钢铁环保.docx
《钢铁环保.docx》由会员分享,可在线阅读,更多相关《钢铁环保.docx(8页珍藏版)》请在冰豆网上搜索。
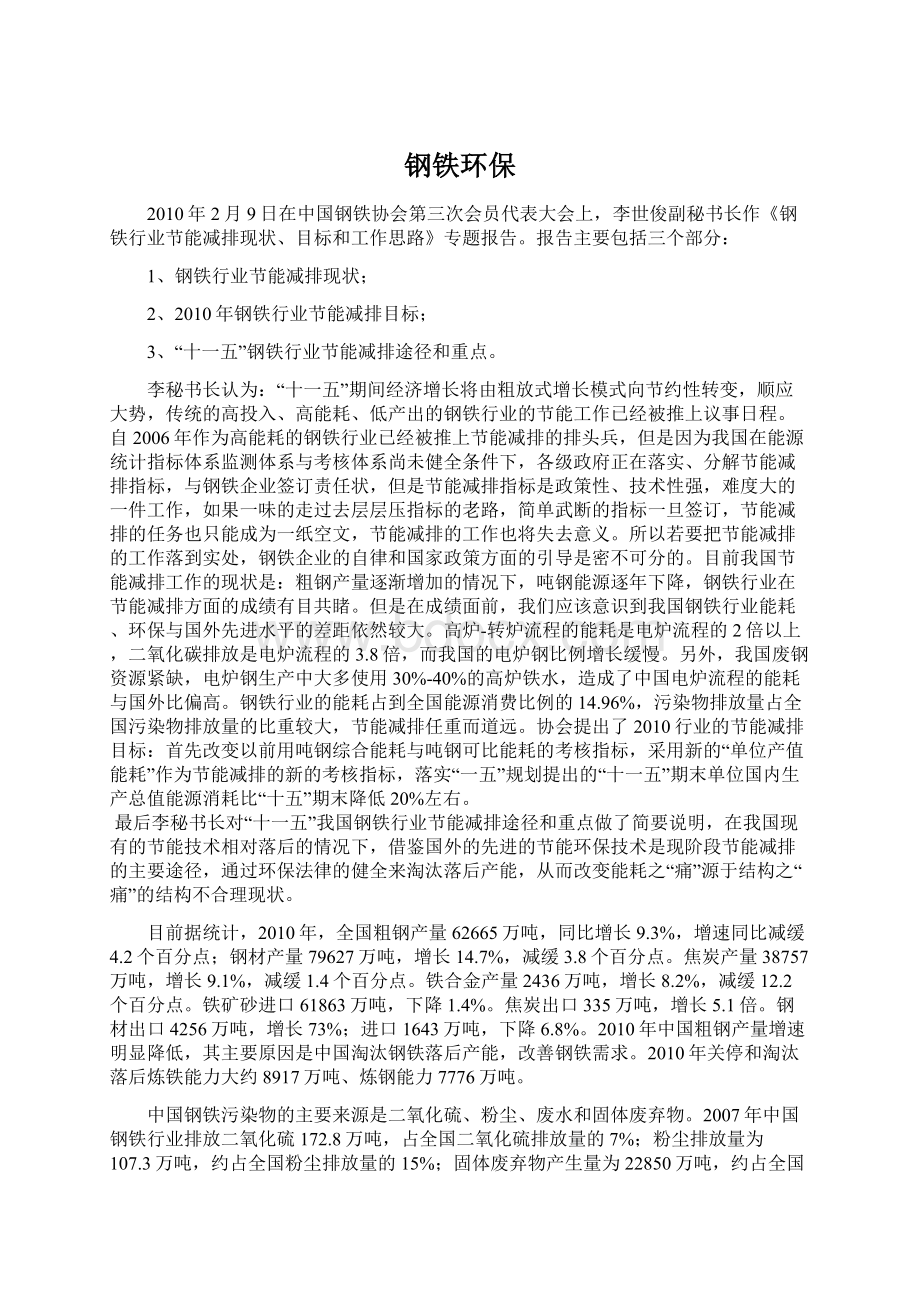
钢铁环保
2010年2月9日在中国钢铁协会第三次会员代表大会上,李世俊副秘书长作《钢铁行业节能减排现状、目标和工作思路》专题报告。
报告主要包括三个部分:
1、钢铁行业节能减排现状;
2、2010年钢铁行业节能减排目标;
3、“十一五”钢铁行业节能减排途径和重点。
李秘书长认为:
“十一五”期间经济增长将由粗放式增长模式向节约性转变,顺应大势,传统的高投入、高能耗、低产出的钢铁行业的节能工作已经被推上议事日程。
自2006年作为高能耗的钢铁行业已经被推上节能减排的排头兵,但是因为我国在能源统计指标体系监测体系与考核体系尚未健全条件下,各级政府正在落实、分解节能减排指标,与钢铁企业签订责任状,但是节能减排指标是政策性、技术性强,难度大的一件工作,如果一味的走过去层层压指标的老路,简单武断的指标一旦签订,节能减排的任务也只能成为一纸空文,节能减排的工作也将失去意义。
所以若要把节能减排的工作落到实处,钢铁企业的自律和国家政策方面的引导是密不可分的。
目前我国节能减排工作的现状是:
粗钢产量逐渐增加的情况下,吨钢能源逐年下降,钢铁行业在节能减排方面的成绩有目共睹。
但是在成绩面前,我们应该意识到我国钢铁行业能耗、环保与国外先进水平的差距依然较大。
高炉-转炉流程的能耗是电炉流程的2倍以上,二氧化碳排放是电炉流程的3.8倍,而我国的电炉钢比例增长缓慢。
另外,我国废钢资源紧缺,电炉钢生产中大多使用30%-40%的高炉铁水,造成了中国电炉流程的能耗与国外比偏高。
钢铁行业的能耗占到全国能源消费比例的14.96%,污染物排放量占全国污染物排放量的比重较大,节能减排任重而道远。
协会提出了2010行业的节能减排目标:
首先改变以前用吨钢综合能耗与吨钢可比能耗的考核指标,采用新的“单位产值能耗”作为节能减排的新的考核指标,落实“一五”规划提出的“十一五”期末单位国内生产总值能源消耗比“十五”期末降低20%左右。
最后李秘书长对“十一五”我国钢铁行业节能减排途径和重点做了简要说明,在我国现有的节能技术相对落后的情况下,借鉴国外的先进的节能环保技术是现阶段节能减排的主要途径,通过环保法律的健全来淘汰落后产能,从而改变能耗之“痛”源于结构之“痛”的结构不合理现状。
目前据统计,2010年,全国粗钢产量62665万吨,同比增长9.3%,增速同比减缓4.2个百分点;钢材产量79627万吨,增长14.7%,减缓3.8个百分点。
焦炭产量38757万吨,增长9.1%,减缓1.4个百分点。
铁合金产量2436万吨,增长8.2%,减缓12.2个百分点。
铁矿砂进口61863万吨,下降1.4%。
