宣钢180tLF炉精炼渣的优化.docx
《宣钢180tLF炉精炼渣的优化.docx》由会员分享,可在线阅读,更多相关《宣钢180tLF炉精炼渣的优化.docx(13页珍藏版)》请在冰豆网上搜索。
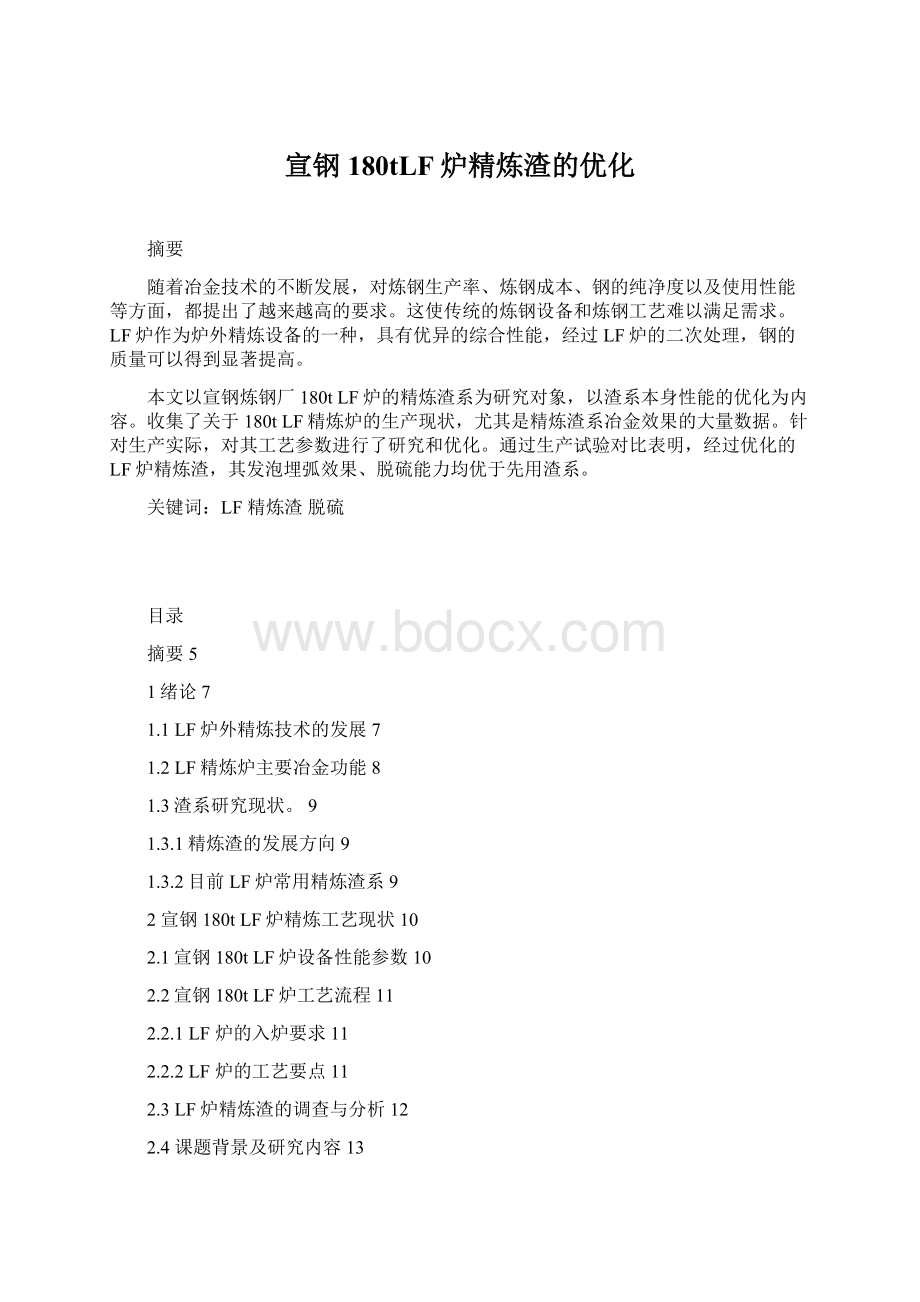
宣钢180tLF炉精炼渣的优化
摘要
随着冶金技术的不断发展,对炼钢生产率、炼钢成本、钢的纯净度以及使用性能等方面,都提出了越来越高的要求。
这使传统的炼钢设备和炼钢工艺难以满足需求。
LF炉作为炉外精炼设备的一种,具有优异的综合性能,经过LF炉的二次处理,钢的质量可以得到显著提高。
本文以宣钢炼钢厂180tLF炉的精炼渣系为研究对象,以渣系本身性能的优化为内容。
收集了关于180tLF精炼炉的生产现状,尤其是精炼渣系冶金效果的大量数据。
针对生产实际,对其工艺参数进行了研究和优化。
通过生产试验对比表明,经过优化的LF炉精炼渣,其发泡埋弧效果、脱硫能力均优于先用渣系。
关键词:
LF精炼渣脱硫
目录
摘要5
1绪论7
1.1LF炉外精炼技术的发展7
1.2LF精炼炉主要冶金功能8
1.3渣系研究现状。
9
1.3.1精炼渣的发展方向9
1.3.2目前LF炉常用精炼渣系9
2宣钢180tLF炉精炼工艺现状10
2.1宣钢180tLF炉设备性能参数10
2.2宣钢180tLF炉工艺流程11
2.2.1LF炉的入炉要求11
2.2.2LF炉的工艺要点11
2.3LF炉精炼渣的调查与分析12
2.4课题背景及研究内容13
3、LF炉精炼渣的优化研究13
3.1精炼炉渣组分的作用13
3.2LF炉精炼渣系的选择16
3.3优化后主要材料及理化指标16
5结论、17
参考文献17
1绪论
1.1LF炉外精炼技术的发展
炉外精炼又称为“二次精炼”,把传统的炼钢流程分为两步:
初炼和精炼。
并在真空、惰性气氛或可控气氛下进行脱氧、脱硫、去气去夹杂、成分微调、控制钢水温度等。
炉外精炼的目的是:
脱硫、脱碳、脱气、合金化、夹杂物形态控制和去除、均匀钢水成分和温度、钢水升温等。
最初的炉外精炼用于冶炼高品质特殊钢,1933年Perrin用高碱度合成渣进行炉外脱硫,开创了炉外精炼的先河。
