涡喷7甲ⅱ级涡盘工装设计.docx
《涡喷7甲ⅱ级涡盘工装设计.docx》由会员分享,可在线阅读,更多相关《涡喷7甲ⅱ级涡盘工装设计.docx(25页珍藏版)》请在冰豆网上搜索。
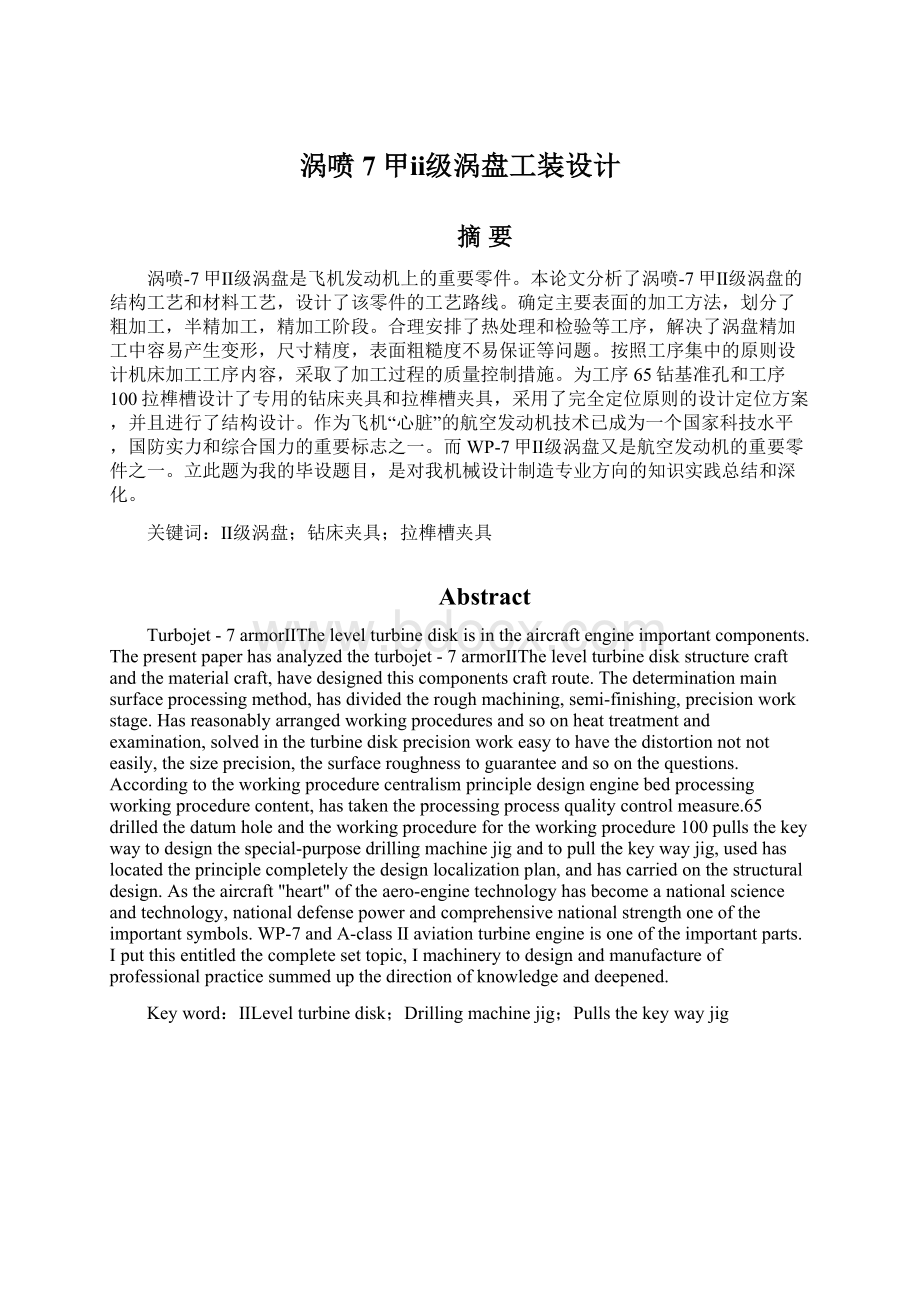
涡喷7甲ⅱ级涡盘工装设计
摘要
涡喷-7甲Ⅱ级涡盘是飞机发动机上的重要零件。
本论文分析了涡喷-7甲Ⅱ级涡盘的结构工艺和材料工艺,设计了该零件的工艺路线。
确定主要表面的加工方法,划分了粗加工,半精加工,精加工阶段。
合理安排了热处理和检验等工序,解决了涡盘精加工中容易产生变形,尺寸精度,表面粗糙度不易保证等问题。
按照工序集中的原则设计机床加工工序内容,采取了加工过程的质量控制措施。
为工序65钻基准孔和工序100拉榫槽设计了专用的钻床夹具和拉榫槽夹具,采用了完全定位原则的设计定位方案,并且进行了结构设计。
作为飞机“心脏”的航空发动机技术已成为一个国家科技水平,国防实力和综合国力的重要标志之一。
而WP-7甲Ⅱ级涡盘又是航空发动机的重要零件之一。
立此题为我的毕设题目,是对我机械设计制造专业方向的知识实践总结和深化。
关键词:
Ⅱ级涡盘;钻床夹具;拉榫槽夹具
Abstract
Turbojet-7armorⅡThelevelturbinediskisintheaircraftengineimportantcomponents.Thepresentpaperhasanalyzedtheturbojet-7armorⅡThelevelturbinediskstructurecraftandthematerialcraft,havedesignedthiscomponentscraftroute.Thedeterminationmainsurfaceprocessingmethod,hasdividedtheroughmachining,semi-finishing,precisionworkstage.Hasreasonablyarrangedworkingproceduresandsoonheattreatmentandexamination,solvedintheturbinediskprecisionworkeasytohavethedistortionnotnoteasily,thesizeprecision,thesurfaceroughnesstoguaranteeandsoonthequestions.Accordingtotheworkingprocedurecentralismprincipledesignenginebedprocessingworkingprocedurecontent,hastakentheprocessingprocessqualitycontrolmeasure.65drilledthedatumholeandtheworkingprocedurefortheworkingprocedure100pullsthekeywaytodesignthespecial-purposedrillingmachinejigandtopullthekeywayjig,usedhaslocatedtheprinciplecompletelythedesignlocalizationplan,andhascarriedonthestructuraldesign.Astheaircraft"heart"oftheaero-enginetechnologyhasbecomeanationalscienceandtechnology,nationaldefensepowerandcomprehensivenationalstrengthoneoftheimportantsymbols.WP-7andA-classⅡaviationturbineengineisoneoftheimportantparts.Iputthisentitledthecompletesettopic,Imachinerytodesignandmanufactureofprofessionalpracticesummedupthedirectionofknowledgeanddeepened.