焦炭出口335万吨,增长5.1倍。
钢材出口4256万吨,增长73%;进口1643万吨,下降6.8%。
2010年中国粗钢产量增速明显降低,其主要原因是中国淘汰钢铁落后产能,改善钢铁需求。
2010年关停和淘汰落后炼铁能力大约8917万吨、炼钢能力7776万吨。
中国钢铁污染物的主要来源是二氧化硫、粉尘、废水和固体废弃物。
2007年中国钢铁行业排放二氧化硫172.8万吨,占全国二氧化硫排放量的7%;粉尘排放量为107.3万吨,约占全国粉尘排放量的15%;固体废弃物产生量为22850万吨,约占全国固体废弃物产生量的13%;废水排放量约占全国总排废水量的8%。
在国家规定的酸雨、SO2“两控区”内的钢产量占全国的75%左右。
在钢铁生产的耗能及污染方面烧结(球团)厂是钢铁企业的耗能和污染大户,主要的污染物有颗粒物(烟粉尘)、SO2、NOx、CO2、CO、二噁英、氟化物、氯化物及重金属等。
工业烟粉尘、SO2是烧结(球团)厂的主要污染物,其中,SO2占钢铁工业总排放量60%左右,工业粉尘占钢铁工业总排放量的25%左右,烟尘占钢铁工业总排放量的20%左右,因此做好烧结(球团)厂的污染防治工作是钢铁企业整体污染防治工作的重点之一。
“十一五”期间,国家对钢铁企业的环境保护工作提出了新的目标,其中烧结烟气脱硫还被列入“十一五”环境保护重点工程。
烧结(球团)厂是钢铁企业的主要污染源之一,主要的污染物:
颗粒物(产生颗粒物的主要工序:
原料场、原料准备、配料混合、冷却破碎、成品整粒及烧结(球团)设备生产所产生的废气)、SO2、NOx、CO2、CO、二噁英、氟化物、氯化物及重金属(主要来自烧结(球团)设备生产所产生的废气)。
据2005年数据统计,烧结工序SO2排放量约43万吨,占钢铁工业的58.94%;烟尘排放量约2.8万吨,占钢铁工业的19.87%;工业粉尘排放量约11万吨,占钢铁工业26.42%。
20世纪90年代以来,我国钢铁工业大气污染物治理有较大的突破,以2004年为例,全年全行业投入大气污染物治理费用29.9亿元,约占环境保护投资总额的50.66%。
我国烧结(球团)在大气污染治理方面与国外相比差距主要表现在对NOx基本没有采取治理措施;SO2治理刚起步;对二噁英等强有毒气体缺乏相应的监测手段、排放标准和治理措施;工业发达国家粉尘排放标准已降至20mg/Nm3,而我国粉尘排放标准50~100mg/Nm3,相应的除尘器效率较低。
另外,在我国,由于地区差异、技术优劣、经济强弱等因素,大型企业与中小企业在环保治理水平上还存在着一定的差距。
大型钢铁企业能够不断采用新工艺、新技术,加大环保投资力度,有效地控制了污染物的排放。
以2002年钢产量300万吨为划分界限,大型企业的烧结烟尘排放浓度平均水平为82.61mg/m3。
而且,从近几年的数据来看,大型企业烟尘、SO2的排放量都呈下降趋势。
