拨叉设计论文综述.docx
《拨叉设计论文综述.docx》由会员分享,可在线阅读,更多相关《拨叉设计论文综述.docx(28页珍藏版)》请在冰豆网上搜索。
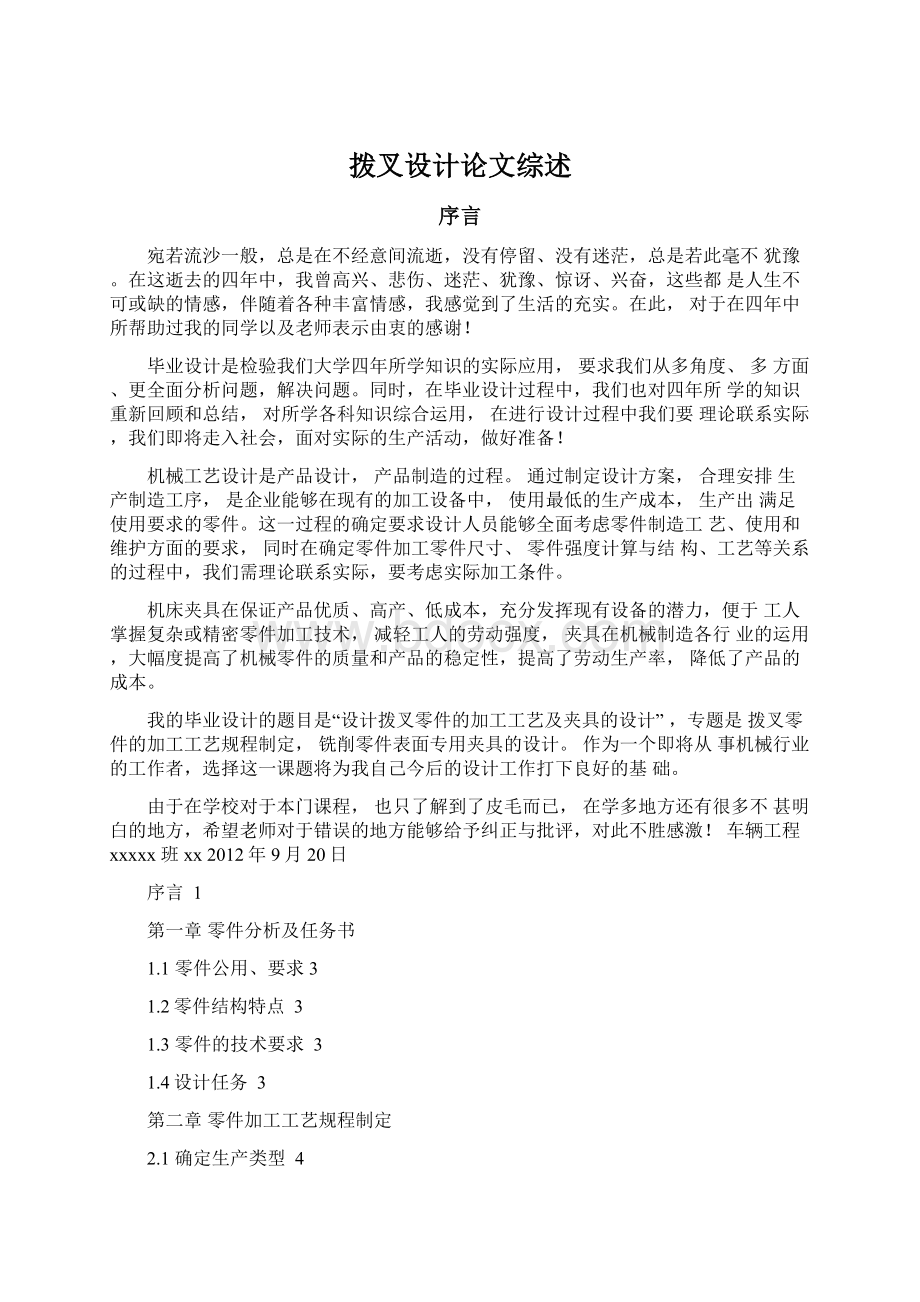
拨叉设计论文综述
序言
宛若流沙一般,总是在不经意间流逝,没有停留、没有迷茫,总是若此毫不犹豫。
在这逝去的四年中,我曾高兴、悲伤、迷茫、犹豫、惊讶、兴奋,这些都是人生不可或缺的情感,伴随着各种丰富情感,我感觉到了生活的充实。
在此,对于在四年中所帮助过我的同学以及老师表示由衷的感谢!
