金工实习指导书热加工部分答案完整版.docx
《金工实习指导书热加工部分答案完整版.docx》由会员分享,可在线阅读,更多相关《金工实习指导书热加工部分答案完整版.docx(44页珍藏版)》请在冰豆网上搜索。
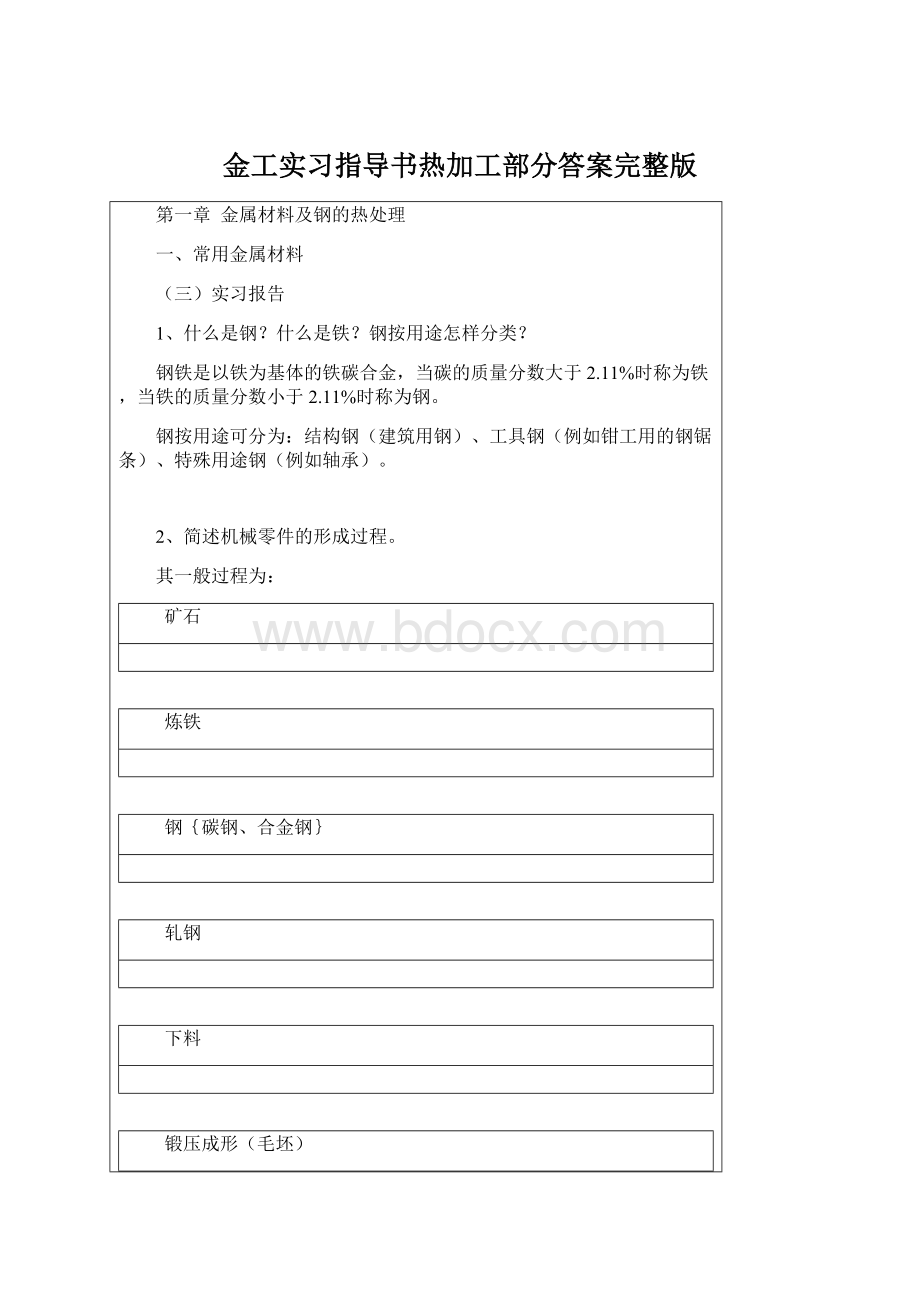
金工实习指导书热加工部分答案完整版
第一章 金属材料及钢的热处理
一、常用金属材料
(三)实习报告
1、什么是钢?
