数控机床仿真加工实训报告.docx
《数控机床仿真加工实训报告.docx》由会员分享,可在线阅读,更多相关《数控机床仿真加工实训报告.docx(11页珍藏版)》请在冰豆网上搜索。
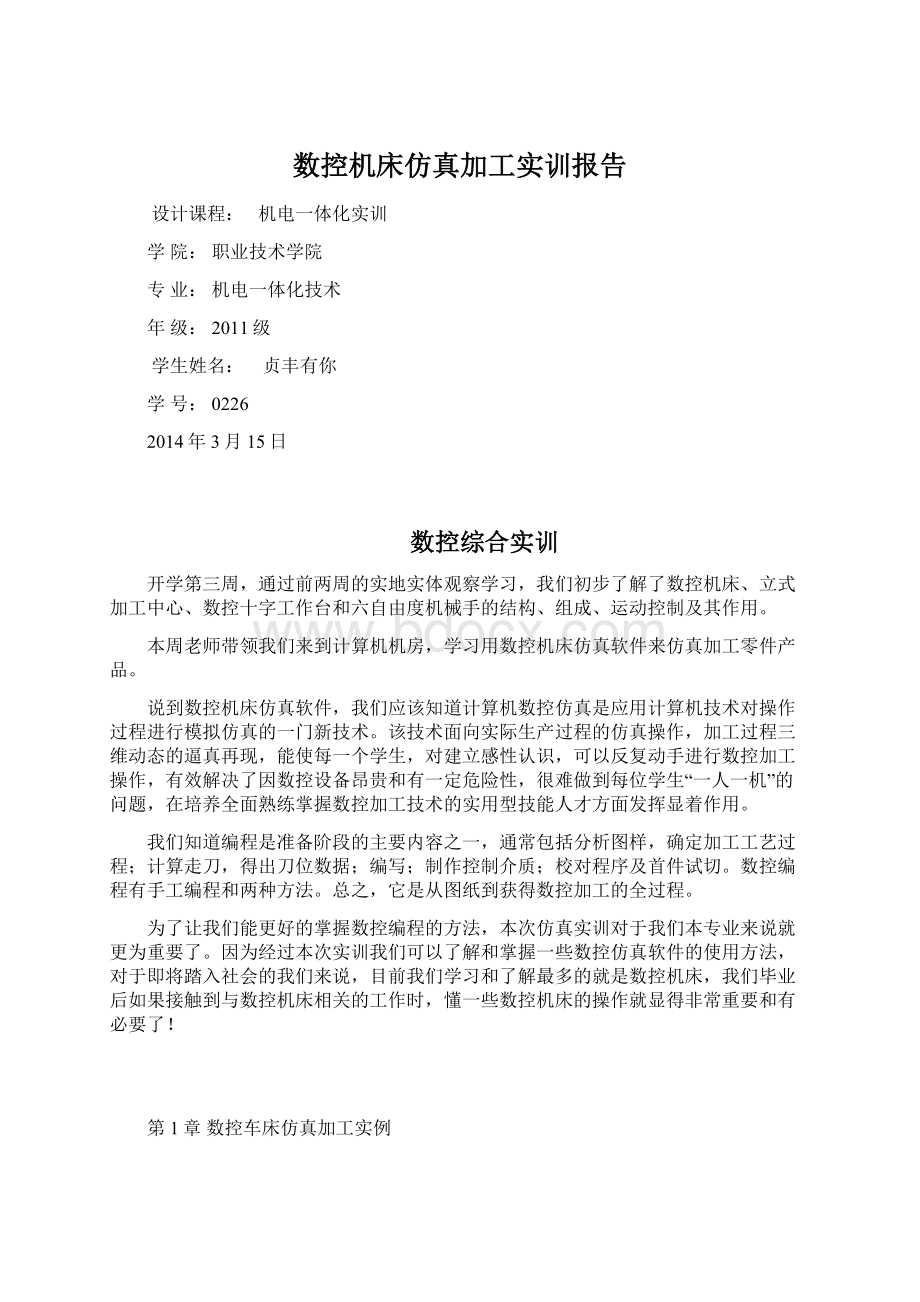
数控机床仿真加工实训报告
设计课程:
机电一体化实训
学院:
职业技术学院
专业:
机电一体化技术
年级:
2011级
学生姓名:
贞丰有你
学号:
0226
2014年3月15日
数控综合实训
开学第三周,通过前两周的实地实体观察学习,我们初步了解了数控机床、立式加工中心、数控十字工作台和六自由度机械手的结构、组成、运动控制及其作用。
本周老师带领我们来到计算机机房,学习用数控机床仿真软件来仿真加工零件产品。
说到数控机床仿真软件,我们应该知道计算机数控仿真是应用计算机技术对操作过程进行模拟仿真的一门新技术。
该技术面向实际生产过程的仿真操作,加工过程三维动态的逼真再现,能使每一个学生,对建立感性认识,可以反复动手进行数控加工操作,有效解决了因数控设备昂贵和有一定危险性,很难做到每位学生“一人一机”的问题,在培养全面熟练掌握数控加工技术的实用型技能人才方面发挥显着作用。
我们知道编程是准备阶段的主要内容之一,通常包括分析图样,确定加工工艺过程;计算走刀,得出刀位数据;编写;制作控制介质;校对程序及首件试切。
数控编程有手工编程和两种方法。
总之,它是从图纸到获得数控加工的全过程。
为了让我们能更好的掌握数控编程的方法,本次仿真实训对于我们本专业来说就更为重要了。
因为经过本次实训我们可以了解和掌握一些数控仿真软件的使用方法,对于即将踏入社会的我们来说,目前我们学习和了解最多的就是数控机床,我们毕业后如果接触到与数控机床相关的工作时,懂一些数控机床的操作就显得非常重要和有必要了!
