轴类零件数控加工工艺设计与编程.docx
《轴类零件数控加工工艺设计与编程.docx》由会员分享,可在线阅读,更多相关《轴类零件数控加工工艺设计与编程.docx(27页珍藏版)》请在冰豆网上搜索。
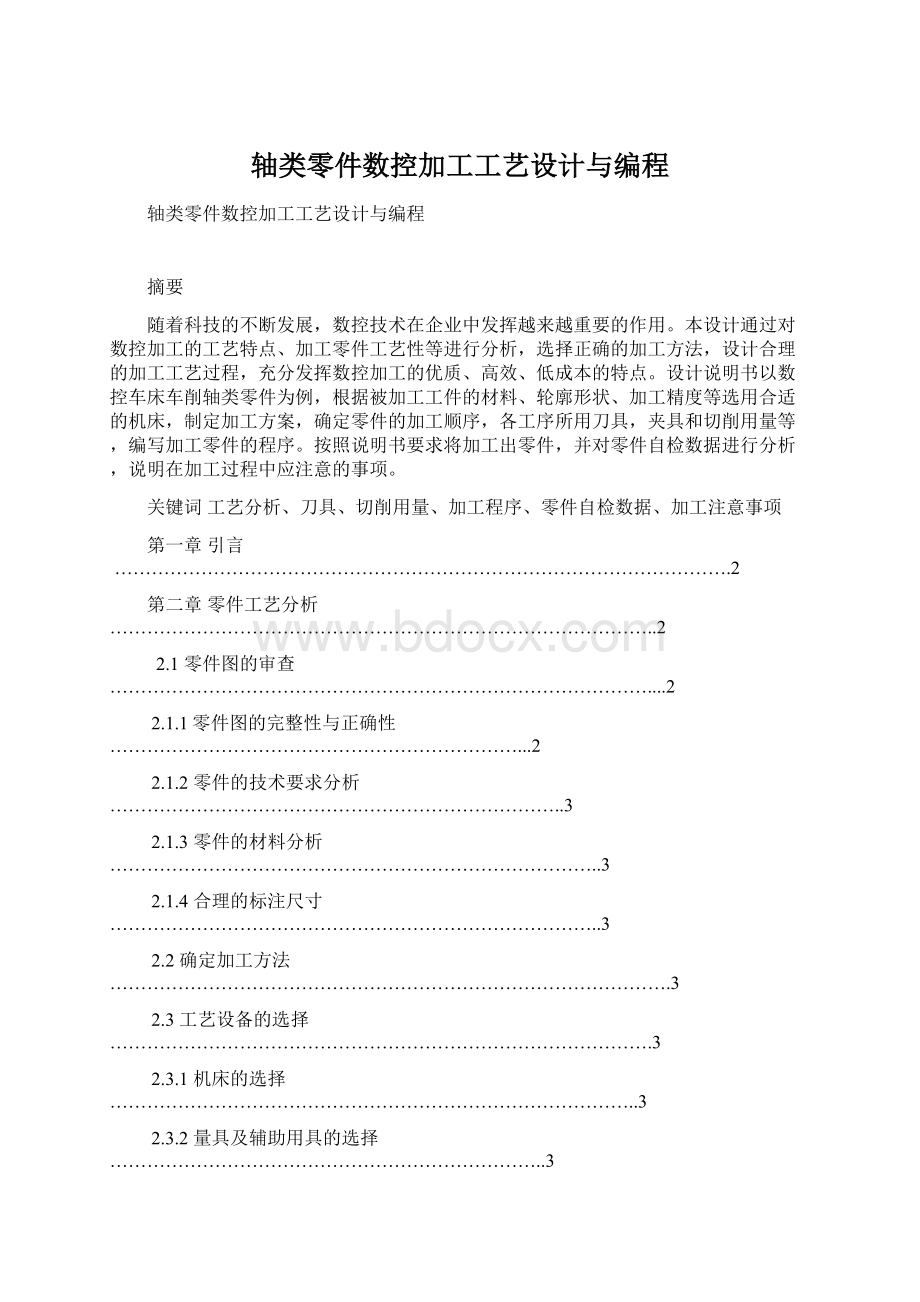
轴类零件数控加工工艺设计与编程
轴类零件数控加工工艺设计与编程
摘要
随着科技的不断发展,数控技术在企业中发挥越来越重要的作用。
本设计通过对数控加工的工艺特点、加工零件工艺性等进行分析,选择正确的加工方法,设计合理的加工工艺过程,充分发挥数控加工的优质、高效、低成本的特点。
设计说明书以数控车床车削轴类零件为例,根据被加工工件的材料、轮廓形状、加工精度等选用合适的机床,制定加工方案,确定零件的加工顺序,各工序所用刀具,夹具和切削用量等,编写加工零件的程序。
按照说明书要求将加工出零件,并对零件自检数据进行分析,说明在加工过程中应注意的事项。
关键词工艺分析、刀具、切削用量、加工程序、零件自检数据、加工注意事项
第一章引言 ……………………………………………………………………………………….2
第二章零件工艺分析……………………………………………………………………………..2
2.1零件图的审查……………………………………………………………………………....2
2.1.1零件图的完整性与正确性…………………………………………………………...2
2.1.2零件的技术要求分析………………………………………………………………..3
2.1.3零件的材料分析……………………………………………………………………..3
2.1.4合理的标注尺寸……………………………………………………………………..3
2.2确定加工方法……………………………………………………………………………….3
2.3工艺设备的选择…………………………………………………………………………….3
2.3.1机床的选择…………………………………………………………………………..3
2.3.2量具及辅助用具的选择……………………………………………………………..3
2.4零件的安装…………………………………………………………………………………..3
2.5选择夹具…………………………………………………………………………………….3
2.6刀具的选择………………………………………………………………………………….3
2.7切削用量的选择…………………………………………………………………………….4
2.7.1主轴转速的确定……………………………………………………………………..4
2.7.2进给速度的确定……………………………………………………………………..5
2.7.3背吃刀量得确定……………………………………………………………………..5
2.8对刀点与换刀点的确定…………………………………………………………………….6
2.9工序与工步的划分……………………………………………………………….................6
2.10加工路线的确定…………………………………………………………………………...6
第三章加工工序的设计…………………………………………………………………………7
3.1工序一……………………………………………………………………………………..7
3.1.2工件的装夹方式……………………………………………………………………7
3.1.4切削用量计算………………………………………………………………………7
3.1.5工艺路线……………………………………………………………………………8