什么是铁?
钢按用途怎样分类?
钢铁是以铁为基体的铁碳合金,当碳的质量分数大于2.11%时称为铁,当铁的质量分数小于2.11%时称为钢。
钢按用途可分为:
结构钢(建筑用钢)、工具钢(例如钳工用的钢锯条)、特殊用途钢(例如轴承)。
2、简述机械零件的形成过程。
其一般过程为:
矿石
炼铁
钢{碳钢、合金钢}
轧钢
下料
锻压成形(毛坯)
热处理(退火、正火)
机加工
铸造
热处理(淬火、回火)
成品零件
3、列表综合Q235、45、ZG40Cr、T10A、20CrMnTi、GCr15、W18Cr4V等钢材的类别、牌号成分、性能、用途。
材料代号
类别
牌号或成分
性能
用途
Q235
普通碳素结构钢
C含量:
0.235%
韧性、塑性优良
建筑或对韧性要求较高的零件
45#
优质碳素结构钢
C含量:
0.45%
各项性能中等
制造各类常用零件
ZG40Cr
铸钢
C含量:
0.40%含铬合金
T10A
优质碳素工具钢
C含量:
10‰
硬度很高
适合做工具、刀具、模具
20CrMnTi
结构钢
C含量:
0.20%含铬锰钛合金
GCr15
轴承钢
轴承类
W18Cr4V
高速钢
车刀
4、什么叫有色金属?
举实例说明铝和铜在机器制造中的用途。
狭义上,有色金属是非铁金属,是铁、锰、铬以外金属的总称;广义上的有色金属还包括有色合金,它是以有色金属为基体(通常大于50%),加入一种或几种其他元素而构成的合金。
实例:
铝—电缆、电器零件、装饰品及日常生活用品;
铜—电线、导电螺钉、储藏器、各种管道。
5、影响金属材料的使用性能有哪些?
性能名称
性能内容
使
用
性
能
物理性能
包括密度、熔点、导电性、导热性、磁性等。
化学性能
金属材料抵抗各种介质的侵蚀能力,如抗腐蚀性能等。
力
学
性
能
强度
在外力作用下材料抵抗变形和破坏的能力,分为抗拉强度σb、抗压强度σbb、抗剪强度σr,单位均为MPa。
硬度
衡量材料软硬程度的指标,较常用的硬度测定方法有布氏硬度(HBS、HBW)、洛氏硬度(HR)和维氏硬度(HV)。
塑性
在外力作用下材料产生永久变形而不发生破坏的能力。
常用指标是伸长率δ(%)和断面收缩率ψ(%),δ和ψ愈大,材料塑性愈好。
冲击韧性
材料抵抗冲击力的能力。
常把各种材料受到冲击破坏时消耗能量的数值作为冲击韧性的指标,用αk(J/cm)表示。
冲击韧度值主要取决于塑性、硬度,尤其是温度对冲击韧度值的影响具有更重要的意义。
疲劳强度
材料在多次交变载荷作用下,不致引起断裂的最大应力。
工艺性能
包括热处理工艺性能、铸造性能、锻造性能、焊接性能、切削加工性能。
二、热处理理论基础及工艺概述
(三)实习报告
1、什么叫做热处理?
其作用是什么?
热处理是将材料放在一定的介质内加热、保温、冷却,通过改变材料表面或内部的组织结构,来控制其性能的一种综合工艺过程。
金属热处理是机械制造中的重要工艺之一,与其他加工工艺相比,热处理一般不改变工件的形状和整体的化学成分,而是通过改变工件内部的显微组织,或改变工件表面的化学成分,赋予或改善工件的使用性能。
其特点是改善工件的内在质量,从而获得最终的实用性能,而这一般不是肉眼所能看到的。
2、什么是退火、正火、淬火、回火方法?
