管道检测机器人设计.docx
《管道检测机器人设计.docx》由会员分享,可在线阅读,更多相关《管道检测机器人设计.docx(30页珍藏版)》请在冰豆网上搜索。
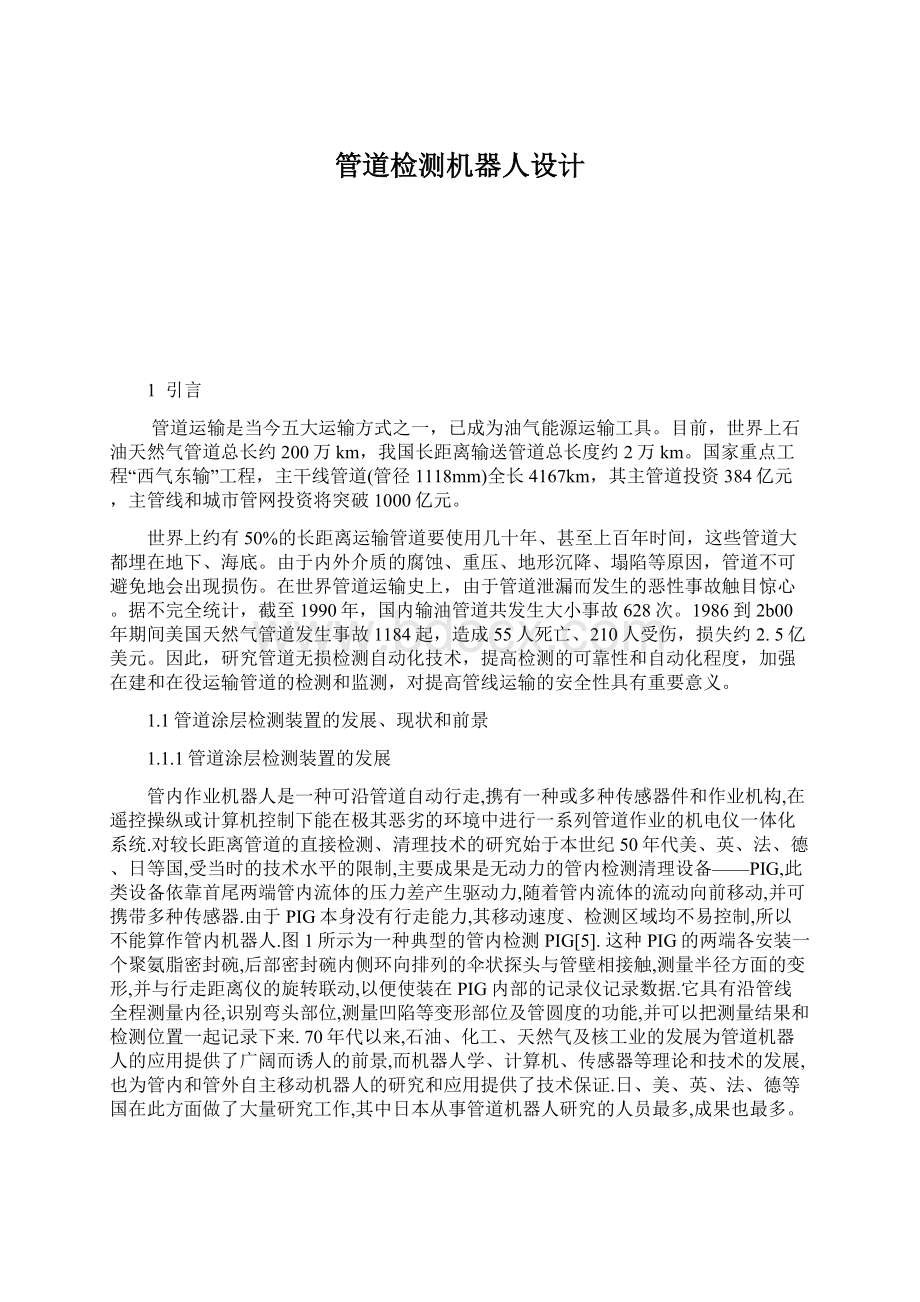
管道检测机器人设计
1引言
管道运输是当今五大运输方式之一,已成为油气能源运输工具。
目前,世界上石油天然气管道总长约200万km,我国长距离输送管道总长度约2万km。
国家重点工程“西气东输”工程,主干线管道(管径1118mm)全长4167km,其主管道投资384亿元,主管线和城市管网投资将突破1000亿元。
世界上约有50%的长距离运输管道要使用几十年、甚至上百年时间,这些管道大都埋在地下、海底。
由于内外介质的腐蚀、重压、地形沉降、塌陷等原因,管道不可避免地会出现损伤。
在世界管道运输史上,由于管道泄漏而发生的恶性事故触目惊心。
据不完全统计,截至1990年,国内输油管道共发生大小事故628次。
1986到2b00年期间美国天然气管道发生事故1184起,造成55人死亡、210人受伤,损失约2.5亿美元。
因此,研究管道无损检测自动化技术,提高检测的可靠性和自动化程度,加强在建和在役运输管道的检测和监测,对提高管线运输的安全性具有重要意义。
1.1管道涂层检测装置的发展、现状和前景
1.1.1管道涂层检测装置的发展
管内作业机器人是一种可沿管道自动行走,携有一种或多种传感器件和作业机构,在遥控操纵或计算机控制下能在极其恶劣的环境中进行一系列管道作业的机电仪一体化系统.对较长距离管道的直接检测、清理技术的研究始于本世纪50年代美、英、法、德、日等国,受当时的技术水平的限制,主要成果是无动力的管内检测清理设备——PIG,此类设备依靠首尾两端管内流体的压力差产生驱动力,随着管内流体的流动向前移动,并可携带多种传感器.由于PIG本身没有行走能力,其移动速度、检测区域均不易控制,所以不能算作管内机器人.