机组启动试运行程序.docx
《机组启动试运行程序.docx》由会员分享,可在线阅读,更多相关《机组启动试运行程序.docx(23页珍藏版)》请在冰豆网上搜索。
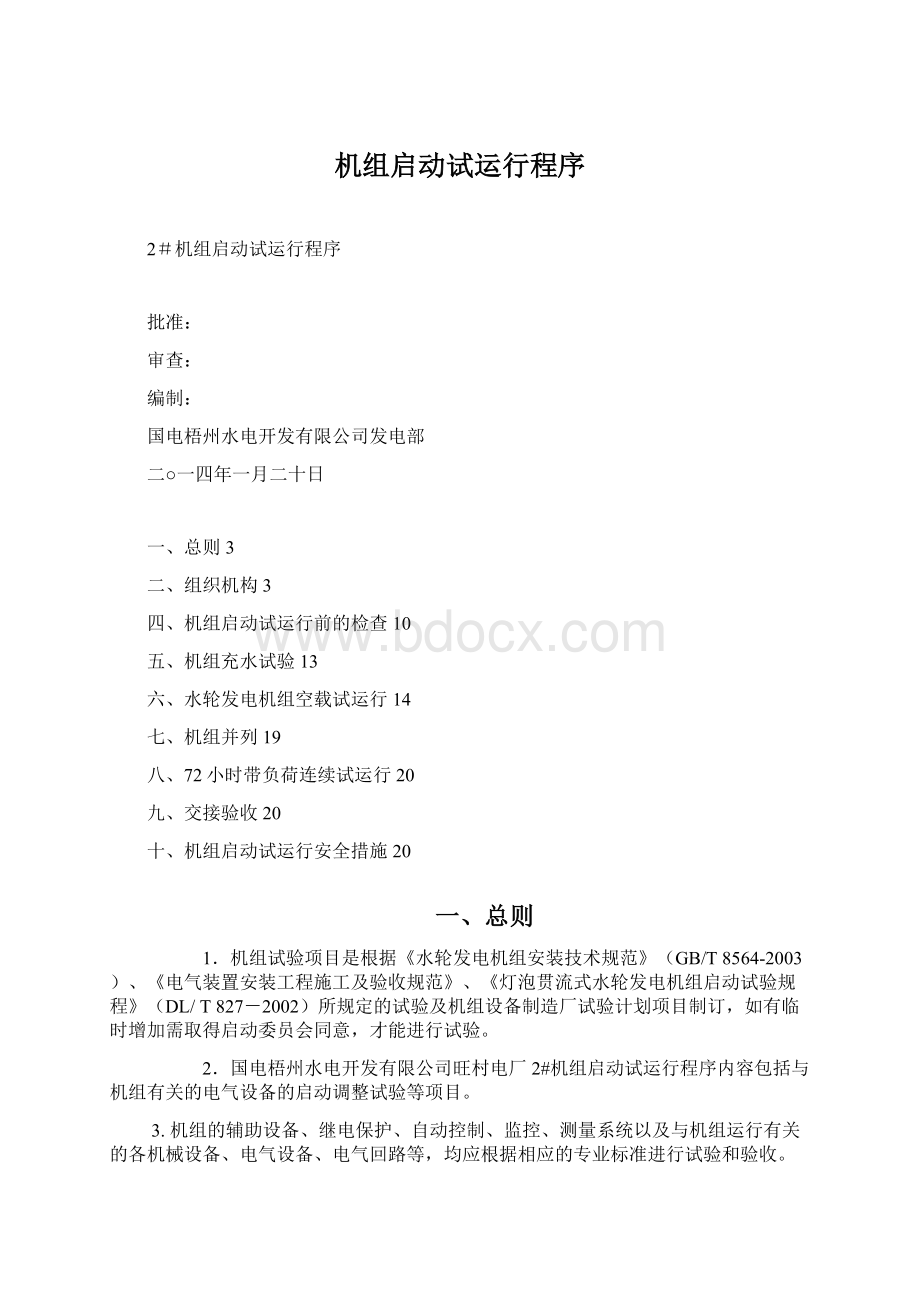
机组启动试运行程序
2#机组启动试运行程序
批准:
审查:
编制:
国电梧州水电开发有限公司发电部
二○一四年一月二十日
一、总则3
二、组织机构3
四、机组启动试运行前的检查10
五、机组充水试验13
六、水轮发电机组空载试运行14
七、机组并列19
八、72小时带负荷连续试运行20
九、交接验收20
十、机组启动试运行安全措施20
一、总则
1.机组试验项目是根据《水轮发电机组安装技术规范》(GB/T8564-2003)、《电气装置安装工程施工及验收规范》、《灯泡贯流式水轮发电机组启动试验规程》(DL/T827-2002)所规定的试验及机组设备制造厂试验计划项目制订,如有临时增加需取得启动委员会同意,才能进行试验。
2.国电梧州水电开发有限公司旺村电厂2#机组启动试运行程序内容包括与机组有关的电气设备的启动调整试验等项目。
3.机组的辅助设备、继电保护、自动控制、监控、测量系统以及与机组运行有关的各机械设备、电气设备、电气回路等,均应根据相应的专业标准进行试验和验收。
4.对机组启动试运行试验过程中出现的问题和存在的缺陷,应及时加以处理和消除,使机组交接验收后可长期、安全、稳定运行。
5.机组启动试运行试验过程中应充分考虑上、下游水位变动对库岸边坡稳定、库区河道航运及周围环境保护和植被生长的影响,保证试运行试验工作的正常进行。
二、组织机构
启动试运行总指挥:
黄胜伟
启动试运行副总指挥:
冉光天、黎万绪
试运行安全员:
蒙好厚
试运行维护组组长:
席桂华
试运行维护组副组长:
杨鹏
维护组成员:
冯宇翔、刘淑萍、甘日湑、苏伟鸿、王文忠、汪如哲、苏家慧、
运行组值长:
陈雪平、朱小喜、包富元、严伟
运行组成员:
张骏飚、刘培桃、黎树焕、覃柳梅、计建华、覃志胜、严健富、黄志贵、董龙平、岑锐、陈童、许鸿钊、黄仲康、张燕妮、韦佰泽、莫庆华
三、技术参数
1、水轮机:
1、水轮机型式:
卧轴灯泡式水轮机
2、水轮机型号:
GZ(K241)-WP-540
3、最大水头(14.32m)/额定水头(9.2m)/最小水头:
(3.0m)
4、额定流量:
247.5m³/s
5、额定出力:
20.62MW
6、额定转速:
107.1r/min
7、最大飞逸转速:
345r/min(非协联)
8、旋转方向:
从上游往下游看顺时针
9、最大水头时的最大轴轴向推力
正向推力265t
10、水轮机安装高程(转轮中心线):
EL-1.2m
2、发电机:
1、型号:
SFWG20-56/6000
2、额定容量:
21.739MVA/20MW
3、额定电压:
VN=10.5kV
4、额定电流:
IN=1195.3A
5、额定功率因数:
cosФN=0.92(滞后)
6、额定频率:
FN=50HZ
7、额定转速:
nN=107.1r/min
8、相数:
3
9、额定励磁电压:
Vfn=219.1V
10、额定励磁电流:
Ifn=702.1A
11、定子、转子绝缘耐热等级:
F级
12、旋转方向:
从上游侧向下游侧看为顺时针方向
13、励磁方式:
可控硅静止励磁
14、测速装置:
残压测频+齿盘测速
15、飞轮力矩(GD2)不小于2220t.m2
16、电机纵轴同步电抗Xd=0.9671(设计值)
17、电机纵轴瞬变电抗Xd’=0.3251(设计值)
18、电机纵轴超瞬变电抗:
Xd”=0.2386(设计值)
19、流道河水水温不高于28℃
20、要求轴承油冷却器和空气冷却器冷却水温不高于30℃,水压应满足0.2MPa要求。
3、机组轴承温度:
1、组合轴承:
报警:
65℃
跳闸:
70℃
2、导轴承:
报警:
65℃
跳闸:
70℃
4、调速器:
1、型号:
WST-100-6.3
2、工作油压:
6.3MPa
3、设计油压:
6.3MPa
4、导叶接力器全关行程时间:
40s第一段关闭时间:
15S
5、浆叶关闭时间:
60s
5、油压装置:
1、型号:
YZ-6.0-6.3
(1)压力油罐:
容积:
6.0m³
罐内油体积:
2.0m³
(2)回油箱:
储油量(正常油位):
6.0m³
最大储油量:
8.0m³
(3)螺杆旋油泵:
最大工作压力:
6.3MPa
输油量(最大工作压力时):
6L/S
(4)油泵电动机:
型号:
Y225M-4B5
功率:
45KW
电源:
~380V,50Hz,三相
转速:
1450r/min
(5)安全阀
排油压力:
7.18MPa
(6)压力开关整定值
工作油泵启动:
6.0
备用油泵启动:
5.8
运转油泵切除:
6.3
低油压报警:
5.0
6、高位油箱:
1、基本参数
有效容积:
2m3
2、油位整定值:
(1)正常工作油位:
距离油箱底部1250mm~1550mm。
(2)高油位(1550mm以上)GYK1发讯,高位油箱液位高报警,二个油泵停止。
(3)事故油位(550mm以下)GYK4用于高位油箱油箱液位低报警,主机停车或不允许启车信号。
在此液位时没箱存油2100L,可提供发电机十分钟的供油。
(4)低油位(低于1250mm,高于550mm),GYK3发讯,高位油箱液位低报警,向主控室发送高位油箱液位低报警,控制备用泵启动,这时两台泵同时进行工作,一直到工人来处理问题。
(5)基准油位(低于1550mm,高于1250mm),GYK2发讯,高位油箱液位正常,并给主控室高位油箱正常信号。
7、低位油箱:
1、基本参数
油箱容积:
7m3
2、油位整定值:
(1)正常工作油位:
距离油箱底部350mm~1450mm。
(2)液位过高(1450mm以上),ZYK1发讯,主油箱液位高报警。
(3)液位过低(250mm以下),ZYK4发讯,主油箱液位过低报警,低压泵组停,向主控室发送停机信号。
(4)液位低(低于350,高于250mm),ZYK3发讯,主油箱液位低报警,向主控室发送主油箱液位低故障信号。
(5)液位高(低于1450,高于350mm),ZYK2发讯,主油箱液位正常是高、低压泵组起动先决条件。
8、漏油箱:
1、基本参数
(1)总容积:
300L
(2)系统公称压力:
1.6MPa
(3)流量:
50L/min
(4)油泵型号:
CB-B40
(5)油泵台数:
1台
(6)电动机型号:
Y2-90S-4
(7)电动机功率:
11KW
(8)运行方式:
油箱中油位到设定位置时启动
2、整定值
(1)上限(900mm)LYK1发讯,漏油泵组起动。
(2)下限(150mm)LYK2发讯,漏油泵组停止。
9、高压油顶起装置:
1、基本数据
型号:
10MCY14-1B
电机:
5.5kW
2、整定值
(1)一台备用,一台主用
(2)机组停机转速下降到95%时主用油泵投入,当转速下降到零时油泵切除。
机组启动之前用主油泵投入,当转速达到95%时油泵切除。
3、高压顶起压力
(1)发电机径向轴承:
11MPa
(2)水轮机导轴承:
4.5MPa
10、机组轴承用油量:
1、发电机正向推力轴承:
180L/min0.2MPa
2、发电机反向推力轴承:
35L/min0.2MPa
3、发电机径向轴承:
35L/min0.2MPa
4、水轮机导轴承:
35L/min0.2MPa
11、检修排水系统:
1、基本参数:
(1)水泵型号:
Q=386~644~772m³/h,H=35~30~25m
(2)电动机功率:
75KW
(3)台数:
2(一用、一备)
12、渗漏排水系统:
1、基本参数
(1)水泵型号:
Q=154~220~264m³/h,H=48~40~20m
(2)电动机功率:
37KW
(3)台数:
2(一用、一备)
13、中压气系统:
1、中压气系统基本参数:
(1)中压空压机型号:
SF-1.1/80型,Q=1.1m³/min,PN=8Mpa,风冷式
(2)功率:
22KW
(3)台数:
2台中压空压机(两台互为备用,正常时为自动启动,也可手动),1个中压气罐(1.3m3,8MPa)。
2、整定值
(1)压力上限(与安全阀开启压力同值,8.2MPa),压力过高故障报警
(2)压力正常(设计值8MPa),主、备用空压机均停机
(3)压力第一下限(7.5MPa),主空压机启动
(4)压力第二下限(7.3MPa),备用空压机启动并发出压力过低故障报警信号
(5)安全阀泄压整定值>70bar
14、低压气系统:
1、基本参数
(1)低压气机型号:
TA-100型,Q=1m³/min,PN=0.7MPa,风冷式
(2)功率:
7.5KW
(3)台数:
两台低压气机(一台主用,正常时为自动启动,也可手动),两个低压气罐(2.0m3,0.7MPa),其中一个为检修储气罐。
2、整定值
(1)压力上限(与安全阀开启压力同值,0.82MPa),压力过高故障报警
(2)压力正常(设计值0.7MPa),主、备用空压机均停机
(3)压力第一下限(0.6MPa),主空压机启动
(4)压力第二下限(0.55MPa),备用空压机启动并发出压力过低故障报警信号
(5)当储气罐压力为0.55MPa时,发出低压警报;
15、主变压器:
1#主变压器
产品型号:
SF11-50000/110
额定容量:
50000KVA
额定电压:
121/10.5KV
额定电流:
238.6/2749.3A
额定频率:
50HZ
相数:
3
分接范围:
121±2×2.5%/10.5KV
联结组标号:
YNd11
冷却方式:
ONAF
绝缘耐热等级:
A
绝缘水平:
h.v.线路端子L1/AC480/200KV
h.v.中性点端子L1/AC325/140KV
1.v.线路端子L1/AC75/35KV