各有什么作用?
退火是将工件加热到适当温度,根据材料和工件尺寸采用不同的保温时间,然后进行缓慢冷却,目的是使金属内部组织达到或接近平衡状态,获得良好的工艺性能和使用性能,或者为进一步淬火作组织准备。
正火是将工件加热到适宜的温度后在空气中冷却,正火的效果同退火相似,只是得到的组织更细,常用于改善材料的切削性能,也有时用于对一些要求不高的零件作为最终热处理。
淬火是将工件加热保温后,在水、油或其它无机盐、有机水溶液等淬冷介质中快速冷却。
淬火后钢件变硬,但同时变脆。
为了降低钢件的脆性,将淬火后的钢件在高于室温而低于650℃的某一适当温度进行长时间的保温,再进行冷却,这种工艺称为回火。
3、画出退火、正火、淬火、回火的热处理工艺曲线。
4、什么是渗碳处理?
其作用和实现的原理是什么?
表面渗碳处理:
将含碳(0.1~0.25%)的钢放到碳势高的环境介质中,通过让活性高的碳原子扩散到钢的内部,形成一定厚度的碳含量较高的渗碳层,再经过淬火、回火,使工件的表面层得到碳含量高的合金,而心部因碳含量保持原始浓度而得到碳含量低的合金,合金的硬度主要与其碳含量有关,故经渗碳处理和后续热处理可使工件获得外硬内韧的性能。
渗碳处理的作用是:
提高表面层的耐磨性(碳含量高的合金),同时保持心部有高的耐冲击能力,即强韧性以及良好的塑性,使零件既能承受磨损和拥有较高的表面接触应力,同时又能承受弯曲应力及冲击载荷。
渗碳处理用于在摩擦冲击条件下工作的零件,如汽车齿轮、活塞销等。
5、什么是氮化处理?
说明其作用和原理。
氮化处理:
在一定温度下,将工件置于渗氮介质中加热、保温,使活性氮原子渗入工件表层的化学热处理工艺。
零件渗氮后表面形成氮化层,氮化后不需淬火,钢件表层硬度可达950~1200HV,这种高硬度和高耐磨性可保持到560~600。
C而不降低,故氮化钢件具有很好的热稳定性,同时具有较高的抗疲劳性和耐腐蚀性且变形很小。
由于上述特点,渗氮在机械工业中得到了广泛应用,特别适宜于许多精密零件的最终热处理,例如磨床主轴,精密机床丝杆,内燃机曲轴以及各种精密齿轮和量具等。
6、何谓预备热处理?
何为最终热处理?
举例说明。
预备热处理包括退火、正火、调质等,退火、正火的工序位置,通常安排在毛坯生产之后、切削加工之前,以消除毛坯的内应力、均匀组织、改善切削加工性能,并为以后的热处理做组织准备。
调质工序一般安排在粗加工之后、精加工或半精加工之前,目的是为了获得更好的综合力学性能,为以后的热处理做组织准备。
调质一般不安排在粗加工之前,以免表面调质层在粗加工时大部分被切削掉,从而失去调质处理的作用。
最终热处理包括淬火、回火及表面热处理等。
零件经过此热处理后,获得所需的使用性能,因其硬度较高,除磨削外不宜进行其他形式的切削加工,故其工序位置一般均安排在半精加工之后。
三、热处理设备
(三)实习报告
1、试说明RX3—45—9、NLQ—75—9、DM—100—13、RJ2—55—6、GGC50—2设备的含义、工作原理、作用(或所能完成的工作等)。
并把这些设备的功率、电压、相数、额定温度(或工作温度)、工作空间及重量等综合列于一表内。
设备型号
名称
功率
电压
额定温度
RX3—45—9
箱式加热电阻炉
45kw
950℃
NLQ—75—9
井式气体渗碳电阻炉
75kw
950℃
DM—100—13
1300℃
RJ2—55—6
井式回火炉
55kw
650℃
GGC50—2
真空管式高频感应加热炉
50kw
380V
2、井式回火炉、井式氮化炉的工作过程或工作原理是什么?