而中小企业的烧结烟尘排放浓度平均水平仅为168.29mg/m3,并且SO2的排放量还略有增加。
近几年来,随着钢铁工业在环保方面投入的不断增加,烧结(球团)厂采用高效除尘设备越来越普遍,在烟(粉)尘治理方面取得了较好的效果。
同时,随着环保产业的不断发展,SO2治理技术也取得了一定的进展,在减少投资费用、提高设备国产化率和谋求副产物资源化方面也已取得明显成效。
国内外烧结烟气SO2治理现状及发展趋势
国内机头烟气SO2治理还刚起步,引用的脱硫工艺也很多。
目前有应用实绩的有(以投运时间为序)湿式空塔清水喷淋再加石灰反应的经典湿式石灰石—亚硫酸钙除氟脱硫工艺(包钢上世纪60年代前苏联援建技术),双碱法工艺(广钢),循环流化床(CFB)(除氟)脱硫工艺(包钢120m2全烟气脱硫、济钢120m2全烟气脱硫、三明钢厂180m2半烟气脱硫),密相干塔工艺(石钢),氨—硫铵法工艺,湿式石灰石—石膏法工艺,旋转喷雾干燥(SDA)脱硫工艺,MEROS工艺。
另外,鞍钢、武钢等一批钢铁企业正在进行实施烧结烟气脱硫规划和论证。
日本水岛4号烧结机于1974年首次采用石灰石—石膏法湿式烧结烟气脱硫,开启世界烧结烟气脱硫的篇章。
早期以氧化镁法、石灰石—石膏法、氨-硫胺法等湿法工艺为主,80年代中期,日本开发活性炭法、欧美开发旋转喷雾干燥法等干法烧结脱硫工艺。
韩国POSCO烧结机脱硫引进日本活性炭吸附法。
烧结烟气脱硫工艺的选择趋势是由“湿”到“干”。
据有关资料介绍,日本在1989年前共建成烧结烟气脱硫装置39套,其中25套为湿式石灰石—石膏法、8套氧化镁法、5套活性炭法、1套氨硫铵法。
从80年中后期开始研发并实施活性炭吸附法干法脱硫工艺,随后烧结机改造或增设脱硫装置基本上全部采用活性炭吸附法脱硫工艺。
德国蒂森86年建设一套完整的湿式石灰石--石膏法烟气脱硫系统,由于高昂的运行费用以及系统维护工作量大,该套装置于93年停止运行。
依靠采购低硫的原燃料控制烧结烟气的二氧化硫浓度,使其低于法规规定的500mg/Nm3。
后由于低硫原料供应难以保证,蒂森公司决定重新实施烧结烟气脱硫工程。
在脱硫工艺的选择上,蒂森放弃了80年代曾经采用的湿法脱硫工艺,计划采用投资和运行成本更省,并且能满足未来更严格环保法规要求的干(半干)法脱硫工艺。
另外还有瑞典基律纳LKAB球团厂96年建有旋转喷雾干燥(SDA)干法脱硫工艺,德国杜依斯堡钢厂108m2烧结机98年建有旋转喷雾干燥(SDA)干法脱硫工艺使用至今。
法国ALSTOM研发NID干法烧结烟气脱硫工艺,并在法国某烧结机上实施。
奥钢联研发MEROS干法脱硫工艺并在LINZ钢厂实施。
从日本烧结脱硫工艺选择的发展趋势、法国ALSTOM和奥钢联(VAI)的干法脱硫工艺的研究、POSC选择日本新日铁的干法活性炭法脱硫工艺,瑞典和德国烧结(球团)采用旋转喷雾干燥(SDA)干法脱硫工艺到蒂森的“弃湿从干”的脱硫工艺选择可看出,国外烧结烟气脱硫工艺的选择总的趋势是由“湿”到“干”。