图1所示为一种典型的管内检测PIG[5].这种PIG的两端各安装一个聚氨脂密封碗,后部密封碗内侧环向排列的伞状探头与管壁相接触,测量半径方面的变形,并与行走距离仪的旋转联动,以便使装在PIG内部的记录仪记录数据.它具有沿管线全程测量内径,识别弯头部位,测量凹陷等变形部位及管圆度的功能,并可以把测量结果和检测位置一起记录下来.70年代以来,石油、化工、天然气及核工业的发展为管道机器人的应用提供了广阔而诱人的前景,而机器人学、计算机、传感器等理论和技术的发展,也为管内和管外自主移动机器人的研究和应用提供了技术保证.日、美、英、法、德等国在此方面做了大量研究工作,其中日本从事管道机器人研究的人员最多,成果也最多。
图1管内检测典型PIG样机
在已实现的管内作业机器人中,按照其行动方式可分为轮式、履带式、振式、蠕动式等几类:
(1)轮式管内机器人
由于轮式驱动机构具有结构简单,容易实现,行走效率高等特点,对此类机器人的研究比较多.机器人在管内的运动,有直进式的(即机器人在管内平动)也有螺旋运动式的(即机器人在管内一边向前运动,一边绕管道轴线转动);轮的布置有平面的,也有空间的.一般认为,平面结构的机器人结构简单,动作灵活,但刚性、稳定性较差,而空间多轮支撑结构的机器人稳定性、刚性较好,但对弯管和支岔管的通过性不佳.轮式载体的主要缺点是牵引力的提高受到封闭力的限制.图2所示为日本的M.Miura等研制的轮式螺旋推进管内移动机器人。
(2)履带式管内机器人
履带式载体附着性能好,越障能力强,并能输出较大的牵引力.为使管内机器人在油污、泥泞、障碍等恶劣条件下达到良好的行走状态,人们又研制了履带式管内机器人.但由于结构复杂,不易小型化,转向性能不如轮式载体等原因,此类机器人应用较少.图2所示为日本学者佐佐木利夫等研制的履带式管内移动机器人[13],其驱动轮可变角度以适应管径的变化,可通过圆弧过渡的90度弯管.