3、可倾式回转炉的作用是什么?
其工作过程或工作原理是什么?
不
4、高频淬火的作用是什么?
简述其操作过程。
高频淬火是指利用高频电流(30k~100kHz)使工件表面局部加热、冷却,获得表面硬化层的热处理方法,这种方法只是对工件一定深度的表面强化,而心部基本上保持处理前的组织和性能,因而可获得高强度、高耐磨性和高韧性的综合性能。
又因为是局部加热,所以能显著减少淬火变形,减低能耗。
正是因为高频淬火拥有上述这些特点,因而在机械加工行业被广泛应用。
5、何谓发黑处理?
其工艺过程如何?
各道工序又有什么作用?
发黑处理是金属表面氧化处理中最常用的一种方法。
其中碱性发黑处理是将工件放在一定的温度的强碱性溶液中进行的氧化处理,它使工件表面形成一层氧化膜(Fe3O4),这层氧化膜组织较为紧密,能牢固地与金属表面结合,依据处理条件的不同,该氧化膜可呈现亮蓝色直到亮黑色,主要应用于碳素钢和低合金钢。
工艺原理:
当工件在浓度很高的碱性和氧化剂的溶液中加热时,表面开始先受到碱的微腐蚀作用,首先析出铁离子,与碱的氧化剂继续作用,生成亚铁酸钠(Na2FeO2)和铁酸钠(NaFe2O4),然后再由亚铁酸钠和铁酸钠进一步作用,生成成分为四氧化三铁的致密氧化膜。
作用:
它不仅对金属表面起防锈作用,还能增加金属表面的美观,对于淬火工件而言,还能起到消除应力的作用。
四、热处理实验和操作
(三)实习报告
1、简述ZG40Cr(采用当时生产中所处理的材料)热处理的整个工艺过程,并说明各工序的作用。
2、何谓调质处理?
处理后材料性能有何特点?
生产中那些零件要采用这种处理工艺。
调质处理是淬火后高温回火的热处理方法称为调质处理。
高温回火是指在500-650℃之间进行回火。
调质可以使钢的性能,材质得到很大程度的调整,其强度、塑性和韧性都较好,具有良好的综合机械性能。
调质处理后得到回火索氏体,它的机械性能均比相同硬度的正火索氏体组织为优,它的硬度取决于高温回火温度并与钢的稳定性和工件截面尺寸有关,一般在HB200~300之间。
调质常常应用在中碳(低合金)结构钢,也用在低合金铸钢中,对力学要求高的结构零部件都要进行调质处理。
调质处理广泛应用于各种重要的结构零件,特别是那些在交变负荷下工作的连杆、螺栓、齿轮及轴类等。
3、简述HRC、HBS、HV的基本原理和操作过程。
A、布氏硬度(HB)
用一定直径的钢球或硬质合金球,以规定的试验力(F)压入式样表面,经规定保持时间后卸除试验力,测量试样表面的压痕直径(L)。
布氏硬度值是以试验力除以压痕球形表面积所得的商。
以HBS(钢球)表示,单位为N/mm2(MPa)。
其计算公式为:
布氏硬度=F/A(压痕球形表面积)
式中:
F—压入金属试样表面的试验力。
测定布氏硬度较准确可靠,但一般HBS只适用于450N/mm2(MPa)以下的金属材料,对于较硬的钢或较薄的板材不适用。
在钢管标准中,布氏硬度用途最广,往往以压痕直径d来表示该材料的硬度,既直观,又方便。
举例:
120HBS10/1000130:
表示用直径10mm钢球在1000Kgf(9.807KN)试验力作用下,保持30s(秒)测得的布氏硬度值为120N/mm2(MPa)。
B、洛氏硬度(HR)
洛氏硬度试验同布氏硬度试验一样,都是压痕试验方法。
不同的是,它是测量压痕的深度。
即,在初始试验力(Fo)及总试验力(F)的先后作用下,将压头(金钢厂圆锥体或钢球)压入试样表面,经规定保持时间后,卸除主试验力,用测量的残余压痕深度增量(e)计算硬度值。