炉外精炼作为现代炼钢流程中的重要生产工序,被世界多数钢铁厂广泛采用。
原苏联在1975年到1990年,炉外精炼比有0.7%提高到45.9%。
随着纯净钢生产技术的发展以及降低生产成本的要求,近20年来炉外精炼技术得以大力发展,炉外精炼工艺与设备迅速普及。
2003年国外精炼比已经>75%,我国炉外精炼发展情况见表1.1。
炉外精炼的发展方向是试验工艺控制智能化、处理设备多功能化及减少污染排放,加强环境保护。
表1.1我国炉外精炼发展情况
1971年日本特殊钢公司(大同钢特殊钢公司)开发了钢包精炼炉,即LadleFurnace简称LF。
LF精炼炉最初最初的发展是使其功能能适应提高电炉生产率和产品质量的要求,最主要的是适应连铸的生产要求。
LF精炼炉的操作和质量稳定,能够在一定时间内提供理想温度的钢水,有效的调节了工序间的配合。
随着LF精炼炉技术和设备的发展,LF精炼炉已不仅只应用于电炉的生产。
在LD-LF-CC生产流程中,LF精炼炉在钢水温度严密调整和工序时间管理方面发挥了最大效果。
使LD能够生产合金钢,扩大了冶炼的品种范围。
发展到现在,尤其是连铸得到大力发展之后,LF炉已经成为LD-LF-CC流程中生产节奏调节的关键。
通过强化LF炉精炼技术,可以显著提高生产率、产品质量,降低综合冶炼消耗,进而降低生产成本。
1.2LF精炼炉主要冶金功能
LF工艺克服了钢液温降过大的缺点,具备氩气搅拌、埋弧加热、渣洗、还原气氛功能,具有极大的灵活性。
而且设备投资少,精炼成本低,适合生产低硫钢和超低硫钢,其特点是:
1)、在稳定的精炼渣下精确地加入合金料,准确地控制钢液化学成份和节省各种合金及脱氧剂;
2)、通过渣系和钙处理,控制夹杂物的数量和形态;
3)、通过氩气在钢液中的强烈的紊流流动,使钢液温度、成份均匀化,促进氧化夹杂物的凝聚和去除,改善钢液的清洁度;
4)、通过降低压力并与促进气体之间物质交换的措施相结合,降低钢中氩和氮含量,以消除白点和减弱氮的有害作用,喷入各种脱硫粉剂,能得到含硫低的钢液,并达到控制硫化物和氧化物形态的目的。
5)、采用石墨电极埋弧加热,精确地调整钢液温度,在初炼炉与连铸机之间起到缓冲与协调作用,稳定连铸工艺,并促进连铸机和热轧机的高温直接连接.