Keyword:
ⅡLevelturbinedisk;Drillingmachinejig;Pullsthekeywayjig
第1章涡喷7甲Ⅱ级涡盘工艺过程设明
1.1零件图的工艺分析
零件图是制造零件的主要技术依据。
在设计工艺路线之前首先要对其进行工艺分析。
了解零件的功用和工作条件,分析精度及其它技术要求,以便更好的掌握构造特点及工艺关键。
1.1.1零件的工作状态及工作条件
涡盘是发动机上的重要零件,是在高温高压条件下工作的,当气流冲到转子叶片上便驱动涡盘高速旋转。
涡盘通过主轴与压气机相连,涡盘转动时,即带动压气机和联结在轴上的附件(如:
发动机,燃油泵等)转动。
工作时,其轮边缘温度高达700℃,而中心只有300℃,温度分布不均匀造成很大热应力作用。
1.1.2零件的结构分析
涡盘的结构有轮缘,腹板,轮毂等部分组成。
Ⅱ级涡盘是实心圆盘,其盘身剖面形状为锥形,在轮缘上有64个安装叶片的榫槽,腹板上有起均匀作用的小孔。
图1.1零件图
图1.2零件图
1.1.3零件的技术条件分析
(1)表面本身精度
表面粗糙度:
涡盘的配合表面,腹板型面,盘心孔,转接圆弧,榫槽表面粗糙度为Ra0.8um,其余表面为Ra1.6um或Ra3.2um。
几何形状精度:
涡盘腹板型面直线度为0.05mm,端面基准的平面度为0.02mm,腹板线轮廓度为0.076mm,榫槽轮廓度为
0.007~
0.025mm。
(2)表面间的位置精度
涡盘的端面平行度为0.02~0.04mm。
涡盘的配合圆柱面与端面垂直度为0.01~0.03mm。
涡盘与涡轮盘的配合表面,盘心孔,腹板型面跳动为0.02~0.05mm。
涡盘的两端轴径配合圆面同轴度为0.02~0.05mm。
精密定位孔位置度为φ0.03~φ0.05mm。
螺栓孔,螺钉孔位置度为φ0.1~φ0.2mm。
(3)零件的其它技术要求
涡盘因采用的材料性能好,其结构日趋薄壁形,刚性差,加工时易变形,加工中应安排消除应力热处理工序,并采用端面压紧和修正端面基准平面度的办法来减小变形。
由于涡盘的特殊条件,在保证锁片自由装入锁片槽内的情况下,允许按锁片厚度加工尺寸L,并保证间隙,热处理后硬度d=3.6~3.2。
涡盘的毛坯为模锻件,零件选用锻压加工,所以检验组别为Ⅱ大类。
表1.1各类别检验的内容
检验类别
类别特性
硬度检验
机械性能检验
Ⅰ类检验
高负荷零件
100%
100%检验从零件上切下来的检验试片(棒),
允许在热处理前切割试件,
但要同零件一起进行热处理。
Ⅱ类检验
中等负荷零件
100%
小型零件每热处理炉和同一熔炼炉批检验
1-2个零件或试样
大批零件每熔炼炉批检验,1-2个零件或试件
Ⅲ类检验
小负荷零件
100%
不检验
Ⅳ类检验
轻负荷零件及棒料
每批零件抽10%检验硬度,如不合格,则要100%检验或整批零件返修处理
不检验
1.1.4零件材料及切削加工性
Ⅱ级涡盘是发动机上的重要零件,工作温度虽比叶片低,但其应力条件异常复杂,且在轮心轮缘榫槽和腹板各部位所受的应力,温度,介质作用程度都不同。
又加上Ⅱ级涡盘所用材料必须能够在高温,高压,高转速的条件下保持很高的强度和抗蠕变的性能,有高的屈服强度,拉伸强度和足够的塑性储备,以防止轮盘内边缘齿槽缺口产生应力集中。
对材料的具体要求是:
(1)材料应具有高的屈服强度,在高温时也能保持高的屈服极限,良好的蠕变强度,高的疲劳强度和低的疲劳性能,组织稳定性和冷热机械性能。
(2)线膨胀系数小。
(3)无缺口敏感性。
(4)具有良好的切削加工性能和一定的抗氧化,耐腐蚀能力。
GH4133属于时效强化变形Ni基高温合金。
