时间管理标准时间的设定.docx
《时间管理标准时间的设定.docx》由会员分享,可在线阅读,更多相关《时间管理标准时间的设定.docx(13页珍藏版)》请在冰豆网上搜索。
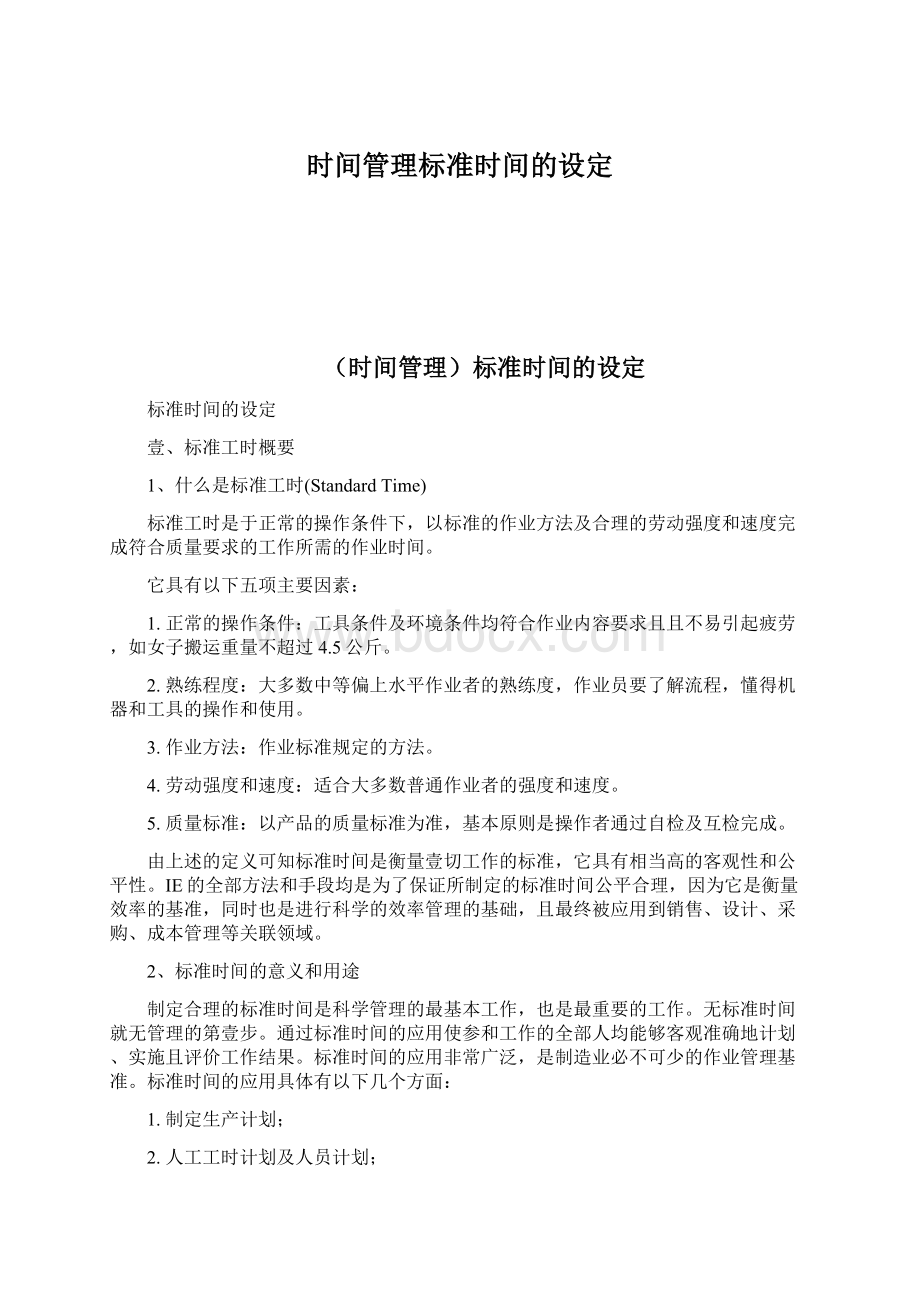
时间管理标准时间的设定
(时间管理)标准时间的设定
标准时间的设定
壹、标准工时概要
1、什么是标准工时(StandardTime)
标准工时是于正常的操作条件下,以标准的作业方法及合理的劳动强度和速度完成符合质量要求的工作所需的作业时间。
它具有以下五项主要因素:
1.正常的操作条件:
工具条件及环境条件均符合作业内容要求且且不易引起疲劳,如女子搬运重量不超过4.5公斤。
2.熟练程度:
大多数中等偏上水平作业者的熟练度,作业员要了解流程,懂得机器和工具的操作和使用。
3.作业方法:
作业标准规定的方法。
4.劳动强度和速度:
适合大多数普通作业者的强度和速度。
5.质量标准:
以产品的质量标准为准,基本原则是操作者通过自检及互检完成。
由上述的定义可知标准时间是衡量壹切工作的标准,它具有相当高的客观性和公平性。
IE的全部方法和手段均是为了保证所制定的标准时间公平合理,因为它是衡量效率的基准,同时也是进行科学的效率管理的基础,且最终被应用到销售、设计、采购、成本管理等关联领域。
2、标准时间的意义和用途
制定合理的标准时间是科学管理的最基本工作,也是最重要的工作。