尺寸:
5360×2366×3042(本体)(单位:
mm)
2#主变压器
产品型号:
SF11-25000/110
额定容量:
25000KVA
额定电压:
121/10.5KV
额定电流:
119.3/1374.6A
额定频率:
50HZ
相数:
3
分接范围:
121±2×2.5%/10.5KV
联结组标号:
YNd11
冷却方式:
ONAF
绝缘耐热等级:
A
绝缘水平:
h.v.线路端子L1/AC480/200KV
h.v.中性点端子L1/AC325/140KV
1.v.线路端子L1/AC75/35KV
16、GIS设备主要技术参数如下表:
序号
参数名称
单位
数值
1
额定电压
kV
72.5
126
2
额定电流
A
1600,2000,3150
3
额定频率
Hz
50
4
额定短时耐受电流(有效值)
kA
主导电回路:
31.5,40
接地回路:
31.5,40
5
额定短时耐受电流(有效值)
kA
80,100
6
额定短路持续时间
s
4
7
额定绝
缘水平
额定短时工频耐受电压(有效值,1min)
对地,极间
kV
160
230
断口
160+42
230+73
额定雷电冲击耐受电(峰值)
对地,极间
350
550
断口
350+59
550+103
8
无线电干扰电压水平(在1.1倍额定极电压下)
μV
≤500
9
局部放电量(整间隔)
pC
〈10
10
额定SF6气体压力(20°C时)
断路器气室
断路器额定短路开断电流
kA
31.5,40
31.5
40
额定压力
MPa
0.50
0.50
0.60
报警压力
0.45
0.45
0.55
闭锁压力(最低功能压力)
0.40
0.40
0.50
其他气室
额定压力
0.40
0.50
报警压力
0.36
0.42
最低功能压力
0.35
0.40
11
气室内SF6气体水分含量
断路器气室
验收值
ppm
(V/V)
150
运行值
300
其他气室
验收值
250
运行值
500
12
Sf6气体年泄漏率
%
≤0.5
13
辅助回路和运动部分防护等级
一
户内IP5X
户外IP5XW
17、共箱封闭母线
10.5kV高压柜(13G)至1#主变段母排额定电流:
4000A
四、机组启动试运行前的检查
1、流道检查
(1)进水口拦污栅已安装调试完工并清理干净检验合格,拦污栅差压测压头与测量仪表已安装完工并检验合格。
(2)进水口闸门门槽已清扫干净并检验合格。
进水口闸门及其启闭装置均已安装完工、检验合格并处于关闭状态。
(3)进水流道、导流板、转轮室、尾水管等过水通流系统均已施工安装完工、清理干净并检验合格。
所有安装用的临时吊耳、吊环、支撑等均已拆除。
混凝土浇注孔、灌浆孔、排气孔等已封堵。
测压头已装好,测压管阀门、测量表计均已安装。
发电机盖板与框架已把合严密,所有进人孔(门)均已封盖严密。
(4)进水流道排水阀、尾水管排水阀启闭情况良好并处于关闭位置。
(5)尾水闸门门槽及其周围已清理干净,尾水闸门及其启闭装置已安装完工并检验合格。
在无水情况下手动、自动操作均已调试合格,启闭情况良好。
尾水闸门处于关闭状态。
(6)水电站上、下游水位测量系统已安装调试合格,水位信号远传正确。
2、水轮机检查
