旋流分离技术在颗粒分级与固液分离中的应用.docx
《旋流分离技术在颗粒分级与固液分离中的应用.docx》由会员分享,可在线阅读,更多相关《旋流分离技术在颗粒分级与固液分离中的应用.docx(10页珍藏版)》请在冰豆网上搜索。
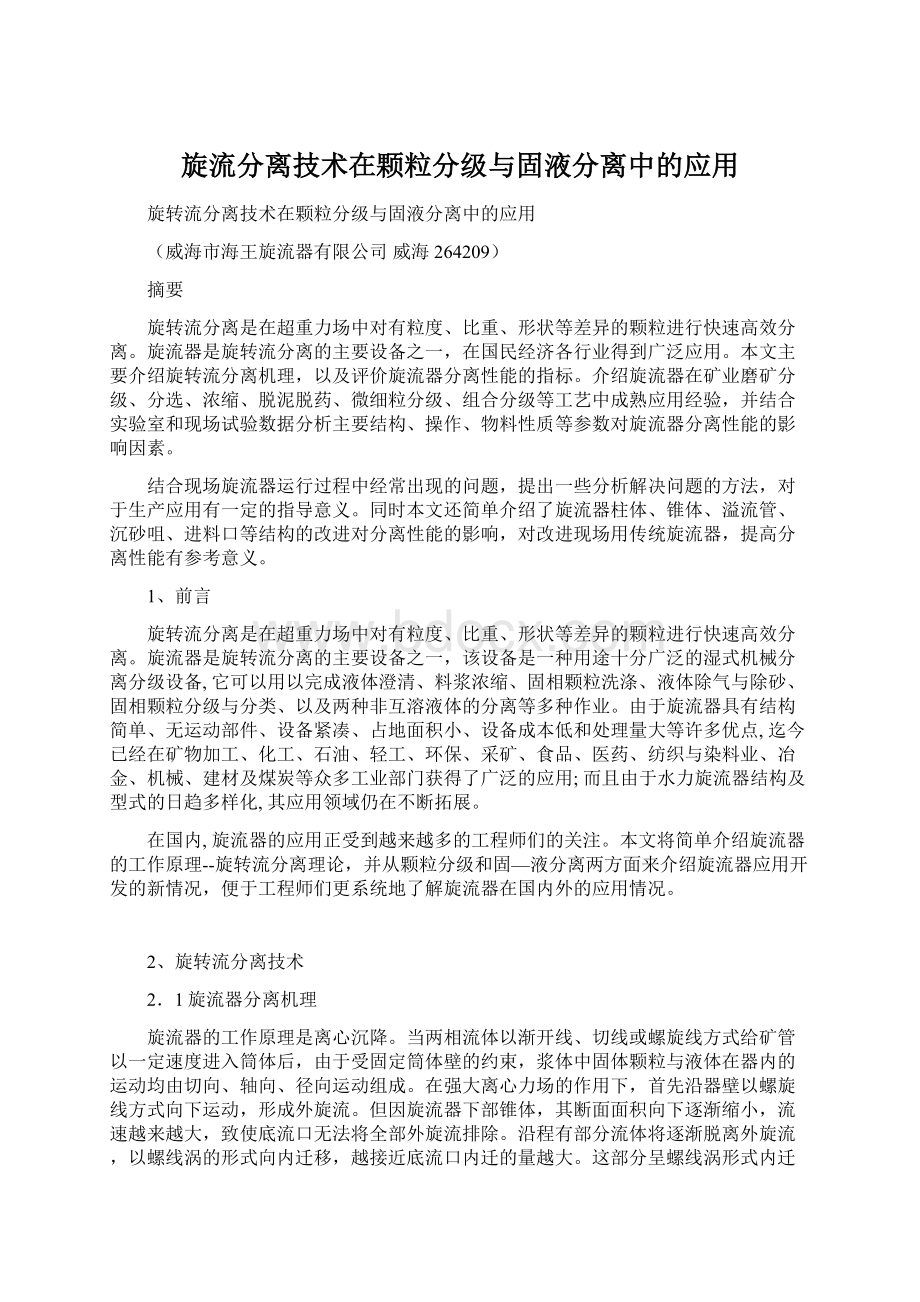
旋流分离技术在颗粒分级与固液分离中的应用
旋转流分离技术在颗粒分级与固液分离中的应用
(威海市海王旋流器有限公司威海264209)
摘要
旋转流分离是在超重力场中对有粒度、比重、形状等差异的颗粒进行快速高效分离。
旋流器是旋转流分离的主要设备之一,在国民经济各行业得到广泛应用。
本文主要介绍旋转流分离机理,以及评价旋流器分离性能的指标。
介绍旋流器在矿业磨矿分级、分选、浓缩、脱泥脱药、微细粒分级、组合分级等工艺中成熟应用经验,并结合实验室和现场试验数据分析主要结构、操作、物料性质等参数对旋流器分离性能的影响因素。
结合现场旋流器运行过程中经常出现的问题,提出一些分析解决问题的方法,对于生产应用有一定的指导意义。
同时本文还简单介绍了旋流器柱体、锥体、溢流管、沉砂咀、进料口等结构的改进对分离性能的影响,对改进现场用传统旋流器,提高分离性能有参考意义。
1、前言
旋转流分离是在超重力场中对有粒度、比重、形状等差异的颗粒进行快速高效分离。
旋流器是旋转流分离的主要设备之一,该设备是一种用途十分广泛的湿式机械分离分级设备,它可以用以完成液体澄清、料浆浓缩、固相颗粒洗涤、液体除气与除砂、固相颗粒分级与分类、以及两种非互溶液体的分离等多种作业。
由于旋流器具有结构简单、无运动部件、设备紧凑、占地面积小、设备成本低和处理量大等许多优点,迄今已经在矿物加工、化工、石油、轻工、环保、采矿、食品、医药、纺织与染料业、冶金、机械、建材及煤炭等众多工业部门获得了广泛的应用;而且由于水力旋流器结构及型式的日趋多样化,其应用领域仍在不断拓展。
在国内,旋流器的应用正受到越来越多的工程师们的关注。
本文将简单介绍旋流器的工作原理--旋转流分离理论,并从颗粒分级和固—液分离两方面来介绍旋流器应用开发的新情况,便于工程师们更系统地了解旋流器在国内外的应用情况。
2、旋转流分离技术
2.1旋流器分离机理
旋流器的工作原理是离心沉降。
当两相流体以渐开线、切线或螺旋线方式给矿管以一定速度进入筒体后,由于受固定筒体壁的约束,浆体中固体颗粒与液体在器内的运动均由切向、轴向、径向运动组成。
在强大离心力场的作用下,首先沿器壁以螺旋线方式向下运动,形成外旋流。
但因旋流器下部锥体,其断面面积向下逐渐缩小,流速越来越大,致使底流口无法将全部外旋流排除。
沿程有部分流体将逐渐脱离外旋流,以螺线涡的形式向内迁移,越接近底流口内迁的量越大。
这部分呈螺线涡形式内迁的流体,只能调转方向向上运动,形成内旋流并从上部溢流管排出。
外旋流和内旋流是旋流器中流体运动的主要形式,它们的旋转方向相同,但其运动方向相反。