3.1.6加工程序……………………………………………………………………………8
3.17加工工序卡片……………………………………………………………………….9
3.1.8加工中的难点与解决方案…………………………………………………………9
3.2工序二……………………………………………………………………………………...10
3.2.1尺寸链的计算………………………………………………………………………10
3.2.3工件的装夹方式……………………………………………………………………10
3.2.4刀具选择……………………………………………………………………………10
3.2.5切削用量计算………………………………………………………………………10
3.2.6工艺路线……………………………………………………………………………11
3.2.7加工程序……………………………………………………………………………12
3.2.8加工工序卡片………………………………………………………………………12
3.2.9加工中的难点与解决方案…………………………………………………………13
第四章注意事项…………………………………………………………………………………13
4.1数控车操作注意事项……………………………………………………………………...13
第五章成品自检数据……………………………………………………………………………13
第一章引言
本设计说明书是根据《鄂东职业技术学院数控技术应用专业毕业设计指导书》要求编写的。
随着我国工业化进程的加速,产业结构的调整和升级,数控技术在现代企业中得到了广泛的应用,使制造业朝着数字化的方向发展。
本设计以熟练掌握数控车床加工为主要目的,在认真分析零件工艺的基础上,综合运用《公差》、《机械制造技术》、《数控加工与编程》、《数控加工工艺》等专业知识,结合数控加工实际操作,按照机械加工工艺规程的内容,制定出的轴类零件数控加工工艺说明书。
本设计说明书包括零件的工艺分析、零件加工过程、加工注意事项、成品自检数据等内容。
并详细介绍零件工艺分析的内容,重点阐述了零件的加工过程,认真分析和解释零件加工的程序的意义。
本设计在编写过程中得到许多老师和同学的支持与帮助,方波老师、熊霞丽老师和周成松老师对本设计进行认真的审阅,提出了许多宝贵的修改意见,在此一并表示衷心的感谢。
由于编者水平有限,设计中难免存在一些错误,恳请老师和同学批评指正。
编 者
2007年11月25日
第二章零件工艺分析
2.1 零件图的审查
2.1.1零件图的完整性与正确性
零件属于短轴类,零件长度为145mm,从左到右依次为:
长23mm、公称直径为30mm、有2mm的45°倒角的普通螺纹;长22mm的20°锥面;长32mm直径为47的圆柱面,并在其表面切出3个间隔5mm的3.5mm深3.5mm的槽;长为13.77mm直径为35的圆柱面;直径为52mm的球面;直径为36mm的圆柱面。
该零件视图正确,表达直观、清楚,绘制符合国家标准,尺寸、公差、表面粗糙度以及技术要求的标注齐全、合理。
2.1.2零件的技术要求分析
分析零件图可知:
20°锥面、φ47mm圆柱面、φ35mm圆柱面和φ36mm圆柱面表面粗糙度Ra为1.6μm,其余表面粗糙度Ra为3.2μm。
大端为φ47mm锥面的轴线对基准A(轴线)的同轴度公差为φ0.025mm,外螺纹中径、顶径公差代号为6g,内螺纹中径、顶径公差代号为6G。
其余尺寸公差等级在IT7~IT10之间。
2.1.3零件的材料分析
