阿胶生产工艺规程.docx
《阿胶生产工艺规程.docx》由会员分享,可在线阅读,更多相关《阿胶生产工艺规程.docx(18页珍藏版)》请在冰豆网上搜索。
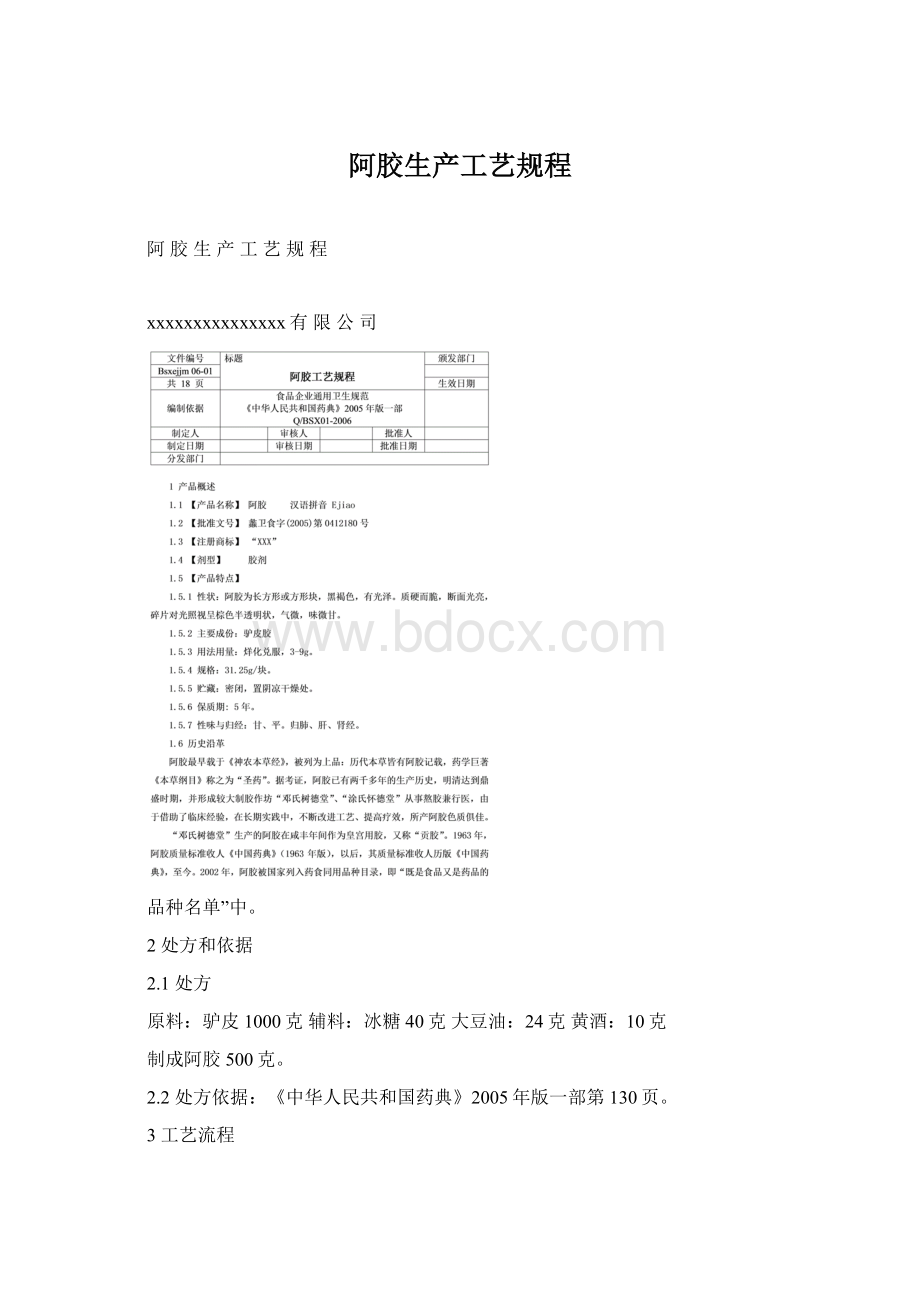
阿胶生产工艺规程
阿胶生产工艺规程
xxxxxxxxxxxxxxx有限公司
品种名单”中。
2处方和依据
2.1处方
原料:
驴皮1000克辅料:
冰糖40克大豆油:
24克黄酒:
10克
制成阿胶500克。
2.2处方依据:
《中华人民共和国药典》2005年版一部第130页。
3工艺流程
驴
皮
挑拣
去杂
浸泡
刮毛割皮
洗皮
提取
过滤
辅料
初浓
续浓
过滤
出胶
凝胶
切胶
晾胶
擦胶、验胶、印字、灭菌
内包料
内包装
前批胶头
外包材
外包装
内为30万级洁净区;
为一般生产区
检验、入库
4原药材的炮制
4.1领料:
依生产部开写的生产指令和原料领料单领取原料驴皮。
双人复核原料质量、称重数量、进厂编号与实物是否相符,是否符合本厂对原料驴皮的有关规定,核对无误后,双人签字。
4.2浸泡
将驴皮投入浸泡池内加水浸泡,浸泡过程中每天按规定换水。
4.3刮毛割皮
将驴皮背部的毛刮去,用刀切割成边长为40cm左右的皮块。
4.4洗皮
将切好的驴皮投入洗皮池中清洗至合格。
4.5工艺技术条件及要求
4.5.1本工序生产工艺时间一般为夏季5天,春、秋、冬季7天。
4.5.2在领料、浸泡、刮毛、割皮及洗皮过程中如发现不合格皮质,及时挑出。
在领料、浸泡过程中挑出的不合格皮质放至原料不合格区内。
在刮毛、切皮及洗皮过程挑出的不合格皮质按废料处理。
5制剂操作过程及工艺条件
5.1提取
5.1.1投料
湿皮称量工将炮制合格的原料装在运料车内,逐车计量,运到提取工序。
提取工将原料投入到蒸球内。
5.1.2焯皮
提取工按标皮重量的0.5%加入碳酸钠,按湿皮与水1:
0.5的比例用水表计量加水量,当达到规定水量后关闭进水阀。
通入清洁蒸汽,通入蒸汽压力控制在0.12-0.15mpa,焯皮40分钟。
然后加饮用水冲洗至洗皮水化验合格。
5.1.3第一次提取
向蒸球内按湿皮与饮用水1:
0.6的比例加水,用水表计量进水量,当达到规定水量后关闭进水阀。
启动蒸球,通入清洁蒸汽,压力表指示压力控制在0.12-0.15mpa,先动态提取1小时,30分钟时停球排汽一次,之后进行静态提取,静态提取6小时,每半小时转动蒸球搅拌2-5分钟。
提取完毕将胶汁过滤至储罐内。
5.1.4第二次提取
向蒸球内按湿皮与饮用水1:
0.5的比例加水,用水表计量进水量,当达到规定水量后关闭进水阀。
启动蒸球,通入清洁蒸汽,控制压力表指示压力在0.12-0.15mpa,动态提取1小时,提取胶汁过滤,与第一次提取的胶汁滤液合并。
提取完毕后出渣。
5.1.5工艺技术条件及要求
5.1.5.1本工序生产工艺时间为16小时。
5.1.5.2严格控制好焯皮、提取加水量及所用气压。
5.2浓缩
5.2.1初浓:
将已过滤放入到初凝锅内的胶汁加热至沸腾,进行初步浓缩放出胶汁,在转至夹层锅内进行续浓。
5.2.2续浓、提沫:
胶汁在可倾式夹层锅内继续浓缩,并将胶汁表面上的浮出的浮沫、杂质提出,每2小时提一次沫,提至胶液表面泛起黄细沫为止。
再转至夹层锅内,并同时将前批次溶化的胶头液转入。