此外,旋流器内部还有短路流、盖下流、空气柱、闭环涡流、零速包络面等几种运动形式存在。
2.2分离性能的评价指标
旋流器的性能评价指标主要是分离粒度、单台处理能力和分级效率。
分离粒度和单台处理能力是选择旋流器的主要指标,而分级效率则是衡量旋流器效率高低的主要指标。
分离粒度定义为:
当某一特定的极窄级别的颗粒,它进入粗产物和进入细产物的概率均等,各为50%,那么,该极窄级别的中值粒径即为分离粒度,又称为平衡粒度或切割粒度,通常用
表示。
它是分级设备的主要性能参数之一。
衡量分级效果的指标主要是分级质效率和分级量效率。
分级质效率又称为牛顿效率,其物理意义是细产物中合格粒级的回收率与细产物中不合格粒级的混入率之差;分级量效率是指分级产品中合格粒级的回收率,为使分级量效率能够科学准确评价分级效果,通常还有一个指标限制,即细度合格的条件。
另外,在选矿过程中,有用粒级的回收率也是评价旋流器分级效果的一个重要指标。
2.3影响旋流器分级性能的因素
根据不同的要求,对旋流器分级分离性能指标的描述有以下几个:
溢流浓度、溢流固相粒度分布、分离粒度、分级效率、分离精度、分股比等。
虽然水力旋流器结构简单,但影响其工作性能指标的因素却非常多,总体上说有结构参数、操作参数、物性参数三部分综合影响,具体如表1所示。
表1影响旋流器分级效果的主要因素
因素类别
因素名称
结构参数
(1)旋流器直径
(2)溢流口直径(3)进料口直径
(4)沉砂口直径(5)溢流管壁厚(6)圆柱段高度
(7)溢流管插入深度(8)旋流器壁面粗糙度(9)锥角(10)安装倾角
操作参数
(1)进料流量
(2)进料压力
物性参数
(1)进料浓度
(2)固相粒度及分布(3)固、液相密度
(4)物料粘度
3、旋流器在矿物加工生产中的应用
3.1磨矿分级
在现代选矿厂中,水力旋流器在各段磨矿中都有应用。
其中,二、三段磨矿和中矿再磨回路中的分级作业几乎全部用水力旋流器。
在某些选矿厂里,只在一段磨矿中部分使用螺旋分级机,也逐渐被水力旋流器所替代。
特别近几年来,一些结构新颖的大直径旋流器替代其它分级设备在闭路磨矿循环工艺取得了成功的应用。
3.1.1新型多锥体旋流器在磨矿回路的应用
对嵌布粒度细的矿石,为了达到有用矿物的充分单体解离,要求磨矿分级系统能够生产出高浓度细粒度的合格产品。
从提高旋流器的分级效率入手,通过改善旋流器的锥体结构,降低溢流颗粒细度,并降低底流产物中的细颗粒夹带量,从而改善磨矿效果以满足生产要求。
较传统旋流器(见图1),新型旋流器(见图2)的设计由三段锥体组成。
第一段锥体角度较大,使旋流器内流体的切向速度达到最大,增大离心力场;第二段锥体较小,锥段长度较大,使被处理矿浆在此有足够的时间和空间进行充分交换;第三段锥体带有较大的锥体角度和直段结构,有利于降低旋流器底流中细颗粒的夹带量。
图1传统旋流器示意图图2新型旋流器示意图
长城铝厂磨矿车间使用新型Ø500多锥体旋流器替代原有的传统Ø500旋流器,与现有Φ3.2×4.9m格子磨,螺旋分级机组合形成一段闭路磨矿流程。
