无碳小车设计说明书1 精品.docx
《无碳小车设计说明书1 精品.docx》由会员分享,可在线阅读,更多相关《无碳小车设计说明书1 精品.docx(21页珍藏版)》请在冰豆网上搜索。
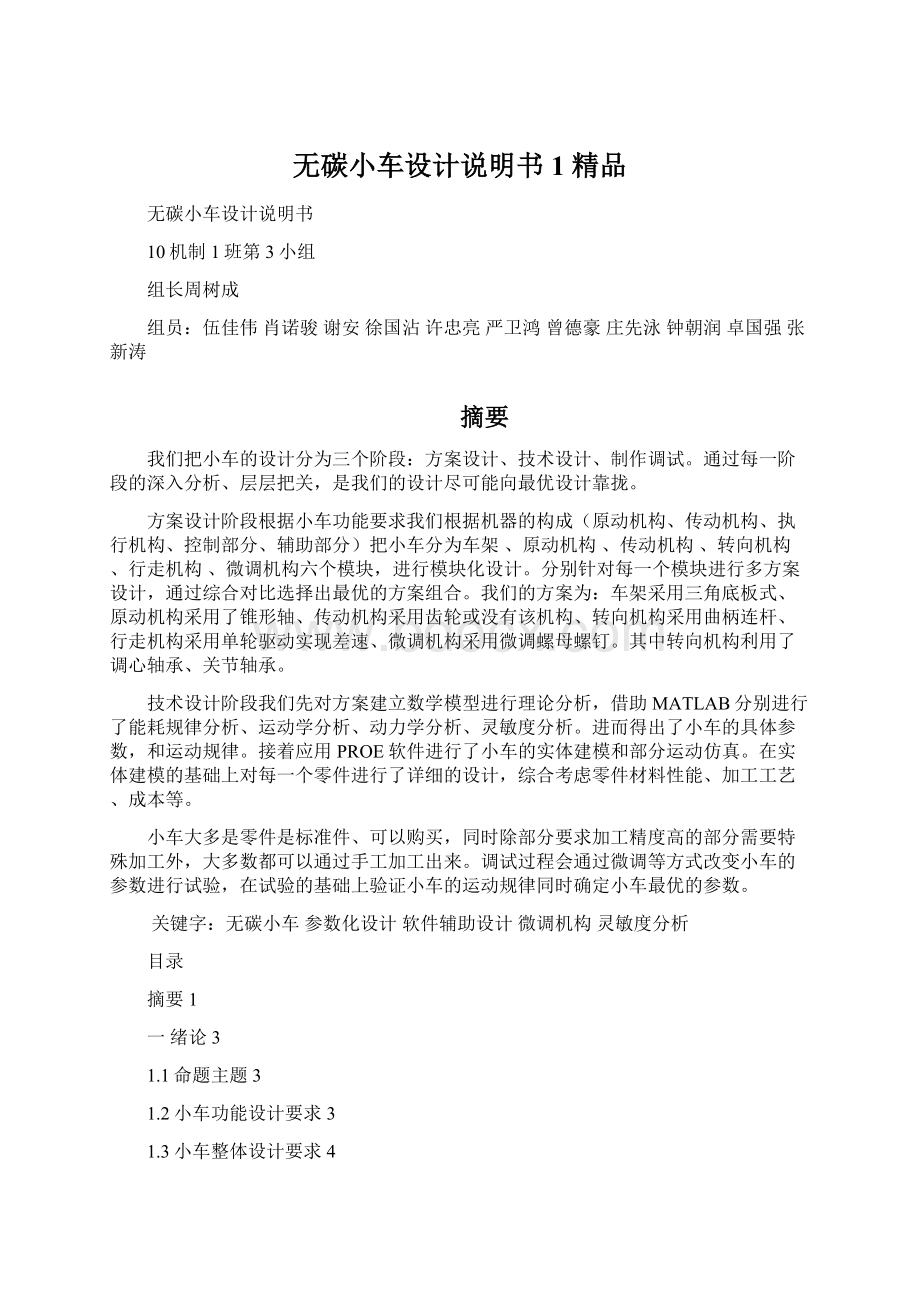
无碳小车设计说明书1精品
无碳小车设计说明书
10机制1班第3小组
组长周树成
组员:
伍佳伟肖诺骏谢安徐国沾许忠亮严卫鸿曾德豪庄先泳钟朝润卓国强张新涛
摘要
我们把小车的设计分为三个阶段:
方案设计、技术设计、制作调试。
通过每一阶段的深入分析、层层把关,是我们的设计尽可能向最优设计靠拢。
方案设计阶段根据小车功能要求我们根据机器的构成(原动机构、传动机构、执行机构、控制部分、辅助部分)把小车分为车架、原动机构、传动机构、转向机构、行走机构、微调机构六个模块,进行模块化设计。
分别针对每一个模块进行多方案设计,通过综合对比选择出最优的方案组合。
我们的方案为:
车架采用三角底板式、原动机构采用了锥形轴、传动机构采用齿轮或没有该机构、转向机构采用曲柄连杆、行走机构采用单轮驱动实现差速、微调机构采用微调螺母螺钉。
其中转向机构利用了调心轴承、关节轴承。
技术设计阶段我们先对方案建立数学模型进行理论分析,借助MATLAB分别进行了能耗规律分析、运动学分析、动力学分析、灵敏度分析。
进而得出了小车的具体参数,和运动规律。
接着应用PROE软件进行了小车的实体建模和部分运动仿真。
在实体建模的基础上对每一个零件进行了详细的设计,综合考虑零件材料性能、加工工艺、成本等。
小车大多是零件是标准件、可以购买,同时除部分要求加工精度高的部分需要特殊加工外,大多数都可以通过手工加工出来。
调试过程会通过微调等方式改变小车的参数进行试验,在试验的基础上验证小车的运动规律同时确定小车最优的参数。
关键字:
无碳小车参数化设计软件辅助设计微调机构灵敏度分析
目录
摘要1
一绪论3
1.1命题主题3
1.2小车功能设计要求3
1.3小车整体设计要求4
1.4小车的设计方法4
二方案设计5
2.1车架7
2.2原动机构7
2.3传动机构7
2.4转向机构8
2.5行走机构9
2.6微调机构10
三技术设计11
3.1建立数学模型及参数确定11
3.1.1能耗规律模型12
3.1.2运动学分析模型14
3.1.3动力学分析模型18
3.1.4灵敏度分析模型20
3.1.5参数确定21
3.2零部件设计21
3.3.1小车运动仿真分析23
四小车制作调试及改进23
4.1小车制作流程23
4.2小车调试方法23
4.3小车改进方法24
五评价分析24
5.1小车优缺点24
5.2自动行走比赛时的前行距离估计24
5.3改进方向24
六参考文献25
一绪论
1.1命题主题
本届竞赛命题主题为“无碳小车”。
命题与高校工程训练教学内容相衔接,体现综合性工程能力。
命题内容体现“创新设计能力、制造工艺能力、实际操作能力和工程管理能力”四个方面的要求。