毕业设计是检验我们大学四年所学知识的实际应用,要求我们从多角度、多方面、更全面分析问题,解决问题。
同时,在毕业设计过程中,我们也对四年所学的知识重新回顾和总结,对所学各科知识综合运用,在进行设计过程中我们要理论联系实际,我们即将走入社会,面对实际的生产活动,做好准备!
机械工艺设计是产品设计,产品制造的过程。
通过制定设计方案,合理安排生产制造工序,是企业能够在现有的加工设备中,使用最低的生产成本,生产出满足使用要求的零件。
这一过程的确定要求设计人员能够全面考虑零件制造工艺、使用和维护方面的要求,同时在确定零件加工零件尺寸、零件强度计算与结构、工艺等关系的过程中,我们需理论联系实际,要考虑实际加工条件。
机床夹具在保证产品优质、高产、低成本,充分发挥现有设备的潜力,便于工人掌握复杂或精密零件加工技术,减轻工人的劳动强度,夹具在机械制造各行业的运用,大幅度提高了机械零件的质量和产品的稳定性,提高了劳动生产率,降低了产品的成本。
我的毕业设计的题目是“设计拨叉零件的加工工艺及夹具的设计”,专题是拨叉零件的加工工艺规程制定,铣削零件表面专用夹具的设计。
作为一个即将从事机械行业的工作者,选择这一课题将为我自己今后的设计工作打下良好的基础。
由于在学校对于本门课程,也只了解到了皮毛而已,在学多地方还有很多不甚明白的地方,希望老师对于错误的地方能够给予纠正与批评,对此不胜感激!
车辆工程xxxxx班xx2012年9月20日
序言1
第一章零件分析及任务书
1.1零件公用、要求3
1.2零件结构特点3
1.3零件的技术要求3
1.4设计任务3
第二章零件加工工艺规程制定
2.1确定生产类型4
2.2确定毛坯4
2.3确定机械加工工艺过程5
2.4确定工序尺寸7
2.5主要切削用量及时间定额9
第三章铣削零件专用夹具设计
3.1铣床夹具选择、结构设计及主要技术要求13
3.2明确设计任务,收集分析原始资料14
3.3拟定夹具的结构方案15
3.4分析计算定位误差18
3.5夹具加紧结构19
3.6拟订总装图尺寸、公差与配合和技术要求23
3.7夹具设计及操作简要说明23
第四章参考文献
第一章工艺规程设计
1.1拨叉零件功用、要求拨叉零件是日常生活中常见的机械传动零件,但在不同的应用场合起机构形状也不尽相同。
由于零件的使用场合要求,要求零件有一定的2强度、韧性及耐磨性要求。
1.2零件的结构特点
设计所给拨叉零件视图正确:
尺寸标注完整,零件技术要求规范正确,零件的结
构工艺合理;零件所选材料为ZG45材料Sn=570MP该材料具有较高的强度,韧性
和塑性,切削性能良好;结构工艺性比较好。
该零件主要加工表面及技术要求分析如下:
⑴同轴孔$16H9、$9H9的同轴度要求小于0.08mm,再设计家具时应考虑加工要求。
⑵零件小端面(8h12mm两拨叉对称度要求不小于0.08mm,在加工时可考虑在一次装夹下将两表面同时加工。
⑶零件加工表面粗糙度最高要求Ra=6.3卩m技工要求不高,尺寸精度等级亦不
算太高,降低了加工的复杂性。
综上所述,根据个加工方法的经济度及一般机床所能达到的位置精度,该零件没有很难的加工表面,上述各表面的技术要求采用常规加工工艺均可保证。
此外,在加工过程中影充分考虑零件结构特点。
1.3零件的技术要求
⑴铸件应该经正火处理,目的改善了切削加工性能,减小表面粗糙度,材料正火后硬
度为140〜163HBS
⑵未注圆角半径为R3〜5mm
