微电机转子冲片模具设计.docx
《微电机转子冲片模具设计.docx》由会员分享,可在线阅读,更多相关《微电机转子冲片模具设计.docx(44页珍藏版)》请在冰豆网上搜索。
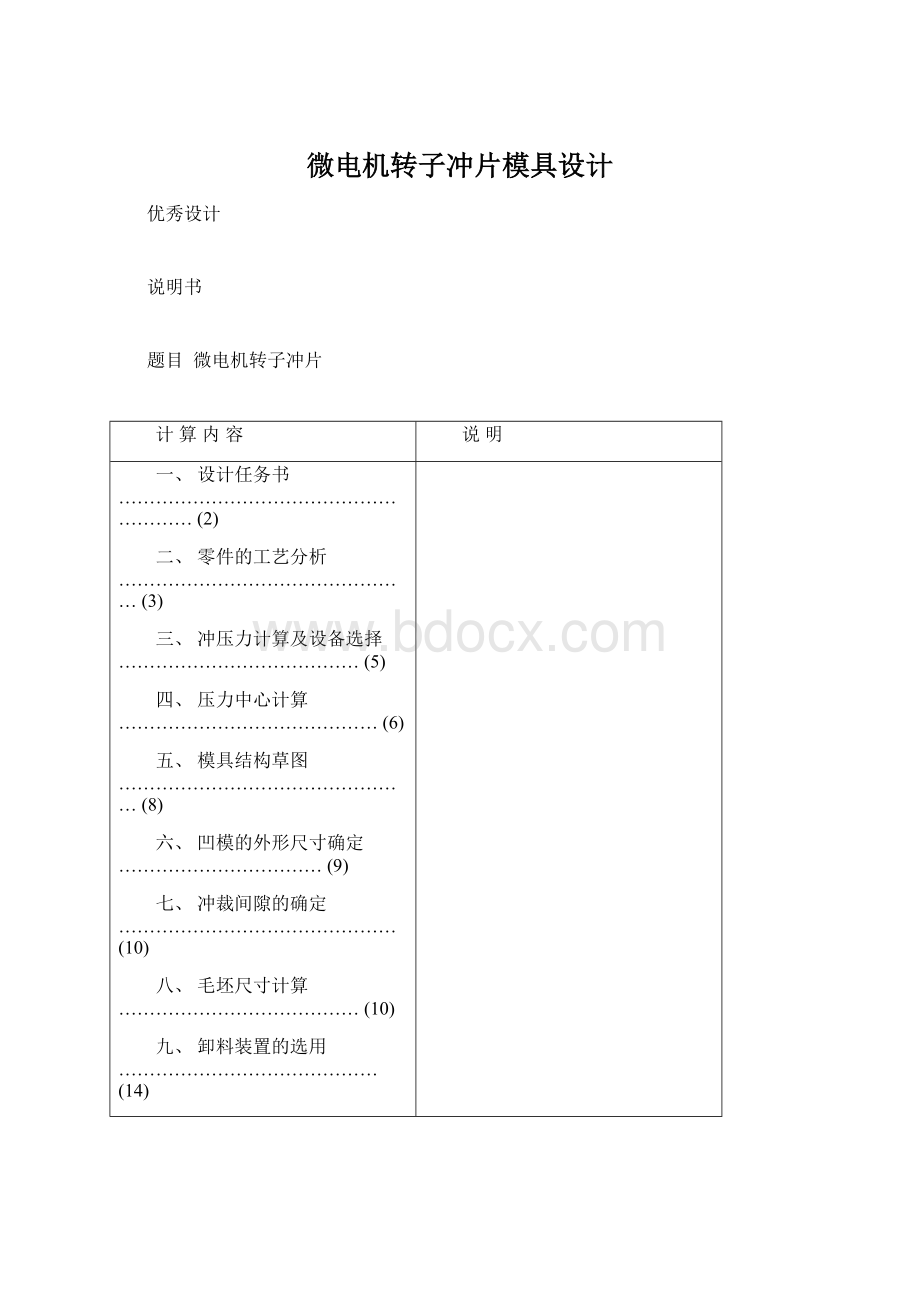
微电机转子冲片模具设计
优秀设计
说明书
题目微电机转子冲片
计算内容
说明
一、设计任务书…………………………………………………
(2)
二、零件的工艺分析…………………………………………(3)
三、冲压力计算及设备选择…………………………………(5)
四、压力中心计算……………………………………(6)
五、模具结构草图…………………………………………(8)
六、凹模的外形尺寸确定……………………………(9)
七、冲裁间隙的确定………………………………………(10)
八、毛坯尺寸计算…………………………………(10)
九、卸料装置的选用……………………………………(14)
一十、材料利用率的计算………………………………………(15)
十一、模具零件设计…………………………………………(16)
十二、设备校核 ……………………………………………(29)
十三、总结…………………………………………………(31)
十四、参考资料……………………………………………(32)
共33页第1页
计算内容
说明
第一章设计任务书
毕业设计(论文)内容及要求:
一、设计内容:
1、绘制产品零件图。
2、绘制模具装配图。
3、绘制整套模具零件图。
4、编写设计说明书。
二、生产纲领:
大批量生产。
三、设计要求:
1、模具结构设计合理,工艺性好。
设计计算正确,参数选用合理。
2、模具绘图布局合理,视图完整、清晰,各项内容符合规范。
3、模具装配图必须采用CAD绘制并打印。
4、绘制全套模具零件图,无后续加工的标准件除外。
5、设计说明书内容完整,分析透彻,语言流畅,参考资料应注明出处。
数字在10000~15000之间。
6、图纸:
装配图一份(零号纸)、全套零件图(不需要后续加工的标准件除外),总量在2张零号纸以上。
7、图纸和说明书打印并交电子档案,资料收集后要刻录存档。
共33页第2页
计算内容
说明
第二章零件的工艺性分析
零件图如下所示:
零件图
1、形状:
微电机转子冲片由中心孔Φ3.238mm、周围由12个冲槽一个R0.5mm的圆弧组成,而其零件总大小为Φ15.98mm,厚度为0.2mm,因此知道其零件较为复杂。
2、尺寸:
该零件尺寸最大直径为Φ15.98mm,而其零件上的各孔、各槽的尺寸小,因此看其尺寸而言,尺寸精度要求高。
所以按要求取其精度等级为IT9级。
3、冲孔、冲槽时工艺:
零件图上中心孔直径为Φ3.238mm,考虑到凸模强度限制,孔的尺寸不宜过小,其数值与孔的形状、材料的机械性能、材料的厚度等有关。
冲槽时,两个孔与孔之间的距离受模具强度和冲裁件质量的限制,其值不能过小,宜取a≥2t。
而零件图上的冲槽之间距离为11.05mm,较合适其强度和质量要求。
4、表面质量:
共33页第3页
计算内容
说明
做为微电机转子冲片,其平面度、同轴度要求高;从零件上所注的公差,则其质量要求高。
5、材料性能:
本零件所给的材料为Ni50坡莫合金,其硬度很高,近似于高碳钢。
则高碳钢的抗拉强度在300~600Mpa之间。
6、制定冲压工艺方案:
由零件图及零件图中的工艺要求,制定冲压工艺方案如下:
本零件的冲压方案有一下几种:
(1)、本零件可以设计为一套复合模,即冲孔——冲槽——落料复合模。