毛坯材料为45#,强度、硬度、塑性等力学性能好,切削性能、热处理性能等加工工艺性能好,便于加工,能够满足使用性能。
毛坯下料为φ60mm×150mm。
2.1.4合理的标注尺寸
零件图上的重要尺寸直接标注,在加工时使工艺基准与设计基准重合,并符合尺寸链最短的原则。
零件图上标注的尺寸便于用卡尺或样板测量。
2.2确定加工方法
经过分析零件的尺寸精度、几何形状精度、位置精度和表面粗糙度要求,确定如下加工方法:
(1)外圆表面:
粗车——半精车——精车
(2)外螺纹:
在精车的外圆表面分数次进给加工
(3)内螺纹:
钻孔——粗镗——半精镗——精镗——在精镗表面分数次进给加工。
2.3工艺设备的选择
2.3.1机床的选择
机床选择的原则:
①要保证加工零件的技术要求,加工出合格的产品。
②有利于提高生产率。
③尽可能降低生产成本(加工费用)。
根据毛坯的材料和类型、零件轮廓形状复杂程度、尺寸大小、加工精度、工件数量、生产条件等要求,选用CJK6132数控车床。
2.3.2量具及辅助用具的选择
加工过程中所需量具有:
游标卡尺、千分尺、百分表、表面粗糙度样板。
辅助用具有:
铜片、铜锤等。
2.4零件的安装
在数控机床上加工零件时,安装零件要合理选择定位基准和夹紧方案,为提高数控机床效率,确定定位基准与夹紧方案时应注意:
(1)力求设计、工艺与编程计算的基准统一(基准重合原则);
(2)减少装夹次数,尽可能在一次定位装夹后,加工出全部待加工表面(基准统一原则);
(3)避免采用占机人工调整式加工方案,以充分发挥数控机床的效能。
2.5选择夹具
夹具用来装夹被加工工件以完成加工过程,同时要保证被加工工件的定位精度,并使装卸尽可能方便、快捷。
数控加工的特点对夹具提出了两个基本要求:
一是要保证夹具的坐标方向与机床的坐标方向相对固定;二是要协调零件和机床坐标系的尺寸关系。
根据零件的尺寸、精度要求和生产条件,选择最常用的车床通用的三爪自定心卡盘。
三爪自定心卡盘可以自动定心,夹持范围大,适用于截面为圆形、三角形、六边形的轴类和盘类中小型零件。
2.6 刀具的选择
数控加工中的刀具选择和切削用量确定是在人机交互状态下完成的要求编程人员必须掌握刀具选择和切削用量确定的基本原则,在编程时充分考虑数控加工的特点,能够正确选择刀刃具及切削用量。
数控刀具有以下特点:
①刚性好(尤其是粗加工刀具)、精度高、抗振及热变形小;②互换性好,便于快速换刀;③寿命高,切削性能稳定、可靠;④刀具的尺寸便于调整,以减少换刀调整时间;⑤刀具应能可靠地断屑或卷屑,以利于切屑的排除;⑥系列化、标准化,以利于编程和刀具管理。
数控机床上用的刀具应满足安装调整方便、刚性好、精度高、耐用度好等要求。
数控车床兼作粗精车削,粗车时吃刀深、进给快,要求车刀有足够的强度,能一次进给车去较多的余量;精车时要达到图样要求的尺寸精度和较小的表面粗糙度,车去的余量较少,要求车刀锋利,切削刃平直光洁,必要时还可磨出修光刃。
为减少换刀时间、方便对刀、提高生产效率,便于实现机械加工的标准化,在数控车削加工时,应尽量采用机夹刀和机夹片刀,机夹片刀常采用可转位车刀。
刀片材质的选择主要依据被加工工件的材料、被加工表面的精度、表面质量要求、切削载荷的大小以及切削过程有无冲击和振动,故加工此零件选择硬质合金刀片。
根据零件的外形结构,加工需要如下刀具:
硬质合金端面车刀、菱形外圆车刀、外切槽刀、外螺纹刀、内孔镗刀、30°外圆尖刀、φ5mm中心钻、φ22mm标准麻花钻。
数控加工刀具卡片
序号
刀具号
刀具规格名称
数量
加工表面
备注
1
T01
45°硬质合金端面车刀
1
平端面
手动
2
T02
