注塑模具毕业设计.docx
《注塑模具毕业设计.docx》由会员分享,可在线阅读,更多相关《注塑模具毕业设计.docx(42页珍藏版)》请在冰豆网上搜索。
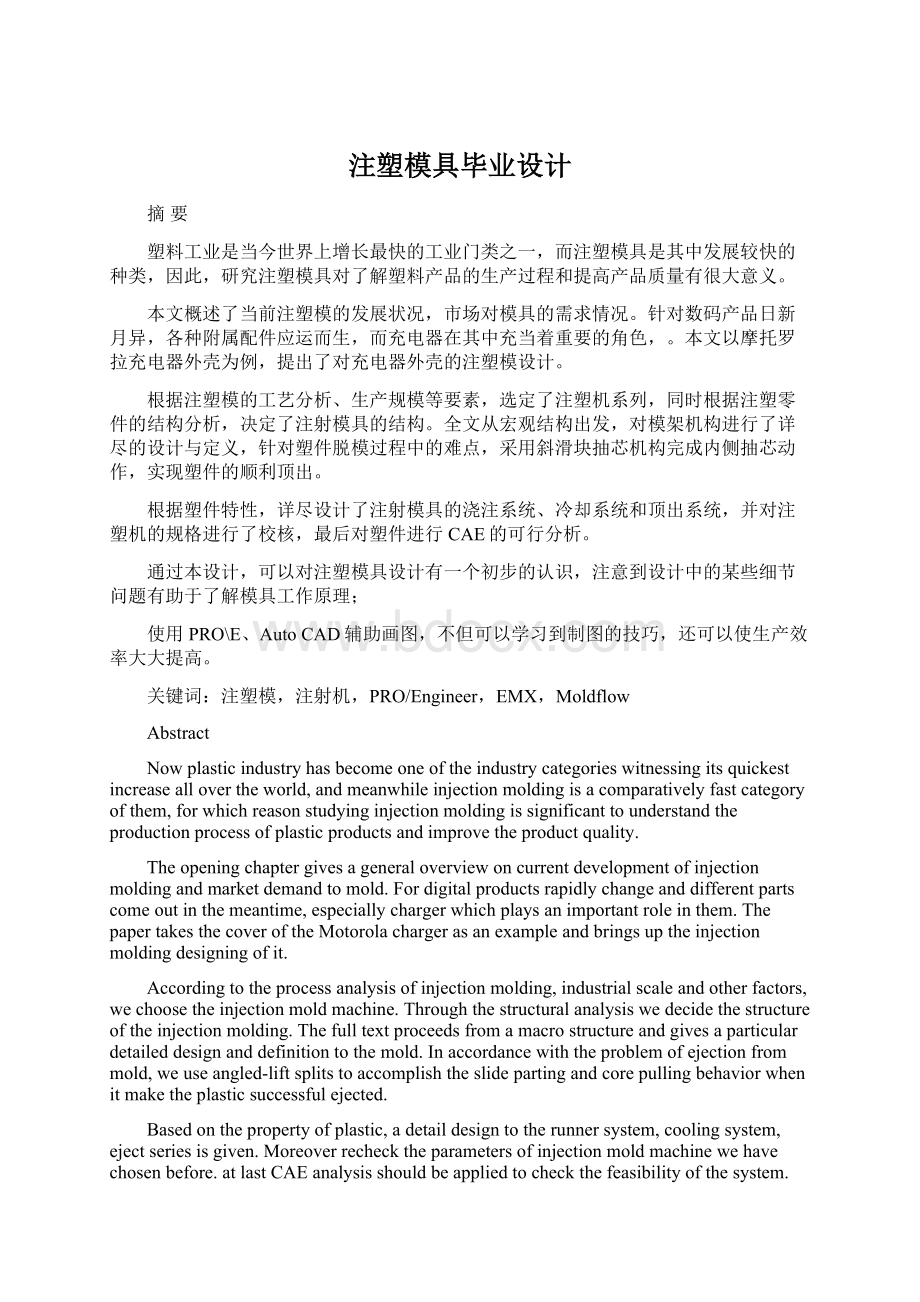
注塑模具毕业设计
摘要
塑料工业是当今世界上增长最快的工业门类之一,而注塑模具是其中发展较快的种类,因此,研究注塑模具对了解塑料产品的生产过程和提高产品质量有很大意义。
本文概述了当前注塑模的发展状况,市场对模具的需求情况。
针对数码产品日新月异,各种附属配件应运而生,而充电器在其中充当着重要的角色,。
本文以摩托罗拉充电器外壳为例,提出了对充电器外壳的注塑模设计。
根据注塑模的工艺分析、生产规模等要素,选定了注塑机系列,同时根据注塑零件的结构分析,决定了注射模具的结构。
全文从宏观结构出发,对模架机构进行了详尽的设计与定义,针对塑件脱模过程中的难点,采用斜滑块抽芯机构完成内侧抽芯动作,实现塑件的顺利顶出。
根据塑件特性,详尽设计了注射模具的浇注系统、冷却系统和顶出系统,并对注塑机的规格进行了校核,最后对塑件进行CAE的可行分析。
通过本设计,可以对注塑模具设计有一个初步的认识,注意到设计中的某些细节问题有助于了解模具工作原理;
使用PRO\E、AutoCAD辅助画图,不但可以学习到制图的技巧,还可以使生产效率大大提高。
关键词:
注塑模,注射机,PRO/Engineer,EMX,Moldflow
Abstract
Nowplasticindustryhasbecomeoneoftheindustrycategorieswitnessingitsquickestincreaseallovertheworld,andmeanwhileinjectionmoldingisacomparativelyfastcategoryofthem,forwhichreasonstudyinginjectionmoldingissignificanttounderstandtheproductionprocessofplasticproductsandimprovetheproductquality.
Theopeningchaptergivesageneraloverviewoncurrentdevelopmentofinjectionmoldingandmarketdemandtomold.Fordigitalproductsrapidlychangeanddifferentpartscomeoutinthemeantime,especiallychargerwhichplaysanimportantroleinthem.ThepapertakesthecoveroftheMotorolachargerasanexampleandbringsuptheinjectionmoldingdesigningofit.
Accordingtotheprocessanalysisofinjectionmolding,industrialscaleandotherfactors,wechoosetheinjectionmoldmachine.Throughthestructuralanalysiswedecidethestructureoftheinjectionmolding.Thefulltextproceedsfromamacrostructureandgivesaparticulardetaileddesignanddefinitiontothemold.Inaccordancewiththeproblemofejectionfrommold,weuseangled-liftsplitstoaccomplishtheslidepartingandcorepullingbehaviorwhenitmaketheplasticsuccessfulejected.
