安得物流仓储系统方案设计.doc
《安得物流仓储系统方案设计.doc》由会员分享,可在线阅读,更多相关《安得物流仓储系统方案设计.doc(18页珍藏版)》请在冰豆网上搜索。
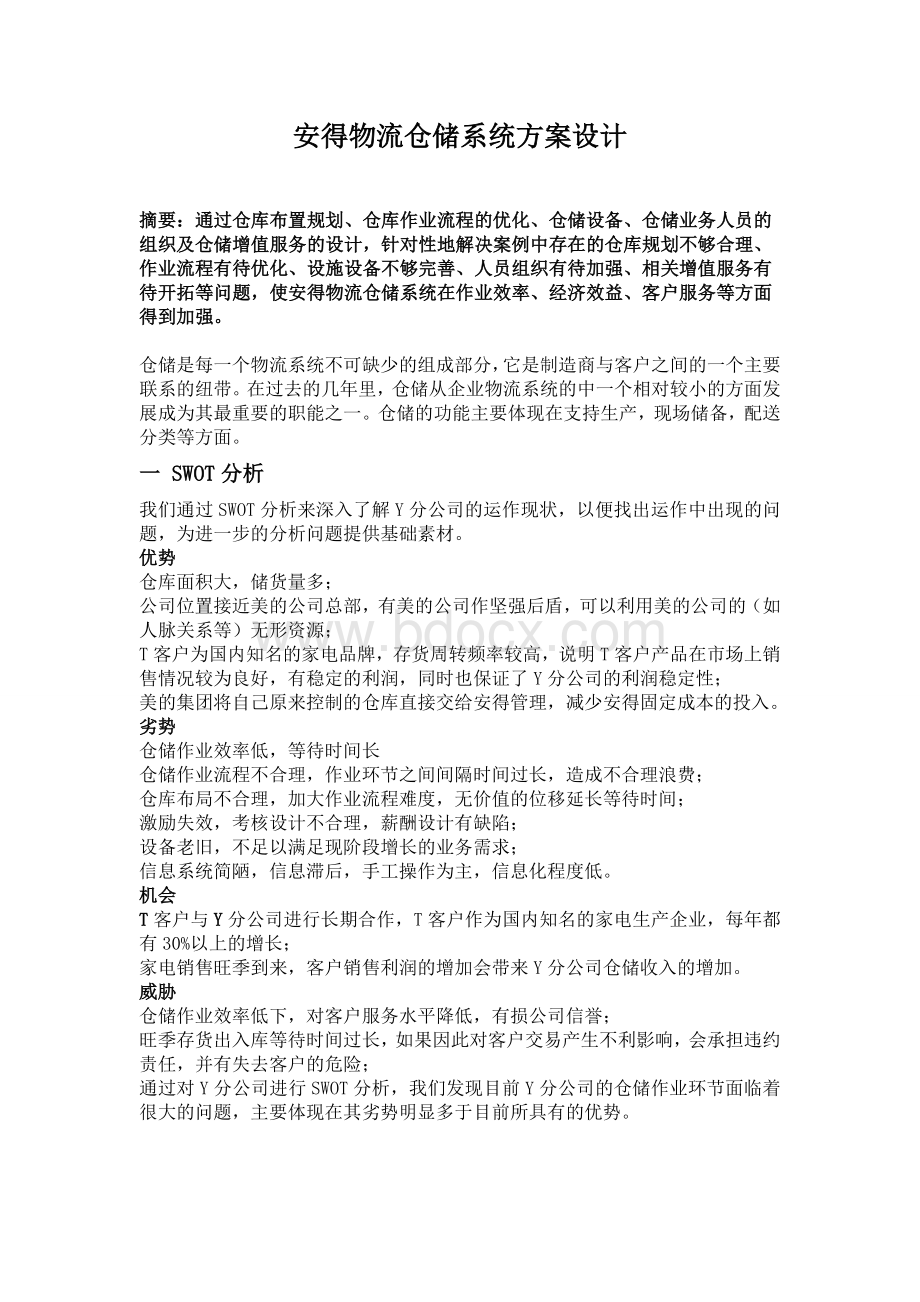
安得物流仓储系统方案设计
摘要:
通过仓库布置规划、仓库作业流程的优化、仓储设备、仓储业务人员的组织及仓储增值服务的设计,针对性地解决案例中存在的仓库规划不够合理、作业流程有待优化、设施设备不够完善、人员组织有待加强、相关增值服务有待开拓等问题,使安得物流仓储系统在作业效率、经济效益、客户服务等方面得到加强。
仓储是每一个物流系统不可缺少的组成部分,它是制造商与客户之间的一个主要联系的纽带。
在过去的几年里,仓储从企业物流系统的中一个相对较小的方面发展成为其最重要的职能之一。
仓储的功能主要体现在支持生产,现场储备,配送分类等方面。
一SWOT分析
我们通过SWOT分析来深入了解Y分公司的运作现状,以便找出运作中出现的问题,为进一步的分析问题提供基础素材。
优势
仓库面积大,储货量多;
公司位置接近美的公司总部,有美的公司作坚强后盾,可以利用美的公司的(如人脉关系等)无形资源;
T客户为国内知名的家电品牌,存货周转频率较高,说明T客户产品在市场上销售情况较为良好,有稳定的利润,同时也保证了Y分公司的利润稳定性;
美的集团将自己原来控制的仓库直接交给安得管理,减少安得固定成本的投入。
劣势
仓储作业效率低,等待时间长
仓储作业流程不合理,作业环节之间间隔时间过长,造成不合理浪费;
仓库布局不合理,加大作业流程难度,无价值的位移延长等待时间;
激励失效,考核设计不合理,薪酬设计有缺陷;
设备老旧,不足以满足现阶段增长的业务需求;
信息系统简陋,信息滞后,手工操作为主,信息化程度低。
机会
T客户与Y分公司进行长期合作,T客户作为国内知名的家电生产企业,每年都有30%以上的增长;
家电销售旺季到来,客户销售利润的增加会带来Y分公司仓储收入的增加。
威胁
仓储作业效率低下,对客户服务水平降低,有损公司信誉;
旺季存货出入库等待时间过长,如果因此对客户交易产生不利影响,会承担违约责任,并有失去客户的危险;
通过对Y分公司进行SWOT分析,我们发现目前Y分公司的仓储作业环节面临着很大的问题,主要体现在其劣势明显多于目前所具有的优势。
二安得物流仓储系统存在的问题
通过以上SWOT分析,进行问题诊断。
案例十“A经理的担忧,仓储设计”所显示的情况,在我国具有一定的代表性,
主要表现在仓库规划不够合理、作业流程有待优化、设施设备不够完善、人员组织有待加强、相关增值服务有待开拓等方面。
案例中Y分公司仓储中存在的问题主要有:
1.出货量不均。
淡旺季出库量差别较明显;同一月中出库量不均,月底最高;
每天出库量在时间分布上也是不均匀的,上午很少。
