实习报告田茂林Microsoft Word 文档.docx
《实习报告田茂林Microsoft Word 文档.docx》由会员分享,可在线阅读,更多相关《实习报告田茂林Microsoft Word 文档.docx(9页珍藏版)》请在冰豆网上搜索。
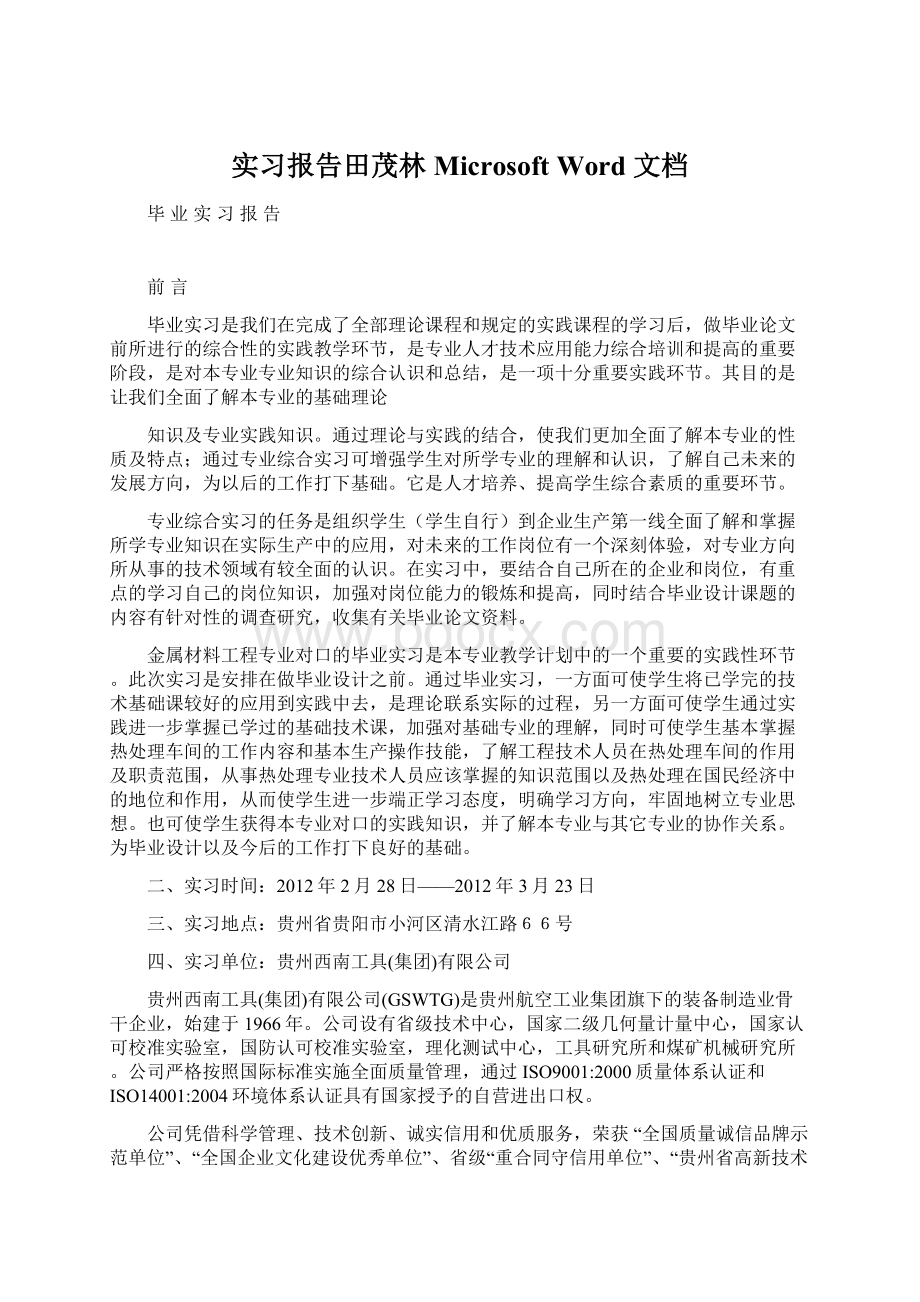
实习报告田茂林MicrosoftWord文档
毕业实习报告
前言
毕业实习是我们在完成了全部理论课程和规定的实践课程的学习后,做毕业论文前所进行的综合性的实践教学环节,是专业人才技术应用能力综合培训和提高的重要阶段,是对本专业专业知识的综合认识和总结,是一项十分重要实践环节。
其目的是让我们全面了解本专业的基础理论
知识及专业实践知识。
通过理论与实践的结合,使我们更加全面了解本专业的性质及特点;通过专业综合实习可增强学生对所学专业的理解和认识,了解自己未来的发展方向,为以后的工作打下基础。
它是人才培养、提高学生综合素质的重要环节。
专业综合实习的任务是组织学生(学生自行)到企业生产第一线全面了解和掌握所学专业知识在实际生产中的应用,对未来的工作岗位有一个深刻体验,对专业方向所从事的技术领域有较全面的认识。
在实习中,要结合自己所在的企业和岗位,有重点的学习自己的岗位知识,加强对岗位能力的锻炼和提高,同时结合毕业设计课题的内容有针对性的调查研究,收集有关毕业论文资料。
金属材料工程专业对口的毕业实习是本专业教学计划中的一个重要的实践性环节。
此次实习是安排在做毕业设计之前。
通过毕业实习,一方面可使学生将已学完的技术基础课较好的应用到实践中去,是理论联系实际的过程,另一方面可使学生通过实践进一步掌握已学过的基础技术课,加强对基础专业的理解,同时可使学生基本掌握热处理车间的工作内容和基本生产操作技能,了解工程技术人员在热处理车间的作用及职责范围,从事热处理专业技术人员应该掌握的知识范围以及热处理在国民经济中的地位和作用,从而使学生进一步端正学习态度,明确学习方向,牢固地树立专业思想。
也可使学生获得本专业对口的实践知识,并了解本专业与其它专业的协作关系。
为毕业设计以及今后的工作打下良好的基础。
二、实习时间:
2012年2月28日——2012年3月23日
三、实习地点:
贵州省贵阳市小河区清水江路66号
四、实习单位:
贵州西南工具(集团)有限公司
贵州西南工具(集团)有限公司(GSWTG)是贵州航空工业集团旗下的装备制造业骨干企业,始建于1966年。
公司设有省级技术中心,国家二级几何量计量中心,国家认可校准实验室,国防认可校准实验室,理化测试中心,工具研究所和煤矿机械研究所。
公司严格按照国际标准实施全面质量管理,通过ISO9001:
2000质量体系认证和ISO14001:
2004环境体系认证具有国家授予的自营进出口权。
公司凭借科学管理、技术创新、诚实信用和优质服务,荣获“全国质量诚信品牌示范单位”、“全国企业文化建设优秀单位”、省级“重合同守信用单位”、“贵州省高新技术企业”、省级“知识产权工作试点单位”、省级“企业文化建设荣誉成就奖”、贵阳市“最高科技创新奖”、贵阳市“创新型试点企业”等称号。