此类合金是在GH4033合金基础上进一步合金化,适当提高强化元素铝,钛含量和添加难溶金属铌而发展成为镍-铬固溶体为基,r'[
(Al,Tr,Nb)]为主要强化时效硬化型合金,该合金的使用温度可以比铁基合金高200℃左右,热强度高,在高温度情况下可承受大的载荷和复杂应力。
1.1.5零件尺寸标注分析
一般表面件的位置尺寸的标注有三种方式:
坐标式,连接式,混合式。
尺寸的标注方式在从某些方面上影响加工的顺序。
涡盘外形较为复杂,加工工艺过程步骤较多也较为复杂,其标注应采用混合式标注。
1.1.6为了保证热处理质量的检验说明
高温合金的热处理主要有固熔处理(淬火),中间处理(2次固熔处理或中间的时效)时效处理。
对于时效强化的高温合金来说,固熔处理的目的是使强化相溶于固熔体中,得到过饱和固熔体和固熔加少量未溶解的强化组织。
中间处理的目的是改变晶界碳化物状态,以强化晶界,或者是造成大小两种尺寸的
相,以改善综合性能和长期稳定组织。
时效对时效强化的高温合金来说,其目的是使强化相,充分而均匀地呈弥散状态析出,使合金强化到技术条件要求。
1.1.7零件的总体工艺分析
涡盘零件的毛坯为模锻件。
此零件因采用的材料性能好,其结构日趋薄壁形,刚性差,加工时易变形,加工中应安排消除应力热处理工序,并采用端面压紧和修正端面基准平面度的办法来减小变形。
涡盘的配合表面精度高,表面粗糙度值小,最后精加工用精密车床车削保证,盘的内腔,腹板型面表面粗糙度值小,精加工应采用数控车床。
盘的榫槽数量多,尺寸精度高,采用高速拉削保证。
盘的精密定位孔,尺寸精度,位置精度要求高,用镗床或钻床加工。
盘的各表面相互位置关系精度要求高,因此精加工时,工序应集中,一次装夹找正,车削尽量多表面,或用同一基准加工各表面。
盘的特殊表面(花键,花边)及螺栓孔,螺钉孔等用不同设备,工艺装备加工。
加工难点:
1涡盘枞树形榫槽的拉削。
解决方法:
涡盘枞树形榫槽的拉削,是属于多刃刀具进行机械加工的,虽然拉削速度低,但这种加工方式,生产效率很高,可以同时完成粗加工和精加工。
2涡盘精加工中容易产生变形,尺寸精度,表面粗糙度不易保证。
解决方法:
1选用好的硬质合金刀具材料。
2合理地选用刀具的几何角度和好的刃磨质量,设计成型刀具时,尺寸取下限值,减少与工件接触面积,保持加工过程刀具的锋利。
3切削过程的量浇注冷却液,充分冷却,延长刀具寿命。
4专用夹具,在腹板端面处增加辅助支承基准,以增加盘件的刚性。
5利用数控车床,加工腹板型面和转接,减少变形和降低表面粗糙度值。
总之,Ⅱ级涡盘是发动机上的重要零件,它的加工要求很高。
从构形总体看,零件表面形状比较复杂,加工方法多种多样。
所以,它的加工工艺较为复杂,加工工序较多。
1.2毛坯的设计
1.2.1毛坯的种类的确定
由于涡盘在高转速下工作,受力大,要求的强度高,所以采用锻造的方法来加工毛坯。
锻压生产的特点如下:
(1)可以改善金相组织,提高金属的机械性能。
(2)可以节约金属材料的切削加工时间,提高金属材料的利用率和经济效应。
(3)具有较高的劳动生产率
Ⅱ级涡盘的毛坯采用模锻件。
Ⅱ级涡盘在机械加工过程中进行超声波检验,以及时发现材质缺陷,超声波表面应留有盲区余量,故加工余量较大,一般有5-6mm,个别部位更大。
模锻的优点如下:
①由于有模腔引导金属的流动,锻件的形状可以比较复杂。
②锻件内部的锻造流体比较完整,从而提高零件机械性能和寿命。
③锻件表面光洁,尺寸精度高,节约了材料和切削加工时间。
④生产率高
⑤操作简便,易于实现机械化。
⑥生产批量越大,成本越低。
毛坯材料:
采用GH4133,不热处理。
批量和生产率:
中批量生产
1.2.2毛坯的工艺参数选择
(1)分模面的确定
形成模锻件的各扇模具之分合面称分模面。
也就是上模和下模的分界面。
确定分模面位置最基本的原则是保证锻件形状可能与零件形状相同,以及锻件容易从锻模型槽中取出。
选定分模面要注意以下几点:
①锻件能从模腔中顺利取出
②金属易于充满模腔
③简化模具制造
④节约金属材料
因此,模锻件的分模面应该选在毛坯的对称面上。
(2)毛坯的余量与公差
1余量的确定
加工余量直接影响工序尺寸,而更重要的是关系到加工质量和加工成本。
若余量过大,不仅浪费材料,而且增加机械加工劳动量,降低生产率,增加产品成本。
若余量过小,一方面毛坯制造困难,另一方面,在机械加工时由于余量过小装夹困难,甚至无法加工而出现废品。
正确确定加工余量具有很大的经济意义。
Ⅱ级涡盘的毛坯余量按直径有10-12mm,厚度有11mm,每面平均余量在5mm左右,毛坯尺寸及公差的确定均按《航空机械设计手册》下册表8-66,8-56,8-57并根据工厂的实际情况及加工经济来确定。
2公差的确定
由于该零件的毛坯的材料采用GH4133检验组别Ⅱ大类,故尺寸比较精确,表面粗糙度比较低,因此机械加工余量和锻造公差都比自由锻小得多。
本锻件余量与公差选取为:
一般公差按GB5800-82
形状和位置公差按GB1182-80
3拔模斜度
在锻件上与分模面相垂直的平面所附加的斜度称为拔模斜度。
此锻件的拔模斜度选为7℃
4圆角半径
锻件上所有面与面的相交线,都必须采用圆角过渡。
锻件内圆角的作用是减少锻造时金属流动的摩擦阻力,减少模具的磨损。
锻件外圆角的作用是使金属易于充满模腔。
避免模具因应力集中而破裂。
下表为按型腔和锻件重量确定的最佳外圆角半径值
表1.2模锻件外圆角半径的选用
锻件重
(Kg)
模锻型腔深度(mm)
备注
≤10
10-25
25-50
≥50
外圆角半径
≤1
1-6
6-16
16-40
40-100
≥100
1
1.5
2
2.5
3
4
1.5
2
2.5
3
4
5
2
2.5
3
4
5
6
3
3.5
4
5
7
8
还应考虑
加工余量
圆角半径的确定:
外圆角半径r=加工余量+零件的圆角半径(或导角),取r=8;内圆角半径R=(2-3)R即R=16-24
圆角半径的标准值选定位:
1,1.5,2,3,4,5,6,8,10,12,15,25,30.从中选择可以选择标准刀具,方便加工。
5技术要求及说明
(1)坯料模锻件硬度d=3.6-3.2
(2)毛坯图未标明模锻斜度为7°
(3)毛坯图未标明圆角R5
(4)允许:
Ⅰ表面缺陷深度不大于按名义尺寸的每面机械加工余量的二分之一;Ⅱ模锻偏移不大于2;Ⅲ允许欠压7
(5)锻件不热处理和不酸洗
(6)毛坯图括号内尺寸为成品尺寸
(7)在盘的标刻位置标刻锻件号,锭节号,材料牌号,熔炼号。
(8)“
”
为半成品超声波探伤面。
“”为热处理打硬度处
(9)当锻锤压力不足时,将会出现以下现象:
Ⅰ锻件在分模面垂直方向的尺寸增大
Ⅱ锻件表面粗糙
产生该现象的原因是:
加热温度低,设备吨位不足,在终锻型槽内锤击次数不够。
锻件按Ⅱ类检验,其内容如下表所示:
表1.3检验内容
热处理状态
预备
最终
检验项目和数量
表面质量和几何尺寸
100%当能确保质量时,模锻件几何尺寸允许抽检
材料牌号
100%
硬度
每炉抽检10%但不少于3件
100%
机械性能
每熔批抽检1件
每验收批抽检1件或在试样上检查
低倍
每熔批抽检一件
断口
按需要每熔批抽检一件
晶粒度
需化学热处理的零件和有需要的其他件每熔批抽检一件
1.3工艺规程的设计
1.3.1工艺路线的制定