其值是个无名数,以符号HR表示,所用标尺有A、B、C、D、E、F、G、H、K等9个标尺。
其中常用于钢材硬度试验的标尺一般为A、B、C,即HRA、HRB、HRC。
硬度值用下式计算:
HR=(K-H)/C
K为常数,金刚石压头时K=0.2MM,淬火钢球压头时K=0.26MM;H为主载菏解除后试件的压痕深度;C也为常数,一般情况下C=0.002MM。
当用A和C标尺试验时,HR=100-e
当用B标尺试验时,HR=130-e
式中e—残余压痕深度增量,其什系以规定单位0.002mm表示,即当压头轴向位移一个单位(0.002mm)时,即相当于洛氏硬度变化一个数。
e值愈大,金属的硬度愈低,反之则硬度愈高。
上述三个标尺适用范围如下:
HRA(金刚石圆锥压头)20-88
HRC(金刚石圆锥压头)20-70
HRB(直径1.588mm钢球压头)20-100
洛氏硬度试验是目前应用很广的方法,其中HRC在钢管标准中使用仅次于布氏硬度HB。
洛氏硬度可适用于测定由极软到极硬的金属材料,它弥补了布氏法的不是,较布氏法简便,可直接从硬度机的表盘读出硬度值。
但是,由于其压痕小,故硬度值不如布氏法准确。
(3)维氏硬度,由英国科学家维克斯首先提出。
以49.03~980.7N的负荷,将相对面夹角为136°的方锥形金刚石压入器压材料表面,保持规定时间后,用测量压痕对角线长度,再按公式来计算硬度的大小。
它适用于较大工件和较深表面层的硬度测定。
维氏硬度尚有小负荷维氏硬度,试验负荷1.961~<49.03N,它适用于较薄工件、工具表面或镀层的硬度测定;显微维氏硬度,试验负荷<1.961N,适用于金属箔、极薄表面层的硬度测定。
维氏硬度计测量范围宽广,可以测量目前工业上所用到的几乎全部金属材料,从很软的材料(几个维氏硬度单位)到很硬的材料(3000个维氏硬度单位)都可测量。
计算公式为:
P为载荷,如10kg。
d为压痕对角线长度(mm)。
4、热处理中易产生哪些缺陷?
有什么危害?
如何防止?
(1)、热处理工艺选择不当对工件的质量产生较大的影响,如淬火工艺的选择不当,容易使淬火工件力学性能不足或产生过热,晶粒粗大和变形开裂等缺陷,严重的会造成零件报废。
(2)、加热不当,会造成过热、过烧,表面氧化和脱碳等问题。
过热使工件的塑性、韧性显著降低,冷却时产生裂纹,过热可通过正火予以消除。
过烧是加热温度接近开始熔化温度,过热后的钢强度低、脆性大只能报废。
生产上应严格控制加热温度和保温时间,钢在高温加热过程中,由于炉内的氧化性气氛造成钢的氧化(铁的氧化)和脱碳。
氧化使金属消耗,工件表面硬度不均,脱碳使工件淬火后硬度、耐磨性、疲劳强度严重下降。
为防止氧化和脱碳,常采用保护气氛加热或盐浴加热等措施。
(3)、在冷却中有时会产生变形和开裂现象,变形和开裂主要是由于加热或冷却速度过快,加热或冷却不均匀等产生的应力造成的。
生产中常采用正确的热处理工艺,淬火后及时回火等措施来防止。
(4)、加热温度或保温的时间不足、冷却速度太慢、工件表面脱碳造成淬火剂温度过高或冷却速度不均匀,会带来表面硬度不均等缺陷,这些都是制定热处理工艺所必须考虑的基本问题。
5、记录G45#经退火、正火、淬火,高温回火后的洛氏硬度值,经氮化或渗碳后的显微硬度值。
对其结果做必要的分析(同学自备报告纸一张)。
第二章铸造
一、铸造概况、浇注系统整体无芯模、挖砂模造型
(三)实习报告
1、进入铸工车间应注意哪些安全问题?
