普通机床的数控化改造毕业论文.docx
《普通机床的数控化改造毕业论文.docx》由会员分享,可在线阅读,更多相关《普通机床的数控化改造毕业论文.docx(21页珍藏版)》请在冰豆网上搜索。
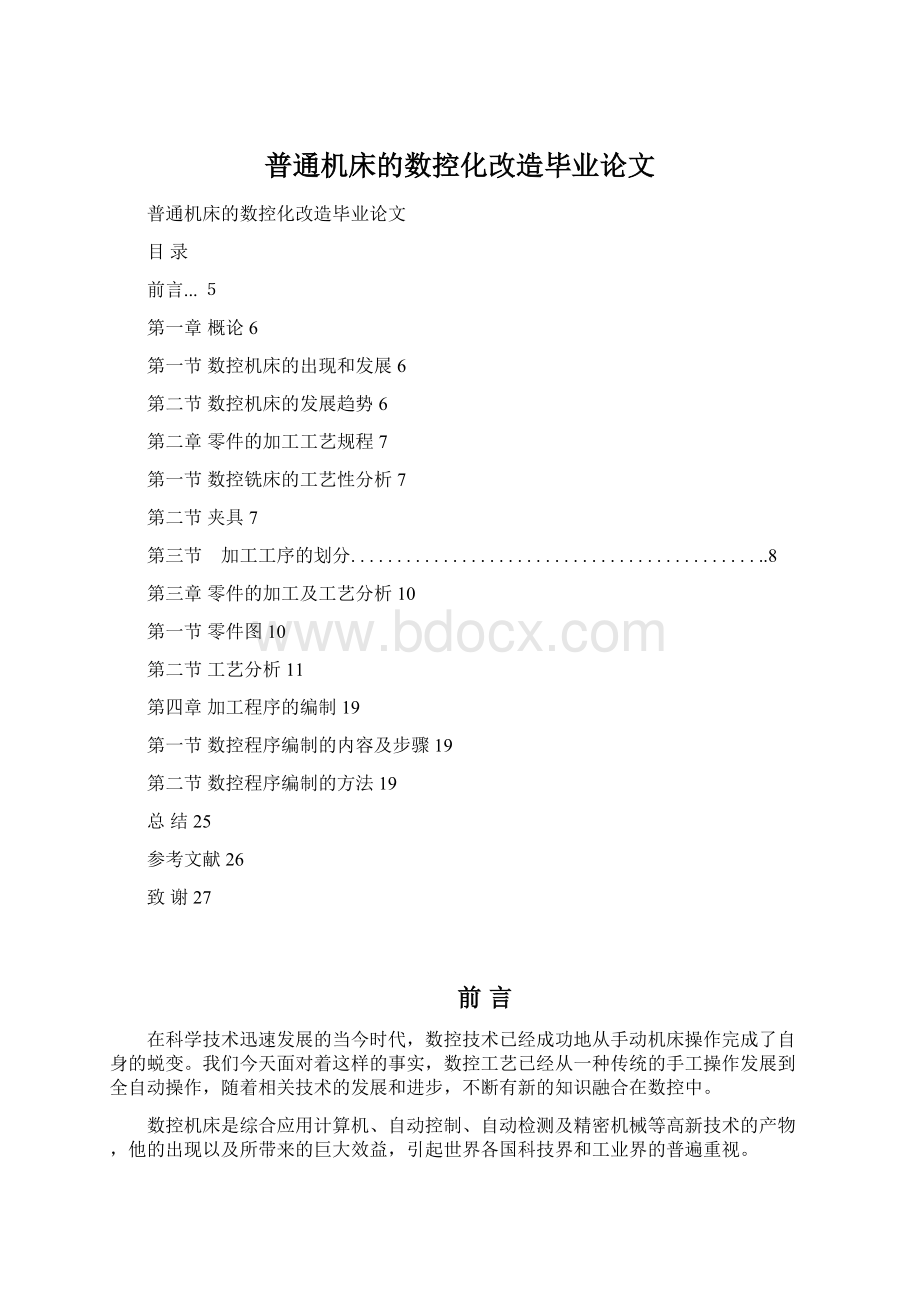
普通机床的数控化改造毕业论文
普通机床的数控化改造毕业论文
目录
前言...5
第一章概论6
第一节数控机床的出现和发展6
第二节数控机床的发展趋势6
第二章零件的加工工艺规程7
第一节数控铣床的工艺性分析7
第二节夹具7
第三节 加工工序的划分..............................................8
第三章零件的加工及工艺分析10
第一节零件图10
第二节工艺分析11
第四章加工程序的编制19
第一节数控程序编制的内容及步骤19
第二节数控程序编制的方法19
总结25
参考文献26
致谢27
前言
在科学技术迅速发展的当今时代,数控技术已经成功地从手动机床操作完成了自身的蜕变。
我们今天面对着这样的事实,数控工艺已经从一种传统的手工操作发展到全自动操作,随着相关技术的发展和进步,不断有新的知识融合在数控中。
数控机床是综合应用计算机、自动控制、自动检测及精密机械等高新技术的产物,他的出现以及所带来的巨大效益,引起世界各国科技界和工业界的普遍重视。
随着科学技术的迅猛发展,数控机床已是衡量一个国家制造工业水平的重要标志。
发展数控机床是当前我国机械制造业技术改造的必由之路,是未来的、工厂自动化的基础。
数控机床的大量使用,需要大批能熟练掌握现代数控机床的编程、操作和维修的工程技术人员。
如果把数控加工编程比喻为我们生命中的阳光、空气和水,难免会感到夸张,但毋庸质疑的一点却是:
数控加工编程已经深深地溶入了现代工业经济中,并在其中显现了十分重要、甚至是不可替代的作用。
数控机床是一种高效的自动化加工设备,它严格按照加工程序,自动的对被加工工件进行加工。
我们把从数控系统外部输入的直接用于加工的程序称为数控加工程序,简称数控程序,它是机床数控系统的应用软件。
数控系统的种类繁多,它们使用的数控程序语言规则和格式也不尽相同,当针对某一台数控机床编制加工程序时,应该严格按机床编程手册中的规定进行程序编制。
第一章概论
第一节数控机床的出现和发展
数控是数字控制(Numericalcontrol)的简称,是近代发展起来的用数字化信息进行控制的自动控制技术。
其含义使用以数值和符号构成的数字信息自动控制机床的运转,数控机床也称NC机床。
随着科学技术的发展,数控系统进过了以下几代的发展:
第一代:
1952年,电子管控制的第一台三坐标联动的铣床;
第二代:
1959年,出现了晶体管控制的“加工中心”;
第三代:
1965年,出现了小规模集成电路。
使数控系统的可靠性得到了进一步的提高;
以上三代数控系统都是采用专用控制硬件逻辑数控系统,称为普通数控系统,即NC系统。
第四代:
1967年以计算机作为控制单元的数控制系统FMS(FlexibleManufacturingSystem),柔性制造系统;
第五代:
1970年,美国英特尔开发使用了微处理器——CNC。
第二节数控机床的发展趋势