国内外烧结机头废气NOx治理技术应用现状
国外烧结烟气实施脱硝的工程案例并不多,下图为日本某烧结机分两步实施的脱硫、脱硝工艺,先实施了烟气脱硫装置,后再实施氨吸附法脱硝装置。
国内还没有应用实例,脱硝技术在烧结工艺应用尚未成熟。
生产工艺减排技术
SO2减排生产技术
烧结生产过程控制SO2排放量基本可从以下几方面考虑:
(1)、尽可能采用低硫的原燃料。
据有关资料介绍,机头废气中SO2主要来源于燃料(当然这要取决于铁矿的含硫率,这里仅指低硫铁矿),在铁矿来源不变的情况下,降低碎焦的使用量可减少SO2的排放量,粗碎焦(6mm)的使用相比使用细碎焦(1mm)产生更少的SO2有报道SO2浓度由800mg/Nm3降至500mg/Nm3。
因此,烧结(球团)生产所需的原料、燃料、熔剂等尽可能采购低含硫率原料,可减少烧结(球团)生产排出的SO2总量。
(2)、高低硫原料分别组织调度进各自烧结机生产
在烧结来料无法改变的情况下,针对不同含硫率的原料通过合理组织生产调度,尽可能将高硫原料集中到某座烧结机进行生产,然后再对该烧结机产生的高硫烟气实施烟气脱硫。
(3)、机头废气循环使用。
方法一:
利用部分机头废气循环至整个烧结机的表面,循环使用的废气量:
40-45%,可达到降低燃料消耗及减少废气排放量。
据介绍Hoogovens已应用此方法。
方法二:
废气分段再循环使用。
机头废气循环使用将增加烧结机一次投资和提高运行管理要求,但可减排废气量约28%,减排SO2约63%,据报道还可削减部分NOx。
(4)、实施脱硫系和非脱硫系
在烧结生产过程中一般在温度大于850℃时烧结原燃料中的S转变生成SO2,烧结机下部各风箱SO2浓度各不相同,根据气体分割法,烧结机下部风箱可根据SO2产生量的不同进行组合,分割成脱硫系和非脱硫系两路烟道,实现半烟气脱硫,降低增设脱硫系统的一次投资和运行成本。
实施脱硫系和非脱硫系工艺,脱硫系统的废气量约为烧结机全部废气量的50%,但脱硫系烟气温度可能会降低,可能会导致烟气温度偏低结露而腐蚀排气系统。
粉尘减排清洁生产技术
(1)、厚料层烧结
烧结过程中加高烧结机台车栏板,使料层厚度增加。
料层厚度的提高对提高烧结矿质量、降低燃料消耗有显著的效果,宝钢1号烧结机料层由400-500mm增加到800mm以上时,工序能耗由80.74kg标准煤/t烧结矿降低到56.51kg标准煤/t烧结矿。
因此,厚料层烧结不仅能提高产量、改善产品质量、降低能耗,还能降低机尾及其以后的整粒筛分及转运过程的废气含尘浓度。
但厚料层烧结工艺增加一次投资及需改变烧结主抽风机性能参数。
(2)、铺底料
铺底料烧结技术是在烧结机上铺厚为30-50mm的Ф10-Ф20的烧结矿作为铺底料,然后上铺混合料进行烧结。