方案比较:
初拟定方案为在细加工阶段进行热处理,而且没有安排加工试件和检查试件。
在调研之后得知这样的工艺安排缺少很多实际意义。
首先应该在粗加工时就进行热处理,因为高温合金的最终热处理工序,安排在毛坯制造中进行。
即在粗加工阶段进行。
加工试件是为了试验拉刀角度是否正确,这样可及时发现问题,免得在正式拉削时产生废品。
所以拟定相对实际意义更大的工艺路线如表(4)工艺路线图表。
(1)加工方法的选择
零件各表面加工方法的选择,不但影响质量,而且也要影响到生产率和制造成本。
所以在选择加工方法时,必须要了解加工方法的过程,工艺特点和应用范围。
对于主要表面经过几次加工,由粗加工到精加工,逐步达到要求。
在加工同一类型的表面时,由于具体条件不同,可能有多种加工方法。
影响表面加工方法的因素有表面的形状,尺寸,精度和粗糙度,以及零件的整体构造,重量,材料及热处理等。
另外,产量和生产条件也是影响因素。
在选择加工方法时,首先应选定最后加工方法;然后再选定最后加工以前的各工序的加工方法;最后选定次要表面的加工方法。
加工方法的选择主要考虑以下几方面:
1)表面的形状和尺寸
2)表面的精度与粗糙度
3)工件的材料与热处理
4)工件的整体构形与重量
5)产量和生产类型
6)现场生产条件
制定Ⅱ级涡盘的工艺路线如下
表1.4工艺路线图表
工序号
工序名称
工序号
工序名称
00
锻件
70
加工试件
05
车台阶
75
钻锪孔
10
车外圆和钻孔
80
切螺纹
15
热处理
85
钳工
20
车超声波检查面
90
拉试件
25
车超声波检查面
95
检查试件
30
超声波检验
100
拉榫槽
35
粗车第一面
105
倒圆角
40
粗车第二面
110
精车圆弧
45
车基面
115
抛光型面
50
精车第一面
120
洗涤
55
精车第二面
125
最终检验
60
腐蚀检验
65
钻基准孔
(2)阶段划分
当工件刚性差,易变形,而加工精度和表面质量要求较高时,为保证加工质量,生产率和经济性,通常把整个工艺过程划分成几个阶段,在不同的加工阶段完成的主要加工内容有所区别。
此零件工艺路线划分成三个阶段:
粗加工阶段,半精加工阶段,精加工阶段。
(3)工序的集中与分散
由于Ⅱ级涡盘的尺寸和重量都比较大,安装和运输困难。
所以,一般宜采用集中原则来进行生产。
采取工序集中原则在生产过程中有很大的好处,可以减少定位次数,减少定位误差,提高零件加工精度,尤其是提高各表面之间的位置精度。
使工序数目减少,简化了生产组织工作,减少了设备数目,从而节省了车间生产面积,减少了安装次数,提高了劳动生产率,有利于采用先进设备,提高产品质量。
(4)基准选择
当毛坯开始加工时,选用锻件的外圆表面为径向基准,端面为轴向基准,此时基准粗基准,采用径向夹紧。
粗加工时选用以加工外圆表面,端面为径向和轴向基准,即精基准。
仍用径向夹紧,因为零件的刚性好。
精加工时采用基准重合原则,用零件配合圆面(内,外表面)盘心孔和端面为基准,使工艺基准与设计基准重合,一次装夹,保证盘一端的内,外表面之间的同轴度,垂直度和跳动,与另一端之间的位置公差,用互为基准加找正的方法保证。
采用轴向夹紧,应多次修正零件端面基准的平面度,在规定范围内(75%-80%),避免基准面变形,影响零件加工精度。
因此,在加工过程中,定位对加工质量有很大影响,需要合理选择定位基准。
定位基准本身准确与否,影响定位的精度,从而影响被加工表面的位置的准确性,所以位置精度要求较高的工序,必须先准备好准确的定位基准,甚至设置专门加工基准的工序。
在Ⅱ级涡轮盘的加工过程中,如工序20,车超声波检验面,先车一个端面,再以此端面为定位基准加工另一面,为工序25作准备。
