白车身设计规则.docx
《白车身设计规则.docx》由会员分享,可在线阅读,更多相关《白车身设计规则.docx(6页珍藏版)》请在冰豆网上搜索。
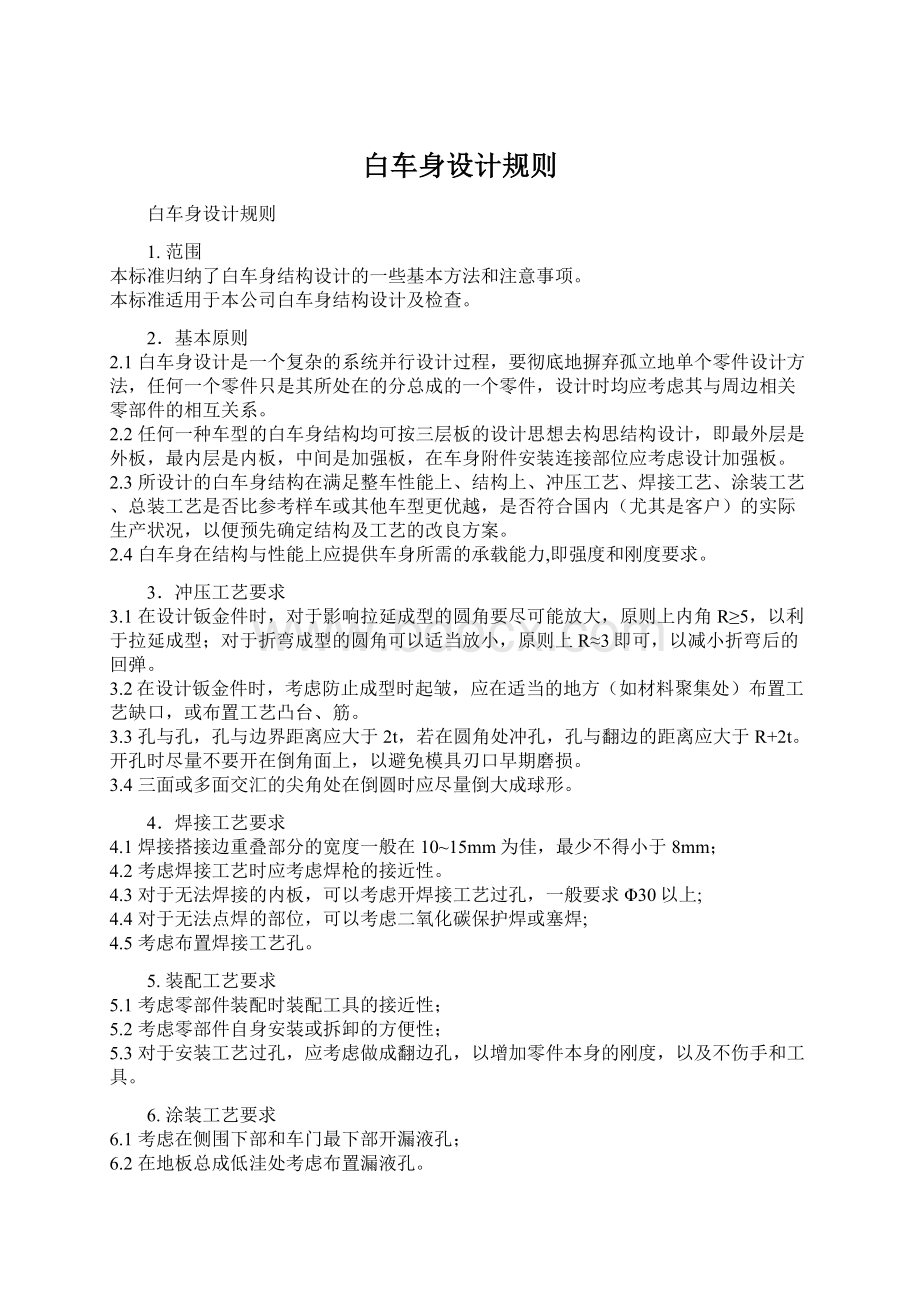
白车身设计规则
白车身设计规则
1.范围
本标准归纳了白车身结构设计的一些基本方法和注意事项。
本标准适用于本公司白车身结构设计及检查。
2.基本原则
2.1白车身设计是一个复杂的系统并行设计过程,要彻底地摒弃孤立地单个零件设计方法,任何一个零件只是其所处在的分总成的一个零件,设计时均应考虑其与周边相关零部件的相互关系。
2.2任何一种车型的白车身结构均可按三层板的设计思想去构思结构设计,即最外层是外板,最内层是内板,中间是加强板,在车身附件安装连接部位应考虑设计加强板。
2.3所设计的白车身结构在满足整车性能上、结构上、冲压工艺、焊接工艺、涂装工艺、总装工艺是否比参考样车或其他车型更优越,是否符合国内(尤其是客户)的实际生产状况,以便预先确定结构及工艺的改良方案。
2.4白车身在结构与性能上应提供车身所需的承载能力,即强度和刚度要求。
3.冲压工艺要求
3.1在设计钣金件时,对于影响拉延成型的圆角要尽可能放大,原则上内角R≥5,以利于拉延成型;对于折弯成型的圆角可以适当放小,原则上R≈3即可,以减小折弯后的回弹。
3.2在设计钣金件时,考虑防止成型时起皱,应在适当的地方(如材料聚集处)布置工艺缺口,或布置工艺凸台、筋。
3.3孔与孔,孔与边界距离应大于2t,若在圆角处冲孔,孔与翻边的距离应大于R+2t。
开孔时尽量不要开在倒角面上,以避免模具刃口早期磨损。
3.4三面或多面交汇的尖角处在倒圆时应尽量倒大成球形。
4.焊接工艺要求
4.1焊接搭接边重叠部分的宽度一般在10~15mm为佳,最少不得小于8mm;
4.2考虑焊接工艺时应考虑焊枪的接近性。
4.3对于无法焊接的内板,可以考虑开焊接工艺过孔,一般要求Φ30以上;
4.4对于无法点焊的部位,可以考虑二氧化碳保护焊或塞焊;
4.5考虑布置焊接工艺孔。
5.装配工艺要求
5.1考虑零部件装配时装配工具的接近性;
5.2考虑零部件自身安装或拆卸的方便性;
5.3对于安装工艺过孔,应考虑做成翻边孔,以增加零件本身的刚度,以及不伤手和工具。
6.涂装工艺要求
6.1考虑在侧围下部和车门最下部开漏液孔;
6.2在地板总成低洼处考虑布置漏液孔。
7.轻量化设计要求
7.1选取轻量化材料
7.1.1在满足强度和刚度的前提下,选取较薄的料厚;
7.1.2在满足强度和刚度的前提下,选取塑料材质;
7.2采用轻量化结构
7.2.1在大于50x50mm的区域内布置加强凹坑,并挖孔;
7.2.2在满足强度和刚度的前提下,考虑布置减重孔。
8.结构复杂化,以求最大强度、刚度设计要求
8.1车身钣金结构尽可能复杂化,在大于50x50mm的区域内布置加强凹坑、筋等特征;
8.2车身钣金结构尽可能复杂化,尽可能用自由曲面代替平面。