(1)、 上班前要穿戴好工作服等防护用品。
(2)、 砂箱堆放要平稳,搬动砂箱要注意轻放,以防砸伤手脚。
(3)、 造型(芯)时不可用嘴吹型(芯)砂,以防飞砂伤割眼睛。
(4)、 浇注时,浇包必须烘干且浇包内的金属液不可过满,一般不超过浇包容量的80%,不操作浇注的同学应远离浇包。
(5)、 浇注过程中要听从指挥,注意安全。
(6)、 铸件冷却后才能用手拿取。
(7)、 清理铸件时,要注意周围环境,防止伤人。
(8)、 工作结束时要清理现场,工具要装入工具箱,摆放整齐。
2、用图表示砂型铸造生产过程。
3、标出铸型装配图及带浇注系统铸件的各部分名称,并分析浇注系统各部分作用。
⑴主流道:
从注射机喷嘴与模具接触处起到分流道为止的一段料流通道,负责将塑料熔体从喷嘴引入模具。
⑵分流道:
主流道与浇口之间的料流通道,是塑料熔体由主流道流入模腔的过渡段,负责将熔体的流向进行平稳的转换,在多模腔中还起着将熔体向各个模腔分配的作用。
⑶浇口:
分流道与模腔之间长度非常短、截废料又很狭窄的一段料流通道,其主要作用如下。
①因浇口截废料狭窄,所以可使经过分流道之后,压力和温度都已有所下降的塑料熔体产生加速度和较大的剪切热,保证熔体充模时具有较快的流动速度和较好的流动性。
②因其长度短、截废料狭窄,所以浇口内可容纳的塑料熔体体积很小,故很容易冷却固化(俗称浇口冻结),从而有助于防止保压力不足或保压时间过短而引起的倒流现象。
③由于截面狭窄,所以在浇口内冷却固化的塑料熔体(废料)强度很低,非常容易断裂,故便于制品和废料分离,并便于制品脱模。
④浇口的长度和截面尺寸一般均可在试模过程中适当调整。
特别是调整其截面尺寸时,截面高度的变化对浇口的容积及浇口冻结时间影响很大;另外,截面积的变化对塑料熔体内的切变速率影响很大,而切变速率又与熔体表观粘度有关,所以改变浇口截面尺寸或截面积的大小,可以控制浇口冻结时间(即补缩时间或补缩程度),以及熔体充模时的流动性能。
⑷冷料穴:
冷料穴一般开设在主流道末端,当分流道较长时,其末端也可设冷料穴。
冷料穴的作用是收集每次注射成型时流动熔体前端的冷料头(前锋冷料),避免这些冷料进入模腔影响制品成型质量,或防止这些冷料堵塞浇口造成制品缺料。
如果需要防止模腔内不同流向的熔体汇合时因冷料头而影响熔接痕的强度,亦可将冷料穴就近开设在熔体汇合之处的模腔外,并与模腔连通。
4、冒口有什么作用?
如何放置?
冒口用于浇铸的时候排出模具中的空气、浇铸金属汁中的杂质等。
一般小的铸件可以不设冒口,稍大的铸件设在离浇口较远的一侧,特别大的浇口设在两端,冒口设在中央。
5、通过挖砂造型说明为什么要设置分型面?
分型面一般都是平面,当分型面为阶梯形或曲面时,则需要通过挖砂来将分型面露出,以便于起模
思考:
浇注系统开设的合理与否与铸件质量有何关系?