Basedonthepropertyofplastic,adetaildesigntotherunnersystem,coolingsystem,ejectseriesisgiven.Moreoverrechecktheparametersofinjectionmoldmachinewehavechosenbefore.atlastCAEanalysisshouldbeappliedtocheckthefeasibilityofthesystem.
Wecangetageneralideatotheinjectionmoldingdesignthroughthisdesignmission,what’smore,takenoticeofsomedetailsduringdesignhelptodeeplyunderstandthetheoryofmold.
UsingComputerAidedDesign(Pro\E,AutoCAD)cannotonlycatchtheskillofdrawing,butalsoraisetheproductionefficiency.
Keywords:
Injectionmolding,injectionmachine,Pro/Engineer,EMX,Moldflow
1绪论
1.1模具及模具工业的发展与现状
模具是生产工业产品的主要工艺装备。
模具工业是整个国民经济的基础工业。
为提高模具的质量、性能、精度和生产效率,缩短制造周期,其零部件多由标准零部件组成,因此模具本身属于标准化程度较高的产品。
采用模具生产零部件,具有生产效率高、质量好、成本低、节省能源和原材料等一系列优点,它已成为当代工业生产的重要手段和工艺发展方向。
现代工业产品的发展和技术水平的提高,很大程度取决于模具工业的发展水平。
在现代化工业生产中,60%~90%的工业产品需要使用模具加工,模具工业已成为工业发展的基础,许多新产品的开发和生产在很大程度上都依赖于模具生产,特别是汽车、轻工、电子、航空等行业尤为突出。
而作为制造业基础的机械行业,根据国际生产技术协会预测,21世纪机械制造工业零件粗加工的75%和精加工的50%都依靠模具完成。
因此模具已成为国民经济的重要基础工业[1]。
目前,世界模具市场供不应求。
近几年,世界模具市场总量一直为600~650亿美元左右,其中美国、日本、法国、瑞士等国每年出口模具约占本国模具的1/3.可见研究和发展模具技术,提高模具技术水平,对于促进国民经济的发展具有特别重要的意义。
在日本,模具被誉为“进入富裕社会的原动力”,在德国则冠以“金属加工中的帝王”,。
可以断言,随着现代工业生产的迅速发展,模具工业在国民经济发展过程中将会发挥越来越重要的作用[2]。
1.2塑料成型模具及其地位
所谓塑料模具,就是利用其本身特定密闭腔体去成型具有一定形状和尺寸的立体形状塑料制品的工业。
在模具工业中,随着塑料成型工业的发展,塑料模具已处于同冲压模具并驾齐驱的地位,在日本全国一万多家企业热衷,生产塑料模和生产冲压模的企业占40%。
在韩国的全国模具专业中,生产塑料模的占43.9%,新加坡的460家企业,60%生产塑料模。
在我国的香港、深圳、江浙等地,其模具工业主要是从事塑料模具的制造和塑料制品的生产。
1.3塑料成型技术的发展趋势
塑料模具占我国模具总量的比正逐年上升,发展潜力巨大。