一、数控系统发展趋势
1、采用开放式结构:
进线、联网、专用要求。
2、向智能化发展。
3、具有自动编程、模糊控制、学习控制、自适应控制、工艺参数自动生成、三维刀具补偿、运动参数动态补偿,人机界面极为友好,有故障专家诊断系统。
二、数控机床发展趋势
1、高速、高效、高精度、高可靠性。
2、模块化、专门化、个性化;智能化、柔性化和集成化。
第二章零件的加工工艺规程
第一节数控铣床的工艺性分析
数控铣削加工的工艺性分析是编程前的重要工艺准备工作之一,关系到机械加工的效果和成败,不容忽视。
由于数控机床是按照程序来工作的,因此对零件加工中所有的要求都要体现在加工中,如加工顺序、加工路线、切削用量、加工余量、刀具的尺寸及是否需要切削液等都要预先确定好并编入程序中。
数控铣削加工有着自己的特点和适用对象,若要充分发挥数控铣床的优势和关键作用,就必须正确选择数控铣床类型、数控加工对象与工序内容。
通常将下列加工内容作为数控铣削加工的主要选择对象:
1工件上的曲线轮廓,特别是有数学表达式给出的非圆曲线与列表曲线等曲线轮廓。
2已给出数学模型的空间曲面;如在图中要加工出六边形时,应先在CAD程序中按其轮廓以缩小的方式画出其图形,至到最后直径小于20时。
3形状复杂、尺寸繁多、划线与检测困难的部位。
4用通用铣床加工时难以观察、测量和控制进给的内外凹槽。
5以尺寸协调的高精度孔或面。
6能在一次安装中顺带铣出来的简单表面或形状。
7采用数控铣削后能成倍提高生产率,大大减轻体力劳动强度的一般加工内容。
第二节夹具
在数控机床上加工零件,由于工序集中往往是在一次装卡中完成全部工序。
因此,对零件的定位、夹紧方式要注意以下几个方面。
一、在选用夹具时应综合考虑产品的生产批量、生产效率、质量保证及经济性等问题。
在小批量时应尽量采用组合夹具;当工件批量较大、精度要求较高时可以考虑设计专用夹具,或采用多工位夹具及气动、液压夹具。
但此类夹具结构较复杂,造价往往较高,而且制造周期较长。
二、零件定位、夹紧的部位应不妨碍各部位的加工、刀具更换以及重要部位的测量。
尤其要避免刀具与工件、刀具与夹具相撞的现象。
三、夹紧力应力求通过靠近主要支撑点或在支撑点所组成的三角形内。
应力求靠近切削部位,并在刚性较好的地方。
尽量不要在被加工孔径的上方,以减少零件变形。
四、零件的装卡、定位要考虑到重复安装的一致性,以减少对刀时间,提高同一批零件加工的一致性。
一般同一批零件采用同一定位基准,同一装卡方式。
根据零件图分析,此零件外型规则,被加工部分的各尺寸、形位及凹凸配合等要求较高。
零件结构较为复杂,包含了平面、圆弧,内外轮廓,挖槽的加工度。
工件选用机用平口钳装夹,校正平口钳固定钳口,使之与工作台X轴移动方向平行。
在工件下表面与平口钳之间放入精度较高的平行垫块(垫块厚度与宽度适当),利用木锤或铜棒敲击工件,使平行垫块不能移动后夹紧工件。
利用寻边器找正工件X,Y轴零点,该零点位于工件上表面的中心位置,设置Z轴零点与机械零点重合。
刀具长度补偿利用Z轴定位器设定。
对于同一把刀具仍调用相等的刀具长度与半径补偿值,但它们设定的工件坐标系不同。
有时也可能不使用刀具长度补偿功能,而根据不同刀具设定多个工件坐标系零点进行编程加工。