5.2.3过滤、出胶
将胶汁用电动隔膜泵输送至洁净区出胶锅内2小时后开始加辅料,依次加入大豆油、冰糖、黄酒。
继续浓缩达到规定出胶水分(26-29%)时出胶,将胶液转入到专用不锈钢胶箱内,送至凝胶房,并使胶箱中胶液面保持水平。
5.2.4工艺技术条件及要求
5.2.4.1本工序生产工艺时间为26小时。
5.2.4.2控制好加辅料时间,提杂符合要求。
5.3凝胶
5.3.1将装有胶液的胶箱,放置在凝胶房的凝胶区,使胶箱中胶液表面保持水平,在温度0-5℃下冷凝,冷凝10-12小时,按挖胶操作规程将胶坨从胶箱中挖出来放到凝胶架上,冷凝至适宜硬度。
5.3.2工艺技术条件及要求
5.3.2.1生产周期:
30小时左右。
5.3.2.2检查并控制好凝胶房温度在规定范围内,严格掌握挖胶时间。
5.4切胶
5.4.1将冷凝合格的胶坨用切大条机切制成使胶条厚度为4.2±0.1cm大胶条,再用刨胶机刨成规则的胶条,根据水分含量确定下刀量,按规格要求切块,将切好的胶块摆在晾胶板床上。
胶块尺寸:
9.6cm×4.2cm×0.7cm±0.1cm(31.25g/块)
5.4.2工艺技术条件及要求
5.4.2.1生产周期:
4-6小时。
5.4.2.2准确称量胶坨
5.4.2.3胶条厚度符合要求。
刨好的胶条符合规定,严格控制刨花大小。
5.4.2.4胶块重量合格。
5.4.2.5根据实际情况控制好环境的温湿度(温度16~25℃;相对湿度为55%~70%)。
5.5晾胶
5.5.131.25g阿胶晾胶办法:
第一次晾胶在丝网床上翻晾3-5天,在晾胶中网床上晾5-6天,拾起放到瓦胶箱内进行第一次瓦箱,瓦3-4天,立箱、倒箱出胶进行第二次晾胶,晾10-12天后拾起进行第二次瓦箱;瓦箱5-7天,立箱、倒箱后出胶进行第三次晾胶,晾15-20天进行第三次瓦箱,瓦箱3-5天立箱、倒箱后报请质检部门检验,检验合格后转下工序,不合格继续晾制。
5.5.2工艺技术条件及要求
5.5.2.1生产周期:
45-60天(含翻胶)
5.5.2.2根据实际情况控制好晾胶环境的温湿度(温度:
第一次晾胶16~25℃;第二、三次晾胶为18~26℃,相对湿度为55%~70%)。
5.5.2.3控制好晾胶、瓦箱时间。
5.5.2.4胶块晾至规定水分方可转入下工序。
5.5.2.5胶块晾置过程中,如出现裂纹等现象,及时向车间及质管部汇报,及时采取措施。
5.6擦胶、灭菌
5.6.1擦胶:
将粗布用60℃左右的纯化水洗涤,用粗布擦拭阿胶六面,使之符合要求。
5.6.2灭菌:
印完字的胶块送入联动烘干灭菌机内用紫外线照射灭菌。
5.6.3工艺技术条件及要求
5.6.3.1生产周期:
36小时。
5.6.3.2擦胶块六面光滑洁净,无黄沫、指印、白点、有传统布纹;印字后的胶块字迹清晰、字体端正、颜色浓淡适宜,且擦而不易掉色;灭菌时联动烘干灭菌机温度控制在30~40℃,灭菌时间30分钟。
5.6.4环境温湿度要求:
温度为18~26℃,相对湿度为55%~68%。
5.7内包装
5.7.1胶块按批包装指令包装成规定小包装。
5.7.2工艺技术条件及要求
5.7.2.1玻璃纸包装应包封紧密,表面无皱褶。
5.7.2.2铝塑包装应严密,边角切割整齐,胶块字体与铝箔字体方向一致。
5.7.2.3环境温湿度要求:
温度为18~26℃,相对湿度为55%~68%。