⑶加工表面不应该有毛刺、裂缝、结疤、夹渣等缺陷,并应清理清洁
⑷所有加工表面应光洁,不可有裂缝、压痕、毛刺、气孔、凹痕以及金属夹杂物,在磨光表面上不该有深痕和黑点。
⑸清除油道及其它部分的金属削,污染物及其它杂物并清洗吸干
⑹精加工后,应经磁力探伤并退磁。
1.4设计任务
设计题目:
设计拨叉零件的加工工艺及夹具的设计
1、、零件图、毛坯图;
2、编写拨叉体的加工工艺;
3、绘制变速拨叉的工艺卡;铣削56H12内侧面)
4、设计一套铣削56H12内侧面夹具;
5、设计说明书一套。
第二章工艺规程制订
2.1确定生产类型
N1=N-n(1+a)•(1+3)
式中:
N1—零件的生产纲领(件/年)
N—产品的生产纲领;
n—每台产品中包含零件的数量;
a—该零件设备的百分率;
3—改零件废品的百分率;
已知零件的年生产纲领为10000件,零件的质量约为2kg,由参考文献
(1)表15-2可确定其生产类型为大批生产。
鼓初步确定工艺安排的基本倾向为:
加工过程划分阶段;工序
适当集中;加工设备一通用设备为主;大量采用专用工装。
这样生产准备工作投资较少,投资快、生产率高。
2.2确定毛坯
2.2.1确定毛坯种类
根据零件材料确定毛坯为铸铁。
并依其结构形状、尺寸大小和生产类型,有参考文献
(1)表15-4确定毛坯的铸造方法选用金属型浇注造型。
根据参考文献
(1)表15-5铸件尺寸公
差等级才哟个CT9级。
2.2.2确定铸件余量及形状
铸件各加工表面机械加工余量见表
表2-1零件各端面加工余量
基本尺寸(mr)i
加工余量
附注
48(上下两端面)
2
单侧
52(56H12内侧面)
2
[单侧,双侧加工
12(8h12外侧面)
2
单侧,双侧加工
对于金属型浇注,根据参考文献
(1)表15-9铸件最小孔的直径,故本零直径16mm及
一下尺寸的孔均不铸出,零件两侧面不需机械加工,可直接铸造成型。
Pl
■
图1拨叉毛坯简图
2.3确定机械加工工艺过程
2.3.1选择定位基准
(一)精基准的选择原则
(1)尽可能的轩加工表面的设计基准为精基准,即“基准重合”原则。
目的:
避免产生基准不重合误差。
(2)应经可能在多数工序中采用同一组精基准定位,即“基准统一”原则。
目的:
家少设计和制造费用并减少基准交换所带来的定位误差。
(3)有些精加工工序,可轩加工表面本身为定位基准,即“自由基准”原则。
(4)对位置精度要求高的表面,可采用“互为基准”,反复加工。
目的:
以保证高的位置精度。
(5)选定位准确、稳定、加紧简单的表面为精基准。
目的:
便于弓箭的安装和加工。
为保证同轴孔的平行度要求,并尽量遵循“基准重合”的原则,选精基准为“一面一长孔”的定位方式,及已$16h12的一端面为精基准,在加工过程中优先加工基准,在加工其余加工免时都以它为基准。
(二)选择粗基准遵循“基准先行”的原则,以拨叉圆弧口内表面及一段面为加工的粗基准先加工内孔及44h12的端面。
232拟订工艺规程
(一)选择表面加工方法
根据各表面加工要求和各种加工方法所能达到的经济精度,根据参考文献
(1)表
15-32〜15-34选择零件主要表面的加工方法与方案如下:
44h12的上下端面:
粗铳(IT10)—半精铳(IT8)。
56H12的内侧面:
粗铳(IT10)—半精铳(IT8)。
8h12的外侧面:
粗铳(IT10)—半精铳(IT8)。
016H9的内孔:
钻(IT12)—扩(IT10)—铰(IT8)。