图2轮式螺旋推进管内移动机器人总体结构图
图3轮式螺旋推进管内移动机器人驱动系统图
(3)振动式管内机器人
振动可以使物体的位置改变,根据这一原理,日本学者森光武则等提出了的振动式管内移动机器人。
其原理为:
在机器人的外表面装有若干与机体成一定角度的弹性针,靠弹性针的变形使其压紧在管壁上.机身内装有偏心重物,由电机驱动.当偏心重物旋转时,离心力使弹性针变形,滑动,从而带动机器人移动.振动式管内机器人结构简单,容易小型化,但行走速度难以控制,而且振动使机器人沿圆周方向自转,姿态不稳定,另外,振动对传感器的工作和寿命均会产生影响.
(4)蠕动式管内机器人
参考蚯蚓、毛虫等动物的运动,人们研制了蠕动式管内机器人。
其运动是通过身体的伸缩(蠕动)实现的:
首先,尾部支承,身体伸长带动头部向前运动,然后,头部支承,身体收缩带动尾部向前运动,如此循环实现机器人的行走.图3所示为日本日历制作所研制的蠕动式管内机器人,其前后两部分各有8条气缸驱动的可伸缩支撑足,中部有一气缸作为蠕动源。
国内在管道机器人方面的研究起步较晚,而且多数停留在实验室阶段。
哈尔滨工业大学邓宗全教授在国家863”计划课题“X射线检测实时成像管道机器人的研制”的支持下,开展了轮式行走方式的管道机器人研制,如图3所示。
该机器人具有以下特点:
(1)适应大管径(大于或等于900mm)的管道焊缝X射线检测。
(2)一次作业距离长,可达2km。
(3)焊缝寻址定位精度高为±5mm。
(4)检测工效高,每道焊缝(900mm为例)检测时间不大于3min;实现了管内外机构同步运动作业无缆操作技术,并研制了链式和钢带式两种新型管外旋转机构,课题研究成果主要用于大口径管道的自动化无损检测[8]。
上海大学研制了“细小工业管道机器人移动探测器集成系统”。
其主要包含20mm内径的垂直排列工业管道中的机器人机构和控制技术(包括螺旋轮移动机构、行星轮移动机构和压电片驱动移动机构等)、机器人管内位置检测技术、涡流检测和视频检测应用技术,在此基础上构成管内自动探测机器人系统。
该系统可实现20mm管道内裂纹和缺陷的移动探测[9]。
图4蠕动式管内移动机器人
1.1.2测量方法的研究进展
按有无破坏性,表面涂镀层厚度测试方法可分为有损检测和无损检测。
有损检测方法主要有计时液流测厚法、溶解法、电解测厚法等,这种方法一般比较繁琐,主要用于实验室。
目前也有便携式测厚仪,适合在现场使用。
常用的无损检测方法有库仑-电荷法、磁性测厚法、涡流测厚法、超声波测厚法和放射测厚法等,各种无损测厚法均有成型的仪器设备,使用起来方便简单,且无需对表面涂镀层进行破坏[1]。
因此,该类方法在管道涂层的测量中已得到了广泛的应用。
常用的无损涂层测量方法有磁性测厚﹑电涡流测厚﹑磁性/涡流测厚﹑超声波测厚等
(1)磁性测厚
磁性测厚法可分为2种:
磁吸力测厚法和磁感应测厚法。
磁吸力测厚法的测厚原理:
永久磁铁(测头)与导磁钢材之间的吸力大小与处于这两者之间的距离成一定比例关系,这个距离就是覆层的厚度。
利用这一原理制成测厚仪,只要覆层与基材的导磁率之差足够大,就可进行测量。
测厚仪基本结构由磁钢、接力簧、标尺及自停机构组成。
磁钢与被测物吸合后,将测量簧在其后逐渐拉长,拉力逐渐增大。
当拉力刚好大于吸力,磁钢脱离的一瞬间记录下拉力的大小即可获得覆层厚度[2]。
新型的产品可以自动完成这一记录过程。
磁感应测厚法的基本原理:
利用基体上的非铁磁性涂覆层在测量磁回路中形成非铁磁间隙,使线圈的磁感应强度减弱;当测量的是非铁磁性基体上的磁性涂镀层厚度时,则随着涂镀层厚度的增加,其磁感应强度也会增加。
利用磁感应原理的测厚仪,原则上可以测量导磁基体上的非导磁覆层厚度,一般要求基材导磁率在500H/m以上。
如果覆层材
料也有磁性,则要求与基材的导磁率之差足够大(如钢上镀镍)。
磁性原理测厚仪可用来精确测量钢铁表面的油漆层,瓷、搪瓷防护层,塑料、橡胶覆层,包括镍铬在内的各种有色金属电镀层以及化工石油行业的各种防腐蚀涂层。
其特点是操作简便、坚固耐用、不用电源、测量前无须校准、价格较低,适合车间做现场质量控制。
(2)电涡流测厚
涡流测厚仪是根据涂镀层与基体材料的导电性有足够的差异来进行金属基材上涂覆层的物性膜厚来测量的。
该方法实质上也属于电磁感应原理,但能否采用该方法进行厚度测定,与基体及涂镀层材料的导电性有关,而与其是否为磁性材料无关。
其工作原理为:
高频交流信号会在测头线圈中产生电磁场,当测头靠近导体时,就在其中形成涡流。
测头离导电基体愈近,则涡流愈大,反射阻抗也愈大。
这个反馈作用量表征了测头与导电基体之间距离的大小,也就是导电基体上非导电覆层厚度的大小。
由于这类测头专门测量非铁磁金属基材上的覆层厚度,所以通常称之为非磁性测头。
非磁性测头采用高频材料做线圈铁芯,例如铂镍合金或其他新材料。
与磁感应原理比较,主要区别是不同的测头、不同的信号频率和大小及不同的标度关系。
采用电涡流原理的测厚仪,主要是对导电体上的非导电体覆层厚度的测量,但当覆层材料有一定的导电性时,通过校准也同样可以测量,只是要求两者的导电率之比至少相差3~5倍(如铜上镀铬)。
(3)磁性/涡流测厚
磁性测厚和涡流测厚均有缺点,为此,很多厂家将两者综合在一起进行测定,采用的探头有3种:
F型、N型和FN型。
其中F型探头采用磁感应原理,可用于钢铁上的非磁性涂镀层,如油漆、塑料、搪瓷、铬和锌等;N型探头采用涡流原理,用于有色金属(如铜、铝、奥氏体不锈钢)上的绝缘层,如阳极氧化膜、油漆和涂料等;而FN型探头同时具有F和N型探头的功能,利用两用型探头,可实现在磁性和非磁性基体上自动转换测量[3]。
目前开发比较成熟的磁性测厚仪有时代公司的TT220,德国EPK公司开发的MINITEST4100/3100/2100/1100系列测厚仪和PHYNIX公司的Surfix/Pocket2Surfix便携式涂镀层测厚仪,可以方便地实现各种条件下的无损测厚。
(4)超声波测厚
超声波测厚仪是利用超声波脉冲反射原理,通过发射的超声波脉冲至涂层/基材,
计算脉冲通过涂层/基材界面反射回发射器所花的时间来计算涂层的厚度。
仪器通过一个发射器发射高频超声波进入涂层,振动波会穿透涂层,遇上不同力学性能的材料(如基材)时,振动波会在不同材料的界面部分反射和传递。
反射部分会被感应器接收,传递的振动波继续传递到底材,同样经历着所有材料界面间的反射、传递过程。
传感器将反射波转换成电信号,这些信号会被仪器数码化,数码化反射波被分析后,便得到振荡波所花的确切传递时间[5]。
从而计算出涂层的厚度。
超声波测厚仪可用于测量多种材料的厚度,如钢、铁、塑料和玻璃等。
新型的超声波测厚仪可以一次测量即可测定多层涂层的总厚度及指定的各层厚度,且精度很高。
1.1.3管内作业机器人的发展前景
为了使管内作业机器人能够尽快地走出实验室,进入实用化阶段,必须在以下几个方面有所突破。
(1)灵活可靠的行走机构