80°菱形外圆车刀
1
粗车零件左端外轮廓
自动
3
T03
55°菱形外圆车刀
1
精车零件左端外轮廓
自动
4
T04
3mm外切槽刀
1
切槽
自动
5
T05
60°外螺纹刀
1
加工外螺纹
自动
6
T06
φ5mm中心钻
1
钻φmm中心孔
手动
7
T07
φ22mm钻头
1
钻底孔
手动
8
T08
45°外圆车刀
1
粗车零件右端外轮廓
自动
9
T09
30°外圆尖刀
1
精车零件右端外轮廓
自动
数控加工刀具卡片续表一
10
T10
80°内镗刀
1
粗镗内孔表面
自动
11
T11
55°内镗刀
1
精镗内孔表面
自动
12
T12
60°内螺纹刀
1
加工内螺纹
自动
2.7 切削用量的选择
数控编程时,必须确定每道工序的切削用量,并以指令的形式写入程序中,切削用量包括主轴转速、进给速度及背吃刀量等。
切削用量的选择原则是:
保证零件加工精度和表面粗糙度,充分发挥刀具的切削性能,保证合理的刀具寿命,充分发挥机床的性能,最大限度的提高生产率,降低成本。
2.7.1主轴转速的确定
(1)车外圆时主轴转速
主轴转速应根据允许的切削速度和工件(或刀具)直径来选择。
其计算公式为
n=1000v/πd
其中 v—切削速度(m/min),由刀具寿命决定;
n—主轴转速(r/min);
d—工件直径或刀具直径(mm)。
(2)车螺纹时主轴的转速
在车削螺纹时,车床的主轴转速将受到螺纹的螺距P(或导程)大小、驱动电机的升降频特性,以及螺纹插补运算速度等多种因素影响,故对于不同的数控系统,推荐不同的主轴转速选择范围。
大多数经济型数控车床推荐车螺纹时的主轴转速n(r/min)为:
n≤(1200/P)-k
式中 P——被加工螺纹螺距,㎜;
k——保险系数,一般取为80。
主轴转速n最后要根据上述计算值、机床说明书而定,选取机床有的或较接近计算值的转速。
2.7.2进给速度的确定
进给速度是数控机床切削用量中的重要参数,主要根据零件的加工精度和表面粗糙度要求以及刀具、工件的材料性质选取。
最大进给速度受机床刚度和进给系统的性能限制。
确定进给速度的原则是:
(1)当工件的质量要求能得到保证时,为提高生产效率,可选择较高的进给速度。
一般在100~200mm/min范围内选取。
(2)在切断、加工深孔或用高速钢刀具加工时,宜选择较低的进给速度,一般在20~50mm/min范围内选取。
(3)当加工精度、表面粗糙度要求较高时,进给速度应选小一些,一般在20~50mm/min范围内选取。
(4)当刀具空行程,特别是远距离“回零”时,可以设定该机床数控系统设定的最高进给速度。
2.7.3背吃刀量的确定
背吃刀量根据机床、工件和刀具的刚度来决定,在刚度允许的条件下,应尽可能使背吃刀量等于工件的加工余量,这样可以减少走刀次数,提高生产效率。
为了保证加工表面质量,可以留少许加工余量,一般为0.2~0.5mm。
切削用量的选择是否合理,对于能否充分发挥机床潜力与刀具的切削性能,实现优质、高产、低成本和安全操作具有很重要的作用。
车削用量的具体选择如下:
粗车时,首先选择一个尽可能大的背吃刀量,其次选择一个较大的进给量,最后确定一个合适的切削速度。
精车时,加工精度和表面粗糙度要求较高,加工余量不大且均匀,因此选择较小的背吃刀量和进给量。
如何确定加工时的切削速度,除了可参考《数控加工技术》表2-1列出的数值外,主要根据实践经验进行确定。
数控车削用量推荐表
工件材料
工件材料
切削深度/mm
切削速度/(m.min-1)
进给量/(mm.r-1)
刀具材料
碳素钢 (δb >600Mpa)
粗加工
5~7
60~80
0.2~0.4