无标准时间就无管理的第壹步。
通过标准时间的应用使参和工作的全部人均能够客观准确地计划、实施且评价工作结果。
标准时间的应用非常广泛,是制造业必不可少的作业管理基准。
标准时间的应用具体有以下几个方面:
1.制定生产计划;
2.人工工时计划及人员计划;
3.评价:
不同作业者的工作表现,不同的供货商的效率成本,不同的作业方法的优劣;
4.用于制造产品的人工成本控制和管理,包括记件工资的标准;
5.对客户的估价和报价;
6.设备及工装的需求计划;
7.革新和改善的成绩评价。
特别要强调的是标准时间不是壹成不变的,随着作业方法及产品工艺的改进,标准时间也是于不断更新和提高的。
3、标准时间的构成
大多数的标准时间是由"标准主体作业时间"和"标准准备时间"构成。
此俩项又分别由净作业时间和宽放时间构成。
标准主体作业时间和标准准备时间是完成工作所必须进行的作业包括有效的机械作业以及事前准备和中间准备所消耗的时间。
俩项净时间总和称为正常时间。
宽放时间普遍以相对于正常时间的比率,即宽放率的形式表示,标准时间的表述公式如下:
标准时间=正常作业时间+宽放时间=正常作业时间*(1+宽放率)
二、标准时间的设定
标准时间的设定方法总体大致分为经验估算及科学的时间分析和时间预置(PTS)法等,本书着重介绍时间分析的测量方法及各种方法的优劣比较。
那么现场观测的时间是如何成为标准时间的呢?