象这种情况还有:
工序35,40;工序55,60;工序65中先钻基准孔,然后再以此为基准钻另外的孔。
因为涡盘在一次按装中完成全部主要表面的加工,所以定位基准在加工过程中完成全部主要表面的加工,所以定位基准在加工过程中一定会产生转换问题。
定位基准在转换时,会引起加工余量的分布不均,从而影响加工表面的形状精度及位置精度。
因此,不但要分析一个工序定位基准如何选择,而且要考虑整个工艺过程中,各工序的定位基准应该如何优化组合,也就是如何保证定位基准之间的位置精度问题。
粗基准的选择:
(1)相互位置要求原则
(2)加工余量合理分配原则
(3)粗基准避免重复使用原则
(4)便于安装原则
精基准的选择:
(1)基准重合原则
(2)互为基准原则
(3)一次装夹原则
(4)基准统一原则
(5)自为基准原则
(6)便于装夹原则
在以上六种方法中,一次装夹和互为基准的方法能够保证较高的位置精度。
因此,定位基准一般采用这种两种方法。
Ⅱ级涡盘的主要表面定位基准的选择如下:
(1)在工序45中②端面③端面之间有平行度要求,可以用②定位③加工,也可以用③定位②加工,它们之间互为基准。
(2)在工序50中
端面对
面有垂直度的要求,采用一次安装来保证。
(3)在工序55中:
加工端面时,采用外圆A作为定位基准;
在工序60中:
加工表面时,也采用外圆作为定位基准;所以,它们之间的位置精度要求采用同一基准来完成。
(4)工序100中,榫槽中心线对盘中心线的平行度的要求采用一次装夹来完成。
通过H点的平面对
表面的平行度以及圆跳动采用一次安装来保证。
(5)在工序55中,型面
对
的圆跳动以外圆
作为定位基准;
(5)热处理工序的安排
热处理工序的性质,特别是热处理工序在工艺路线中的位置,对机械加工工序的内容,数目和顺序有很大的影响。
因此,在设计工艺路线时,需要进行仔细的分析。
Ⅱ级涡盘是采用高温合金制成的盘,所以最终热处理工序安排在毛坯制造中进行。
热处理目的:
(1)提高材料的机械性能
(2)改善材料的加工性(3)消除内应力
(6)辅助工序的安排
辅助工序的种类:
一般检验,特种检验,表面处理,洗涤等。
超声波探伤有脉冲反射法,穿透法,共振法。
脉冲反射法用,的最多,其其原理是:
当探头发出的超声波脉冲在工作中传播时,就发生反射,被探头接收后,通过高频放大,检波,视波放大后,在荧光屏上显示出来,这样可以根据反射波的有无,强弱及波形来判断缺陷的有无,大小及位置。
超声波探伤具有灵敏度高,操作方便,快速经济易于实现自动化等特点。
对探伤面的要求:
(1)表面平整,光洁,无氧化皮,锈蚀斑痕。
光洁度越高,声波接触越好,灵敏度越高,表面粗糙度不大于2.5um。
(2)厚度大于超声波探伤仪的盲区(纵波探伤通常大于7mm,轴类棒材,直径应大于40mm)。
(3)腐蚀检查:
用化学腐蚀的方法来检查零件表面,具体方法是将零件先在汽油槽(或酒精槽)中洗涤干净,然后侵入5-10%的硝酸溶液中腐蚀20-30s,然后在汽油中洗涤,晾干后,用5-10倍的放大镜检查有无裂纹和黑斑。
它在精加工阶段进行,以便在精加工后保证工件合格的进入以后工序。
洗涤:
洗涤工序应用的场合较广,如抛光,磁力探伤后,以及最终检验之前,都要将工件洗净。
所以安排洗涤工序。
Ⅱ级涡盘的加工工序中,最终检验之前安排了洗涤。
(7)工艺路线总体分析
工
序
号
工序内容
工艺图
工
序
00
毛坯采用模锻件
工
序
05
车台阶为下一步做好定位,夹紧基准的准备。
和
面作为初始定位基准。
加工出圆柱面
及孔
。
工
序
10
车外圆和钻孔以