YT类
粗加工
2~3
80~120
0.2~0.4
精加工
0.2~0.3
120~150
0.1~0.2
钻中心孔
500~800
W18Cr4V
钻孔
~30
0.1~0.2
切断(宽度<5mm)
70~110
0.1~0.2
YT类
铸铁
(200HBS以下)
粗加工
50~70
0.2~0.4
YG类
精加工
70~100
0.1~0.2
切断(宽度<5mm)
50~70
0.1~0.2
此外,在安排粗、精车削用量时,应注意机床说明书给定的允许切削用量范围,对于主轴采用交流变频调速的数控车床,由于主轴在低转速时扭矩降低,尤其应注意此时的切削用量选择。
2.8对刀点与换刀点的确定
工件装夹方式确定后,即可通过确定工件原点来确定工件坐标系。
如果要运行这一程序来加工工件,必须确定刀具在工件坐标系开始运动的起点。
程序起始点或起刀点一般通过对刀来确定,所以,该点又称为对刀点。
在编制程序时,要正确选择对刀点的位置。
对刀点设置原则是:
(1)便于数值处理和简化程序编制;
(2)易于找正并在加工过程中便于查找;(3)引起的加工误差小。
对刀点可以设置在加工零件上,也可以设置在夹具或机床上,尽可能设在零件的设计基准或工艺基准上。
换刀点是指加工过程中需要换刀时刀具的相对位置点。
换刀点往往设在工件的外部,以能顺利的换刀、不碰撞工件和其他部件为准。
本零件将对刀点设在装夹后右端面中心,换刀点设在离对刀点x、z方向分别为100,100的位置。
2.9工序与工步的划分
在数控机床上加工零件,工序可以比较集中,一次装夹应尽可能完成全部工序。
常用工序划分原则有:
(1)保证精度原则。
数控加工要求工序应尽可能集中,通常粗、精加工在一次装夹下完成,为减少热变形和切削力变形对工件的形状、位置精度、尺寸精度和表面粗糙度的影响,应将粗、精加工分开进行。
此时可用不同的机床或不同的刀具进行加工,通常在一次安装中,不允许将零件的某一部分表面加工完毕后,再加工零件的其他表面。
对轴类或盘类零件,将待加工面先粗加工,留少量余量再精加工,以保证表面质量要求。
对轴上有孔、螺纹加工的工件,应先加工表面而后加工孔、螺纹。
(2)提高生产效率的原则。
在数控加工中,为减少换刀次数,节省换刀时间,应在需用同一把刀加工的加工部位全部完成后,再换另一把刀来加工其他部位。
同时应尽量减少空行程,当用同一把刀加工工件的多个部位时,应以最短的路线到达各加工部位。
按照上述划分原则,综合本零件的工艺性,装夹一次为一个工序,换一次刀为一个工步。
故加工此零件划分两个工序,加工左端为第一道工序,有5个工步;调头后加工为第二道工序,有7个工步。
2.10 加工路线的确定
在数控加工中,刀具刀位点相对于工件的运动轨迹和方向称为加工路线。
即刀具从对刀点开始运动起,直至结束,加工程序所经过的路径,包括切削加工的路径及刀具引入、返回等非切削空行程。
加工路线的确定原则主要有以下几点:
(1)应能保证零件的加工精度和表面粗糙度的要求,且效率高。
(2)应尽量缩短加工路线,既可以减少程序段,又可以减少刀具空程移动时间。
(3)应使数值计算简单,以减少编程工作量。
此外,确定加工路线时,还要考虑工件的加工余量和机床、刀具的刚度等情况,确定是一次走刀,还是多次走刀完成加工。
按照上述原则,确定如下加工路线:
工序一:
①夹φ60mm毛坯,平端面;
②粗车φ30mm外圆柱面、20°锥面、φ47mm圆柱面;
③精加工上述轮廓;
④切槽;
⑤车M30×2螺纹。
工序二:
①调头夹φ47mm圆柱面,打φ5mm中心孔;
②粗车φ36mm圆柱面、R10mm圆弧面、φ52mm圆球面和φ35mm圆柱面;