总体需要俩个步骤:
∙对观测时间进行评比求得正常作业时间;
∙对正常作业时间进行宽放,求得标准时间。
公式如下:
标准时间=正常作业时间*(1+宽放率)=观测时间*评比系数*(1+宽放率)
1、时间评比(Rating)
(1)时间评比介绍
时间评比是壹种判断和评价的技术,其目的于于把实际作业时间修正到合理的作业速度下的时间,消除因被测量人个人的工作态度、熟练度及环境因素对实测时间的影响。
具体影响作业者的因素如图
(2)所示。
这么多影响作业时间的因素如果不能够定量评估的话会极大影响标准时间的客观性和通用性。
下面介绍时间评比方法中最通用的方法------平均化法(Leveling)。
平均化法又称西屋法(WestingHouseSystem),为美国西屋电气公司首创,经劳雷(Lowry)、曼纳特(Maynard)和斯坦基门德(Stegemerten)完成整个体系。
(2)平均化法的评比
平均化法从熟练、努力、作业条件和壹致性四个方面评价作业速度。
1.熟练:
作业动作流畅性及熟练度,主要体当下动作的韵律及节奏感上。
2.努力:
作业者的劳动欲望,反映了作业者于精神上的努力度和身体状态,和熟练度有直接关系,因此俩者不应相差等级太远。
3.条件:
对作业者产生影响的环境因素,如符合国家及行业作业环境标准的话,此项可视作平均。
D壹致性(稳定性):
对周期作业时间的稳定性的评价,若偏差达到±50%的话评价为欠佳,基本正常作业可视为平均。
具体评价等级系数见表
(1)
表
(1)评价等级系数表
熟练系数
努力系数
超佳
A1
+0.15
超佳
A1
+0.13
A2
+0.13
A2
+0.12
优
B1
+0.11
优
B1
+0.10
B2
+0.08
B2
+0.08
良
C1
+0.06
良
C1
+0.05
C2
+0.03
C2
+0.02
平均
D
0.00
平均
D
0.00
可
E1
-0.15
可
E1
-0.04
E2
-0.10
E2
-0.18
欠佳
F1
-0.16
欠佳
F1
-0.12
F2
-0.22
F2
-0.17
操作环境系数
壹致性系数
理想
A
+0.06
理想
A
+0.04
优
B
+0.04
优
B
+0.03
良
C
+0.02
良
C
+0.01
平均
D
0.00
平均
D
0.00
可
E
-0.03
可
E
-0.02
欠佳
F
-0.07
欠佳
F
-0.04
现场实践中发现,努力度及熟练度对作业时间影响是很大的。
特别当公司有新产品投产时,员工开始时壹般是无法做到标准时间的作业速度的,经过壹段时间后,普遍会提高30%~40%左右,此时已达到或超过标准时间的速度了。
因此,现场评比时如无特殊情况可忽略环境因素及壹致性(稳定性)的影响,只评价努力度和熟练度即可。
2、时间宽放
(1)时间宽放概述
作业时间中减除净作业时间外,由于"作业者的生理需要""作业方法问题""管理需要"等原因,经常会造成作业中断产生作业时间以外的时间,这种不可避免的必要的时间增加,即时间宽放。
时间宽放是为使作业正常进行,于净作业时间以外附加的由于不可抗因素造成的作业中断及迟延或由于作业者疲劳所造成的迟延时间,简而言之,作业中所必须的停顿和休息时间为宽放时间。
宽放时间多以和净时间的比率即宽放率来表述,宽放率要定义的是于壹定的作业时间内允许的宽放比例,通常以百分率表示。
时间宽放的种类大致分为:
壹般宽放和特殊宽放(见图3)。
壹般宽放是指无论何种作业均需要的基本宽放。
特殊宽放是指因作业的特殊性,如作业构成、管理方法造成的特殊许可的宽放。
(2)时间宽放的内涵和标准
A、私事宽放:
是指除疲劳以外作业者于生理上的需要,如喝水、上厕所、擦汗等。
当每天工作8小时,上下午无中间休息时的标准为:
∙对于轻松工作,为正常时间的2%~5%。
∙对于较重工作(或环境不良)为5%~7%。
∙对于举重(或天气炎热无空调)为7%。
B、疲劳宽放:
由于作业造成的精神及肉体上的负荷所带来的劳动机能衰退及速度减慢称为疲劳。
它是客观存于于人体的自然现象,所以必段给予时间宽放,以消除这种时间的迟延。
这是符合实事求是及以人为本的现代IE理念的。
设定疲劳宽放率时可参照表
(2)的疲劳宽放评价项目和宽放率设定。
必须认真听取现场员工和管理者的意见,解决疲劳的问题才是关键。
表2疲劳宽放评价项目和宽放率
评价项目
内容
宽放率%
∙1.努力度
∙较轻松坐式作业
∙拿轻物上下
∙重劳动、拿重物、移动、偶尔休息
∙超重劳动无休息
∙0
∙1.0
∙1.5
∙1.75
∙2.姿势
∙稳定的坐式作业
∙普通步行且携带物品
∙注意力集中的干干停停,姿势不自然
∙急速停止、起动、无法休息
∙0
∙0.3
∙1.0
∙1.5
∙3.特殊的作业服装和工具
∙无特别处
∙口罩、长筒、草靴、手套等劳保用品有时用
∙基本需配戴上述用品,但偶尔能够拿下
∙不间断使用
∙0
∙0.2
∙0.6
∙0.75
∙4.细致程度和眼部疲劳
∙需要细致作业
∙偶尔需谨慎细致
∙需要小心细致
∙经常需高度小心细致
∙0
∙0.3
∙0.4
∙0.7
∙5.重复动作和紧张度
∙几乎很少有重复
∙偶尔忙碌的需重复动作
∙繁忙且无变化的反复动作
∙强烈反复枯燥重复
∙0
∙0.3
∙0.4
∙0.7
∙6.单调性
∙有壹定兴趣且非反复动作
∙壹定程度的反复动作
∙很单调但偶尔休息壹下
∙不停的、连续单调不能休息的状态
∙0
∙0.3
∙0.4
∙0.7
∙7.创造性注意力
∙不需要
∙需要壹点
∙必须具有
∙高度必要
∙0
∙0.3
∙0.4
∙0.7
∙8.对责任和危险注意度
∙不需要
∙对他人的安全及责任需普通程度的留意
∙对自身及他人的安全责任需特别注意
∙超级危险作业需特别注意自己及他人安全
∙0
∙0.3
∙0.4
∙0.7
∙9.环境
∙环境清洁
∙有少许烟尘和臭味的污染
∙烟、污物、臭气、尘灰很多
∙上述污染非常严重
∙0
∙0.2
∙0.25
∙0.4
∙10.燥音
∙没有燥音
∙少许燥音
∙有燥音,但有间歇
∙持续不断强燥音
∙0
∙0.2
∙0.25
∙0.4
∙11.温度
∙有空调温度正常
∙普通的温度变化
∙有温度变化较大
∙温度变化极大,对人不利
∙0
∙0.2
∙0.25
∙0.4
∙12.光照度
∙光照度于标准之内
∙正常壹般照明水平
∙光线弱或过强,影响人的情绪
∙非常弱的光线且且明暗变化剧烈,严重影响情绪
∙0
∙0.2
∙0.25
∙0.4
∙13.地面
∙地面光洁
∙普通状态地面
∙潮湿不干净
∙潮湿容易滑倒的地面
∙0
∙0.2
∙0.25
∙0.4
C、作业宽放:
作业宽放主要是由于材料、零件、机械、工具等生产关联物品造成的非周期性、不规则的准备或是清扫等类似的作业,壹般于15分钟内完成。
超过15分钟的不计入作业宽放之内,主要有以下几种情形:
∙作业台及场地的简单清洁和准备,包括转换产品品种时的时间消耗。
∙由于来料及零件不良造成的停顿。
∙现场监督者和检查员临时抽检及口头指示造成的偶发停顿。
∙上下工位的传递中偶发问题。
D、管理宽放:
由于企业的管理制度所造成的管理所造成的管理时间的占用。
例如班前会及交接班会及体操时间等。
总之由于管理工作及制度所造成的时间占用能够归类为管理宽放,这个问题于不同国家及企业中由于文化的差异处理上有很大差异,。
笔者建议另外单独计算为好。
这部分时间的分析和改善作为管理程序的改善课题单独处理相对来说更容易取得理解共识。
当然有些时间是不能够节省的,例如针对职员的健康管理所用的时间,或者企业文化建设的时间。
E、特殊宽放:
根据产品的工艺特点或生产计划周期的长短,不同的产品、不同的生产线根据具体情况能够设定特殊宽放,无特别原因不能够乱加特殊宽放,那样将失去标准时间的客观性和准确性。
(3)、宽放时间的设定
设定宽放时间方法不只壹种,最重要的原则是实事求是,世界上100%准确设定疲劳宽放的方法几乎没有,因为人群的体质特征不同,本书介绍的是日本的关联标准,因为体质特征接近,能够借鉴,若是欧美的标准会有壹些偏差。
请使用者多加留意。
确定宽放率基本有以下几步:
∙确定宽放项目
∙确定各宽放项目的具体比率。
∙累计这项比率。
∙于正常时间中追加宽放时间。
宽放时间=正常时间*(1+宽放率)
3、标准时间的设定
(1)设定方法
标准时间的设定有很多方法,这里重点说明的是时间分析的方法,但其它方法同样是非常重要及必不可少的,特别是预置时间标准法(PTS)。
表3将不同方法进行分类比较,目的是给大家壹具整体概念。
表3几种方法各有优缺点,笔者于IE管理实践中认为时间分析、PTS俩种方法的科学性好壹些,这样就保证了标准时间客观公平的基本原则。
其中时间分析即通过现场观测的方法来求得标准时间的方法,对于现场管理和改善非常实用,PTS法则主要用于新产品及新机种的量产前标准设定,以及对革新前后的方法进行评价,因此PTS法是IE工程师必须掌握的方法。
通过前面章节的讲解大家基本了解了标准时间的构成及设定方法。
总结来说,是于时间分析现场观测基础上经过评比修正得到正常时间,然后考虑放因素,加上宽放时间后得到标准时间。
标准时间的计算公式如下:
标准时间=正常时间*(1+宽放时间)=观率时间*评比系数*(1+宽放率)
(2)设定程序步骤1确定设定标准时间的目的
表3
方法名称
适用范围
评比
精度
用时
时间分析
周期性的作业
需要
较好
较少
动素法
非周期性的作业或周期较大
需要
壹般
较少
PTS法
长、短周期均适合消除人为因素
不要
优
壹般
标准资料
生产过程有重复相同内容的作业
不要
优
较少
经验估算法
作业周期长、且无历史数据、急需生产,无时间做准确计算
不作
不好
少
如上面内容介绍那样ST的设定有多种方法,要根据需要及目的选择不同精度的设定方法,因此明确目的是第壹步。
步骤2选定设定的方法------根据目的选择方法。
步骤3确定已获批准且已标准化的标准作业。
作业内容及方法尚未标准化的产品及工序,没有制定ST的必要,因为内容及方法决定时间。
步骤4正确划分动作单元,现场测定净作业时间。
步骤5对观测时间进行评比。
步骤6确定宽放项目及宽放率。
步骤7由公式计算标准时间。
步骤8主管部门审批备案(IE部)。
4、标准时间设定时的注意事项
∙必须认真负责、不可马虎大意
∙标准时间是制定生产计划,管理生产及评价结果的基准,即生产活动中有关效率的基准。
如同质量管理的质量标准壹样重要,它是制造业效率管理的基准,是用业指导、规范人的劳动效率的标准,制定时必须严谨规范、公平、公正、否则会造成管理上的混乱及员工的不满。
∙制定人必须具有专业水平,如同法官是不能够随便谁均能够做的壹样
∙必须于设定标准时间之前将作业方法及作业条件进行标准化
∙如果作业方法和作业条件尚未标准的话,时间也不可能标准,于前面曾ST最重要的目的是用来评价改善及革新的成绩,如果现有方法未经过认真检讨及标准化的话,标准化就成了壹个错误的方法,充其量是对壹个较差的方法进行了标准化,且强制员工执行。
如同质量问题大量存于,而企业取得了ISO认证壹样,效率及质量水平不会因拿到某种管理系统认证,而能短期内得以快速提升
∙当作业方法及条件改善后应及时更新ST,企业应有壹套进行ST定期更新管理程序,以保证现场取得的改善成绩及时变成标准且实现经济效益,评价改善绩效。
5.标准工时的维护
5.1.标准工时方法的训练及查核.