深为2mnm勺沟槽:
拉削(IT6)。
09H9的内孔:
钻(IT12)—铰(IT8)。
(二)确定工艺过程方案
(1)拟订方案由于各表面加工方法及粗精基准已基本确定,现按照“先粗后精“先主
后次”“先面后孔”“基准先行”的原则,初步拟定两种工艺过程方案,见表2-2
万案
万案
工序号
工序内容
工序号
工序内容
1
铸坯
1
铸坯
2
热处理
2
热处理
3
粗铳44h12的上端面
3
粗铳、半精铳44h12的上端面
4
粗铳44h12的下端面
4
粗铳、半精铳44h12的下端面
5
半精铳44h12的上端面
5
钻d=15mm的孔
6
半精铳44h12的下端面
6
扩d=15.85mm的孔
7
钻d=15mnm勺孔
7
铰016H9的孔
8
扩d=15.85mm的孔
8
粗、半精铳8h12的外侧面
9
铰016H9的孔
9
粗、半精铳56H12的内侧面
10
拉H=2mnt勺键槽
10
钻、铰09H9孔,孔口倒角1
X45°
11
粗、半精铳8h12的外侧面
11
钳工去毛刺
12
钻、铰09H9孔,孔口倒角1
X45°
12
终检
13
粗、半精铳56H12的内侧面
14
钳工去毛刺
15
终检
(2)方案论证两种方案的主要区别在于加工过程中粗精加工顺序的排列,还有两种方
案中队09H9的孔的加工工序的安排。
方案一的优点在于:
①粗精加工划分了明确的加工阶段:
工序3〜4为粗加工阶段,工
序5〜6为半精加工阶段,个表面加工互不影响,精度逐渐提高,有利于保证表面加工质量。
②工序中吧加工56H12内侧面的工序安排到09H9的孔侠义道工序,为了方便在加工56H12
内侧面时的定位需要。
该方案的明显弊端是:
1村精加工工序分开增加了供需数量和安装次数,安装误差较大。
2工序过程中把加工56H12内侧面和8h12外侧面工序分开,由于中间的钻、铰工序需换机
床,增加了装夹次数,对拨叉爪的对称度要求有影响。
方案二的特点是:
①基本遵循了粗精加工划分原则。
②粗精铣在一次装夹中完成,减小由零件多次装夹产生的误差。
③加工56H12内侧面和8h12外侧面是虽然需两次装夹工件,
但不需要换机床加工,有利于拨叉对成都的要求。
方案二的不足之处,加工过程中采用铸造表面未经加工的基准,加工误差大,不能保证零件精度要求。
在铳削56H12内侧面时,采用了零件侧面(铸造表面)定位的方法,精度低,误差大。
根据以上分析,确定方案一为拨叉零件加工的工艺路线。
2.4确定工序尺寸
(一)确定工序尺寸的一般方法是,有加工表面的最后工序往前推算,最后工学尺寸岸零件图的要求标注。
当无基准转换时,统一表面多次加工的工序尺寸至于工序(或工号)的加工余量有关。
当基准不重合时,工序尺寸应用工艺尺寸链解算。
选择工序间加工余量的主要原则:
(1)采用最小的加工余量。
以缩短加工时间,并降低零件的制造费用;
(2)加工余量应能保证得到图纸上所规定的表面粗糙度及精度;
(3)决定加工余量时应考虑到零件热处理时引起的变形,否则可能产生废品;
(4)决定加工余量时应考虑到所采用的加工方法和设备,以及加工过程中零件可能发生的变形;
(5)决定零件加工余量时应考虑到被加工零件的大小,零件愈大,则加工余量也愈大。
公差的选择原则:
(1)公差不应超出经济的加工精度范围;
(2)选择公差时应考虑到加工余量的大小,因公差的界限决定加工余量的最大与最小尺寸;
(二)零件中加工工序尺寸确定
