精品水运材料复习参考.docx
《精品水运材料复习参考.docx》由会员分享,可在线阅读,更多相关《精品水运材料复习参考.docx(109页珍藏版)》请在冰豆网上搜索。
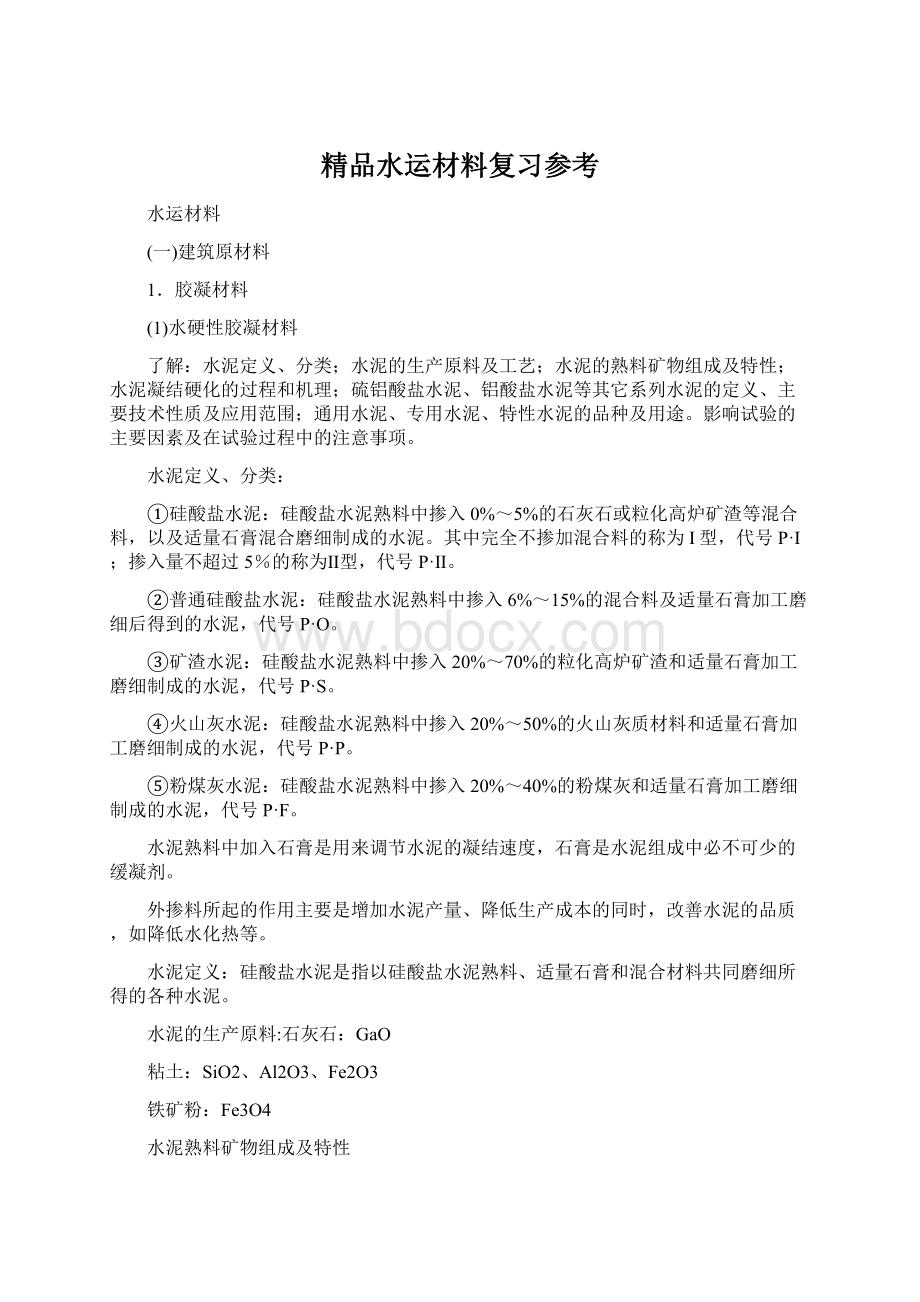
精品水运材料复习参考
水运材料
(一)建筑原材料
1.胶凝材料
(1)水硬性胶凝材料
了解:
水泥定义、分类;水泥的生产原料及工艺;水泥的熟料矿物组成及特性;水泥凝结硬化的过程和机理;硫铝酸盐水泥、铝酸盐水泥等其它系列水泥的定义、主要技术性质及应用范围;通用水泥、专用水泥、特性水泥的品种及用途。
影响试验的主要因素及在试验过程中的注意事项。
水泥定义、分类:
①硅酸盐水泥:
硅酸盐水泥熟料中掺入0%~5%的石灰石或粒化高炉矿渣等混合料,以及适量石膏混合磨细制成的水泥。
其中完全不掺加混合料的称为I型,代号P·I;掺入量不超过5%的称为Ⅱ型,代号P·Ⅱ。
②普通硅酸盐水泥:
硅酸盐水泥熟料中掺入6%~15%的混合料及适量石膏加工磨细后得到的水泥,代号P·O。
③矿渣水泥:
硅酸盐水泥熟料中掺入20%~70%的粒化高炉矿渣和适量石膏加工磨细制成的水泥,代号P·S。
④火山灰水泥:
硅酸盐水泥熟料中掺入20%~50%的火山灰质材料和适量石膏加工磨细制成的水泥,代号P·P。
⑤粉煤灰水泥:
硅酸盐水泥熟料中掺入20%~40%的粉煤灰和适量石膏加工磨细制成的水泥,代号P·F。
水泥熟料中加入石膏是用来调节水泥的凝结速度,石膏是水泥组成中必不可少的缓凝剂。
外掺料所起的作用主要是增加水泥产量、降低生产成本的同时,改善水泥的品质,如降低水化热等。
水泥定义:
硅酸盐水泥是指以硅酸盐水泥熟料、适量石膏和混合材料共同磨细所得的各种水泥。
水泥的生产原料:
石灰石:
GaO
粘土:
SiO2、Al2O3、Fe2O3
铁矿粉:
Fe3O4
水泥熟料矿物组成及特性
性能指标
熟料矿物
C3S
C2S
C3A
C4AF
水化速率
快
慢
最快
快
凝结硬化时间
快
慢
最快
快
28d水化热
多
少
最多
中
强度
早期
高
低
低
低
后期
高
高
低
低
经1700℃煅烧后磨细
熟悉:
通用水泥(硅酸盐系列水泥)的主要技术指标:
强度等级、细度、凝结时间、需水性、安定性、烧失量、不溶物、氧化镁、三氧化硫、碱含量、水化热;水泥的选用。
细度:
硅酸盐比表面积大于300m2/kg,其他80μm方孔筛不大于10%;
凝结时间:
初凝不早于45min,终凝:
硅酸盐不迟于6.5h,其他10h;
氧化镁不大于5%,压蒸安定性合格时,允许放宽到6%;
三氧化硫含量不得超过3.5%,矿渣不得超过4%。
掌握:
硅酸盐系列水泥检验规则,取样方法、废品及不合格品的判定,对水泥出厂试验报告的要求、对水泥出厂交货与验收的规定;水泥的物理力学性能检测及评定方法(包括所用材料、仪器设备、试验步骤或程序、试验结果处理及评定);对试验室内温、湿度要求及养护制度要求。