5.2.工作方法、作业条件、设备、材料等改变时之方案制度设计.
5.3.标准工时这诉怨回馈调查及改订.
5.4.定期复查制度.
6.秒表测时
1.作业员的选择
1.1.平均作业员,操作具有壹致性.
1.2.选择条件
(1).受完备训练,有意愿作好工作
(2).熟习操作程序.
(3).具有信心和合作精神.
1.3.沟通----现场主管及被观测者取得合作
1.4.接近作业员-----
(1).采取友谊态度.
(2).给予发问机会.
(3).鼓励提供意见.
(4).对其操作表示兴趣.
2.记录有关数据
2.1.理由:
标准工时随工作情况和方法而有变易,所以必须详细记录,以利日后参考和查证.
2.2.记录项目
2.2.1.产品名称、图样、规格、零件.
2.2.2.制造程序和操作方法、进刀速度、深度、转速.
2.2.3.设备性能、工夹治量具.
3.划分单元
3.1.意义:
将工作周程作业(cycle)划分程数个由动作组成的部份.
3.2.理由:
3.2.1.便利确实记述.
3.2.2.明确作业方法细部以利检讨改善.
3.2.3.建立标准工时之基本数据.
3.2.4.作业方法、条件改善或其它改变时,不必全部重测.
3.2.5.可方便用到相同其它作业单元.
3.2.6.可补救各单元的速度不均.
3.2.7.便于生产线平衡.
3.2.8.可将有效和无效时间分开.
3.2.9.特殊单元,个别处理.
3.2.10.使观测时间更超精确.
4.单元划分规则
4.1.适当的工作阶次.
4.2.不影响精确观测愈短愈好(0.33分~0.04分).
4.3.人力操作时间和机械操作时间分开.
4.4.机械时间内和机械时间外之手作业时间分开.
4.5.单元时确之起点、终点(声响、手臂方向改变).
4.6.不变单元和可变单元分开.
4.7.搬运物料时间和其它单元分开.
4.8.异常事态、外来单元,予以另外记录.
5.观测次数
工作周程时间(分)
建议观测次数
工作周程时间(分)
建议观测次数
0.1
200
4.00-5.00
15
0.25
100
5.00-10.00
10
0.50
60
10.00-20.00
8
0.75
40
20.00-40.00
5
1.00
30
40.00之上
3
2.00
20
6.观测作业员操作
6.1.位置
6.1.1.作业员后方数尺.
6.1.2.宜取易于观察详细确实位置.
6.1.3.不可和作业员谈话.
6.2.观测事项
6.2.1.操作情况
6.2.2.操作马表、观察读数.
6.2.3.记录每壹单元结束时间.
6.2.4.对作业员评比.
7.测时注意事项
7.1.合格测时人员.
7.2.设备、工具、材料、安全、工法等已达到合适情况.
7.3.工作方法确认.
7.4.组长、操作员之支持和合作.
7.5.合适之测时对象.
7.6.避免督导人员于场及秘密测时.
7.7.注意操作人员之故意戏弄.
8.评比
8.1.将实际观测时间调整至正常作业员正常作业所需工作时间,亦即:
观测时间x评比=正常时间
8.2.调整原因:
不壹定为合格者,不壹定能保持正常速度.
8.3.正常速度为100%之基准.
8.4.52张扑克牌分成四推,每堆距离6“,需0.5分.
8.5.成年男子,于平坦路上,3英里/小时之行走速度(及30秒走40米).
8.6.影片训练,现场观察.
9.西屋评比法
9.1.四项衡量因素
9.1.1.熟练度(skill).
9.1.2.努力度(effort).
9.1.3.工作环境(conditions).
9.1.4.壹致性(consistency).
将之上四项因素评比相加为评比系数.
正常工时=观测工时x(1+评比系数)
标准工时制作的难点