③精车上述轮廓;
④钻φ22mm孔;
⑤粗镗孔;
⑥精镗孔;
⑦车M30×2内螺纹。
第三章 加工工序的设计
经过零件的工艺分析,确定加工零件时采用调头加工,编程时尺寸公差取中间值。
编程所用尺寸说明:
20°锥面小端的直径为39.2416mm,φ36圆柱面长度为7.3726mm,R10圆弧面与Sφ52圆球面相交处直径为40.4444mm,此点距零件右端面距离为13.6580mm,Sφ52圆球面与φ35圆柱面相交处距右端面距离为49.2289mm。
3.1 工序一
3.1.1 确定工件坐标系
装夹毛坯φ60mm外圆,平端面,对刀,将工件原点设在右端面中心(此端面为精加工表面,以后不再加工)。
换刀点选在离对刀点x、z方向分别为100,100的位置。
3.1.2 工件的装夹方式
用三爪自定心卡盘夹毛坯φ60mm外圆,探出100mm左右,车零件左端至φ47mm与φ35mm外圆相交处。
3.1.3 加工刀具的选择
T0101——45°端面车刀,车端面,刀尖圆弧半径0.8mm。
T0202——90°菱形外圆右偏刀,粗车外圆,刀尖圆弧半径0.8mm。
T0303——80°菱形外圆右偏刀,精车外圆,刀尖圆弧半径0.8mm。
T0404——3mm外切槽刀,车槽,刀尖圆弧半径0.8mm。
T0505——60°外螺纹刀,车螺纹,刀尖圆弧半径0.8mm。
3.1.4 切削用量计算
根据《数控车削用量推荐表》,选择合适的切削用量。
(1)车端面时选择主轴转速为500r/min;
(2)粗车外圆时,选取Vc=120m/min,f=0.2mm/r,ap=2mm,粗加工时直径为60mm。
则:
主轴转速:
n=1000Vc/πd
=[(1000×120)/(3.14×60)]r/min=636r/min
进给速度:
F=f×n=(0.2×636)mm/min=127mm/min
考虑刀具强度、机床刚度等实际情况,选择n=600r/min,F=150mm/min,ap=2mm。
(3)精车外圆时,选取Vc=150m/min,f=0.1mm/r,ap=0.2mm,精加工时取直径40mm。
则:
主轴转速:
n=1000Vc/πd
=[(1000×150)/(3.14×40)]r/min=1194r/min
进给速度:
F=f×n=0.1×1194mm/min=119.4mm/min
考虑刀具强度、机床刚度等实际情况,选取n=1200r/min,F=100r/min,ap=0.2mm。
(4) 车槽时,选择Vc=70m/min,f=0.1mm/r,车槽时直径为47mm。
则:
主轴转速:
n=1000Vc/πd
=[(1000×70)/(3.14×47)]r/min=474r/min
进给速度:
F=f×n=(0.1×474)mm/min=47.4mm/min
考虑刀具强度、机床刚度等实际情况,选取n=400r/min,F=30r/min。
(5)车螺纹时,主轴转速n≤(1200/P)-k,k为安全系数,一般取80。
则:
n≤[(1200/2)-80]/r/min=520r/min
考虑刀具强度、机床刚度等实际加工情况,选取n=400r/min.
3.1.5 工艺路线
(1)用1号端面车刀手动平端面;
(2)用2号80°菱形外圆车刀使用G71外圆粗车复合循环粗车零件左端外轮廓:
φ30mm圆柱面、20°锥面、φ47mm圆柱面;
(3)用3号55°菱形外圆车刀精车上述轮廓;
(4)用4号外切槽刀车φ47mm圆柱面上的三个槽;
(5)用5号60°外螺纹刀车M30×2螺纹;
3.1.6 加工程序
%0001 ;程序头
T0202