9.节约成本—对称性设计要求
在模具设计时,两对称件是做成一套模具的,同时对称件设计也减少设计时间,故设计时应尽量考虑左右件做成对称件,或者做成大结构对称,局部特征根据需要不对称。
10.节约成本—同一件设计要求
对于一些零部件(如一些小的加强板,比较规则的纵横梁等),可以考虑设计成自身是关于某一面对称的,这样左右件可以使用同一件。
以节约模具成本。
11.密封性要求
零部件设计中,要考虑车厢不应出现漏水或渗水的情况。
11.1侧车门和侧围门框之间的密封条断面设计应合理,压缩量应均匀一致,一般以1/3~1/2为宜,并绘出相应的密封条断面图;
11.2行李箱盖(或后背门)和行李箱盖框(或后背门框)之间的密封条断面设计应合理,压缩量应均匀一致,一般以1/3~1/2为宜,并绘出相应的密封条断面图;
11.3机舱盖和相应的发动机舱密封配合板金之间的密封条断面设计应合理,压缩量应均匀一致,一般以1/3~1/2为宜,并绘出相应的密封条断面图;
注:
11.1、11.2、11.3中的密封条应和相关的汽车密封件厂家交流沟通,根据车身结构的具体情况,请供应厂家提供合理的相应密封条断面图,最后应予以校核确认。
11.4相关的密封试验方法
11.4.1按GB/T12478-1990“客车防尘密封性试验方法”,通过防尘密封性试验;
11.4.2按GB/T12480-1990“客车防雨密封性试验方法”,通过防雨密封性试验。
12.美观与缝隙均匀性要求
12.1外观件处于高可见区,应考虑分缝缝隙的均匀性;
12.2处于高可见区或可见区(如车门打开后可看见的侧围区域)应考虑美观要求,面应光顺,不应出现面扭曲面的情形。
13.白车身组成
白车身由前围焊接总成、地板焊接总成、左/右侧围焊接总成、后围焊接总成、顶盖焊接总成组成。
13.1外覆盖件设计
13.1.1白车身外覆盖件由翼子板、侧围外板、车顶外板组成;
13.1.2边界条件:
前舱盖、前后车门、门框密封条、后行李箱盖,后行李密封条、侧围附件及总布置的硬点报告等;
13.1.3设计过程
第一步:
熟悉效果图,领会造型师设计意图和造型风格。
分析各部分安装结构及实现的可能性。
如结构不能实现或有疑问,则立即反馈给造型师,让造型师修改造型或作出解释。
第二步:
熟悉油泥模型、熟悉参考样车零件,注意其安装形式、壁厚以及与边界搭接关系。
第三步:
确定结构分块及固定方式、确定主断面、硬点。
硬点:
主断面、造型面、安装点、门框密封条、后行李箱密封条、后行李箱盖、侧围附件等。
固定方式:
翼子板安装方式主要在翼子板内板、加强板和轮罩上,螺栓安装。
侧围外板、车顶外板通过和内板焊接固定在白车身上。
第四步:
确定材料、料厚、成型方式、拔模方向、安装结构。
第五步:
结构设计
a)根据翼子板硬点设计它的固定孔;根据密封结构和断面设计侧围外板和车顶外板的焊接边。
翼子板的固定孔应合理分析在该零件的周围,不应集中在同侧,固定孔一般选择可调节的腰型孔;与分块线相关的棱角倒角R1~R5,以不加大整车的分块线宽度,和相邻分块线均匀为原则。