塑料模具中为汽车和家电配套的大型注塑模具,为集成电路配套的塑封模,为电子信息产业和机械及包装配套的多层、多腔、多材质、多色精密注塑模,为新型建材及节水农业配套的塑料异型材挤出模及管路和喷头模具等,目前虽然已有相当技术基础并正在快速发展,但技术水平与国外仍有较大差距,总量也供不应求,每年进口几亿美元。
近年来,随着塑料工业的飞速发展和通用与工程塑料在强度和精度等方面的不断提高,塑料制品的应用范围也在不断扩大,如:
家用电器、仪器仪表,建筑器材,汽车工业、日用五金等众多领域,塑料制品所占的比例正迅猛增加。
一个设计合理的塑料件往往能代替多个传统金属件。
随着工业产量应用范围的不断扩大,工业产品和日用产品塑料化的趋势不断上升,对塑料制件在数量、质量、精度等方面也提出了越来越高的要求,并促进塑料成型技术不断向前发展。
1.4CAD/CAE在设计过程中的应用
Pro/ENGINEER3.0是美国PTC公司(ParametricTechnologyCorporation——参数技术公司)开发的大型CAD/CAM/CAE集成软件,是全方位的产品开发软件。
该软件集产品设计、装配、加工、钣金设计等功能于一体,其模块众多、内容丰富、功能强大,已广泛应用于电子、航天、汽车、家电和玩具等行业。
在充电器外壳模具设计过程中,主要应用Pro/ENGINEER3.0进行了模具型腔模块进行结构设计,包括分形面、型腔、浇注系统等方面的设计。
EMX(ExpertMoldbaseExtension)作为PTC的专用插件,是一个基于知识库的模架装配和细化工具,它增强了现有Pro/ENGINEER模具工具的功能。
专门为模具设计人员开发的这套工具,提供了快速创建和修改完整模具零部件的功能,能简化模具设计过程,提高生产效率[3]。
在充电器外壳模具设计过程中,应用EMX4.1进行了模架结构及标准零件设计。
MoldflowPlasticAdvisers是Moldflow公司开发的快速试模分析软件,可以对塑件和模具进行注塑分析和优化,能帮助设计人员在早期发现问题。
在充电器外壳模具设计过程中,应用MoldflowPlasticAdvisers模流分析,包括浇口位置、材料选择、熔接痕位置、困气、流动时间、压力和温度分布分析等。
AutoCAD是最常用的工程制图软件。
由Pro/ENGINEER产生的工程图纸不规范,所以后期需要导入AutoCAD2006进行完善。
塑料模具CAD技术是一种全新的设计技术,有助于提高产品及模具设计的质量和实现产品的最佳性能。
塑料模具CAD的工作主要在于理解注塑过程模拟的分析结果,判读数据并做出合适的变更设计抉择,熟悉CAD技术并有效地应用于模具设计也有赖于设计人员的素质和经验。
塑料模具CAD的难点在于建立丰富的材料性能数据库,以及模具零件的标准化。
燕秀工具箱V2.3为cad外挂软件,它集成了各大模具标准零件生产厂家的标准零件库,如龙记(LKM)、明利(MINGLEE)、环胜(EVER)等,大大提高设计的效率及实用性。
1.5论文构成及研究内容
本次毕业设计的注塑模主要从塑料的性能、产品的使用性能和要求出发,分为几个方面的设计,重点阐述了材料性能、模具结构分析及工作原理以及成型分析、理论计算几个方面,同时运用分析软件对注塑过程进行了CAE分析
该塑件结构比较简单,精度要求低,运用常用的拉杆、顶杆、通过充模、保压、开模至推出塑件。
具体过程,详见以后说明书内容分析和计算。
本设计过程是根据《塑料成型工艺与模具设计》上的相关工艺编写的。
本说明书的内容包括:
目录、课程设计指导书、课程设计说明书、参考文献等。
编写本说明书时,力求符合设计步骤,详细说明了塑料注射模具设计方法,以及各种参数的具体计算方法,如塑件的成型工艺、塑料脱模机构的设计。