LF炉的几大精炼功能是互相影响、互相依从与互相促进的,其关系如图1.1
图1.1LF炉精炼功能的关系
1.3渣系研究现状。
1.3.1精炼渣的发展方向
1)系列化。
随着对高品质钢材的需求增加,单一配方的LF炉渣已经不能满足纯净钢的生产需要,必须根据自己的需要针对不同钢种类别开发系列化的LF炉精炼用渣。
LF炉的合成渣精炼功能可以取代电炉的还原操作,更好地完成脱硫、脱氧和去气去夹杂任务,因此合成精炼渣技术日益受到广泛重视。
2)无氟化。
CaF2在冶炼过程中易与渣中其它组元反应,产生含氟气体,危害人体健康,污染环境;另外渣中过高的CaF2,还会使炉渣粘度过小,不利于埋弧加热,加剧对炉衬的侵蚀。
3)高碱度。
国外精炼渣的特点是高碱度,并获得了较好的精炼效果。
国内LF炉精炼渣的碱度大多处于2.0~3.0,脱硫效果比较差。
因此提高碱度也是国内LF炉精炼用渣的发展方向。
1.3.2目前LF炉常用精炼渣系
到目前为止,人们已经研究了多种精炼渣系,应用范围最广的是CaO基渣系。
这是由于CaO具有很强的脱硫能力,而且原材料丰富,成本低廉。
CaO基渣系主要包括以下几个渣系:
1)CaO—CaF2,渣系
CaO—CaF2渣系具有很强的脱硫、脱氧能力。
该渣系在1500℃下的硫容高达0.03,CaO—CaF2渣系中,CaO的主要作用是提高碱度,而CaF2的主要作用是降低合成渣的熔化温度,提高炉渣流动性,这样更有利于脱硫。
CaO与CaF2应有一合适比例,比值过高,渣中CaO含量过高,流动性差,炉渣熔化温度高,既浪费了能源,又使精炼效果不理想;比值过低,渣中CaF2含量过高,碱度不够,对脱硫不利,对炉衬的侵蚀加剧。
国内外常用的CaO/CaF2比值介于6/4和8/2之间,个别的也有达到钟9/l的。
该渣系的最大缺点是含有较高的CaF2,一方面对炉衬的侵蚀较快,使炉龄缩短;另一方面又对大气造成了污染,同时冶金过程中挥发的氟会危害操作工人的身体健康。
2)CaO—A1203渣系
CaO—A1203渣系也具有较强的脱硫能力,该渣系也被用来生产超低硫钢。
ET.Turkdogan等人对熔融氧化物的硫容进行了研究,他们认为与硅酸盐相比,铝酸盐的脱硫速度和硫容更大。
可见,采用该渣系脱硫潜力很大。
近年来,国内外钢厂从经济和环保等角度考虑,也迫切要求采用无氟或低氟的精炼渣系来代替CaO-CaF2渣系。
到目前为止,已知的精炼渣系CaO/A1203介于1/1与2/l之间,但该渣系的炉渣流动性稍差,这需要在以后的工作中进一步研究、解决。
3)Cao—A1203—CaF2渣系
就国内外应用的情况来看,无氟渣存在流动性升不好的缺点,完全采无氟渣系还有待于研究。
国内部分钢厂和国外很多钢厂都在CaO—A1203渣系的基础上加入适量CaF2,形成CaO—A1203—CaF2渣系,但在实际生产过程中,由于脱氧产物和精炼渣原料中都会不可避免的带入部分Si02,因而实际渣系为CaO—A1203—CaF2一siO2四元渣系。
Kor和Richardson测定了该渣系在1550℃时的硫容量。
测定结果表明,CaF2渣的对硫含量影向很小,而主要取决于CaO/A1203的大小。
当CaO/A1203值一定时,随CaF2含量增加,1gKs呈一平滑抛物线,Ks变化不大,而当CaO/A1203值增加时,1gKs显著增加。
对该渣系进行研究后得出CaO/CaF2大于O.15后,脱硫效果才比较理想。
2宣钢180tLF炉精炼工艺现状