1.2小车功能设计要求
给定一重力势能,根据能量转换原理,设计一种可将该重力势能转换为机械能并可用来驱动小车行走的装置。
该自行小车在前行时能够自动避开赛道上设置的障碍物(每间隔1米,放置一个直径20mm、高200mm的弹性障碍圆棒)。
以小车前行距离的远近、以及避开障碍的多少来综合评定成绩。
给定重力势能为5焦耳(取g=10m/s2),竞赛时统一用质量为1Kg的重块(50×65mm,普通碳钢)铅垂下降来获得,落差500±2mm,重块落下后,须被小车承载并同小车一起运动,不允许掉落。
要求小车前行过程中完成的所有动作所需的能量均由此能量转换获得,不可使用任何其他的能量形式。
小车要求采用三轮结构(1个转向轮,2个驱动轮),具体结构造型以及材料选用均由参赛者自主设计完成。
要求满足:
①小车上面要装载一件外形尺寸为60×20mm的实心圆柱型钢制质量块作为载荷,其质量应不小于750克;在小车行走过程中,载荷不允许掉落。
②转向轮最大外径应不小于30mm。
1.3小车整体设计要求
小车设计过程中需要完成:
机械设计、工艺方案设计、经济成本分析和工程管理方案设计。
命题中的工程管理能力项要求综合考虑材料、加工、制造成本等各方面因素,提出合理的工程规划。
设计能力项要求对参赛作品的设计具有创新性和规范性。
命题中的制造工艺能力项以要求综合运用加工制造工艺知识的能力为主。
1.4小车的设计方法
小车的设计一定要做到目标明确,通过对命题的分析我们得到了比较清晰开阔的设计思路。
作品的设计需要有系统性规范性和创新性。
设计过程中需要综合考虑材料、加工、制造成本等给方面因素。
图一
二方案设计
为了方便设计这里根据小车所要完成的功能将小车划分为五个部分进行模块化设计(车架、原动机构、传动机构、转向机构、行走机构、微调机构)。
图二
在选择方案时应综合考虑功能、材料、加工、制造成本等各方面因素,同时尽量避免直接决策,减少决策时的主观因素,使得选择的方案能够综合最优。
图三
2.1车架
车架不用承受很大的力,精度要求低。
考虑到重量加工成本等,车架采用木材加工制作成三角底板式。
2.2原动机构
原动机构的作用是将重块的重力势能转化为小车的驱动力。
能实现这一功能的方案有多种,就效率和简洁性来看绳轮最优。
小车对原动机构还有其它的具体要求。
1.驱动力适中,不至于小车拐弯时速度过大倾翻,或重块晃动厉害影响行走。
2.到达终点前重块竖直方向的速度要尽可能小,避免对小车过大的冲击。
同时使重块的动能尽可能的转化到驱动小车前进上,如果重块竖直方向的速度较大,重块本身还有较多动能未释放,能量利用率不高。
3.由于不同的场地对轮子的摩擦摩擦可能不一样,在不同的场地小车是需要的动力也不一样。
在调试时也不知道多大的驱动力恰到好处。
因此原动机构还需要能根据不同的需要调整其驱动力。
4.机构简单,效率高。
2.3传动机构
传动机构的功能是把动力和运动传递到转向机构和驱动轮上。