按标准对试验结果进行评定,编制和审核检测报告。
硅酸盐系列水泥检验规则
编号:
水泥出厂前按同品种、同强度等级编号和取样。
袋装水泥和散装水泥应分别进行编号和取样。
每一编号为一取样单位。
水泥出厂编号按水泥厂年生产能力规定:
120万t以上,不超过1200t为一编号;
60万t至120万t,不超过1000t为一编号;
30万t至60万t,不超过600t为一编号;
10万t至30万t,不超过400t为一编号;
10万t以下,不超过200t为一编号
当散装水泥运输工具的容量超过该厂规定出厂编号吨数时,允许该编号的数量超过取样规定吨数。
分割样品质试验:
①分割样试验每季度进行一次。
可任选一个品种、标号。
②分割样的品质试验结果必须符合水泥标准技术要求。
③分割样取得后应立即进行试验。
全部样品必须在一周内进行完毕。
④当分割样试验结果有低于水泥的技术要求时,或28天抗压强度变异系数大于6%时,即应每季度进行二次;当仍有低于技术要求时,或变异系数大于6%时,则每月进行一次。
⑤当分割样试验结果全部符合水泥标准技术要求时,方可恢复为每季一次。
⑥增加试验时,一般应用同品种、标号的水泥。
取样方法
取样应有代表性,可连续取,亦可从20个以上不同部位取等量样品,总量至少12kg。
①自动取样器取样:
将装置安装在尽量接近于水泥包装机的管路中,从流动的水泥流中取出样品,然后将样品放入洁净、干燥、不易受污染的容器中。
②取样管取样:
随机选择20个以上不同的部位,将取样管插入水泥适当深度,用大拇指按住气孔,小心抽出取样管。
将所取样品放入洁净、干燥、不易受污染的容器中。
③槽形管状取样器取样:
当所取水泥深度不超过2m时,采用槽形管式取样器取样。
通过转动取样器内管控制开关,在适当位置插入水泥一定深度,关闭后小心抽出。
将所取样品放入洁净、干燥、不易受污染的容器中。
废品及不合格品的判定
凡游离氧化镁、三氧化硫、初凝时间、安定性中任一项指标不符合规定,均判为废品水泥,严禁在工程中使用;
凡细度、终凝时间、不溶物和烧失量中任一项指标不符合规定,或混合料掺入量超过最大限量和强度低于商品强度等级指标时,判为不合格水泥。
当水泥包装标志中水泥品种、强度等级、生产者名称和出厂标号不全的也属于不合格品。
对水泥出厂试验报告的要求、对水泥出厂交货与验收的规定
试验报告内容应包括本标准规定的各项技术要求及试验结果,助磨剂、工业副产石膏、混合材料的名称和掺加量,属旋窑或立窑生产。
当用户需要时,水泥厂应在水泥发出之日起7天内寄发除28天强度以外的各项试验结果。
28天强度值,应在水泥发出之日起32天内补报。
交货与验收:
①交货时水泥的质量验收可抽取实物试样以其检验结果为依据,也可以水泥厂同编号水泥的检验报告为依据。
采取何种方法验收由买卖双方商定,并在合同或协议中注明。
②以抽取实物试样的检验结果为验收依据时,买卖双方应在发货前或交货地共同取样和签封。