2.仓库的规划布局不尽合理。
仓管员寻找库位不是很迅速,单次出入库行走的
平均距离长,影响了工作效率,降低了服务质量。
3.作业流程有待优化,等待时间长。
装车、卸车时间较长;装完一车到开始装
第二车,中间间隔时间长;装卸过程采用流水作业方式,一般是库内2人,移动2人,车上2人,经常出现交替等待现象;出入库是依据车到仓库的先后顺序排队,由于受品种影响,有时需依次在两个仓库排两次队。
这些环节中时间的等待,降低了工作效率,造成了无法计量的成本损耗。
4.设施设备不够完善,仓库现代化程度不高。
只有5台柴油叉车,14台液压手推车,没有托盘和货架,仓库使用垫仓板,作用只是防潮,不能作搬运用,每次装车需要经过转板、平移、卸货、装车作业过程,每次卸车需要经过卸货、上板、平移、堆码作业过程,工作效率低,且易损坏物品,加大了物流成本。
5.人员组织有待加强,员工工作不够积极。
装卸工有时在晚上由于作业时间长,
出现干劲不足磨洋工的现象,有时会计较同一组内劳动强度大小及是否快干多干;仓管工、叉车工也会出现出工不出力的情况。
6.服务项目单一,相关增值服务有待开拓。
案例中Y分公司仓库的服务内容比较单一,基本只进行货物的保管。
我们结合案例十“A经理的担忧,仓储设计”提出一整套切实可行的解决方案。
三安得物流仓库规划设计
1安得仓库合理布局的目标
(1)在不增加成本的前提下,有效地提高仓库运作效率
安得公司目前仓库存在的最大问题即为运作效率低下。
在不增加成本的前提下有效提高其作业效率,不仅能增加公司的经营效益,而且能大大提高客户及承运商的满意度,有利于公司的长远发展。
(2)最有效的利用仓库容量
在出货高峰时,仓库容量并不能满足客户需求;而在淡季时,仓库内又存在大量闲置,造成大量浪费。
因此,如何更有效地利用现有仓库容量才是提高仓库效益及提高公司服务质量的重要途径之一。
(3)最有效的利用仓库设备
有问题分析可看出,公司仓库内的设备比较落后且数量不多,因此,要有效提高仓库的运作效率,就要最大限度地发挥设备的功能,提高其利用率及利用质量。
(4)最有效的使用现有人力
由问题分析可看出,公司人力资源利用不够合理,人员利用率不高,作业效率低下。
公司仓库现在主要为手工操作,因此,人员的工作效率会直接影响整个仓库的运作效率。
(5)全部储存货物具有最好的可采性
货物的可接近性也是衡量仓库布局是否合理的重要指标之一,其也会对仓库作业效率产生重要影响。
(6)全部货物能得到最好的保护
货物的安全性直接影响到对客户的服务质量,保证货物的安全与完整性是仓库运营的重要目标之一。
总的来说,一个合理布局的仓库就是由受过良好训练的人用合适的设备将货物存放在合适的空间内,并能实现低成本,高效率,高质量的货物移动,使得准确品种与数量的货物在正确的时间,按照正确的路线到达正确的地点。
2安得仓库布局原则
(1)最小移动距离原则