各加工方法的经济精度确定其尺寸偏差。
①对直接保证设计尺寸的工序尺寸,可按实际尺寸偏差要求确定其尺寸偏差。
②铸件尺寸按要求其公差带对称分布。
③其余独立的中间尺寸按“入体方向”确定偏差。
(1)该报差两件孔的加工,零件中有两个孔需加工,切凌空的直径都小于20mm采用
的加工方式钻—扩—铰,各加工步骤的加工余量及公差等级及加工所能达到的表面粗糙度见表2-3
表2-3孔加工尺寸及公差
加工表面
加工内容
加工
余量
精度
等级
工序尺寸
表面粗糙度
Ra
(卩m
工序余量
最小
最大
铸件
IT7
+0.036
1.6
铰孔
0160
0.15
+0.084
0.066
0.0193
016H9
扩孔
IT9
015.850
3.2
0.85
IT12
+0.21
0150
12.5
0.64
0.934
钻孔
铸件
IT7
+0036
1.6
铰孔
090
09H9
0.2
IT12
+0.18
08.80
12.5
0.02
0.236
钻孔
(2)确定铳削加工时的余量,本零件中,56H12内侧面和8h12的外侧面需铳削加工,
加工时的工艺基准与设计基准重合。
前面确定了工件表面的总加工余量,现更具刀具切削用
量及相关资料确定个表面精加工、半径加工余量,有后向前推算工序尺寸,并确定其公差。
见表2-4
表2-4各端面的加工工序余量及公差
加工表面
加工内容
加工
余量
精度等级
工序尺寸
表面粗糙度Ra
(卩m
工序余量
最小
最大
铸件
2
0
44h12
IT12
44.5-0.052
12.5
1.5
1.75
半粗铳
1.75
0
的端面
IT11
44-0.25
6.3
0.18
0.25
精铳
0.25
铸件
2
+0.6
56H12
IT12
55.50
12.5
1.5
1.75
半粗铳
1.75
+03
内侧面
IT11
560.
6.3
0.18
0.25
精铳
0.25
铸件
2
8h12的
IT12
8.5-0.30
12.5
1.5
1.75
半粗铳
1.75
0
外侧面
IT11
8-0.15
6.3
0.18
0.25
精铳
0.25
2.5主要切削用量及时间定额
2.5.1工序(3〜6)铣削端面的切削用量及时间定额
工序过程中,在能够达到表面加工精度的情况下,粗精加工采用同一把车刀,加工材料
为ZG45,Sb=570MP,铸件,机床为X62卧式铳床,工件采用夹具装夹。
(一)选择道具刀具选用硬质合金整体套式面铳刀,铳刀直径do=80mmZ=10,根据参
考文献
(1)表3.1-37。
由于甲供材料Sb<800MR故选铳刀前角丫o=20d°,后角a。
=12°(周齿),ao=6°(端齿),根据参考文献
(2)表3.2。
(二)粗加工端面选择切削用量
(1)选择切削深度ap工件表面的加工方法为粗精铳加工,粗加工切削加工精度ap=1.75mm半精加工时切削深度ap=0.25mm。
(2)确定每齿进给量fz根据参考文献
(2)表3.3,铳床功率7.5kw工艺系统刚性中等,粗尺铳刀加工钢料,查的每齿进给量0.09〜0.18mm/z,取fz=0.15mm/z。
(3)选择铳刀磨顿标准及刀具寿命根据参考文献
(2)表3.7,铳刀刀齿厚道面最大
磨损量为0.3mm,铳刀直径do=80mm故刀具寿命T=180min,参考文献
(2)表3.8。
(4)确定刀具切屑速度VC和工作台每分钟进给量fMZ切削速度可根据参考文献
(2)表
3.27中的计算
Cvd?