取样数量为20kg,缩分为二等份。
一份由卖方保存40天,一份由买方按规定的项目和方法进行检验。
在40天以内,买方检验认为产品质量不符合标准要求,而卖方又有异议时,则双方应将卖方保存的另一份试样送省级或省级以上国家认可的水泥质量监督检验机构进行仲裁检验。
③以水泥厂同编号水泥的检验报告为验收依据时,在发货或交货时买方在同编号水泥中抽取试样,双方共同签封后保存三个月;或委托卖方在同编号水泥中抽取试样,签封后保存三个月。
在三个月内,买方对水泥质量有疑问时,则买卖双方应将签封的试样送省级或省级以上国家认可的水泥质量监督检验机构进行仲裁检验。
水泥的物理力学性能检测及评定方法(包括所用材料、仪器设备、试验步骤或程序、试验结果处理及评定)
a、维卡仪法稠度测定的方法
①拌制水泥净浆。
将搅拌锅和搅拌叶片先用湿布擦过,将拌和水倒入锅中,然后5s~10s内小心将称好的500g水泥加入锅中,启动搅拌机,低速搅拌120s,停15s,同时将叶片和锅壁上的水泥浆刮入锅中间,接着高速搅拌120s停机。
②拌和结束后,立即将拌制好的水泥净浆装入已放在玻璃板上的试模中,用小刀插捣,轻轻振动数次,刮去多余的净浆。
③抹平后迅速将试模和底板移到维卡仪上,并将其中心定在试杆下,降低试杆直到与水泥净浆表面接触,拧紧螺丝1s~2s后,突然放松,使试杆垂直自由地沉入水泥净浆中。
在试杆释放30s时或试杆不再下沉时记录试杆到底板的距离,升起试杆后,立即擦净。
④整个操作应在搅拌后1.5min内完成。
以试杆沉入净浆并距底板6mm±1mm
的水泥净浆为标准稠度净浆,其拌和用水量为该水泥的标准稠度用水量。
试锥法(代用法):
采用代用法测定水泥标准稠度用水量可用调整水量和不变水量两种方法的任一种测定。
不变水量法时的拌和水量用142.5mL。
①拌制水泥净浆。
②拌和结束后,立即将拌制好的水泥净浆装入锥模中,用小刀插捣,轻轻振动数次,刮去多余的净浆;
③抹平后迅速放到试锥下面固定的位置上,将试锥降至净浆表面,拧紧螺丝1~2s后,突然放松,让试锥垂直自由地沉入水泥净浆中。
到试锥停止下沉或释放试锥30s时记录试锥下沉深度。
整个操作过程应在搅拌后1.5min内完成。
④调整水量法以试锥下沉深度28mm±2mm时的净浆为标准稠度净浆,其拌和用水量为该水泥的标准稠度用水量,按水泥质量的百分比计。
不变水量法,根据测得的试锥下沉深度S(mm)计算标准稠度用水量P=33.4-0.185S。
当试锥下沉深度小于13mm时,应改用调整水量法测定。
调整水量法和固定水量法发生争议时,以调整水量法为准。
当固定水量法的试锥下沉深度小于13mm时,应采用调整水量法。
b、安定性测定的标准方法——雷氏夹法;代用法——试饼法;
目前的安定性检测方法只是针对游离CaO的影响,并未涉及游离MgO和石膏造成的安定性问题。
国家对游离MgO和SO3在水泥中的含量均有严格的限制,超出指标的水泥即为废品水泥,严禁在工程中使用。
