木门厂质量管理办法1.docx
《木门厂质量管理办法1.docx》由会员分享,可在线阅读,更多相关《木门厂质量管理办法1.docx(4页珍藏版)》请在冰豆网上搜索。
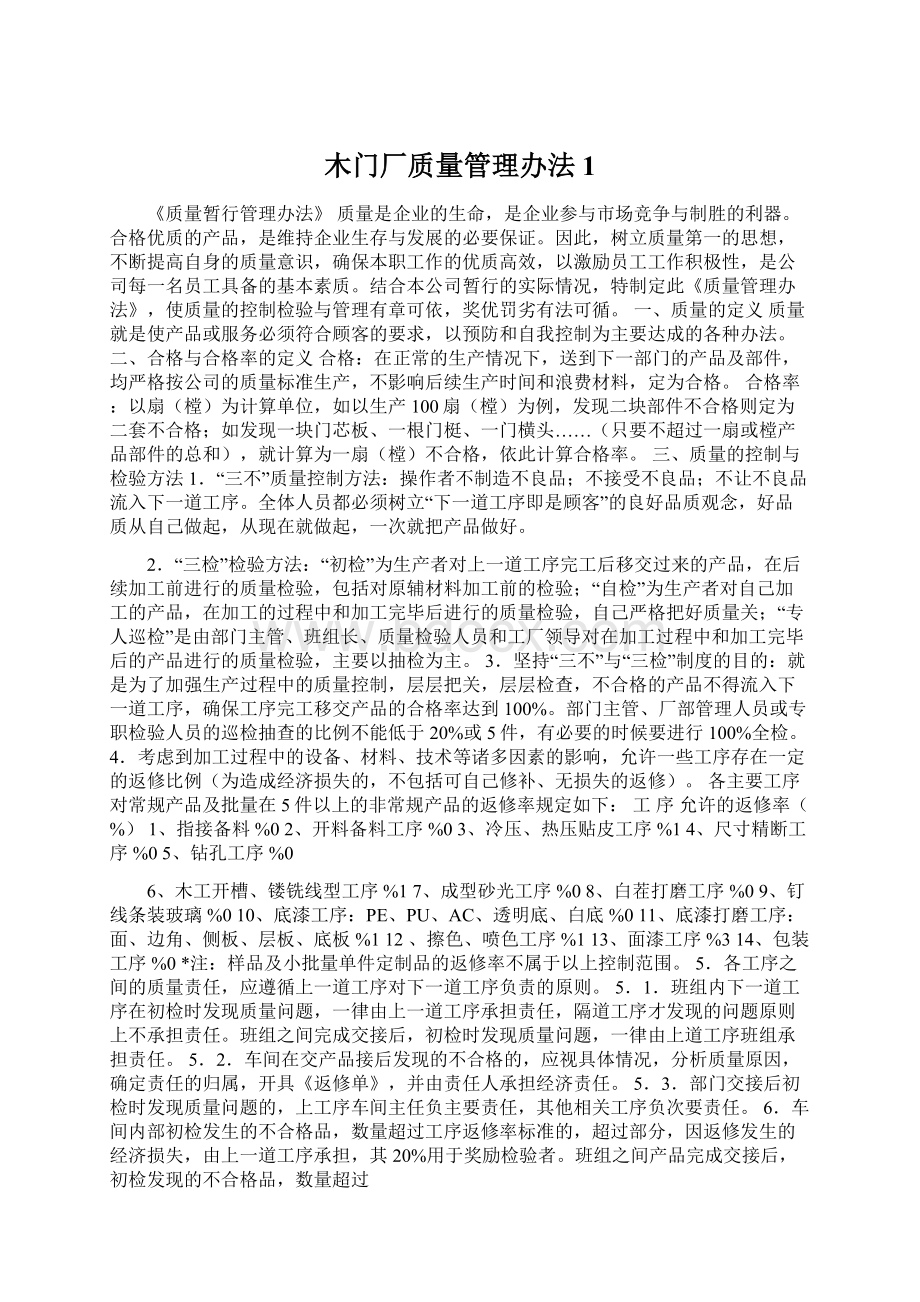
木门厂质量管理办法1
《质量暂行管理办法》质量是企业的生命,是企业参与市场竞争与制胜的利器。
合格优质的产品,是维持企业生存与发展的必要保证。
因此,树立质量第一的思想,不断提高自身的质量意识,确保本职工作的优质高效,以激励员工工作积极性,是公司每一名员工具备的基本素质。
结合本公司暂行的实际情况,特制定此《质量管理办法》,使质量的控制检验与管理有章可依,奖优罚劣有法可循。
一、质量的定义质量就是使产品或服务必须符合顾客的要求,以预防和自我控制为主要达成的各种办法。
二、合格与合格率的定义合格:
在正常的生产情况下,送到下一部门的产品及部件,均严格按公司的质量标准生产,不影响后续生产时间和浪费材料,定为合格。
合格率:
以扇(樘)为计算单位,如以生产100扇(樘)为例,发现二块部件不合格则定为二套不合格;如发现一块门芯板、一根门梃、一门横头……(只要不超过一扇或樘产品部件的总和),就计算为一扇(樘)不合格,依此计算合格率。
三、质量的控制与检验方法1.“三不”质量控制方法:
操作者不制造不良品;不接受不良品;不让不良品流入下一道工序。
全体人员都必须树立“下一道工序即是顾客”的良好品质观念,好品质从自己做起,从现在就做起,一次就把产品做好。
2.“三检”检验方法:
“初检”为生产者对上一道工序完工后移交过来的产品,在后续加工前进行的质量检验,包括对原辅材料加工前的检验;“自检”为生产者对自己加工的产品,在加工的过程中和加工完毕后进行的质量检验,自己严格把好质量关;“专人巡检”是由部门主管、班组长、质量检验人员和工厂领导对在加工过程中和加工完毕后的产品进行的质量检验,主要以抽检为主。
3.坚持“三不”与“三检”制度的目的:
就是为了加强生产过程中的质量控制,层层把关,层层检查,不合格的产品不得流入下一道工序,确保工序完工移交产品的合格率达到100%。
部门主管、厂部管理人员或专职检验人员的巡检抽查的比例不能低于20%或5件,有必要的时候要进行100%全检。
4.考虑到加工过程中的设备、材料、技术等诸多因素的影响,允许一些工序存在一定的返修比例(为造成经济损失的,不包括可自己修补、无损失的返修)。
各主要工序对常规产品及批量在5件以上的非常规产品的返修率规定如下:
工序允许的返修率(%)1、指接备料%02、开料备料工序%03、冷压、热压贴皮工序%14、尺寸精断工序%05、钻孔工序%0
6、木工开槽、镂铣线型工序%17、成型砂光工序%08、白茬打磨工序%09、钉线条装玻璃%010、底漆工序:
PE、PU、AC、透明底、白底%011、底漆打磨工序:
面、边角、侧板、层板、底板%112、擦色、喷色工序%113、面漆工序%314、包装工序%0*注:
样品及小批量单件定制品的返修率不属于以上控制范围。
5.各工序之间的质量责任,应遵循上一道工序对下一道工序负责的原则。