本说明书在编写过程中,得到老师和同学的大力支持和热情帮助,在此谨表谢意。
由于本人设计水平有限,在设计过程中难免有错误之处,敬请各位老师批评指正。
2模具的结构设计
2.1塑件工艺分析
(1)塑件形状与尺寸
如图2.1、图2.2分别为充电器外壳的三维立体图和二维工程图。
注塑成型后,塑件表面须经过磨砂处理,所以其粗糙度不做明确要求。
塑件内侧有一凸台螺纹孔。
在注塑成型设计时,可以看作是一个普通凸台孔,该凸台孔可以通过螺纹配合形成螺纹孔。
图2.1塑件三维图
图2.2塑件二维图
(2)塑件的精度
该产品形状相当于挖壳后的矩形,大体尺寸为65×40,表面精度与粗糙度要求不高,所以由表1可得,ABS材料精度为5级,对应的尺寸公差为0.46(表2)。
塑件注塑后须经过表面磨砂处理,使得产品手感好,使用过后不留指纹,外观显得稳重而又耐用。
表2.1塑件精度推荐值
类别
塑料名称
高精度
一般精度
低精度
Ⅰ
聚苯乙烯
ABS
聚甲基丙烯酸甲酯
聚砜
聚碳酸酯
3
4
5
Ⅱ
聚酰胺6,66,610,9,1010
氯化聚醚
聚氯乙烯
4
5
6
Ⅲ
聚甲醛
聚丙烯
高密度聚乙烯
5
6
7
Ⅴ
聚氯乙烯(软)
低密度聚乙烯
6
7
8
表2.2常见材料的公差等级推荐值(SJ1372—1978)
公称尺寸
精度等级
1
2
3
4
5
6
7
8
公差数值
-3
0.04
0.06
0.08
0.12
0.16
0.24
0.32
0.48
>3-6
0.05
0.07
0.08
0.14
0.18
0.28
0.36
0.56
6-10
0.06
0.08
0.10
0.16
0.20
0.32
0.40
0.64
>10-14
0.07
0.09
0.12
0.18
0.22
0.36
0.44
0.72
>14-18
0.08
0.10
0.12
0.20
0.26
0.40
0.48
0.80
>18-24
0.09
0.11
0.14
0.22
0.28
0.44
0.56
0.88
>24-30
0.10
0.12
0.16
0.24
0.32
0.48
0.64
0.96
>30-40
0.11
0.13
0.18
0.26
0.36
0.52
0.75
1.0
>40-50
0.12
0.14
0.20
0.28
0.40
0.56
0.80
1.2
>50-65
0.13
0.16
0.22
0.32
0.46
0.64
0.92
1.4
>65-85
0.14
0.19
0.26
0.38
0.52
0.76
1.0
1.6
(3)材料特性
ABS树脂为微黄色或者白色不透明颗粒,无毒无味;是丙烯腈―丁二烯―苯乙烯共聚物,。
丙烯腈使聚合物耐油、耐热、耐化学腐蚀;丁二烯使聚合物具有卓越的柔性、韧性;苯乙烯赋予聚合物良好的刚性和加工流动性。
因此ABS具有突出的力学性能,和良好的综合性能。
ABS的缺点是可燃、耐热性低,热变形温度一般在93°C左右,连续工作温度为70°C左右,只能在不高的温度下使用。
耐候性差,在紫外线作用下容易变脆,加入炭黑、紫外线吸收剂或涂以不透明涂料可提高其耐候性。
ABS塑料广泛应用于制造汽车内饰件、电器外壳,手机、电话机壳、等,依然可以用于生产板材、管材等。
(4)塑件生产批量
从产品来源来看,本品在常温中使用,精度要求不高,一般只要满足要求,尽可能取较低的精度,所以从经济利益上看来尽可能采用一模多腔。
该产品大批量生产,故设计的模具要有较高的注塑效率,可采用侧浇口自动脱模结构,由于塑件较小,模具可采用一模四腔结构。
(5)塑件工艺参数
ABS塑料的其余参数如下:
收缩率(/%):
0.4~0.7
密度(/g·㎝-3):
1.02~1.16
注射机:
螺杆式
