汽车材料.docx
《汽车材料.docx》由会员分享,可在线阅读,更多相关《汽车材料.docx(7页珍藏版)》请在冰豆网上搜索。
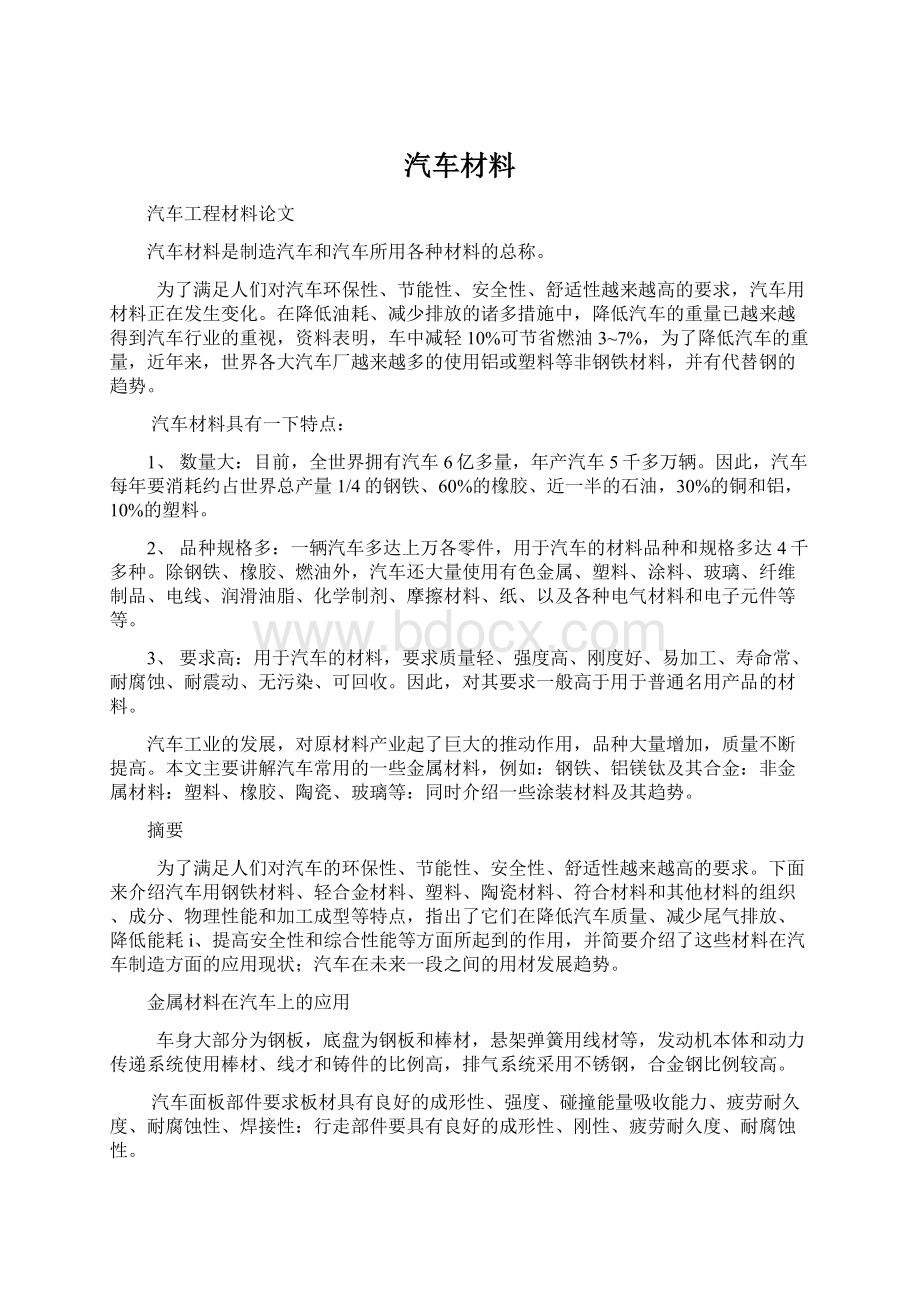
汽车材料
汽车工程材料论文
汽车材料是制造汽车和汽车所用各种材料的总称。
为了满足人们对汽车环保性、节能性、安全性、舒适性越来越高的要求,汽车用材料正在发生变化。
在降低油耗、减少排放的诸多措施中,降低汽车的重量已越来越得到汽车行业的重视,资料表明,车中减轻10%可节省燃油3~7%,为了降低汽车的重量,近年来,世界各大汽车厂越来越多的使用铝或塑料等非钢铁材料,并有代替钢的趋势。
汽车材料具有一下特点:
1、数量大:
目前,全世界拥有汽车6亿多量,年产汽车5千多万辆。
因此,汽车每年要消耗约占世界总产量1/4的钢铁、60%的橡胶、近一半的石油,30%的铜和铝,10%的塑料。
2、品种规格多:
一辆汽车多达上万各零件,用于汽车的材料品种和规格多达4千多种。
除钢铁、橡胶、燃油外,汽车还大量使用有色金属、塑料、涂料、玻璃、纤维制品、电线、润滑油脂、化学制剂、摩擦材料、纸、以及各种电气材料和电子元件等等。
3、要求高:
用于汽车的材料,要求质量轻、强度高、刚度好、易加工、寿命常、耐腐蚀、耐震动、无污染、可回收。
因此,对其要求一般高于用于普通名用产品的材料。
汽车工业的发展,对原材料产业起了巨大的推动作用,品种大量增加,质量不断提高。
本文主要讲解汽车常用的一些金属材料,例如:
钢铁、铝镁钛及其合金:
非金属材料:
塑料、橡胶、陶瓷、玻璃等:
同时介绍一些涂装材料及其趋势。
摘要
为了满足人们对汽车的环保性、节能性、安全性、舒适性越来越高的要求。
下面来介绍汽车用钢铁材料、轻合金材料、塑料、陶瓷材料、符合材料和其他材料的组织、成分、物理性能和加工成型等特点,指出了它们在降低汽车质量、减少尾气排放、降低能耗i、提高安全性和综合性能等方面所起到的作用,并简要介绍了这些材料在汽车制造方面的应用现状;汽车在未来一段之间的用材发展趋势。
金属材料在汽车上的应用
车身大部分为钢板,底盘为钢板和棒材,悬架弹簧用线材等,发动机本体和动力传递系统使用棒材、线才和铸件的比例高,排气系统采用不锈钢,合金钢比例较高。
汽车面板部件要求板材具有良好的成形性、强度、碰撞能量吸收能力、疲劳耐久度、耐腐蚀性、焊接性:
行走部件要具有良好的成形性、刚性、疲劳耐久度、耐腐蚀性。
从生产工艺特点划分为热轧钢板、冷轧钢板和涂镀层钢板。
从强度角度可忽而分为:
普通钢板、低合金高强度钢板、普通高强度钢板、和先进高强度钢板等。
近来汽车生产中铝等轻质材料不断增加,但是高强度钢,镀锌薄钢板,超细晶粒钢,不锈钢还是占据着不可替代的地位。
刚强度钢相对普通钢来说具有高强度、质量轻、成本低、安全性能高等。