5.8外包装
5.8.1装盒:
将小包装按规定装盒,并密封。
5.8.2装箱:
按批包装指令将产品装入箱内,装入装箱单,印上规定内容,封箱,请验。
5.8.3请验、入库
车间填写请验单报车间QA取样,送质量检验室检验,检验合格者发放合格报告及合格证。
不合格的产品按规定程序处理。
5.8.4工艺技术条件及要求
包装盒印制批号、生产日期和保质期应正确、清晰、端正;装盒数量准确;热缩后包装盒的外观应严密、美观、无破损等;装箱单印制内容正确、齐全;包装箱所印批号、生产日期、保质期等内容正确;装箱数量符合规定。
6各工序质量监控
主要过程控制点及控制项目
工序
控制点
控制项目
检查次数
炮
制
物料
核对物料标志、合格证
每批
挑拣
无杂质
随时
浸泡
浸泡程度
随时
刮毛切皮
去毛程度、切皮大小
随时
洗皮
洗净程度,洗皮水澄清度、氯离子含量
每批
提取
称量
数量
每批
焯皮
洗皮水澄清度、氯离子含量、PH
每批
提取
加水量、时间、温度、压力
随时
过滤
过滤液无明显沉淀杂质
每批
浓缩
浓缩
气压、真空度、温度、相对密度
随时
提沫、加前批胶头
提沫程度、胶头批号、水分、数量
每批
添加辅料
品种、数量
每批
切胶
出胶
水分、水不溶物、挥发性碱性物质、灰分、凝冻浓度、含氮量、砷盐、重金属
每批
切条
尺寸
随时
切块
重量差异、方正度
晾胶
晾胶、瓦胶
外观、水分
每批
擦胶
擦胶
洁净
随时
灭菌
时间
随时
内包装
内包材
外观、洁净度、合格证
每批
内包装
密封性(玻璃纸包装);密闭性(铝塑包装)
随时
外包装
说明书
品名、内容、数量、文字清晰度
每批
装盒
品名、内容、产品批号、数量、保质期、生产日期
抽查
装箱
品名、产品批号、数量、装箱单、捆扎、保质期、生产日期
送检
成品检验
每批
6.1原料炮制工序制定《原料炮制工序现场监控规程》
6.2提取工序制定《提取工序现场监控规程》
6.3浓缩工序制定《浓缩工序现场监控规程》
6.4凝胶工序制定《凝胶工序现场监控规程》
6.5切胶工序制定《切胶工序现场监控规程》
6.6晾胶工序制定《晾胶工序现场监控规程》
6.7擦胶工序制定《擦胶工序现场监控规程》
6.8内包装工序制定《内包装工现场序监控规程》
6.9外包装工序制定《外包装工序现场监控规程》
7质量标准
7.1原料
7.1.1驴皮执行《驴皮质量标准》
7.2辅料
7.2.1大豆油执行《大豆油质量标准》
7.2.2冰糖执行《冰糖质量标准》
7.2.3黄酒执行《黄酒质量标准》
7.3包装材料
7.3.1药用PVC板:
执行《聚氯乙烯(PVC)硬片质量标准》
7.3.2铝箔:
执行《药品包装用铝箔质量标准》
7.3.3使用说明书:
执行《阿胶说明书质量标准》。
7.3.4包装盒:
执行《阿胶包装盒质量标准》。
7.3.5包装箱:
执行《阿胶包装箱质量标准》。
7.3.6玻璃纸:
执行《玻璃纸质量标准》。
7.3.7PVC膜:
执行《PVC膜质量标准》。
7.3.8打包带:
执行《打包带质量标准》。
7.4中间产品的质量标准
7.4.1制胶车间
7.4.1.1挥发性碱性物质≤0.10g/100g
依《中国药典》2005年版一部130页阿胶项下和附录IXL氮测定法的第二法检测。
7.4.1.2总灰分≤1.0%
依《中国药典》2005年版一部附录48页总灰分检查方法检测。