螺杆转速(/r·min-1):
30~60
料筒一区(/°C):
150~170
料筒一区(/°C):
180~190
料筒一区(/°C):
200~210
喷嘴(/°C):
180~190
模具(/°C):
50~70
注塑(/MPa):
60~100
保压(/MPa):
40~60
注塑时间(/s):
2~5
保压时间(/s):
5~10
冷却时间/(s):
5~15
周期(/s):
15~30
2.2凹凸模零件工作尺寸的计算
2.2.1凹凸模的结构设计
1、凹凸模的配合
凹模结构有整体式凹模、整体嵌入式凹模、局部镶拼式凹模、四壁拼合式凹模、螺纹型环。
本塑件采用整体嵌入式凹模。
将稍大于塑件外形的较好的材料制成凹模,再将此凹模嵌入模板中固定。
其优点是“好钢用在刀刃上”。
既保证了凹模使用寿命,又不浪费价格昂贵的材料,并且凹模损坏后,维修、更换方便。
整体嵌入式凹模与模板的采用H7/m6的配合方式[4]。
整体式凸模浪费材料且切削加工量大,在当今的模具结构中几乎没有这种结构,主要是整体嵌入式凸模和镶拼组合式凸模。
本塑件采用整体嵌入式凸模。
整体嵌入式凹模与模板采用m6/H7配合方式。
2、凹凸模的精度
成型零件的工作尺寸是指凹模和凸模直接构成塑件的尺寸。
凹凸模工作尺寸的精度直接影响塑件的精度。
影响工作尺寸的因素如下:
(1)塑件收缩率的影响
由于塑料热胀冷缩的原因,成型冷却后的塑件尺寸小于模具型腔的尺寸。
(2)凹凸模工作尺寸的制造公差
它直接影响塑件的尺寸公差,通常凹、凸模的制造公差取塑件公差的1/3~1/6,表面粗糙度取Ra值为0.8~0.4μm。
(3)凹凸模使用过程中的磨损量及其他因素的影响
通常凹、凸模的工作尺寸根据塑料的收缩率,凹、凸模零件的制造公差以及磨损量3个因素确定。
2.2.2凹凸模的尺寸计算
凹凸模的工作尺寸计算依据以上的三种因素来确定,依次计算凹凸模的工作尺寸。
(1)凹模的工作尺寸计算
凹模是成型塑件的外形的模型零件,其工作尺寸属于包容尺寸,在使用过程中会使包容尺寸逐渐增大。
所以,为了使得模具的磨损留有修模的余地以及装配的需要,在设计模具时,包容尺寸尽量取下限尺寸。
尺寸公差取上偏差。
凹模的径向尺寸计算公式:
(2.1)
凹模的深度尺寸计算公式:
(2.2)
式中:
L塑——塑件外形公称尺寸
H塑——塑料高度方向的公称尺寸
K——塑料的平均收缩率,取
△——塑件的尺寸公差
δ——模具制造公差,一般去塑件相应尺寸公差的1/3~1/6
因此:
=65.01+0.08
=39.95+0.06
=9.92+0.03
(2)凸模的工作尺寸计算
凸模是成型塑件内形的,其工作尺寸属于被包容尺寸,在使用过程中凸模的磨损回使被包容尺寸逐渐的减小。
所以为了使得模具的磨损留有修模的余地以及装配需要,在设计模具时,被包容尺寸尽量取上限尺寸,尺寸公差取下偏差。
凸模的径向尺寸计算公式:
(2.3)
凸模的高度尺寸计算公式:
(2.4)
式中:
——塑件内形径向公称尺寸
——塑件位置尺寸
因此:
=62.69-0.08
=37.47-0.06
=8.68-0.03
2.3型腔尺寸的确定
注塑成型过程中,型腔承受塑料熔体的高压作用,因此凹模、凸模的底板必须具有足够的强度和刚度。
如果凹模和地板的厚度过小,则强度、刚度会不足。
强度不足会导致型腔产生塑性变形甚至破裂;刚度不足将产生过大的弹性变形,并产生溢流间隙。
1、组合型腔壁厚a计算
由于注塑成型受温度、压力、塑料特性及塑件形状复杂等因素的影响,所以通过刚度、强度的计算公式得到的数据,并不能真实反映结果。
在模具设计中,型腔壁厚及支撑板厚度通常是经验与计算相结合。
如下:
型腔壁厚a计算
镶拼式型腔壁厚