第三节:
加工工序的划分
在数控机床上特别是在加工中心上加工零件,工序十分集中,许多零件只需在一次装卡中就能完成全部工序。
但是零件的粗加工,特别是铸、锻毛坯零件的基准平面、定位面等的加工应在普通机床上完成之后,再装卡到数控机床上进行加工。
这样可以发挥数控机床的特点,保持数控机床的精度,延长数控机床的使用寿命,降低数控机床的使用成本。
在数控机床上加工零件其工序划分的方法有
一、刀具集中分序法
即按所用刀具划分工序,用同一把刀加工完零件上所有可以完成的部位,在用第二把刀、第三把刀完成它们可以完成的其它部位。
这种分序法可以减少换刀次数,压缩空程时间,减少不必要的定位误差。
二、粗、精加工分序法
这种分序法是根据零件的形状、尺寸精度等因素,按照粗、精加工分开的原则进行分序。
对单个零件或一批零件先进行粗加工、半精加工,而后精加工。
粗精加工之间,最好隔一段时间,以使粗加工后零件的变形得到充分恢复,再进行精加工,以提高零件的加工精度。
三、按加工部位分序法
即先加工平面、定位面,再加工孔;先加工简单的几何形状,再加工复杂的几何形状;先加工精度比较低的部位,再加工精度要求较高的部位。
本设计的数控加工工序:
数控加工削铣分7次切削进行加工:
1、用直径φ10mm的铣刀加工零件的四个方角;2、使用直径为φ10mm的铣刀加工零件中的四方形槽;3、用直径为φ10mm的铣刀加工零件中的直径为φ70mm的圆槽;4、用直径为φ10mm的铣刀加工零件中的六方形;5、选用直径为φ10mm的铣刀加工零件中直径为φ20mm的圆槽;6、用直径为6的铣刀加工零件中的直径为φ12mm的孔;7、用直径为φ6的铣刀加工零件中直径为φ6mm的圆孔。
(见第三章图一)
表一:
数控加工工序卡
机械厂
数控加工工艺卡
产品名称或
代号
零件名称
零件图号
零件
0403-13
工艺序号
程序编号
夹具名称
夹具编号
使用设备
车间
%0403
定心心轴
数控铣床
机3
工步号
工步内容
加工面
刀具号
刀具
规格
主轴转速
进给速度
背吃刀量
备注
1
加工零件四周上深度a=5的部分
T01
直径10mm
1000r/min
500mm/min
2
加工深度a=10的四方槽
T01
3
加工深度a=15的直径为φ70的圆槽
T01
300mm/min
4
加工深度a=20内接圆直径为φ70的六方形
T01
5
加工零件中直径为
φ20mm的圆槽
T01
6
加工零件中的直径为φ12mm的孔
T02
直径6mm
7
加工零件中直径为
φ6mm的圆孔
T02
第三章零件的加工及工艺分析
第一节零件图
图一要加工的零件图
第二节工艺分析
如零件图所示,工件毛坯为95mmx95mmx30mm的零件,材料为铸铁,要加工成形为中间的槽。
零件加工的工序安排:
1铣削工件四边上的四个角,使其达到指定的要求。
2加工零件中的四方槽,使其达到指定的要求。
3加工零件中直径φ70的圆槽。
4加工零件中的六方形。
5加工零件中的直径φ20的圆槽。
6换用直径φ6的铣刀,加工直径为φ12的孔。
7工直径为φ6的孔。
一、刀具的选择和切削参数
数控机床,特别是加工中心,其主轴转速较普通机床的主轴转速高1~2倍,某些特殊用途的数控机床、加工中心主轴转速高达数万转,因此数控刀具的强度与耐用度至关重要。