要使小车行驶的更远及按设计的轨道精确地行驶,传动机构必需传递效率高、传动稳定、结构简单重量轻等。
1.不用其它额外的传动装置,直接由动力轴驱动轮子和转向机构,此种方式效率最高、结构最简单。
在不考虑其它条件时这是最优的方式。
2.带轮具有结构简单、传动平稳、价格低廉、缓冲吸震等特点但其效率及传动精度并不高。
不适合本小车设计。
3.齿轮具有效率高、结构紧凑、工作可靠、传动比稳定但价格较高。
因此在第一种方式不能够满足要求的情况下优先考虑使用齿轮传动。
2.4转向机构
转向机构是本小车设计的关键部分,直接决定着小车的功能。
转向机构也同样需要尽可能的减少摩擦耗能,结构简单,零部件已获得等基本条件,同时还需要有特殊的运动特性。
能够将旋转运动转化为满足要求的来回摆动,带动转向轮左右转动从而实现拐弯避障的功能。
能实现该功能的机构有:
凸轮机构+摇杆、曲柄连杆+摇杆、曲柄摇杆、差速转弯等等。
凸轮:
凸轮是具有一定曲线轮廓或凹槽的构件,它运动时,通过高副接触可以使从动件获得连续或不连续的任意预期往复运动。
优点:
只需设计适当的凸轮轮廓,便可使从动件得到任意的预期运动,而且结构简单、紧凑、设计方便;缺点:
凸轮轮廓加工比较困难。
在本小车设计中由于:
凸轮轮廓加工比较困难、尺寸不能够可逆的改变、精度也很难保证、重量较大、效率低能量损失大(滑动摩擦)因此不采用
曲柄连杆+摇杆
优点:
运动副单位面积所受压力较小,且面接触便于润滑,故磨损减小,制造方便,已获得较高精度;两构件之间的接触是靠本身的几何封闭来维系的,它不像凸轮机构有时需利用弹簧等力封闭来保持接触。
缺点:
一般情况下只能近似实现给定的运动规律或运动轨迹,且设计较为复杂;当给定的运动要求较多或较复杂时,需要的构件数和运动副数往往比较多,这样就使机构结构复杂,工作效率降低,不仅发生自锁的可能性增加,而且机构运动规律对制造、安装误差的敏感性增加;机构中做平面复杂运动和作往复运动的构件所长生的惯性力难以平衡,在高速时将引起较大的振动和动载荷,故连杆机构常用于速度较低的场合。
曲柄摇杆
结构较为简单,但和凸轮一样有一个滑动的摩擦副,其效率低。
其急回特性导致难以设计出较好的机构。
差速转弯
差速拐是利用两个偏心轮作为驱动轮,由于两轮子的角速度一样而转动半径不一样,从而使两个轮子的速度不一样,产生了差速。
小车通过差速实现拐弯避障。
差速转弯,是理论上小车能走的最远的设计方案。
和凸轮同样,对轮子的加工精度要求很高,加工出来后也无法根据需要来调整轮子的尺寸。
(由于加工和装配的误差是不可避免的)
综合上面分析我们选择曲柄连杆+摇杆作为小车转向机构的方案。
2.5行走机构
行走机构即为三个轮子,轮子又厚薄之分,大小之别,材料之不同需要综合考虑。
有摩擦理论知道摩擦力矩与正压力的关系为
对于相同的材料为一定值。
而滚动摩擦阻力,所以轮子越大小车受到的阻力越小,因此能够走的更远。
但由于加工问题材料问题安装问题等等具体尺寸需要进一步分析确定。