式中Cv=186,qv=0.2,xv=0.1,yv=0.4,uv=0.2,pv=0,mv=0.2,「=24,kv=1.
二D二80
根据所用X62性卧式铳床主轴尸姬转速选择n=600r/min,参考文献
(1)表4.2-39。
则实际加工过程中切削速度vc=150.72m/min
(三)半精加工端面切削用量的选择
(1)切削深度确定半精加工时切削深度:
-p=0.25mm
(2)确定每齿进给量fz每齿进给量0.09〜0.18mm/z,取fz=0.09mm/z。
(3)确定刀具切削速度vc和工作台每分钟进给量fMZ切削速度可根据参考文献
(2)BIAO3.27的公式计算;
v
Cvd:
k
yvUnPnv
二二z
v
Cvd:
vcmxv
T:
-p
式中Cv=186,qv二0.2,Xv二0.1,yv=0.4,%二02Pv=0,m=0.2,=24,k^1.
186工800.2
fy^-UnzPnkv=1800'20.250.10.090.4240.2100-252.08m/min
1000v1000252.08
n1003.5r/min
二D\:
80
根据所用X62型卧式铳床主轴转速选择n=950r/min,参考文献
(1)表4.2-39。
则尸姬加工过程中切削速度Vc=238.64m/mim
2.5.2工序(7〜9、12)为孔的加工,确定切削用量及时间定额
(一)选择道具加工016H9孔的加工步骤:
钻(高速钢锥柄麻花钻)一扩(高速锥柄扩孔钻)一铰(锥柄机用铰刀)
加工09H9的加工步骤:
钻(高速钢锥柄麻花钻)一一铰(锥柄机用铰刀)
10
(二)选择切削用量
(1)钻孔(d=15mm是刀具采用手动进给。
根据参考文献
(2)表2.12,钻头厚道面最大磨损限量取0.8mm确定钻头耐用度T=25min。
(2)确定钻孔的切削速度v根据参考文献(20biao2.14=570MP:
的45钢的加工
属性属4类,根据参考文献
(2)表2.7确定钻头的进给量f=0.31〜0.37mm/r,取进给量
f0.35mm/r,有参考文献
(2)表2.13确定切削速度v=17m/min。
(3)扩孔的切削速度v根据参考文献
(2)表2.3公式
Cvd:
v「
▼-严十v
PI
式中式中:
Cv=16.5,zv二0.6,x=0.2,yv二0.3,m=0.25,p二0.85,kv=1。
根据参考文献
(2)2.10,确定扩孔钻进给量f=0.6据参考文献
(2)表2.12,确定钻头耐用度T=30min。
1000vn二D
100044.55
895.14r/min
二15.85
n=680r/min。
根据参考文献
(1)表4.2-15,确定所选Z525历史钻床主轴转速
(4)铰孔的切削速度v根据参考文献
(2)表2.3公式
式中:
Cv=115.7,zv=0.3,xv=0,yv=0.65,m=0.7,p=0.15,kv=1。
根据参考文
献
(2)2.11,确定扩孔钻进给量f=0.65〜1.4mm/r,取飞=0.65mm/r,根据参考文献
(2)
表2.12,确定铰刀的耐用度T=40min。
1000v10005.31…“.