(1)2#水轮发电机组已安装完毕并检验合格。
转轮叶片与转轮室之间的间隙已检查合格,且无遗留杂物。
(2)导水机构已安装完工、检验合格,并处于关闭状态,接力器锁定投入。
导叶最大开度和导叶立面、端面间隙及压紧行程已检验合格,并符合设计要求。
(3)主轴及其保护罩、水导轴承系统已安装完工、检验合格,轴线调整符合设计要求。
(4)主轴工作密封与检修密封已安装完工、检验合格,密封自流排水管路畅通。
检修密封经漏气试验合格,充水前检修密封的空气围带处于充气状态。
(5)各过流部件之间(包括转轮室与外导环、外导环与外壳体、内锥体与内导环、内导环与内壳体等)的密封均已检验合格,无渗漏情况。
所有分瓣部件的各分瓣法兰均已把合严密,符合规定要求。
(6)伸缩节间隙均匀,密封有足够的紧量。
(7)各重要部件连接处的螺栓、螺母已紧固,预紧力符合设计要求,各连接件的定位销已按规定全部点焊牢固。
(8)受油器已安装完毕,经盘车检查,其轴摆度合格。
(9)各测压表计、示流计、流量计、摆度、振动传感器及各种信号器、变送器均已安装完工,管路、线路连接良好,并已清理干净。
(10)水轮机其他部件也已安装完工、检验合格。
3、调速系统的检查
(1)调速系统及其设备已安装完工、并调试合格。
油压装置压力、油位正常,透平油化验合格。
各表计、阀门、自动化元件均已整定符合要求。
(2)压力油罐安全阀按规程要求已调整合格,且动作可靠。
油压装置油泵在工作压力下运行正常,无异常振动和发热,主、备用泵切换及手动、自动工作正常。
集油箱油位信号器动作正常。
高压补气装置手动、自动动作正确。
漏油装置手动、自动调试合格。
(3)手动操作将油压装置的压力油通向调速系统管路,检查各油压管路、阀门、接头及部件等均应无渗油现象。
(4)调速器的电气/机械/液压转换器工作正常。
(5)进行调速系统联动调试的手动操作,并检查调速器、接力器及导水机构联动动作的灵活可靠性和全行程内动作平稳性。
检查导叶开度、接力器行程和调速器柜的导叶开度指示器等三者的一致性。
录制导叶开度与接力器行程的关系曲线,应符合设计要求。
(6)重锤关机等过速保护装置和分段关闭装置等均已调试合格,分别用调速器紧急关闭和重锤关机办法初步检查导叶全开到全关所需时间。
(7)锁定装置调试合格,信号指示正确,充水前应处于锁定状态。
(8)由调速器操作检查调速器柜和受油器上的桨叶转角指示器的开度和实际开度的一致性。
模拟各种水头下导叶和桨叶协联关系曲线。
(9)对调速器自动操作系统进行模拟操作试验,检查自动开机、停机和事故停机各部件动作准确性和可靠性。
(10)机组测速装置已安装完工并调试合格,动作触点已按要求初步整定。
4、发电机检查
(1)发电机整体已全部安装完工并检验合格。
发电机内部已进行彻底清扫,定、转子及气隙内无任何杂物。
(2)正反向推力轴承及各导轴承已安装调试完工,检验合格。
(3)各过流部件之间包括定子机座与管形座内壳体、定子机座与冷却套等)和各分瓣部件的法兰面的密封均已检验合格,符合规定要求。
(4)空气冷却器已检验合格,水路畅通无阻,阀门无渗漏现象。
冷却风机、除湿器、电加热器已调试,运行及控制符合设计要求。
(5)发电机内灭火管路、火灾探测器、灭火喷嘴已检验合格。
管路及喷嘴手动动作准确,通压缩空气试验畅通无阻。