多次荣获LG电子、松下万宝、华润三洋等公司授予的“优秀供应商”、“优秀分承包商”、“优秀服务奖”、“最佳质量奖”等称号。
SWT牌卡尺、立铣刀荣获“中国名牌产品”称号。
家用空调压缩机叶片和涡旋式压缩机零部件及组件被列为国家重点新产品计划,压缩机叶片软氮化技术和涡旋式压缩机零部件及组件项目荣获省级“科学技术进步奖”。
公司坚持以满足市场和客户的需求为衡量一切工作的标准,坚持“变革、创新、快速”的文化价值观,按照“源于工具、延伸工具、超越工具”的发展思路,以“创新、合作、卓越、成功”为数控机床发展理念,努力打造以数控机床为主产品,以工量具和精密零部件制造为专业化优势的、现代化的装备制造业骨干企业。
五、实习报告的主要内容及相关知识:
(一)热处理的基本知识:
热处理工艺一般包括加热、保温、冷却三个过程,有时只有加热和冷却两个过程。
这些过程互相衔接,不可间断。
1、加热温度:
加热温度是热处理工艺的重要工艺参数之一,选择和控制加热温度,是保证热处理质量的主要问题。
加热温度随被处理的金属材料和热处理的目的不同而异,但一般都是加热到相变温度以上,以获得需要的组织。
另外转变需要一定的时间,因此当金属工件表面达到要求的加热温度时,还须在此温度保持一定时间,使内外温度一致,使显微组织转变完全,这段时间称为保温时间。
采用高能密度加热和表面热处理时,加热速度极快,一般就没有保温时间或保温时间很短,而化学热处理的保温时间往往较长。
2、冷却:
冷却也是热处理工艺过程中不可缺少的步骤,冷却方法因工艺不同而不同,主要是控制冷却速度。
一般退火的冷却速度最慢,正火的冷却速度较快,淬火的冷却速度更快。
但还因钢种不同而有不同的要求,例如空硬钢就可以用正火一样的冷却速度进行淬硬。
3、热处理分类:
金属热处理工艺大体可分为整体热处理、表面热处理、局部热处理和化学热处理等。
根据加热介质、加热温度和冷却方法的不同,每一大类又可区分为若干不同的热处理工艺。
同一种金属采用不同的热处理工艺,可获得不同的组织,从而具有不同的性能。
钢铁是工业上应用最广的金属,而且钢铁显微组织也最为复杂,因此钢铁热处理工艺种类繁多。
4、整体热处理:
整体热处理是对工件整体加热,然后以适当的速度冷却,以改变其整体力学性能的金属热处理工艺。
钢铁整体热处理大致有退火、正火、淬火和回火四种基本工艺。
5、退火:
退火是将工件加热到适当温度,根据材料和工件尺寸采用不同的保温时间,然后进行缓慢冷却,目的是使金属内部组织达到或接近平衡状态,获得良好的工艺性能和使用性能,或者为进一步淬火作组织准备。
正火是将工件加热到适宜的温度后在空气中冷却,正火的效果同退火相似,只是得到的组织更细,常用于改善材料的切削性能,也有时用于对一些要求不高的零件作为最终热处理。
6、淬火:
淬火是将工件加热保温后,在水、油或其它无机盐、有机水溶液等淬冷介质中快速冷却。
淬火后钢件变硬,但同时变脆。
为了降低钢件的脆性,将淬火后的钢件在高于室温而低于710℃的某一适当温度进行长时间的保温,再进行冷却,这种工艺称为回火。
退火、正火、淬火、回火是整体热处理中的“四把火”,其中的淬火与回火关系密切,常常配合使用,缺一不可。