前面已经提到,管内作业机器人在弯管、支岔管中的通过性问题仍未解决。
而要解决这一问题,首先要在机构上保证机器人能够在这些特殊环境中顺利行走.如何寻找一种融合各种机构优点,既能够提供较大的牵引力,又快速灵活,可靠性高的驱动方案是值得研究的问题.另外,还特别要在动力系统、传动机构的小型化方面下工夫。
应该指出的是,要解决管内机器人的通过性问题,除了要在机械结构方面推陈出新之外,还应该结合控制方案来考虑。
例如前述日本于1994年推出的BEAGLE200管内探伤系统,采用3台电机分别驱动空间均布的3个主动轮,虽然机构较复杂,但由于3个驱动轮可分别控制,从而为提高其在弯管段的通过性提供了可能。
(2)智能化的传感器系统
对管道内部这类非结构化环境,现有的管内作业机器人中的传感器或无法正常发挥作用,或过多地依赖人的介入,已经不能满足其发展的需要。
经过多年的实践,人们已经认识到传感器的集成,即多种传感器(光,机,电,仪)的综合运用是解决上述问题的有效手段。
特别是以摄像机为基础的视觉传感器,由于其直观性,应引起足够的重视。
同时,先进的感知算法的研究是必要的,只有将感知算法与传感器的硬件结合起来,形成智能化的传感器,才能为提高管内作业机器人的控制水平打下良好的基础。
(3)高度自治的控制系统
在管道内部复杂的环境中,为减轻操作人员的负担,机器人具有自主能力是必要的。
但这有赖于先进的传感器技术,特别是管内环境识别技术作保证。
例如,目前已有人在机械手控制中引入视觉伺服技术,即利用视觉传感器来实现机械手的位置闭环控制。
视觉对管内机器人具有重要意义,利用视觉,可以:
①确定作业位置;
②识别管内环境(是否拐弯,是否有枝杈等);
③识别机器人的姿态(是否有转体,相对于作业位置的距离等)。
在管内作业机器人中采用视觉伺服技术,可以有效地克服现有传感器的不足,有利于提高其控制性能和自主能力,并对其智能化进程有重要意义。
目前的关键问题是如何提高图像处理的速度,神经网络、人工智能的引入将有助于解决这一问题。
另外,先进的控制策略,如路径规划,控制器参数的在线优化等的研究也必将使管内作业机器人的智能化水平得到进一步的提高。
1.2本次设计的目的
通过本次毕业设计,达到温习巩固以前所学的所有知识,并将其在实际设计中加以的运用。
熟悉一般工程设计的步骤方法:
调研收集资料,方案论证比较,确定方案,完成管道涂层厚度检测装置的设计,绘制装配图及零件图等图纸。
2总体方案的设计
2.1管道涂层厚度检测装置的技术要求
该设备能在管道中行走的,采集管道中各处的涂层厚度,采集到的数据能实现远程传送。
本设计主要包括行走系统机构、测量机构和控制部分,要求实现测量系统在管道中行走,行走速度为0.5m/min。
2.2主要技术参数
本次设计的管道内防腐涂层厚度测量仪的具体指标如下:
1.内径:
200mm2管道长度200m
3涂层测量范围0~500µm4误差±(1±3%)µm
5行走速度500mm/min6工作环境温度0—50℃
2.3总体方案的分析与确定
该测量装置由行走系统机构、测量机构和控制部分构成。
行走机构和测量机构要通过8051单片机接受上位机的控制,进行自动行走和测量,并将所测得的数据进行整理计算传送到上位机。
行走系统是由一个直流电动机通过齿轮减速机构和带传动驱动两个驱动轮,从而实现整个测量装置的前进和后退。
测量机构采用超声波传感器,其原理是利用超声波的反射法,通过记录回波信号的时间差来计算出涂层的厚度。