目前硬质合金涂镀刀具已广泛用于加工中心,陶瓷刀具与立方氮化硼等刀具也开始在加工中心上运用。
一般说来,数控机床所用刀具应具有较高的耐用度和刚度,刀具材料抗脆性好,有良好的断屑性能和可调、易更换等特点。
1、面铣削应选用不重磨硬质合金端铣刀或立铣刀。
一般采用二次走刀,第一次走刀最好用端铣刀粗铣,沿工件表面连续走刀。
注意选好每次走刀宽度和铣刀直径,使接刀刀痕不影响精切走刀精度。
因此加工余量大又不均匀时,铣刀直径要选小些。
精加工时铣刀直径要选大些,最好能包容加工面的整个宽度。
2、铣刀和镶硬质合金刀片的端铣刀主要用于加工凸台、凹槽和箱口面。
为了提高槽宽的加工精度,减少铣刀的种类,加工时可采用直径比槽宽小的铣刀,先铣槽的中间部分,然后用刀具半径补偿功能铣槽的两边。
3、削平面零件的周边轮廓一般采用立铣刀。
车削用量的选择原则是:
车削时,首先考虑选择一个尽可能大的背吃刀量ap,其次选择一个较大的进给量f,最后确定一个合适的切削进度v。
增大背吃刀量ap可使走刀次数减少,增大进给量f有利于断屑,因此根据以上原则选择粗车切削用量对于提高生产效率,减少刀具消耗,降低加工成本是有利的。
根据其形状及数值参数可得,在加工外轮廓时,因其拐角的直径等因素可选择直径为φ10的铣刀,在加工里边的方槽、圆槽、六边形槽时因其余量较大,因此也要可选用直径为φ10的铣刀。
而在加工阶梯小孔时,因其直径要求,则只能选用直径为φ6的铣刀。
挖槽加工是轮廓加工的扩展,它既要保证轮廓边界,又要将轮廓内的多余材料铣掉。
根据图纸的要求不同,选择合适的刀具型号。
根据所挖槽的不同形状及要求,对于挖槽的编程和加工要选择合适的刀具直径,刀具直径大小将影响加工效率,刀具直径太大可能使某些转角难以切削,或由于岛屿的存在形成不必要的加工盲区。
如第一节零件图所示的图形,在加工外轮廓上的四个角及内轮廓时,由于拐角的直径和内轮廓的加工余量较大,因此选择直径为φ10的铣刀。
而在加工里边的小孔时,则因为其直径的关系,而选用直径为φ6的铣刀。
在铣削外轮廓时,因其要求而要加上刀具补偿命令,而在加工内轮廓时,运用的是自动循环命令,其自带刀补因此在加工内轮廓时又得将刀补取消,以免造成过切现象或留下多余的凸台。
刀具选择的结果如下:
表二:
刀具的切削参数
加工步骤
刀具切削参数
序号
加工内容
刀具规格
主轴转速
r/min
进给速度
mm/min
刀具补偿
类型
材料
长度
半径mm
1
加工零件的四个角
直径φ10mm铣刀
1000
500
H1/T1D1
5
2
加工四方槽
3
加工直径φ70的圆槽
直径φ10mm铣刀
300
5
4
六方形
5
直径为φ20的圆槽孔
6
加工直径为φ12的孔
直径φ6mm铣刀
300
3
7
加工直径为φ6的孔
二、确定对刀点与换刀点
对于数控机床来说,在加工开始时,确定刀具与工件的相对位置是很重要的,它是通过对刀点来实现的。
“对刀点”是指通过对刀确定刀具与工件相对位置的基准点。
在程序编制时,不管实际上是刀具相对工件移动,还是工件相对刀具移动,都把工件看作静止,而刀具在运动。
对刀点往往也是零件的加工原点。
选择对刀点的原则是:
1、便于数学处理和简化程序编制。
2、在机床上容易找正,便于确定零件的加工原点的位置。
3、加工过程中便于检查。
4、引起的加工误差小。
对刀点可以设在零件上、夹具上或机床上,但必须与零件的定位基准有已知的准确关系。
当对刀精度要求较高时,对刀点应尽量选在零件的设计基准或工艺基准上。
对于以孔定位的零件,可以取孔的中心作为对刀点。
在程序开头就要设置工件坐标系,大多的数控系统可用G92指令建立工件坐标系,或用G54~G59指令选择工件坐标系。
工件坐标系一旦建立便一直有效,直到被新的工件坐标系所取代。
根据以上要求,结合本加工零件图,因其为对称的图形,零件的形状比较规则,所以在选择程序零点的时候,应考虑编程的方便,应选择零件的中心线为程序的编程零点。
在对刀的时候当零件装夹好以后,一般对刀在零件的右下角上边点上为对刀原点,在对刀过程中尽量采用点动方式来进行对刀操作,因为采用点动方式进行对刀其移动最小量可以达到10INC,这样能够精确对刀点的位置,保证零件加工中的精度的要求。
然后在设置G54编程时的程序原点时,根据以上分析要以零件的中心为编程原点,因此在设置G54时,应根据对刀原点的坐标通过计算得出刀具在工件中心位置的坐标,然后输入到G54里边。
在换铣刀的时候,应使工件与刀具之间有一个适当的距离,使得在换刀的时候不至于会发生刀具和工件的碰撞。
而且在刀具装好后,使刀具与工件之间的距离可以使刀具在下步的定位时可以走一个安全距离,使程序中的刀补及其它的参数能够充分的应用。
三、选择走刀路线
走刀路线是数控加工过程中刀具相对于被加工件的的运动轨迹和方向。
走刀路线的确定非常重要,因为它与零件的加工精度和表面质量密切相关。
确定走刀路线的一般原则是:
1、保证零件的加工精度和表面粗糙度。
2、方便数值计算,减少编程工作量。
3、缩短走刀路线,减少进退刀时间和其他辅助时间。
4、尽量减少程序段数。
在本设计中,根据零件的轮廓要求,应先加工出零件的四个角的形状,进而按层次加工零件里边的槽。
最后换刀再加工零件里边的6个小阶梯孔。
另外,在选择走刀路线时还要充分注意以下几种情况:
1、避免引入反向间隙误差
数控机床在反向运动时会出现反向间隙,如果在走刀路线中将反向间隙带入,就会影响刀具的定位精度,增加工件的定位误差。
例如精镗如下图中所示的四个孔,当孔的位置精度要求较高时,安排镗孔路线的问题就显得比较重要,安排不当就有可能把坐标轴的反向间隙带入,直接影响孔的位置精度。
这里给出两个方案,方案A如图a)所示,方案B如图b)所示。
图二镗铣加工路线图
从图中不难看出,方案A中由于Ⅳ孔与Ⅰ、Ⅱ、Ⅲ孔的定位方向相反,X向的反向间隙会使定位误差增加,而影响Ⅳ孔的位置精度。
在方案B中,当加工完Ⅲ孔后并没有直接在Ⅳ孔处定位,而是多运动了一段距离,然后折回来在Ⅳ孔处定位。
这样Ⅰ、Ⅱ、Ⅲ孔与Ⅳ孔的定位方向是一致的,就可以避免引入反向间隙的误差,从而提高了Ⅳ孔与各孔之间的孔距精度。
2、切入切出路径
在铣削轮廓表面时一般采用立铣刀侧面刃口进行切削,由于主轴系统和刀具的刚度变化,当沿法向切入工件时,会在切入处产生刀痕,所以应尽量避免沿法向切入工件。
当铣切外表面轮廓形状时,应安排刀具沿零件轮廓曲线的切向切入工件,并且在其延长线上加入一段外延距离,以保证零件轮廓的光滑过渡。