7、“四把火”随着加热温度和冷却方式的不同,又演变出不同的热处理工艺。
为了获得一定的强度和韧性,把淬火和高温回火结合起来的工艺,称为调质。
某些合金淬火形成过饱和固溶体后,将其置于室温或稍高的适当温度下保持较长时间,以提高合金的硬度、强度或电性磁性等。
这样的热处理工艺称为时效处理。
把压力加工形变与热处理有效而紧密地结合起来进行,使工件获得很好的强度、韧性配合的方法称为形变热处理;在负压气氛或真空中进行的热处理称为真空热处理,它不仅能使工件不氧化,不脱碳,保持处理后工件表面光洁,提高工件的性能,还可以通入渗剂进行化学热处理。
8、表面热处理:
表面热处理是只加热工件表层,以改变其表层力学性能的金属热处理工艺。
为了只加热工件表层而不使过多的热量传入工件内部,使用的热源须具有高的能量密度,即在单位面积的工件上给予较大的热能,使工件表层或局部能短时或瞬时达到高温。
表面热处理的主要方法,有激光热处理、火焰淬火和感应加热热处理,常用的热源有氧乙炔或氧丙烷等火焰、感应电流、激光和电子束等。
9、化学热处理:
化学热处理是通过改变工件表层化学成分、组织和性能的金属热处理工艺。
化学热处理与表面热处理不同之处是后者改变了工件表层的化学成分。
化学热处理是将工件放在含碳、氮或其它合金元素的介质(气体、液体、固体)中加热,保温较长时间,从而使工件表层渗入碳、氮、硼和铬等元素。
渗入元素后,有时还要进行其它热处理工艺如淬火及回火。
化学热处理的主要方法有渗碳、渗氮、渗金属、复合渗等。
(二)退火--淬火--回火:
1、退火的种类
(1)完全退火和等温退火
完全退火又称重结晶退火,一般简称为退火,这种退火主要用于亚共析成分的各种碳钢和合金钢的铸,锻件及热轧型材,有时也用于焊接结构。
一般常作为一些不重要工件的最终热处理,或作为某些工件的预先热处理。
(2)球化退火
球化退火主要用于过共析的碳钢及合金工具钢(如制造刃具,量具,模具所用的钢种)。
其主要目的在于降低硬度,改善切削加工性,并为以后淬火作好准备。
(3)去应力退火
去应力退火又称低温退火(或高温回火),这种退火主要用来消除铸件,锻件,焊接件,热轧件,冷拉件等的残余应力。
如果这些应力不予消除,将会引起钢件在一定时间以后,或在随后的切削加工过程中产生变形或裂纹。
2、淬火
为了提高硬度采取的方法,主要形式是通过加热、保温、速冷。
最常用的冷却介质是盐水,水和油。
盐水淬火的工件,容易得到高的硬度和光洁的表面,不容易产生淬不硬的软点,但却易使工件变形严重,甚至发生开裂。
而用油作淬火介质只适用于过冷奥氏体的稳定性比较大的一些合金钢或小尺寸的碳钢工件的淬火。
3、回火
(1)降低脆性,消除或减少内应力,钢件淬火后存在很大内应力和脆性,如不及时回火往往会使钢件发生变形甚至开裂。
(2)获得工件所要求的机械性能,工件经淬火后硬度高而脆性大,为了满足各种工件的不同性能的要求,可以通过适当 回火的配合来调整硬度,减小脆性,得到所需要的韧性,塑性。
(3)稳定工件尺寸
(4)对于退火难以软化的某些合金钢,在淬火(或正火)后常采用高温回火,使钢中碳化物适当聚集,将硬度降低,以利切削加工。