镀锌薄钢板具有良好的抗腐蚀能力、是通过冷轧钢——加热——冷却至镀锌温度——镀锌——冷却——矫直。
超细晶粒钢具有优良的抗疲劳性能、较高的强度以及良好的低温韧性等优点。
不锈钢与普通钢相比,其高温强度大,抗腐蚀性好,密度小,能减少车身质量的45%,成型过程简单,节省加工费用。
铝及其合金在汽车上的应用
铝具有优良的塑造性,铸造方法多,声产效力高。
主要用与发动机部件、离合器壳体、后桥壳、转向器壳体、变速器壳体、正时齿轮体:
也可用于制造保险杠、车轮、发动机框架、转向节液压泵总成、刹车箝等部件。
形变铝合金与铸造铝合金相比,强度、韧性都大优优势。
在汽车上主要用于制造发动机罩、保险杠、消声罩、防抱死制动系统、热交换器、车身构架、作为、车厢地板等零部件。
且铝的导热性约高于铸铁的3倍,因此最适合制造散热器,这也是铝活塞所要求的特征。
国外采用铝合金制造汽车零部件的例子┌───┬──────────────────────────┐│国别│用铝合金制造的汽车零部件│├───┼──────────────────────────┤│日本│气缸体,气缸盖,离合器壳,车轮盘,进气管,变速器壳│├───┼──────────────────────────┤│俄罗斯│气缸体,气缸盖,正时齿轮盖,活塞,挺杆,摇臂军,油底│││壳,机油泵壳体│├───┼──────────────────────────┤│法国│气缸盖,进气管,离合器壳,变速器壳,活塞,盘式制动器│││壳,制动效,万向节又,车轮盘│├───┼──────────────────────────┤│美国│气缸盖,离合器壳,水泵壳,转向器壳,主制动缸壳,进气│││管,活塞,车轮悬架│├───┼──────────────────────────┤│意大利│气缸盖,变速器壳体,进气管,离合器壳,气缸体,活塞,│││车轮盘│├───┼──────────────────────────┤│德国│气缸体,气缸盖,化油器壳体,方向盘,悬臂架,制动鼓│││(镶嵌铸铁社香)│├───┼──────────────────────────┤│美国│气缸盖,进气管,气缸体│└───┴──────────────────────────┘ 铝合金材料在国产汽车上的应用还较少,我国与欧美、日等发达国家相比差距较大。
国内产量最大的几种载货车如解放、东风、南京跃进等每辆车上铝铸件的总重均不超过1Okg。
据统计,国外交通运输业铝合金消耗水平为铝产量的26%,而我国仅为5.7%。
9O年代国外每辆车平均用铝量达130kg,而我国目前生产的轿车最高用铝量仅55kg/辆,由此看来,我国汽车制造业在扩大铝合金的应用方面还有很大潜力可挖。
三、常用铸铝汽车零件及其铸造工艺 3.1气缸体 气缸体是发动机中最大的零件,也是最复杂的零件。
采用铝合金代替铸铁制造气缸体的最大优点是使发动机重量大大减轻。