保持仓库内各项操作之间的最经济距离,货物和人员流动距离尽量缩短,以节省物流时间,降低物流费用。
(2)直线前进原则
要求设备安排,操作流程应能使货物搬运和存储按自然顺序逐步进行,避免迂回,倒流。
(3)充分利用空间,场地的原则
设备,人员,货物在垂直与水平方向上的布局应适当的配合,以充分利用仓储空间。
(4)生产力均衡原则
维持各种设备,各工作站的均衡,使全库能维持一个合理的运行速度。
(5)安全性原则
设计时要考虑操作人员的安全与方便
(6)顺利运行原则
根据仓库空间环境的布局,尽量保持货物存取的顺利。
3仓库规模设计
案例十“A经理的担忧,仓储设计”中的具体情况是T客户公司租赁Y分公司的仓库,仓库规模已经确定,并且基本能满足存储量的需要,因此我们不作更改的建议。
仓库平面面积的确定方法:
仓库平面面积主要由储存货物的数量确定,但还受到其他因素的制约,例如地
面结构的承重能力的大小便影响到单位面积堆存量,还有货物的包装强度影响着堆存高度,又如库房内装卸搬运货物的机械化程度对库房面积的确定也产生影响。
库场总面积可按下式计算:
A=E/λq
式中:
A——库场总面积/m2
E——库场堆存容量/t
E=QK1/T×t
式中:
Q——年库场货物总储量/t
K1——库场不平衡系数
K1=Hmax/H
式中:
Hmax——月最大货堆存天吨数/吨/天
H——月平均货物堆存吨天数/吨/天
t——货物在库场的平均堆存期/天
T——仓库年营运天数,一般取350365天
λ——库场总面积利用系数,为有效面积占总面积的百分比。
有效面积是
实际可供堆存货物的面积,等于总面积中扣除办公室、通道、堆存
间距与墙之间的距离等。
q——单位有效面积货物堆存量(t/m2),该值可以根据实际堆存情况进
行测定,也可在有关手册中查得。
考虑到仓储中可能存在淡季仓库利用率不高的情况,我们建议根据预测,确定
淡季货物的存储量,根据存储量确定所需仓库的面积,对于闲置的仓库空间采取转租给第三方的形式。
4仓库布置设计
仓库内布置设计,是根据仓库场地条件、仓库业务性质和规模、物资储存要求
以及技术设备的性能和使用特点等因素,对仓库各组成部分,如库房、货场、辅助建筑物、库内道路、附属固定设备等,在规定的范围内进行合理安排和布置。
仓库分为储备型和流通型两大类,针对案例十“A经理的担忧,仓储设计”给出的资料,我们认为案例十中的仓库应属于流通型仓库,对此在仓库内部布置设计方面,提出如下建议:
考虑到案例中的3仓库和4仓库应该是Y分公司仓库群组中的2个,整个仓库群组应该另外设有办公楼、设备维修处等机构,因此没必要在每个仓库里都设置这些区域,在此,我们将仓库划分为入库区、检验区、存储区、备货区、出库区。
由于仓库面积(3仓库19000m2,4仓库24000m2)大于2000m2,按标准布置仓库的长宽比为1:
6,以3仓库为例,19000m2按1:
6布置为56m×339m,调整成6m的倍数为60m×318m。
由于长远大于宽,将仓库的进出口分别设置在位于两长边中间的地方(图1-1),以缩短仓库内部作业距离,改善案例十Y分公司仓库中由于单个仓库面积较大,单次出入库行走距离长的问题。
图1-1仓库外观图
(1)仓库各区面积的确定
入库区检验区、备货区出库区面积可用临时保管场地的面积来计算,计算公式:
S=QK/360q
式中:
S——临时保管物资的占地面积;
Q——通过临时保管场地的年进货量;
360——年日历天数;
q——每平方米堆放的数量,即物资存放定额;
K——进货不均衡系数,指在一定时间内(通常以年或季计算)最大进货量
与同期平均进货量之比,一般应大于1。
由案例十“A经理的担忧,仓储设计”得表1-1、图1-2,从中可看出,年平均
入库量为888053,年平均出库量为892194,最大入库量为1141867,最大出库量为1311165,产品堆码标准即每平方米堆放的数量q为25台。
表1-1T客户产品出入库明细表
图1-2客户产品出入库数量图
由于表中给出的年平均出、入库量为3仓库(19000m2)和4仓库(24000m2)的总平均年出、入库量,两个仓库都是给T客户公司服务,这里将出、入库量按仓
库面积比例分配给3仓库和4仓库,以3仓库为例进行规划设计。
仓库入库区检验区面积计算:
仓库年平均入库量=总年平均入库量×3仓库所占比例
=888053×19000/19000+24000=392396
Q=3仓库年平均入库量×12=392396×12=4708752
K=年最大进货量/年平均进货量=1141867/888053=1.286
代入S=QK/360q
得S=4708752×1.286/360×25=673m2
考虑到仓库还有别的客户,T客户平均每月的合同面积占仓库面积的90%,对
算出的面积进行调整,将它扩大10%得3仓库入库区检验区面积为:
S=673×(1+10%)=740m2
仓库备货区出库区面积计算:
仓库年平均出库量=年平均出库量×3仓库所占比例
=892194×19000/19000+24000=394225
Q=年平均出库量×12=394225×12=4730700
K=年最大出货量/平均出货量=1311165/892194=1.470
代入得:
S=4730700×1.470/360×25=773m2
对算出的面积进行调整,将它扩大10%得3仓库备货区出库区面积为:
S=773×(1+10%)=850m2
(2)装卸作业平台规划设计
仓库的各项作业中,进出货是重要的作业项目,装卸作业平台的吞吐能力是影
响此项作业的最大关键。
因此,完善的码头规划及设施兴建,将可大幅提升进出货
作业的顺畅性。
针对案例中Y分公司仓库的具体情况我们提出如下建议:
1建议在仓库的另一侧修建一个同等规模的装卸作业平台(图1-3),以提高