(三)常用炉型的选择:
炉型应依据不同的工艺要求及工件的类型来决定
1、对于不能成批定型生产的,工件大小不相等的,种类较多的,要求工艺上具有通用性、多用性的,可选用箱式炉。
2、加热长轴类及长的丝杆,管子等工件时,可选用深井式电炉。
3、小批量的渗碳零件,可选用井式气体渗碳炉。
4、对于大批量的汽车、拖拉机齿轮等零件的生产可选连续式渗碳生产线或箱式多用炉。
5.对冲压件板材坯料的加热大批量生产时,最好选用滚动炉,辊底炉。
6、对成批的定型零件,生产上可选用推杆式或传送带式电阻炉(推杆炉或铸带炉)
7、小型机械零件如:
螺钉,螺母等可选用振底式炉或网带式炉。
(四)加热缺陷及控制:
1、过热现象
我们知道热处理过程中加热过热最易导致奥氏体晶粒的粗大,使零件的机械性能下降。
(1)一般过热:
加热温度过高或在高温下保温时间过长,引起奥氏体晶粒粗化称为过热。
粗大的奥氏体晶粒会导致钢的强韧性降低,脆性转变温度升高,增加淬火时的变形开裂倾向。
而导致过热的原因是炉温仪表失控或混料(常为不懂工艺发生的)。
过热组织可经退火、正火或多次高温回火后,在正常情况下重新奥氏化使晶粒细化。
(2)断口遗传:
有过热组织的钢材,重新加热淬火后,虽能使奥氏体晶粒细化,但有时仍出现粗大颗粒状断口。
产生断口遗传的理论争议较多,一般认为曾因加热温度过高而使MnS之类的杂物溶入奥氏体并富集于晶界,而冷却时这些夹杂物又会沿晶界析出,受冲击时易沿粗大奥氏体晶界断裂。
(3)粗大组织的遗传:
有粗大马氏体、贝氏体、魏氏体组织的钢件重新奥氏化时,以慢速加热到常规的淬火温度,甚至再低一些,其奥氏体晶粒仍然是粗大的,这种现象称为组织遗传性。
要消除粗大组织的遗传性,可采用中间退火或多次高温回火处理。
2、过烧现象
加热温度过高,不仅引起奥氏体晶粒粗大,而且晶界局部出现氧化或熔化,导致晶界弱化,称为过烧。
钢过烧后性能严重恶化,淬火时形成龟裂。
过烧组织无法恢复,只能报废。
因此在工作中要避免过烧的发生。
3、脱碳和氧化
钢在加热时,表层的碳与介质(或气氛)中的氧、氢、二氧化碳及水蒸气等发生反应,降低了表层碳浓度称为脱碳,脱碳钢淬火后表面硬度、疲劳强度及耐磨性降低,而且表面形成残余拉应力易形成表面网状裂纹。
4、氢脆现象
高强度钢在富氢气氛中加热时出现塑性和韧性降低的现象称为氢脆。
出现氢脆的工件通过除氢处理(如回火、时效等)也能消除氢脆,采用真空、低氢气氛或惰性气氛加热可避免氢脆。
(五)钢的氮化及碳氮共渗:
1、钢的氮化(气体氮化)
(1)氮化是向钢的表面层渗入氮原子的过程,其目的是提高表面硬度和耐磨性,以及提高疲劳强度和抗腐蚀性;它是利用氨气在加热时分解出活性氮原子,被钢吸收后在其表面形成氮化层,同时向心部扩散。
(2)氮化通常利用专门设备或井式渗碳炉来进行。
适用于各种高速传动精密齿轮、机床主轴(如镗杆、磨床主轴),高速柴油机曲轴、阀门等。
(3)氮化工件工艺路线:
锻造-退火-粗加工-调质-精加工-除应力-粗磨-氮化-精磨或研磨。
由于氮化层薄,并且较脆,因此要求有较高强度的心部组织,所以要先进行调质热处理,获得回火索氏体,提高心部机械性能和氮化层质量。