b)要点
1.门框密封条(第二道密封),侧密封条(第一道密封)的安装面一般由侧围外板设计人员先确定好,门的设计人员应在此安装面基础上根据相应的密封条结构形式偏移一定的距离来设计密封配合面。
2.铰链及锁扣安装面一般应先由开闭件(门)确定,然后再设计此安装面周边的相邻结构。
3.门控开关的安装面一般应先由开闭件(门)确定,然后再设计此安装面周边的相邻结构。
4.外饰件安装配合处的结构原则上由侧围外板设计人员先确定,外饰设计人员在此基础上进行相应的结构设计,在设计过程中双方人员应沟通协调,做到最优化设计。
5.考虑四大工艺性,侧围外板多数特征(除去周边需整形,侧冲等)可先定脱模方向大致为Y向,按此方向来设计各特征的脱模方向和拔模角。
6.与分块线相关的棱角倒角R2、R3,以不加大整车的分块线宽度,和相邻分块线均匀为原则。
7.充分考虑工艺性
第六步:
检查
断面检查、硬点检查、工艺检查。
检查修改完善后提交专家审查。
13.2内板件结构设计
13.2.1侧围焊接总成内板件设计
13.2.1.1侧围总成由侧围外板、A柱内板、A柱加强板、B柱内板、B柱加强板、C柱内板、前、后门槛粱内板、前、后门槛粱加强板、侧围上边粱及侧围附件等大件组成。
13.2.1.2边界条件:
密封结构,侧围附件安装硬点等。
13.2.1.3设计过程
第一步:
熟悉效果图,领会造型师设计意图和造型风格。
分析各部分安装结构及实现的可能性。
如结构不能实现或有疑问,则立即反馈给造型师,让造型师修改造型或作出解释。
第二步:
熟悉油泥模型、熟悉参考样车零件,注意其安装形式、壁厚以及与边界搭接关系。
第三步:
确定结构分块及固定方式、确定主断面、硬点。
硬点:
主断面、造型面、安装点、门框密封条、后行李密封条、后行李盖、侧围附件。
固定方式:
焊接
第四步:
确定材料、料厚、成型方式、拔模方向。
第五步:
结构设计
a)附件安装面原则上根据附件安装要求设计安装结构及其周边结构。
注:
对于三点式安全带的安装结构设计要求。
b)内饰安装结构原则上随白车身走,设计期间应相互协调沟通,优化结构。
c)电器元件结构原则上随白车身走,设计期间应相互协调沟通,优化结构。
d)与外表面配合面不能贴合外表面,留取3~5mm间隙并开盛胶槽,由外表面offset一定距离获得。
1.内外轮罩处的结构设计
2.内外板之间应形成空腔,以增大整车的结构刚度。
g)侧围加强板设计
加强板处在内外板之间,对侧围总成薄弱区起到加强作用,在设计时应考虑仅在加强区域和搭接边处焊接,其它区域应留一定空挡,尽量避免面与面大面接触,一方面增大加强功能另一方减少冲压制造误差带来的焊接困难,典型结构。
第六步:
检查
断面检查、硬点检查、工艺检查。
检查修改完善后提交专家审查。
13.2.1.4结构设计参数
13.2.1.4.1任何一种车型的车身侧围总成均可按三层板的设计思想去构思结构设计,即最外层是外板,最内层是内板,中间是加强板。