5.1.班组内下一道工序在初检时发现质量问题,一律由上一道工序承担责任,隔道工序才发现的问题原则上不承担责任。
班组之间完成交接后,初检时发现质量问题,一律由上道工序班组承担责任。
5.2.车间在交产品接后发现的不合格的,应视具体情况,分析质量原因,确定责任的归属,开具《返修单》,并由责任人承担经济责任。
5.3.部门交接后初检时发现质量问题的,上工序车间主任负主要责任,其他相关工序负次要责任。
6.车间内部初检发生的不合格品,数量超过工序返修率标准的,超过部分,因返修发生的经济损失,由上一道工序承担,其20%用于奖励检验者。
班组之间产品完成交接后,初检发现的不合格品,数量超过
工序返修率标准的,超过部分因返工发生的经济损失,由上道工序班组和车间主任承担,其20%用于奖励初检检验者。
初检不合格品的型号、数量、不合格原因应在当时填写于《车间生产日报表》和《返修单》上,立即报厂部以便于计算损失和奖励金额。
如果发现有质量问题,不上报而直接返工的,发现一例,按所有成本的100%处罚检验(包括初检者)。
7.车间产品移交的规定7.1.产品移交必须先进行自检,以检验产品的孔位、尺寸、线形、整体造型的准确性,检验必须完整、全面。
由部门主管负责进行组织,质量检验人员监督执行,移交产品时应通知检验人员到场进行评定,不合格的产品不得继续生产或移交下一道工序后续生产。
7.2.车间内部检验合格的产品,质量检验人员必须对其组成的板(部)件进行抽检,抽检的比例不得少于20%(或5件)。
7.3.车间班组完工移交产品的检验合格率规定如下(批量50扇以上):
班组合格率合格率指接、备料100%成型组装、99%整修99%油漆打磨、100%油漆(底、面漆)97%包装100%7.4.移交结束的产品,在后续加工的过程中,发现因前道工序加工造成的不合格品,应立即开具《返修单》退回前道工序进行返修。
返修品数量在规定的返修率内的,前道工序不承担经济责任,返修数量
超过规定返修率的,前道工序要承担由此造成的经济损失。
返修率=1-产品合格率=返修产品的数量/移交产品的数量/100%(注)以上产品合格率规定:
工序合格率为板件数量的合格率;班组移交产品的合格率为成套产品的合格率。
四、对各部门的考核1.公司产品合格率最终是以发出产品的开箱合格率来计算的。
1.1.产品合格率=发出产品中不合格品数量÷发出产品数量*100%1.2.发出产品中不合格数量为当月所有因生产原因造成的不合格退货返修产品的总件数,不包括运输、工地损坏的产品。
1.3.发出产品总量为当月发出产品的总件数。
1.4.计算时间为上月公司另外在定。
1.5.发出产品数量与退、返修产品的时间忽略不计,外地发生的退换货产品以工厂收到时间为准。
2.对生产工人的考核2.1.个人当月发出产品合格率达到98%的,每上升一个百分点奖励增加50元。
2.2.个人当月发出产品合格率低于98%的,每减少一个百分点罚款50元。
并视情况决定是否要赔偿其他相应费用。
2.3.不足一个百分点的按比例增减奖罚金额,经济损失另外计算。
3.对车间生产管理(检验)人员的考核3.1.生产管理(检验)人员的工作业绩与本车间完工并移交的产品