雷氏夹试件的制备方法:
养护24h±2h。
雷氏夹法结果判别:
当两个试件煮后增加距离的平均值不大于5.0mm时,即认为该水泥安定性合格,当两个试件煮后增加距离的差值超过4.0mm时,应用同一样品立即重做一次试验。
再如此,则认为该水泥为安定性不合格。
试饼法结果判别:
试饼从玻璃板取下时,先检查试饼是否完整(如已开裂、翘曲,要检查原因,确定无外因时,该试饼已属不合格,不必沸煮),在无缺陷的情况下沸煮后目测试件未发行裂缝,用钢直尺检查也没有弯曲的试饼为安定性合格;反之为不合格。
当两个试饼判别结果有矛盾时,该水泥的安定性为不合格。
沸煮的条件:
30min±5min内加热水至沸腾,并恒沸3h±5min。
c、凝结时间测定的操作方法、注意事项。
初凝时间测定:
①测定前准备工作,调整凝结时间测定仪的试针接触玻璃板,使指针对准零点。
②以标准稠度用水量制成标准稠度净浆,记录水泥全部加入水中的时间作为凝结时间的起始时间。
一次装满试模,振动数次刮平,立即放入湿气养护箱中。
③计时开始30min后进行第一次测定,测定时,从湿气养护箱中取出试模放到试针下,降低试针与水泥净浆表面接触。
拧紧螺丝1s~2s后,突然放松,使试杆垂直自由地沉入水泥净浆中。
观察试针停止沉入或释放试针30s时指针的读数。
④临近初凝时,每隔5min测定一次。
当试针沉至距底板4mm±1mm时,为水泥达到初凝状态。
⑤达到初凝时应立即重复测一次,当两次结论相同时才能定为达到初凝状态。
终凝时间测定:
①完成初凝时间测定后,立即将试模连同浆体以平移的方式从玻璃板下翻转180°,直径大端向上,小端向下放在玻璃板上,再放入湿气养护箱中继续养护。
②临近终凝时间每隔15min测定一次,当试针沉入试件0.5mm即环行附件开始不能在试件上留下痕迹时,为水泥达到终凝状态。
③达到终凝时应立即重复测一次,当两次结论相同时才能定为达到终凝状态。
注意事项:
在最初测定的操作时应轻轻扶持金属柱,使其徐徐下降,以防止试针撞弯,但结果以自由下落为准;在整个测试过程中试针沉入的位置至少要距试模内壁10mm。
每次测定不能让试针落入原针孔,每次测试完毕须将试针擦净并将试模放回湿气养护箱内,整个测试过程要防止试模振动
d、常用筛析法检测水泥细度的操作方法和特点。
负压筛法:
①筛析试验前,应把负压筛放在筛座上,盖上筛盖,接通电源打开仪器,检查控制系统,调节负压至4000~6000Pa范围。
②称取25g水泥试样,记作m,倒在洁净的负压筛上,扣上筛盖并放到筛座上。
开动负压筛析仪,连续过筛2min。
如筛析过程中看到有水泥附着在筛盖上,可通过敲击使试样落下。
③筛析结束后,用天平称取筛中的筛余物,记作Rs。
水筛法:
①筛析试验前,使水中无泥、砂,调整好水压及水筛架位置,使其正常运转。
喷头底面和筛网之间距离为35mm~75mm。