2.1宣钢180tLF炉设备性能参数
宣钢150t炉区拥有两座双工位旋转式180tLF精炼炉两座。
钢包容量:
最大180t,最小120t;变压器:
容量38000KVA,二次额定电流42KA,一次电压35KV,二次电压493-361V。
电极直径:
500mm电极行程3000mm。
升温速度>5℃/min
2.2宣钢180tLF炉工艺流程
宣钢180tLF炉精炼工艺流程如图2.1所示
图2.1宣钢180tLF炉精炼工艺流程
2.2.1LF炉的入炉要求
1)进站钢水符合YB9058—92的要求。
2)使用红包出钢。
3)进站钢水顶渣厚度<50mm,保证净空高度≤550mm。
4)做到良好密封。
5)进站钢水[C]控制在目标中、下限。
2.2.2LF炉的工艺要点
1)入LF炉前所有设备:
风、水、电、机、液处于良好状态,并联系好高压电。
钢包必须烘烤,包沿无钢瘤,包内无残渣,氩气畅通。
2)钢包入坐包位后,钢包车开到加热位,吹氩正常3min后测温、取样。
3)根据氩气和渣厚情况,布料供电,约10min后断电,调整氩气和炉渣流动性等。
4)根据分析结果调整成分,供电化合金,温度≥出战温度20~30℃。
5)成分、温度合适,在线喂丝。
调整氩气流量,确保软吹不裸露钢液。
6)加覆盖剂后开回精炼位,同时调小除尘,防止降温和二次氧化。
7)吹氩时间达到要求,温度合适即可出钢。
2.3LF炉精炼渣的调查与分析
由于150t炉区以中低碳钢为主,本文以CO2气体保护实芯焊丝钢ER70S-6为例进行了调查。
物料加入数量及顺序:
合成渣1500-1700㎏,白灰200-300㎏,铝矾土≤200㎏,埋弧渣100㎏,萤石根据渣况调节400-600㎏,初次上电尽可能不要加萤石,保证炉渣发泡充分埋弧。
其渣样分析及脱硫率见表2.1。
该渣系碱度均值1.6,脱硫率较低,由于精炼硫高强打线脱硫改钢为ER50-6比例达9%,遇有硫高铁水则靠铁水预脱硫和转炉控硫,生产波动频繁,周期不好保。
一旦出钢硫≥0.030﹪时则靠LF炉很难按ER70S-6钢工艺降硫到要求范围。
调查发现:
虽然进精炼钢水硫较低,但精炼脱硫率低,脱硫过多依赖起前几道工序;精炼辅助时间长,有效精炼时间短;渣系中SiO2含量高,碱度低,渣量大渣料加入多成本高等现象。
以上诸多因素使得焊丝钢中夹杂物的形态、大小和数量难控,影响铸坯的内在质量,导致盘条在拉拔过程中发生断裂,且影响焊丝的使用性能和焊缝质量,也造成焊缝金属缺陷。
本文对统计2011年9月冶炼148炉数据进行了统计,部分数据如表2.1:
表2.1精炼后的渣样
炉号
CaO%
MgO%
SiO2%
Al2O3%
MnO%
FeO%
R
110403529
34.02
6.64
21.18
19.60
2.63
2.06
1.6
110403531
33.67
6.61
21.28
15.34
3.02
2.02
1.58
110504264
34.30
6.92
23.60
12.82
3.94
1.76
1.45
110504266
40.87
9.27
24.65
12.77
6.52
0.92
1.66
110503637
31.77
6.81
21.95
14.74
2.97
1.76
1.45
110503641
37.13
6.27
18.69
19.20
2.99
2.72
1.98
有表2.1中炉渣成分数据计算得出以下结论:
1)、炉渣的碱度偏低。