第1章数控车床仿真加工实例
第1节数控车床仿真加工零件图
如图所示的零件,毛坯为Ф42×200mm的45号钢材料,其中圆柱面不加工。
图
第2节零件加工工艺分析
设定工件坐标系
按基准重合原则,将工作坐标系的原点设定在零件右端面与回转轴线的交点上,对刀时根据程序选择零件右端面端点对刀。
根据零件图的加工要求和编程情况,需要加工零件的端面、圆柱面、圆锥面、圆弧面、倒角,共需用两把刀具。
1号刀,外圆车刀,刀体参数:
刀杆长度160mm,刀杆宽度25mm;刀片类型:
选刀片斜度为35°,刀片边长20mm,刀片厚度3mm。
2号刀,外圆精车刀,刀体参数:
刀杆长度160mm;刀片类型:
选刀片斜度为35°或55°,刀片边长12mm,刀片厚度3mm。
第3节编写数控加工程序
仿真加工零件(图)的数控加工编程程序如下:
程序
注释
O0226
N1T0101
N2M03S1000
N3G00
N4G01
N5
N6
N7
N8
N9
N10
N11
N12
N13
N14
N15
N16G70P3Q15F50
N17G00
N18M05
N19T0202
N20M03S1200
N21G00
N22G02
N23
N24
N25G03
N26G01
N27G00
N28M05
N29M30
程序名
选择01号外圆车刀和01号刀补
主轴正转,转速设定为1000r/min
刀具快速定位至对刀上方位置
刀具快速定位至切削位置
车削右端面倒角
车Ф20mm端面,长26mm
车第二个倒角
车Ф24mm端面,长22mm
车削长度为35mm的斜面
X方向退刀至Ф40mm的位置
Z方向前进20mm
X方向进给到Ф35mm的位置
向z方向车削5mm
X方向退刀至Ф40mm的位置
Z方向前进20mm,到达128mm处
精加工N3到N15步骤
快速退刀到换到位置(回零)
主轴停
换02号外圆精车刀和02号刀补
主轴正转,转速设定为1200r/min
快速定位到凹圆切削位置
顺时针车削R为5mm的凹圆
X方向退刀至Ф30mm的位置
Z方向前进55mm,到达103mm处
逆时针车削R为18mm的凸圆
X方向退刀至Ф40mm的位置
快速退刀到换到位置(回零)
主轴停
程序结束
第4节数控仿真软件的安装运行
本次我选用的是南京宇航数控仿真系统版本中的”FANUC0iT“车床模块来介绍具体操作过程。
在网上下载好“南京宇航数控仿真系统”版本软件的压缩包后,解压压缩包,在解压包文件夹中点应用程序“”后出现如图的界面,选择“FANUC0iT”车床,即可进入如图所示的FANUC-0iT系统标准的操作界面。
图系统选择界面图版本信息
图FANUC-0iT标准面板
第5节数控仿真加工过程
机床回零
点击紧急停止按钮开关使其松开,机床将出现“请回机床参考点”提示,回零按钮
指示灯亮,CRT上显示
;单击
按钮,此时操作面板上X轴的回零指示灯亮
,X轴将自动回零,同时CRT上的X坐标变到零;同样操作可使机床Z轴回零。
此时CRT和操作面板上的指示灯如图所示。
图回零提示及回零后面板的显示
安装零件
点击菜单栏“工件操作/工件大小”或点左边竖着的快捷栏
-工件大小设置-工件大小,在“设置毛坯尺寸”对话框(如图)中,改写零件尺寸高和直径,单击按确定按钮。
为了节省材料可以使用工件长度短一点(128mm以上)的工件进行加工,操作方法是:
点击桌面左边竖着的快捷栏的最后两个向前
和向后
来控制零件移动的方向和尺寸大小,使零件伸出128mm以上防止碰刀(本次仿真假设的毛坯长度是200mm的,不用调节)。
图毛坯尺寸设置与显示
装刀具
点击菜单栏“机床操作/刀具库”或页面最左边竖栏的刀具管理快捷按钮
,在“刀具库管理”对话框中,根据加工方式选择所需选择刀具时双击所需刀具进入设置对话框(如图所示),设置好后点击确定退出,装好刀具后,机床如图所示。
注:
根据毛坯直径和加工的程序,外圆车刀的刀片边长必须大于等于13mm,不然会碰刀。
图修改刀具对话框
图刀具添加成功后的对话框
对刀和设定刀补
对刀:
点击菜单栏的“机床操作/对刀”或者点左边快捷栏的对刀
按钮,选择右端点为对刀点,如图所示。
设定刀补:
点击菜单栏的“工件测量/测量进入”,得到所车外圆直径D=,刀尖点所在Z坐标为0,如图所示;在MDI键盘上点击参数输入按钮