通过长期的现场运行表明:
采用新型旋流器后,该系统产能提高了3%,在同种工况下,旋流器的综合分级效率提高4~8%,溢流细度提高了3~10%。
3.1.2闭路磨矿回路中大直径旋流器应用
随着大型选矿厂的建设,大直径磨机被广泛使用,目前与其形成磨矿回路的优选设备是旋流器,众所周知,小直径旋流器具有分离粒度小、分离精度高,但处理量小,因此采用小直径旋流器组占地面积大、管理困难、分配器到旋流器之间的连接管较长,易堵塞和磨损等缺点,因此,研究和使用结构新颖的大直径旋流器与大型磨机组成磨矿分级系统来获得高浓度高细度溢流产品成为目前旋流器大型化的发展趋势。
使用大直径旋流器获得高浓度高细度溢流产品是可以实现的。
从分离粒度的计算公式可以看出,d50与给料浓度的平方根成正比,适当降低给料浓度,不仅可以降低分离粒度,而且可以提高分离精度,从而得到高质量的返砂。
根据使用Ø700、Ø850、Ø1000直径旋流器对粗煤泥分级浓缩的试验证明,单台处理量达到了400~800m3/h。
目前设计的Ø700旋流器将在金堆城Ø3.2×4.0m格子磨磨矿回路中应用,实现“1台磨机+1台旋流器”的简单模式。
3.2脱泥
在矿物加工过程中,原生矿泥和次生矿泥均对选别过程和指标有重大影响。
通常,为了给选别过程创造有利条件和得到满意的选别指标,对某些含泥多的矿产资源在入选前进行脱泥作业。
而旋流器的脱泥流程,必须根据原矿的性质和指标的要求而定。
微细粒级钛铁矿占整个攀枝花资源的很大一部分,这部分矿浆的特点是:
体积量大,含有大量的-10um的细粒级,而且浓度低(4%~6%)。
因此,解决它的浓缩分级是提高钛资源综合利用率的关键。
根据物料的性质和现场的工艺要求,采用Ø125mm多锥体旋流器组对其进行分级浓缩,浓缩后底流的浓度达到60%,底流中+10um粒级回收率达到95%的良好指标。
又如:
某选矿厂铁矿属微细粒级嵌布的磁铁矿和赤铁矿混合矿类型,可选性研究表明,原矿磨矿分级入选前的产物中-10um粒级的泥质物含铁量很低,如果能在入选前脱除-10um的矿泥就可以改善精矿的质量。
研究决定采用Ø125mm旋流器进行脱泥,其脱泥效率能达到82.09%,+10um粒级的回收率达到90%。
3.3浓缩
浓缩的目的是为了获得高浓度的底流(最终目的是使固相物料脱水)。
浓缩用旋流器处理某些物料时,其底流体积浓度可高达50%,若底流管再联用小型增稠器,则可获得更高浓度的底流。
在某些场合,浓缩用旋流器系统可被用来替代那些体积大得多、且成本高得多的重力沉降槽。
3.3.1过滤设备前的预浓缩
旋流器用作浓缩设备时的典型用途是对真空过滤机、筛分设备、脱水离心机以及其它浓缩设备的进料进行预浓缩。
图3为旋流器在皮带过滤机前的预浓缩工艺流程图。
图4为旋流器在真空过滤机前的预浓缩工艺流程图。
图3旋流器与皮带过滤机图4旋流器与真空过滤机