(6)发电机制动闸与制动环之间的间隙合格风闸吸尘装置动作准确。
机械制动系统的手动、自动操作已检验调试合格,动作正常,充水前风闸处于制动状态。
(7)发电机转子集电环、碳刷、碳刷架已检验并调试合格。
(8)发电机灯泡体内所有阀门、管路、接头、电磁阀、变送器等均已检验合格,处于正常工作状态。
灯泡体内外所有母线、电缆、辅助线、端子板、端子箱均已检查正确无误。
(9)发电机水平支撑和垂直支撑已检验合格。
(10)测量发电机工作状态的各种表计、振动摆度传感器、轴电流监测装置、气隙监测装置、局部放电监测仪等均已安装完工,调试整定合格。
(11)爬梯、常规及事故照明系统已安装完工,检验合格。
灯泡体内已清扫干净,设备的补漆工作已完成并检查合格。
5、励磁系统检查
(1)励磁盘柜已安装完工并检验合格,系统回路已做耐压试验并合格。
(2)励磁电源变压器已安装完工并检验合格,高、低压端连接线已检查,电缆已检验并合格,耐压试验已通过。
(3)励磁调节器及功率柜经开环调试,有关的整定工作已初步完成。
(4)励磁功率柜通风系统已安装完毕,运转正常。
5、油、水、气系统检查
(1)全厂透平油、绝缘油系统已投入运行,能满足该台机组供油、用油和排油的需要。
油质经化验合格。
(2)轴承高位油箱、轮毂高位油箱、轴承回油箱、漏油箱上各液位信号器已调整,油位符合设计规定,触点整定值符合设计要求。
各油泵电动机已做带电动作试验,油泵运转正常,主、备用切换及手动、自动控制工作正常。
电加热器检验合格。
(3)正反向推力轴承及各导轴承润滑油温度、压力、油量检测装置已调试合格,整定值符合设计要求。
(4)导轴承的高压油顶起装置已调试合格,压力继电器工作正常,各单向阀及管路阀门均无渗油现象。
高压油顶起系统手动、自动控制正常。
(5)全厂高、低压空气压缩机均已调试合格,储气罐及管路无漏气,管路畅通。
各压力表计、温度计、流量计、安全阀及减压阀工作正常。
整定值符合设计要求。
(6)所有高、低压空气管路已分别分段通入压缩空气进行漏气检查合格。
(7)机组冷却、主轴密封等技术供水系统管路、过滤器、阀门、表计、接头等均已安装完工、检验合格。
(8)主轴密封水的水质已检查并满足设计要求,水压、水量已调整至设计允许的范围内。
(9)对于采用二次冷却的机组,各循环水泵、压力及流量检测元件已安装调试合格,油冷却器支路和空气冷却器支路各自水量、水压满足设计要求。
液位计调试合格,水位正常。
各水泵运转正常并处于设定工作状态。
(10)各管路、附属设备已按规定涂漆,标明流向,各阀门已标明开关方向,挂牌编号。
以上各项确认全部已达到具备充水条件,即可进行机组充水试验。
五、机组充水试验
1、充水条件
(1)确认坝前水位已蓄至最低发电水位。
(2)确认进水口闸门、尾水闸门处于关闭状态。
确认各进人门已关闭牢靠,各检修排水阀门已处于关闭状态。
确认调速器、导水机构处于关闭状态,接力器锁定已投入。
确认空气围带、制动器处于投入状态。
(3)确认水电站厂房检修、渗漏排水系统运行正常。
2、流道充水
(1)流道检查完毕,各进人孔已封堵,各检修排水阀已关闭。
(2)开启导叶至5%开度。
(3)发电机制动闸处于手动加闸位置。
(4)检修密封充气。