两次,点CRT屏幕上的软键
按钮两次会出现如图所示对话框,用方向键把光标移动到01刀具X位置,输入;单击CRT屏幕上的软键
按钮,把光标移动到Z位置,输入;单击CRT屏幕上的软键
按钮,如图和图;测量好01号刀后,点击“工件测量/测量退出”,从刀具中选择把02号刀转到加工位(图),然后用01号刀具对刀方法完成02号外圆精车刀的对刀。
对刀完成后CRT屏幕如图所示。
图对刀图测量刀补
图图
图图
输入NC程序
方法一:
先打开程序保护锁,然后点击编辑按钮
程序按钮
,再写O0226点击插入按钮
,然后写入程序内容,记得每写一步后面都要输入分号
,这样才会生产一个个步骤。
方法二:
程序用导入的方法,使用记事本或写字板等编辑软件输入完成后,点击“另存为”选择保存格式为所有格式,然后把文件名改为。
也可以先保存成txt格式,再重命名为NC格式的。
文档保存好以后,回到仿真操作面板,打开程序保护锁,点击操作面板上的编辑按钮
,使其指示灯亮;单击MDI键盘的程序按钮
,在MDI键盘上输入程序名称O0226;单击编辑栏的插入
按钮,然后点菜单栏上的“文件/打开”出现一个查找对话框,对话框的“文件类型”选择“NC代码文件”,找到保存好的程序所在的文件夹,找到,点击以后对话框左边会出现程序的内容,点打开后即可输入预先编辑好的数控程序,如图所示,此时CRT界面如图所示。
图图
检查运行轨迹
点菜单栏下方编辑快捷栏的
,查看对刀好以后的走到轨迹,看走到轨迹是否合理正确,会不会出现碰刀情况,其运行轨迹如图所示。
图
仿真自动加工
首先选择菜单栏的“机床操作/舱门”关闭舱门或者点击页面最左边竖栏的舱门开关
关闭舱门,点击操作面板中自动运行按钮
,再点击操作面板中循环启动按钮
,机床就开始自动加工,加工过程中和加工完成的工件的如图所示。
测量数据如图所示。
图
图
第2章数控铣床仿真加工
第1节数控铣床仿真加工零件图
图
第2节数控铣床加工程序
程序
注释
O0226
T01
G54
M03S1000
G00
G01F100
G00
M05
T02
M03S1000
G01F100
G00
M05
T03
M03S1200
G00
G90G03
G00
G01F100
M05
M30
程序名
选择01号刀
建立工件坐标系
主轴正转,转速设定为1000r/min
刀具快速定位至铣台的中心位置
刀具向Z轴方向的铣削深度为5mm
刀具快速退刀到铣台中心上方位置
主轴停
换02号刀具
主轴正转,转速设定为1000r/min
刀具向Z轴方向的铣削深度为25mm
刀具快速退刀至铣台中心上方位置
主轴停
换03号刀具
主轴正转,转速设定为1000r/min
刀具快速定位至铣台的中心位置,深度5mm
绝对值编程整圆加工程序,铣削深度5mm
快速定位至深度为5mm的铣台中心位置
刀具向Z轴方向的铣削深度为25mm
快速退刀到换到位置(回零)
主轴停
程序结束
第3节零件加工工艺分析
设定工件坐标系
针对加工中心的特点,将对刀原点设置在毛坯的左前端面。
刀具选择
1号刀,方肩铣刀或面铣刀,参数:
直径100mm,刀杆长度100mm;
2号刀,钻头刀,参数:
直径8mm,刀杆长度100mm
3号刀,镗刀,参数:
直径8mm,刀杆长度100mm(如图)
图方肩铣刀钻头刀镗刀
第4节数控铣床仿真加工
数控铣床的仿真加工与数控车床的仿真加工面板和操作过程基本一样,只是在对刀时有所区别,因此相同的操作过程参照第一章的相关内容。
FANUC0iM数控铣床操作面板
在解压包文件夹中点应用程序“”,选择“FANUC0iM”,即可进入如图所示的FANUC-0iM的操作界面。
铣床回零、工件装夹、刀具选择
回零:
铣床在按了急停按钮后的回零过程中多了一个Y轴的回零。
工件装夹:
点击菜单栏“工件操作/工件大小、原点”或左侧快捷栏按钮
设置工件尺寸是长150mm宽145mm,高100mm,如图所示;“工件操作/工件装夹”选择喜欢的装夹方式,如图所示。
图图
刀具选择:
根据第二章第三节的“”修改和添加刀具,确认后的对话框如图所示。
注:
刀具的选择与设置是根据所编写的程序来决定的,参数设置错误会导致加工的工件尺寸不合!