合格率挂钩,当月累计达到本车间移交产品合格率的,对生产管理人员一次性奖励100以上元。
达不到产品移交合格率的每降低一个百分点,罚款100以上元。
3.2.当月发出产品合格率达到(上述7.3条)规定的,生产管理人员一次性奖励100元,每超过一个百分点增加100元。
3.3.当月发出产品合格率低于上述规定的,每减少一个百分点,对生产管理人员罚款100元。
五、不合格品经济损失赔偿规定1.以公司相关规定处罚。
六、经济损失的计算1.指接、备料、开料组内部发生的质量事故,经济损失=生产材料成本×1.1计算;2.贴皮组内部发生的质量事故,经济损失=材料成本×1.1计算;3.成型组装组内部发生的质量事故,经济损失=材料成本×1.2计算4.整修组内部发生的质量事故,经济损失=材料成本×1.3计算5.底漆发生的质量事故,经济损失=材料成本×1.4计算6.打磨组发生的质量问题,经济损失=材料成本×1.5计算(底漆)--1.6计算(面漆)7.面漆发生的质量事故,经济损失=材料成本×1.6计算8.包装组发生的质量事故,经济损失=材料成本×1.7计算9.材料成本计算原则:
A.板材:
以实际面积÷80%×单价计算
B.木材:
按板面每立方米÷60%×单价计算C.木皮:
按板面实际面积÷70%×单价计算D.底漆:
一遍15元/平方米E.面漆:
一遍20元/平方米F.擦色、修色:
5元/平方米+底漆或面漆平方价G.打磨:
底漆20元/平方米;面漆25元/平方米H.五金、包装物品按采购成本×1.1计算10.人为原因产生报废的,按材料成本的100%计算损失。
七、成品库的质量管理1.成品库在接收包装完工的时侯,应做到:
A.检查外包装的完好程度;B.检查外包装的标示填写是否完整、齐全(包括批号、包装章、颜色章等);C.对完工产品进行抽检,检查外包装的标示与包装内的产品,是否一致;D.核对产品数量。
2.成品库的产品堆放应根据不同产品的结构特点,分别确定堆放的方式及高度,使仓储库损减少到最低。
3.成品库的发货准确率为100%,发出商品要严格按发货清单执行,不得有错发、漏发,有批号要求的不得混合配发。
如发生错发、漏发或混发,造成客户退货现象,库管员必须全额赔偿因此而造成的损失,如影响巨大,除全额赔偿损失以外,将按照公司的相关规定处罚。
4.成品库在装车、卸车、搬运、整理仓库时,一定要文明操作,绝对禁止野蛮装卸、操作。
5.成品库每月发生的库损,不得超过库存产品的万分之一,超过部分,成品库要承担经济损失的赔偿,由于野蛮装卸造成的损失全额赔偿。
八、技术部门的质量管理1.技术部负责生产所需要的所有技术文件的制定,并以此指导生产顺利进行,因此技术部门必须做到:
A.打样产品的技术文件根据需要随时跟踪;B.内销定型产品必须在产品定型后在公司规定的时间内完成全面技术文件的制定;C.内销产品的改型,相应技术文件的修改,在公司规定的时间内,同时通知各有关部门,包括(车间、家伙、采购、仓库、销售和质量检验人员);D.由于产品改型未能及时通知销售、仓库、车间等有关部门,造成退货、换货等,由此造成的损失,设计部门要承担经济损失;E.由于技术文件的原因造成的产品质量事故,技术部门承担经济损失。