7.4.1.3重金属≤30ppm
依《中国药典》.2005年版一部附录45页重金属检查方法检测。
7.4.1.4砷盐≤3ppm
依《中国药典》.2005年版一部附录46页砷盐检查方法检测。
7.4.1.5含氮量≥12.0%
按《胶剂含氮量检测操作规程》检验。
7.4.1.6水不溶物≤2.0%
按《胶剂水不溶物检测操作规程》检验。
7.4.1.7凝冻浓度≤12%
按《胶剂凝冻浓度检测操作规程》检验。
7.4.1.8油气孔检验合格率≥90%
按《胶剂油气孔检测操作规程》检验。
7.4.2切胶车间
7.4.2.1重量差异依定量包装商品净含量计量检验规则检测应符合规定。
7.4.2.2胶块方正度合格率≥90%
按《胶剂方正度检测操作规程》检验。
7.4.3晾胶车间中间产品:
7.4.3.1水分≤15%
按《中国药典》2005年版第一部附录47页水分测定方法检测。
7.4.3.2边角齐全率≥90%
按《胶剂边角齐全率检查操作规程》检验。
7.4.3.3平整率≥90%
按《胶剂平整率检查操作规程》检验。
7.5成品的质量标准
执行Q/BSX01-2006阿胶质量标准。
7.5.1性状:
本品为长方形或方形块,黑褐色,有光泽。
质硬而脆,断面光亮,碎片对光照视呈棕色半透明状。
气微,味微甘。
7.5.2水分≤15%
按GB/T5009.3规定的方法进行。
7.5.3总灰分≤1.0%
按GB/T5009.4规定的方法进行。
7.5.4水不溶物≤2.0%
按《中国药典》2005年版规定的方法进行。
7.5.5挥发性碱性物质(N计)≤0.10%
按《中国药典》2005年版规定的方法进行。
7.5.6蛋白质≥70%
按GB/T5009.5规定的方法进行。
7.5.7总砷检验≤0.5mg/kg
按GB/T5009.11规定的方法进行。
7.5.8总铅检验≤1.0mg/kg
按GB/T5009.12规定的方法进行。
7.5.9总铜检验≤2.0mg/kg
按GB/T5009.13规定的方法进行。
7.5.10总汞检验≤0.3mg/kg
按GB/T5009.17规定的方法进行。
7.5.11菌落总数检验≤1000cfu/g
按GB/T4789.2规定的方法进行。
7.5.12大肠菌群检验≤30MPN/100g
按GB/T4789.3规定的方法进行。
7.5.13致病菌检验(指肠道致病菌和致病性球菌)不得检出
按GB/T4789.4、GB/T4789.5、GB/T4789.10、GB/T4789.11、和GB/T4789.15规定的方法进行。
8设备与计量
8.18m3蒸球主要技术参数
序号
名称
指标
1
蒸球内径
直径2.5m
2
蒸球容积
8m3
3
设计压力
0.275MPa
4
设计温度
141℃
5
物料名称
水(3m3)
6
试验压力
0.38MPa
7
最高压力
0.25MPa
8
电动机
型号
Y132M2-6
功率
5.5KW
转速
960转/分
电压
380V
9
外形尺寸
长
3.50m
宽
2.50m
高
3.15m
10
容器净重
1900kg
8.2可倾式夹层锅主要技术参数
容积
600L
换热面积
2.2m2
容器净重
215kg
介质
蒸汽
设计温度
140℃
最高工作压力
0.25MPa
设计压力
0.27MPa
耐压试验压力
0.34MPa
8.3HL-290直线往复式阿胶切片机主要技术参数