浇注系统是液态金属充填铸型型腔的通道,是铸造工艺设计中的一个重要组成部分。
浇注系统设计的成败,直接影响到铸件的质量和成品率。
根据现场资料统计分析,因浇注系统设置不当,常导致气孔、裂纹、疏松、缩孔以及冷隔和浇不足等多种铸造缺陷的产生,其比率占铸件废品量的30%以上。
二、型砂、整体有芯模样造型
(三)实习报告
1、湿型砂的组成是什么?
湿型铸造用型砂的组成物除了旧砂、新砂以外,还加入水、膨润土、煤粉等材料。
此外还有可能加入其它附加物如糊精、-淀粉、重油液、纸浆废液、糖浆、木粉等。
2、记录湿型砂的混制工艺及过程。
混制工艺:
碾轮式混砂机、摆轮式混砂机、转子式混砂机。
湿型砂的制配过程是:
先加入新砂、旧砂、膨润土和煤粉等干混2~3min,再加水湿混5~12min,性能符合要求后即从出砂口卸砂。
混好的型砂应堆放4~5h,使粘土膜内水分均匀(调匀)。
使用前还要用筛砂机或松砂机进行松砂,以打碎砂团和提高型砂性能,使之松散好用。
3、干、湿型砂在组成、性能和用途上有何不同?
干型砂中常用普遍粘上,湿型砂中常用膨润土。
干型砂有较高的干强度和较高的透气性,不轻易产生冲砂、粘砂、气孔等缺陷。
湿型砂具有湿度、流动性、强度、可塑性与韧性、不粘模性。
4、型砂的性能是什么?
对铸件质量产生什么影响?
型砂应具备:
可塑性、具有一定的强度、良好的耐火性透气性,及一定的退让性。
影响:
1.型砂的粒度决定铸件的表面质量即粗糙度,一般沙粒越细越好;2.型砂的黏度决定型腔抗铸液的冲击性能和型腔的成型能力,沙粒不易脱落,一般越粘越好;3.具体成分决定型腔受温度收缩影响程度和型砂熔点;4.透气性决定型腔的排气能力,也即铸液的充满型腔能力,一般越好越容易保证铸液充满型腔。
5、铸铁、铸钢、有色金属选用型砂有何不同?
为什么?
铸铁用石英沙,加陶土,煤粉和水混合而成。
石英沙耐高温,陶土粘接剂,煤粉能使铸件光滑。
铸钢件用湿型砂中不加煤粉,因为铸钢湿型砂要求是耐火度及气流通畅及渗碳原因,而不是铸铁湿型砂要求造还氧性气氛的气膜。
有色金属用炉衬砂和天然砂,其中含游离二氧化硅70%以上。
6、型芯的工作环境如何?
常用的芯砂有哪些?
高温。
常由原砂和粘结剂(水玻璃、树脂等)配成的芯砂。
7、如何简化复杂铸件的造型工艺和形成铸件内部形状?
从造型的角度看:
内外表面的局部凸起要尽量设置在分型面上,避免曲面分型;外表和内腔以分型面为基准,逐步减少投影面积,以便于拔模,规避设置活块。
从铸件避免因热应力而开裂的角度,壁厚要均匀,避免突变或尖角过渡,对热节点(转角、交叉点)处要特别注意。
从铸造缺陷规避的角度,回避需大面积加工的平面。
三、砂型铸造工艺、三通模样造型
(三)实习报告
2、确定三通铸件的分型面、浇注位置、大致的工艺参数和浇冒口系统,并绘制工艺简图。
3、芯头和芯座间有什么关系?
铸型上和模样上芯头位置是如何考虑的?