②称取试样50g,置于洁净的水筛中,立即用淡水冲洗至大部分细粉通过后,放在水筛架上,用水压力为0.05MPa±0.02MPa的喷头连续冲洗3min。
筛毕,用少量水把筛余物冲至蒸发皿中,等水泥颗粒全部沉淀后,小心倒出清水,烘干并用天平称量筛余物。
(Rs)
③计算:
水泥细度用筛余百分率
表示
④合格评定时,每个样品应称取两个试样分别筛析,取筛余平均值为筛析结果。
若两次结果绝对误差大于0.5%时(筛余值大于5.0%时可放至1.0%),应再作一次试验,取两次相近结果的算术平均值作为最终结果。
e、水泥胶砂试验的操作方法。
⑴材料:
水泥从取样到试验要保持24h以上时,应将其储存在基本装满和气密的容器中,容器不能和水泥反应;试验水为饮用水,仲裁试验时用蒸馏水。
⑵仪器设备:
试验筛、搅拌机、试模、振实台、抗折强度试验机、抗压强度试验机、抗压强度试验机用夹具、养护箱或雾室、天平、量筒等。
⑶试件成型。
成型前将试模擦净,四周的模板与底座的接触面上应涂黄油,紧密装配,防止漏浆,内壁均匀地刷一薄层机油。
水泥与ISO砂的质量比为1:
3,水灰比0.5。
每成型三条试件需称量的材料及用量为:
水泥450g±2g;ISO砂1350g±5g;水225mL±1mL。
将水加入锅中,再加入水泥,把锅放在固定架上并上升至固定位置。
然后立即开动机器,低速搅拌30s,在第二个30s开始时均匀将砂子加入。
高速搅拌30s。
停拌90s,在停拌的第一个15s内用胶皮刮具将叶片和锅壁上的胶砂刮入锅中。
在高速下继续搅拌60s。
用振实台成型时,将空试模和模套固定在振实台上,用勺子直接从搅拌锅中将胶砂分为两层装入试模。
装第一层时,每个槽里约放300g砂浆,用大播料器垂直架在模套顶部,沿每个模槽来回一次将料层播平,再振实60次。
再装入第二层胶砂,用小播料器播平,再振实60次。
移走模套,从振实台上取下试模,并用刮尺以90°的角度架在试模顶的一端,沿试模长度方向以横向割据动作慢慢向另一端移动,一次将超出试模的胶砂刮去。
并用同一直尺在近乎水平的情况下将试件表面抹平。
在试模上做记号标明试件的编号和试件相对于振实台的位置。
⑷养护
编号后,将试模放入养护箱内,水平放置,刮平面朝上。
对于24h龄期的,应在破型试验前20min内脱模。
对于24h以上龄期的,应在成型后20h~24h内脱模。
试件脱模后放入水槽中养护,试件之间间隙和试件上表面的水深不得小于5mm。
试验前15min从水中取出,抹去试件表面沉淀物,并用湿布覆盖。
⑸强度试验
各龄期(从水泥加水搅拌开始算起)的试件应在下列时间内进行强度试验:
龄期
24h
48h
72h
7d
28d
试验时间
24h±15min
48h±30min
72h±45min
7d±2h
28d±8h
抗折强度试验:
以中心加荷法测定抗折强度。
采用杠杆式抗折试验机时,试件放入前,应使杠杆成水平状态,将试件成型侧面朝上放入抗折试验机内,调整夹具,使杠杆在试件折断时尽可能地接近水平位置。