如美国通用汽车公司VS发动机气缸体采用铸铁时重量为94.4kg,而采用铝合金后重量仅为24.5kg,采用铸铁和铸铝的重量之比为3.9:
1。
早期铝气缸体的生产工艺一般采用低压铸造工艺和金属型铸造工艺,也有少量采用砂型铸造工艺。
从近年来的倾向看,采用高压压铸工艺生产铝气缸体的厂家居多数。
目前国内使用铝合金缸体的是Q492汽油发动机,其铸造方法仍是采用低压铸造工艺。
过去在较长一段时间里,铝气缸体并不像铝气缸盖那样被广泛采用,原因是铝气缸体的成本比铸铁气缸体的成本高,且通常使用的铝合金材料在某些性能方面(如耐磨性)也不如铸铁好。
随着能源需求和环保的要求导致追求车辆轻量化成为一种观念之后,人们才认识到采用铝合金代替铸铁制造气缸体是一种必然趋势。
同时,铝合金材料技术也在不断进步,一批性能优异的铝合金开始用于生产,如美国雷诺金属公司研制的39O合金。
另一方面,铝铸件制造技术的发展使得大批量生产铝气缸体的成本费用也在不断下降。
目前铸铝气缸体的应用已十分广泛,在现代轿车中的应用已经到了普及阶段。
3.2气缸盖 现代设计的轿车发动机缸盖都是用铝合金制造的。
气缸盖在发动机中的工作特点是处于高温状态下工作,承受较大的热冲击和产生应力集中。
采用铝合金制造气缸盖的优点除了重量轻以外,还有一个突出的优点就是导热性好。
对于轿车、轻型车发动机来说,使用铝合金气缸盖可以使发动机热效率更好,避免缸盖燃烧室中的零件产生过热现象。
由于气缸盖是一种内腔结构复杂、壁厚又不均匀的铸件,且缸盖内腔还有压力密封性要求,给铸造工艺带来一定困难。
传统上铝气缸盖铸造方法多采用金属型铸造工艺和低压铸造工艺,8O年代以来出现了两种新颖的铸造工艺——气化模铸造工艺和砂型低压铸造工艺,特别是气化模实型铸造工艺很适于气缸盖、进气管这类内腔复杂,需要砂芯成型的铸件。
该工艺与传统工艺相比有许多特点:
不分型、不起模、不使用砂芯、铸件容易清理、铸件表面光洁、尺寸精度高、适用于大批量生产。
镁合金在汽车上的应用
镁的优点是刚性好,质量轻;低的融化粘滞性和良好的填住成型;可回收利用;可大规模生产;储量丰富。
适用于离合器外壳、引擎阀罩壳、变速箱外壳、变速箱上盖、发动机罩盖、方向盘、座椅支架等。
1.首先是镁合金的价格回归到有竞争力的水平。
目前镁价格已经处于合理区间并在2009以来保持相对稳定。
2.中国对汽车油耗的管理正趋于严格。
国家《第三阶段乘用车燃料消耗量评价方法及指标》标准即将于今年公布。
据了解,第三阶段标准制定的油耗限值比第二阶段下降20%。
到2015年,全国平均乘用车燃油消耗量将降为7L左右。
与前两个阶段最大的不同是,第三阶段标准不再以单一车型为评价对象,而是将汽车企业作为整体进行评价。
这与美国CAFE(公司平均燃料经济性)法有些类似。
汽车企业将会更加重视轻量化。
3.新能源汽车将会是中国汽车业发展的重点,对轻量化要求更高。
4.中国汽车轻量化有很大潜力:
自主轿车平均比发达国家同类轿车重8%-10%,相同自重下,安全性差2-3个等级;商用车平均重10%-15%。
。
5.2010年1-3月,中国汽车产量455.45万辆,同比增长76.99%预计全年产量达到1500万辆。
根据规划,2015年汽车总产量达到2500万辆,摩托车产量达到3800万辆。
6.中国自主品牌的汽车产量正在逐步增加,乘用车自主品牌达到180个,2009年已经达到乘用车总产量的44%。
据尚轻时代调查,国内主要的汽车企业都已经采用镁合金零部件,并制订了未来扩大用镁合金的发展计划。
例如:
奇瑞汽车:
5年内单车用镁合金力争达到30Kg。
GMAC)建有铝合金、镁合金、高压铸造生产线,镁铝回收熔化生产线,年生产能力达到120万汽车零部件压铸件。
东风汽车:
已经开发应用了车身、底盘、变速箱、发动机、大型复杂类等多类25种镁合金部品。
随着镁合金价格回落,镁合金部品的生产已经逐步恢复。
长安汽车:
已成功开发出10个全新镁合金汽车零部件,并集成应用在自主品牌轿车上,实现单车最大用镁量超过20千克,
一汽集团:
已经形成1500吨/年镁合金压铸生产能力。
加入稀土生产新型耐热压铸镁合金。
已经开发并生产出10多种镁合金部件。
钛合金在汽车上的应用
钛合金属于新型结构材料。
具有优异的综合性能,密度小,比断韧性断强度高,抗腐蚀性能优异,在高温下能保持较高的强度。
用于制造汽车可以减轻汽车发动机的质量、提高汽车车速、降低平均油耗,在改善发动机性能上有很大优势。
钛合金是一种新型结构及功能材料,它具有优异的综合性能,密度小,比强度高。
WWW.cnmN.COM.Cn。
钛的密度为4.51g/cm3,介于铝(2.7g/cm3)和铁(7.6g/cm3)之间。
WWW.cnmN.COM.Cn。
钛合金的比强度高于铝合金和钢,韧性也与钢铁相当。
WWW.cnmN.COM.Cn。
钛及钛合金抗蚀性能好,优于不锈钢,特别是在海洋大气环境中抵抗氯离子的侵蚀和微氧化气氛下耐蚀性好,钛合金的工作温度较宽,低温钛合金在-253℃还能保持良好的塑性,而耐热钛合金的工作温度可达550℃左右,其耐热性明显高于铝合金和镁合金。
WWW.cnmN.COM.Cn。
同时具有良好的加工性、焊接性能。
钛在汽车上的用途主要分两大类,第一类是用来减少内燃机往复运动件的质量(对作往复运动的内燃机零件来讲,即使减少几克质量都是重要的);第二类是用来减少汽车总质量。
WWW.cnmN.COM.Cn。
根据设计和材料特性,钛在新一代汽车上主要分布在发动机元件和底盘部件上。
WWW.cnmN.COM.Cn。
在发动机系统,钛可制作阀门、阀簧、阀簧承座和连杆等部件;在底盘部件主要为弹簧、排气系统、半轴和紧固件等。
WWW.cnmN.COM.Cn。
据资料介绍,除了上述所举重点外,还有:
发动机部件的摇臂、悬簧、活塞销、涡轮增压器转子、紧固件、挂耳螺帽、车挡支架、门突入梁、制动器卡钳活塞、销轴栓、离合器圆板、压力板、变速按钮等等。
WWW.cnmN.COM.Cn。
降低钛合金成本的途径
尽管钛及钛合金早在上个世纪50年代就进入了汽车制造领域,但发展比较缓慢,其原因主要是价格因素,为了满足汽车行业用钛,钛工业者在熔炼、加工,制造等方面进行了大量的工作。
WWW.cnmN.COM.Cn。
以满足汽车业的需求。
WWW.cnmN.COM.Cn。
钛金属熔点高,化学性质十分活泼,与O、H、N、C等元素有极强的化学亲和力,致使纯钛提取困难。
WWW.cnmN.COM.Cn。
工业上普遍使用的Kroll镁还原法生产海绵钛。
WWW.cnmN.COM.Cn。
Kroll镁还原法生产海绵钛工艺复杂,能耗高,周期长,并且不能连续生产,同时需用大量的金属镁作还原剂,生产成本较高。
WWW.cnmN.COM.Cn。
钛合金价格高的另一个原因是合金化元素价格较高。
WWW.cnmN.COM.Cn。
随着钛冶炼技术的进步,将钛在生产、加工过程中所产生的边角余料、废屑等残料经系列处理后作为炉料添加,实现循环生产,是降低原材料成本有效方法。
WWW.cnmN.COM.Cn。
实践表明,每利用1%的残钛,可使钛锭生产成本降低0.8%。
WWW.cnmN.COM.Cn。
如果采用电子束冷床炉、等离子束冷床炉进行熔炼,不仅可以改善钛锭的冶金质量,同时可以大量使用回收炉料,有效降低铸锭成本。
WWW.cnmN.COM.Cn。
汽车玻璃
汽车玻璃是汽车本身附件必不可少的,主要起防护作用。
目前汽车玻璃以夹层钢化玻璃和夹层区域钢化玻璃为主,能承受较强是冲击力。
阻断玻璃主要包括UV吸收剂涂焱剂、UV吸收剂本体型,可有效减少车内空调制冷的负荷。
还有电热风扇玻璃是组合玻璃车内测的玻璃表面被附透明的导电膜所构成的玻璃;隐蔽玻璃、憎水性玻璃、访腐玻璃、组合玻璃、双层窗玻璃等。
夹层玻璃是由两层或两层以上的玻璃用一层或数层透明的粘结材料粘合而成的玻璃制品。
高抗冲击强度,受冲击后,脆性的玻璃破碎,但由于它和有弹性的PVB相结合,使夹层玻璃具有高的抗穿透能力,仍能保持能见度。
粘结力高,玻璃与PVB粘结力高,当玻璃破碎后,玻璃碎片仍然粘在PVB上不剥落,不伤人,具有安全性。
耐光、耐热、耐湿、耐寒。
汽车橡胶
橡胶是是高弹性的高分子化合物。
分为天然橡胶和合成橡胶两种。
主要应用于轮胎类——外胎、内胎、垫带、气门芯;密封胶条类——门窗胶条、门窗玻璃胶条、风窗玻璃胶条;管路类——发动机进气管、发动机进水管、发动机燃油管;传动类——发动机风扇水泵皮带、空调压缩机皮带;减震类——车架减震胶条、散热器减震带、变速器减震垫、操作件防尘罩等。
表面光洁美观、无接痕。
具有良好的弹性和抗压缩变形性,耐老化性能优异。
阻燃性能优异,低烟、低毒。
产品挤出稳定,尺寸精度高。