该工艺使得机头废气中含尘量由5-6g/Nm3(不设铺底料时)降至1-2g/Nm3,烧结机尾废气含尘量由10-30g/Nm3(不设铺底料时)降至5-15g/Nm3。
(3)、机头废气电除尘器最后一个电场(若为三电场电除尘器则第三电场)收集的粉尘抛弃法烧结烟气粉尘中含有钾钠等碱金属,碱金属的特性是高比电阻及比重较轻,约为0.3t/m³左右,大部分进入机头电除尘器最后一个电场(若为三电场电除尘器则第三电场),该部分粉尘回收利用易富集,同时导致除尘效率降低及产生两次扬尘。
因此,建议最后一个电场的收下粉尘废弃。
烧结废气余热利用清洁生产技术
烧结矿在冷却过程中,产生大量高温废气。
鼓风冷却高温段的废气温度较高,达350~450℃,抽风冷却高温段的废气温度较低,一般为200℃左右。
这部分高温废气含有大量的显热,约占烧结全部热支出的30%。
因此,国内外烧结技术界越来越重视烧结余热的利用。
这样不仅合理地利用了余热,而且也消除了热污染。
烧结余热的利用方法主要有:
(1)、将余热直接用于烧结过程
①用作点火器、保温炉燃烧用空气,以节省焦炉煤气回收一定温度的废气余热可以提高烟气的含氧量,同时节省燃料消耗。
②预热混合料,以降低焦粉单位能耗
点火前,将温度为300~400℃的热空气以0.7~1.0Nm3/m³·s的流量抽过料层。
预热1~2分钟,使表层混合料在完全干燥的情况下进行点火,缩短烧结时间,且由于预热气体带入显热,焦炭燃烧温度提高,扩大了烧结带。
一般情况下,用300℃左右的热废气作为点火保温的助燃空气比用常温空气可节省25%~30%的煤气消耗量。
直接将冷却器的第一段冷却抽出的废气引出作为点火器保温炉的助燃空气以节省煤气。
(2)、将废气余热用来产生蒸汽以代替部分锅炉燃料。
①环冷机废气余热锅炉余热回收
环冷机废气流程为,从余热回收区域(环冷机上部的两个排气筒)抽出的废气经
重力式除尘器净化,进入余热锅炉进行热交换,锅炉排出的约150~200℃的低温废气再经循环风机返回至环冷机风箱连通管。
废气循环使用。
由远距离手动操作循环风机入口阀来调节废气量。
此外,系统中设有一台常温风机,其作用是余热回收设备运行时补充系统漏风,余热回收设备不运行而烧结生产仍在进行时,打开环冷机余热回收区上排气筒的阀门,启用该风机以保证环冷机的正常生产并使环冷机卸出的冷烧结矿温度低于150℃。
②烧结主排废气余热锅炉余热回收
烧结主排气烟气流程为,从余热回收区域抽也的烟气经重力除尘器净化,进入余热锅炉进行热交换,锅炉排出约150-200℃的低温烟气再经烟气循环风机返回烧结机主排气管。
系统中设有旁通管,当最后一个风箱由于漏风而使温度下降时,可将此风箱的烟气送回至前面合适的主排气管道内,以保证抽出的烟气温度在一个较高的水平上。
当最后一个风箱温度回升时,这部分烟气又可继续回收利用。