(4)钢在氮化后,不再需要进行淬火便具有很高的表面硬度及耐磨性。
氮化处理温度低,变形很小,它与渗碳、感应表面淬火相比,变形小得多
2、钢的碳氮共渗:
碳氮共渗是向钢的表层同时渗入碳和氮的过程,习惯上碳氮共渗又称作氰化。
目前以中温气体碳氮共渗和低温气体氮碳共渗(即气体软氮化)应用较是广。
中温气体碳氮共渗的主要目的是提高钢的硬度,耐磨性和疲劳强度,低温气体碳氮共渗以渗氮为主,其主要目的是提高钢的耐磨性和抗咬合性。
3、调质处理:
一般习惯将淬火加高温回火相结合的热处理称为调质处理。
调质处理广泛应用于 各种重要的结构零件,特别是那些在交变负荷下工作的连杆、螺栓、齿轮及轴类等。
调质处理后得到回火索氏体组织,它的机械性能均比相同硬度的正火索氏体组织为优。
它的硬度取决于高温回火温度并与钢的回火稳定性和工件截面尺寸有关,一般在HB200~350之间。
(六)回火的种类及应用:
根据工件性能要求的不同,按其回火温度的不同,可将回火分为以下几种:
低温回火(150~250℃)
低温回火所得组织为回火马氏体。
其目的是在保持淬火钢的高硬度和高耐磨性的前提下,降低其淬火内应力和脆性,以免使用时崩裂或过早损坏。
它主要用于各种高碳的切削刃具,量具,冷冲模具,滚动轴承以及渗碳件等,回火后硬度一般为HRC58-64。
2、中温回火(350~500℃)
中温回火所得组织为回火屈氏体。
其目的是获得高的屈服强度,弹性极限和较高的韧性。
因此,(它主要用于各种弹簧和热作模具的处理,回火后硬度一般为HRC35-50。
3、高温回火(500~650℃)
高温回火所得组织为回火索氏体。
习惯上将淬火加高温回火相结合的热处理称为调质处理,其目的是获得强度,硬度和塑性,韧性都较好的综合机械性能。
因此,广泛用于汽车,拖拉机,机床等的重要结构零件,如连杆,螺栓,齿轮及轴类。
回火后硬度一般为HB200-330。
(七)各种加热设备的结构、用途及名称:
名称
用途
结构
主要参数
高频感应表面淬火仪
表面淬火
高频电源、感应线圈
200KHZ
中频感应加热仪
加热
中频电源、感应线圈
10~20MHZ
高温淬火炉
高温淬火
电阻丝、盐浴
1100℃
中温淬火炉
中温淬火
电阻丝、盐浴
渗碳渗氮炉
渗碳渗氮碳氮共渗
电阻丝、炉膛结构
890,520
中温回火炉
中温回火
电阻丝、盐浴
450℃
钎杆抛丸强化机
钎杆抛丸
金属丸循环系统
B22~35D32~81(mm)
镫粗机、领盘机
镫粗、车领盘
中频感应加热仪模具
1050℃~1150℃
轧钢煤气加热炉
轧钢
煤气发生炉加热炉
(八)感应加热表面淬火:
1、感应加热就是利用电磁感应在工件内产生涡流而将工件进行加热。
感应加热表面淬火与普通淬火比具有如下优点:
(1)热源在工件表层,加热速度快,热效率高
(2)工件因不是整体加热,变形小
(3)工件加热时间短,表面氧化脱碳量少
(4)工件表面硬度高,缺口敏感性小,冲击韧性、疲劳强度以及耐磨性等均有很大提高。
有利于发挥材料地潜力,节约材料消耗,提高零件使用寿命
(5)设备紧凑,使用方便,劳动条件好
(6)便于机械化和自动化
