速度;
(4)烘烤介质管道:
将各种燃料介质及助燃介质从介质供应接口处输送、汇集到烘烤烧嘴接口处;
(5)管道调节阀:
控制烘烤介质管道的开闭和流量的调节;
(6)计量仪表:
提供管道上检测和指示的压力与流量数值;
(7)立式钢包烘烤装置其他零部件:
烘烤装置支架、烘烤盖支架及升降和回转机构、钢包放置底板;
(8)卧式钢包烘烤装置。
装置特点;烘烤盖板、烘烤烧嘴、鼓风机、排气烟囱、部分烘烤介质管道、管道调节阀、计量仪表等安装在烘烤盖板移动底座上并使它们随着移动底座一起移动。
3.钢包运载设备(即:
钢包回转台)
(1)钢包回转台的用途和分类
用途:
运载和承托钢包
图3-10 钢包回转台类型图
A-直臂式;b-双臂单独升降式;c-带钢水包加盖功能
(2)蝶型钢包回转台的主要结构特点
特点:
设有两个用来支撑钢包的叉形壁,并装有称量梁和保温盖,可单独旋转和升降。
(1)钢结构部分
1)叉型臂;2)旋转盘与上部轴承座;3)回转环;4)塔座
(2)回转驱动装置
(3)事故驱动装置
(4)回转夹紧装置
(5)升降装置
(6)称量装置
(7)润滑装置
图3-11 蝶形钢包回转台结构图
1-钢包盖装置;2-叉型臂;3-旋转盘;4-升降装置;5-塔座;6-称量装置;7-回转环;8-回转夹紧装置9-回转驱动装置;10-气动马达;11-背撑梁
(3)钢包回转台的工作特点
1)重载
2)偏载两边满载:
一满一空,一满一无,一空一无,两无两空。
3)冲击
4)高温
(4)钢包回转台的主要特点
1)回臂动作灵活,能快速交换盛钢桶而不必降低拉速。
2)地面积较小,对连铸操作干扰小。
3)操作安全可靠,易于定位和实现远距离操作。
4)回转半径小,一座回转台只能供一台或二台连铸机用。
5)设备复杂,维护检修困难。
(5)对回转台主要参数的要求
1)承载能力:
承受在一侧加