速度
100次/分
生产能力
200kg/h
电机功率
1.5KW
8.4联动烘干灭菌机主要技术参数
电动机转速
250转/分
设备运行速度
0.43米/分
电机功率
1.1KW
紫外线灯之间距离
1m
紫外线灯与被照射物之间距离
上下各60cm
晾胶床尺寸
长×宽91cm×76cm
设备净重
6吨
外形尺寸(长×宽×高)
1300cm×120cm×150cm
8.5DPP-250自动泡罩铝塑包装机
冲截频率
20-30次/分
最大成形面积
240mm×140mm
成形深高
≤26mm
标准行程
80mm
行程可调范围
40-140mm
电机功率
1.1KW
成形加热频率
上下各1.5KW
热封加热频率
1.5KW
气压
≥0.7Mpa
气泵排气量
≥0.3立方米/分
包装材料
1药用PVC130mm×0.25mm
2铝箔PTP130mm×0.02mm
整机重量
1.2吨
整机外形尺寸
长×宽×高2200mm×650mm×1700mm
8.6各类量器、衡器、仪表、精密仪器及时校验,并有计量监督部门核发的计量检验合格证书。
9安全与环保
9.1安全
9.1.1技术安全:
加强对职工的安全教育,各种设备都要严格按岗位标准操作,不得违章作业,杜绝一切事故发生,做好防烫伤、刀伤、防爆、防腐蚀、防毒等工作。
经常监督检查并做好记录。
9.1.2劳动保护:
在生产过程中按规定及时为职工发放劳动和防护用品,安装保护设施。
9.1.3严格遵守安全生产管理规程。
9.2环保
9.2.1废水的管理和处理:
该产品生产废水主要来自泡皮、洗皮和搓皮等工序,主要污染物有泥沙、驴毛、悬浮物,可对其适当沉淀处理后用于灌溉。
9.2.2废渣的处理和管理
该产品主要废渣为毛渣和锅炉用煤产生的废渣,存放于远离制剂车间专用区,并有专职人员每3天彻底清运出厂,不造成污染。
9.2.3废气的处理
该产品产生的废气主要来自提取工序,并由管道引入到地下,其它工序产生的废气量极少,一般无需回收处理。
9.2.4烟尘
锅炉释放的烟尘经过过滤后,达标排放。
9.2.5噪音的管理
该产品在生产中没有超过国家排放标准的噪音产生,不需特殊处理。
10劳动组织、定岗定员、工时定额及生产周期
10.1岗位定员与工时定额(每批产品计划产量500kg)
工序
人员定额
主要工作内容
工作量或产量
原料处理
人
泡皮、刮毛切皮、洗皮、清场
每日处理批原料用量
提取
人
投料、焯皮、提取、出渣、清场
每日生产批产品
浓缩
人
初浓、提沫、过滤加辅料、清场
每日生产批产品
凝胶
人
出胶、凝胶、递胶、清场
每日挖胶批,递胶批
切胶
人
切胶、摆胶、清场
每日切胶批,摆胶批
晾胶
人
晾胶、瓦胶、清场
每日交产品至少批
包装
人
擦胶、验胶、灭菌、包装
每日至少包装批产品
10.2产品生产周期
10.2.1原料炮制处理工序:
夏季5天;春、秋、冬季7天。
10.2.2投料提取:
16小时
10.2.3浓缩出胶:
26小时
10.2.4凝胶:
30小时
10.2.5切胶:
2.5小时
10.2.6晾胶(含翻胶):
45-60天(31.25g胶块)。
10.2.7包装:
25小时
10.2.8合计:
31.25g阿胶需55-75天。
10.3劳动组织划分
10.3.1原料的炮制与提取浓缩为一生产车间。
10.3.2凝胶、切胶为一车间。