此外,在回收区与不回收区之间不设隔板,由远距离手动操作循环风机入口阀门来调节烟气量。
从而保证在烧结操作变化时不影响烧结生,同时保证主电除尘器入口温度在露点以上。
(3)、用余热发电,并入电网。
目前,有实际应用的余热发电方式按循环介质的种类分可分为:
废热锅炉法、加
压热水法及有机媒体法三种。
①废热锅炉法
一般废热温度在400℃以上时,采用废热锅炉法回收余热发电。
②加压热水法
加压热水法的特点是废热回收量高,适用于分散、量少、间断废热的回收,特别适用于废气温度在300-400℃余热的回收。
③有机媒体发电
从热循环来说,有机媒体法类似废热锅炉法,所不同的是使用低沸点的有机媒体代体水作为热交换和循环介质。
这种方式对废气温度低于200℃以下的气体特别适合。
含铁尘泥回收利用清洁生产技术
钢铁各生产工序均会产生含铁尘泥,为可再利用的资源,绝大部分回烧结再利用。
(1)、转炉OG泥回用技术
转炉炼钢一次烟气除尘采用湿法(OG)工艺,其烟气除尘浊循环水系统会产生大量的污泥。
该污泥固体成分中含铁达50%左右,具有极好的回收利用价值。
目前有几种其本的利用途径:
一是利用压滤设备压成尘饼外销;二是压成尘饼用卡车运到原料场堆放,使含水率小于15%以下作为混匀矿配料;三是用管道输送到烧结泥浆回用系统。
前两种利用途径存在:
OG泥汽车运输沿途滴撒,造成环境两次污染;料场堆放过程中由于铁氧化发生热反应,出现硬块和表面干燥,刮风二次扬尘严重。
OG泥的特点是颗粒极细,小于0.6μm的占60%以上,其次是OG泥类似胶体溶液,很难浓缩。
而烧结矿在进入烧结机前的一次混合机时需将烧结料加水湿润。
因此,可将转炉炼钢一次烟气湿法(OG)除尘产生的污泥利用管道输送至烧结区经贮存及调整浓度后,以一定的比例均匀的喷入一次混合机内回收利用是一个可重点考虑的回用技术。
根据污泥发生量、污泥排放制度、污泥泵输送能力及配置情况,同时考虑一次混合机的用泥能力,作业率的匹配等综合平衡,确定污泥输送能力、泥浆浓度、混合泥浆泵流量调节措施等,以满足实际生产时不同需要的调节。
可考虑采用全部加水、全部加泥浆、部分加水和部分加泥浆三种输送操作方式。
(2)、除尘灰回用技术
各除尘系统设统一的吸引压送罐车接口,在烧结区设贮存不同种类粉尘的几组粉仓。
利用吸引压送罐车将从原料、炼铁、炼钢、轧钢等各除尘系统收集的除尘灰、焦化区焦粉及石灰区石灰粉密闭输送至烧结区压送到不同的干粉尘仓暂存。
烧结(球团)生产污染防治环境管理内容有:
烧结(球团)生产技术发展要求
根据《烧结厂设计规范》和国家钢铁产业发展政策:
(1)、烧结机的规模规定:
大型:
烧结机单机面积等于或大于300m2。
中型:
烧结机单机面积等于或大于180m2至小于300m2。
小型:
烧结机单机面积小于180m2。
要求大中型烧结机一律采用带式烧结机。