(2)、本零件可以设计为一套连续模,即第一工位为冲中心孔和两个导正孔;
第二工位为冲槽工位;第三工位为空工位;第四工位为落料工位;第五工位为空工位。
在依据其零件工艺要求、材料的利用率以及模架的设计方案和加工要求而选用连续模。
同时根据其精度分析如下:
(1)、本零件采用高精度的滚动导向连续冲裁,且模架为四导柱模架。
(2)、本零件采用条料送进。
(3)、模具中的定位采用侧刃定距。
共33页第4页
计算内容
说明
第三章冲压力计算及设备选择
1、冲裁力的计算:
各工位的主要工序是冲裁,利用式(1——3)计算冲裁力。
Ni50坡莫合金的抗剪强度θb=500Mpa。
第一工位:
F1=L1*t*θb
=[3.14*(3.238/2)²+3.14*4²+8+2+17.98+7.5+(0.5²+0.5²)½]x0.2x500
=94.457*0.2*500
=9445.71N
第二工位:
F2=L2*t*θb
=12*{[3.14*(1.25/2)*(1.25/2)]/2+[3.14*(2.45/2)*(2.45/2)]/2
+0.47*2+0.67+2*[(12.92-8.3)/2]}*0.2*0.5
=12*(0.98+2.36+0.94+0.67+4.62)*0.2*500
=11484N
第三工位:
空工位。
第四工位:
F4=L4*t*θb
=[3.14*(15.98/2)*(15.98/2)-1+0.5*0.5*3.14-12*0.67]*0.2*500
=(200.46-1+0.79-8.04)*0.2*500
=19220N
第五工位:
空工位
因此总冲裁力为:
F总=F1+F2+F3+F4+F5
=40149.71068N
2、卸料力的计算:
Fθ1=K1*F
查表1——7卸料力系数K1=2.3~2.5
则Fθ1=K1*F
=2.5*40149.7068
=100374.2767N
参见《冲压工艺与模具设计》
1——7
1——11
P25、26
共33页第5页
计算内容
说明
所以总冲压力:
F0=Fθ1+F总
=40149.7+100374.28
=140523.9767N
3、设备的选择:
根据零件高精度的要求,以及其多工位的要求,同时根据计算所得选定压力机为开式双柱可倾压力机。
因F0=38195.795N,所以选定压力机为J23——10。
其压力机的主要规格如下:
型号J23——10
公称压力/KN100
滑块行程/mm45
滑块行程次数/(次/min)145
最大闭合高度/mm200
最大装模高度/mm145
连杆调节长度/mm35
模柄孔尺寸/mmΦ30x65
倾斜角30º
封闭高度调节量/mm50
滑块中心到床身距离/mm120
立柱间距离/mm180
工作台板厚度/mm50
工作台尺寸/mm(左右)360
工作台尺寸/mm(前后)240
工作台孔尺寸/mm(左右)180
工作台孔尺寸/mm(前后)90
工作台孔尺寸/mm(直径)130
第四章压力中心计算
1、排样图如下:
参考
《冲压设计手册》
压力机的选择
共33页第6页
计算内容
说明
排样图
2、材料搭边值:
查表2——10,取其最小工艺搭边值:
a=1.8mma1=2.0mm
3、计算步距:
S0=D+a=15.98+1.8=17.78mm
4、决定定距方式:
由于工位数较多,从节省材料考虑决定采用双侧刃定距,即:
采用B型侧刃,其侧刃长度L=17.78+(0.05~0.1)=17.83mm;宽度b=8mm
5、确定首件定位线:
首件定位线是指条料端头在第一工位应处的位置线。