由于小车是沿着曲线前进的,后轮必定会产生差速。
对于后轮可以采用双轮同步驱动,双轮差速驱动,单轮驱动。
双轮同步驱动必定有轮子会与地面打滑,由于滑动摩擦远比滚动摩擦大会损失大量能量,同时小车前进受到过多的约束,无法确定其轨迹,不能够有效避免碰到障碍。
双轮差速驱动可以避免双轮同步驱动出现的问题,可以通过差速器或单向轴承来实现差速。
差速器涉及到最小能耗原理,能较好的减少摩擦损耗,同时能够实现满足要运动。
单向轴承实现差速的原理是但其中一个轮子速度较大时便成为从动轮,速度较慢的轮子成为主动轮,这样交替变换着。
但由于单向轴承存在侧隙,在主动轮从动轮切换过程中出现误差导致运动不准确,但影响有多大会不会影响小车的功能还需进一步分析。
单轮驱动即只利用一个轮子作为驱动轮,一个为导向轮,另一个为从动轮。
就如一辆自行车外加一个车轮一样。
从动轮与驱动轮间的差速依靠与地面的运动约束确定的。
其效率比利用差速器高,但前进速度不如差速器稳定,传动精度比利用单向轴承高。
综上所述行走机构的轮子应有恰当的尺寸,可以如果有条件可以通过实验来确定实现差速的机构方案,如果规则允许可以采用单轮驱动。
2.6微调机构
一台完整的机器包括:
原动机、传动机、执行机构、控制部分、辅助设备。
微调机构就属于小车的控制部分。
由于前面确定了转向采用曲柄连杆+摇杆方案,由于曲柄连杆机构对于加工误差和装配误差很敏感,因此就必须加上微调机构,对误差进行修正。
这是采用微调机构的原因之一,其二是为了调整小车的轨迹(幅值,周期,方向等),使小车走一条最优的轨迹。
微调机构可以采用下面两种方式微调螺母式、滑块式如图五
图五
由于理论分析与实际情况有差距,只能通过理论分析得出较优的方案而不能得到最优的方案。
因此我们设计了一种机构简单的小车,通过小部分的改动便可以改装成其它方案,再通过试验比较得到最优的小车。
三技术设计
技术设计阶段的目标是完成详细设计确定个零部件的的尺寸。
设计的同时综合考虑材料加工成本等各因素。
3.1建立数学模型及参数确定
通过对小车建立数学模型,可以实现小车的参数化设计和优化设计,提高设计的效率和得到较优的设计方案。
充分发挥计算机在辅助设计中的作用。
3.1.1能耗规律模型
为了简化分析,先不考虑小车内部的能耗机理。
设小车内部的能耗系数为,即小车能量的传递效率为。
小车轮与地面的摩阻系数为,理想情况下认为重块的重力势能都用在小车克服阻力前进上。
则有
为第i个轮子对地面的压力。
为第i个轮子的半径。
为第i个轮子行走的距离
为小车总质量
为了更全面的理解小车的各个参数变化对小车前进距离的变化下面分别从1.轮子与地面的滚动摩阻系数、2.轮子的半径、3.小车的重量、4.小车能量转换效率。
四方面考虑。
通过查阅资料知道一般材料的滚动摩阻系数为0.1-0.8间。
下图为当车轮半径分别为(222mm,70mm)摩阻系数分别为0.3,0.4,0.5.....mm