b——矩形型腔内壁短边尺寸
所以:
a=0.1×40+5=9mm
取整得:
a=10mm
2、型腔间距b计算
对于b≧a/2,一般取12~20mm,这里取15mm。
型腔之间有流道时,一般取25~30mm,这里取30mm
图2.3型腔尺寸关系
3、型腔底板厚度C计算
型腔底板实际上就是支承板,假设支撑板上受力均匀。
1)当A<10时,C=A+10
2)当
时,C=0.125A+18.75
3)当
时,C=0.1A+20
A——塑件在分型面上的投影面积
塑件大概尺寸为A=26㎝2
所以:
C=0.125×26+18.75=22,这里取C=25mm
4、模套壁厚d计算
组合式矩形型腔需要嵌套在模套之内,所以必须对模套进行计算,保证其强度。
d=0.482b+2.72
b——矩形型腔内壁短边尺寸,即塑件外壳的宽。
所以:
d=0.482×40+2.72=22,这里取d=25mm。
2.4模具冷却系统确定
为了缩短成型周期,需要对模具进行冷却,常用水对模具进行冷却。
即在注塑完成后通循环冷却水到靠近型腔的零件上或成型腔零件上的孔内,以便快速使模具冷却。
冷却系统设计应遵循如下原则:
1.设计冷却系统应先于推出机构
2.注意凹模和型芯的热平衡
3.冷却水道数量应尽量多,截面积应尽量大
4.合理确定冷却水道至型腔避的距离
5.冷却水道入口处水流温差应尽量小
6.加强浇口处的冷却
7.冷却水道应沿着塑料收缩的方向设置
1、冷却时间计算
塑件在模具内的冷却时间,通常是指塑料熔体从充满模具型腔起到可以开模取出塑件时止的这一段时间。
可以开模的标准时塑件以及那个充分固化,具有一定的强度和刚度,在开模推出时不致变形、开裂。
衡量塑件已固化的准则如下:
(1)塑件最大壁厚中心的部分温度已冷却到该模具塑料的热变形温度以下。
(2)塑件截面内的平均温度已达到所规定的塑件出模温度。
(3)对于结晶型塑料,最大壁厚中心层达到固熔点,或者结晶达到某一百分比
采用第一种固化标准,则塑件冷却时间:
(2.5)
式中:
S——塑件的壁厚,塑件壁厚S=1.5mm
α——塑料扩散率,对于ABS,α=0.080mm2/s
TC——塑料注射温度,对于ABS,TC=220°C
TM——模具温度,对于ABS,TM=60°C
T1——塑料的热变形温度,对于ABS,T1=105°C(载荷0.46MPa)
所以:
2、水道数目确定
(1)塑料传给模具的热量
单位质量的ABS再成型温度下,单位热流量为Q为4.0×102kj/kg。
2)模具冷却时所需冷却介质流量为:
(2.6)
式中:
qv——冷却介质的体积流量,
W——单位时间内注入模具中的塑料质量,对于ABS,成型周期为T=30S,则每小时成型次数N=3600/T=120次。
每次注射质量为M=50g。
,则W=NM=120×50=6Kg/h。
ρ——冷却介质的密度,冷却水的密度为ρ=1×103Kg/m3。
C2——冷却介质的比热容,冷却水的比热容为C2=4.187×103J/(kg·°C)
T3——冷却介质出口温度,冷却水出口温度为T3=30°C
T4——冷却介质入口温度,冷却水入口温度为T4=24°C
所以
取冷却管道直径d=10mm,求得冷却水的流速为
3)冷却水道总传热面积
A——冷却水道总传热面积
K——冷却水道孔壁与冷却介质之间的传热膜系数,
——模温与冷却介质温度之间的平均温差,
——冷却介质温度有关的物理系数,从表中选取f=6.48(25°C环境下)
则:
=0.172×104(KJ/(m·h·°C))
所以:
4)冷却水道数目的计算
(2.7)
式中:
n——冷却水道数
L——冷却水道开设方向的模具长(或宽)
所以:
取整n=5
习惯认为凸模比凹模散热条件差,易存储热量,