在胶管保护套方便,他们的产品光泽度、硬度、耐磨、耐酸碱、耐油、抗冲击等。
主要用作轮胎、门窗密封条、胶管、减振制品、防尘罩、胶带、油封、皮碗、皮膜等。
同时,诸如密封、胶管、胶带等在其他交通运输工具中也有广泛的应用。
此处仅以橡胶在汽车工业中的应用为例进行介绍。
橡胶占汽车用材料总质量的5%,每辆车上多达400~500个橡胶件。
随着环保和汽车多样化,橡胶的再生利用、耐热性以及进一步降低成本已成为汽车橡胶发展的主要课题。
新型弹性体材料,如热塑性弹性体、高饱和丁腈橡胶在汽车上取得了长足的发展,其在汽车上用量已占汽车橡胶总消耗量的20~50%(除轮胎)。
汽车上大量使用氟胶、硅胶、丙烯酸酯橡胶等高档胶和耐热弹性体仍是汽车橡胶发展的主流方向。
我国汽车工业对橡胶材料的需求量。
汽车轮胎方面,橡胶材料的使用目标为进一步推广汽车轮胎子午化,西欧已全部实现轮胎子午化,而我国子午化水平仅为40%。
随着轮胎使用条件的提高,冬季防滑轮胎、超低滚动阻力轮胎、安全轮胎、双胎面花纹轮胎将进一步得到推广应用,其发展方向是节能、高速、稳定、轻量化、耐久性。
为了节能,橡胶材料应具有滚动阻力小即高反弹性,然而轮胎高速稳定性却要求材料具有高耐蠕变即低反弹性,因此最近开发的末端改性的S-SBR材料有可能满足上述矛盾的性能要求。
一般来说,胎面使用E-SBR、S-SBR、NR、异戊橡胶IR、胎体使用NR、聚丁二烯橡胶BR、IR等胶。
节能性和安全性较好的硅橡胶和S-SBR胶配合的轮胎材料也在研究开发中。
汽车密封制品占汽车橡胶件质量的25~28%(除轮胎)。
近来,具有耐臭氧、耐气候老化的EPDM胶广泛用于制造汽车门窗密封条,并逐步取代传统的NR和CR胶。
每辆轿车上平均使用40m长的各种密封条。
由于热塑性弹性体材料具有着色和再生利用方便的特点,同时为了降低成本和保持美观,国内外厂商开始使用热塑性弹性体材料制造汽车门窗密封条。
汽车工业中油封材料多用丁腈、氢化丁腈、丙烯酸酯橡胶耐油材料。
由于耐热性能的提高,特殊橡胶如对氟橡胶的要求和品种日益扩大。
陶瓷材料
陶瓷是以粘土为主要原料以及各种天然矿物质经过粉碎混炼、成型和煅烧制的。
汽车上使用智能陶瓷产品,包括功能材料、驱动系统与反馈系统相结合的智能材料系统或结构。
有汽车减震装置、汽车智能雨刷、汽车有源消声陶瓷材料。
汽车发动机,过去都用合金钢制造,汽缸工作温度只有1000℃左右,而且还要用水冷却。
汽缸的活塞销,由于耐高温摩擦性能较差,压缩效率下降较快,因而成了新型汽车工业的拦路虎。
1980年日本五十铃汽车公司采用氮化硼陶瓷汽车发动机(DE),这种新型发动机的温度可达到1300℃~1500℃,不要水冷却,再加上它的密度只有钢的一半(钢为7.9,氮化硅为3.2),所以,汽车重量减轻。
它不仅可节省30%的热能,而且工作效率提高了15%~20%。