在冲孔工位确定首件
位线,主要考虑条料送至落料工位时应有足够的搭边。
在排样草图上容易做到这一点,如上图。
确定初始定位线是为了确定入端侧刃型孔的位置。
显然,入端侧刃型孔与冲中心孔、导正孔的中心线对齐。
6、计算压力中心:
为了保证压力机和模具平稳的工作,必须使冲模的压力中心一压力机滑块中心线相重合,对于使用模柄的中小型模具就是要使其压力中心与模柄轴线相重合,否则将使冲模和压力机滑块承受侧向力,引起凸、凹模间隙不均匀和导向零件加速磨损,甚至还会引起压力机导轨的磨损、影响压力机精度。
对与工件外行尺寸大、形状复杂、多凸模的冲裁模和级进模,正确确定其压力中心就显得更为重要。
参考《
冷冲压工艺与模具设计》
P56
共33页第7页
计算内容
说明
根据以上的排样图计算如下:
L1=8.23mmX1=0mmY1=0mm
L2=14.13mmX2=8.99mmY2=0mm
L3=126.396mmX3=17.98mmY3=0mm
L4=191.8125mmX4=17.98x3=53.94mmY4=0mm
L5=17.98mmX5=0mmY5=0mm
L6=2mmX6=8.99mmY6=10.99mm
X=(X1*L1+X2*L2+X3*L3+X4*L4+X5*L5+X6*L6+)/(L1+L2+L3+L4+L5+L6)
=(0*8.23+8.99*14.13+126.396*17.98+191.8125*53.94+0*17.98+2*8.99)
/(8.23+14.13+126.396+191.8125+17.98+2)
=35.40155
Y=(YI*L1+Y2*L2+Y3*L3+Y4*L4+Y5*L5+Y6*L6)/(L1+L2+L3+L4+L5+L6)
=(0*8.23+0*14.13+126.396*0+191.8125*0+17.98*0+2*8.99)
/(8.23+14.13+126.396+191.8125+17.98+2)
=0.0498
经计算得压力中心的坐标为:
X0=35.40155Y0=0.0498。
可取X0=35Y0=2,作为设计模具的参数。
第五章模具结构草图
结构草图如下:
参考《
冷冲压工艺与模具设计》
P87
2——39
2——40
共33页第8页
计算内容
说明
第六章凹模的外形尺寸确定
1、如上排样图所示,从型孔边界画一矩形lxb初定为凹模有效面积。
凹模有效面积矩形的对称中心应与压力中心重合,以便使模柄的中心线通过压力中心。
但压力中心对于矩形的宽度b处于对称位置,因此应将矩形的长度增大为l’,使压力中心对于l’处于对称位置,即压力中心到矩形左边的距离为实际凹模有效面积矩形长度的一半。
则修正后的凹模有效面积矩形长度l’与宽度b分别为:
L=2x(3x17.78+0.5)=107.68≈108mm
B=2x(1.5+7.99+8+4+2)=46.98≈47mm
参考《
冷冲压工艺与模具设计》
P135
共33页第9页
计算内容
说明
2、估算凹模的外行尺寸:
如上排样图所示,从凹模有效面积矩形l’xb向四周扩大30~40mm,即为凹模外行尺寸LxB的尺寸范围:
L=108+2x(30~40)mm=168~188mm
B=47+2x(30~40)mm=107~127mm
选用标准凹模:
查表14——6得:
LxB=165x200
厚度的选择:
查表14——5得:
h=22~28mm
根据要求厚度选择如下:
h=25mm
第七章冲裁间隙的确定
根据零件的材料和厚度查表1——3确定零件的冲裁间隙:
材料厚度t硬钢Wc(0.5%~0.6%)
Z/tZminZ/tZmax
0.27%0.0149%0.018
第八章毛坯尺寸
1、条料宽度:
如下图所示:
参考《
冷冲压工艺与模具设计》
P13
表1——3
共33页第10页
计算内容
说明
B=(D+2a1+nb1+2*2+1*1.5)0-Δ
=[15.98+(2*2)+(1*1.5)]0-0.05
=220-0.05
导料板的入端导料尺寸:
B1=B+C1
查表2——13最小双面导料间隙C1:
C1=0.1
即:
B1=21.48+0.1=21.58mm
出端导料尺寸:
B2=D+2a1+C2+2*2
查表2——14出端导料间隙C2:
C2=0.1
即;B2=15.98+(2x2)+0.1=20.08mm
参考《
冷冲压工艺与模具设计》
P136
共33页第11页
计算内容
说明
2、主要刃口尺寸计算:
从排样图看,不仅有冲孔、落料、冲槽,而且还有侧刃冲裁。
如果按基本加工制度处理刃口尺寸,即冲孔以凸模为基准件,落料以凹模为基准件,则凹模即作配作件又作基准件。
不如凹模只作配作件,可一次线切割加工出全部凹模型孔,容易保证所有冲裁间隙都比较均匀。
这样只需计算刃口尺寸,凹模型孔按要求的冲裁间隙配作。
凸模刃口尺寸共有五种类型,分别计算如下:
(1)、冲孔凸模刃口尺寸:
各冲孔凸模的刃口尺寸均属于磨损后减小的尺寸,应按式(2——34)计算,即:
Bb=(bmin+xΔ)0-Δ/4查公差为IT10级,则Δ=+0.013mm,冲孔尺寸为:
b1=Φ3.2380+0.013mm
则按式(2——34)计算冲孔凸模刃口尺寸分别为:
B1=[3.238+(1x0.013)]0-0.013/4
=3.2510-0.003mm
(2)冲槽凸模刃口尺寸:
各冲槽凸模的刃口尺寸属于磨损后减小的尺寸,应按式(2——34)计算,即:
Bb=(bmin+xΔ)0-Δ/4。
零件图中所注的公差为IT10级,各槽的尺寸为:
b1=0.670+0.007mm
b2=2.450+0.06mm
b3=1.250+0.06mm
b4=8.820+0.022mm
参考《
冷冲压工艺与模具设计》
P136——137
共33页第12页
计算内容
说明
则按式(2——34)计算冲槽凸模刃口尺寸分别为:
B1=[0.67+(1x0.007)]0-0.007/4
=0.6770-0.002mm
B2=[2.45+(1x0.06)]0-0.06/4
=2.510-0.015mm
B3=[8.82+(1x0.022)]0-0.022/4
=8.8420-0.005mm
(3)、落料凸模尺寸:
落料凸模尺寸均属于磨损后增大的尺寸,现以凹模为配作件,需计算落料凸模刃口尺寸,应按式(2——36)进行计算,即:
Bp=(amax-xΔ+Δ/4-Zmin)0-Δ/4。
工件落料尺寸为:
b1=Φ15.980-0.012mm
尺寸15.98的公差为IT10级,取x=1;按板料厚度0.2mm,查表1——3其最小冲裁间隙Zmin=0.014mm。
则按式(2——36)计算落料凸模刃口尺寸为:
B1=(15.98-1x0.012+0.012/4-0.014)0-0.012/4
=15.9570-0.003mm
(4)、导正孔凸模尺寸:
导正孔凸模尺寸均属于磨损后减小的尺寸,应按式(2——34)计算,即:
Bb=(bmin+xΔ)0-Δ/4,其公差要求为IT10级,取x=1。
冲孔尺寸为:
b1=30+0.058mm
参考《
冷冲压工艺与模具设计》
P136——137