一般精炼渣中碱度为(R﹦2.2~3.0),低碱度(R﹦(1.6~2.2)。
渣样分析中最高碱度R﹦1.98,最低碱度R﹦1.45,属于低碱度范围。
2)、炉渣氧化性较强。
渣样分析中最高FeO含量为2.72%,最低FeO含量为0.98%;最高(FeO+MnO)%﹦7.44,最低(FeO+MnO)%﹦4.69%。
3)、LF炉渣中MgO%偏高,渣样分析中MgO%最高为9.27%,渣样分析中MgO%最低为6.27%。
说明精炼炉渣对钢包内衬镁碳砖的侵蚀严重,随着精炼时间的增加,精炼渣中的MgO%越高。
会增加炉渣的粘度,使炉渣流动性恶化;为了改善炉渣流动性又会补加萤石,又加剧了对钢包内衬镁碳砖的侵蚀,如此形成恶性循环。
2.4课题背景及研究内容
LF精炼是目前宣钢生产品种钢的关键技术,而LF精炼炉渣是实现LF炉各项功能不可或缺的组成部分。
一台硬件设备先进的LF炉,若没有相应的精炼渣与之匹配,其精炼功能根本不可能发挥。
国内外研究和生产实践表明,要充分发挥LF炉的作用,对于不同的钢中类别,最好有相应的精炼渣系与之配合。
随着两座180tLF陆续投产,LF炉生产的品种数量越来越多,产量越来越大,但由于现有LF炉精炼渣配方单一,不但严重限制了LF炉在高级品种钢生产中的优势发挥,而且已经不能满足品种钢生产的需要,特别是对夹杂物级别要求较高的钢中。
因此,根据国内外的研究情况和其它厂家的生产经验,结合宣钢生产实际,CO2气体保护实芯焊丝钢ER70S-6用精炼渣系进行优化研究。
论文具体内容包括:
1)精炼炉渣组分的作用的研;
2)LF炉精炼渣系的选择;
3)造渣材料和具体操作的优化。
4)优化后的渣系及其效果
3、LF炉精炼渣的优化研究
3.1精炼炉渣组分的作用
1)、CaO
CaO主要影响精炼渣的碱度。
精炼渣的碱度对精炼过程的脱氧脱硫有较大影响。
精炼渣的碱度不能过大,如碱度过大,精炼渣熔化困难,流动性不好,影响脱氧脱硫效果。
碱度R(CaO/Si02)≥2为高碱度渣,高碱度渣适用于一般铝镇静钢精炼,在钢水脱硫等方面具有较好的效果。
对于具有特殊要求的钢种,如帘线钢、钢丝绳钢、轴承钢等,需采用低碱度渣。
CaO—SiO2—MgO—A1203渣系脱硫实验表明,渣碱度R对渣钢硫分配比Ls具有较大影响。
当碱度R<3.0时,碱度增加,Ls随之增加:
而当R>3.0时,继续增加R,Ls下降。
随CaO含量的提高,[S]降低,但当CaO>60%后,CaO含量提高能使脱硫效果降低
2)、A1203
A1203属于两性氧化物,在LF炉精炼渣中行为作用复杂,A1203其本身无脱硫作用,一般认为它在LF炉精炼渣中呈酸性,降低精炼渣碱度。
另外,A1203过高时还不利于钢中A1203夹杂的去除。
但是A1203可以显著降低LF炉精炼渣的熔点,提高流动性,促进脱硫反应的进行。
目前,为研究A1203在LF炉精炼渣中的行为规律,很多冶金工作者用渣的指数(又称曼内斯曼指数)对脱硫的影响规律来表征A1203的作用。
很多实验研究表明,渣指数在0.2~0.4时,硫的分配比最大,因此,一般精炼渣中A1203的含量控制在10%~18%,。
宣钢180tLF炉精炼渣中的平均含量为15%左右,的配比是比较合理的。
但是,A1203含量的波动范围比较大,对于品种钢的生产来说,现在宣钢180tLF炉精炼渣中A1203的的这个配比对铝镇静钢的精炼稍微偏高,不利于钢中A1203夹杂的去除;对于硅镇静钢来说,A1203的配比则还可以提高,以进一步发挥精炼渣的脱硫作用。