陶瓷DE是在燃烧室和活塞的部分表面用比金属更加耐热的陶瓷材料,从而提高了零部件的耐热性,进一步简化了冷却系统,除可减少冷却损失,提高热效率外,还可使DE更加紧促,使自身重量减轻。
将来会出现副燃烧室、活塞头、汽缸衬套、汽缸头、增压转子等陶瓷部件与零件。
这些部位可以采用氮化硅结合碳化硅或部分稳定氧化锆等特种陶瓷材料。
机械强度则必须达到抗折强度为500MPa以上,热膨胀系数≤3.5*10-6/℃。
上述陶瓷材料基本上即能满足这些要求。
尤其是部分稳定氧化锆陶瓷不仅强度高达1000MPa,而且热导率也比其它材料低很多。
在燃气涡轮发动机方面,家用轿车为实现与柴油机同量的燃烧费用,涡轮进口温度要高达1350℃,而可以忍耐这一高温的只有碳化硅及氮化硅陶瓷材料。
目前,汽车与材料专家们都对碳化硅与氮化硅材料寄予厚望,并确认将来汽车涡轮的转子、定子使用上述特种陶瓷材料最为理想。
用陶瓷材料作结构主体的陶瓷发动机的实用化,促进汽车的轻量化和小型化。
预计2014年,陶瓷汽车发动机投入批量生产。
陶瓷制动器,陶瓷制动器在碳纤维制动器的基础上制造而成。
一块碳纤维制动碟,最初由碳纤维和树脂构成,它被机器压制成型,碟片表面会有规则的小孔,背面是螺旋发散线状的沟槽,用于散热。
压制成型之后,趁着碟片仍有一定温度,马上被送入高温炉,高温定型。
炉膛内充满氮气,温度接近1000℃,在这种情况下,所有非碳有机物都将转化成碳,因此这道工序也叫碳化。
尽管碳化工序后,炉膛的温度继续提升至1420℃,此时碳蝶会表现出强大的“亲和力”,甚至能够吸收液化的硅,当它冷却之后,得到的硅碳化物表面,硬度甚至接近钻石。
碟片内的碳纤维结构使它坚固耐冲击,而坚硬耐腐蚀的的材质,也让碟片极为耐磨。
据测算,一副陶瓷制动碟,能用上30万公里。
在2001年奔驰SLR概念车就采用了一项当时最新的主动安全系统——陶瓷刹车盘。
这种刹车盘不会因水浸而降低性能,而且减速非常快,即使是像SLR这样动力巨大的车,都被它管束得服服帖帖,而且刹车过程还很均匀,绝不突然,让人有理由相信这种新技术前景广阔。
SLR的前刹车卡钳是名厂“布伦博”的8活塞式,同样也是新产品。
2001年奔驰新款敞篷SL系列跑车将率先采用质轻而坚固的陶瓷刹车盘,奔驰计划达到制动系列行使10万公里以上免维护的目标。
保时捷的陶瓷制动系统(PCCB),其制动碟表面的摩擦系数在制动初段比铸铁高25%,这样在急刹车时,车子无需额外的制动辅助技术,单靠制动器便能迅速提供充足的制动力。
陶瓷制动器采用6活塞的制动卡钳,在活塞与制动片之间,装有陶瓷隔热体,用以防止制动时产生的高热传入液压组件和制动液,这套刹车系统更可以在800℃高温下正常工作。
什么是陶瓷发动机
在传统柴油机或燃气轮机用的金属零件中,铝合金的耐温极限为350℃,钢和铸铁的为450℃,最好的超级耐热合金的耐温极限也不能超过1093℃。
金属材料的上述耐温极限大大限制了发动机的工作温度(热效率)。