在车身附件安装处一般应考虑设计加强板。
13.2.1.4.2由于侧围都会有大片的外覆盖面的存在,而这些地方往往都会受到一定的外界冲击,为了增强其刚性而不容易变形,减少相互振动,必须的在内板与外板之间会涂一层3~5mm左右的传力胶。
在车身结构设计过程中要保证有足够的强度和刚度,车身的震动和噪音要达到有关的法规要求,给人一安静舒适感。
还要考虑整车车厢的密封性,各件转角处所留最大空隙应能使焊接粘贴胶密封住,以保证水不会通过任何缝隙渗入车厢内部。
13.2.2?
前围设计注意
a)机盖和翼子板的间隙,一般4-5mm;
b)大灯和机盖、翼子板、保险杠、格栅的间隙根据实际样车或配套厂协商,现在轿车追求美观,间隙都比较小;并且大灯尽量装在焊接件上;
1.前纵梁的设计尽量尊重原设计,在满足发动机悬制前提下,尽量平直;
d)机舱里的零部件多,小件的设计要满足强度和冲压工艺的要求。
13.2.3地板焊接总成设计
13.2.3.1地板总成由前地板、前地板加强板、地板内纵梁、地板外纵梁、座椅横梁、中地板、安全带加强板、后地板、备胎板、地板加强横梁、油箱安装支架等组成。
13.2.3.2边界条件:
密封结构,车身和底盘附件安装硬点等。
13.2.3.3设计过程
第一步:
熟悉效果图,领会造型师设计意图和造型风格。
分析各部分安装结构及实现的可能性。
如结构不能实现或有疑问,则立即反馈给造型师,让造型师修改造型或作出解释。
第二步:
熟悉油泥模型、熟悉参考样车零件,注意其安装形式、壁厚以及与边界搭接关系。
第三步:
确定结构分块及固定方式、确定主断面、硬点。
硬点:
主断面、造型面;传动轴和消音器(间隙一般取10-15MM)、油箱、后悬架、后备胎等底盘系统的安装空间和安装位置;座椅总成、安全带安装点等车身附件的安装空间及人机工程。
固定方式:
焊接
第四步:
确定材料、料厚、成型方式、拔模方向。
第五步:
结构设计
a)安装面原则上根据附件安装要求设计安装结构及其周边结构。
b)内饰安装结构原则上随白车身走,设计期间应相互协调沟通,优化结构。
c)电器元件结构原则上随白车身走,设计期间应相互协调沟通,优化结构。
d)内外板之间应形成空腔,以增大整车的结构刚度。
e)纵梁与地板之间形成空腔,以增大正面碰撞能力。
f)地板加强板设计:
加强板处在内外板之间,对地板总成薄弱区起到加强作用,在设计时应考虑仅在加强区域和搭接边处焊接,其它区域应留一定空挡,尽量避免面与面大面接触,一方面增大加强功能,另一方面减少冲压制造误差带来的焊接困难。
1.地板支架设计:
在保证强度和冲压工艺的前提下考虑安装的设计空间。
第六步:
检查
断面检查、硬点检查、工艺检查。
检查修改完善后提交专家审查。
13.2.3.4结构设计参数
13.2.3.4.1任何一种车型的车身地板总成均可按三层板的设计思想去构思结构设计,即最外层是外板,最内层是内板,中间是加强板。
在车身附件安装处一般应考虑设计加强板。