3)、CaF2
CaF2可显著降低精炼渣粘度,使炉渣流动性改善,增加传质,有利于脱硫。
但其量过大,不仅不利于脱氧,而且对炉衬侵蚀也较快。
对发泡效果而言,其影响是两方面的。
一方面,CaF2量的增加使表面张力降低,有利于炉渣发泡,但另一方面,使炉渣粘度降低,不利于发泡,不过在整个发泡过程中,张力起主导作用。
因此,CaF2的增加有利于炉渣发泡,但其缺点是稳定性较差,所以,在与CaO量相匹配的基础上控制其加入量为5%~15%。
图3.1显示了CaF2作为助熔剂具有显著韵效果,可以明显的降低精炼渣中高熔点组分的熔化温度,这对于冶炼过程中减轻LF炉的负担、增加冶炼强度、缩短冶炼周期是有利的。
图3.1CaF2的二元系相图
4)、MgO
MgO为碱性氧化物,精炼渣中的MgO主要来源于渣料和耐火材料,从热力学角度看,MgO也能提供O2离子,其脱硫能力略低于CaO。
LF炉精炼渣中的MgO可降低SiO2的活度,提高CaO的活度,从而提高Ls;但MgO得不利因素是提高LF炉精炼渣的熔点,特别是MgO含量>8%后,使炉渣变粘;MgO含量达到10%后,使渣进入两相区。
目前国内外使用的。
LF炉精炼渣中一般人含有一定量的MgO,主要是为了减少包衬侵蚀,提高钢包寿命。
5)、渣中其它组元
在炉外精炼渣中,通常还含有FeO、MnO、P205等组元。
(FeO+MnO)含量的多少标志着炉渣氧化性的大小,因此渣中w(FeO+MnO)对炉外精炼过程渣——钢间硫的分配比有重要影响。
因为炉渣中∑(FeO+MnO)含量的减少,促使与之平衡钢水氧活度降低,从而有利于脱硫反应的进行。
目前,精炼终点一般将渣中的(FeO十MnO)含量控制在1%以下,国外冶炼超低硫钢时基本都控制在0.5%以下。
文献认为要使终点硫含量小于10-5,则渣中(FeO+MnO)含量应不大于0.6%.进行生产试验。
在这次的试验中,他们考虑了炉渣的氧化性对脱硫率的影响。
(FeO+MnO)含量对实际硫分配比(Ls)的影想如图3.2所示。
图3.2渣中(FeO+MnO)含量对Ls′的影响
图中可见,在w(FeO+MnO)<2.O~2.5%时,实际硫分配比随其含量降低而升高,几乎呈线性增加。
其原因是渣中(FeO+MnO)含量减少,促使钢中氧活度降低,从而使Ls提高。
因此应尽量降低渣中(FeO+MnO)含量,其最佳值为w(FeO+MnO)<2.0%,最大不超过2.5%。
在研究中指出:
作为还原尺度的渣中(Feo+MnO)对硫的全配比成反比关系,即随着渣中(Feo+MnO)含量的提高,硫的分配比降低,对炉渣脱硫不利,见图3.3
图3.3渣中(Feo+MnO)含量与硫分配比的关系
3.2LF炉精炼渣系的选择
优化LF炉渣料渣系可实现对钢水质量进一步的提高,满足用户对焊丝钢的更高要求。
根据产品结构和实际情况,秉承既往精炼熔渣为三元渣系(CaO-Si02-A1203)不变,但渣中不同组元对LF炉精炼效果的影响明显,因此,对渣料、渣系进行调整优化。
应选CaO-Al203-SiO2系三元图的低熔点位置的渣系。
基础渣最重要的因素是控制碱度,在精炼中更好的脱氧、脱硫,通常精炼渣分为高碱度渣和低碱度渣。
对脱硫而言,应造高碱度、低氧化性、流动性良好的渣子;对控制夹杂物而言,应造低碱度、低氧化性、流动性良好的渣子。
因此,对渣料、渣系进行调整优化。
图3.4CaO-Al203-SiO2系相图
根据研究结果,选定其优化后精炼渣成分如下:
碱度3.0~3.5、(CaO)48-55%、(SiO2)14-18%、(Al2O3)15%~18%、(FeO)<1%。
即CaO和Al2O3基本位于CaO-Al203-SiO2相图中的3CaO·Al203和12CaO·7Al203之间。
3.3优化后主要材料及理化指标
对于精炼前的不完全脱氧钢,活性石灰和萤石在钢水到精炼过程中铝合金化之后加人。
根据精炼钢水量、下渣量和预融渣加入量、出钢硫含量的多少加人。
需加人活性石灰量为0.9-1.4㎏/T钢,加人萤石量为活性石灰的10%-30%,两者同时加人。
优化后物料加入数量及顺序:
出钢预融渣加入200㎏.精炼物料加入:
出钢S≤0.023﹪时,白灰1300㎏,铝矾土250㎏,萤石300㎏,埋弧渣100㎏。
出钢S在0.024—0.028﹪时,白灰1600㎏,铝矾土250㎏,萤石400㎏,埋弧渣100㎏。
出钢S≥0.028﹪时,白灰1800㎏,铝矾土250㎏,萤石500㎏,埋弧渣100㎏。
对于只升温的炉次,每升温一次应多加一次活性石灰及萤石。
加活性石灰和萤石吸附钢中夹杂物。
只有流动性好的精炼渣,才能吸附钢中的夹杂物溶解在其中,达到吸附夹杂物的目的。
由于精炼过程加人一定活性石灰和萤石,改变了渣的组成,不仅提高了顶渣碱度改善了顶渣流动性,而且新渣系组成有利于提高渣中硫容,因此有利于脱硫。
精炼时添加一定量的活性石灰和萤石,可以提高精炼钢水渣系的碱度,降低了熔渣的熔点,改善了熔渣的流动性,对钢水有一定的脱S作用,同时降低钢中夹杂物总量,提高了精炼钢水的质量;钢水精炼时添加一定量的活性石灰和萤石,不仅满足了生产工艺要求,还避免了由于过去脱硫站故障不能脱硫导致停机事故,转炉脱硫压力大导致的炉况、钢水终点恶化等现象,保证生产顺行。
表3.1所用主要材料及理化指标
主要材料
优化前
优化后
造渣剂
合成渣、少量转炉石灰
预融渣、清洁小块石灰
脱氧剂
Al造渣剂
Al造渣剂、Si-Fe粉
化渣剂
铝矾土、普通萤石
铝矾土、优质萤石
其他
埋弧渣
埋弧渣
表3.2合成渣成分
CaO+MgO%
SiO2%
Al2O3%
CaF2%
S%
水分%
熔点℃
62-69
<5
5-8
5-15
≤0.05
≤0.5
〈1500
表3.3清洁小块石灰
CaO+MgO%
SiO2%
P%
S%
活性度ml
粒度mm
≥90
<2
≤0.05
≤0.05
≥310
5-15
表3.4预熔精炼渣
CaO%
SiO2%
Al2O3%
MgO%
其它
熔点℃
48-52
≤5
38-42
6
2
1350
表3.5优质萤石
牌号
化学成分%
CaF2
SiO2
S
P
FL-90
≥90
≤9.3
≤0.1
≤0.06
结论
1与宣钢现用精炼渣相比,新渣系的显著特点是:
渣的碱度显著提高,以改善LF炉的精炼效果;渣中MgO含量合适,能够有效提高钢包寿命;
5.2LF生产结果表明:
所设计的精炼渣的电弧开始埋弧时间都小于3min,发泡埋弧效果较好,且性能稳定;
5.3通过转炉出钢改加预融渣,使钢水在脱氧脱硫预成基础渣方面减轻了LF炉压力,对快速造白渣,保软吹都有利;
5.4替代渣系的脱硫率有了近10个百分点的提高,减轻了转炉的控硫压力,保证了钢质量,提高了命中率;
5.5取消使用合成渣后,精炼渣量减少,精炼成本降低,效益可观;
5.6利用三个月时间,将LF炉精炼的所有品种钢渣系进行了优化,并使其标准化。
既全面提升了精炼水平,又创造了价值。
参考文献