抗折试验加荷速度为50N/s±10N/s,直至折断,并保持两个半截棱柱试件处于潮湿状态直至抗压试验。
抗压强度试验:
抗折试验后的断块应立即进行抗压试验。
清除试件受压面与加压板间的砂粒或杂物,将试件成型时的两个侧面作为受压面,底面靠紧夹具定位销,断块试件应对准抗压夹具中心。
压力机加荷速度应控制在2400N/s±200N/s速率范围内,在接近破坏时更应严格掌握。
影响水泥力学强度形成的主要因素:
水泥自身熟料矿物组成、细度、水灰比、试件制作方法、养护条件和时间。
影响强度的试验条件:
养护方式及时间、压力机量程范围、试验材料配合比等。
抗折强度计算:
抗折强度结果取三个试件平均值,精确至0.1MPa。
当三个强度中有超过平均值的±10%的,应剔除后再平均,以平均值作为抗折强度试验结果。
抗压强度计算:
;Fc为破坏荷载。
抗压强度结果取6个断块试件抗压强度的算术平均值,精确至0.1MPa。
如果6个强度中有一个超过平均值的±10%的,应剔除后以剩下的5个值的算术平均值作为最后结果。
如果5个值中再有超过平均值±10%的,则此组试件无效。
对试验室内温、湿度要求及养护制度要求
试件成型试验室应保持温度为20℃±2℃(包括强度试验室),相对湿度大于50%。
水泥试样、ISO砂、拌和水及试模等的温度应与室温相同。
养护箱或雾室温度为20℃±1℃,相对湿度大于90%,养护水的温度20℃±1℃。
试件成型试验室的空气温度和相对湿度在工作期间每天应至少记录一次。
养护箱或雾室温度和相对湿度至少每4h记录一次。
在自动控制的情况下,记录次数可以酌减至一天记录2次。
在给定温度范围内,控制所设定的温度应为此范围的中值。
(2)气硬性胶凝材料
了解:
石灰、石膏、水玻璃等气硬性胶凝材料的定义、分类及应用范围。
石膏:
以硫酸钙为主要成分组成的气硬性胶凝材料。
分为:
天然二水石膏(CaSO4‧2H2O)
天然硬石膏(无水石膏)(CaSO4)
建筑石膏(CaSO4‧1⁄2H2O)
石灰:
以碳酸钙为主要成分的石灰石为原料,经高温煅烧所得的以氧化钙为主要成分的产品。
按化学成分分为:
钙质石灰(MgO<5%)、
镁质石灰(MgO>5%)、
白云石消石灰粉(MgO含量为24%~30%)
熟悉:
石灰、石膏、水玻璃的主要技术性质。
石灰的主要技术性质:
①消化时放热量大,体积膨胀大(1~2.5倍);
②饱水性和可塑性好;
③硬化缓慢且强度低;
④硬化时体积收缩大,且易开裂;
⑤耐水性差。
石膏的主要技术性质:
①凝结硬化块:
7~12min;
②硬化后空隙率大,强度低;
③体积稳定:
微膨胀0.05%~0.15%;
④不耐水:
有强吸湿性,吸湿后强度剧烈降低;
⑤防火性能好;
⑥有一定的调湿作用;
⑦装饰性好。
技术要求:
抗折强度(1.8MPa~2.5MPa)
抗压强度(3.0MPa~5.0MPa)
细度优等品方孔筛筛余不大于5%
凝结时间初凝:
不早于4min左右(根据等级),