本装置中采用两个传感器呈
180°布置,可同时测量两个点的涂层厚度。
在实际的测量中要求随时确定测量装置的确切位置即测量装置在管道内行走的距离。
为了得到测量装置在管道中行走的距离,专门设计了计程轮,此轮上安装了霍尔元件,通过霍尔元件采集的脉冲数可得到轮子所转圈数,从而得出测量装置行进的距离。
控制系统以单片机8051为中心,它控制着直流电机—机器人的动力源的前进、后退和停止、2个传感器的通断,并将厚度信号和转换信号进行处理,传送给上位机,接受上位机的监控。
其框图如下:
图5测量装置整体框图
3机械结构设计
3.1管道涂层测厚装置的运动原理
微型管道机器人采用了有缆驱动的驱动方式,其运动机理由两组车轮沿径向呈三等分均布,其中四个从动轮在扇形齿轮的作用下被支撑在管道的内壁上,另外两个则是驱动轮。
电机带动锥齿轮旋转,从而使得装有皮带轮的轴转动,车轮随之转动。
由于车轮与管壁之间的摩擦力,车体便可以在管中前进或后退。
尾部还有一个柔性的计程轮,其作用:
1.计算小车前进的距离。
2.支撑车体,保持平衡。
3.2管道涂层测厚装置行走机构的设计
机器人的移动机构具有结构紧凑和较大的负载能力,满足管道内行走的基本条件。
移动机构的前后两组支撑中,三个车轮都是沿径向均匀分布的,而前后两部分都是沿轴向对称的,支撑点共六个,因此满足形封闭条件。
当移动机构行走时,三个轮子呈径向均匀分布,三点确定一个平面,三点始终在一个圆柱面上,因此可以实现自定心,在支撑装置的作用下,驱动轮被紧紧压在管道内壁上,具有较强的适应性。
整个系统由于利用了对称性,抵消了机器人在运动过程中各方面不平衡力偶的干扰,从而使所有的力集中到电机运转轴线上所在的竖直平面上,同时,又在通过电机轴线的竖直平面上保证机器人的重心与电机运转轴心之间适当的距离,从而保证了整个机器人运行过程中的平稳性。
3.3电动机的选择
由于管道的直径很小,所以根据尺寸选择j55ZYT—PX微型减速电机。
其减速比为216.输出转速为14r/min。
输出转矩18730mN.m。
其计算过程为:
车轮与管壁的摩擦系数为
=0.8车体的重量为50kgG=mg=50×10N=500N
压紧机构产生的压紧力为500N
则:
车体对管壁的正压力N=1000N
F=μN=0.8×N=800N
电动机所需要的工作功率为
各轴输入功率为:
各轴的输入转矩:
所以所选的电机符合条件。
3.4传动的总体方案设计
此测量装置在500mm/min的速度下前进,速度比较低。
初选车轮直径为40mm则此时车轮的角速度以及减速后最终的角速度为:
ω=60v/(π×d)=60×500/3.14×40×60=3.98r/min
由于电机的初速度为14r/min,由传动比公式i=14/w=14/3.98=3.5
所以传动比i=3.5
我选用直齿圆锥齿轮来传递能量和动力。
因为其可以实现两相交轴之间的传动。
锥齿轮设计、制造及安装均较简单,用于低速传动,非常适合此装置的要求。
考虑到机器人在前进过程中要托缆,因此将此机器人设计成前后轮共同驱动的方式,以获得较大的牵引力。
由于尺寸限制,只能将轮放在另外一根轴上,用皮带将两轴连接起来,它没有调速的作用,只需使两轴具有同样的旋转速度。
3.5压紧装置的设计
压紧装置主要是为了让机器人能够撑紧管壁,从而达到平稳前进的目的。
我所设计的压紧装置是通过一个扇形齿轮和一个齿条的相互啮合实现的。
具体如图6所示:
图6压紧装置
此结构的原理非常简单,但却很实用。
当管壁直径变化时,压紧轮就会以销轴为中心,进行旋转,同时齿条就会因为啮合的作用前后移动,弹簧也跟着压缩或拉长。
以此来调节适当的压紧力,保证车体的平衡。
3.6计程轮的设计
计程轮的设计是为了知道车体在管道中行进的距离,已达到正确测量管道中某点涂层厚度的目的。
计程轮设计如图6所示,它的结构比较简单,是用四个导向螺钉将轮固定在支撑体上,导向螺钉上装有压缩弹簧,压缩弹簧的一端连在支架上,另一端连在支撑体上,由此支架可以沿着导向螺钉的方向上下移动,而车轮通过销轴连在支架上,可以随支架一起运动,以保证计程轮始终与地面接触。
计程轮上安装有霍尔传感器。
霍尔传感器就是利用霍尔效应原理,通过磁场、电流对被测量的控制,使包含有被测量变化信息的霍尔电压发生变化,在利用后继的信号检索和信号放大电路,就可以得到被测量脉冲信号的信息。
正因为霍尔传感器的基本原理霍尔效应只包含了磁场、电流、电压三个常用物理量,使得采用霍尔传感器的被测量的测量简单易行,而磁场强度、电流、电压是磁场、电场的基本物理量,所以霍尔传感器可以进行精确的非接触测量。
图7计程轮
它具有灵敏度高,线性度好,稳定性高、体积小和耐高温等特点,在机车控制系统中占有非常重要的地位。
本装置中选用霍尔元件DN6837,它是一个开关集成霍尔传感器,其输出的脉冲信号经过一级三极管放大,在送到单片机的输入口。
3.7轴的设计与校核
轴的材料是决定其承载能力的重要因素,制造轴的主要材料是碳素钢及合金钢。
45号优质中碳钢是最常用的材料。
Q235-A等普通碳素钢用于不重要的轴或受载较小的轴;合金钢具有较高的机械强度用于受载荷较大、结构尺寸受限制、需提高轴颈耐磨性及处于高温或腐蚀等条件下的轴;球墨铸铁和一些高强度铸铁一般用于铸成外形复杂的轴,他们吸振性好,对应力集中敏感性低。
一般机器中的轴常用优质中碳钢制造,这类钢比合金钢廉价,对应力集中的敏感性较低,其中45号钢最为常用。
为了提高材料的力学性能,通常进行调质或正火处理。
由于振动磨的主轴旋转会产生高频率的振动,且产生的离心力相当大,所以应选45号钢作为此传动轴的材料。
一般常见的轴按其轴线的形状和功用分为直轴、曲轴两大类,因为本次设计只涉及直轴,所以我们在此只讨论直轴。
直轴一般都做成实心,若因机器特殊需要也可制成空心轴。
考虑到应加工方便,轴的截面多为圆形,为了使轴上零件定位及装拆方便,轴多做成阶梯轴。
一些结构简单或特殊要求在轴中装设其它零件或者减小轴的质量具有重大作用的场合,轴才做成等直径的轴(光轴)或空心轴。
空心轴内径与外径比通常为0.5~0.6,以保证轴的刚度及扭转稳定性。
根据轴的承载情况,可分为:
转轴——工作中既受弯矩又受转矩的轴;有时还受较大轴向力的作用,这类轴在各种机器种最常见;心轴——工作中只承受弯矩、不受转矩或转矩较小的轴,心轴又分为转动心轴(轴转动)和固定心轴(轴不转动)两种;传动轴——工作中只传递转矩、不承受弯矩或受弯矩很小的轴。
下面首先通过扭转强度对轴进行设计,然后再用弯扭组合进行校核。
按扭转强度条件计算
选择轴的材料为45钢,经调质处理,首先估算最小轴径,根据下列公式进行计算
,
d——截面处轴的直径,单位mm,
p——轴的传递功率,单位kw;
n——轴的转速,单位r/min,
——许用扭转切应力,单位MPa,45钢的
值为25~45;
——其中45钢的
的取值为126~103。
因选择的电动机功率