2.技术文件中应包括如下内容:
A.产品下料清单;B.产品加工孔位图、线形大样图;C.产品包装作业指导,及包装箱规格尺寸;D.产品材料清单,包括玻璃、五金配件清单;E.产品的装配、安装图纸;
F.产品的制造成本预算与核算;G.物料、人工定额。
九、质量(检验)管理人员的工作职责范围1.质量(检验)管理人员包括:
品质检验人员、部门主管(班组长)和厂部生产负责人。
2.品质检验人员的职责范围:
2.1.根据车间所加工产品的技术质量标准,在车间内巡检,随时抽查产品的加工质量。
2.2.对所有完工产品试装进行监督、检验,确保试装的完整性、全面性,不合格产品严禁流入下道工序或进入成品库。
如当时未发现品质不良现象,在下一部门(班组)生产时发现品质不良现象,如需承担经济损失的,员工负40%责任,部门主管(班组长)负60%责任。
2.3.对车间班组已完工,等待交接的产品进行检验,并在《工序流程卡》上签字确认。
未经检验的半成品、成品不得流入下一道工序。
2.4.对固装产品进行全检,对散装产品(零部件)批次数量大的抽检,抽检检验比例:
备料≥30%;成型≥20%;贴皮≥20%;整修≥20%油漆≥60%;包装≥20%;成品库≥5%(每批次)以抽检结果推断总体质量状况,低于合格率标准的增加抽检数量,或退回相关班组重新自检、维修,完成后再进行检验,直到达到合格率标准。
所有返回班组自检、维修的产品,返修不得超过2次,第三次质量检验人员有权拒检,并上报厂部。
2.5.对不合格产品,应立即会同车间班组负责人和相关技术工人、厂部技术管理人员分析原因,提出改进措施,并开具《质量事故报告单》,报厂部。
2.6.适时监督返修品的质量和进度,保证按时交货。
3.部门主管(班组长)的质量工作职责范围3.1.负责本部门加工产品的质量巡检,确保加工质量满足技术质量要求。
3.2.对本部门(及各班组)完工产品进行质量检验,并在《工序流程卡》上签字。
3.3.对不合格产品分析原因,追查责任,监督返修质量和保证货期。
3.4.严格要求自己下属的操作人员对其加工的产品(零部件)按《质量标准》规定的要求进行自检,相邻的两工序互检,共同把好质量关。
十、售后产品的质量管理1.产品发出后,由于各种原因造成损伤,需要回厂进行维修的,须由销售或成品库管人员依据客户反馈的信息先进行登记,并及时反映到生产部负责人,便于统一安排返修。
2.问题产品回厂后,由质量检验人员和相关部门对退回产品进行质量鉴定,确定责任归属,填写《质量事故报告单》,并及时上报生产负责人进行处理,计算损失。
3.所有需要维修的产品应在公司规定的时间内维修完成。
4.退回产品由运输公司造成的,由运输公司承担经济责任,并由相关联系人负责追回。
5.客户有关缺少板件、五金配件的质量投诉,如调查属包装组漏包错包等原因,由包装组承担责任,经济损失按实际损失全额计算。
6.退回产品经质量鉴定,属于相关班组在生产过程中造成的,由相关班组承担经济责任,经济损失按全额计算。
。
十一、此管理办法与《生产管理办法》配套实施,互相补充。
十二、此管理办法自公布日起正式执行,此前所有有关的质量问题均不在此规定内。
上海典藏门业有限公司