(5)提尾水闸门充水阀向流道充水至与尾水位相平,检查转轮室、伸缩节、主轴密封处、定子上、下游法兰及流道盖板、测压系统等处,应无漏水,记录测压系统的读数。
(6)将导叶关至全关。
(7)作静水中尾水门的启闭试验,然后将尾水闸门保持在全关位置。
(8)提进水闸门充水阀向进水流道充水,检查流道、灯泡体、管形座、框架盖板、导水机构各密封面应无渗漏现象,充水至平压,提起进水口闸门。
充水过程监视进水道压力表的读数并检查测压系统传感器应显示正确。
(9)提起尾水闸门并保持在全开位置。
六、水轮发电机组空载试运行
1、首次手动开机前的准备
(1)确认充水试验中出现的问题已处理合格。
(2)主机周围各层场地已清理干净,吊物孔盖板已盖好,通道畅通,通讯指挥系统可随时使用,各部位运行人员已进入岗位。
各测量仪器、仪表已调整就位。
(3)上、下游水位已记录。
各部位原始温度已记录。
(4)投入主轴密封供水,水压正常,投入油冷却器供水,水压正常。
(5)水轮机检修密封排气。
(6)润滑油系统投入运行状态,调速器处于准备开机状态,漏油装置处于自动位置。
(7)测速系统各设备投入。
(8)计算机监控系统投入,温度测量显示正确。
(9)发电机出口断路器断开并在试验位置,转子集电环碳刷拔出。
(10)拆除电气所有试验用的短接线及接地线。
(11)外接标准频率表监视发电机转速。
(12)启动高压油顶起装置,确认机组大轴能正常顶起。
(13)检查机组机械制动情况,然后手动复归制动闸。
2、首次手动开机
(1)启动高压顶起装置。
(2)将调速器控制方式转换开关置“手动”,操作导叶控制开关开启导叶至机组开始转动(仅转数周),然后立刻关闭导叶,由各部位观察人员检查和确认无异常情况。
如果一切正常,一步一步打开活动导叶使机组启动,待机组转速升至50%ne时作暂时停升速,观察无异常后升至额定转速,让机组在额定转速下运转几分钟,记录机组在此水头(上、下游水位)下的启动开度和空载开度。
(3)手动切除高压油顶起装置。
(4)由专人负责监视轴承温度、摆度、振动、转速和水压等,轴承温度记录。
(5)观察机组各部位有无异常现象。
如发现金属碰撞声、瓦温突然升高、机组摆度、振动过大等不正常现象应立即停机。
(6)测量、记录机组运行摆度(双幅值),其值应满足厂家设计规定值。
(7)测量、记录机组各部位振动。
(8)测量发电机残压、相序,相序应正确。
(9)打磨发电机转子集电环表面,将转子集电环炭刷插回原位。
3、调速系统的调整试验
(1)运行至瓦温基本稳定后进行调速器试验。
检查调速器测频信号、其波形应正确,幅值符合要求。
电液伺服阀活塞的振动应正常。
频率给定的调整范围应符合设计要求。
进行手动的自动切换试验时,接力器应无明显摆动。
(2)空载扰动试验应选择适当的调节参数,使之满足以下要求:
①扰动量一般为8%;
②转速最大超调量,不应超过转速扰动量的30%;
③超调次数不超过两次;
④从扰动开始到不超过机组转速摆动规定值为止的调节时间应符合设计规定。
(3)记录油压装置油泵向压力油罐送油的时间及工作周期。
在调整器自动运行时记录导叶接力器活塞摆动值及摆动周期。
4、手动停机及停机后的检查
(1)投入高压油顶起装置。
(2)手动操作停机,当机组转速降至30%ne时手动投入机械制