图
数控铣床对刀方法
该数控铣床仿真系统没有自动对刀的快捷键,可用基准芯棒来手动对刀。
手动对刀之前先选择基准芯棒,通过点击菜单栏“机床操作/基准芯棒选择”或左侧快捷工件设置
快捷键选择“基准芯棒选择”,参数:
基准芯棒H=100mm,D=20mm,塞尺h=1mm如图所示。
图左边为选择界面右边为选择以后的实物图包括基准芯棒和塞尺
本次的对刀选择毛坯左前端来对刀,通过以下的调节方式来手动移动X轴、Y轴和Z轴的机床坐标:
方法一:
连续移动
。
这种方法用于较长距离的台面移动。
(1)点击面板上的手动进给方式
,置模式旋钮在
位置;
(2)选择各轴
灯亮,按加
减
按钮来使各轴运动。
方法二:
点动
,这种方法用在对基准操作中的微量调整。
(1)置模式旋钮在手动脉冲方式“INC”位置
:
选择步进量
(2)选择各轴
按加
减
按钮来使各轴运动,每按一次加减,会进给设置的步进量的值,松开后停止。
对刀:
如图,用上面的方法一移动当基准芯棒到达毛坯左前端的位置时,左下角出现“塞尺检查:
过紧或过松”时用方法二来调节,使左下角的塞尺检查显示的是“合适”这样就可以停止调节,双击操作面板上的参数输入按钮
,选择屏幕下方的“坐标系”出现图的界面后,通过计算得到基准芯棒的半径为10mm,塞尺厚1mm,我们要向左边移动,于是找到G54工件坐标系的X轴,输入X,点击屏幕下方的测量
,便可得到X轴的坐标值;用相同的方法找到Y轴的对刀点,输入Y,得到Y轴的坐标值,如图。
对于Z轴的对刀是在毛坯上表面来对刀,当塞尺检查显示合格以后,输入即可得到Z轴的坐标值,如图。
完成后卸下测量芯棒。
对刀完成后的数值如图所示。
注:
对刀的数据可能会有一些小误差,可根据仿真加工后所测量的偏差值进行修改。
图X轴的对刀图操作面板图Y轴的对刀
图Z轴的对刀图对刀完成后操作面板的数据
对刀好以后便是输入程序(参照第一章相关内容),然后点显示刀轨
查看刀轨是否会碰刀,如下图。
图
仿真加工
总结
在本次实训中我发现作为一名即将走向工作岗位的大学毕业生,应当养成一种认真严谨的态度。
经过本次的上机模拟练习让我学到了许多数控相关的知识,让我有很大收获的。
这次实践练习给了我一次全面的、系统的锻炼的机会,巩固了我们这两年多以来所学的关于数控方面的理论知识,增强了我的实际操作能力,使我进一步从实践中认识到了数控的重要性。
同时,使我认识到在工作中光有理论知识是不够的,还要能把理论运用到实践中去才行。
正如俗话说的:
实践是检验真理的唯一标准。
这次实训把理论知识运用到实际操作中,既是对实际操作能力的培训,又是对理论知识的复习巩固和延伸。
首先要完全理解数控车床安全操作规程,然后通过电脑让我们熟悉操作面板。
在老师的教导下,我们掌握了数控车床的开机与关机;回零的操作以及什么情况下必须回零操作;手动方式主轴正转;编制程序以及如何输入程序;如何对刀和换刀操作,以及使用刀具补偿命令编制程序,尤其是系统在编制程序中使用的G代码等。
经过反复的练习,我们基本熟练掌握了这些实际操作必备的技能。
?
最后,衷心感谢老师的悉心指导和帮助!