物料进入过滤或其他浓缩设备之前的预浓缩,如将物料预先分为粗粒级产品和细粒级产品,将粗粒级产品作为过滤机的底层物料,然后再送细粒级产品去过滤,这时粗粒级产品起到预敷层助滤作用,这样可以获得质量良好的滤液,过滤速度也会显著提高。
3.3.2尾矿的浓缩分级
近几年来,国内矿山尾矿的综合利用技术得到了快速的发展,出现了利用尾矿资源取用建筑粗砂,制作免烧砖和水泥添加剂等新工艺。
利用旋流器和高频振动脱水筛组成联合工艺在尾矿的分级浓缩作业中取得许多成功的应用。
某选矿厂的尾矿中存在大量的+150um粗粒级,通过“旋流器分级浓缩-振动筛脱水”二段浓缩脱泥新工艺后(图5),可从尾矿中回收含水率低、级配合理的粗砂(图6),回收后的粗砂的水分<15%,产率>30%。
图5旋流器与振动筛图6筛上粗砂
莱芜矿业公司选矿厂使用尾矿压滤技术提高尾矿的浓度以达到尾矿充填的工艺要求,该工艺具有一次投资大,尾矿充填成本高等缺点。
2006年,采用“旋流器-旋流澄清器”分级浓缩新工艺与现有15万吨/年的压滤浓缩工艺进行了对比工业试验,工业试验结果表明:
通过分级浓缩新工艺后可使浓缩后的综合尾矿浓度达到充填采空区的浓度要求,而每吨尾矿的处理成本下降50%,一次性投资降低60%,现场工作环境也得到了明显改善。
该成果获冶金科技进步二等奖。
3.4组合分级
在颗粒分级过程中,为了得到更细的溢流产品通常会采用两级分级设备串联来达到效果。
在浓缩或澄清工艺中,为了得到高纯净的液相或高浓度的固相物料,常采用旋流器溢流或底流多级串联的工艺流程,虽然部分满足了现场的工艺要求,但势必造成相关设备投资大、工艺复杂、能耗高、占地面积大等缺点,与节能降耗的原则背道而驰。
近年来,开发了一些具有新颖结构的母子旋流器和组合分级浓缩工艺在实际流程中取得了一些成功的应用。
3.4.1串联多产品分级
在矿物加工过程中,根据矿石的特性,需要将物料分成多个粒级级别的产品,根据每个级别的物料性质采取不同的处理方式。
某化工厂钾镁肥车间,采用FX350-2ר200的旋流器对转化后的料浆进行分级,通过母子旋流器可以得到+80目、-80目+200目和-200目三个级别的料浆,由于+80目K+含量低,Na+含量高可以作为尾矿直接丢弃,-80目+200目产品返回转化槽继续反应,-200目作为成品进入下道工序,通过采用母子旋流器可以取代原有“旋流器-振动筛”分级流程。
3.4.2多级串联分级浓缩
在金矿的磨矿分级工段,为了得到更细的溢流产品通过采用两段分级流程,即第一级旋流器的溢流通过泵给入第二次旋流器,从而得到高细度的溢流产品(-200目85%)。
通过采用合适的母子旋流器代替原有的两段分级流程,不但可以得到合格的溢流产品,而且还可以降低能耗,减少相关设备的投资,具有明显的经济和社会效益。
该工艺已经在河北某金矿炭浆厂得到了验证,其工艺流程如图7。
图7母子旋流器与球磨机组成闭路磨矿系统
通过两段分级后的溢流产品的浓度较低(25%~30%),不能满足氰化工序的浓度(50%)要求。
因此,需要采用浓缩设备进行预浓缩。