13.2.3.4.2由于地板面积较大,比较平整,且地板内部就是乘员乘坐的空间。
为了避免在车辆行驶过程中因外界的冲击而产生的相互振动,通常在地板外表面会涂一层3~5mm左右的减震隔热胶,以增强其刚性而不容易变形,同时也减少了车厢内部和外部的热量交换,提高了乘坐舒适性。
在地板结构设计过程中还要考虑整车车厢的密封性。
前、中、后地板搭边处、地板与前围、地板与侧围搭边处,以及各件转角处所留最大空隙应能使焊接粘贴胶密封住,以保证水不会通过任何缝隙渗入车厢内部。
13.2.3.4.3前纵梁的设计:
车身正面碰撞能否通过,前纵梁的正确设计很重要:
1)有CAE分析得出前纵梁的最大横节面;2)前纵梁的方向尽量水平,在X、Y、Z向上不要有大变化。
13.2.3.4.4地板设计注意事项
1.前后地板的筋的设计
2.地板上一个很重要的结构特征就是筋。
有的筋是为了结构需要,实现如座椅等附件的功能;
3.但多数筋的结构是为了增加刚度。
地板上筋的深度一般在5-10mm之间,象这样的筋结构它有刚度相当于6mm—10mm厚的钢板,可以最大限度的增加车身刚度,降低车身重量。
4.设计地板(尤其是前地板),有时会采用前后贯通的筋,这样可以提高地板的刚度,但同时在前后地板搭边处也会产生间隙,造成密封困难。
这一点在设计时应该综合考虑;
5.与悬架(尤其是与后悬)的配合问题
6.有时候悬架按照实体建模,有些杆臂并没有转到位,这样就容易造成设计后期检查时的干涉问题;因此在设计初期应注意与总布置部门的沟通;
7.在有悬架托架时应特别注意悬架托架和悬架的同轴性;
8.地板纵梁和纵梁内加强板之间在设计时应该预留间隙(通常两边各为0.3~0.5mm),因为纵梁及其内加强板材料厚、刚度大、尺寸长,预留间隙可以包容一定的变形量,这样在将来零件装配时较容易实现。
9.后地板备胎包的翻边:
因车型不同,该处翻边型式很多,但应注意在向下翻边时,不要与离去角干涉;
10.地板左右对称件的处理:
地板上左右对称、小尺寸的零件较多,在条件允许的情况下尽量做成其本身是关于中心线对称的,以便左右可以共用一个零件;
11.非对称的注意事项:
由于底盘零件布置的变化,有些零件大体上是关于x-z平面对称的,但有些小的特征,如凸台、孔的尺寸、位置并不是关于x-z平面对称的,在利用左右对称copy功能做零件时应该特别注意,不要错误的copy非对称的特征;
12.地毯、地板隔热垫的设计:
地毯在布置设计时应考虑压缩量,一般为3mm;
13.倒角的问题
14.在设计建模初期就应该考虑到倒角的状态,比如:
所留的焊接边在倒角以后的宽度尺寸至少应大于10mm;所定的孔位在倒角以后应该不会位于倒角的圆弧面上;零件的边界在倒角后不应与倒角面干涉。
15.对于有配合关系的两个零件来说,更要注意倒角的大小关系,一般来说,被包容的零件的倒角应当大一些,以免干涉。
16.在倒角困难的情况下,有时候会通过修改型面以实现倒角要求,在这种情况下应注意与之配合的配合面、配合零件的相应修改。