同样,在切出零件轮廓时也应从工件曲线的切向延长线上切出。
如下图a)所示。
当铣切内表面轮廓形状时,也应该尽量遵循从切向切入的方法,但此时切入无法外延,最好安排从圆弧过渡到圆弧的加工路线。
切出时也应多安排一段过渡圆弧再退刀,如下图b)所示。
当实在无法沿零件曲线的切向切入、切出时,铣刀只有沿法线方向切入和切出,在这种情况下,切入切出点应选在零件轮廓两几何要素的交点上,而且进给过程中要避免停顿。
图三铣削外内圆加工路径
为了消除由于系统刚度变化引起进退刀时的痕迹,可采用多次走刀的方法,减小最后精铣时的余量,以减小切削力。
在切入工件前应该已经完成刀具半径补偿,而不能在切入工件时同时进行刀具补偿,如下图a)所示,这样会产生过切现象。
图四刀具半径补偿点
为此,应在切入工件前的切向延长线上另找一点,作为完成刀具半径补偿点,如上图b)所示。
在本零件的加工中,在加工外边的四个角中的两个三角形角和凸面时,按编程的下刀点及刀具的移动轨迹,可以选用刀具左补偿。
而在加工凹面时,因其直径均为10而选用的铣刀直径也为10,所以不用采用刀补,当确定了下刀点后,直接下刀。
在利用循环加工零件的中间部分时,则不用再在程序中加刀补命令,只用编写参数值既可。
3、立体轮廓的加工
加工一个曲面时可能采取的三种走刀路线,如下图所示。
即沿参数曲面的u向行切、沿w向行切和环切。
对于直母线类表面,采用下图b)的方案显然更有利,每次沿直线走刀,刀位点计算简单,程序段少,而且加工过程符合直纹面的形成规律,可以准确保证母线的直线度。
如下图a)方案的优点是便于在加工后检验型面的准确度。
因此实际生产中最好将以上两种方案结合起来。
如下图c)所示的环切方案一般应用在内槽加工中,在型面加工中由于编程麻烦,一般不用。
但在加工螺旋桨桨叶一类零件时,工件刚度小,采用从里到外的环切,有利于减少工件在加工过程中的变形。
图五三种可能走刀路线
4、内槽加工
内槽是指以封闭曲线为边界的平底凹坑,如下图所示。
加工内槽一律使用平底铣刀刀具边缘部分的圆角半径应符合内槽的图纸要求。
内槽的切削分两步,第一步切内腔,第二步切轮廓。
切轮廓通常又分为粗加工和精加工两步。
粗加工时从内槽轮廓线向里平移铣刀半径R并且留出精加工余量y。
由此得出的粗加工刀位线形是计算内腔走刀路线的依据。
图六粗加工刀位线形
切削内腔时,环切和行切在生产中都有应用。
两种走刀路线的共同点是都要切净内腔中的全部面积,不留死角,不伤轮廓,同时尽量减少重复走刀的搭接量。
环切法的刀位点计算稍复杂,需要一次一次向里收缩轮廓线,算法的应用局限性稍大,例如当内槽中带有局部凸台时,对于环切法就难于设计通用的算法。
从走刀路线的长短比较,行切法要略优于环切法。
但在加工小面积内槽时,环切的程序量要比行切小。
表三:
机床刀具运行轨迹图
机械厂
机床刀具运行轨迹图
比例
共页
第页
零件图号
02001-30
零件名称
成型
程序编号
%0612
机床型号
ZK7640
刀具号
TX30
加工零件的四个边角上的部分深度为5mm
加工四方槽、圆槽、六边形的槽深度分别为5mm、10mm、15mm
加工中间的小孔和6个小阶梯孔
刀具直径