共33页第13页
计算内容
说明
则按式(2——34)计算导正凸模刃口尺寸为:
B1=[3+(1x0.058)]0-0.048/4
=3.0480-0.012mm
(5)、侧刃尺寸:
侧刃工作尺寸应与步距尺寸协调,一般两者取相同的尺寸,当考虑草测刃冲切后在条料台阶处产生的毛刺影响送料精度时,可将侧刃工作尺寸增大0.02~0.05mm。
本模具采用了B型侧刃,冲裁后产生的毛刺对送料步距的影响很小。
因此侧刃工作尺寸可与步距相同。
其公差按模具国标规定为0.02mm,并取负偏差,则侧刃工作尺寸及公差为:
S=17.780-0.02
侧刃的其余尺寸可参照标准侧刃确定。
凹模侧刃型孔则按侧刃实际尺寸配作。
可见,以凹模为配作件是比较合理的。
第九章卸料装置的选用
卸料装置的功用是在一次冲裁结束之后,将条料或工序件与落料凸模或冲孔凸模脱离,以便进行下一次冲裁。
因本模具零件精度要求较高,同时为防止零件的变形。
因此采用弹性卸料,而因零件精度高,在采用弹性卸料的同时要采用导柱导向。
所以初步选用橡胶块和卸料板。
选用橡胶块的计算如下:
其材料厚度t为0.2mm,经计算卸料力Fx为1644.8N,选用卸料橡胶块,其计算过程如下:
1)、假设考虑模具结构,决定用4个厚壁筒形的聚氨脂弹性体。
共33页第14页
计算内容
说明
2)、计算每个弹性体的预压力Fy:
Fy=1644.8N/4=411.2N
3)、考虑橡胶块的工作压缩量较小,取预压缩率εy=10%,并由表2——27查得单位压力Fq=1.1Mpa。
4)、按式(2——49)计算弹性体的截面面积A:
A=Fy/Fq=411.2/1.1=373.8mm²
5)、如果选用直径为8mm的卸料螺钉,选取弹性体穿卸料螺钉孔的直径
d=Φ8.5mm。
则弹性体的外径D可按下式求得:
π(D²-d²)/4=A
则D=(4A/π+d²)1/2
=(4x373.8/π+8.5²)1/2
=22.8mm
验算外径D:
Fy=AxFq
=[π/4(22.8²-8.5²)x1.1]
=355.3N
因此取D=23mm
6)、橡胶块高度的确定:
H=hg/εj-εy
=0.2+1/35%-10%
=15mm
所以经计算选取卸料橡胶块为:
橡胶块的高度为H=15mm
总计块数为n=8
橡胶块的材料为邵氏70~80A的聚氨脂橡胶
第十章材料利用率的计算
一段条料能冲出的工件的重量与这段条料重量之比的百分数称为材料利用率。
由于板料冲裁时板厚是一定的,所以材料利用率可用面积之比,即一段条料的有效面积与这段条料的面积之比,来代替重量之比。
参考《
冷冲压工艺与模具设计》
P105——107
共33页第15页
计算内容
说明
同一工件,排样不同时,材料利用率也会不同,材料利用率越高者越省料。
因此,材料利用率是判断排样是否经济的重要参数。
但材料利用率并不是选择排样的唯一标准。
一般按下述原则选择:
对于铜板等较贵重材料,特别是在生产量较大时,应尽量选择材料利用率较高的排样。
如果某种排样不其它排样的材料利用率提高不到5%,且使模具复杂化时,那么这种排样是不可取的。
而在生产量小时,应尽可能选择比较简单的排样,以便模具容易制造。
按条料计算材料利用率来计算:
η=n*A/L*B
A=π*R²
=3.14*7.99²
=200.458mm
即:
η=4*200.458/71.92*22
=50.17%
式中说明:
n——一根条料能冲出的工件数;
L——条料的长度(mm);
A——一个工件的实际面积(mm²)
第十一章模具零件设计
1、工作零件设计:
1)、工作凸、凹模设计:
凸模设计的三原则:
为了保证凸模能够正常工作,设计任何结构形式的凸模都必须满足如下三原则:
(1)、精确定位
凸模安装到固定板上以后,在工作过程中其轴线或母线不允许发生任何方向的位移,否则将造成冲裁间隙不均匀,降低模具寿命,严重时可造成啃模。
(2)、防止拔出
回程时,卸料力对凸模产生拉伸作用。
凸模的结构应能防止凸模从固定板中拔出来。
参考《
冷冲压工艺与模具设计》
P64
共33页第16页
计算内容
说明
(3)、防止转动
对于工作段截面为圆形的凸模,当然不存在防转问题。
可是对于一些截面比较简单的凸模,为了使凸模固定板上安装凸模的型孔加工容易,常常将凸模固定段简化为圆形。
这时就必须保证凸模在工作过程中不发生转动,否则将啃模。
工作凸、凹模的设计包括冲导正孔凸模、中心孔凸模、冲槽凸模、落料凸模及侧刃凸模。
(1)、导正孔凸模的设计及加工:
根据冲裁时凸模所受的力,为满足其需要,设计结构形式如下:
根据以前所取,各凸、凹模都以凸模为基准,凹模为配作件,则凸模的尺寸计算如下:
根据式(2——34)计算,即:
Bp=(bmin+xΔ)0-Δ/4
凸模根据其强度要求,选用Cr12MoV,而热处理后的硬度为58~60HRC
凸模的安装与固定方法如下:
因所设计的凸模为圆凸模,所以其固定方式为凸模固定板上加工出台阶来固定。
(示图如下:
)
参考《
冷冲压工艺与模具设计》
P64
共33页第17页
计算内容
说明
凸模与固定板的配合为过渡配合。
凸模的装配方法为压入法,其特点为连接牢固可靠,对配合孔的精度要求高。
加工成本高,因以凹模为配作件,所以凹模以凸模为基准配作,保证单面间隙为0.014mm~0.018mm。
其结构图如下:
其加工方法采用钻、铰加工(精度高时精孔钻加工)。
凹模的固定采用销钉、螺钉紧固方法。
凸模的加工方法:
冲压模具的凸模都需进行淬火等热处理工艺,获得高硬度和高耐磨性,则可采取以下加工方案:
(1)、粗车(留磨削余量)——热处理——磨削
(2)、粗车——热处理——精车、抛光
(3)、精车成行——热处理——抛光
综合各种实际因素,则采用方案为
(1)。
凸模长度的确定:
设计标准模具时,当选定了典型组合以后,凸模的长度就确定了。
设计非标准模具时,凸模的长度一般根据结构上的需要,并考虑磨损量和安全因素来确定。
因本模具采用的是标准模具,因此凸模的长度就可以通过公式来求,具体计算如下:
弹性卸料方式的凸模长度按下式计算:
(2——17)
L=h1+h4+h5-0.2
=15+8+15-0.2
=37.8mm
式中说明:
h1——凸模固定板厚度(mm)
h2——弹压卸料板厚度(mm)
参考《
冷冲压工艺与模具设计》
P70
2——17
共33页第18页
计算内容
说明
h5——预压状态下卸料橡皮厚度(mm),h5=(0.85~0.9)H,
H为自由状态下橡胶的皮厚。
公式中的0.2mm是凸模端面缩进卸料板的距离。
(2)、中心孔凸模设计:
根据冲裁时凸模所受的力,为满足其需要,设计结构形式如下:
根据以前所取,各凸、凹模都以凸模为基准,凹模为配作件,则凸模的尺寸计算如下:
根据式(2——34)计算,即:
Bp=(bmin+xΔ)0-Δ/4
凸模根据其强度要求,选用Cr12MoV,而热处理后的硬度为58~60HRC
凸模的安装与固定方法如下:
因所设计的凸模为圆凸模,所以其固定方式为凸模固定板上加工出台阶来固定。
(示图如下:
)
共33页第19页
计算内容
说明
凸模与固定板的配合为过渡配合。
凸模的装配方