(7)不仅用在表面淬火还可用在穿透加热与化学热处理等。
2、感应加热的基本原理
(1)将工件放在感应器中,当感应器中通过交变电流时,在感应器周围产生与电流频率相同的交变磁场,在工件中相应地产生了感应电动势,在工件表面形成感应电流,即涡流。
这种涡流在工件的电阻的作用下,电能转化为热能,使工件表面温度达到淬火加热温度,可实现表面淬火。
(2)表面淬火的目的在于获得高硬度,高耐磨性的表面,而心部仍然保持原有的良好韧性,常用于机床主轴,齿轮,发动机的曲轴等。
表面淬火采用的快速加热方法有多种,如电感应,火焰,电接触,激光等,目前应用最广的是电感应加热法。
(3)感应加热表面淬火就是在一个感应线圈中通以一定频率的交流电(有高频,中频。
工频三种),是感应圈周围产生频率相同的交变磁场,置于磁场之中的工件就会产生与感应线圈频率相同,方向相反的感应电流,这个电流叫涡流。
由于集肤效应,涡流主要集中在工件的表层。
由涡流所产生的电阻热使工件表层被迅速加热到淬火温度,随即向工件喷水,将工件表层淬硬。
(4)感应电流的频率愈高,集肤效应也愈强烈,故高频感应加热用途最广。
高频感应加热常用频率是200~300kHz,其加热速度极快,通常只有几秒种,淬硬层深度一般为0.5~2mm。
主要用于要求淬硬层较薄的中,小型零件,如齿轮,轴等。
3、感应表面淬火后的性能
(1)表面硬度:
经高、中频感应加热表面淬火的工件,其表面硬度往往比普通淬火高2~3个单位(HRC)。
(2)耐磨性:
高频淬火后的工件耐磨性比普通淬火要高。
这主要是由于淬硬层马氏体晶粒细小,碳化物弥散度高,以及硬度比较高,表面的高的压应力等综合的结果。
(3)疲劳强度:
高、中频表面淬火使疲劳强度大为提高,缺口敏感性下降。
对同样材料的工件,硬化层深度在一定范围内,随硬化层深度增加而疲劳强度增加,但硬化层深度过深时表层是压应力,因而硬化层深度增打疲劳强度反而下降,并使工件脆性增加。
一般硬化层深δ=(10~20)%D。
较为合适,其中D。
为工件的有效直径。
(九)热处理操作流程:
热处理前的准备工作:
1、热处理设备的调试。
加热设备:
加热设备应保证加热温度准确、均匀、少氧化或无氧化,因此,在对零件进行加热前,需要对加热设备调试。
高温盐浴炉启动后应进行高温脱氧,将温度升到1290——1300℃,不开吸风机进行脱氧,脱氧剂加入量为2㎏左右,保温10min,进行捞渣取样分析。
氧化钡的质量分数应小于0.5℅,生产过程中每连续4h脱氧一次,加入量为0.5㎏。
电阻炉的使用特点:
优点,工作范围宽,为600——1600℃炉温稳定均匀。
加热效率高。
结构紧凑、占地面积小,便于安装易实现机械化和自动化操作,劳动条件好,污染小。
缺点,炉子造价高,耗电量大,工作加热速度较慢,易脱碳氧化。
盐浴炉的使用特点:
定义,是利用液体作为介质进行加热或冷却工作的一种热处理炉。
工作温度:
60——1350℃除随炉冷却外,可进行淬、回火、退火处理。
主要特点:
因为工作在盐浴炉中加热与液体介质想接触,靠对流换热,具有加热速度快,温度均匀和不易氧化脱碳的优点,且结构简单。
缺点,与电阻炉相比,装料少,只适用于中小型零件的加热。