终凝:
不迟于30min。
2.骨料
1)细骨料
了解:
细骨料定义。
粒径在0.15~4.75mm之间的骨料
熟悉:
水运工程中对细骨料质量要求的规定。
细骨料的品质检测方法:
颗粒级配筛分析、含泥量及泥块含量、表观密度(标准法、简易法)、堆积密度及紧密密度、吸水率、含水率(标准法、快速法)、含泥量(标准法、虹吸管法)、泥块含量、有机物含量、轻物质含量、坚固性、硫化物及硫酸盐含量、氯离子含量、碱活性等试验(包括目的及适用范围、仪器设备、试验步骤、结果处理及评定)。
(1)、水运工程中对细骨料质量要求的规定:
⑴海水环境工程中严禁采用活性细骨料,淡水环境工程中用细骨料,经验证若有活性时,应使用碱含量小于0.6%的水泥。
⑵当砂的级配不合格时,经试验证明能确保工程质量时,方可允许使用。
⑶采用海砂作细骨料时,海砂含盐量应符合下列规定。
①浪溅区、水位变动区的钢筋混凝土,海砂中的氯离子含量不宜超过0.07%(占水泥重量的百分比计)。
否则应淋洗至限值以下,确有困难时,可在拌制的混凝土中掺入占水泥重量0.6%~1.0%的亚硝酸钠或其他经论证的缓蚀剂。
如拌和用水和外加剂中,氯离子含量低于规定值时,砂的含盐量可适当放宽,但应满足混凝土拌和物中氯离子的最高限值。
②采用碳素钢丝、钢绞线及钢筋永存应力大于400MPa的预应力混凝土不宜采用海砂。
不得不采用时,海砂中氯离子含量不宜超过0.03%(占水泥重量的百分比计)。
(2)、细骨料颗粒级配筛分试验
目的及使用范围:
仪器:
烘箱、天平、方孔筛(.15/.3/.6/1.18/2.36/4.75/9.5mm及筛底、筛盖)、摇筛机、搪瓷盘、毛刷等
试验步骤:
①按规定取样,并将试样缩分至约1100g,在105℃±5℃的烘箱中烘干至恒重,冷却至室温后,筛除大于9.5mm的颗粒(并计算其筛余百分率)分为大致相等的两份备用。
②准确称取烘干试样约500g(m1),准确至1g,置于套筛最上面一只,然后将套筛装入摇筛机,摇筛约10min,然后取出套筛,再按筛孔大小顺序,从最大的筛号开始,在清洁的浅盘上逐个进行手筛,直到每分钟的筛出量小于试样总量的0.1%时为止,将筛出通过的颗粒并入下一号筛,和下一号筛中的试样一起过筛,以此顺序进行到各号筛全部筛完为止。
③称量各筛筛余试样的质量,精确至1g。
试样在各筛号上的筛余量不得超过按下式计算出的量:
;A为筛面面积mm2,d为筛孔尺寸mm。
否则应按下列方法之一进行处理:
a、将该粒级试样分成少于按上式计算出的量,分别过筛,并以筛余量之和作为该号筛的余量;
b、将该粒级及以下各粒级扽筛余混合均匀,称出其质量,精确至1g。
再用四分法缩分为大致相等的两份,取其中一份,称出其质量,精确至1g,继续筛分。
计算该粒级以下各粒级的分计筛余量时应根据缩分比例进行修正。
结果处理及评定:
①计算分计筛余百分率,精确至0.1%;
②计算累计筛余百分率,精确至0.1%;
③砂的细度模数计算,精确至0.01:
;
④累计筛余百分率取两次试验结果的算术平均值,精确至1%。
细度模数取两次试验结果的算术平均值,精确至0.1;如两次试验的细度模数之差超过0.20时,须重新试验。
⑤根据细度模数大小,将砂分为四级:
粗砂:
细度模数在3.7~3.1之间
中砂:
细度模数在3.0~2.3之间
细砂:
细度模数在2.2~1.6之间
特细砂:
细度模数在1.5~0.7之间
(3)、含泥量及泥块含量
略
(4)、表观密度(标准法、简易法)
仪器:
天平,感量1g;容量瓶,500mL;烘箱、干燥器、烧杯、浅盘、温度计、铝制料勺。
测定步骤:
①称取烘干试样300g(m0),装入盛有半瓶冷开水的容量瓶中,摇转容量瓶,使试样在水中充分搅动以排除气泡,塞紧瓶塞。
②静置24h后,打开瓶塞,然后用滴管添水,使水面与瓶颈刻度线平齐。
塞紧瓶塞,擦干瓶外水分,称其重量(m1)。
③倒出瓶中的水和试样,将瓶内外清洗干净,再向瓶内注入与上项水温相差不超过2℃的冷开水至瓶颈刻度线,塞紧瓶塞,擦干瓶外水分,称其重量(m2)。
④试验应在15℃~25℃的温度范围内进行,并进行温度修正。
从试样加水静置的最后2h起至试验结束,其温度相差不应超过2℃。
结果计算:
试样的表观密度
——考虑称量时水温对表观密度影响的修正系数。
以两次平行试验结果的算术平均值作为测定值,如两次结果之差大于20kg/m3时,应重新取样进行试验。
(5)、堆积密度及紧密密度
仪器:
台秤称量5000g,感量5g;容量筒,容积1L;标准漏斗;烘箱;小勺、直尺、浅盘等。
容量筒应先校正其容积。
以温度为20℃±2℃的饮用水装满容量筒,用玻璃板沿筒口滑行,使其紧贴水面,不能夹有气泡,擦干筒外壁水分,然后称重G2。
称量容积筒、玻璃板重量为G1。
V=G2-G1(L)
试样制备:
用四分法缩取试样约3L,置于温度为105℃±5℃的烘箱中烘干至恒重,取出并冷却至室温,再用5mm孔径的筛子过筛,分成大致相等的两份备用,试样烘干后如有结块,应在试验前先予捏碎。
测定步骤:
堆积密度:
①称容量筒重量m0(kg),将其放在不受振动的桌上的浅盘中,用料斗将1份试样徐徐装入容量筒,料斗出料口距容量筒筒口不应超过50mm,直至试样装满并超出容量筒筒口。
②用直尺将多余的试样沿筒口中心线向相反方向刮平,称容量筒连试样的总重量m1。
紧装密度:
①取试样1份,分两层装入容量筒。
装完一层后,在筒底垫放一根直径为10mm的钢筋,将筒按住,左右交替颠击地面各25下,然后再装入第二层。
②第二层装满后用同样方法颠实(但筒底所垫钢筋方向应与第一层放置方向垂直),两层装完并颠实后,添加试样超出容量筒筒口,用直尺将多余的试样沿筒口中心线向相反方向刮平,称容量筒连试样的总重量m2。
结果计算:
试样的堆积密度
;
试样的紧装密度
以两次试验结果的算术平均值作为测定值。
(6)、吸水率、含水率(标准法、快速法)
(7)、含泥量(标准法、虹