而使用各种冷却装置又使发动机设计复杂,增加重量和耗费许多功率。
长期以来,人们在寻觅用一种理想的材料来代替发动机用的金属材料。
发动机用材料的重大改革则是用高性能陶瓷零件逐步代替金属零件,直至发动机的主要零件,这就是人们常说的陶瓷发动机。
高性能陶瓷有许多优于金属的性能,例如耐高温、耐磨损、耐腐蚀、重量轻和隔热性能好。
这些特殊性能可使传统发动机面临的热效率低和结构复杂等许多难题得到合理解决,并提高发动机的性能和耐久性。
因此,有专家认为,高性能陶瓷是自内燃机发明以来最鼓舞人心的新发展,它将最终解决发动机要在苛刻环境下工作的问题。
21世纪,将会出现许多陶瓷发动机。
最初,人们研究和使用的是陶瓷涂层和单一整体陶瓷制的发动机零件。
陶瓷涂层技术成熟、成本低、寿命较高,采用等离子喷涂工艺,可涂覆二氧化锆、碳化钛和二氧化钛等陶瓷,获得1毫米以内的耐久涂层。
为了解决陶瓷涂层太薄的问题,人们研究用二氧化锆、氮化硅、碳化硅和钛酸铝制造发动机的整体陶瓷零件。
此外,还研究了玻璃瓷、氧化铝等整体陶瓷件。
塑料
塑料是一种高分子材料,主要应用与前照面、保险杠、发动机罩、行李箱罩、顶盖一些车身骨架构建。
有众多优点——质量轻、成型容易、缓冲能力强、耐腐蚀性强、改变内外饰。
汽车工业的发展离不开汽车塑料化的进程,目前我国工程塑料自给率不足16%。
据中国工程塑料协会估计,2010年自给率约为10%汽车行业是聚丙烯(PP)最大用户。
聚丙烯用于汽车工业具有较强竞争力,但因其模量和耐热性较低,冲击强度较差,因此不能直接用作汽车配件材料,轿车中使用的均为改性聚丙烯产品,其耐热性可由80℃提高到145℃~150℃,并能承受一定时间的持续高温。
据报道,日本丰田公司推出的新一代聚丙烯HEHCPP产品,可作为汽车仪表板、保险杠,比以TPO(聚烯烃热塑性弹性体)为原料的同类产品成本降低30%,改性聚丙烯用作汽车配件材料来源具有十分广阔的开发前景。
汽车行业证券分析师比较看好改性塑料。
“改性塑料是塑料制品行业中附加值最高的一类产品。
”国内改性塑料行业处于起步阶段,发展前景广阔。
业内人士称,在高端塑料制品领域,国内企业的主要瓶颈在于技术水平跟不上,产能较小。
与改性塑料相关的上市公司有普利特、金发科技(600143)等。
普利特的改性塑料基本为车用。
尽管今年汽车销量增速与去年相比有所放缓,不过这不会影响到车用改性塑料的下游需求。
汽车产量的增加和汽车轻量化发展趋势都在刺激汽车改性塑料产品需求的增加。
国外汽车重量的20%源于改性塑料,而国内的比例是11%。
金发科技是国内产品最齐全、产量最大的改性塑料生产企业,公司的销售收入中约40%来自家电、25%来自汽车。
汽车轻量化,使包括聚丙烯、聚氨酯、聚氯乙烯、热固性复合材料、ABS、尼龙和聚乙烯等在内的塑材市场得以迅速放大。
近两年,车用塑料的最大品种聚丙烯,每年都在高速增长。