热量损失大,要耗盐、碱等介质,劳动条件差。
热处理后需要对工件进行清洗,适用于尺寸较小,形状复杂,表面要求较高的工模具及其精密零件。
热处理设备的维护与保养。
应熟悉设备的结构,=电气控制原理。
定期检查常动部位润滑情况及松动。
定期清除温控柜、电控柜的灰尘,保持清洁,定期检查各气体‘液体管道,及时排除堵塞和渗漏情况。
检查电热体的损坏情况,防止短路和及时更换。
检查炉砖有无开裂和塌陷。
分析常见淬火缺陷及产生原因。
淬火硬度不足或偏高,淬火硬度不均匀。
材料本身问题,材料的含碳量处于上下极限位置加热温度或保温时间选择不当。
淬火介质选择不当。
淬火开裂及变形。
材料选择不当或材料本身有缺陷。
淬火加热温度时间及淬火介质选择不当。
零件的结构设计不合理。
热处理操作不正确,事故保障能力差。
工艺部分。
依据工作要求,确定工艺流程和淬火工艺参数。
加热温度910——930℃渗碳保温时间设为9h,炉冷840——860℃均温0.5h后油冷后重新淬火及回火。
重新淬回火的主要工艺参数。
在盐浴中重新加热到850℃保温6——10min油淬,在180——200℃进行1.5——2h回火热处理。
画出加热淬火曲线标出工艺参数。
对工艺进行分析。
工件形状简单,尺寸较小,但有表面硬度,深层深度要求应严格控制渗碳及热处理工艺参数。
由于工件为杆状零件硬度要求较高,对变形度要求较高,对变形度有要求,因此需对零件进行重新加热淬火。
2、盐浴炉的使用范围及特点:
(1)工作温度:
60—13500C除随炉冷却外,可进行淬火,回火,退火处理。
(2)主要特点:
工件装盐浴炉中加热与液体介质相接触,靠对流换热,具有加热速度快,温度均匀和不易氧化脱碳等优点,且结构简单。
(3)缺点:
a.与电阻炉相比,装料少,只适用于中小型零件的加热。
b.热量损失大,需耗盐、碱等介质,劳动条件差。
c.热处理后需对工件进行清洗,适用于尺寸小,形状复杂,表面要求较高的工模具及其精密零件。
3、常见淬火缺陷及产生原因:
(1)淬火硬度不足或偏高,淬火硬度不均匀,原因:
材料本身问题,加热温度和保温时间选择不当,淬火介质选择不当。
(2)淬火变形及开裂,原因:
材料选择不当或材料本身有缺陷,淬火加热温度时间及淬火介质选择不当,零件的结构设计不当,热处理操作不正确。
九、实习心得
“纸上得来终觉浅,绝知此事需躬行”通过这次到工厂生产实习让我学到及掌握了很多金属材料反面的专业。
平时有许多东西看似已经懂了,但真正到了实践中却又是另一种情况。
有时自己认为自己已把握的东西可能仅是一些肤浅的表面或总体的一个方面,甚至有时是错误的熟悉,而假如没有这次生产实践,我是无法发现这些问题的。
这次实习给我们每个人一个很好的机会学习课堂上不能学到的知识,通过我们自己的实际动手参加一线生产实习,还查找各种图书资料以及到网上搜寻相关资料,使我们的知识得以巩固和完善,不仅增长了我们的见识,而且对生产操作有了进一步的掌握,对工人也有了一中全新的熟悉。
感谢领导、老师给我们这次充实自己、增长见识的机会!
同时我也希望学校及学院在今后的学习和生活中能为我们提供更多的实习机会,让我们在实际生产中得到锻炼。