目前,国内大部分金矿选矿厂采用浓密机进行浓缩作业,具有占地面积大,浓缩效果差等缺点。
目前,南非的工程师们采用了一种三段旋流器先分级后浓缩的组合方式与球磨机构成闭路磨矿流程取代氰化前的浓缩设备。
在这种流程(图8)中,两段旋流器分级后的溢流给入后续的小直径旋流器进行浓缩作业,浓缩旋流器的溢流返回一段旋流器的给料槽,经过浓缩后的旋流器底流进入后续的氰化工序。
据报道,已有两家选矿厂采用这种类型的流程后彻底停用了原有笨重的重力沉降设备。
现在,这种流程的设计思路也在世界范围内的矿物加工领域得到广泛的推荐和研究。
图8三段分级与球磨机组成分级浓缩流程图
4.旋流器的运行诊断
在旋流器的生产运行过程中,经常会出现“砂泵喘气”、“溢流跑粗”、“沉砂夹细”等现象,为了使生产中的旋流器能正常稳定的工作,我们将导致异常现象的原因和消除办法总结归纳入表2,供选矿厂的工程师参考。
表2旋流器工作过程中异常现场、产生原因及消除方法
异常现象
产生原因
消除方法
砂泵喘气
1、工艺流量与泵流量、旋流器处理能力不匹配
2、泵与旋流器选型不合理
3、实际生产能力达不到设计要求
1、更换小直径旋流器
2、自动调节泵的转速
3、部分溢流返回给料槽
4、泵排出管上加装阀门
沉砂口
堵塞
1、物料参数控制不当
2、结构参数匹配不合理
3、矿浆中存在杂物
4、进料浓度过高
1、更换大直径沉砂嘴
2、泵槽前或泵吸入口加设筛网
3、选用大直径旋流器
4、增大旋流器锥角
沉砂浓度过低
1、进料浓度过低
2、进料压力过低
3、进料粒度变细
1、更换小直径沉砂口
2、更换小直径旋流器
3、调整旋流器的结构配置
4、泵出口加阀门或更换高扬程泵
溢流跑粗
1、溢流管直径过大
2、进料压力过低
3、进料浓度过高
1、降低进料及溢流浓度
2、调整溢流管及沉砂口径
3、调整旋流器的锥角结构配置
沉砂夹细
1、沉砂口过大
2、进料压力高
3、旋流器型号偏小
4、进料浓度高,干涉沉降严重
5、旋流器磨损严重,影响分级效率
1、调整旋流器的结构参数
2、检查旋流器的磨损情况
磨损严重
1、压力过大
2、粒度组成变粗
3、颗粒形状不规整
1、换用耐磨材质
2、调整磨机的工作状况
当然,旋流器工作影响因素较多,针对现场出现的问题,要具体分析,对症下药,综合考虑,方能拿出切实可行的方案来,从而达到增产节约、降低消耗的目的。
5.结语
(1)旋流器在颗粒分级与固液分离作业中扮演着越来越重要的角色,凡是有密度差异或粒径差别可以导致沉降速度不同的场合,均可以考虑应用旋流器的可能性。
(2)由于旋流器处理能力大,结构的小幅度变化对分离性能的影响显著,因此可以从进料方式、锥体结构、安装方式等方面进行改进,取得明显的效果。
(3)旋流器的串联组合,可以将剩余能量充分利用,在磨矿分级、浓缩、宽粒度组成物料的分级等单元操作上将显示优越的性能。
(4)分析旋流器运行过程中存在的问题,需充分考虑系统布置、上下游设备间相互的影响与制约、物料参数、操作条件、结构参数等因素,只有从系统角度上才能找到解决问题的切实途径。