30mm
直径补偿
30mm
刀具长度
265mm
刀具运行轨迹A-B-C-D-E-F-G-H
第四章加工程序的编制
第一节数控程序编制的内容及步骤
数控编程是指从零件图纸到获得数控加工程序的全部工作过程。
如图所示:
图七程序编制步骤
第二节数控程序编制的方法
一、手工编程
手工编程指主要由人工来完成数控编程中各个阶段的工作(如工件夹紧与放松、冷却液的开闭、刀具的自动更换、各轴的进给等),加工出图样要求的零件,如图所示。
图八手工编程步骤
手工编程的特点:
耗费时间较长,容易出现错误,无法胜任复杂形状零件的编程。
据国外资料统计,当采用手工编程时,一段程序的编写时间与其在机床上运行加工的实际时间之比,平均约为30:
1,而数控机床不能开动的原因中有20%~30%是由于加工程序编制困难,编程时间较长。
二、计算机编程
计算机编程是指在编程过程中,除了分析零件图样和制定工艺方案由人工进行外,其余工作均由计算机辅助完成。
采用计算机自动编程时,数学处理、编写程序、检验程序等工作是由计算机自动完成的,由于计算机可自动绘制出刀具中心运动轨迹,使编程人员可及时检查程序是否正确,需要时可及时修改,以获得正确的程序。
又由于计算机自动编程代替程序编制人员完成了繁琐的数值计算,可提高编程效率几十倍乃至上百倍,因此解决了手工编程无法解决的许多复杂零件的编程难题。
因而,自动编程的特点就在于编程工作效率高,可解决复杂形状零件的编程难题。
三、程序格式
1、程序段格式
段是可作为一个单位来处理的连续的字组,是数控加工程序中的一条语句。
一个数控加工程序是若干个程序段组成的。
程序段格式举例:
N30G01X88.1Y30.2F500S3000T2M08
在程序段中,必须明确组成程序段的各要素:
移动目标:
终点坐标X、Y、Z
沿怎样的轨迹移动:
准备功能字G
进给速度:
进给功能字F
切削速度:
主轴转速功能字S
使用刀具:
刀具功能字T
机床辅助动作:
辅助功能字M
2、加工程序的一般格式
1)程序开始符、结束符程序开始符、结束符是同一个字符,ISO代码中是%,EIA代码中是EP,书写时要单列一段。
2)程序名程序名有两种形式:
一种是英文字母O和1~4位正整数组成;另一种是由英文字母开头,字母数字混合组成的。
一般要求单列一段。
3)程序主体程序主体是由若干个程序段组成的。
每个程序段一般占一行。
4)程序结束指令程序结束指令可以用M02或M30。
一般要求单列一段。
在此我们选用手动编程
四、零件程序
0403121
N10G54G90G94G71G17(数控加工的固定格式)
N20M03S1000T1D1(起动主轴,设定转速,确定刀具号)
N30G0X-47.5Y47.5(刀具定位)
N40Z2
N50G1Z-5F500(以下用直径为10的刀加工零件的四个角)
N60G0Z2
N70X37.5Y47.5G41(加工外轮廓时要加上刀补)
N80G1Z-5F500
N90G2X47.5Y37.5CR=10
N100G0Z2
N110X47.5Y-37.5
N120G1Z-5F500
N130X37.5Y-47.5
N140G0Z2
N150X-37.5Y-47.5
N160G1Z-5F500
N