(2)、为了强调建设规模,市场准入的最小面积为180m2,禁用一切二手设备。
(3)、确定工艺流程时必须采用冷烧结矿。
(4)、新建和改、扩建烧结机均应采用烧结矿整粒与分出铺底料工艺。
(5)、生产废水经处理后循环使用。
(6)、发展余热余能发电,要力争电力自给有余。
除尘系统最佳环境管理实践
(1)、除尘器安装后做耐压试验,稳压12小时;
(2)、各尘源抽风点应设手动调节阀便于调节风量,必要时设阻力平衡器;(3)、除尘系统投运时应进行全系统风量平衡和调试工作,使各抽风点处于合理的风量范围。
根据除尘系统的实际使用情况,应定期对除尘系统进行风量平衡调节或测试工作,使除尘系统长期处于最佳工况下运行;
(4)、除尘风管内流速合理,一般取16~18m/s,不应低于15m/s,以免管内积灰。
弯头及三通等异形管件应适当增加耐磨措施;
(5)、除尘系统采用全自动控制;
(6)、粉尘汽运回用可考虑采用吸引压送罐车密闭输送技术,避免粉尘在输送过程中泄漏飞扬。
脱硫工艺最佳环境管理实践
(1)、尽可能利用低硫原料和燃料,以降低机头废气中SO2的含量;
(2)、尽可能采用烧结废气循环使用,以降低废气排放量,减少脱硫系统的规模,降低脱硫系统的一次投资和运行成本;
(3)、烧结工艺优先考虑将烟气划分为脱硫系和非脱硫系,脱硫系实施烟气脱硫,非脱硫系作为烟气加热热源,并预留未来脱硝的位置。
这样做将大大降低污染控制设施的一次投资和运行成本;
(4)、在满足环保要求的前提下科学、合理、经济的确定脱硫效率,使脱硫系统处于最佳、最经济的条件下运行;
(5)、结合企业脱硫剂来源,脱硫剂选择的原则:
以废治废、价廉源广、稳定易得;
(6)、烧结烟气有不同于锅炉烟气和有色冶炼烟气的特点,它的脱硫工艺要求比火电行业更迅速的负荷跟踪和调节能力;
(7)、确定合理的脱硫效率:
脱硫系统脱硫效率的确定或选择的依据是原始SO2浓度、排放标准、当地环境容量和企业的总量控制指标。
要求合理、经济、科学并有一定前瞻性。
脱硫系统的选择在关注脱硫效率的同时,还应关注系统投运后的运行成本和稳定性以及管理和维护等。
烧结烟气脱硫工艺选择要综合考虑烧结生产和烟气的特点、副产物的合理处置,系统管理维护和运行成本,以及其他污染物的交叉影响等。
(8)、烟囱防腐蚀:
建议内衬优选硼硅酸泡沫玻璃砖或另建湿烟囱;
(9)、脱硫系统布置:
与烧结(球团)排气系统“并联”布置。
二噁英控制最佳环境管理实践
(1)、尽可能减少氯化物的输入量,生石灰和轧钢氧化铁皮的含油量控制在<1%的水平,尽可能减少烧结机本身及排气系统的漏风,以减少二恶英的产生量。
(2)、在二恶英控制技术中需添加活性炭,对活性炭的品质要求如下:
比表面积(BET):
1000m2/g粒径:
≤0.4mm,粒径<100μm占90%容重:
400~500kg/m3。