芯头的尺寸和型腔上芯座尺寸相配合,保证砂芯安装稳定。
砂芯与铸型连接的部分,称为芯头,芯头是砂芯的重要组成部分,它起着固定砂芯、支撑和排气的作用,芯头不与金属液接触,不构成铸件轮廓,芯头必须要能承受砂芯的重力和金属液的浮力,要使下芯合型方便,有适当的斜度和间隙来适应砂芯和铸型的制造误差又要少出飞翅,要考虑到砂芯的堆放搬运方便。
4、何为三箱造型,它与二箱造型有哪些不同?
三箱造型定义:
用三个砂箱制造铸型的方法。
二箱造型是用两个砂箱制造铸型的方法
四、铸铁的熔化、浇注和活块造型
(三)实习报告
1、画出冲天炉简图,并注明各部门名称和作用。
2、简述冲天炉工作原理、操作过程及所要完成的任务。
冲天炉,将铸铁块熔化成铁水后浇注到砂型中待冷却后开箱而得到铸件。
冲天炉的工作过程:
先将一定量的煤炭装入炉内作为底焦,点火后,将底焦加至规定高度,然后按炉子的熔化率将配好的石灰石、金属炉料和层焦按次序分批地从加料口加入。
在整个开炉过程中保持炉料顶面在加料口下沿。
经风口鼓入炉内的空气同底焦发生燃烧反应,生成的高温炉气向上流动,对炉料加热,并使底焦顶面上的第一批金属炉料熔化。
熔化后的铁滴在下落到炉缸的过程中,被高温炉气和炽热的焦炭进一步加热。
随着底焦的烧失和金属炉料的熔化,料层逐渐下降。
每批炉料熔化后,燃料由外加的层焦补充,使底焦高度基本上保持不变,整个熔化过程连续进行。
3、冲天炉炉料的组成及其作用?
生铁,焦炭,石灰石。
作用分别是:
铁来源;燃料并且与生铁中的部分氧化铁发生还原反应;石灰石起到熔解杂质和渣的作用最后生成炉渣。
4简述铝合金熔炼原理、过程及注意事项。
在铝中加入某些其他元素,可改变铝的某些性质,改善其性能。
铝合金熔炼过程如下:
装炉→熔化(加铜、锌、硅等)→扒渣→加镁、铍等→搅拌→取样→调整成分→搅拌→精炼→扒渣→转炉→精炼变质及静置→铸造。
注意事项:
1、控制好熔炼温度2.选用优良的熔剂和适当的精炼工艺 3.晶粒细化。
5、浇注过程应注意哪些问题?
在浇注前应将空浇注包进行全面检查,视其是否符合要求,并检查机械传动装置是否灵活、可靠,还要检查吊装设备及运送设备是否完好。
浇注时,所有和金属熔液接触的工具,如扒渣棒、火钳等均需预热,因冷工具接触会产生飞溅。
浇注时,型腔内的气体、型砂水分及可燃物等,受热后迅速膨胀、气化、燃烧而由出气孔和冒口溢出,要及时引火燃烧,以免引起爆炸或一氧化碳中毒。
浇注包盛铁水不得太满,不得超过容积的80%,以免洒出伤人。
浇注后的剩余铁水、铁渣要倾倒在专用的砂坑、渣坑或渣包内。
无论是合箱还是浇注,往往是集体操作,因此,现场应有专人统一指挥,要有口令或手势作信号,以免行动不协调而造成事故。
6、什么情况下采用活块造型?
活块造型有何优缺点?
当模样上有妨碍起模的侧面部分伸出部分时,常将该部分做成活块。
起模时,先将模样主体取出,再将留在铸型内的活块单独取出,这种方法称为活块造型。
活块用销式燕尾与模样的主体连接,在起模时须先取出模样主体,然后取出活块。
活块造型的操纵难度较大,生产率低,仅适用于单件生产。
7、画出活块模样造型合箱图和比较分型面选择方案。
思考:
熔炼与铸件质量有何关系?
熔炼是生产高质量铸铁件的前提和基础,铸铁的熔炼技术直接影响铸造企业产品质量控制水平。
铸铁的内在质量、外观质量,以及缺陷的控制都与铁液质量有直