10.3.3晾胶工序为一车间。
10.3.4擦胶、印字灭菌、内包装、外包装为一车间。
10.3.5锅炉班、空调组、维修班、电力班为一车间,负责全厂动力能源的供应和生产设备检修、保养等工作。
11消耗定额
11.1中间产品消耗定额
11.1.1切胶成品率31.25g阿胶不低于75%。
11.1.2晾胶中间产品不合格率不高于3%。
11.1.3包装中间产品破损率不高于1%。
11.2包装材料消耗定额
11.2.1PVC板定量8Kg/100Kg损耗不超过1%
11.2.2铝箔纸定量1.4Kg/100Kg损耗不超过1%
11.2.3小包装玻璃纸1.2Kg/100Kg损耗不超过1%
11.2.4包装盒、说明书定量损耗不超过1%
11.2.5包装箱损耗不超过2%
11.3动力消耗定额(800Kg/批)
11.3.1用水消耗定额:
每100kg阿胶,水60吨。
11.3.2用电消耗定量:
每100kg阿胶,电230度。
11.3.3用煤消耗定额:
每100kg阿胶,煤0.7吨。
12物料平衡的计算方法:
12.1制胶车间物料平衡计算公式:
实际产量/理论产量×100%
实际产量为该批产量折干数减去加入前批鲜胶头折干数及干胶头数。
理论产量为计划产量。
12.2切胶车间物料平衡计算公式:
(中间产品数量+胶头数量)/接收产品数量×100%
中间产品数量为交出的产品块数乘以产品规格。
胶头数量为胶头的折干数。
接收产品数量为本批鲜胶重量的折干数。
12.3晾胶车间物料平衡计算公式:
(交出中间产品数量+胶头数量+取样量)/接收中间产品数量×100%。
交出中间品数量为交下工序产品数量(合格产品块数乘以产品规格)。
胶头数量为胶头的称量数量。
取样量为取样块数乘以产品规格。
12.4包装车间
12.4.1产品物料平衡计算公式:
(包装产品入库数量+检验和留样数量+胶头数量)/接收产品数量×100%
12.4.2包装材料物料平衡计算:
(包装盒、标签、说明书)领用数=使用数+破损数+退回数×100%
物料平衡平衡值:
工序(岗位)
平衡值
工序
平衡值
制胶车间
90%-110%
切胶车间
98%-101%
晾胶车间
97%-100%
包装车间
98%-100%
包装盒、说明书
100%
13有关计算公式
13.1下刀量计算公式:
下刀量(g)={500(1-14%)}/(1-t)
式中t:
为本批鲜胶含水量
13.2切胶成品率计算公式:
切胶成品率(%)={交下道工序的产品重量(切出的中间产品胶块重量)/接上工序鲜胶的折干胶重量}×100%
折干胶重量(kg)={鲜胶重量(1-鲜胶含水量)}/(1-14%)
式中14%:
为阿胶水分的厂控标准。
13.3晾胶破损率计算公式:
晾胶破损率(%)={(实际接收切胶工序重量-实际交给包装工序的重量)/实际接收上工序的重量}×100%
13.4包装中间产品破损率计算公式:
包装中间产品破损率(%)={本工序破损重量/实际接收晾胶工序重量}×100%
13.5包装材料破损率计算公式:
包装材料破损率(%)={破损数量/(领取数量-退库数量)}×100%
13.6动力消耗定额计算公式:
动力消耗定额(水、电、汽)=每月实际消耗用量/本月阿胶的产量(入库成品)
15附页(供修改本工艺时记录用)
修改时间
修改原因
修改前内容
修改后内容
修改申请人
批准人