n105.7r/min
二Dc;16
根据参考文献
(1)表4.2-15,确定所选Z525立式钻床主轴转速n=97r/min
(三)加工$9H9的切削用量的选择钻孔(d=8.8mm)时刀具采用手动进给。
根据参考文献
(2)表2.12,钻头厚道面最大磨损限量取0.8mm确定钻头的耐用度T=25min。
根据
参考文献
(2)表2.7确定钻头的进给量f=0.31〜0.37mm/r,取进给量f=0.35mm/r,确定主轴转速n=272r/min,铰孔时所用铰刀d=9mm铰刀进给量f=0.65mm/r,切削速度v=97r/mm
11
2.5.3工序(11、13)为端面加工,确定切削用量及时间定额
工序过程中,在能够到达表面加工精度要求的情况下,粗精加工采用同一把车刀,加工
材料为ZG45、p=570MP:
,铸件,机床为Z52K立式铳床,工件采用专用夹具装夹。
(一)选择刀具刀具选用硬纸盒经错齿三刃面盘铳刀铳刀直径d。
=50mm,z=12,根
据参考文献
(1)表3.1-37。
由于甲供材料800MP:
故选铳刀主偏角k^60,副偏角kr=2。
(二)粗加工端面选择切削用量
(1)选择切削深度:
-p工件表面的加工方法为粗精铳加工,粗加工切削深度=1.75mm,半精加工时切削深度〉p=0.25mm。
(2)确定每齿进给量fz根据参考文献
(2)表3.3,铳床功率为7.5kw工艺系统刚性中等,粗齿铳刀加工钢料,查得每齿进给量0.09〜0.18mm/z,取fz=0.15mm/z。
(3)选择铳刀磨顿标准及刀具寿命根据参考文献
(2)表3.7,铳刀刀齿后面最大磨
损两为0.3mm,铳刀直径d°=50mm,故刀具寿命为T=120min,参考文献
(2)表3.27中
的公式计算:
则实际加工过程中切削速度vc=94.2m/min
c
(三)半精加工敦勉切削用量选择
12
3.27中的公式计算:
根据所用X52K型立式铳床主轴转速选择n=750r/min,参考文献
(1)表4.2-39
则尸姬加工过程中切削速度vc=117.75m/min
第三章铣削零件专用夹具设计
3.1铣床夹具选择、结构设计及主要技术要求
3.1.1铣床夹具选择原则
(1)在小批或成批生产中,通常采用通用化和规划化的各种构造的铣床用虎钳。
根据工件的形状和尺寸以及工艺定位要求设计装配于虎钳上的专用钳口。
设计用钳口时,应使切削力朝向固定钳口,并在夹紧时不致有抬起工件的趋势。
(2)在大批小量生产中,通常采用通用的带刻度回转盘进行工件的多面铣削或分度铣削加工。
(3)在大批小量生产中,应设计专用铣夹具完成各种不同的铣削加工,并尽量设计多件加工、联动夹紧或气动夹紧装置。
(4)在大批量生产中,为了缩短设计和制造周期,往往采用通用化和规格化的立轴或卧轴转分度盘,根据工件的形状及工艺定位夹紧要求,配以专门设计的专用夹具来完成工件的多面铣削或分度铣
3.1.2夹具的结构设计要则
(1)由于铣削过程不是连续切削,以及加工余量较大,不但所需的切削力较大,而且切削力的大小及方向随时都可能在变化,致使在铣削过程中产生振动。
因此铣床夹具要有足够的夹紧力,夹具结构要有足够的刚性。
(2)为了提高铣床夹具的刚性,工件待加工表面应尽量不超出工作台,在确保夹具有
足够的排削空间的前提下,尽量降低夹具的高度,一般夹具高与宽之比w1〜1.25.
(3)对于以铸、锻件毛坯面定位的铣夹具,因以毛坯图作为设计夹具的依据,以免对工件毛坯余量尺寸和形状误差、分型面或浇冒口等问题因考虑不周而影响夹具的合理性和可靠性。
(4)以工件毛坯面定位时,为避免毛坯误差,应多设计若干个辅助支承。
(5)要特别注意在铣